Anspach
Electric High Power Drilling and Cutting Systems
eMax 2 Plus High Speed Electric System Instructions for Use
156 Pages
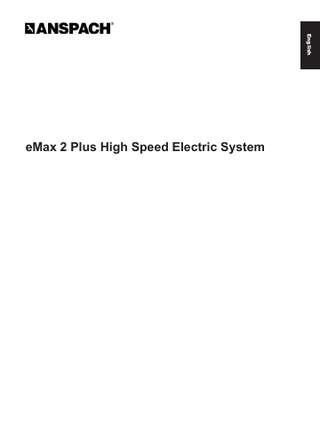
Preview
Page 1
English
eMax 2 Plus High Speed Electric System
i
English
Contents General Information...2 System Assembly...6 System Operation...6 System Shutdown...8 Additional Information...8 Console Alerts, Codes, and Displays...8 Trouble Shooting...9 Technical Specifications (IEC-60601-1-2 3rd Edition)...10 Technical Specifications (IEC-60601-1-2 4th Edition)...14
1
English
General Information System Description
High Speed Electric Drill System consisting of a console (SC2100, SC2101 or SC2102), handpiece (EMAX2PLUS), foot control (E-FP, E-FP-DIR or E-FP-DIR/IRR), country or region specific medically rated A/C Power Cord, attachment (various options) and dissection tool (various options). There is also an optional hand control (EMAX2-HC or E-HC) and irrigation accessories.
Indications for Use
Cutting and shaping bone including bones of the cranium and spine.
Cleaning and Sterilization
•• Prior to first use the equipment must be processed as per the included Anspach Cleaning and Sterilization instructions. •• At the point of use the device must be cleaned as soon as possible after use to prevent drying of blood, tissue, other biological debris and contaminants on the device. •• Refer to the Anspach Cleaning and Sterilization instructions accompanying this device.
Features & Compatibility Foot Control Features
Handpiece
•
•
•
E-FP-DIR
•
•
•
•
E-FP-DIR/IRR
•
•
•
•
•
EPLUS-FP
•
•
•
•
•
EPLUS-FP-NS
•
•
•
EMAX2PLUS
•
•
•
Two Foot Control Ports *
•
Two Handpiece Ports *
•
Console Irrigation
•
E-HC
E-FP
EMAX2-HC
SC2102
Console Features
Hand Controls
Active Irrigation Control Switch
SC2101
Active Direction Control Switch
SC2100
Foot Controls
Consoles
•
•
•
* If two foot controls or two handpieces are connected upon startup of console it will default to Foot Control 1 and/or Handpiece 1. The following instructions are written such that the handpiece and attachments are held with distal end pointed away from user.
Symbols
2
Anspach Product Icon
Consult Operating Instructions
Located on the Foot Pedal switch this indicates a change state (on/off) for the console Irrigation System
Located on the Foot Pedal switch this indicates a change of rotational direction for the handpiece
Direction of rotation
Keep Dry (A.K.A. Protect from Moisture)
Direction of rotation for lock position
Indicates position, alignment or location
Indicates setting, position or location
AC Power Source
Indicates setting, position or location
Indicates position or location
Indicates the attachment setting, refer to MADRIVER & MA-D20 section in this document for further details
Located on the Console this indicates motor or handpiece connector
Indicates the drill tip exposure
Symbol with yellow background: CAUTION: refer to accompanying documentation
Symbols Located on the Console this indicates Foot Control connector
Duty Cycle of the DRIVER
Revolution per Minute
Located on the Console this indicates Forward (Clockwise rotation when looking at handpiece from proximal end).
Located on the Console this indicates Reverse (Counter-Clockwise rotation when looking at the handpiece from proximal end) Located on the Console this indicates a change of irrigation state for the Console Irrigation System
Indicates action of rotation and position for Secure (LOCK) and Release (UNLOCK) Direction of rotation
Direction of rotation for lock position
Located on the Foot Pedal switch this indicates a change of rotational direction for the handpiece
00/0000
Direction of rotation 1. Console Control Touch pad: indicates a change state (on/off) for the Console Irrigation System 2. Irrigation Pump: Indicates irrigation tube direction towards the irrigation source Located on the Foot Pedal switch this indicates a change state (on/off) for the Console Irrigation System
Located on the Console this indicates a change of rotational speed rate for the Handpiece
NO NOT DISPOSE OF IN HOUSEHOLD WASTE
Temperature Limits
Sterile unless damaged or open
CE Mark (A.K.A. CE Mark [Notified body number], Conformité Européenne) Meaning: Device complies with applicable EEC Directives
United States Federal Law restricts this device to sale by or on the order of a physician or other licensed health-care provider
Found on the Console ON/OFF
Located in the Console Irrigation Pump this indicates a possible finger pinch point
Lock (Run)
Unlock (Load)
Located on the Console Irrigation Pump these symbols are not used by the user since the pump is self-adjusting to the Irrigation Tube Diameter
Located on the Handpiece this indicates position of the knurl knob to the desired location
Reference Number (A.K.A> Item Number, Catalogue Number, Part Number)
Serial Number
Lot (A.K.A. Lot Number, Batch Number, Batch Code)
Transmitter Interference may occur in the vicinity of equipment marked with this symbol.
Manufacturer
Type B Electrical Equipment
Use By Date (A.K.A. Expiration Date, Expiry)
Product warranty is void if seal is damaged or removed.
Authorized European Union Representative
Single Use Only (A.K.A. Do Not Reuse)
Sterilized Using Irradiation
CAUTION: Refer to accompanying documentation
Date of Manufacture
Global Trade Item Number (GTIN)
Batch or Lot Number
Expiration Date (YYMMDD)
Serial Number
Quantity
Global Trade Item Number Indicates Environmental Friendly Use Period of 10 years in China.
Certified/Accredited Test House
English
Located on the Console this indicates Hand Control activation
Indicates Environmental Friendly Use Period of 50 years in China. Indicates Environmental Friendly Use Period in China, this product does not contain any hazardous substances exceeding concentration limits. Compliant with IEC 60601-1-2 Ed. 4.0 (2014-02) Electromagnetic compatibility.
3
English
Warnings
•• Always use continuous irrigation to prevent heat build-up. Irrigation is necessary for proper performance. •• Surgeon is responsible for learning proper techniques in use of equipment; improper use may cause serious injury to user or patient or damage to system. •• Instrument operator and all operating room personnel must wear eye protection. •• Visually inspect for damage before using; do not use if damage is evident. •• Do not use if the product sterilization barrier or its packaging is compromised. •• Do not use, or discontinue use of powered equipment exhibiting excessive temperatures that can cause patient injury (necrosis) and/or user discomfort. •• Use of damaged or improperly maintained power equipment and/or misused powered equipment can result in excessive temperatures. •• Use caution to avoid cutting or tearing gloves while handling dissection tools. •• Disssection tools must be adequately retained within attachment to prevent distal migration, which may cause injury. Confirm attachment is proper size for dissection tool and that it is secure. •• Gently pull on dissection tool shaft to ensure it is fully seated and properly installed. •• Only cut visible areas unless an image intensifier is utilized. •• Delicate structures in proximity to dissection must be thoroughly protected to prevent injury. •• Maintain firm control of instrument at all times. •• Do not bend or use as a lever. •• Use a gentle tapping motion or side-to-side motion and let instrument do cutting. •• Do not use excessive force. •• Forceful side loading of dissection tool may cause fracture of dissection tool, which may cause injury. •• Dissection tools are disposable and intended for single patient use only. Do not re-sterilize and/or re-use dissection tools. Reuse and/or re-sterilization of these devices could result in reduced performance, material degradation and/or patient contamination •• Use standard protocol for disposal of sharp instruments. •• Continuous extreme cutting at or near stalling conditions will quickly overheat handpiece. •• Do not operate in an explosive flammable environment. •• Do not modify ground or power cord. •• Do not allow liquid into console. •• Do not use a craniotome in conjunction with Hand Control. Excessive rotational force on hand control may move it, thus shutting handpiece down. •• Use of accessories or cables other than those provided by DePuy Synthes Power Tools and specified for use with the eMax 2 Plus System may result in increased emissions or decreased immunity. •• The eMax 2 Plus should not be used adjacent to or stacked with other equipment and that if adjacent or stacked use is necessary, the eMax 2 Plus should be observed to verify normal operation in the configuration in which it will be used. •• Medical Electrical Equipment needs special precautions regarding EMC and needs to be installed and put into service according to the EMC information provided in this accompanying documentation. •• The emissions characteristics of this equipment make it suitable for use in industrial areas and hospitals (CISPR 11 class A). This equipment generates, uses, and can radiate radio frequency energy and, if not installed and used in accordance with the instruction manual, may cause harmful interference to radio communications. •• Operation of this equipment in a residential area (for which CISPR 11 class B is normally required) this equipment might not offer adequate protection to radio frequency communication services. •• In the event of interference, the user might need to take mitigation measures such as relocating or reorienting the equipment. •• Portable and Mobile RF communications equipment can affect Medical Electrical Equipment. •• Portable RF communications equipment (including peripherals such as antenna cables and external antennas) should be used no closer than 30 cm (12 inches) to any part of the EMAX2PLUS system. Otherwise, degradation of the performance of this equipment could result. •• Power source should comply with applicable IEC, CEC, and NEC requirements. Grounding reliability can only be achieved when this equipment is connected to a receptacle marked “HOSPITAL GRADE.” •• Do not use in oxygen rich environment. •• No modification of this equipment is allowed. •• Do not modify. Modifications could result in loss of electrical safety. •• Dispose of items contaminated with body fluids with other biohazardous waste. •• At end of life recycle or dispose of device in accordance with local and national regulations. •• To avoid the risk of electric shock, this equipment must only be connected to a supply mains with protective earth. The use of Accessories, transducers, and cables other than those specified, with the exception of transducers and cables sold by the Manufacturer of this device as replacement parts for internal components, may result in increased Emissions or decreased Immunity of the eMax 2 Plus System.
4
Cautions
English
•• United States Federal law restricts this device to sale by or on order of a physician or other licensed healthcare provider. •• Do not use accessories other than those provided by DePuy Synthes Power Tools and specified for use with Anspach Systems. •• To insure equipment operates as designed, read and follow manufacturer’s instructions. •• Do not operate handpiece without an attachment and the corresponding dissection tool. •• Do not engage safety mechanism while handpiece is running; doing so makes safety mechanism inoperable. •• Only Anspach Dissection Tools should be used with eMax 2 Plus Systems. •• Use care to protect hose when handling, cleaning, and during system use. •• Damage to hose can cause leaking, rupture, or other related failures. •• Do not step on, set equipment on, pinch, kink, clamp, or otherwise occlude handpiece hose during use. •• Do not engage safety mechanism while handpiece is running; doing so makes safety mechanism inoperable. •• Do not use the eMax 2 Plus System with MS-OSC or MS-SAG; attempting to do so will result in damage to saws and possible damage to the eMax 2 Plus Handpiece.
Latex Information
Not made with natural rubber latex.
Warranty & Return Policies
Warranty and return policy is available upon request. Warning: All Instrument System components returned for servicing or repair should be properly cleaned and sterilized as applicable prior to shipping.
Warning: Transmissible Spongiform Encephalopathies (TSE)
DePuy Synthes Power Tools will not authorize or accept the return of products that directly contact patients or are contaminated with a patient’s body fluids who is suspected or confirmed with a Transmissible Spongiform Encephalopathies/ Creutzfeldt-Jakob Disease (TSE/CJD) diagnosis. DePuy Synthes Power Tools recommends that all Anspach products used on a patient confirmed with a TSE/CJD diagnosis be incinerated. Anspach Dissection Tools used on a patient suspected of TSE/CJD diagnosis must be incinerated. Contact your Sales Representative for replacement of product incinerated under this policy or for temporary equipment while original equipment is quarantined. Contact the DePuy Synthes Power Tools Customer Service Department regarding TSE/CJD contamination for additional information.
5
English
System Assembly Warning
Prior to first use the equipment must be processed as per the included Anspach High Speed System Cleaning and Sterilization instructions. Note: When following these instructions hold handpiece and attachments with distal end pointing away from user. 1. Plug hospital grade AC power cord into AC power inlet on back of console. Plug opposite end of power cord into standard, hospital grade grounded wall outlet. Connect to supply mains with protective earth only. 2. Insert foot control cord connector into Foot Control 1 connector port. (A second foot control cord may be connected into Foot Control 2 connector port on applicable consoles.) Foot control cord connector is keyed. Align foot control cord connector with connector port on front of console. Do not push foot control cord connector into console connector port when out of alignment. 3. Plug handpiece hose connector into Handpiece 1 connector port located on front of console. (A second handpiece may be connected into Handpiece 2 connector port on applicable consoles.) Handpiece hose connector is keyed. Align handpiece hose connector with connector port on front of console. Do not push handpiece hose connector into console connector port when out of alignment. 4. Activate console by depressing power switch located on back of console to “I” position. Appropriate face panel light emitting diodes (LED) illuminate and a beep will sound. 5. For operating instructions see Console Face Panel Operation and Foot Control Operation below. Note: Handpiece is fully functional at this time. Irrigation Assembly for Consoles with Optional Irrigation (Excludes SC2102) 1. 2. 3. 4.
Upon startup “Irrigation” is OFF, and LED is not illuminated. Insert IV pole into bracket on back of console. Hang irrigation bag onto IV pole. Check integrity of irrigation tubing package and use by date.
Warning: Discard product if sterilization barrier or its packaging is compromised or if past its expiration date. 5. Remove tubing and hose clips from package. 6. Connect small diameter tubing to proximal end of attachment clip. 7. Secure clip to handpiece and attachment. 8. Route tubing along handpiece hose and secure to hose using hose clips. 9. Remove protective cap from bayonet and insert bayonet into irrigation bag. 10. Hold irrigation bag and tubing vertical and allow fluid to completely fill large diameter tubing. 11. Depress button located on right side of console to eject pump head. 12. Lift top of pump head and insert large diameter section of tubing into pump. Refer to diagram on pump housing to ensure tubing is routed properly (smaller diameter tubing flows towards Anspach Handpiece). Note: Verify there are no air bubbles between irrigation bag and pump. If air bubbles are present, remove tubing from pump and allow fluid to completely fill large diameter tubing and reinstall to pump. 13. Check position of tube in pump to avoid damage to irrigation tubing and close pump head. 14. To activate, depress “Irrigation” button on face panel. LED illuminates. 15. To control flow of irrigation, depress arrows located to right of irrigation button on face panel. Note: Irrigation can also be activated from certain optional Foot Controls (see Step 5 of Foot Control Operation). 16. Depress Irrigation Control Switch on top right of foot control. Upon activation, LED on face panel illuminates. Caution: Tubing can disconnect from connectors without warning if occluded. Do not step on, set equipment on, pinch, kink, clamp, or otherwise occlude tubing during use. Do not operate with pump head open. Warning: Irrigation tubing, attachment clip, and hose clip are SINGLE USE ONLY. Reuse and/or re-sterilization of these devices could result in reduced performance, material degradation and/or patient contamination. For proper operation only use at ambient temperatures between 65°F to 85°F (18°C to 29°C).
System Operation
Upon startup, console is set to operate handpiece in forward (clockwise when viewed from proximal end of handpiece) direction at maximum speed and display reads 80,000 RPM. System operation, including optional irrigation, can be controlled from console face panel. On applicable consoles LED’s on face panel correspond to connector ports on connector panel. System operation can also be controlled by several available foot control options and an optional hand control.
Console Face Panel Operation
1. To increase or decrease speed of handpiece, depress blue arrows located on console face panel. Speed increases and decreases in 10,000 RPM increments. 2. To change direction, depress “R” or “F” arrow located on console face panel. Console beeps once, indicating handpiece direction has changed. Direction can only be changed when handpiece is not running. A series of three beeps indicates console is set to operate handpiece in reverse/counterclockwise direction. LED on console face panel located to left of “F” indicates forward direction. LED located to left of “R” indicates reverse direction. 3. (Optional) To activate irrigation, depress “Irrigation” button on face panel. LED illuminates. To control flow of irrigation, depress arrows located to right of irrigation button on face panel.
6
Foot Control Operation
Certain optional foot controls have direction and irrigation control switches.
Note: Handpiece is fully functional at this time.
English
1. See Step 2 of Console Face Panel Operation to set operational direction of handpiece. 2. (Optional) Depress “Foot” button on face panel to activate Foot Control 1, depress again to activate Foot Control 2. Only one foot control may be active at a time. 3. Press on foot control pedal to start handpiece. Increase pressure on pedal to increase speed of handpiece and release pressure on pedal to decrease speed of handpiece. 4. (Optional) To change direction of handpiece, depress Directional Control Switch located on top left of foot control for a minimum of one second. When direction changes, a single beep will sound and LED on console face panel indicates direction of rotation. Direction can only be changed when handpiece is not running. 5. (Optional) To activate irrigation, depress Irrigation Control Switch on top right of foot control for a minimum of one second and then step on center of foot control pedal. Upon activation, LED on face panel illuminates; irrigation pump and handpiece start.
Hand Control Assembly and Operation
Optional hand-control attachment for handpiece allows user to control operation with a lever attached to handpiece. Warning: Do not expose handpiece to magnets (such as laying handpiece on magnetic drapes) when in hand control mode, as handpiece operation may occur. Warning: It is recommended that a craniotome not be used in conjunction with Hand Control. Excessive rotational force on hand control may move it resulting in handpiece shutting down. 1. Upon console startup Hand Control is OFF. LED is not illuminated. 2. Rotate handpiece until small dimple at proximal end (hose end) of handpiece faces up. Slide hand control over distal end of handpiece such that notch on hand control slides over dimple at proximal end (hose end) of handpiece. Slide Hand Control onto handpiece until secure. 3. To activate Hand Control, depress “Hand” button on console face panel. This deactivates Foot Control; Hand Control LED on face panel illuminates. 4. To prevent inadvertent operation, ensure silver lever on Hand Control is fully inserted in “Lock” position. 5. Extend silver lever from “Lock” position for operation. 6. Apply pressure on Hand Control to operate handpiece. Note: Handpiece is fully functional at this time. 7. To deactivate Hand Control, depress “Foot” button on console face panel. To remove hand control from handpiece, slide towards distal end of handpiece and remove.
System Operational Assessment
1. Confirm attachment and dissection tools are properly locked in place. 2. Depress foot pedal to assure you have properly functioning device prior to proceeding. 3. Confirm device functions as expected. If device does not function as expected refer to troubleshooting chart. Straight Attachments Angle Attachments Craniotomes Perforator Driver Foot Pedals
EMAX2PLUS
SC2100 SC2101 SC2102
Prior to Use Inspection Visually inspect for any damage to the tube. Visually inspect for bent or broken drive shaft and for any damage to the tube. Visually inspect for bent or broken foot. Visually inspect for overall damage or missing components. Visually inspect for damage to the electrical cord or connector. Visually inspect for damage or cracks to the housing or pedal. Visually inspect for damage to the silicone hose or to the electrical connector. Connect to console and operate. The handpiece should operate smoothly. There is no requirement to operate with attachment or dissection tool. Visually inspect for damage or cracks to the housing. Visually inspect for damage to the electrical power cord. Power the system and inspect for illumination of the LEDs. If there is an irrigation pump present check for proper function.
NOTE: DRIVER Duty Cycle 30 Sec ON, 30 Sec OFF for eight cycles. The recommendations for times of use for the DRIVER attachments have been determined under average load and worst case ambient air temperature of 85°F (29°C).
7
English
System Shutdown
1. There are no special procedures for system shutdown. Depress power switch on rear of console to shut down system. 2. To disconnect power cord from mains, grasp ridged portion of connector between thumb and forefinger of one hand. Gently pull connector away from console. Connector should remove easily. If not, ensure only ridged portion of connector is pulled. Do not pull on smooth part of connector, as connector will not disengage from console.
Additional Information End of Life
Return all equipment for proper disposal.
Recommended Manufacturer Service Interval
It is recommended that the equipment be returned to DePuy Synthes Power Tools at a minimum every 9 months for full product inspection and service.
Console Alerts, Codes, and Displays Console Indicators Code E1, E8 * E2 E3 E4, E5 * E6, E7 E9 * (none)
Description System Fault Handpiece Lock Engaged Handpiece Stall Warning Fault in Handpiece Handpiece Overheat Warning Handpiece Not Recognized Handpiece Set to Reverse
Audible Signal ** none 10 slow beeps 10 fast beeps none 5 second beep none 3 beeps
* If these codes are displayed, return handpiece and console to DePuy Synthes Power Tools for servicing. ** Note: Consoles with software version 3.0 and higher do not generate an “Audible Signal” for Codes E1 – E9. To determine software version press the irrigation rate buttons at the same time on the console touchpad. The console will display two digits. Example Only: “30” means version 3.0. On non-irrigation console models, the buttons can be found in the same location, although they are not marked.
8
Trouble Shooting English
Trouble Shooting Chart Problem Possible Cause Possible Solution Excessive handpiece 1. Faulty internal component. 1. Return attachment to DePuy Synthes noise. Power Tools for service. Lack of power to 1. Plug is not fully inserted/power switch not 1. Verify plugs to wall and back of console are console. turned on. pushed in completely. 2. Outlet is not functional. 2. Verify another piece of electrical equipment can receive power from outlet. Handpiece vibration 1. Faulty internal component. 1. Return to DePuy Synthes Power Tools for or extremely hot. 2. Internal motor overheats due to continuous service. extreme cutting at near stalling conditions. 2. Decrease cutting force, allow motor to cool. 3. Hose may be kinked. 3. Unkink hose (verify it is not being pinched 4. Handpiece out of balance. or clamped to table). 5. Handpiece hose damaged. 4. Return to DePuy Synthes Power Tools for service. 5. Return to DePuy Synthes Power Tools for service. Excessive vibration 1. Dissection tool may be bent. 1. Replace with new dissection tool. of dissection tool. 2. Dissection tool may not be fully seated. 2. Reassemble dissection tool and attachment. 3. Improper attachment and dissection tool 3. Only use correct dissection tool with combination. appropriate attachment. 4. Possible attachment bearing damage. 4. Return to DePuy Synthes Power Tools for service. Attachment is hot. 1. Debris lodged inside attachment. 1. Clean attachment using Anspach 2. Possible bearing damage. Attachment Cleaning Instructions. 2. Return attachment to DePuy Synthes Power Tools for service. Craniotome 1. Excessive force used in operation. 1. Do not use, replace attachment. attachment is bent. Inoperative Foot 1. Selected foot control on face panel does not 1. Press Foot Control button on face panel to Control (LEDs are match foot control in use select other Foot Control illuminated on face 2. System is set in hand control mode (LED 2. Press Foot Control button on face panel panel) light is illuminated) to set it for Foot Control 1 or 2, depending 3. Plug may not be fully inserted which one is in use. 4. Handpiece in “Safe” position or cutter is 3. Verify plug for handpiece and foot control not rotating are fully inserted. Plug will latch in place 5. Defective attachment once fully inserted. 4. Verify cutting burr is completely engaged and handpiece’s knurled knob is in secure position. 5. Clean attachment or replace attachment. Inoperative Hand 1. Defective internal component 1. Return hand control to DePuy Synthes Control 2. Hand Control may not be fully installed. Power Tools for service. 3. Selected Hand Control on face panel not 2. The circumferential groove on handpiece in use. housing will be exposed when the Hand 4. Internal handpiece switch activating Hand Control is fully installed. Control may be damaged. 3. Press Hand Control button on face panel to illuminate Hand Control LED 4. Return handpiece to DePuy Synthes Power Tools for service.
9
English
Technical Specifications for Devices Compliant with IEC-60601-1-2 3rd Edition The device complies with the following standards:
IEC 60601-1:2005: + CORR. 1 (2006) + CORR. 2 (2007), EN 60601-1:2006 +A11:2011, ANSI/AAMI ES60601-1:2005, CAN/CSA-C22.2 No.60601-1:08, (3rd edition) Medical electrical equipment part 1: General requirements for basic safety and essential performance; UL 60601-1:2003 (Revised 2006), IEC 601-1:1988 +A1:1991 + A2:1995; EN60601-1:1990 with A1 and A12:1993, A2:1995 and A13:1996; and CAN/CSA C22.2 No. 601.1-M90, Standard for Medical Electrical Equipment – Part 1 General Requirements for Safety With regard to electrical shock, fire, mechanical hazards, this ETL classified device conforms to AAMI STD ES60601-1, UL STD 60601-1, and is certified to CSA STD C22.2 No.60601-1 and 601.1 This device complies with applicable EEC directives. Medical Device Directive 93/42/EEC as amended by 2007/47/EC. Machinery Directive 2006/46/EC.
Temperature Relative Humidity Atmospheric Pressure
Environmental Conditions Operating: 18°-30°C (65°-85°F) Transportation and Storage: -29° – +50°C (-20° - +120°F) Operating: 30% to 70% Transportation and Storage: 10% to 90% Operating: 0.7–1.06bar Transportation and Storage: Not applicable
Console (SC2100, SC2101, and SC2102) Specifications Primary: 100-240VAC, 50/60 Hz, 250 VA Class I: Protective Earth Fluid Ingress Protection: IPX0 Type B: Applied Part, Continuous Operation Foot Pedal (E-FP, E-FP-DIR, E-FP-DIR/IRR) Specifications Size: 26.7 cm x 16.5 cm x 14.7 cm (10.5 in x 6.5 in x 8.5 in) Weight: 2.0 kg (4.41 lbs) Cord: 3.66 m (12 ft) in length Fluid Ingress Protection: IPX8
10
Table 1: Emission
Guidance and manufacturer’s declaration – electromagnetic emissions The Anspach High Speed Electric System is intended for use in the electromagnetic environment specified below. The customer or the user of the Anspach High Speed Electric System should assure that it is used in such an environment. Emission test Compliance Electromagnetic environment – guidance The Anspach High Speed Electric System uses RF energy only RF emissions for its internal function. Therefore, its RF emissions are very low Group 1 and are not likely to cause any interference in nearby electronic CISPR 11 equipment. RF emissions. RF emissions The Anspach High Speed Electric System is suitable for use Class A in all establishments, other than domestic establishments and CISPR 11 those directly connected to the public low-voltage power supply Harmonic emissions network that supplies buildings used for domestic purposes. Class A IEC 61000-3-2 Voltage fluctuations / flicker emissions Complies IEC 61000-3-3
English
The Anspach High Speed Electric System is composed of the eMax 2 Plus Handpiece model: EMAX2PLUS; Electric Consoles models SC2100, SC2101, & SC2102; Foot Control models E-FP, E-FP-DIR, E-FP-DIR/IRR, EPLUS-FP, EPLUSFPNS; Hand Controls EMAX2-HC and E-HC.
Table 2: Immunity (all devices) Guidance and manufacturer’s declaration – electromagnetic immunity The Anspach High Speed Electric System is intended for use in the electromagnetic environment specified below. The customer or the user of Anspach High Speed Electric System should assure that it is used in such an environment. Electromagnetic environment – Immunity test standard IEC 60601 test level Compliance level guidance Floors should be wood, concrete or Electrostatic discharge ±6 kV contact ±6 kV contact ceramic tile. If floors are covered with (ESD) synthetic material, the relative humidity ±8 kV air ±8 kV air IEC 61000-4-2 should be at least 30% ±2 kV for power supply ±2 kV for power supply Mains power quality should be that Electrical fast transient / lines lines of a typical commercial or hospital burst environment. ±1 kV for input/output ±1 kV for input/output IEC 61000-4-4 lines lines Mains power quality should be that Surge ±1 kV line to line ±1 kV line to line of a typical commercial or hospital IEC 61000-4-5 ±2 kV line to earth ±2 kV line to earth environment. <5% UT <5% UT Mains power quality should be that (>95% dip in UT) (>95% dip in UT) of a typical commercial or hospital for 0.5 cycle) for 0.5 cycle) environment. Voltage dips, short interruptions and voltage variations on power supply lines IEC 61000-4-11
40% UT (60% dip in UT) for 5 cycle)
40% UT (60% dip in UT) for 5 cycle)
70% UT (30% dip in UT) for 25 cycle)
70% UT (30% dip in UT) for 25 cycle)
<5% UT <5% UT (>95% dip in UT) (>95% dip in UT) for 5 sec) for 5 sec) Note: UT is the a.c. mains voltage prior to application of the test level. Power frequency (50/60 Hz) 3 A/m 3 A/m magnetic field IEC 61000-4-8
Power frequency magnetic fields should be at levels characteristic of a typical location in a typical commercial or hospital environment.
11
English Table 3: Immunity (not life-supporting devices) Guidance and manufacturer’s declaration – electromagnetic immunity The Anspach High Speed Electric System is intended for use in the electromagnetic environment specified below. The customer or the user of the Anspach High Speed Electric System should assure that it is used in such an environment. Immunity test standard IEC 60601 test level Compliance level Electromagnetic environment – guidance Conducted RF Portable and mobile RF communications 3 Vrms 3 Vrms equipment should be used no closer 150 kHz to 80 MHz IEC 61000-4-6 to any part of the Anspach High Speed Electric System, including cables, than the recommended separation distance calculated from the equation applicable to the frequency of the transmitter. Recommended separation distance d = 1.2
Radiated RF IEC 61000-4-3
3 V/m 80 MHz to 2.5 GHz
3 V/m
d = 1.2
80 MHz to 800 MHz
d = 2.3
800 MHz to 2.7 GHz
Where P is the maximum output power rating of the transmitter in watts (W) according to the transmitter manufacturer and d is the recommended separation distance in metres (m). Field strengths from fixed RF transmitters, as determined by an electromagnetic site survey,a should be less than the compliance level in each frequency range.b Interference may occur in the vicinity of equipment marked with the following symbol:
Note 1: At 80 MHz and 800 MHz, the higher frequency range applies. Note 2: These guidelines may not apply in all situations. Electromagnetic propagation is affected by absorption and reflection from structures, objects and people. a Field strengths from fixed transmitters, such as base stations for radio (cellular/cordless) telephones and land mobile radios, amateur radio, AM and FM radio broadcast and TV broadcast cannot be predicted theoretically with accuracy. To assess the electromagnetic environment due to fixed RF transmitters, an electromagnetic site survey should be considered. If the measured field strength in the location in which the Anspach High Speed Electric System s used exceeds the applicable RF compliance level above, the Anspach High Speed Electric System should be observed to verify normal operation. If abnormal performance is observed, additional measures may be necessary, such as re-orienting or relocating the device containing the Anspach High Speed Electric System. b Over the frequency range 150 kHz to 80 MHz, field strengths should be less than 3 V/m.
12
Table 4: Recommended separation distances (not life-supporting devices)
English
Recommended separation distances between portable and mobile RF communications equipment and the Anspach High Speed Electric System The Anspach High Speed Electric System is intended for use in the electromagnetic environment in which radiated RF disturbances are controlled. The customer or the user of the Anspach High Speed Electric System can help prevent electromagnetic interference by maintaining a minimum distance between portable and mobile RF communications equipment (transmitters) and the Anspach High Speed Electric System as recommended below, according to the maximum output power of the communication equipment. Separation distance according to frequency of transmitter Rated maximum output 150 kHz to 80 MHz to 800 MHz to power of transmitter 80 MHz 800 MHz 2.5 GHz W d = 1.2 d = 1.2 d = 2.3 0.01 12 cm 12 cm 23 cm 0.1 38 cm 38 cm 73 cm 1 1.2 m 1.2 m 2.3 m 10 3.8 m 3.8 m 7.3 m 100 12 m 12 m 23 m For transmitters rated at a maximum output power not listed above, the recommended separation distance d in metres (m) can be estimated using the equation applicable to the frequency of the transmitter, where P is the maximum output power rating of the transmitter in watts (W) according to the transmitter manufacturer. Note 1: At 80 MHz and 800 MHz, the separation distance for the higher frequency range applies. Note 2: These guidelines may not apply in all situations. Electromagnetic propagation is affected by absorption and reflection from structures, objects and people.
13
English
Technical Specifications for Devices Compliant with IEC-60601-1-2 4th Edition The device complies with the following standards:
AAMI ES60601-1 Issued: 2006/03/09 Medical Electrical Equipment - Part 1: General Requirements for Basic Safety and Essential Performance, Amendment 1 – 2012 CSA C22.2#60601-1 Issued: 2014/03/01 Ed: 3 Medical Electrical Equipment - Part 1: General Requirements for Basic Safety and Essential Performance IEC 60601-1-6 Issued: 2013/10/29 Ed: 3 Medical Electrical Equipment - Part 1-6: General Requirements for Basic Safety and Essential Performance - Collateral Standard: Usability; Amendment 1 IEC 60601-1: 2005 + CORR. 1:2006 + CORR. 2:2007 + AM1:2012 (or IEC 60601-1: 2012 reprint) EN 60601-1: 2005 + A1:2013, IEC 60601-1 / EN 60601-1, Medical electrical equipment Part 1: General requirements for basic safety and essential performance (CB Scheme) IEC 62366 Medical devices – Application of usability engineering to medical devices IEC 62366: 2007 (First Edition) + A1: 2014 (CB Scheme) IEC 60601-1-6:2010 (Third Edition) + A1:2013 for use in conjunction with IEC62366:2007 (First Edition) + A1:2014 and IEC 60601-1:2005 (Third Edition) + Corr.1 (2006) + Corr.2 (2007) + A1: 2012 or equivalent consolidated version IEC 60601-1:2012 (Ad.3.1), Medical electrical equipment Part 1-6 General requirements for safety - Collateral Standard: Usability IEC 60601-1-2:2014 (Edition 4) Collateral Standard: Electromagnetic Compatibility- Medical Electrical Equipment. This device complies with applicable EEC directives. Medical Device Directive 93/42/EEC as amended by 2007/47/EC. Machinery Directive 2006/46/EC.
Temperature Relative Humidity Atmospheric Pressure
Environmental Conditions Operating: 18°-30°C (65°-85°F) Transportation and Storage: -29° – +50°C (-20° - +120°F) Operating: 30% to 70% Transportation and Storage: 10% to 90% Operating: 0.7–1.06bar Transportation and Storage: Not applicable
Console (SC2100, SC2101, and SC2102) Specifications Primary: 100-240VAC, 50/60 Hz, 250 VA Class I: Protective Earth Fluid Ingress Protection: IPX0 Type B: Applied Part, Continuous Operation Foot Pedal (E-FP, E-FP-DIR, E-FP-DIR/IRR) Specifications Size: 26.7 cm x 16.5 cm x 14.7 cm (10.5 in x 6.5 in x 8.5 in) Weight: 2.0 kg (4.41 lbs) Cord: 3.66 m (12 ft) in length Fluid Ingress Protection: IPX8
14
Table 1: Emission
Guidance and manufacturer’s declaration – electromagnetic emissions The Anspach High Speed Electric System is intended for use in the electromagnetic environment specified below. The customer or the user of the Anspach High Speed Electric System should assure that it is used in such an environment. Emission test Compliance Electromagnetic environment – guidance The Anspach High Speed Electric System uses RF energy only RF emissions for its internal function. Therefore, its RF emissions are very low Group 1 and are not likely to cause any interference in nearby electronic CISPR 11 equipment. RF emissions. RF emissions The Anspach High Speed Electric System is suitable for use Class A in all establishments, other than domestic establishments and CISPR 11 those directly connected to the public low-voltage power supply Harmonic emissions network that supplies buildings used for domestic purposes. Class A IEC 61000-3-2 Voltage fluctuations / flicker emissions Complies IEC 61000-3-3
English
The Anspach High Speed Electric System is composed of the eMax 2 Plus Handpiece model: EMAX2PLUS; Electric Consoles models SC2100, SC2101, & SC2102; Foot Control models E-FP, E-FP-DIR, E-FP-DIR/IRR, EPLUS-FP, EPLUS-FP-NS; Hand Controls EMAX2-HC and E-HC.
Table 2: Immunity (all devices) Guidance and manufacturer’s declaration – electromagnetic immunity The Anspach High Speed Electric System is intended for use in the electromagnetic environment specified below. The customer or the user of Anspach High Speed Electric System should assure that it is used in such an environment. Electromagnetic environment Immunity test standard IEC 60601 test level Compliance level guidance Floors should be wood, concrete or Electrostatic discharge ±8 kV contact ±8 kV contact ceramic tile. If floors are covered with (ESD) synthetic material, the relative humidity ±15 kV air ±15 kV air IEC 61000-4-2 should be at least 30% ±2 kV for AC lines ±2 kV for AC lines Mains power quality should be that Electrical fast transient / of a typical commercial or hospital ±1 kV for I/O lines ±1 kV for I/O lines burst environment. 100 kHz Pulse Repetition 100 kHz Pulse Repetition IEC 61000-4-4 Frequency Frequency Mains power quality should be that Surge ±0.5 kV line to line ±0.5, 1 kV line to line of a typical commercial or hospital IEC 61000-4-5 ±0.5, 1, 2 kV line to earth ±0.5, 1, 2 kV line to earth environment. 0% UT (100% dip in UT) 0% UT (100% dip in UT) Mains power quality should be that for 0.5 periods at 0°, 45°, for 0.5 periods at 0°, 45°, of a typical commercial or hospital 90°,135°, 180°, 225°, 90°,135°, 180°, 225°, environment. 270°, 315° 270°, 315° If the user of the EMAX2PLUS Voltage dips, short 0% UT (100% dip in UT) 0% UT (100% dip in UT) system requires continued operation interruptions and voltage for 1 period for 1 period during power mains interruptions, it variations on power is recommended that the system be 70% UT (30% dip in UT) 70% UT (30% dip in UT) supply lines powered from an uninterruptible power for 25 periods (50 Hz) for 25 periods (50 Hz) supply or a battery. IEC 61000-4-11 30 periods (60 Hz) 30 periods (60 Hz) Interruptions 0% UT Interruptions 0% UT (100% dip in UT) for (100% dip in UT) for 250 periods (50 Hz) 250 periods (50 Hz) 320 periods (60 Hz) 320 periods (60 Hz) Note: UT is the AC mains voltage prior to application of the test level. Power frequency (50/60 Hz) 30 A/m 30 A/m magnetic field IEC 61000-4-8
Power frequency magnetic fields should be at levels characteristic of a typical location in a typical commercial or hospital environment.
15
English Table 3: Immunity (not life-supporting devices) Guidance and manufacturer’s declaration – electromagnetic immunity The Anspach High Speed Electric System is intended for use in the electromagnetic environment specified below. The customer or the user of the Anspach High Speed Electric System should assure that it is used in such an environment. Immunity test standard IEC 60601 test level Compliance level Electromagnetic environment – guidance 3 Vrms 3 Vrms Portable and mobile RF communications Conducted RF 150 kHz to 80 MHz 150 kHz to 80 MHz equipment should be used no closer to any part of the Anspach High Speed IEC 61000-4-6 6 Vrms in ISM bands 6 Vrms in ISM bands Electric System, including cables, than the 150 kHz to 80 MHz 150 kHz to 80 MHz recommended separation distance calculated from the equation applicable to the frequency of the transmitter. Recommended separation distance d = 1.2
Radiated RF IEC 61000-4-3
3 V/m 80 MHz to 2.5 GHz
3 V/m 80 MHz to 2.5 GHz
80% at 1 kHz (AM modulation)
80% at 1 kHz (AM modulation)
d = 1.2
80 MHz to 800 MHz
d = 2.3
800 MHz to 2.7 GHz
Where P is the maximum output power rating of the transmitter in watts (W) according to the transmitter manufacturer and d is the recommended separation distance in meters (m). Field strengths from fixed RF transmitters, as determined by an electromagnetic site survey,a should be less than the compliance level in each frequency range.b Interference may occur in the vicinity of equipment marked with the following symbol:
Note 1: At 80 MHz and 800 MHz, the higher frequency range applies. Note 2: These guidelines may not apply in all situations. Electromagnetic propagation is affected by absorption and reflection from structures, objects and people. a Field strengths from fixed transmitters, such as base stations for radio (cellular/cordless) telephones and land mobile radios, amateur radio, AM and FM radio broadcast and TV broadcast cannot be predicted theoretically with accuracy. To assess the electromagnetic environment due to fixed RF transmitters, an electromagnetic site survey should be considered. If the measured field strength in the location in which the Anspach High Speed Electric System is used exceeds the applicable RF compliance level above, the Anspach High Speed Electric System should be observed to verify normal operation. If abnormal performance is observed, additional measures may be necessary, such as re-orienting or relocating the device containing the Anspach High Speed Electric System. b Over the frequency range 150 kHz to 80 MHz, field strengths should be less than 3 V/m.
16
385
450 710 745 780
704–787
LTE Band 13, 17
Pulse modulationb 217 Hz
0.2
0.3
9
800–960
GSM 800/900; TETRA 800; iDEN 820; CDMA 850; LTE Band 5
Pulse modulationb 18 Hz
2
0.3
28
1,700–1,990
GSM 1800; CDMA 1900; GSM 1900; DECT; LTE Band 1, 3, 4, 25; UMTS
Pulse modulationb 217 Hz
2
0.3
28
2,400–2,570
Bluetooth; WLAN 802.11b/g/n; RFID 2450; LTE Band 7
Pulse modulationb 217 Hz
2
0.3
28
810 870 930 1,720 1,845 1,970
2,450
English
EMAX 2PLUS System Enclosure Port Immunity to RF wireless communications equipment (IEC 61000-4-3) Servicea Modulationb Maximum Distance IMMUNITY power (m) TEST LEVEL (W) (V/m) Pulse b 380–390 TETRA 400 modulation 1.8 0.3 27 18 Hz FMc ±5 kHz GMRS 460; 430–470 2 0.3 28 deviation FRS 460 1 kHz sine
Test frequency Banda (MHz) (MHz)
5,240 Pulse WLAN 5,500 5,100–5,800 modulationb 0.2 0.3 9 802.11a/n 217 Hz 5,785 Note: If necessary to achieve the IMMUNITY TEST LEVEL, the distance between the transmitting antenna and the EMAX2PLUS System may be reduced to 1 m. The 1 m test distance is permitted by IEC 61000-4-3. a For some services, only the uplink frequencies are included. b The carrier shall be modulated using a 50% duty cycle square wave signal. c As an alternative to FM modulation, 50% pulse modulation at 18 Hz may be used because while it does not represent actual modulation, it would be worst case.
17
English Table 4: Recommended separation distances (not life-supporting devices) Recommended separation distances between portable and mobile RF communications equipment and the Anspach High Speed Electric System The Anspach High Speed Electric System is intended for use in the electromagnetic environment in which radiated RF disturbances are controlled. The customer or the user of the Anspach High Speed Electric System can help prevent electromagnetic interference by maintaining a minimum distance between portable and mobile RF communications equipment (transmitters) and the Anspach High Speed Electric System as recommended below, according to the maximum output power of the communication equipment. Separation distance according to frequency of transmitter Rated maximum output 150 kHz to 80 MHz to 800 MHz to power of transmitter 80 MHz 800 MHz 2.5 GHz W d = 1.2 d = 1.2 d = 2.3 0.01 12 cm 12 cm 23 cm 0.1 38 cm 38 cm 73 cm 1 1.2 m 1.2 m 2.3 m 10 3.8 m 3.8 m 7.3 m 100 12 m 12 m 23 m For transmitters rated at a maximum output power not listed above, the recommended separation distance d in metres (m) can be estimated using the equation applicable to the frequency of the transmitter, where P is the maximum output power rating of the transmitter in watts (W) according to the transmitter manufacturer. Note 1: At 80 MHz and 800 MHz, the separation distance for the higher frequency range applies. Note 2: These guidelines may not apply in all situations. Electromagnetic propagation is affected by absorption and reflection from structures, objects and people.
18
Manufacturer
The Anspach Effort, Inc.
4500 Riverside Drive Palm Beach Gardens, FL 33410 USA Tel: (800) 327 6887 / +1 561 627 1080 Fax: (800) 327 6661 / +1 561 625 9110 Web: www.depuysynthes.com Email: infoPowerTools@DPYUS.jnj.com
Synthes GmbH
Eimattstrasse 3 4436 Oberdorf Switzerland Tel: +41 61 965 61 11 Fax: +41 61 965 66 00
18-0085 Rev G 11/19 For patent information go to http://www.depuysynthes.com/patentmarking © DePuy Synthes 2019. All rights reserved.