Manual
78 Pages
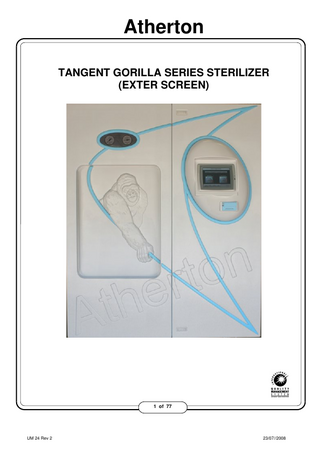
Preview
Page 1
Atherton TANGENT GORILLA SERIES STERILIZER (EXTER SCREEN)
1 of 77
UM 24 Rev 2
23/07//2008
Atherton WORD FROM ATHERTON This manual contains important information on the proper use and maintenance of the Atherton TANGENT SERIES Sterilizer range. All operators and Departmental Heads are urged to carefully read this manual and become familiar with the warnings, cautions and instructions contained within it. A thorough Scheduled Maintenance Programme is essential for safe and reliable sterilization. You are urged to contact the ATHERTON SERVICE MANAGER in your State to arrange a maintenance programme for your equipment. Due to the continuous programme of research and development conducted by ATHERTON, all design details are subject to change without notice. IMPORTANT: For warranty to be valid, complete, sign, and return the "INSTALLATION AND COMMISSIONING" form to: Atherton P.O. Box 116, Northcote, Victoria, Australia, 3070.
Warning
Caution
Note & Important
Must be followed carefully to Avoid endangering human life And / or damage to equipment
Should be followed to ensure proper operation of equipment
Contains important information and useful tips on operation of equipment
ADELAIDE
MELBOURNE
BRISBANE
UNIT 22, 11-31 PORT WAKEFIELD ROAD GEPPS CROSS, S.A. 5094 TEL. (08) 8262 9044. FAX (08) 8262 9344
COMPANY HEAD OFFICE Athertom 364 DAREBIN ROAD, THORNBURY VICTORIA, 3071, AUSTRALIA ACN 004 104 607 TEL. (03) 9497 2500. FAX (03) 9497 1190 www.atherton.net Email: [email protected]
66 RAYNHAM STREET SALISBURY, QLD, 4107 TEL. (07) 3277 1321. FAX (07) 3875 1512
PERTH UNIT 3/1914 BEACH ROAD MALAGA, W.A. 6062 TEL. (08) 9249 6166. FAX (08) 9249 6353
SYDNEY 23 LIDCO STREET ARNELL PARK, N.S.W. 2148 TEL. (02) 9679 8911. FAX (02) 9679 8922
2 of 77
UM 24 Rev 2
23/07//2008
Atherton Section 1
2
3
4
5
Topic
Page
INSTALLATION
8
1.1 1.2 1.3 1.4
8 9 10 10
TRANSPORT PROTECTION DOOR SUPPORT INSTALLED CHECK LIST INTRODUCTION
GENERAL NOTE ABOUT TOUCHSCREEN DISPLAY
11
2.1 2.2 2.3 2.4 2.5 2.6
11 11 12 12 12 13
TITLE BAR FUNCTIONALITY MAIN AREA FUNCTIONALITY BOTTOM NAVIGATION BAR CYCLE START SCREENS OPERATING SCREENS TREND SCREEN
USER SECTION
14
3.1
14 14 15 17
RUNNING A CYCLE 3.1.1 Select Cycle Family 3.1.2 Select Specific Cycle 3.1.3 Select The Start Cycle Button
ADMINISTRATOR SECTION
18
4.1 4.2 4.3 4.4 4.5 4.6 4.7
CUSTOMISING YOUR STERILIZER SETTING TIME & DATE FAULT REPORT ANALOGUE READINGS TANGENT ADMINISTRATOR MENU SETTING NEW OPERATOR NAME & I.D. CODES SETTING FAVOURITE CYCLES 4.7.1 CREATE, MODIFY OR DELETE A FAVOURITE CYCLE 4.7.2 DELETE OR MODIFY A FAVOURITE CYCLE 4.7.3 CREATE FAVOURITE CYCLE 4.8 CUSTOMISED OPERATION 4.8.1 Data Logging 4.8.2 Enable Standby Mode and Fluid Probe Cool down 4.8.3 Warm-Up Parameters 4.8.4 Abort Parameters 4.8.5 Auto Holding Time 4.8.6 Daily Log Print Out 4.8.7 Generator Blowdown (Generator Units) 4.8.8 Unloading Door (Double Door Units Only) 4.8.9 Automatic Door Customization 4.8.10 Customise Operating Screen 4.9 ADMINISTRATOR LEVEL 4.10 SERVICE TECHNICIAN LEVEL
18 19 20 21 22 22 23 24 25 26 28 29 30 31 31 32 33 34 34 35 35 36 36
STERILIZATION CYCLES
37
5.1 5.2
37 37 37 38 38 38 38 39 39 39
GENERAL DESCRIPTION PRE-VAC FAMILY 5.2.1 Pre-Vac Cycle 5.2.2 Bowie Dick Test Cycle 5.2.3 Leak Rate Test Cycle 5.2.4 Air Detector Function Test Cycle 5.2.5 Air Detector Performance Test Cycle 5.3 GENERAL PURPOSE CYCLE TYPES 5.3.1 Porous Load 5.3.2 Hard Goods Cycle 3 of 77
UM 24 Rev 2
23/07//2008
Atherton 5.3.3 Hard Goods Cycle SPECIAL CYCLE TYPES 5.4.1 Lab Vac 5.4.2 FO Cycle 5.4.3 Fast Vac Cycle 5.5 FAVOURITE CYCLE TYPES 5.6 OPERATOR INTERFACE
39 40 40 40 40 41 41
USEFUL GUIDELINES
43
6.1 6.2 6.3
43 43 44
5.4
6
7
8
9
PREPARING THE LOAD LOADING THE STERILIZER UNLOADING THE STERILIZER
GETTING STARTED
45
7.1 7.2 7.3
HELP MENU DOOR OPERATION RUNNING A CYCLE 7.3.1 Select Cycle Family 7.3.2 Select Specific Cycle 7.3.3 Select The Start Cycle Button 7.3.4 Cycle Completion 7.4 ABORTING A CYCLE 7.5 FAULT 7.6 FIXED AND VARIABLE CYCLES 7.6.1 Adjusting Variable Cycle Parameters 7.7 PRINTING 7.8 RE-PRINTING 7.9 DATA LOGGING 7.10 DOUBLE DOOR UNITS
46 46 48 48 49 51 52 53 54 55 55 57 57 58 58
ROUTINE MAINTENANCE
59
8.1 8.2 8.3 8.4
60 60 61 62
CLEANING DOOR (Weekly) GASKET REMOVAL SERVICE VALIDATION
WIRING DETAILS 9.1 9.2 9.3 9.4 9.5 9.6 9.7
64
PLC CONFIGURATION 64 INPUT TABLE 64 RTD WIRING 64 WIRING SCHEMATIC STEAM HEATED MODEL 65 WIRING SCHEMATIC STEAM GENERATOR MODEL 66 WIRING SCHEMATIC STEAM HEATED, DOUBLE DOOR MODEL 67 WIRING SCHEMATIC ELECTRIC STEAM GENERATOR, DOUBLE DOOR MODEL 68
10 PIPING SCHEMATIC 10.1 10.2 10.3 10.4
69
PIPING SCHEMATIC STEAM HEATED MODEL 69 PIPING SCHEMATIC INDEX STEAM HEATED MODEL 70 PIPING SCHEMATIC ELECTRIC STEAM GENERATOR MODEL 71 PIPING SCHEMATIC INDEX ELECTRIC STEAM GENERATOR MODEL 72
11 RECOMMENDED SPARE PARTS
73
12 INSTALLATION AND COMMISSIONING WARRANTY FORM
74
13 INSTALLATION AND COMMISSIONING REFERENCE FORM
75
14 COMMISSIONING CHECK LIST
76
4 of 77
UM 24 Rev 2
23/07//2008
Atherton YOUR WARRANTY COVER All equipment manufactured and work performed by the Company is warranted to be of good material throughout, and of good careful workmanship. The Company undertakes to correct and make good any defect or defects, which may develop under normal and proper use within the warranty period which are due to workmanship, provided that the Company is notified immediately after the defect is discovered. The warranty period is twelve months and shall be from the date delivery is made, or notification to the client that delivery can be made. The Company’s liability is limited as provided in these conditions and does not extend to consequential damage, either direct or indirect, that may be caused by any malfunction of the equipment, or to any expense for repair or replacement otherwise paid or incurred without the authority of the Company. The Company does not accept liability or responsibility for the defects or depreciation caused by wear and tear, accidents, lightning, corrosion, neglect, misuse, incorrect installation not carried out by the Company’s personnel or nominees of the Company, incorrectly maintained, incorrect operation or other abnormal conditions. Should field service be required, costs incurred in travelling to and from location of equipment, including travelling time, transportation and accommodation costs, and freight charges of sending replacement parts to and from a nominated Atherton office, are borne by the buyer. All field service will be carried out during normal working hours. If warranty service is requested outside normal working hours such work will be charged at the ruling overtime rates. Requests for replacement parts or components under warranty must be accompanied with a purchase order for the replacement part or component at the ruling spare parts price cost. The defective part or component must be returned to the Atherton office handling the warranty claim complete with details of serial number, catalogue or model number or some means of verifying the unit and its delivery date. After receipt and inspection of the defective part or component the Company shall decide at its sole discretion whether a warranty claim applies. If the claim is granted a credit will be issued for the replacement amount previously charged. Material and equipment not manufactured by the Company are sold under such warranty only as the makers give the Company and the Company is able, without legal expense to enforce, but are not guaranteed by the Company in any way. The warranty and warranty period does not cover such articles which are considered to be expendable, including but not limited to gaskets, filters, bellows, globes, gauges, electrical components.
5 of 77
UM 24 Rev 2
23/07//2008
Atherton WARNINGS & CAUTIONS Throughout this manual reference is made to: Warnings and Cautions. Please take notice of these, to help we have listed a summary with appropriate page reference. Warnings
Page
Installation personnel
8
Hot surfaces
28
Entry to chamber
28
Door operation
28
Hot surfaces
36
Minimum maintenance
41
Entry to chamber
41
Cautions
Page
Over current
8
Routine maintenance
41
Cleaning the chamber
42
Gasket replacement
45
6 of 77
UM 24 Rev 2
23/07//2008
Atherton SYSTEM WARNINGS The Tangent Control System has predetermined warnings and these warnings are not dangerous to the operator but may indicate a drop in performance. The following Low Battery screen, and on Steam Generator models, Generator Fault screen may appear and if so, please turn off the power to the equipment and contact your local Atherton agent.
The following screen may appear and if so, the door mechanism has encountered a problem.
Touch the screen to return to the door screen then contact your local Atherton agent.
BEFORE YOU BEGIN
7 of 77
UM 24 Rev 2
23/07//2008
Atherton 1 Installation A Technical Data Sheet showing all the utility and space requirements for the installation of the equipment was sent to the purchaser after the order for this sterilizer was received. The clearances requested are necessary for easy installation, proper operation and maintenance of the equipment. If you are not in possession of these documents, and require them, you can order additional copies from the ATHERTON office in your state, giving the serial number and model number of the equipment. After installing the sterilizer according to the instructions provided, complete the following checklist to ensure that the installation is correct and complete. If you are in any doubt as to the correctness of the installation, you are strongly advised to contact your ATHERTON office, as incorrect installation and /or commissioning can invalidate your warranty. Installation and commissioning should only be carried out by fully qualified personnel, familiar with installing this type of equipment. Ignorance or carelessness can cause death.
Over current protection is required in the power supply to the unit.
1.1
TRANSPORT PROTECTION Your Tangent series sterilizer is supplied with transport protection and this must be removed before installing your sterilizer.
8 of 77
UM 24 Rev 2
23/07//2008
Atherton 1.2
DOOR SUPPORT First open the front panel where the touch screen is located by disengaging the top and bottom panel clips, then swing the panel open. Remove the 4 screws holding the second panel and then swing the panel open. Remove the 2 door lock bolts as shown below. Failure to remove “Door Lock Bolts” may damage the door actuator.
If your tangent series sterilizer is a double door unit, this must be done at both ends.
9 of 77
UM 24 Rev 2
23/07//2008
Atherton 1.3
INSTALLED CHECK LIST Isolation valves for maintenance purposes should be installed in steam and water lines, at a point near to the sterilizer. Electrical isolating switch should be provided to the sterilizer. Check that the electrical supply is rated as per Atherton requirements and is installed by a qualified electrician to AS 3000 and the requirements of the local supply authority. If multiple units are installed adjacent to each other, isolating valves and switches should be installed for each piece of equipment. Ensure the electrical connection can be made before placing the unit in its final position. Check that the sterilizer chamber is level, and is at the height shown on the equipment drawing. Place a spirit level on the sterilizer end frame or chamber floor in both directions, to ascertain correct positioning. If a recessed unit has been ordered, the panel trim should be tight fitting against the wall opening. Reticulated steam supply line MUST provide condensate free steam at not less than 0.97 dryness factor. Steam supply pressure should be between 400-500 KPa. Cold water supply to the sterilizer should be between 200-500 KPa. Use the adjustable feet at base of the unit for levelling.
1.4
INTRODUCTION This operating manual covers the TANGENT GORILLA SERIES sterilizer system, its operation, servicing, and hardware design.
10 of 77
UM 24 Rev 2
23/07//2008
Atherton 2 GENERAL NOTE ABOUT TOUCHSCREEN DISPLAY Your Tangent Gorilla sterilizer is fitted with a state of the art hi-resolution Exter T100 touch screen. To aid with system navigation a commonality of function has been programmed into the design of the screen layout. For the most common screens the touch screen area has been divided into three sections, a title bar, the main body area and the bottom navigation bar. 2.1
TITLE BAR FUNCTIONALITY The area at the top of the screen is referred to as the title bar for “most” screens this area acts as a return to previous screen function. The reason not all screens have this functionality is due to the fact that for some functions it is necessary that the user complete a series of tasks which may require a set navigational sequence. However for the vast majority of screens touching the title bar will return the user to the previous screen. For example from the Main Menu if the user selects the Help Menu button the Help Menu screen is displayed, then to return to the Main Menu the user can either choose the button at the bottom of the screen or use the title bar:
HELP MENU
Selecting the title bar from the Help Menu returns the user to the Main Menu. 2.2
MAIN AREA FUNCTIONALITY The middle of the screen is referred to as the main area and contains the functionality buttons and any display items. For example the main area of the Analogue Readings screen contains the analogue input values displayed in dial form:
11 of 77
UM 24 Rev 2
23/07//2008
Atherton 2.3
BOTTOM NAVIGATION BAR The bottom area of the screen is reserved for navigation and committing a change to the memory. Using the above example of the Analogue Readings screen the bottom navigation bar allows the user to return to the previous screen or the Main Menu – referred to here as the Home Screen or the Help Menu:
2.4
CYCLE START SCREENS Once a cycle has been selected from the cycle family screens the system displays the parameters for the chosen cycle. If the user is satisfied that the parameters are appropriate the user then selects ‘START CYCLE’.
The cycle start screens all follow the same format – the parameters are displayed in the centre of the screen, a user with the required access level can alter the parameters for all variable cycles. The user then has the option of either starting a cycle or cancelling and returning the cycle family screen.
2.5
OPERATING SCREENS The operating screens display the sterilizer state while running a sterilizing or test cycle. All the operating screens are similar; there are three sections in the green background area of the screen and a lower navigation bar. In the green background area the three sections are; the parameters section at the top 12 of 77
UM 24 Rev 2
23/07//2008
Atherton which is unique for each cycle, the temperature and pressure section in the middle, and the cycle stage, elapsed time and warning text section in the lower third. On the navigation bar the user can view a cycle trend, the full set of temperature and pressure readings, and a system schematic, as well as abort the cycle.
2.6
TREND SCREEN The cycle trend screen has the capability to display historical information. If the user touches the middle of the trend graph the trend stops updating and a navigation bar appears at the base of the trend graph. Use the arrows to move back forward in time and then to zoom in or out.
13 of 77
UM 24 Rev 2
23/07//2008
Atherton 3 USER SECTION 3.1
RUNNING A CYCLE This section describes the procedure for setting the sterilizer to run a cycle, the procedure is the same for all cycles – including favourites. In summary the procedure is: 1. Select cycle family. 2. Select specific cycle or favourite. 3. If the cycle parameters are correctly matched to the items to be sterilized select the start cycle button.
3.1.1 Select Cycle Family This demonstration assumes the user has started from the home screen.
Select Cycle Family – In this case we are going start a Pre Vac Cycle, therefore select the PRE VAC CYCLES button: This will bring up the Pre Vac Family screen – this screen displays all the available cycles that have a pulsing Pre Vacuum stage. At this stage it important to note that the above steps are repeated for General Purpose cycles, Special Purpose cycles and Favourites cycles each cycle family has its own Cycle Family screen from there the user selects the unique cycle.
14 of 77
UM 24 Rev 2
23/07//2008
Atherton
3.1.2 Select Specific Cycle Using the buttons on this screen we select the PRE VAC CYCLE button
The operating parameters that will be applied to the selected cycle are displayed in the centre of the screen. Because the cycle we have chosen is a variable cycle we have the option of modifying the parameters. This option is 15 of 77
UM 24 Rev 2
23/07//2008
Atherton only available to users who have supervisory level access. To modify the parameters touch the value, in this case I am going to change the sterilizing temperature and the holding time. Before I can modify these parameters I have to enter the supervisor password:
Once I have entered my password I then touch the parameter again and this time the parameter input box appears:
In this case I am going to change the sterilizing temperature from 134°C to 121°C and at the same time alter the holding time 15 minutes.
16 of 77
UM 24 Rev 2
23/07//2008
Atherton
Now that I am happy with the operating parameters I select the START CYCLE button. 3.1.3 Select The Start Cycle Button
This will cause the display to change to the Operating Screen – each screen is tailored to display the parameters of the cycle, in this case the Pre Vac Cycle has three operating parameters: Sterilizing Temperature, Holding Time & Drying Time:
17 of 77
UM 24 Rev 2
23/07//2008
Atherton 4 ADMINISTRATOR SECTION 4.1
CUSTOMISING YOUR STERILIZER Your Tangent sterilizer can be customised in many ways to suit your specific needs. The customisation can be done on 4 levels: 1. Operator Level 2. Operator level with authorization 3. Supervisor Level 4. Service Technician Level OPERATOR LEVEL All operators have access to this level of the Tangent series control system. The Time/Date settings can be changed, the fault report, analog monitoring and a re-print of the last cycle are available. This information and settings are accessed from the main screen (“Main Menu”) via the “Help Menu” button.
18 of 77
UM 24 Rev 2
23/07//2008
Atherton 4.2
SETTING TIME & DATE To set the time, select the HELP MENU button from Main Menu also referred to as the home screen then select SET CLOCK, the following screen will appear
The HOURS, MINUTES, SECONDS values can be adjusted by touching the raised area around the value, a numeric keypad will pop up allowing the new value to be entered:
For example to adjust the hours value, which must be entered in 24hr format, touch the hour value and enter the new value using the key pad.
To alter the day indicator select the arrows to advance the day, the new day is indicated by the highlighted white text:
. When the time & date are correct, select the SAVE button. If however you do not want the changes to be saved Touch the title bar or the HELP MENU button to exit.
Touch SAVE to commit the changes.
Otherwise anywhere on the title bar to leave without committing the changes. 19 of 77
UM 24 Rev 2
23/07//2008
Atherton OR.
Either of these buttons will also not commit the changes. Time & Date must always be entered together.
4.3
FAULT REPORT The previous 20 faults can be viewed by touching the FAULT REPORT button on the Tangent Help menu.
The faults are listed as run number and fault description. To clear or print the fault list use the buttons on the bottom navigation bar. When finished the user can either return to the previous screen or return to the Main Menu by selecting the appropriate button from the bottom navigation bar.
20 of 77
UM 24 Rev 2
23/07//2008