Aesculap
Compressed-air hoses Instructions for Use V4.0
Instructions for Use
234 Pages
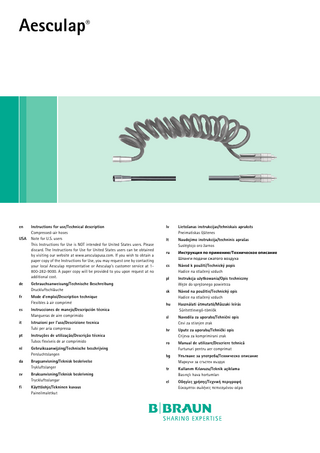
Preview
Page 1
Aesculap®
Aesculap Power Systems
en USA
Instructions for use/Technical description Compressed-air hoses Note for U.S. users This Instructions for Use is NOT intended for United States users. Please discard. The Instructions for Use for United States users can be obtained by visiting our website at www.aesculapusa.com. If you wish to obtain a paper copy of the Instructions for Use, you may request one by contacting your local Aesculap representative or Aesculap's customer service at 1800-282-9000. A paper copy will be provided to you upon request at no additional cost.
lv
Lietošanas instrukcijas/tehniskais apraksts Pneimatiskas šļūtenes
lt
Naudojimo instrukcija/techninis aprašas Suslėgtojo oro žarnos
ru
Инструкция по примению/Техническое описание Шланги подачи сжатого воздуха
cs
Návod k použití/Technický popis Hadice na stlačený vzduch
pl
de
Gebrauchsanweisung/Technische Beschreibung Druckluftschläuche
Instrukcja użytkowania/Opis techniczny Węże do sprężonego powietrza
sk
fr
Mode d’emploi/Description technique Flexibles à air comprimé
Návod na použitie/Technický opis Hadice na stlačený vzduch
hu
es
Instrucciones de manejo/Descripción técnica Mangueras de aire comprimido
Használati útmutató/Műszaki leírás Sűrítettlevegő-tömlők
sl
it
Istruzioni per l’uso/Descrizione tecnica Tubi per aria compressa
Navodila za uporabo/Tehnični opis Cevi za stisnjen zrak
hr
pt
Instruções de utilização/Descrição técnica Tubos flexíveis de ar comprimido
Upute za uporabu/Tehnički opis Crijeva za komprimirani zrak
ro
nl
Gebruiksaanwijzing/Technische beschrijving Persluchtslangen
Manual de utilizare/Descriere tehnică Furtunuri pentru aer comprimat
bg
da
Brugsanvisning/Teknisk beskrivelse Trykluftslanger
Упътване за употреба/Техническо описание Маркучи за сгъстен въздух
tr
sv
Bruksanvisning/Teknisk beskrivning Tryckluftsslangar
Kullanım Kılavuzu/Teknik açiklama Basınçlı hava hortumları
el
fi
Käyttöohje/Tekninen kuvaus Paineilmaletkut
Οδηγίες χρήσης/Τεχνική περιγραφή Εύκαμπτοι σωλήνες πεπιεσμένου αέρα
GA460R 3 m GA430 COMFORT PNEUMATIC DRILL
GA194R 3 m GA195R 5 m SYSTEM AESCULAP-DRÄGER
GA464R 3 m GA466R 5 m
GA461R 3 m GA437 COMFORT PNEUMATIC DRILL GA099 GA463R 3 m GA465R 5 m
GA087R 5 m DIN
FK898R KAIRISON
SYNTHES GA206R
RT040R UNITRAC-PNEUMATIC RETRACTION ARM
SCHRADER GA468R 5 m
SYSTEM SCHRADER/ SYNTHES
en
Aesculap® Compressed-air hoses Legend
Contents
1
1. 1.1 1.2 2. 2.1 2.1.1 2.2 2.2.1 2.2.2 2.2.3 2.3 2.3.1 2.3.2 2.4 2.4.1 2.5 2.5.1 2.5.2 2.6 2.7 2.8 3. 3.1 3.2 3.3 3.4 3.5 3.6 3.7 3.7.1
2
Foldout page 1: Possible combinations of motor, compressed-air supply and hose variants for macro motors Foldout page 2: Possible combinations of motor, compressed-air supply and hose variants for microLAN-/miniLAN-/HiLAN motors
Symbols on product and packages Caution Observe important safety information such as warnings and precautions in the instructions for use.
YYYY-MM
Maintenance indicator Date of the next recommended servicing (year-month) by the international B. Braun/Aesculap agency, see Technical service Two-dimensional machine readable code The code contains a unique serial number that can be used for electronically tracking individual instruments. The serial number is based on the worldwide sGTIN (GS1) standard. Manufacturer
Date of manufacture
Non-sterile medical device
Manufacturer batch ID Manufacturer’s serial number Manufacturer's order number Temperature limits during transport and storage
Air humidity limits during transport and storage
Atmospheric pressure limits during transport and storage According to US federal law, this product may only be sold by a physician or on the orders of a physician CE mark according to Regulation (EU) 2017/745
Medical device
2
About this document... Scope... Safety messages... Clinical use... Product description... Operating principle... Areas of use and limitations of use... Intended use... Indications... Contraindications... Safety information... Clinical user... Sterility... Preparation... Compressed-air supply... System set-up... Connecting the accessories... Connecting the compressed-air supply... Functional test... Application... Troubleshooting... Validated reprocessing procedure... General safety instructions... General information... Reusable products... Preparations at the place of use... Dismantling prior to carrying out the reprocessing procedure Preparing for cleaning... Cleaning/Disinfection... Product-specific safety information on the reprocessing method... 3.7.2 Validated cleaning and disinfection procedure... 3.8 Manual cleaning/disinfection... 3.8.1 Manual cleaning and wipe disinfecting... 3.9 Mechanical cleaning/disinfection... 3.9.1 Mechanical alkaline cleaning and thermal disinfecting... 3.10 Inspection... 3.10.1 Visual inspection... 3.10.2 Functional test... 3.11 Packaging... 3.12 Steam sterilization... 3.13 Storage... 3.13.1 Ambient conditions... 4. Maintenance and service... 4.1 Maintenance... 4.2 Technical service... 4.3 Accessories / spare parts... 5. Disposal...
3 3 3 3 3 3 3 3 3 3 3 3 3 4 4 4 4 4 5 5 5 6 6 6 6 6 6 6 7 7 7 8 8 9 9 10 10 10 10 10 10 10 11 11 11 11 11
en 6. 6.1 6.2
Technical data... 11 Classification acc. to Regulation (EU) 2017/745... 11 Performance data, information about standards... 11
1.
About this document
Note General risk factors associated with surgical procedures are not described in these instructions for use.
1.1
Scope
These instructions for use apply for compressed-air hoses. ► For article-specific instructions for use as well as information on material compatibility see B. Braun eIFU at eifu.bbraun.com
1.2
Safety messages
Safety messages make clear the dangers to patient, user and/or product that could arise during the use of the product. Safety messages are labeled as follows: DANGER Indicates a possible threat of danger. If not avoided, death or serious injury may result. WARNING Indicates a possible threat of danger. If not avoided, minor or moderate injury may result. CAUTION Indicates a possible threat of material damage. If not avoided, the product may be damaged.
2.
Clinical use
2.1
Product description
2.1.1 Operating principle The compressed-air hoses convey compressed air from the compressed-air source to the pneumatic motor. The compressed-air hoses have an instant-cutout coupling. This coupling prevents the escape of compressed air when the pneumatic motor is detached from the hose. Compressed-air hoses with exit air recycling Some hoses are equipped with an exit air recycling conduit. In these hoses, the supply hose is embedded in an additional exit air hose, which takes the exit air away from the operating field. The are two exit air recycling systems: ■ Aesculap-Dräger system for complete exit air recycling: The exit air is channeled back from the O.R. into the central gas supply system. In this way, air turbulences and adverse effects on the climate and hygiene in the O.R. are avoided. ■ Shrader coupling and others, no complete air recycling: The exit air escapes within the O.R. through an open hose end or a diffuser.
Coil-shaped compressed-air hose Compressed-air hose GA460R is coiled into a helix shape. to save space when the hose is put down on the instruments table. This also reduces the risk of contamination in the sterile area, as the compressed-air hose does not "sag".
2.2
Areas of use and limitations of use
2.2.1 Intended use Compressed-air hoses are used for connecting pneumatic driven devices to a central gas supply system or to compressed air cylinders. They are suitable for use with compressed air or nitrogen. 2.2.2 Indications Note The manufacturer is not responsible for any use of the product against the specified indications and/or the described applications. The different compressed-air hoses are used in the following applications: ■ GA460R, GA461R, GA463R-GA466R and GA468R for motors, foot control and pneumatic driven devices ■ GA505R-GA507R, GA513R and GA523R for microLAN-/miniLAN/HiLAN motors ■ GA087, GA194R and GA195R as extension hoses ■ GA099 and GA206R to connect motors, motor hoses, Unitrac, Kairison with compressed air hoses. 2.2.3 Contraindications No known contraindications.
2.3
Safety information
2.3.1
Clinical user
General safety information To prevent damage caused by improper setup or operation, and to not compromise the manufacturer warranty and liability: ► Use the product only according to these instructions for use. ► Follow the safety and maintenance instructions. ► Ensure that the product and its accessories are operated and used only by persons with the requisite training, knowledge and experience. ► Store any new or unused products in a dry, clean, and safe place. ► Prior to use, check that the product is in good working order. ► Keep the instructions for use accessible for the user. Note The user is obligated to report all severe events in connection with the product to the manufacturer and the responsible authorities of the state in which the user is located. Notes on surgical procedures It is the user's responsibility to ensure that the surgical procedure is performed correctly. Appropriate clinical training as well as a theoretical and practical proficiency of all the required operating techniques, including the use of this product, are prerequisites for the successful use of this product. The user is required to obtain information from the manufacturer if there is an unclear preoperative situation regarding the use of the product. 2.3.2 Sterility The product is delivered in an unsterile condition. ► Clean the new product after removing its transport packaging and prior to its initial sterilization.
3
en 2.4
Preparation
Non-compliance with these rules will result in complete exclusion of liability on the part of Aesculap. ► When setting up and operating the product, adhere to: – national regulations for installation and operation, – national legal regulations pertaining to compressed-air supply, – national regulations on fire and explosion protection. 2.4.1
Compressed-air supply
Operation with compressed-gas cylinders according to DIN EN ISO 11117 The following conditions must be met: ■ Compressed air or nitrogen is used ■ An adequate stock of full gas cylinders is in place ■ Cylinder pressure reduced to operating pressure of 6 bar to 10 bar through a pressure reducer (e.g., GA099) ► Operating pressure must be read from the scale on the device and set with the T-screw.
DANGER Danger of fire and explosion when operating devices that run on oxygen! ► Only use compressed air or nitrogen to power pneumatic motors. DANGER Operating pressures in excess of 10 bar will damage the motor system! ► Set an operating pressure of between 6 bar and 10 bar. DANGER Damage to persons and/or property due to the placing of the hose! The user may injure the patient with an unintentional movement due to shock. ► Do not damage the pneumatic hose. ► Ensure annual repair. Operation with central gas supply according to DIN EN ISO 5359 The gas supply must provide clean, dry air and must be set as follows: Nominal operating pressure
6 bar
Maximum allowable operating pressure
10 bar
Maximum allowable backup pressure in exit air conduit while motor is operating (with exit air recycling)
0.5 bar to 0.7 bar
Minimum gas-supply delivery
300 l/min
When operating the motor with compressed gas cylinders, the exhaust air is not removed from the operative field, but instead emerges from the end of the hose, away from the operative site.
2.5
System set-up
CAUTION Lack of performance of the pneumatic motor/bursting of damaged compressed-air hoses! ► Lay compressed-air hoses only through unobstructed areas. ► Do not squeeze or block open hose ends or diffusers. ► Do not coil up compressed-air hoses to tightly (minimum coil diameter 20 cm). ► Do not kink, squeeze or clamp compressed-air hoses. ► Verify that the compressed-air hoses are not damaged (e.g. by scalpels) or loaded with sharp objects (e.g. cloth clips). 2.5.1 Connecting the accessories Combinations of accessories that are not mentioned in the present instructions for use may only be employed if they are specifically intended for the respective application, and if they do not compromise the performance and safety characteristics of the products. ► Please address your B. Braun/Aesculap partner or Aesculap Technical Service with any inquiries in this respect; for a contact address, see Technical service. 2.5.2 Connecting the compressed-air supply ► Make certain that the requirements concerning the central gas supply or the compressed-gas cylinder are fulfilled, see Compressed-air supply. ► Keep to the possible combinations of motor, compressed-air supply and hose variants (see foldout pages) and choose the appropriate combination. Long hoses may cause a backup of exhaust air and thus a loss of performance of the pneumatic motor. ► Keep hose lines as short as possible. ► Use a compatible extension hose if necessary.
4
en Connecting pneumatic motors with foot control Pneumatic motors without hand-operated control must only be connected using the associated GA521 foot control with the compressed-air supply. Connect the pneumatic motor and the foot control according their respective instructions for use: ► Make certain the slide for selecting the sense of rotation on the pneumatic motor is in ”0” position. ► To connect the pneumatic motor to the foot control: – Pull back the sleeve on the compressed-air hose and connect the compressed-air hose with its immediate-cutoff coupling to the pneumatic motor. – Insert the connector of the compressed-air hose into the foot control. ► To connect the foot control to the compressed-air supply: – Pull back the sleeve on the compressed-air hose and connect the compressed-air hose with its immediate-cutoff coupling to the foot control. – Insert the connector of the compressed-air hose into the compressed-air supply. Connecting pneumatic motors with hand-operated control Pneumatic motors with hand-operated control are connected directly to the compressed-air supply via a compressed-air hose. Connect the pneumatic motor according to its instructions for use: ► Make certain the slide for selecting the sense of rotation on the pneumatic motor is in ”0” position. ► Pull back the sleeve on the compressed-air hose and connect the compressed-air hose with its immediate-cutoff coupling to the pneumatic motor. ► Insert the connector of the compressed-air hose into the compressedair supply.
2.6
2.8
Troubleshooting
Malfunction Detection
Cause
Remedy
Motor is not running
No compressed air
Fill or change cylinder
Insufficient power
Leaky hose
Gas cylinder empty Pressure Gauge set to "0" No compressed air at the wall outlet
Open valve
Hoses are not correctly connected
Fully connect the hose connector
Pressure at the compressed-air supply set too low
Compressedair supply pressure too low
Set higher pressure
Hose is too long Hoses excessively kinked or crushed
High air resis- Use shorter hoses tance in the Do not kink or hose squeeze hoses
Exit air does not flow freely
Unblock the exit air channel
Pneumatic motor runs jerkily
Pneumatic motor faulty
Have product repaired by the manufacturer
Hose squeezed, torn or deformed
Hose damaged
Have product repaired by the manufacturer
Hose coupling deformed
Hose coupling defective
Have product repaired by the manufacturer
Functional test
► Verify that all compressed-air hoses are coupled correctly and do not
leak, see Inspection.
2.7
Application
WARNING Risk of injury and/or malfunction! ► Prior to each use, inspect the product for loose, bent, broken, cracked, worn, or fractured components. ► Always carry out a function test prior to each use of the product.
5
en 3.
Validated reprocessing procedure
3.1
General safety instructions
Note Adhere to national statutory regulations, national and international standards and directives, and local, clinical hygiene instructions for sterile processing. Note For patients with Creutzfeldt-Jakob disease (CJD), suspected CJD or possible variants of CJD, observe the relevant national regulations concerning the reprocessing of products. Note Mechanical reprocessing should be favored over manual cleaning as it gives better and more reliable results. Note Successful processing of this medical device can only be ensured if the processing method is first validated. The operator/sterile processing technician is responsible for this. Note If there is no final sterilization, then a virucidal disinfectant must be used. Note For up-to-date information about reprocessing and material compatibility, see B. Braun eIFU at eifu.bbraun.com The validated steam sterilization procedure was carried out in the Aesculap sterile container system.
3.2
General information
Dried or affixed surgical residues can make cleaning more difficult or ineffective and lead to corrosion. Therefore the time interval between application and processing should not exceed 6 h; also, neither fixating precleaning temperatures >45 °C nor fixating disinfecting agents (active ingredient: aldehydes/alcohols) should be used. Excessive measures of neutralizing agents or basic cleaners may result in a chemical attack and/or to fading and the laser marking becoming unreadable visually or by machine for stainless steel. Residues containing chlorine or chlorides e.g. in surgical residues, medicines, saline solutions and in the service water used for cleaning, disinfection and sterilization will cause corrosion damage (pitting, stress corrosion) and result in the destruction of stainless steel products. These must be removed by rinsing thoroughly with demineralized water and then drying. Additional drying, if necessary.
6
Only process chemicals that have been tested and approved (e.g. VAH or FDA approval or CE mark) and which are compatible with the product’s materials according to the chemical manufacturers’ recommendations may be used for processing the product. All the chemical manufacturer's application specifications must be strictly observed. Failure to do so can result in the following problems: ■ Optical changes of materials, e.g. fading or discoloration of titanium or aluminum. For aluminum, the application/process solution only needs to be of pH >8 to cause visible surface changes. ■ Material damage such as corrosion, cracks, fracturing, premature aging or swelling. ► Do not use metal cleaning brushes or other abrasives that would damage the product surfaces and could cause corrosion. ► Further detailed advice on hygienically safe and material-/value-preserving reprocessing can be found at www.a-k-i.org, link to "AKIBrochures", "Red brochure".
3.3
Reusable products
Influences of the reprocessing which lead to damage to the product are not known. A careful visual and functional inspection before the next use is the best opportunity to recognize a product that is no longer functional, see Inspection.
3.4
Preparations at the place of use
► Remove any visible surgical residues to the extent possible with a
damp, lint-free cloth. ► Transport the dry product in a sealed waste container for cleaning and
disinfection within 6 hours.
3.5
Dismantling prior to carrying out the reprocessing procedure
► Separate the compressed-air hose from the pneumatic motor and from
the foot control, if applicable.
3.6
Preparing for cleaning
► Prior to first mechanical cleaning/disinfection process: Assemble
ECCOS holder GB673R in a suitable tray (e.g. JF214R). ► Carry out non-fixating/NaCl-free pre-cleaning immediately after use.
en 3.7
Cleaning/Disinfection
3.7.1
Product-specific safety information on the reprocessing method Damage to, or destruction of the product caused by mechanical cleaning/disinfection! ► Only clean and disinfect compressed-air hose GA087 and pressure regulator GA099 manually. ► Do not sterilize the compressed-air hose GA087 and pressure regulator GA099 under any circumstances. Damage to or destruction of the product due to inappropriate cleaning/disinfecting agents and/or excessive temperatures! ► Following the manufacturer's instructions, use cleaning and disinfecting agents – that are approved for plastic material and high-grade steel, – that do not attack softeners (e.g., in silicone). ► Dry the product for at least 10 minutes at a maximum of 120 °C. Note The indicated drying temperature is a guide temperature only. It must be checked taking into account the specific conditions (e.g. load) and if applicable adjusted ► Do not clean the compress-air hoses by ultrasonic bath and do not
immerse the product in any fluid. To avoid the risk of corrosion/malfunctioning, allow any fluid that has entered the product to drain out immediately. 3.7.2
Validated cleaning and disinfection procedure
Validated procedure
Specific requirements
Reference
Manual cleaning and wipe disinfection
■ Clean the instrument under running tap water with a suitable cleaning brush
Chapter Manual cleaning/disinfection and subsection:
where necessary for as long as it takes to remove all discernible residues.
■ When cleaning products with movable hinges, ensure that these are in an open position and, if applicable, move the joint while cleaning.
■ Chapter Manual cleaning and wipe disinfecting
■ Drying phase: Use a lint-free cloth or compressed air for medical purposes ■ Ensure that the product is positioned in such a way that water will not enter the product e.g. through coupling interfaces. (Immediately remove any fluid that entered the product inadvertently.) Mechanical alkaline cleaning and thermal disinfection
■ Insert the product in its proper position in the ECCOS holder. – – – – –
GB463R – Compressed-air hose GA460R, GA464R, GA466R GB480R – Compressed-air hose GA468R GB564R – Compressed-air hose GA505R, GA513R, GA523R GB575R – Compressed-air hose GA506R GB576R – Compressed-air hose GA507R
Chapter Mechanical cleaning/disinfection and subsection:
■ Chapter Mechanical alkaline cleaning and thermal disinfecting
■ Place the instrument in a tray that is suitable for cleaning (avoiding rinsing blind spots: Compressed-air extension hose GA194R/GA195R.
■ Connect compressed-air extension hose GA194R/GA195R.
7
en 3.8
Manual cleaning/disinfection
► Prior to manual disinfecting, allow water to drip off for a sufficient
length of time to prevent dilution of the disinfecting solution. ► After manual cleaning/disinfection, check visible surfaces visually for
residues. ► Repeat the cleaning/disinfection process if necessary.
3.8.1
Manual cleaning and wipe disinfecting
Phase
Step
T [°C/°F]
t [min]
Conc. [%]
Water quality
Chemical
I
Cleaning
RT (cold)
-
-
D–W
-
II
Drying
RT
-
-
-
-
III
Wipe disinfection
-
>1
-
-
Meliseptol HBV wipes 50 % Propan-1-ol
IV
Final rinse
RT (cold)
0.5
-
FD-W
-
V
Drying
RT
-
-
-
-
D–W: FD–W: RT:
Drinking water Fully desalinated water (demineralized, low microbiological contamination: drinking water quality at least) Room temperature
Phase I ► Clean the product under running faucet water, using a suitable clean-
ing brush until all visible residues have been removed from the surfaces. ► Mobilize non-rigid components, such as set screws, links, etc. during cleaning. Phase II ► Dry the product in the drying phase with suitable equipment (e.g. cloth,
compressed air), see Validated cleaning and disinfection procedure. Phase III ► Wipe all surfaces of the product with a single-use disinfectant wipe.
Phase IV ► After the specified exposure time (at least 1 min), rinse the disinfected
surfaces under running FD water. ► Drain any remaining water fully.
Phase V ► Dry the product in the drying phase with suitable equipment (e.g. cloth,
compressed air), see Validated cleaning and disinfection procedure.
8
en 3.9
Mechanical cleaning/disinfection
Note The cleaning and disinfection device must be of tested and approved effectiveness (e.g. FDA approval or CE mark according to DIN EN ISO 15883). Note The cleaning and disinfection device used for processing must be serviced and checked at regular intervals. 3.9.1 Mechanical alkaline cleaning and thermal disinfecting Machine type: single-chamber cleaning/disinfection device without ultrasound Phase
Step
T [°C/°F]
t [min]
Water quality
Chemistry/Note
I
Pre-rinse
<25/77
3
D–W
-
II
Cleaning
55/131
10
FD-W
■ Concentrate, alkaline: – pH = 13 – <5 % anionic surfactant
■ 0.5 % working solution – pH ~ 11* III
Intermediate rinse
>10/50
1
FD–W
-
IV
Thermal disinfection
90/194
5
FD-W
-
V
Drying
-
-
-
According to the program for cleaning and disinfection device
DW: Drinking water FD–W: Fully desalinated water (demineralized, low microbiological contamination: drinking water quality at least) *Recommended: BBraun Helimatic Cleaner alkaline
► Check visible surfaces for residues after mechanical cleaning/disinfect-
ing.
9
en 3.10 Inspection
3.11 Packaging
► Allow the product to cool down to room temperature.
► Always follow the instructions for use of the respective packaging and
► Dry the product if it is wet or damp.
storage devices (e.g. instructions TA009721 for Aesculap-ECCOS storage system). ► Insert the product in its proper position in the ECCOS holder, or put it on a tray in such a way that the product is protected against damage. Ensure that any blades and/or sharp edges are protected. ► Package trays appropriately for the sterilization process (e.g. in Aesculap sterile containers). ► Ensure that the packaging will prevent a recontamination of the product.
3.10.1 Visual inspection ► Make certain that all soiling has been removed. In particular, pay
attention to mating surfaces, hinges, shafts, recessed areas, drill grooves and the sides of the teeth on rasps. ► If the product is dirty: repeat the cleaning and disinfection process. ► Check the product for damage, e.g. insulation or corroded, loose, bent, broken, cracked, worn or severely scratched and fractured components. ► Check the product for missing or faded labels. ► Check the products with long, slim shapes (in particular rotating instruments) for deformities. ► Check the product for damage to the spiral element. ► Check the cutting edges for continuity, sharpness, nicks and other damage. ► Check the surfaces for rough spots. ► Check the product for burrs that could damage tissue or surgical gloves. ► Check the product for loose or missing parts. ► Immediately put aside damaged or inoperative products and send them to Aesculap Technical Service, see Technical service. 3.10.2 Functional test ► Each time the pneumatic motor is processed and a function check is
carried out, check for: – Secure seating of push fit nipple and hose coupling – Damage to the hose mantle, e.g. splits or porosity – Air-tightness of the air supply duct: Connect the compressed-air hose to the supply and check air-tightness acoustically. – Air-tightness of the exhaust duct: Connect the pneumatic motor, connect the compressed-air hose to the supply, and check air-tightness acoustically or in a water bath. ► Slightly grease the mobile sleeves on the hose connections with sterilizable maintenance oil that is permeable to vapor before each cleaning and before each sterilization (Aesculap-STERILIT oil spray GB600). ► Prior to an extended period of non-use, always store the compressedair hose cleaned and dried according to the instructions. ► Check that the product functions correctly. ► Check that all moving parts are working property (e.g. hinges, locks/latches, sliding parts etc.). ► Check the product for any atypical running noise, overheating or excessive vibration. ► Check for compatibility with associated products. ► Immediately put aside inoperative products and send them to Aesculap Technical Service, see Technical service.
10
3.12 Steam sterilization Note The product can be sterilized either in disassembled or in assembled condition. Note The product may only be sterilized in disassembled condition. ► Check to ensure that the sterilizing agent will come into contact with
all external and internal surfaces (e.g., by opening any valves and faucets). ► Validated sterilization process – Disassemble the product – Steam sterilization using fractional vacuum process – Steam sterilizer according to DIN EN 285 and validated according to DIN EN ISO 17665 – Sterilization using fractionated vacuum process at 134 °C/holding time 5 min ► If several devices are sterilized at the same time in the same steam sterilizer: ensure that the maximum permitted load according to the manufacturers’ specifications is not exceeded.
3.13 Storage ► Store sterile products in germ-proof packaging, protected from dust, in
a dry, dark, temperature-controlled area. 3.13.1 Ambient conditions The following environmental conditions apply to the transport and storage of the product: Temperature
-10 °C to 50 °C
Relative humidity
10 % to 90 %
Atmospheric pressure
500 hPa to 1 060 hPa
en 4.
Maintenance and service
5.
4.1
Maintenance
WARNING Risk of infection due to contaminated products! ► Adhere to national regulations when disposing of or recycling the product, its components and its packaging.
To ensure reliable operation, the product must be maintained in accordance with the maintenance label, or at least once a year. The service instructions can be requested from Aesculap Technical Service. For services to that end, please contact your national B. Braun/Aesculap agency, see Technical service.
4.2
Technical service
DANGER Danger to life of patients and users if the product malfunctions and/or protective measures fail or are not used! ► Do not perform any servicing or maintenance work under any circumstances while the product is being used on a patient. CAUTION Modifications carried out on medical technical equipment may result in loss of guarantee/warranty rights and forfeiture of applicable licenses. ► Do not modify the product. ► For service and repairs, please contact your national B. Braun/Aesculap agency. Service addresses Aesculap Technischer Service Am Aesculap-Platz 78532 Tuttlingen / Germany Phone: +49 7461 95-1601 Fax: +49 7461 16-2887 E-Mail: [email protected] Other service addresses can be obtained from the address indicated above.
4.3
Disposal
WARNING Risk of injury due to sharp-edged and/or pointed products! ► When disposing of or recycling the product, ensure that the packaging prevents injury by the product. Note The user institution is obliged to reprocess the product before its disposal, see Validated reprocessing procedure. ► Detailed information concerning the disposal of the product is avail-
able through your national B. Braun/Aesculap agency, see Technical service.
6.
Technical data
6.1
Classification acc. to Regulation (EU) 2017/745
Art. no.
Designation
Class
Various
Compressed-air hoses
I
6.2
Performance data, information about standards
Operating pressure
6 bar to 10 bar (85 PSI to 142 PSI)
Exit air backup
0.5 bar to 0.7 bar (7 PSI to 10 PSI)
Accessories / spare parts
Art. no.
Designation
Illustration
GA099
Pressure reducer for compressed-gas cylinders according to DIN EN ISO 11117 (8/89)
GB463R
Holder for compressed-air hose GA460R, GA464R, GA466R
–
GB480R
Holder for compressed-air hose GA468R
–
GB564R
Holder for compressed-air hose GA505R, GA513R, GA523R
–
GB575R
Holder for compressed-air hose GA506R
GB576R
Holder for compressed-air hose GA507R
–
GB600
Aesculap STERILIT oil spray
–
TA011106
Instructions for use compressed-air hoses
–
11