ARTISTIC HEALTHCARE SEATING PTY LTD
Treatment chairs
THOMPSON MaxiLift 2 TREATMENT CHAIR Instructions for Safe Use 2008
Instructions for Safe Use 2008
12 Pages
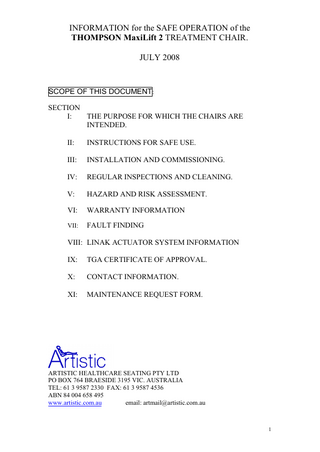
Preview
Page 1
INFORMATION for the SAFE OPERATION of the THOMPSON MaxiLift 2 TREATMENT CHAIR. JULY 2008
SCOPE OF THIS DOCUMENT: SECTION I: THE PURPOSE FOR WHICH THE CHAIRS ARE INTENDED. II:
INSTRUCTIONS FOR SAFE USE.
III:
INSTALLATION AND COMMISSIONING.
IV:
REGULAR INSPECTIONS AND CLEANING.
V:
HAZARD AND RISK ASSESSMENT.
VI:
WARRANTY INFORMATION
VII:
FAULT FINDING
VIII: LINAK ACTUATOR SYSTEM INFORMATION IX:
TGA CERTIFICATE OF APPROVAL.
X:
CONTACT INFORMATION.
XI:
MAINTENANCE REQUEST FORM.
ARTISTIC HEALTHCARE SEATING PTY LTD PO BOX 764 BRAESIDE 3195 VIC. AUSTRALIA TEL: 61 3 9587 2330 FAX: 61 3 9587 4536 ABN 84 004 658 495 www.artistic.com.au email: artmail@artistic.com.au
1
I:
THE PURPOSE FOR WHICH THE CHAIRS ARE INTENDED.
The THOMPSON MaxiLift 2 Treatment chair has been designed and manufactured with the intention that it be used for the treatment of Renal Dialysis patients, or similar treatments requiring comfortable and safe seating, and is a further development of the MaxiLift Model. It is presumed that the patient will at all times be under the supervision of trained staff who will have been instructed in the safe operation of the chair, and that they will not allow the chair to be used in a manner for which it was not intended. The chair is designed so that the occupant will be seated in a typical seated position with the hips moved back so that their back will be against the backrest and the legs outstretched and supported by the seat and legrest. The weight of the occupant must not exceed 180kg. The Bariatric must not exceed 250kg. Although the chair is fitted with casters, these are intended to aid cleaning and positioning of the chair within the room, and are not to allow the chair to be used as a transporter. If the chair has been fitted with dual hand controls, it is intended that the programmable unit is for the use of the staff only, and the dual recline unit be used by the patient. This safety initiative is to ensure that the chair is not raised or lowered, or reclined onto an obstruction by the occupant, and presumes the staff member will be better positioned to ensure the area surrounding the chair is free from obstruction. It is the staff member’s responsibility to ensure that prior to operating the chair that the surrounding walls or equipment will not come into contact with nor obstruct the free movement of the chair. It is the staff members’ responsibility to ensure the patient is briefed on the safe operation of the chair, and if he or she believes the patient cannot safely operate the chair, removes the patient hand control from reach. In an emergency, the chair can be lowered to the Trendelenburg position where CPR may be performed. It is the staff members’ responsibility to ensure that the chair is in the correct position for CPR and that the resuscitation method used is in line with Hospital policy. In addition, staff should ensure to the Hospitals satisfaction that the chair is suitable for those resuscitation methods. In general, no responsibility or liability can be accepted by the manufacturer for failure to adhere to these and the subsequent guidelines and instructions.
2
II:
INSTRUCTIONS FOR SAFE USE.
1. Ensure the brakes are locked on and positioned to give minimum interference to staff. 2 The seat height may be raised to give maximum comfort whilst in the seated position and should be elevated to minimize bending for staff. It is normal to cannulate whilst in this position. 3. The gas spring-assisted armrests are positioned by loosening the knob and allowing the armrest to comfortably support the patients’ arm. Retighten the knob. 4. If fitted, loosen the underneath knob to swivel the armrest out and retighten. 5. If the patient has an individual hand control this allows operation of the seat/footrest and backrest position. Allow the patient to position themselves for maximum comfort, and to regularly alter this position. 6. For safety, only nursing staff can operate the Hi/Lo function and this control should be kept out of reach of the patient at the rear of the chair. 7. Unless set differently, in an EMERGENCY, press Memory position #1 and the backrest and legrest will go to their flattest position and the chair will lower until the backrest is supported by the rear support bar. CPR may be performed in this position. NOTE: It is not intended that these instructions override any Hospital instructions for emergency treatment. 8. The armrests may be lowered flat to the seat level to allow side transfer. Raise or lower the seat height to prevent unnecessary bending or lifting. 9. To allow the patient to rise from the chair, lower the chair and return it to the upright position. (PRESS MEMORY POSITION #2) 10. If Memory Position #3 is available, this will have been preset to a position suitable for Blood Collection for Red Cross or similar, or for ICU to a position suitable for safe side transfer. 11. To reprogram the preset positions: Step 1: Step 2:
Step 3:
Remove the velcroed cover from the Nurse Hand control (large unit). If reprogramming Position #1, drive the chair to the CPR position, (fully down, laid back and reclined so that the backrest is resting on the support bar), briefly press the S (for store) button and then button #1. You may hear a confirming ‘beep’. Repeat these steps as required for other positions. Replace the cover.
12: The power cord should be left in the power supply and switched on. The backup batteries will recharge automatically and slow to trickle charge when full.
3
III:
INSTALLATION AND COMMISSIONING.
All chairs can be installed by the manufacturer or by staff approved by the manufacturer or its agent. Generally the chairs are positioned by the unit staff, but care should be taken that when positioned no part of the chair will come into contact with any equipment or structures, particularly during emergency procedures. Installation would normally comprise positioning the chair, removing any temporary ties or packaging which will be advised by the manufacturer, plugging the power cord to an approved 240 V supply and taking the chair through its complete range of movements. The power cord should be left in the power supply and switched on. The backup batteries will recharge automatically and slow to trickle charge when full. The chair can be operated in the normal manner immediately after commissioning. When moving the chairs within the institution, always leave the temporary armrest covers on until the chairs are in their intended operating position. No claims for transport damage will be accepted 7 days after delivery date.
4
IV:
REGULAR INSPECTIONS AND CLEANING.
A regular inspection at least monthly should be made of each chair to ensure that each chair operates safely and as intended by the manufacturer. Any faults or warranty claims should be reported immediately to the manufacturer or its agent. No liability can be accepted by the manufacturer if the chair is operated whilst faulty and further damage occurs. Cleaning should conform to the standards set by the Hospital. All materials used in the manufacture of the chairs have been found to be suitable to be cleaned with standard Hospital cleaning products, however to ensure suitability, a test should be carried out on an inconspicuous piece of material, or a sample provided by the manufacturer. The following should be used as a guideline only and no claims will be accepted for damage or otherwise from following these guidelines: RECOMMENDED CLEANING PROCEDURE FOR DIALYSIS CHAIRS The following recommended procedure should only be used if it generally conforms to Infection Control guidelines of the Hospital. STEP 1
IF REQUIRED, REMOVE THE SEAT AND BACKREST BY GENTLY PULLING OR LIFTING.
STEP 2:
REMOVE AS MUCH OF THE SPILT LIQUID AS POSSIBLE USING A SPONGE TYPE MATERIAL WITH A DABBING MOTION.
STEP 3:
POUR ON MILTON SOLUTION 1% WATER VOLUME SODIUM HYPO-CHLORIDE AND WIPE WITH A MOPPING ACTION.
STEP 4:
USE A GENERAL PURPOSE DETERGENT CLEANER WITH WARM WATER ON A CLOTH FOR A FINAL CLEAN.
Unless otherwise stated, upholstery fabrics used on these chairs conform to the following Australian Standards: Flame Retardant tested to AS1530.3 Cigarette Burn test AS 37441.1 UV stabilised AS1441.1
5
V:
HAZARD AND RISK ASSESSMENT.
Identifiable Hazard
Component
Control
A: Electric Shock
Power Supply to Control box cord
Double insulation and suggest Earth Leakage switch in Ward.
B: Crushing
Chair body when lowered by staff member.
Staff to ensure no person allows any item to be placed under the chair at any time.
Chair body when lowered by patient
Staff hand control to be placed behind chair out of patients’ reach.
.
6
VI: ARTISTIC HEALTHCARE SEATING PTY LTD WARRANTY and CONDITIONS of SALE 2004 1: Artistic Healthcare Seating Pty Ltd will repair or replace, at its discretion, any component or assembly, (except those items listed in #4), which exhibits failure or undue wear when subjected to normal use, and used in the manner which was intended at the time of sale. 2:
The Warranty is limited to the original purchaser at the original delivery address.
3: When sold by a Reseller, this Warranty covers costs at the premises of the Reseller, and if required in approved situations, transport costs from the Reseller to and from Melbourne, or to some other party. 4:
Items Not Covered by Artistic Warranty.
LINAK Actuator systems are guaranteed for 1 year from Date of Purchase on a Return to Base arrangement. (ie parts only) Casters from various manufacturers for 12 months, parts or replacement only. Upholstery vinyl and fabrics/leather: Individual suppliers warranty. All 3rd Party components are covered only by individual warranties. 5:
Artistic products Warranty periods: Thompson Treatment chairs:
6:
1 year.
Artistic chairs are not covered by Warranty if used outdoors.
7: The use of unauthorised labour will void the Warranty. Contact Artistic prior to commencing work for approval. 8. If there are visible signs of fault and it is possible to swap components ie: swap the seat and back motor connections and by a process of elimination the faulty component can be determined. 9. Take note of the Serial Number of the chair. On lift chairs it is on the right hand side on the base frame and on other Thompson’s is on the right hand side on the Backrest frame. 10.Please fill in the attached Maintenance Form and fax to us with all information, together with an Order number. This will allow us to promptly process the repair if not covered by Warranty.
7
VII: FAULT FINDING In the event the chair fails to operate correctly please take the following steps prior to contacting Artistic or its Agent. 1. Check the Power Point is active. 2. Check that the chair is plugged in and switched on correctly. 3. If the above are OK:
a. Check the Green Light is glowing on top of the Control Box. b. If necessary remove the Perspex cover (held on be Velcro) or the steel cover (bolted on) and check light.
4. If the chair has batteries fitted, (MaxiLift and PowerLift), ensure they have been on charge at least overnight. 5. Check that the connections into the Control Box have not been dislodged. a. with single or dual motor systems just push the plugs in. b. with systems with more than 2 motors remove the retaining clip before checking and replace it afterwards. 6. Ensure there are no nicks or cuts in the Hand Control or actuator cables. 7. Determine what is not operating: a. the Seat motor (vertically mounted behind the footrest or horizontally mounted under the seat). b. The Back motor (mounted behind the backrest). c. The Lift motor ( mounted under the base) OR the Column (silver vertical aluminium post). NOTE: if the backrest is Manually operated with a lever and Gas strut, check to see if it is holding the Backrest up, or not returning it to an upright position. 8. If there are visible signs of fault and it is possible to swap components ie: swap the seat and back motor connections and by a process of elimination the faulty component can be determined. 9. Take note of the Serial Number of the chair. On lift chairs it is on the right hand side on the base frame and on other Thompson’s is on the right hand side on the Backrest frame. 10.Please fill in the attached Maintenance Form and fax to us with all information, together with an Order number. This will allow us to promptly process the repair if not covered by Warranty.
8
IX:
CONTACT INFORMATION
DESIGNER and MANUFACTURER: ARTISTIC HEALTHCARE SEATING PTY LTD, 15 CENTURY Drive, PO BOX 764 BRAESIDE VICTORIA 3195. AUSTRALIA TEL: 1300 889 330 FAX: 61 3 9587 4536 e-mail: artmail@artistic.com.au ABN: 84 004 498 695
12