Technical Product Profile
32 Pages
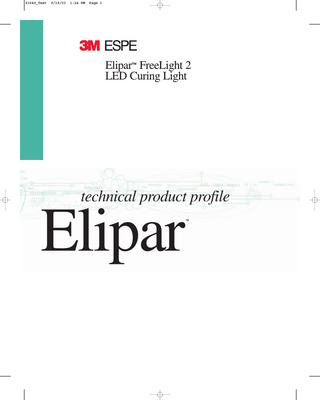
Preview
Page 1
61649_Text
9/19/03
1:24 PM
Page 1
Elipar™ FreeLight 2 LED Curing Light
technical product profile
Elipar
TM
61649_Text
2
9/19/03
1:24 PM
Page 2
CX 61649_Text 9/23/03 4:25 PM Page 3
Table of Contents Introduction...5 Technical Design...10 Indications...11 Technical Properties...12 Technique Guide...16 Instructions for Use...18 Questions and Answers...26 Summary...27 References...28 Technical Data...30
3
61649_Text
4
9/19/03
1:24 PM
Page 4
61649_Text
9/19/03
1:24 PM
Page 5
Introduction The long-term success of clinical composite restorations depends on complete and appropriate polymerization, optimal materials, and a suitable dentin bonding system. The efficiency of light-initiated polymer curing is generally discussed in terms of radiation flux density, or light intensity (mW/cm2). High light intensities were required for complete composite polymerization, particularly for deep cavities. Incomplete polymerization allows deterioration of mechanical and physical material properties, and increases both water absorption and susceptibility to discoloration. The effective range of the light emission spectrum that can initiate polymerization is narrow. Though halogen lamps are the most frequently used dental polymerization devices, only a small part of their wide spectral emission occurs in the useful range. Much of the light emitted from these lamps is, therefore, ineffective and may cause unwanted increases in tooth temperature. Unlike halogen lamps, light emitting diodes (LEDs) combine specific semi-conductors to produce blue light. LEDs generate a narrow emission spectrum ideally suited for the polymerization of dental composites.
Overview of Light Curing Technologies The effectiveness of blue light in light curing of dental composites has been known since the 1970s. Halogen lamps are the most frequently used source of light for this purpose. Blue light with wavelengths between 410 and 500 nm is of central importance because the absorption maximum of the sensitizer component of most dental material photoinitiator systems (camphorquinone) occurs in this range (465 nm). When camphorquinone is exposed to light in the presence of an amine-based co-initiator, radicals are formed, initiating polymerization. At present, the following three major technologies for light curing of materials are used in dental practice: • Halogen lamps • Plasma arc lamps • LED lamps Key differences, benefits, and drawbacks of these three light sources are compared below.
5
61649_Text
9/19/03
1:24 PM
Page 6
Halogen Lamps The physical basis for light production is that heated objects emit electromagnetic radiation. In the case of halogen lamps (the most commonly used light source for polymerization of dental materials), light is produced when an electric current flows through a thin tungsten filament. Because the filament acts as a resistor, the passage of current generates heat. A filament heated to approximately 100°C gives off heat energy in the form of infrared radiation (long wavelengths). When the temperature is increased to between 2000 and 3000°C, a significant portion of the radiation is emitted in the visible light spectrum (shorter wavelengths). Wien’s law describes the shift in light color produced by rising temperature. Incremental increases in the temperature increase the intensity proportion of the still shorter wavelength radiation, including wavelengths in the blue light range. Therefore, with further heating a red-hot object becomes incandescent. To provide blue light for photopolymerization, halogen lamps must be heated to very high temperatures. Consequently, preferential production of blue light is not possible with this kind of technology. Further benefits and drawbacks of halogen lamps are shown in Table 1. Table 1. Benefits and drawbacks of halogen lamps Benefits
Drawbacks
Low cost technology
Low efficiency
Longest history in dental industry
Short service life High temperatures (lamp is cooled by a ventilating fan) Continuous spectrum must be narrowed by filter systems
Halogen lamps emit a range of wavelengths covering a large part of the spectrum, and therefore are analogous to a Planck radiator. Their collective emission results in production of white light. In order to produce light of a specific color, unwanted portions of the spectrum must be filtered out. As a result, the largest part of the radiative power of this light source is wasted. The central drawback of halogen lights is the need to overcome waste heat produced during wide spectrum light production. In addition, since a fan cooling air current must enter and exit through slots in the frame casing, disinfection of the handpiece is compromised. Another drawback of halogen lights is that the bulb, reflector, and filter can degrade over time, interfering with light unit power output and contributing to bulb fading. The lamp reflector may lose its reflective properties because of loss of reflective material, or deposition of surface impurities. Filter coatings may become pitted, chipped, or flaky, and the filters themselves may crack or break. Loss of these properties typically reduces light output.
6
61649_Text
9/19/03
1:24 PM
Page 7
Plasma Arc Lamps Plasma arc curing lamps are also among recently developed methods for light curing. Manufacturers of these devices claim that cured materials retain mechanical properties comparable to those produced by conventional treatment, while curing times are significantly reduced. Light produced by plasma arc lamps is different from that generated by halogen lamps. Rather than relying upon a heated tungsten filament, plasma arc lamps work by application of high voltage current across two closely placed electrodes, resulting in a light arc between the electrodes. However, Planck’s radiation law also pertains to plasma arc lamps. Like halogen lamps, plasma arc lamps emit a continuous spectrum of light, so their operating temperatures increase in proportion to the amount of blue light produced. Table 2. Benefits and drawbacks of plasma arc technology Benefits
Drawbacks
Shorter polymerization times
Very low efficiency
High temperature development (lamp is situated in the base unit and cooled by a ventilating fan) Continuous spectrum must be narrowed by filter systems Expensive
LED Lamps (such as Elipar™ FreeLight and FreeLight 2 LED Curing Lights)
In contrast to halogen and plasma arc lamps, LEDs produce visible light by quantum-mechanic effects. LEDs comprise a combination of two different semiconductors, the ‘n-doped’ and the ‘pdoped’ type. N-doped semiconductors have an excess of electrons while p-doped semiconductors require electrons, resulting in creation of electron ‘holes.’ When these two types of semiconductors are combined and a voltage is applied, electrons from the n-doped type connect with holes from the p-doped type. A characteristic light with a specific wavelength range is then emitted from the LED. The color of an LED light, its most important characteristic, is determined by the chemical composition of the semiconductor combination. Semiconductors are in turn characterized by their band gap. In LEDs, this gap is directly utilized for light production. When electrons in the semiconductor combination move from higher to lower energy levels, the energy difference of the band gap is released in the form of a photon of light (Figure 1). Figure 1. Structure of an LED (from Scientific American, 2, 63-67 (2001))
7
61649_Text
9/19/03
1:24 PM
Page 8
In contrast to halogen and plasma arc lamps, LEDs produce light with a narrow spectral distribution. This is the main difference between light produced by LEDs and other light sources, as light of selected wavelengths can be preferentially produced using LEDs with appropriate band gap energies. This innovative method of light production therefore creates a more efficient way of converting an electric current into light. Table 3 summarizes the benefits and drawbacks of LED technology. Table 3. Benefits and drawbacks of LED technology Benefits
Drawbacks
Consistent output, with no bulbs to change
Due to the narrow emission spectrum LEDs can only polymerize materials with an absorption maximum between 430 and 480 nm (camphorquinone as photoinitiator)
No need for filter systems High efficiency leads to: Low temperature development (no ventilation fan required) Low power consumption (battery-operation is possible) Frame can be easily cleaned, since no slots for a ventilation fan are needed Long service life of the LEDs Quiet
LEDs offer new options in light-catalyzed polymerization of dental materials. Their use has been considered in dentistry since the development of blue diodes in the 1990s. Investigations by Fujibayashi et al, demonstrated that at a constant light intensity of 100mW/cm2, the depth of composite curing and the degree of monomer conversion was significantly improved using an LED versus a halogen lamp.1 This study demonstrates that the quality of polymerization depends upon the narrow absorption peak of the initiator system, and makes the emitted spectrum an important determinant of a curing light’s performance. The primary absorption curve of camphorquinone ranges from 360 to 520 nm, with its maximum found at 465 nm. Within this range, optimal emission of the light source lies between 450 and 490 nm.2 In conventional curing devices, most photons are emitted outside the optimal spectrum range for light curing. Without additional events, these photons cannot be absorbed by camphorquinone. In contrast, 95% of photons emitted by blue LEDs occur between 440 and 500 nm, while the emission maximum of the blue LEDs used in the Elipar™ FreeLight 2 LED curing light is approximately 465 nm, almost identical to the absorption peak of camphorquinone. Most blue LED photons can therefore interact with camphorquinone, explaining the greater depth of cure and monomer conversion noted with LED versus halogen lamps, despite their operating at an equivalent light intensity of 100mW/cm.2
1. Fujibayashi K, Ishimaru K, Takahashi N, Kohno A. Newly developed curing unit using blue light-emitting diodes. Dent. Jpn, 1998, 34:49-53. 2. Nomoto R. Effect of light wavelength on polymerization of light-cured resins. Dent Mater J, 1997, 16:60-73.
8
61649_Text
9/19/03
1:24 PM
Page 9
At clinically relevant light intensities, a slight increase in the depth of cure was noted when composites were polymerized with an LED lamp versus a halogen lamp. This difference occurred despite use of an LED lamp with a measured output only 70% that of the halogen lamp (276 versus 388 mW/cm2, measured between 410 and 500 nm).3 This finding underscores the importance of considering the emission spectra of curing lamps relative to the absorption spectrum of camphorquinone when assessing the quality of light polymerization.
Technology Trends Two key technical developments have recently taken place regarding lights used for dental curing. First, lights with fast curing capabilities now offer considerable time savings, which is extremely important to dental clinicians. However, very rapid curing claims of several seconds are controversial, as restoration quality associated with these processes does not meet conventional standards. Rapid curing devices are currently available with halogen and plasma arc lamps. The major disadvantage of these devices is that they consume large amounts of power, necessitating bulky desktop devices or traditional pistol grip hand pieces with fan and power cords. Second, LED-based curing lights have been developed for photopolymerization of dental materials. These devices are considerably more efficient than halogen or plasma arc bulbs, and their small size and portability have enhanced their market success. The first generation LED curing lights achieved performance only comparable to that of standard halogen lights. High power LEDs have since made it possible to merge the two key technical developments in dental curing lights, allowing LED-based systems to achieve a 50% reduction in cure time. LED-based systems are now comparable in this regard to high intensity halogen or plasma arc curing lights.
3. Mills RW, Jandt KD, Ashworth SH. Dental composite depth of cure with halogen and blue light emitting diode technology. Brit Dent J, 1999,186(8):388-391.
9
61649_Text
9/19/03
1:24 PM
Page 10
Technical Design A single high-intensity LED generates light in the Elipar™ FreeLight 2 LED curing light. In contrast to conventional LEDs, a high-intensity LED uses a substantially larger semiconductor crystal, which increases both the illuminated area and light intensity, enabling a 50% reduction in cure time. Presented below are the technical requirements ensuring that the full performance of the Elipar FreeLight 2 LED curing light is maintained with a high-intensity LED. Dissipation of heat generated by the LEDs during operation is crucial for durability of LED-based systems. With an array of several standard LEDs, heat build-up is distributed to many individual components. If a single high-intensity LED is used instead of an array of standard LEDs, this characteristic must be addressed, as heat development occurs mainly in the single LED. With the Elipar FreeLight 2 LED curing light, heat is dissipated by a heat sink of highly thermally conductive aluminum integrated in the housing. The high conductivity of this material ensures that a low LED temperature is maintained, during continuous operation of several minutes, protecting LED longevity. When the unit is turned off, heat temporarily stored in the heat sink is dissipated to the environment by interaction with the aluminium composite housing. This design dispenses with the need for fans or other means of air cooling the device. This kind of heat management is possible only with the moderate amount of heat produced by the LED, which represents less than 5% of the amount produced by a halogen lamp. Nevertheless, heating and effective heat dissipation are crucial for the performance of a light polymerization unit based on high-intensity LED. An efficient optical arrangement is required for delivery of the high light intensity necessary for light-induced polymerization. To do this, a conical reflector at the base of the light guide is used to ensure maximum light flux. This reflector consists of a metal-free interference reflecting foil with unique optical qualities, enabling optimum coupling of light generated by the LED into the light guide.
10
61649_Text
9/19/03
1:24 PM
Page 11
Indications The Elipar™ FreeLight 2 LED curing light is a universal light polymerization device for composites, compomers, adhesives and light-cured glass ionomer materials. Effective curing of these materials by the Elipar FreeLight 2 LED curing light requires that they contain camphorquinone as a photoinitiator. Dental materials using alternative photoinitiators with absorption spectra outside the range of 430-480 nm are not compatible. Table 4 shows a list of materials that have photoinitiators compatible with the Elipar FreeLight 2 LED curing light. For each listed compatible products, the cure time indicated by the manufacturer should be reduced by 50%. Table 4. Compatibility of common dental materials with the Elipar FreeLight 2 LED Curing Light Product Restorative Composites
Compatible
Admira® Charisma® Clearfil™ AP-X Compoglass® F Definite® Dyract™ AP EsthetX™ F2000 Compomer Restorative Filtek™ A110 Anterior Restorative Filtek™ Flow Flowable Restorative Filtek™ P60 Posterior Restorative Filtek™ Supreme Universal Restorative Filtek™ Z250 Universal Restorative Heliomolar® Herculite® XRV™ Point 4™ Prodigy™ Solitaire® II SureFil™ Tetric® Bleach Tetric® Ceram Tetric® Flow TPH® Spectrum® Z100™ Restorative
x x x x x x x x x x x x x x
Glass Ionomers
Fuji II™ LC Photac™ Fil Quick Vitremer™ Glass Ionomer
x x x
Cements
RelyX™ ARC Adhesive Resin Cement RelyX™ Unicem Self-Adhesive Resin Cement RelyX™ Veneer Cement Variolink® II
x x x x
Liners
Vitrebond™
x
Sealants
Clinpro™ Sealant
x
Adhesive Systems Adper™ Prompt™ Self-Etch Adhesive Adper™ Scotchbond™ Multi-Purpose Dental Adhesive Adper™ Single Bond Dental Adhesive Excite® OptiBond Solo™ Plus Prime & Bond® NT™ Syntac® Classic
Not Compatible
x x x x x
x x x x x
x x x x x x x
11
61649_Text
9/19/03
1:24 PM
Page 12
Technical Properties The Elipar™ FreeLight 2 LED curing light is a high intensity light instrument designed for composite curing. Though halogen lamps are the standard in the field of light polymerization, the following studies demonstrate that the Elipar FreeLight 2 LED curing light offers polymerization quality equivalent to that achieved by conventional halogen lights, but achieves this goal in half the exposure time. The properties of different restoratives evaluated included the following items: • Mechanical properties of light-cured materials prepared using the Elipar FreeLight 2 LED curing light or Elipar™ TriLight curing light. • The development of temperature during use of the Elipar FreeLight 2 LED curing light and halogen lamps. • A comparison of the depth of polymerization achieved with Elipar™ FreeLight curing light, Elipar FreeLight 2 LED curing light or halogen lamps. • The emission spectra of the Elipar FreeLight curing light, Elipar FreeLight 2 LED curing light and halogen lamps and their respective compatibility with camphorquinone.
Internal Measurements Mechanical Properties of Light-cured Materials Prepared Using the Elipar FreeLight 2 LED Curing Light or Elipar TriLight Curing Light. The measurements were made in the clinical research laboratory of 3M ESPE, according to ISO 4049 (resin-based filling materials). All tests were carried out with the Elipar TriLight curing light according to the manufacturers’ instructions and compared to the Elipar FreeLight 2 LED curing light with a 50% reduction in the manufacturers’ curing time. Table 5 summarizes the flexural strengths, e-modulus, and the depths of polymerization of the tested materials as measured for the Elipar FreeLight 2 LED curing light and Elipar TriLight curing light, respectively. The information in this table constitute representative results derived from a larger data set generated to test and verify the efficacy of the Elipar FreeLight 2 LED curing light. Table 5. Mechanical Properties of Clearfil™ APX, Pertac™ II, Prodigy™ and Spectrum® TPH®
Clearfil AP-X
Pertac II
Prodigy
Spectrum TPH
Flexural strength [MPa]
FreeLight 2 TriLight
162 163
107 106
127 124
124 131
e-modulus [MPa]
FreeLight 2 TriLight
16747 16447
7850 7460
8552 7279
9002 9300
Depth of polymerization [mm]
FreeLight 2 TriLight
1.9 2.1
1.7 2.1
2.2 2.4
2.3 1.9
Clearfil APX, Pertac II, Prodigy, and Spectrum TPH were evaluated according to ISO 4049.
12
9/19/03
1:24 PM
Page 13
The Development of Temperature During Use of the Elipar™ FreeLight, Elipar™ FreeLight 2 LED Curing Lights and a Halogen Lamp. Data on polymerization-related temperature development within restorative composites is of practical interest, though experimental design and data interpretation are demanding. In principle, two different “heat sources” may contribute to a rise in temperature of composite restorations: • Irradiated light of the polymerization lamp (dTrad) • Heat generated by the polymerization reaction (dTpoly). The peak temperature development of in-vitro samples cured with various lights is shown in Figure 2 (Clinical Research Lab, 3M ESPE). The peak temperature rise of samples cured with the Elipar FreeLight 2 LED curing light is statistically lower than samples cured with the high intensity light (Optilux™ 501). Figure 2. Peak temperature development comparisons of Elipar FreeLight, Elipar FreeLight 2 LED curing light and Optilux 501 during light polymerization
Elipar FreeLight 12
Optilux
Elipar FreeLight 2
11.1
10
9.4
8.9 7.9
8 Temp, °C
61649_Text
7.9 6.6
6
5.8
5.7 4.7
4 2 0 Tetric Ceram
Filtek Z250
Spectrum TPH
13
61649_Text
9/19/03
1:24 PM
Page 14
A Comparison of the Depth of Polymerization Achieved with Elipar™ FreeLight, Elipar™ FreeLight 2 LED Curing Light and a Halogen Lamp. 3M ESPE R&D
The following standardized procedure describes the protocol to establish the depth of cure (ISO 4049). A composite is packed into a metal cylinder. The top surface is exposed to a visible light source for the recommended length of time. After exposure, the composite is removed from the mold and uncured material is scraped away using a plastic instrument. The value recorded is half the height of the cylinder of cured material after it is scraped back. Figure 3 shows the cure depth of 3M ESPE Filtek™ Supreme, EsthetX™, and Point 4™ restoratives polymerized according to manufacturers’ recommendations with the Elipar FreeLight curing light. Also shown are the cure depths at a 50% reduction in the recommended cure times with the Elipar FreeLight 2 LED curing light, the L.E. Demetron I curing light and Kerr’s Optilux™ 501 operated in “Boost” mode and using the turbo and light guide. With all three composites, the Elipar FreeLight 2 LED curing light achieved equivalent depths of cure compared to the results of the Optilux 501 with the same cure time. Figure 3. Depth of Cure of Filtek Supreme universal restorative, EsthetX and Point 4 restoratives.
Elipar FreeLight
Optilux 501
Elipar FreeLight 2
LEDemetron
4
mm
3
2
1
0 Filtek Supreme
14
Point 4
EsthetX
CX 61649_Text 9/24/03 5:30 PM Page 15
The Emission Spectra of the Elipar™ FreeLight, Elipar™ FreeLight 2 LED Curing Light and Optilux™ 501 and Their Respective Compatibility with Camphorquinone. (3M ESPE R&D)
Information about the spectral composition of the emitted light from a polymerization lamp can advance understanding about the improved efficiency of the LED technology. Absorption curves are commonly used for the characterization of photoinitiators and the overlap between them and light source emission spectra predict reaction efficiencies. The absorption spectrum of camphorquinone is shown in Figure 4. As indicated by the spectrum, camphorquinone has the capacity to absorb light ranging from 380 to 500 nanometers. Since camphorquinone in the presence of amine-based coinitiators can start polymerization, the camphorquinone absorption curve constitutes the total range of light that can initiate a polymerization reaction. For example, light in the range 380-430 nm could be absorbed by camphorquinone but the probability is lower than wavelengths at its absorption maximum of 465 nm. Light of 465 nm wavelength is much more likely to start a photopolymerization reaction and therefore is more efficient than light of other wavelengths. As shown in Figure 4, the emission spectrum of the Elipar FreeLight curing light, the Elipar FreeLight 2 LED curing light, and the absorption spectrum of camphorquinone are very similar. Both the Elipar FreeLight and Elipar FreeLight 2 LED curing lights exhibit nearly identical efficiencies of light polymerization of composites while the latter offers a higher total light intensity (equivalent to the area under the emission curve). Figure 4. Absorption spectrum of camphorquinone and emission spectra of the Elipar FreeLight Curing Light, the Elipar FreeLight 2 LED Curing Light, the Elipar FreeLight, and the Optilux 501 Curing Light.
40 35
Elipar™ FreeLight 2 1007 mW/cm2
30
Elipar™ FreeLight 410 mW/cm2
mW / (cm2nm)
Optilux 501
25
Optilux 501 was used in boost mode with turbo tip.
20
Camphorquinone absorption
15 10 5 0 380
400
420
440
460
480
500
520
540
nm
Source: 3M ESPE laboratory test data
15
61649_Text
9/19/03
1:24 PM
Page 16
Technique Guide USAGE TIPS Elipar™ FreeLight 2 LED Curing Light Removing the Battery Cap: • Rotate the cap at the bottom of the handpiece counter-clockwise until it stops, and then remove the cap. 1
Inserting the Battery: • Insert the rechargeable battery in a fluent motion as directed by the arrow until you hear or feel the battery SNAP into place. • Replace the cap and rotate clockwise until it locks into place. • Malfunction of the light will result if the battery has not been seated fully and secured into the handpiece. • In the event of malfunction, remove the battery from the handpiece as instructed below.
2
Removing the Battery: • Push a small spatula or similar aid between the cylinders of the battery until the snap-lock releases the battery. 3
• Remove the battery as illustrated in figure 4. Reinsert the battery or insert a new battery and replace the cap as described and illustrated in figure 2 above. 4
Charging Steps: • Place the charger base on a level surface. Do not obstruct the vent slots on the bottom of the unit. • Plug in the charger base. The green LED on the left side of the device should illuminate indicating the unit is ready for operation. • Prior to the first use, place the handpiece in the charger base to charge the new battery. • The yellow LED on the left side of the charger base will illuminate after approximately 2 seconds. The battery is charged once the yellow LED turns off. • Note: it will take 3 TO 4 charging cycles (completely discharged and recharged) before the battery reaches maximum charging capacity.
16
5
6
61649_Text
9/19/03
1:24 PM
Page 17
Cleaning/Disinfecting the Charger Base and Handpiece: • Wipe handpiece and charger base for disinfection. Do not spray. Disinfecting agents must not enter openings on unit. • Apply disinfecting agent with a soft cloth and allow disinfectant to remain on surface for the amount of time recommended by the manufacturer. Follow precautions for use. • Perform a final wipe with a clean cloth to remove any residual deposits of the disinfectant solution. • Wet charge contacts will shut down the charging process and will be signaled by ongoing beeps and a flashing yellow light on the charging base. If this occurs, simply remove handpiece from charging base and thoroughly dry contacts on charging base and handpiece as described above. • Do not use solvents or abrasive cleaning agents as these may damage plastic parts. Cleaning/Sterilizing the Light Guide: • Cured composite on the tip of the light guide should be removed with alcohol. A plastic spatula may help in removing the material. Do not use any sharp or pointed instruments. • The light guide can be steam autoclaved. Do not sterilize with dry heat or chemicals. • Water spots should be wiped off both ends of the light guide before and after steam sterilization. 3M ESPE Customer Hotline 1-800-634-2249 Please refer to Instructions for Use for more detailed information as well as precautionary and warranty information.
7
8
9
70-2009-3593-3 © 2003 3M
17
61649_Text
9/19/03
1:24 PM
Page 18
Instructions for Use Product Description Elipar™ FreeLight 2, manufactured by 3M ESPE, is a high-performance light unit for intraoral polymerization of dental materials. The unit consists of a charger and a cordless handpiece powered by a rechargeable battery. The unit is designed for use on a table and cannot be wallmounted. The unit uses a high-performance Light Emitting Diode (LED) as the light source. In contrast to halogen light units, the unit emits light mainly in the wavelength range of 430 to 480 nm, e.g. the relevant range for camphorquinone-containing products. The optimal match of the wavelength range to the intended purpose ensures that the polymerization performance is similar to that of halogen light-emitting units, albeit at lower light intensity. The polymerization performance of this light unit is so high, that the exposure times can be reduced by 50%, compared to a conventional halogen light unit. Exposure time options: 5, 10, 15, or 20 seconds. The charger is equipped with an integral light intensity testing area. The device is shipped with a turbo light guide with an 8 mm diameter light exit. It is not permissible to use the light guides of other units. The “maxi fiber rod” with a diameter of 13 mm for larger areas (e.g. for fissure sealing), and the “proxi fiber rod” with a point-shaped light exit (e.g. for use in interproximal areas), are available as accessories. Both the maxi fiber rod and the proxi fiber rod may only be used for the mentioned purposes and not for the polymerization of usual fillings, as otherwise complete polymerization can not be guaranteed. The handpiece is equipped with a “power-down” function to minimize the unit’s energy consumption. The handpiece switches to “power-down” mode once it is placed in the charger or if left unused for approximately 10 minutes outside the charger. In stand-by mode, the charger consumes maximally 0.75 W. Starting in 2003, this value will be recommended for the stand-by mode by the EU according to the “Code of Conduct” on efficiency of external power supplies.
Fields of Application Polymerization of light-curing dental materials with photoinitiator for the wavelength range 430480 nm. Though the majority of light-curing dental materials are responsive in this range of wavelengths, you may wish to contact the manufacturer of the material in question to confirm the wavelength range.
18
61649_Text
9/19/03
1:24 PM
Page 19
Installation of the Unit Factory Settings The factory settings of the unit are 20 seconds operation time.
Initial Steps Charging 1. Please ensure first that the voltage stated on the rating plate corresponds to the existing main supply voltage. The rating plate is attached to the bottom of the unit. 2. Place the charger on a level surface. – To protect the device from over-heating, do not obstruct the vent slots on the bottom of the unit. 3. Plug in the charger base. 4. Connect the power cable of the charger to the power supply of the Charger. – The green LED on the left side of the device is illuminated. This shows that the unit is ready for operation; please refer to the section, “LED display of the charger.”
Light Guide/Handpiece Never insert the handpiece in the charger unless the battery is inserted in the handpiece first! • Steam Autoclave the light guide prior to first use. • Then insert the light guide in the handpiece until it snaps into place. • Place the enclosed glare shield on the light guide.
Inserting the Battery • Rotate the lid at the lower end of the handpiece counterclockwise until it hits the stop, and then remove the lid. • To avoid malfunction, make sure the battery is properly inserted. Lay the handpiece upside down and insert the rechargeable battery in a fluent motion as directed by the arrow until you hear the battery snap into place. • Replace the lid and rotate clockwise until it locks into place. • In the event of malfunction, remove the rechargeable battery from the device and re-insert as described above.
19
61649_Text
9/19/03
1:24 PM
Page 20
Battery Charging • Prior to the first use, place the handpiece in the charger to fully load the new rechargeable battery. – The yellow LED of the charger illuminates after approximately 2 seconds; please see also section, “LED Display of the Charger.” The battery is fully charged once the yellow LED is turned off. – Note: Several cycles of charging and discharging may be necessary before the optimum cure time per charge is obtained. LED Display of the Charger
Green LED
Yellow LED
Acoustical signal
Handpiece inserted in charger?
On
Off
–
No
Charger is ready for operation
On
Off
–
Yes
Charging has been completed
On
On
–
Yes
Rechargeable battery is being charged
On
Flashing
–
Yes is defective
Rechargeable battery
On
Flashing
Ongoing Beeps
Yes are wet
Charging contacts
Indicates
Table Holder for the Handpiece While performing a procedure, the handpiece can be placed in a table holder.
Operation Selection of Exposure Time Exposure times of 5, 10, 15, and 20 seconds are available. • For the compatible product at hand, use the exposure time as stated in the product’s Instructions for Use and reduce to half. • Select the exposure time by pressing the “sec” button. – The selected exposure time is indicated by the 4 green LEDs. 20