Atherton
PR-MN-CU-009 User Manual (PCB Model) Rev 1
User Manual
22 Pages
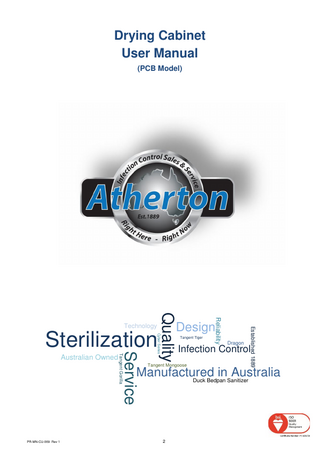
Preview
Page 1
Drying Cabinet User Manual (PCB Model)
Design Tangent Tiger
Dragon
Established 1889
Reliability
Tangent Gorilla
PR-MN-CU-009 Rev 1
Service
Australian Owned
Cyber Series
Sterilization
Quality
Technology
Infection Control
Tangent Mongoose
Manufactured in Australia Duck Bedpan Sanitizer
2
PR-MN-CU-009 Rev 1
3
This manual contains important information on the proper use and maintenance of this equipment All operators and Departmental Heads are urged to carefully read this manual and become familiar with the warnings, cautions and instructions contained within it. A thorough Scheduled Maintenance Programme is essential for safe and reliable sterilization. You are urged to contact the Atherton SERVICE MANAGER in your state to arrange a maintenance programme for your equipment. Due to the continuous programme of research and development conducted by Atherton, all design details are subject to change without notice. IMPORTANT: For warranty to be valid, complete, sign, and return the "Installation and Commissioning" form to: A. E. Atherton & Sons Pty. Ltd. P.O. Box 116, Northcote, Victoria, Australia, 3070.
WARNING Must be followed carefully to avoid endangering human life and/or damage to equipment.
CAUTION Should be followed to ensure proper operation of equipment.
NOTE & IMPORTANT Contains important information and useful tips on operation of equipment
Atherton Sales and Service Victoria, South Australia, Northern Territory, Western Australia, Tasmania, ACT & New South Wales
Ph: 1300 580 870 Atherton Head Office and Sterilizer Manufacturing Facility 364 Darebin Road, Thornbury, Victoria, Australia Queensland Contact
Sterilizing Equipment Sales & Service Ph: 07 3849 1077
PR-MN-CU-009 Rev 1
4
TABLE OF CONTENTS
Your Warranty Cover
Page 5
Section 1
Installation
Page 6
Section 2
Operating Instructions
Page 12
Section 3
Maintenance
Page 14
Section 4
Troubleshooting
Page 15
Section 5
Wiring diagrams
Page 16 & 17
Section 6
Replacement parts
Page 18 & 19
Section 7
Test Report
Page 20
Section 8
Installation and Commissioning
Page 21
PR-MN-CU-009 Rev 1
5
YOUR WARRANTY COVER All equipment manufactured and work performed by the Company is warranted to be of good material throughout, and of good careful workmanship. The Company undertakes to correct and make good any defect or defects which may develop under normal and proper use within the warranty period, which are due to workmanship, provided that the Company is notified immediately after the defect is discovered. The warranty period is twelve months and shall be from the date delivery is made, or notification to the client that delivery can be made. The Company’s liability is limited as provided in these conditions and does not extend to consequential damage, either direct or indirect, that may be caused by any malfunction of the equipment, or to any expense for repair or replacement otherwise paid or incurred without the authority of the Company. The Company does not accept liability or responsibility for the defects or depreciation caused by wear and tear, accidents, lightning, corrosion, neglect, misuse, incorrect installation not carried out by the Company’s personnel or nominees of the Company, incorrectly maintained, incorrect operation or other abnormal conditions. Should field service be required, costs incurred in traveling to and from location of equipment, including traveling time, transportation and accommodati9on costs, and freight charges of sending replacement parts to and from a nominated Atherton office, are borne by the buyer. All field service will be carried out during normal working hours. If warranty service is requested outside normal working hours such work will be charged at the ruling overtime rates. Requests for replacement parts or components under warranty must be accompanied with a purchase order for the replacement part or component at the ruling spare parts price cost. The defective part or component must be retuned to the Atherton office handling the warranty claim complete with details of serial number, catalogue or model number or some means of verifying the unit and its delivery date. After receipt and inspection of the defective part or component the Company shall decide at its sole discretion whether a warranty claim applies. If the claim is granted a credit will be issued for the replacement amount previously charged. Material and equipment not manufactured by the Company are sold under such warranty only as the makers give the Company and the Company is able without legal expense to enforce, but are not guaranteed by the Company in any way. The warranty and warranty period does not cover such articles which are considered to be expendable, including but not limited to, gaskets, filters, bellows, globes, gauges, electrical components.
PR-MN-CU-009 Rev 1
6
INSTALLATION Details of overall dimensions and service requirements will be found under the technical details of pages 7, 8, 9 and 10.
INSTALLATION CHECK LIST
1.
Electrical isolating switch for maintenance purposes to be installed near the equipment (by others).
2.
After removing cabinet from pallet, tilt back or lay cabinet down. Screw adjustable legs into threaded plates. (See diagram 1.1)
3.
Plug in power lead
4.
On pass through models and built-in models, place cabinet in opening.
4.1
Check that cabinet is level
5.
Fit 6 x grid shelves to RDC cabinet. Fit 3 x grid shelves to SDC cabinet. Fit 4 x grid shelves to MDC cabinet.
6.
The RDC and MDC cabinet should be positioned to allow air to flow freely through the air intake filter. (See diagram 1.2)
7.
The location of the exhaust duct should be considered if the exhaust air is to be ducted away. (See diagram 1.2)
PR-MN-CU-009 Rev 1
7
h At
e
rto
n
Atherton
PR-MN-CU-009 Rev 1
8
MODEL RDC, MDC, RDCD, MDCD SUMMARY OF FEATURES This cabinet is supplied with the following: 1.
Glass door
2.
Touch pad with electronic timer and temperature controller (adjustable)
3.
On/off switch
4.
Operator manual
5.
Six half shelves (Model RDC, RDCD)
6.
Thirty nozzles (Model RDC, RDCD)
7.
Four full shelves (Model MDC, MDCD)
8.
Over temperature automatically set 2°C above set temperature.
TECHNICAL DATA Model RDC, MDC, RDCD, MDCD Overall size: 1675H x 880W x 670D Internal size: 1250H x 700W x 605D Power requirement: 10amp, GPO
EXHAUST VENT Size: Diameter 127mm OD direct to atmosphere (can be connected to duct)
PR-MN-CU-009 Rev 1
9
RDCD MDCD typical view
PR-MN-CU-009 Rev 1
10
RDC MDC Typical view
PR-MN-CU-009 Rev 1
11
MODEL SDC SUMMARY OF FEATURES This cabinet is supplied with the following: 1.
Glass door
2.
Temperature thermostat (adjustable)
3.
On/Off switch
4.
Operator manual
5.
Two shelves
6.
Adjustable overtemperature thermostat (Factory set at 65°C)
TECHNICAL DATA Model SDC Overall size: 545H x 470W x 310D Internal size: 450H x 290W x 250D Power requirement: 10 amp, GPO
AIR VENT Size: 2 x Ø25 direct to atmosphere
Rev 4.0 6/03 PR-MN-CU-009 Rev 1
12
OPERATING INSTRUCTIONS – RDC/MDC
Step 1.
Load articles onto shelves allowing space between articles for air circulation. If unit is fitted with tube nozzles and rails, hang tubes on appropriate mountings and close door.
Step 2.
Press POWER ON. Power on indicator and temperature indicator will illuminate. Digital display will display 30ºC.
Step 3.
Set desired temperature (normally 65ºC) by using up/down arrows on touch pad.
Step 4.
Should timer operation be required, press TIME push button. Time indicator will illuminate and digital display will display 000. Set desired time (00-999) minutes by using up/down arrow on touch pad. Following a short time delay, the digital display will revert to displaying actual cabinet temperature.
Step 5.
If timer operation is not required, omit Step 4 and proceed as follows:Press “MANUAL ON” – manual on indicator will illuminate.
Step 6.
Close door.
Do not slam door shut on double door unit as this will force the opposite door to open. To revert to timer operation from manual operation, proceed as follows:Press MANUAL ON push button Digital display will display 00. accordance with Step 4.
PR-MN-CU-009 Rev 1
13
Set required time in
In the event of over temperature 1.
The over temperature set point is factory set at 2ºC above selected temperature. In the event of over temperature condition, the digital display will display flashing 888.
2.
Open door – when over temperature condition no longer exists, the digital display will revert to displaying actual cabinet temperature.
3.
Note that over temperature alarm will be triggered if set point temperature is lowered by more than 2ºC below actual cabinet temperature.
4.
Close door and resume normal operation.
5.
If over temperature condition persists, switch unit off and contact your Atherton service Centre 1300 580 870.
CABINET OPERATING PRINCIPLES Fresh air is drawn through the roughing filter, through the intake damper into the circulation fan. It is then forced over the element, down the duct at the side of the cabinet, then vertically upward through the load in the chamber. This upward flow of air is assisted by natural convection. Model RDC - the air is also forced down the tube drying nozzles.
Depending on the setting of the recirculation damper, all the air may be exhausted to atmosphere (recirculation damper closed) or, with the damper in various positions, a proportion of the exhaust air may be mixed with the fresh air intake, to be recirculated back through the chamber. This is achieved by virtue of the design of the damper system.
OPERATING INSTRUCTIONS – SDC Step 1.
Load articles onto shelves allowing space between articles for air circulation.
Step 2.
Set thermostat to desired operating temperature. An over temperature thermostat has been fitted to the cabinet and set at 65ºC. Do not turn thermostat knob past 60ºC.
Step 3.
Turn the power switch to ON position.
PR-MN-CU-009 Rev 1
14
MAINTENANCE The following procedure should be performed at regular intervals as indicated.
WARNING: Always shut off electrical power to the unit at the isolating switch before cleaning.
DAILY: Allow the unit to cool, then clean the internal and external surfaces of the unit using a damp cotton cloth with mild detergent solution. Wipe with dry cotton cloth.
Never use a wire brush or steel wool on internal and external surfaces.
QUARTERLY: Make a visual check to ensure electrical controls and indicating lights are operating correctly. Silicone spray door gasket hinge side to prevent binding.
HALF YEARLY: Have electrician check insulation, resistance, earthing, terminals, connections and elements. Remove roughing filter medium located on top of cabinet and wash in cold soapy water.
PR-MN-CU-009 Rev 1
15
TROUBLE SHOOTING This section describes the type of unit malfunctions likely to occur and indicates probable causes. If you are unable to correct the problem, contact the Atherton Service Manager in your state.
Always shut off electrical power to the unit at the isolating switch before attempting any repair work on electrical components. Problem
Possible Cause and Correction
1. No power
Check main isolating switch – Turn on Check fuse – replace fuse if blown
2. No heat
Check ON-OFF switch – Turn on Element burnt out – replace element
3. No air circulation
Burnt out fan – replace fan Blocked air filter – remove and clean
PR-MN-CU-009 Rev 1
16
WIRING DIAGRAMS MODEL RDC, MDC, RDCD, MDCD DRYING CABINET WIRING DIAGRAM
PR-MN-CU-009 Rev 1
17
MODEL SDC DRYING CABINET WIRING DIAGRAM
PR-MN-CU-009 Rev 1
18
REPLACEMENT PARTS MOELS:
RDCD, MDCD, RDC, MDC
Description
Part Number
Touch Pad
020099
Control PCB
020070
Triac PCB
139394
Cooling fan 120mm2
137640
Circulating fan
138640
Element
136275
Gasket, black 206 size 1490 x 765
137819
Nozzle respiratory S&R air hose
017993
Fitting air bag plastic tube
017994
Nozzle endotracheal tube
017995
Nozzle breathing bag
014340
Hose
137607
Over temperature thermostat
134838
Glass, clear complete with logo
137775
Glass, clear (RDCD, MDCD only)
137830
Filter, disposable Drying Cabinet
139126
PR-MN-CU-009 Rev 1
19
MODEL: SDC
PR-MN-CU-009 Rev 1
Description
Part Number
Element
137512
Thermostat control and over temperature
134877
Flush handle
137513
Control switch (Swan)
137514
Fan
137522
Thermometer
137515
20
DRYING CABINET FINAL TEST REPORT Test Date _____________________
Check List
1. Electrical
a) Touch pad operation
OK
FAIL
2ND TEST
OK
b) Control PCB operation
OK
FAIL
2ND TEST
OK
c) Overtemp thermostat
OK
FAIL
2ND TEST
OK
d) Fan
OK
FAIL
2ND TEST
OK
e) Cooling fan
OK
FAIL
2ND TEST
OK
f)
OK
FAIL
2ND TEST
OK
Terminals secure
Tested by……………………………………….. 2. Panels a) Fit
OK
FAIL
2ND TEST
OK
b) Finish
OK
FAIL
2ND TEST
OK
Tested by……………………………………….. 3. Door a) Door gasket
OK
FAIL
2ND TEST
OK
b) Hinge mechanism
OK
FAIL
2ND TEST
OK
c) Micro switch
OK
FAIL
2ND TEST
OK
Tested by……………………………………….. 4. Performance Test a) Heating
OK
FAIL
2ND TEST
OK
Tested by………………………………………..
PR-MN-CU-009 Rev 1
21