BBraun
microspeed uni motor system Instructions for Use v6
Instructions for Use
888 Pages
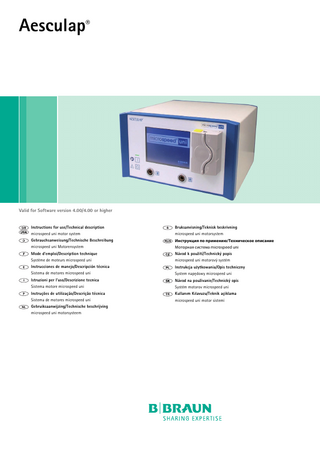
Preview
Page 1
GD670
1
2
3
4
8 7 6 9
5 10
11
12
5
3
13
39
GD671
20 21
18
17 16 15
14
19
GD668 18
22
23 24
25
GD673
26
33 27
GD684 34
29
35
28
30 28 31
GD672
GD682 36
37
38
44
GD674
36
40
38
GD676 GD681 GD677 GD678
32
44
41 42 43
GD679 GD685
GD675
Aesculap® microspeed uni motor system
microspeed uni motor Aesculap system®
Captions first foldout page: Control units and foot controls 1 microspeed uni control unit with cooling unit GD670 2 Display and touch-control panel 3 Release buttons 4 Coolant pump 5 Motor sockets 6 Mains OFF switch 7 Mains ON switch 8 Mains ON display 9 Bottle holder 10 Adapter for bottle holder 11 Ventilation grille 12 Cable plug 13 Fuse holder 14 Connection socket for foot control 15 Stacking cones 16 Locking screw 17 Terminal for potential equalization lead 18 Function key for foot control 19 Right pedal 20 Left pedal 21 microspeed uni two-pedal foot control GD671 22 Motor direction changeover switch 23 Pedal 24 microspeed uni one-pedal foot control GD668 39 These connections may only be used by the manufacturer
2
Captions second foldout page: Motor cable with motor-side plug connection and motors with integrated motor cable 25 Motor release switch 26 Function key for hand control 27 microspeed uni motor cable for hand control GD673 28 Release buttons 29 Lever 30 Motor release switch 31 microspeed uni motor cable for foot control GD672 32 Motors with motor-side plug connection (motor GD677 is no longer available) 33 microspeed uni mini pistol handpiece GD684, mini-Line-coupling 34 Upper trigger 35 Lower trigger 36 Suction control lever 37 microspeed uni shaver handpiece GD682 38 Tube connector 40 microspeed uni shaver handpiece for hand control GD681 41 Front trigger 42 Rear trigger 43 microspeed uni XS Highspeed motor GD675, Hi-Line-XS-coupling 44 Unlocking sleeve
Symbols on the control unit Caution; general warning symbol Caution, see documentation supplied with the product Follow the instructions for use
Type BF applied part
Input from irrigation bottle (coolant pump)
Outlet to handpiece (coolant pump)
Pumping direction (coolant pump)
Terminal for equipotential bonding conductor
Fuse Alternating current Foot control Marking of electric and electronic devices according to directive 2002/96/EC (WEEE). see Disposal
Symbols on the display: display symbols in the motor control panels (Selected) maximum speed setting (example: 20 000 1/min) Motor speed in 1/min
Qualitative indicator of actual motor speed (for shaver handpiece GD681, GD682 and for perforator driver GD685 actual tool speed); Symbol displayed on gray background in motor control panel if the respective motor is not activated Qualitative indicator of actual motor speed (for shaver handpiece GD681, GD682 and for perforator driver GD685 actual tool speed); active while motor is in operation Motor direction indicator for right rotation when the motor is inactive or when right rotation was not selected via foot control GD668; in an inactive motor control panel, this symbol is displayed on a gray background Motor direction indicator for right rotation active when the motor is in operation or in standby, provided this motor direction was selected and foot control GD668 is connected to the control unit Motor direction indicator for left rotation when the motor is inactive or when left rotation was not selected via foot control GD668; in an inactive motor control panel, this symbol is displayed on a gray background Motor direction indicator for left rotation active when the motor is in operation or in standby, provided this motor direction was selected and foot control GD668 is connected to the control unit Hand control active if connected hand control is recognized Foot control active if connected foot control is recognized and at least one motor is not operated by a hand control device No response when foot control is pressed active if neither a foot control nor a hand control device is registered as connected
3
Aesculap® microspeed uni motor system
GD675 microspeed uni XS Highspeed motor (coupling system: Hi-Line XS) connected. If the motor can be activated (is released), the symbol is highlighted by a green background
GD685 microspeed uni perforator driver (coupling system: HUDSON) connected. If the motor can be activated (is released), the symbol is highlighted by a green background
GD676 microspeed uni Hi 150 motor (Highspeed motor; 150 W; coupling system: Hi-Line (XS)) connected If the motor can be activated (is released), the symbol is highlighted by a green background
Operating mode “Burr” (only in conjunction with shaver handpiece GD681 and GD682 if no shaver blade is recognized)
GD677 microspeed uni Hi 100 motor (Highspeed motor; 100 W; coupling system: Hi-Line (XS)) connected If the motor can be activated (is released), the symbol is highlighted by a green background Note: The motor is no longer available. GD678 microspeed uni micro 150 motor (low-speed motor; 150 W; coupling system: micro-Line) If the motor can be activated (is released), the symbol is highlighted by a green background
GD679 microspeed uni micro 100 motor (low-speed motor; 100 W; coupling system: micro-Line) If the motor can be activated (is released), the symbol is highlighted by a green background
GD674 microspeed uni mini 100 motor (low-speed motor; 100 W; coupling system: mini-Line) connected If the motor can be activated (is released), the symbol is highlighted by a green background GD681 microspeed uni shaver handpiece with hand control connected. If the motor can be activated (is released), the symbol is highlighted by a green background GD682 microspeed uni shaver handpiece connected If the motor can be activated (is released), the symbol is highlighted by a green background
GD684 microspeed uni mini pistol handpiece (coupling system: mini-Line) connected If the motor can be activated (is released), the symbol is highlighted by a green background
4
Operating mode “Shaver blade” (only in conjunction with shaver handpiece GD681 and GD682 if no shaver blade is recognized) Oscillating or tapping mode (only in connection with pistol handpiece GD684) Displayed when oscillating or tapping mode is enabled in the instruction menu, but has not been activated via the pistol handpiece Oscillating or tapping mode active (only in connection with pistol handpiece GD684) Displayed when oscillating or tapping mode is enabled in the instruction menu and activated via the pistol handpiece (by holding down the upper trigger for three seconds)
Symbols on the display: display/control key symbols in the motor control panels Increasing the maximum speed setting
Reducing the maximum speed setting
Status indicator/control key of the saw program This symbol indicates that the saw program, which can only be selected in conjunction with motors GD678 and GD679, is deactivated Status indicator/control key of the saw program This symbol indicates that the saw program, which can only be selected in conjunction with motors GD678 and GD679, is activated
Motor direction indicator when left rotation is not selected, and control key for selecting left rotation The control key symbol is only displayed, and a motor direction can only be selected if hand control GD673 is connected
Symbols on the display: display symbols in the pump control panel Display of selected dosage is always active
Motor direction indicator when left rotation is selected, and control key for selecting left rotation The control key symbol is only displayed, and a motor direction can only be selected if hand control GD673 is connected Motor direction indicator when right rotation is not selected, and control key for selecting right rotation The control key symbol is only displayed, and a motor direction can only be selected if hand control GD673 is connected Motor direction indicator when right rotation is selected, and control key for selecting right rotation The control key symbol is only displayed, and a motor direction can only be selected if hand control GD673 is connected Switchover button “Release right motor socket” This control key symbol is displayed in the inactive, right motor control panel (only if a XS Highspeed motor GD675 and a shaver handpiece GD682 are connected to the control unit at the same time) Switchover button “Release left motor socket” This control key symbol is displayed in the inactive left motor control panel (only if a XS Highspeed motor GD675 and a shaver handpiece GD682 are connected to the control unit at the same time)
Symbols on the display: control key symbols in the pump control panel Status indicator and “Flush” button “Pump inactive” indicator Symbol as displayed with the motor inactive and the pump inactivated in the pump control panel Status indicator and “Flush” button “Pump active” indicator Symbol as displayed with the motor activated and the pump activated in the pump control panel Symbol as displayed during actuation of this control key when activating the pump Increasing the delivery rate
Reducing the delivery rate
“Pump OFF” indicator and control key for activating the pump The symbol is displayed in the respective motor control panel. “Pump ON” indicator and control key for activating the pump Active when, in conjunction with the selected motor, the pump is switched on via the function button (hand or foot control) or by actuating this field. The symbol is displayed in the respective motor control panel.
5
Aesculap® microspeed uni motor system
Symbols on the display: control key symbols in the display Selection of the secondary operating level instruction menu Button can only be activated while no motor is active
IPX8
Housing protection class according to IEC/DIN 60529 (Foot control GD668 and GD671) Release (Motor GD674, GD681, GD682 and GD684) Motor speed control (Motor GD684) Right/left rotation switch (Motor GD684)
Symbols on foot controls, motor cable and motor Caution; general warning symbol Caution, see documentation supplied with the product
YYYY-MM
Service label on motor and motor cable Recommended date of next service (format: YYYYMM) by international B. Braun/Aesculap agents see Technical Service
Oscillating or tapping mode (Motor GD684) Protection against inadvertent activation (Motor GD684) Marking of electric and electronic devices according to directive 2002/96/EC (WEEE). see Disposal
Right-hand rotation (Symbol on front trigger of shaver handpiece with hand control GD681) Oscillating mode (Symbol on rear trigger of shaver handpiece with hand control GD681, only permitted in “Shaver blade” operating mode) Function button (Foot control GD668, GD671, motor cable GD673) Motor direction changeover switch Selection of left or right rotation (Foot control GD668) Pedal for left/right rotation (according to the motor direction preselected via the motor direction changeover switch, foot control GD668) Pedal for right rotation (Foot control GD671) Pedal for left rotation (Foot control GD671) Oscillating operation when both pedals are pressed (permitted only in “Shaver blade” operating mode in conjunction with shaver handpiece GD682, foot control GD671) Class AP anesthetic test (IEC/DIN EN 60601-1) (Foot control GD668 and GD671) 6
Symbols on the packaging Manufacturer’s batch designation Manufacturer’s serial number Manufacturer’s article number Date of manufacture
Contents 1. 2. 2.1 2.2 2.3 2.3.1 2.4 2.4.1 2.4.2 2.4.3 2.4.4 2.4.5 2.4.6 2.4.7 2.4.8 2.4.9 2.4.10 2.4.11 2.4.12
Safe handling Product description Scope of supply Components required for operation Intended use Field of application of the motors Operating principle Control unit Control and display interface Explanation of control panels on the display Motor control panels Pump control panel Instruction menu Motor recognition Auto-save device settings Overload protection Close coolant pump Motor cable Motors with motor-side plug connection GD674, GD676, GD677, GD678 and GD679 GD685 2.4.13 Motors with fixed motor cable GD675, GD681 and GD682 GD684 2.4.14 Foot controls 3. Preparation and setup 3.1 First use 3.2 Mounting the control unit on the mobile stand 3.3 Dismounting the control unit from the mobile stand 3.4 Connecting the power supply 4. Working with the microspeed uni motor system 4.1 System set-up 4.1.1 Connecting the accessories 4.1.2 Connecting the foot control to the control unit 4.1.3 Connecting the tube set 4.1.4 Connecting the motor cable to the control unit 4.1.5 Connect motors (GD674, GD676, GD677, GD678, GD679 and GD685) to motor cable. 4.1.6 Connecting handpieces/attachments/cranial perforators/ blades 4.1.7 Activating/deactivating the control unit 4.2 Function checks 4.3 Safe operation 4.3.1 Operation and setup of motors GD674, GD675, GD676, GD677, GD678, GD679 and GD685 4.3.2 Operation and setup of microspeed uni shaver handpiece GD681 4.3.3 Operation and setup of microspeed uni shaver handpiece GD682
4.3.4 8 9 9 9 9 10 10 10 11 11 11 12 12 12 13 13 13 13
4.4 4.4.1
14
5.5.2 5.5.3 5.6 5.6.1
15 18 19 19 20 20 20 20 21 21 22 22 23
4.4.2 4.4.3 5. 5.1 5.2 5.3 5.3.1 5.3.2
5.4 5.5 5.5.1
5.6.2 5.7 5.8 5.8.1 5.9 5.9.1 5.10 5.10.1 5.10.2
24 24 28 29 29 29 33 35
5.10.3 5.10.4 5.11 5.12 5.13 5.14 6. 7. 7.1
Operation and setup of microspeed uni mini pistol handpiece GD684 Settings in the instruction menu Submenu for information on the errors indicated in the display Submenu Device-specific settings Submenu Motor (type)-specific settings Validated reprocessing procedure General safety instructions General information Dismantling prior to carrying out the reprocessing procedure microspeed uni control unit with cooling unit (GD670) and foot controls (GD668/GD671) microspeed uni motors (GD674-GD679, GD685), motor cable (GD672-GD673), shaver handpieces (GD681GD682) and microspeed uni mini pistol handpiece (GD684) Preparations at the place of use Preparation before cleaning microspeed uni motors (GD674-GD679, GD685) and motor cable (GD672-GD673) microspeed uni shaver handpieces GD681 and GD682 microspeed uni mini pistol handpiece (GD684) Cleaning/disinfection Product-specific safety instructions for the reprocessing procedure Validated cleaning and disinfection procedure Wipe disinfection for electrical devices without sterilization Manual cleaning/disinfecting Manual cleaning and wipe disinfecting Mechanical cleaning/disinfecting Mechanical alkaline cleaning and thermal disinfecting Inspection, maintenance and checks microspeed uni control unit with cooling unit GD670 and microspeed uni foot controls GD668/GD671 microspeed uni motors GD674, GD675, GD676, GD677, GD678, GD679, GD685 and motor cable GD672 and GD673 microspeed uni shaver handpieces GD681 and GD682 microspeed uni mini pistol handpiece (GD684) Packaging Steam sterilization Sterilization for the US market Storage Maintenance Troubleshooting list Malfunctions with error numbers
39 43 44 44 46 49 49 49 50 50
50 50 50 50 50 51 51 51 53 53 54 54 55 55 56 56
56 56 56 56 57 57 57 57 58 58 7
Aesculap® microspeed uni motor system
7.2 7.3 8. 9. 9.1 9.1.1 9.1.2 9.1.3 9.1.4 9.1.5 9.2 10. 10.1 10.2 10.2.1 10.3 10.4 10.4.1 10.4.2 10.4.3 10.5 10.5.1 10.5.2 10.6 10.7 11. 12. 13.
8
Other malfunctions Fuse replacement Technical Service Accessories/Spare parts Accessories microspeed uni motors, motor cables, and foot controls Cooling unit Other components Mains power cords/equipotential bonding leads Care/Processing Spare parts Technical data Classification acc. to Directive 93/42/EEC microspeed uni control unit with cooling unit GD670 Factory settings microspeed uni foot control GD668 (one pedal) and GD671 (two pedals) Low-speed motors Low-speed motors with micro-Line coupling Low-speed motors with mini-Line coupling microspeed uni perforator driver GD685 Highspeed motors Highspeed motors with Hi-Line and Hi-Line-XS coupling microspeed uni XS Highspeed motor GD675 with Hi-LineXS coupling microspeed uni shaver handpieces GD681 and GD682 microspeed uni mini pistol handpiece GD684 Ambient conditions Disposal Distributor in the US/Contact in Canada for product information and complaints
61 62 62 62 62 62 62 63 63 63 63 64 64 64 65
1.
Safe handling
CAUTION Federal law restricts this device to sale by, or on order of a physician!
DANGER
WARNING
65 65 65 66 66 67 67 WARNING 67 68 68 69 69 69
Risk of death by electric shock! ► Do not open the product. ► Connect the product only to a grounded power supply. The mode of operation, function, control and setup of the microspeed uni motor system is not consistent with these instructions for use! ► The given instructions for use only describe the handling of the microspeed uni motor system above software version 4.00/4.00. The installed software version can be viewed via the instruction menu. For further information, refer to the Settings chapter in the instruction menu. ► For updating the control unit to the software version specified above, please contact your national B. Braun/Aesculap agency (see Technical Service chapter). Risk of injury and material damage due to incorrect handling of the accessories! ► Use the products only according to their instructions for use. ► Follow the safety advice and instructions.
► Thoroughly clean the new product after removing from the packaging
and prior to initial processing, see Validated cleaning and disinfection procedure. ► Prior to use, check that the product is in good working order. ► Observe “Notes on Electromagnetic Compatibility (EMC)“, see TA022130. ► To prevent damage caused by improper setup or operation, and in order not to compromise warranty and manufacturer liability: – Use the product only according to these instructions for use. – Follow the safety and maintenance instructions. – Only combine Aesculap products with each other. ► Ensure that the product and its accessories are operated and used only by persons with the requisite training, knowledge, or experience. ► Keep the instructions for use accessible for the user. ► Always adhere to applicable standards. ► Ensure that the electrical installations at the premises where the device is to be used meet all requirements acc. to IEC/DIN EN.
► Disconnect from the power supply by pulling on the plug, never on the
power cord. ► Do not use the control unit and motors in potentially explosive areas. ► Carry out sterile processing in any reusable motor(s), motor cable(s), handpiece(s) and tools prior to use. ► When handling, observe the instructions for use that are relevant to Aesculap-Eccos bracket systems; see TA009721 instructions for use under www.extranet.bbraun.com ► Operate the handpieces/motors and tools only at the recommended speeds.
2.
Product description
2.3
Intended use
The microspeed uni motor system is used in traumatology (small fragments), neurosurgery, spinal surgery, hand/foot surgery, ENT/OMF surgery, plastic surgery and arthroscopy. The microspeed uni system is used for working on hard and soft tissues. The microspeed uni motor system can be operated entirely from the sterile area, using either foot or hand control. The motor system fulfills the requirements of Type BF in accordance with IEC/DIN EN 60601-1. The foot controls are Class AP devices. The foot control circuit is ignitionsafe and approved for operation in medical environments according to IEC /DIN EN 60601-1. The housing is constructed according to Protection Type IPX8. Operation Indoors, control unit, and motors outside of the explosion-hazard area.
2.1
Scope of supply Installation location of the control unit
Art. no.
Designation
GD670
microspeed uni control unit with cooling unit
GD412804
Bottle holder
TA022089
Instructions for use
TA022130
Notes on electromagnetic compatibility (EMC)
2.2
Table, equipment cart or mobile stand in the non-sterile area.
Components required for operation
■ microspeed uni control unit with cooling unit GD670 ■ Power cord ■ Motor ■ Motor cable (when using a motor with motor-side plug connection) ■ Foot control (when using a motor cable without hand control, the microspeed uni XS Highspeed motor GD675, or the shaver handpiece GD682) ■ Bottle holder (when using the coolant pump) ■ Tubing set (when using the coolant pump) ■ Surgical suction device (when using the shaver handpiece)
9
Aesculap® microspeed uni motor system
2.3.1
Field of application of the motors
Art. no.
Designation
Field of application
GD674
microspeed uni mini 100 motor
Hand/foot surgery, OMF surgery, plastic surgery
GD675
microspeed uni XS Highspeed motor
Neurosurgery, spinal surgery and ENT surgery
GD676
microspeed uni Hi 150 motor
Neurosurgery, spinal surgery and ENT surgery
GD677
microspeed uni Hi 100 motor
Neurosurgery, spinal surgery and ENT surgery
GD678
microspeed uni micro 150 motor
Traumatology (small fragments), neurosurgery, spinal surgery, hand/foot surgery, ENT/OMF surgery, plastic surgery and arthroscopy
GD679
microspeed uni micro 100 motor
Neurosurgery, spinal surgery and ENT/OMF surgery
GD681
microspeed uni shaver handpiece with hand control
Arthroscopy
GD682
microspeed uni shaver handpiece
Arthroscopy
GD684
microspeed uni mini pistol handpiece
Traumatology (small fragments), hand/foot surgery, ENT/OMF surgery, plastic surgery and arthroscopy
GD685
microspeed uni per- For operating trepanation instruforator driver ments in neurosurgery
10
2.4
Operating principle
The microspeed uni motor system comprises the following components: ■ control unit with coolant pump for universal application ■ two motor connection cables (with and without hand control) ■ various motors with different types of coupling ■ one pistol handpiece ■ two shaver handpieces (with and without hand control) ■ two foot controls 2.4.1
Control unit
Control unit 1 has been designed for the mains voltage range 100 V to 240 V / 50 Hz to 60 Hz. The mains voltage is converted into protective low voltage for supplying the motors. Control unit 1 features two motor connection sockets 5 for connecting two (different) motors, and one foot control connection socket 14 (on rear panel of the unit). The following maximum number of devices can be connected to control unit 1 at the same time: ■ two motors and ■ one foot control (GD668 or GD671). Note Only one motor can be activated at any one time. ► Do not connect two shaver handpieces GD682 at the same time. ► Do not connect two XS Highspeed motors GD675 at the same time. Motors with motor-side plug connection GD674, GD676, GD677, GD678, GD679 and GD685 can be used, both with hand control (motor cable GD673) and with foot control GD668 or GD671 (with motor cable GD672).
Note When two motors without hand control are connected to the control unit (motor cable GD672), a motor can only be activated if the motor release switch of the motor that is to be activated is in the “ON” position while the other motor is disabled (motor release switch in “OFF” position). With one shaver handpiece GD682 and one XS Highspeed motor GD675 connected to the control unit, operation can be switched from one motor to the other only by pressing the appropriate control key on the display in the inactive motor control panel, provided the motor is not active.
2.4.2
Control and display interface
2.4.4
Display 2 indicates the current device status (operating and error status) at all times. The display is divided into motor control panel(s) and a pump control panel. The parameter settings of the device can be changed by pressing the control keys. All symbols used in the motor and pump control panels, are listed at the start of the instructions for use. Pressing the control key “Instruction menu” calls up the instruction menu.
A
2.4.3
E
Explanation of control panels on the display
The display is divided into three different control panels, which are described in the following chapters.
A
B
Motor control panels
B C D
F G H I
Fig. 2
C Fig. 1 Legend A Motor control panel(s) B Pump control panel C Instruction menu
Legend A Status display and control key for releasing (symbol highlighted by green background)/locking the pump B Activation mode indicator: hand control or foot control C Current maximum speed setting D Qualitative display of the actual motor speed E Control keys for increasing or decreasing the maximum speed setting F Motor direction display G Operating mode selected for the connected motor type, e.g. saw program for motors GD678 and GD679 H Connected motor type I Maximum selectable speed setting for the connected motor type or with the selected operating mode, respectively Each motor connected to control unit 1 has a designated motor control panel. Two motor control panels are opened in display 2 only if two motors 32 are actually connected to control unit 1. Only one motor control panel appears when only one motor is connected. There is a clear optical reference between the control panels and the respective motor connection sockets 5.
11
Aesculap® microspeed uni motor system
A motor control panel is displayed as an active control panel when the motor assigned to the motor control panel: ■ is in operation ■ was the last motor operated. The symbol of the connected motor type is highlighted by a green background whenever a motor control panel is released for operation. 2.4.5
Pump control panel
A B C
B
Fig. 3 Legend A Status indicator and “Flush” button of the coolant pump 4. The symbol is highlighted by a green background while the pump is active. The pump can only be activated if it has been released for operation and if the motor is active. “Flush” button function: This function can be activated at any time. During flushing, the coolant pump is active at the highest dosage setting. After an activation period of more than two seconds, a special drive control function prevents leakage of further coolant. B Control keys for increasing or decreasing the delivery rate C Display of preselected dosage The preselected dosage C applies to the motor, the settings of which are displayed in the released motor control panel (highlighted by white background).
12
2.4.6
Instruction menu
Note The instruction menu can only be called up on the control unit. This control key is pressed to call up the instruction menu. The instruction menu can be used to change the information about errors indicated on the display and device settings such as the user language and volume of the acoustic alarms/signals. It can also be used to control motor type-specific adjustments and settings: ■ Deceleration and acceleration ramps for each motor type ■ Oscillating or tapping mode (for pistol handpiece GD684) ■ Oscillation frequency and acceleration ramp in oscillating mode (in shaver blade operating mode of shaver handpieces GD681 and GD682) ■ Reset: for restoring the factory settings 2.4.7
Motor recognition
The control unit 1 recognizes the motor type connected to one of the motor connection sockets 5 on the control unit 1 and displays this type in the corresponding motor control panel of the display 2. The most recent settings for this motor type at the same motor connection socket are shown on display 2. The settings can be changed, within the motor-specific ranges, either on the display or via hand or foot control (in the device settings menu), see Technical data. The motor control panel of the most recently activated motor is always illuminated, whereas the motor control panel of the motor not most recently activated, or disabled, has a gray background. If only one motor is connected to control unit 1, the corresponding control panel is illuminated, provided this motor is not disabled. Saw program (only in conjunction with low-speed motors GD678 and GD679) In this program, the maximum speed setting is limited to 16 000 1/min. The settings most recently used with the saw program (selected maximum speed, dose level for coolant pump 4) are recalled automatically.
2.4.8
Auto-save device settings
The most recent settings for this motor type at this motor connection socket (maximum speed setting, delivery rate, etc.), are called up automatically after a motor change, whenever the same motor type is registered as being connected to the same motor connection socket of control unit 1. Note After each system power-up, both the coolant pump and all motor typespecific special functions such as the saw program (for GD678 and GD679) or the oscillating or tapping mode (for GD684), are generally deactivated (even if previously released or activated). All parameters are reset when the control key “Factory setting” in the instruction menu is pressed. 2.4.9
Overload protection
The motor temperature is monitored in order to protect the micro motors against thermal destruction. Initially, the user is warned of thermal overload (overheating) well in advance of protective shutdown. ■ Level 1: An acoustic warning signal is emitted and the display 2 flashes “Temp. Motor”. Continued overloading causes control unit 1 to switch to level 2. ■ Level 2: The motor is deactivated and the message “Error 7 - Motor overheated” appears on display 2. After a cooling phase the motor can be reactivated. We recommend keeping a replacement motor on standby. 2.4.10
Close coolant pump
Note The coolant pump only works when a motor is running! After each system power-up, coolant pump 4 is generally deactivated (even if previously released for operation). The microspeed uni control unit 1 is equipped with coolant pump 4. This coolant pump serves exclusively for cooling or irrigating the tools. For the coolant, we recommend infusion solutions up to 1000 ml, e.g. NaCl 0.9 % from B. Braun. The delivery rate at the highest dose level is approx. 100 ml per minute. The coolant pump can be activated either in the respective motor control panel or via the appropriate hand or foot control device. The delivery rate can be set via the pump control panel or the device settings menu, see Submenu Device-specific settings.
Exception: For pistol handpiece GD684 and shaver handpiece with hand control GD681, the pump can be activated and the delivery rate changed, only via the appropriate control panels on the control unit. Any one of 21 dosage settings can be selected. At dosage settings 1 to 5, coolant pump 4 runs in intermittent mode. The pump can be activated and deactivated, and the delivery rate changed, even while the motor is active. At dosage setting 4 or higher, a special drive control function prevents leakage of further coolant after the motor has been active for more than two seconds. Additionally, the “Flush” button function allows instant filling of the pump tube with the coolant. When pressing the “Flush” button, the coolant pump is activated at the highest dosage setting. After flushing for more than two seconds, a special drive control function prevents further leakage of coolant. This function can be activated at any time, with or without connection or activation of a motor. 2.4.11
Motor cable
WARNING
Risk of injury due to uncontrolled movement of skin abrading handpiece GB280 in conjunction with a motor cable and hand control GD673! ► Use skin abrading handpiece GB280 only with motor cable GD672 and foot control.
Note A motor cable is required to connect motors (with motor-side plug connection) GD674, GD676, GD677, GD678, GD679 and GD685 to the control unit. The microspeed uni motor system comprises a motor cable for foot control (GD672) and a motor cable with hand control (GD673). Both motor cables can be used in conjunction with all motors with a motor-side plug connection. Either of the two motor cables can be connected to any of the two motor connection sockets 5. Note The selection of motor cable depends on the application and handpiece to be used. Note When using saws GB128R, GB129, GB130R and the motor cable with hand control GD673, we recommend guiding the saw with both hands for optimal handling. If single-handed saw guidance is required, use motor cable GD672 with a foot control for optimal handling.
13
Aesculap® microspeed uni motor system
microspeed uni motor cable for foot control GD672
Legend 25 Motor release switch: Position “ON”: motor released for operation Position “OFF”: motor locked against operation 26 Function key for hand control: Brief actuation: activation/deactivation of the coolant pump Press for more than three seconds (with the motor inactive): switching to device settings menu 29 Lever: Actuator for reference speed setting
30
Note This motor cable cannot be used in connection with a foot control device. The motor coupled to this motor cable can only be activated if the motor release switch is in the “ON” position. 2.4.12 Motors with motor-side plug connection GD674, GD676, GD677, GD678 and GD679 GD685
Fig. 4 Legend 30 Motor release switch Note This motor cable can only be used in conjunction with a foot control. The motor coupled to this motor cable can only be activated if motor release switch 30 is in the “ON” position. When using two motor cables GD672 at the same time, a motor can be activated only if it has been released (motor release switch 30 in “ON” position) and the other motor is deactivated (motor release switch 30 in “OFF” position). microspeed uni motor cable with hand control GD673
29
Fig. 5
14
25
26
Note Motor cable GD672 or GD673 is required for connecting motors with motor-side plug connection to the control unit! For performance data and adjustable parameters for the individual motor types, see Technical data. The motor GD677 is no longer available. microspeed uni motors GD674, GD676, GD677 and GD678 GD679 Depending on the field of application, five different motor types can be selected with the three standard Aesculap coupling systems Hi-Line (or Hi-Line XS), micro-Line (Intra-coupling system as per DIN 13940 or ISO 3964) and mini-Line. Each motor can be operated in right or left (clockwise or counterclockwise) rotation mode. When in left-rotation mode, control unit 1 emits an acoustic signal. Motor types GD678 and GD679 offer the option to select a saw program. In this saw program the maximum speed setting is limited to 16 000 1/min.
microspeed uni perforator driver GD685
microspeed uni shaver handpieces GD681 and GD682
Note The perforator driver GD685 was modified. Above series number SN:0700, the maximum speed setting has been increased to 1 200 1/min. The modified motor (imprinted with 1 200) can be operated without limitation only on software version 4.00/4.00 (or higher). Older perforator drivers (up to SN:0699 or not imprinted with 1 200) can be upgraded. For upgrades, please consult your national B. Braun/Aesculap agent, see Technical Service. Improper use can result in injury to the dura mater and brain tissues! The perforator driver GD685 is fitted with a HUDSON tool coupling.
Note When using the shaver handpieces GD681 and GD682 a surgical suction device must be used.
Note The operator is responsible for the compatibility and proper, safe use of the tools used with this applied part. The perforator driver GD685 can be used both with the foot control GD668 or GD671 (in conjunction with the motor cable GD672) and with the hand control (motor cable GD673). The perforator driver can only be operated in right-rotation mode; left rotation is disabled. 2.4.13 Motors with fixed motor cable GD675, GD681 and GD682 GD684 Note The motors are directly connected to the control unit. An additional motor cable is not required. For performance data and adjustable parameters for the individual motor types, see Technical data. microspeed uni XS Highspeed motor GD675 Note The XS Highspeed motor GD675 can only be operated with the control unit software version 3.01/3.01 (or higher)! The microspeed uni XS Highspeed motor GD675 is fitted with a Hi-Line XS coupling. The XS Highspeed motor GD675 can be operated in both left and right rotation. When in left-rotation mode, control unit 1 emits an acoustic signal. The microspeed uni XS Highspeed motor GD675 can be used if only one XS Highspeed motor GD675 has been connected to the control unit 1. If a shaver handpiece GD682 and a XS Highspeed motor GD675 are connected to the control unit at the same time, the motor connected to the left motor socket is switched to active status after activation (or poweron self-test). Operation can be switched to the other motor by pressing the appropriate control key on the display in the inactive motor control panel, only if the motor is not active (see Selecting the motor circuit with a simultaneous connection of an XS Highspeed motor GD675 and shaver handpiece GD682).
► Only use authentic Aesculap blades! ► Always observe the instructions for use of blades TA011579.
Two types of blade are available for shaver handpieces GD681 and GD682: Burrs and shaver blades. Control unit 1 recognizes whether the coupled blade is a burr or a shaver blade. The respective operating mode (burr or shaver blade) is indicated on the display. An acoustic signal is emitted whenever a blade of a different type is inserted, and the respective symbol is displayed in the appropriate motor control panel. Operating mode “Burr”: With a burr coupled, the motor can be operated in right or left rotation, but not in oscillating mode. The maximum speed setting is limited to 8 000 1/min (with an acoustic signal emitted by control unit 1 when a motor is running in left-rotation mode). The symbol for the operating mode “Burr” is displayed in the motor control panel. Operating mode “Shaver blade”: With a shaver blade coupled, the motor can be operated in right or left rotation as well as in oscillating mode. The maximum speed setting is limited to 5 000 1/min. The symbol for the operating mode “Shaver blade” is displayed in the motor control panel.
15
Aesculap® microspeed uni motor system
microspeed uni shaver handpiece with hand control GD681
Operating mode “Burr”: The symbol for the operating mode “Burr” is displayed in the motor control panel. Note When the operating mode “Burr” is preselected, the handpiece can be operated in right or left rotation, but not in oscillating mode. ► To activate right rotation: Briefly press front trigger 41.
36
41 42
38
40
Fig. 6 Legend 36 Suction control lever: Lever for regulating suction performance 38 Tube connector: Connection to the surgical suction device via a suction tube 41 Front trigger (clockwise) 42 Rear trigger (oscillating mode) Note The shaver handpiece with hand control GD681 can only be operated with control unit software version 3.01/3.01 (or higher). The shaver handpiece GD681 is activated by briefly pressing the appropriate trigger. The shaver handpiece GD681 runs at the maximum speed setting in the display. The motor is stopped again by pressing any trigger (front trigger 41 or rear trigger 42). ■ Two shaver handpieces with hand control GD681 can be connected to the control unit at the same time. ■ One shaver handpiece with hand control GD681 and one shaver handpiece GD682 can be connected to the control unit at the same time. ■ If two shaver handpieces GD681 are connected to the control unit before it is switched on, the motor connected to the left motor socket will be switched to active status after activation (or power-on selftest). There is a special operating mode for using the shaver handpiece with hand control GD681 and foot control GD671. ► For more information in this respect, please contact your national B. Braun/Aesculap agency, see Technical Service.
16
The motor direction indicator for right rotation is illuminated in the motor control panel, and shaver handpiece 40 runs clockwise. ► To activate left rotation: Briefly press front trigger 41 and rear trigger 42 at the same time. The motor direction indicator for left rotation is illuminated in the motor control panel, and shaver handpiece 40 runs counterclockwise. Control unit 1 emits an acoustic signal. ► To stop the motor: Briefly press any of the two triggers (front trigger 41 or rear trigger 42). Operating mode “Shaver blade”: The symbol for the operating mode “Shaver blade” is displayed in the motor control panel. Note When the operating mode “Shaver blade” is preselected, the handpiece can be operated in right and left rotation as well as in oscillating mode. ► To activate right rotation: Briefly press front trigger 41.
The motor direction indicator for right rotation is illuminated in the motor control panel, and shaver handpiece 40 runs clockwise. ► To activate left rotation: Briefly press front trigger 41 and rear trigger 42 at the same time. The motor direction indicator for left rotation is illuminated in the motor control panel, and shaver handpiece 40 runs counterclockwise. ► To activate oscillating mode: Briefly press rear trigger 42. The motor direction indicators for left and right rotation in the motor control panel are illuminated alternately. Shaver handpiece 40 alternately runs clockwise and counterclockwise. ► To stop the motor: Briefly press any of the two triggers (front trigger 41 or rear trigger 42).
microspeed uni shaver handpiece GD682
microspeed uni mini pistol handpiece GD684
34
36
38
Fig. 7
35
Legend 36 Suction control lever: Lever for regulating suction performance 38 Tube connector: Connection to the surgical suction device via a suction tube Note The shaver handpiece GD682 must be used with foot control GD671. Shaver handpiece GD682 can be used if: ■ a motor with motor cable GD673 is connected at the second motor connection socket, or ■ a shaver handpiece with hand control GD681 is connected at the second motor connection socket, or ■ a pistol handpiece GD684 is connected at the second motor connection socket, or ■ a motor with motor cable GD672 is connected at the second motor connection socket and the motor release switch of that cable is in its “OFF” position, or ■ only one shaver handpiece GD682 is connected to control unit 1. If a shaver handpiece GD682 and a XS Highspeed motor GD675 are connected to the control unit at the same time, the motor connected to the left motor socket is switched to active status after activation (or poweron self-test). Operation can be switched to the other motor by pressing the appropriate control key on the display in the inactive motor control panel, only if the motor is not active (see Selecting the motor circuit with a simultaneous connection of an XS Highspeed motor GD675 and shaver handpiece GD682).
Fig. 8 Legend 34 Upper trigger 35 Lower trigger Note The pistol handpiece can be locked against inadvertent actuation by gently pressing and turning the upper trigger by 90°. The pistol handpiece cannot be used with foot control. The pistol handpiece GD684 is fitted with the Aesculap mini-Line coupling system. A protective sleeve is supplied with the handpiece. This sleeve serves to protect against injury and damage when inserting Kirschner wires. There are two operating modes for the pistol handpiece GD684: ■ Standard operation ■ Oscillating or tapping mode
17
Aesculap® microspeed uni motor system
When control unit 1 recognizes that a pistol handpiece GD684 is connected, the pistol handpiece operates in standard mode (default setting). The device parameter settings (maximum speed setting, delivery rate, pump status) can be changed only via the touch control panel of control unit 1. Oscillating or tapping mode can be preselected via the instruction menu. The symbol for “Oscillating or tapping mode” is displayed in the respective motor control panel. Oscillating or tapping mode is activated via the upper trigger. An acoustic warning signal is emitted and“ Oscillating or tapping mode active” flashes in the respective motor control panel. In this operating mode, the maximum speed setting cannot be changed via the touch control panel on control unit 1. The oscillating or tapping mode can be deactivated again via the upper trigger. On system power-up and each time the pistol handpiece is connected, the “oscillating or tapping” mode is deactivated by default and has to be reactivated via the pistol handpiece. The setting selected in the instruction menu is saved and remains in the memory even after system restart. Standard operation: Right and left rotation mode (when in left-rotation mode, control unit 1 emits an acoustic signal). Motor direction switch/trigger for left rotation 34, see Fig. 8: ■ Pressing lower trigger 35 while holding down upper trigger 34 makes the pistol handpiece operate in left-rotation mode. ■ The motor direction is changed by pressing trigger 34 with trigger 35 already actuated. Motor speed control trigger 35: ■ Actuator for reference speed setting (motor speed proportional to the actuation stroke). ■ If only trigger 35 is pressed, the pistol operates in right rotation mode. Oscillating or tapping mode: Activating or deactivating the operating mode: see Fig. 8: ■ This operating mode is activated (and deactivated) by pressing and holding upper trigger 34 for three seconds. Working in “Oscillating or tapping mode”: ■ The pistol handpiece is operated in tapping mode by pressing lower trigger 35 within the first half of the total actuation stroke. The motor speed is proportional to the actuation stroke. Tapping mode means: Clockwise angled rotation (forwards) followed by counterclockwise rotation (backwards) at a smaller angle. ■ The pistol handpiece is operated in oscillating mode by pressing lower trigger 35 within the second half of the total actuation stroke. The motor speed is proportional to the actuation stroke. Oscillating mode means: Clockwise angled rotation followed by counterclockwise rotation at the same angle. The pistol handpiece is operated in left-rotation mode by pressing lower trigger 35 at the same time as upper trigger 34.
18
2.4.14
Foot controls
Note The microspeed uni motor system contains two different foot controls (GD668 and GD671). Only one foot control can be connected to control unit GD670 at the same time. microspeed uni one-pedal foot control GD668 18
22
23
Fig. 9 Legend 18 Function key for foot control: Brief actuation: Switching the coolant pump on and off; actuation for more than three seconds (with the motor is inactive): switching to device settings menu 22 Motor direction changeover switch: Selection of right or left rotation 23 Pedal Actuator for reference speed setting
microspeed uni two-pedal foot control GD671
3.
Preparation and setup
Non-compliance with the following instructions will preclude all responsibility and liability in this respect on the part of Aesculap. ► When setting up and operating the product, adhere to – national regulations for installation and operation, – national regulations on fire and explosion protection. – Instructions for use according to IEC/DIN EN regulations.
18
Note For the safety of patients and users it is essential that the mains power cord and, especially, the protective earth connection are intact. In many cases defective or missing protective earth connections are not registered immediately. ► Using the potential equalization lead 17 mounted to the rear panel of
the device, connect the device to the potential equalization system of the room used for medical purposes. Note The potential equalization lead can be ordered from the manufacturer as art. no. GK535 (4 m length) or TA008205 (0.8 m length).
20
19
Fig. 10 Legend 18 Function key for foot control: Brief actuation: activation/deactivation of the coolant pump Actuation for more than three seconds (with the motor inactive): switching to device settings menu 19 Right pedal: Actuator for reference speed setting in right rotation 20 Left pedal: Actuator for reference speed setting in left rotation
WARNING
Fire and explosion hazard! ► Do not use the control unit and motors in potentially explosive areas.
The foot control circuit is ignition-safe and approved for operation in medical environments according to IEC /DIN EN 60601-1.
3.1
First use
WARNING
Risk of injury and/or product malfunction due to incorrect operation of the electromedical system! ► Adhere to the instructions for use of any medical device.
Note The control unit can be mounted on a Aesculap mobile rack for microspeed uni (height-adjustable) GA411 or on a Aesculap mobile rack for surgical devices GD416M. Other Aesculap devices must not be stacked on top of the control unit.
19