Alere
Afinion AS100 Analyzer User Manual Rev B Jan 2014
User Manual
40 Pages
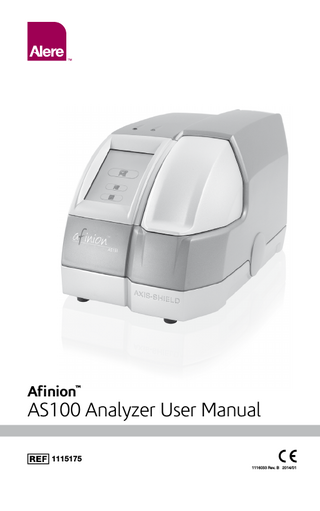
Preview
Page 1
Afinion
™
AS100 Analyzer User Manual 1115175 1116033 Rev. B 2014/01
Dear Customer, Congratulations on the purchase of your Afinion™ AS100 Analyzer. Upon arrival of your Afinion™ AS100 Analyzer we recommend that the serial number along with the software version be recorded in the table provided below. The additional rows in the table are to be utilized if a software upgrade is performed on your AS100 Analyzer. The recorded information will be of great value if and when a question is reported, or the desire to add a new Afinion™ test to your Analyzer arises.
Serial number (see label on the underside of the Analyzer or on the transport container) NOTE! The Analyzer must be turned off when the label on the underside is read.
Software records Date
Software version*
Afinion™ tests available
Upon receipt 1. SW upgrade 2. SW upgrade 3. SW upgrade 4. SW upgrade 5. SW upgrade * See start-up menu when you power on the Analyzer (see “How to power on the Analyzer”, page 10).
Notes
Technical Support Call 1.866.216.9505
1
AfinionTM AS100 Analyzer System Intended use Afinion™ AS100 Analyzer with Afinion™ Data Connectivity Converter (ADCC) is a compact multi-assay analyzer for point-of-care testing, designed to analyze the Afinion™ Test Cartridges. The ADCC is a small device for automatic transfer of data, including patient and control assay results, from the Afinion™ Analyzer to a laboratory information system or another electronic journal system. Afinion™ AS100 Analyzer System, consisting of Afinion™ AS100 Analyzer with Afinion™ Data Connectivity Converter (ADCC), Afinion™ Test Cartridges and Afinion™ Controls is for in vitro diagnostic use only.
CLIA Statements
Waived Afinion™ tests Afinion™ HbA1c is waived under the Clinical Laboratory Improvement Amendment of 1988 (CLIA`88). A CLIA Certificate of Waiver is needed to perform testing in a waived setting. If the laboratory does not have a Certificate of Waiver, the Application for Certification (Form CMS-116), can be obtained at https://www.cms.gov/cmsforms/downloads/cms116.pdf. The form should be mailed to the address of the local State Agency of the State in which the laboratory resides (https://www.cms.gov/CLIA/12_State_Agency_&_Regional_Office_CLIA_Contacts.asp). If the laboratory modifies the Afinion™ test or Afinion™ AS100 Analyzer system instructions, the test no longer meets the requirements for waived categorization. A modified test is considered to be highly complex and is subject to all applicable CLIA requirements.
Conformity to the IVD directive The Afinion™ AS100 Analyzer meets all provisions in the European directive 98/79/EC on In Vitro Diagnostic Medical Devices and is CE marked accordingly.
Safety standards Afinion™ AS100 Analyzer has been tested and found to be in conformity with IEC, UL, CAN/CSA-C22.2: 61010-1 (Safety requirements for electrical equipment for measurement, control, and laboratory use), IEC 61010-2-081:2001 + A1 and IEC 61010-2-101:2002 (Particular requirements for in vitro diagnostic (IVD) medical equipment).
EMC standards Afinion™ AS100 Analyzer has been tested and found to be in conformity with EN 61326-1:2006 (Electrical equipment for measurement, control, and laboratory use – EMC requirements) and EN 61326-2-6:2006 (In vitro diagnostic (IVD) medical equipment) and CFR 47 Telecommunications, Chapter I- FCC Part 15 – Radio Frequency Devices – Subpart B: unintentional radiators.
Axis-Shield PoC AS P.O. Box 6863 Rodeløkka NO-0504 Oslo, Norway ISO 9001 and ISO 13485 certified company
2
TABLE OF CONTENTS
Table of contents INTRODUCTION
ANALYZER SYSTEM DESCRIPTION
About this User Manual
5
Examining the package contents
5
Description of the Afinion™ AS100 Analyzer
6
Description of the Afinion™ Test Cartridge
7
How the Afinion™ AS100 Analyzer System works
8
Internal process control
8
The Analyzer self-test
8
The fail-safe mechanisms
8
External process control
GETTING STARTED
CONFIGURATION
8
Operator ID
8
Quality Control lockout
8
Calibration
8
Installing your Analyzer
9
Connecting power supply
9
Connecting additional equipment
9
How to power ON the Analyzer
10
How to power OFF the Analyzer
10
How to operate the Analyzer
11
Afinion menues
12
Setting the configuration
13
Patient ID configuration
13
Patient ID enable/disable Operator configuration
QUALITY CONTROL
8
Patients ID
13 14
Operator ID enable/disable
14
Operator login expiration
14
Operator management
14
Copy operator list
15
Choosing language
15
Setting date and time
15
Adjusting screen/beeper volume settings
16
QC lockout configuration
17
Select assay type
17
QC lockout
17
QC lockout interval
17
Control lot database
17
Why quality control testing?
18
Choosing control material
18
Handling and testing controls
18
Frequency of control testing
18 Table of contents continues on next page
3
TABLE OF CONTENTS
TESTING PROCEDURES
Operating precautions
19
When handling the Test Cartridge
19
Preparing for an Afinion™ analysis
19
Collecting a sample
20
Analyzing a patient/control sample
21
Using the operator ID function
22
Entering operator ID
22
Using the patient ID function
22
Entering patient ID
22
Using the control ID function
23
Entering Control ID
23
Using the QC lockout function
24
QC lockout status
24
Running controls with enabled QC lockout function
25
Passed (Within the acceptable control range)
25
Failed (Above or below the acceptable control range)
25
Patient and control results records View, print and export patient and control results INFORMATION CODES AND TROUBLESHOOTING
MAINTENANCE AND WARRANTY
TECHNICAL SPECIFICATIONS
GALLERY OF ICONS SYMBOLS AND ABBREVIATIONS
4
19
When operating the Analyzer
26 26
When an information code appears
27
Information codes caused by assay specific limitations
27
Information codes caused by sample or Test Cartridge failure
28
Information codes or messages caused by Analyzer failure
28
Other information codes
29
Service information
29
Cleaning and maintenance
30
Cleaning the exterior
30
Cleaning the cartridge chamber
30
Disposal of the Analyzer
30
Software upgrade
30
Warranty
31
Afinion™ AS100 Analyzer
32
Additional equipment
32
The touch buttons and their function
33
Other symbols and signs
35 36
Introduction
About this User Manual This User Manual will guide you through installation, operation and maintenance of your Afinion™ AS100 Analyzer. The User Manual also explains how the Analyzer works, describes the quality assurance system and assists you in troubleshooting. For analyzing patient samples or controls, please also read the test specific information given in the Package Inserts found in the Afinion™ test kits. The Quick Guides highlight the main steps of the test procedures and contains information on proper quality control routines. It is recommended that you become familiar with the user instructions before you start operating the Afinion™ AS100 Analyzer. Some of the information in this User Manual is accompanied with a symbol that points you to the following particulars: Operator’s handling Warnings and precautions References to the Package Inserts and Quick Guides for the specific Afinion™ tests and control kits
Examining the package contents When unpacking, check the contents against the list below and examine the components for signs of shipping damage. The Afinion™ AS100 package unit includes: • • • • • •
Afinion™ AS100 Analyzer Power cable Power cord adapter, 24 volt power supply Quick Guides for the available Afinion™ tests User Manual Installation video (CD-ROM)
If the package unit is found incomplete, please report missing items or shipping damage to your supplier. It is recommended to keep the shipping box in case of later transportation of the Analyzer.
5
ANALYZER SYSTEM DESCRIPTION
Description of the Afinion™ AS100 Analyzer Figure 1 shows the main exterior parts of the Afinion™ AS100 Analyzer.
1 2 3 4 5 6
Figure 1 1
ON/OFF button:
Turns the power to the Analyzer on and off.
2
Red and green LEDs:
Light emitting diodes (LEDs) that indicate whether the Analyzer is busy or not.
3
Touch screen:
Allows you to communicate with the Analyzer through touch icons and messages.
4
The lid:
Covers and protects the cartridge chamber.
5
Cooling ribs:
Facilitate temperature control.
6
Connectors:
Connection to power cord adapter USB port- Options for printer, barcode reader, export of patient and control record to USB flash and SW upgrade. RS232- Connectivity options to EMR and/or HIS/LIS systems through the Afinion Data Connectivity Converter (ADCC)
Do not open the lid manually.
6
ANALYZER SYSTEM DESCRIPTION
Description of the Afinion™ Test Cartridge The Afinion™ Test Cartridge is unique for each analyte to be measured, as the reagent composition, reagent volumes and the integrated devices are test specific. The Test Cartridge and the sampling device labels have a unique color for each test. The Test Cartridges are separately packed in foil pouches to protect the chemicals and plastic devices from light, dirt and humidity. A single Test Cartridge contains all necessary reagents for one test and is ready to use. An integrated sampling device is used for collection of the patient sample or control. The Test Cartridge cannot be re-used. Figure 2 illustrates an Afinion™ Test Cartridge with its functional parts:
Left side
Right side
1b
1a 2 4 5
7
6
3
Figure 2 1
Sampling device:
For collection of patient sample or control. 1a - closed position 1b - lifted position
2
Capillary:
Capillary to be filled with sample material.
3
Reaction wells:
Contains all necessary reagents for one test.
4
Handle:
For correct finger grip.
5
Barcode label:
Contains assay and lot specific information for the Analyzer.
6
Optical reading area:
Area for transmission measurement.
7
ID area:
Space for written or labeled sample identification.
7
ANALYZER SYSTEM DESCRIPTION
How the Afinion™ AS100 Analyzer System works The Afinion™ AS100 Analyzer System uses different chemical and mechanical assay methods combined with advanced, computerized processing and measuring technology. A Test Cartridge with patient sample or control is placed in the cartridge chamber of the Analyzer. By manually closing the lid, the Test Cartridge is transported into the analysis compartment of the Analyzer. Test and lot-specific information is obtained from the barcode label (Figure 2). When the Test Cartridge enters the Analyzer, the integrated camera reads the barcode. The calibration data for the actual lot are read, which then initiates the processing of the Test Cartridge. The sample and reagents are automatically transferred between the wells. An integrated camera monitors the entire process. Light-emitting diodes (LEDs) illuminate the reaction area, which can be either a colored membrane or a reaction well. The camera detects the reflected or transmitted light, which is converted to a test result and displayed on the touch screen. When the user accepts the result, the lid covering the cartridge chamber opens automatically and the used Test Cartridge can be removed and discarded. The Analyzer is then ready for the next run.
Internal process control The Analyzer self-test
A self-test is performed during start-up of the Analyzer to ensure that the instrument is operating according to established specifications. The self-test validates: • • • •
Hardware and software integrity Test Cartridge transport system Liquid transport system Camera vision system
If the self-test fails at any point the red LED will start flashing and an information code will be displayed on the touch screen (see “Information codes and troubleshooting”, page 27). When the Analyzer is powered on for a longer period, it will automatically restart once a day to ensure that a self-test is done regularly. This procedure does not interrupt any analysis of the Test Cartridge.
The fail-safe mechanisms
Fail-safe mechanisms are included to secure safe processing. The integrated camera inspects the test cartridges initially before the process starts and during the assay. If defects are detected (e.g. broken capillary or the cartridge is used past its expiry date), the Test Cartridge is rejected and an information code is displayed. During processing vital functions and components (e.g. pumps and heater) are supervised. When problems are detected by the built-in safety mechanism, the process will be aborted and an information code will be displayed.
External process control Patient ID
The Afinion patient ID functionality will, if configured, allow up to four patient ID fields to be entered. The Patient ID will be stored with each patient test result in the result records.
Operator ID
The Afinion operator functionality will, if configured, require the operators to login before testing. The functionality may also prevent un-authorized operators to login, perform tests and configuration. The operator ID will be stored with each test result in the result records.
Quality Control lockout
The Afinion QC lockout function allows you to configure the instrument to automatically enforce your local required frequency of control testing. If the required control test has not been performed or the control result is outside the acceptable range, the instrument will disable patient testing for this assay. For manufacturer recommendations see Frequency of control testing page 18. For more information regarding these functionalities, see Setting the configuration page 13.
Calibration The Afinion™ AS100 Analyzer has been manufactured to deliver reliable and accurate results. During manufacturing, the Analyzers are calibrated against a reference system. This procedure has been established to ensure that all Analyzers operate within identical tolerance limits. Test specific calibration data are established for each lot of Test Cartridges and then stored in the barcode label (Figure 2). When the Test Cartridge enters the Analyzer, the integrated camera reads the barcode. The calibration data for the actual lot are transferred to the instrument and used for calculating the results. Calibration by the operator is thus not required.
8
Getting started
Installing your Analyzer Place your Afinion™ AS100 Analyzer on a dry, clean, stable and horizontal surface. Make sure that the Analyzer is located with sufficient surrounding airspace, at least 5 inches on each side. Acclimate the Analyzer to ambient operating temperature (15-32°C, 59-89°F). The Analyzer might be impaired by: • Condensing humidity and water • Heat and large temperature variations • Direct sunlight
• Vibrations (e.g. from centrifuges and dishwashers) • Electromagnetic radiation (e.g.from mobile phones) • Movement of the Analyzer during processing of a Test Cartridge
Connecting power supply - Connect the power cable to the power cord adapter. - Insert the plug from the power cord adapter into the power socket (Figure 3) in the back of the Analyzer. - Plug in the power cord to a wall outlet. Always use the correct supply voltage. The power supply voltage must match the information quoted in the section “Technical specifications”, page 32.
Figure 3 1 Not in use 2 USB-A connectors for printer, USB flash and/or barcode reader 3 RS-232 port for connection to HIS or LIS systems. 4 Power input for power supply connection
Connecting additional equipment Optional equipment, not provided with your Afinion™ AS100 Analyzer are: • External barcode reader – for reading barcoded sample or operator identification. • Printer – for optional print out of test results. • Afinion™ Data Connectivity Converter - For data transfer to HIS or LIS systems (see “Additional equipment”, page 32.) For additional information regarding the barcode reader, printer, and connection to HIS or LIS systems, please contact your local Afinion™ supplier. Connecting the equipment should be done while the Analyzer is powered off.
9
Getting started
How to power ON the Analyzer 1
Power on the Analyzer by pressing the ON/OFF button (Figure1). An automatic start-up procedure will be initiated. Please wait. Do not open the lid manually.
2
The automatic start-up procedure will be initiated shortly after the Analyzer has been powered on. The red light on the top of the Analyzer will turn on, indicating that the Analyzer is busy. The Analyzer is ready for use when the start-up menu is displayed and the green indicator light turns on.
3
Start-up menu The Analyzer’s software version (SW X.XX) will appear in the upper left corner of the Start-up menu screen. The temperature displayed in the Start-up menu is the operating analyzer temperature. Make sure that the operating temperature is within the recommended range for your Afinion™ test (see the Package Insert for the Afinion™ test). If the Analyzer fails during the start-up procedure, an information code will appear referring to a message given in the “Information codes and troubleshooting”, page 27.
How to power OFF the Analyzer Power off the Analyzer by pressing the ON/OFF button (Figure 1). The Analyzer should be powered off after the end of a working day. Please note: • When the power is turned off, a closing down procedure is initiated. The cartridge carriage will move to a safe position and the display will be active a few seconds while the Analyzer shuts down. The Analyzer can be powered off, or the power supply disconnected, without loss of stored results. • The Analyzer can only be powered off when the cartridge chamber is empty and the lid is closed. If the ON/OFF button is pressed and the lid is open, the message ”Close lid” will appear on the screen.
10
Getting started
How to operate the Analyzer The Afinion™ AS100 Analyzer has two main user interfaces, the touch screen and the cartridge chamber. The Analyzer is easily operated using the touch buttons that appear on the screen. When a button is touched, its function will be activated. Text messages that appear on the screen will help guide you through the testing procedure. The functions of the touch buttons are explained in the “Gallery of icons”, page 33. The other main operative part of the Afinion™ AS100 Analyzer is the cartridge chamber. The cartridge chamber is designed to receive the Test Cartridge in one orientation only. The lid must be manually closed, but opens automatically. When a new Test Cartridge is placed in the chamber, manually closing the lid will initiate the analysis. When the analysis is complete the lid will open automatically. The lid protects the cartridge chamber from dust, dirt, light and humidity during processing and when the Analyzer is not in use. • The lid must be manually closed, but opens automatically. Do not open the lid manually. • Use the fingertips only on the touch screen. Do not use pens or other sharp instruments.
3
Figure 4 1 Text message 2 Touch buttons 3 The lid in open position 4 The cartridge chamber with a Test Cartridge
1
2 4
Screen saver
The screen saver will turn on after 3 minutes, if the touch screen is not in use. To re-activate, touch the screen.
Light signals (the red and green LEDs)
The red diode is illuminated when the Analyzer is busy. A flashing red light is seen when an information code is displayed. The green diode is illuminated when the Analyzer is ready for use. A flashing green light indicates completion of an analysis.
Sound signals
A short beep indicates completion of an analysis. Two beeps mean that an information code or message is displayed.
11
configuration
The Afinion Menues Start-up menu
Main menu
Configuration menu
Patient ID configuration menu
Operator configuration menu
QC lockout configuration menu
Language settings
Date/Time Menu
Screen and beeper volume menu
12
configuration
Setting the configuration Before using your Afinion™ AS100 Analyzer you should set the configuration according to your needs. To enter the configuration menu, do the following:
1
Start-up menu
2
Main menu
Touch
Touch
3
to enter main menu.
to enter configuration menu.
Configuration menu Select an item for configuration (see following pages).
Patient ID configuration Patient ID enable/disable The patient identification (ID) function can be enabled or disabled. The patient ID function is enabled as a default setting by the manufacturer. When the patient ID function is enabled, the patient ID must be entered for each Test Cartridge to be analyzed. If the patient ID function is disabled, a run number will automatically replace the patient ID and be displayed in the upper left corner of the screen. This numbering is reset each day at midnight. Touch
in the configuration menu to enter the patient ID on/off option. Select
to disable the patient ID function.
Select
to enable the patient ID function.
Touch
to accept and return to the configuration menu.
13
configuration
Operator configuration The Operator ID function is disabled as a default setting by the manufacturer. in the configuration menu to enter the operator configuration menu. Touch
Operator ID enable/disable Touch
in operator configuration menu to enable/disable operator ID. Select
to disable the operator ID function.
Select
to enable operator ID. Any operator ID is accepted.
Select
to enable operator ID with verification.
· To enable this function at least one supervisor is required to be present in the operator list. · When operator ID verified is enabled, instrument configuration will only be available to the supervisors. · To log in, the operator ID entered is required to be present in the operator list. See Operator management, bottom of the page. Touch
to accept and return to the configuration menu.
Operator login expiration Touch
in the operator configuration menu to set automatic logout of the operator. Enter the number of minutes before automatic logout of operator. The operator will automatically be logged out after the configured number of minutes after analysis of the test is complete.. Touch
to confirm and return to previous view.
Operator management Touch
1
2
in operator configuration menu to enter operator list. Touch
to add new operator.
Touch desired operator ID and touch
to delete or
to edit the highlighted operator.
Enter new/edit operator ID Enter new/edit operator ID and touch to enter. Both letters and numbers can be entered (maximum 16 characters). If a barcode reader is connected to the Analyzer, a barcoded operator ID can be entered.
14
configuration
3
Configure the operator level: Select whether this operator will be a user or supervisor. 1) User 2) Supervisor Configure tests accessible by checking the appropriate test boxes for this operator.. Check of the test accessible for this operator. Touch
to return and edit the operator ID.
Touch IDs.
to accept and store new operator in the operator list. The operator list can store 500 operator
Supervisors will be marked with * in the operator list. When instrument is configured to Operator ID verified, configuration of instrument settings will only be available to the supervisors.
Copy operator list
It is possible to copy operator lists between instruments using a USB flash drive. Insert USB flash in instrument USB port. Touch to export operator list from instrument to USB flash. Move USB to new import operator list. Any existing operator list on the instrument will be instrument and touch to deleted.
Choosing language Touch in the configuration menu to enter the language selection. The default setting by manufacturer is English. Other languages are available. Touch the arrow in the window to view other options. Scroll down until you find the preferred language. Touch to accept and return to the configuration menu.
Setting date and time The correct date and time should always be set because the date and time for the analyses are stored and displayed in the patient and control records. The date format is YYYY:MM:DD, where YYYY is the year, MM is the month (01 to 12), and DD is the day (01 to 31). The time format is hh:mm, where hh is the hour from 00 to 23 and mm is minutes from 00 to 59. Touch
1
2
in the configuration menu to enter date/time setting. Touch
to enter date setting.
Touch
to enter time setting.
Enter today’s date or time. Touch
to confirm and return to the previous view.
15
configuration
Adjusting screen/beeper volume settings Touch
in the configuration menu to enter the screen/beeper volume settings.
The screen contrast can be adjusted. Touch
to enter the screen contrast setting.
Touch
to enter the screen alignment setting.
Touch
to enter the beeper volume setting.
Screen contrast setting Adjust the screen contrast by touching Touch
or
to confirm and return to previous view.
Screen alignment setting Tap the cross-hair object (+) in the upper left corner using a blunt pencil to be precise. Repeat for the object appearing in the lower right corner and in the center of the screen. The previous screen view will automatically return.
Beeper volume setting Adjust the beeper volume by touching Touch
16
or
to confirm and return to the previous view.
configuration
QC lockout configuration The QC lockout function is disabled as a default setting by the manufacturer. Touch in the configuration menu to enter the QC lockout setting menu.
1
Touch
to configure QC lockout for the assay selected.
Touch
to configure QC lockout interval.
Touch
to view/add/delete stored control lots in the control lot database.
Select assay type Touch the arrow in the window to open the drop down menu to select the assay type. Touch the assay to select.
2
QC lockout Select
to disable the QC lockout function. No QC runs will be required for this assay
to enable the QC lockout function. It is required to run ONE passed control, Select control level C I OR C II, to reset the QC lockout interval. to enable the QC lockout function. It is required to run TWO passed control, Select both control level C I AND C II, to reset the QC lockout interval. Touch
3
to confirm and return to the previous view.
QC lockout interval Select
to configure QC lockout interval by number of runs.
Select
to configure QC lockout interval by hours.
Touch
to enter/edit number of runs/hours to QC lockout.
displays the number of runs/hours configured in the QC lockout interval. to confirm and return to the previous view. Touch
4
Control lot database To add a control to the control lot database, the Afinion Control Data is required. The Afinion Control Data is a numeric data string which contains all lot spesific data: • Afinion control lot number • Control type (assay) • Control level (CI or CII)
• Control expiry date • Acceptable control range • CRC (check sum to validate the previous data)
The Afinion Control Data and its accompanying barcode is found in the Afinion Control kit package insert. If the Afinion Control Data is not available, contact your local supplier. and either manually enter the Control Data or if a barcode reader is connected to the Analyzer Touch (recommended), scan the barcode. The Afinion Control Data may also be entered before, during or after a control run. The control lot will automatically be stored in the database. See page 25. to delete selected lot number from the control lot database. When a control lot has reached its Touch expiry date, the control will automatically be deleted from the instrument control database. The control lot database can store 100 control lots.
17
Quality control
Why quality control testing? Quality control testing should be done to confirm that your Afinion™ AS100 Analyzer System is working properly and providing reliable results. Only when controls are used routinely and the values are within the acceptable ranges can accurate results for patient samples be assured.
Choosing control material Controls recommended by manufacturer should be used for quality control of your the Afinion™ AS100 Analyzer System. These control kits contain control materials with established acceptable ranges for the Afinion™ AS100 Analyzer System.
Handling and testing controls Consult the Package Insert that comes with each control kit for detailed instructions on handling and storage of the control material. To run a control, follow the procedure in the section “Testing procedures”, page 19-26. The measured value should be within the acceptable range stated on the control vial label or in the control package insert. If the control results are within the acceptable ranges, patient samples may be tested and results reported. If the result obtained for a control is outside the acceptable limits, make sure that: - The control vial has not passed its expiry date. - The control vial has not passed its open vial expiry date. - The control vial and Afinion™ Test Cartridges have been stored according to recommendations. - There is no evidence of bacterial or fungal contamination of the control vial. Correct any procedural error and re-test the control material. If no procedural errors are detected, it is recommended to examine the laboratory’s quality control record to investigate the frequency of control failures. Ensure that there is no trend in out-of-range quality control results. Re-test the control material using a new control vial. Patient results must be declared invalid when controls do not perform as expected. Contact your Technical service representative (1.866.216.9505) for advice before analyzing patient samples.
Frequency of control testing Controls should be analyzed: • When starting up an Afinion™ AS100 Analyzer for the first time. • With each new shipment of Afinion™ test kits. • With each new lot of Afinion™ test kits. • Users with a low frequency of testing should analyze controls at least every 30 days. • When training new operators in correct use of the Afinion™ AS100 Analyzer. • Anytime an unexpected test result is obtained. • After software upgrade of the Afinion™ AS100 Analyzer. The controls should always be analyzed if an unexpected test result is obtained (see the Afinion™ test Package Insert, section Test result reporting). If local, state and/or federal regulations require more frequent testing of control materials, then quality control should be performed in compliance with these regulations. Each laboratory site can benefit from establishing a quality control plan. The laboratory director should determine whether additional testing is appropriate for their laboratory.
18
Testing procedures
Operating precautions When operating the Analyzer • Use your fingertip to operate the touch screen. Do not use pens or other objects that may scratch or damage the screen. Exception: If the screen alignment function is required, you will need to use a blunt pencil. • The lid opens automatically, but must be closed manually. Do not try to open the lid manually. • The lid protects the cartridge chamber from dust, dirt, light and humidity. Empty the cartridge chamber and keep the lid closed when the Analyzer is not in use. • If an information code appears on the screen during the analysis, please consult the “Information codes and troubleshooting” section, page 27. • Do not move the Analyzer when a Test Cartridge is being processed.
When handling the Test Cartridge • Do not use Test Cartridges after the expiry date, or if the Test Cartridges are not stored in accordance with the recommendations. • Do not touch the Test Cartridge optical reading area. Hold the Test Cartridge by the handle. (Figure 2). • Do not use the Test Cartridge if the foil pouch, the desiccant bag or the Test Cartridge itself is damaged. • The Test Cartridges must reach recommended operating temperature before use. • Do not open the foil pouch until just before use. Once opened, the Test Cartridge has limited stability. • Handle and dispose the Test Cartridges and sample collection equipment as potential biohazardous materials. Use gloves. • Do not re-use any part of the Test Cartridge. Consult the Package Insert that comes with each Afinion™ test kit for assay specific information.
Preparing for an AfinionTM analysis -
Allow the Afinion™ Test Cartridges to reach the recommended operating temperature before use. Power on your Afinion™ Analyzer so it is ready for the day’s first analysis. Enter the operator ID (optional). See procedure on page 22. The patient ID, control ID or Afinion Control Data can be entered before or during processing of the Test Cartridge in the Analyzer. See procedures on page 21–25.
Consult the Package Insert that comes with each Afinion™ test kit for assay specific information.
1
2
3
Open the foil pouch. Grip the handle and remove the Test Cartridge from the pouch. Discard the desiccant bag and foil pouch in suitable waste containers.
Inspect the Cartridge. Do not use the Test Cartridge if it is damaged or if loose desiccant particles are found on the Test Cartridge.
Mark the Test Cartridge with the patient or control ID. Use the ID area on the Test Cartridge. An ID label can also be used.
When first opened, the Test Cartridge has limited stability.
Use the handle to avoid touching the optical reading area.
Do not write on the barcode label or allow it to become wet, dirty or scratched. If an ID label is used, this must fit into the ID area.
If a barcode reader is connected to the Analyzer, a barcoded patient ID, control ID or Afinion Control Data can be entered.
19