BBraun
Ennovate – FRI Instruments
258 Pages
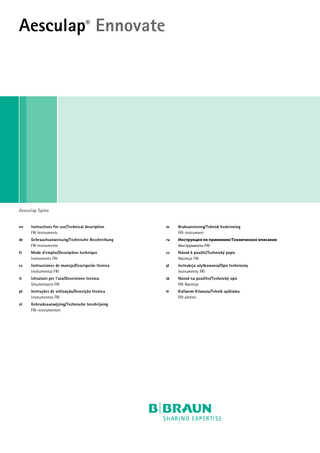
Preview
Page 1
Aesculap® Ennovate
Aesculap Spine
en
Instructions for use/Technical description FRI Instruments
sv
Bruksanvisning/Teknisk beskrivning FRI-instrument
de
Gebrauchsanweisung/Technische Beschreibung FRI Instrumente
ru
Инструкция по примению/Техническое описание Инструменты FRI
fr
Mode d’emploi/Description technique Instruments FRI
cs
Návod k použití/Technický popis Nástroje FRI
es
Instrucciones de manejo/Descripción técnica Instrumental FRI
pl
Instrukcja użytkowania/Opis techniczny Instrumenty FRI
it
Istruzioni per l’uso/Descrizione tecnica Strumentario FRI
sk
Návod na použitie/Technický opis FRI Nástroje
pt
Instruções de utilização/Descrição técnica Instrumentos FRI
tr
Kullanım Kılavuzu/Teknik açiklama FRI aletleri
nl
Gebruiksaanwijzing/Technische beschrijving FRI-instrumenten
en
Aesculap® Ennovate FRI Instruments Legend 1 2 3 4 5 6 7 8 9
Ennovate FRI downtube SZ405R Ennovate FRI insert pusher, short SZ406R Ennovate FRI rod pusher, short SZ407R Ennovate FRI set screw driver, short SZ408R Ennovate FRI distraction arm SZ411R Ennovate FRI spindle C-ring SZ412R Ennovate/S4 FRI fixation nut wrench FW237R Ennovate/S4 FRI parallel distractor FW238R Ennovate/S4 FRI distraction spindle FW241R
The depictions in this document are schematic representations only and may deviate from the actual product.
Contents 1. 1.1 1.2 2. 2.1 2.1.1 2.1.2 2.1.3 2.1.4 2.2 2.2.1 2.2.2 2.2.3 3. 3.1 3.2 3.3 3.4
About this document... 3 Scope... 3 Warnings... 3 Clinical application... 3 Areas of application and restrictions on use... 3 Intended purpose... 3 Indications... 3 Absolute contraindications... 3 Relative contraindications... 3 Safety instructions... 3 Clinical user... 3 Product... 3 Sterility... 3 Operation... 3 Couple downtube SZ405R to pedicle screw... 4 Screw in pedicle screw with screwdriver SZ381R... 4 Determine rod length with rod length caliper SZ382R... 5 Adjust ligamentotaxis with insert pusher SZ406R and parallel distractor FW238R... 6 3.4.1 Mount insert pusher SZ406R in downtube SZ405R... 6 3.4.2 Mount parallel distractor FW238R on downtube SZ405R... 6 3.4.3 Adjust ligamentotaxis... 6 3.5 Perform angle correction/reposition with distraction spindle FW241R... 7 3.6 Adjust rod length with rod cutter FW206R... 7 3.7 Bend rod with french rod bender SZ270R... 7 3.8 Insert rod with rod inserter SZ384R/SZ385R... 7 3.9 Verify rod with rod indicator SZ387R... 8 3.10 Press rod and insert set screw... 9 3.10.1 Push rod with rod pusher SZ407R and insert set screw with set screw driver SZ408R... 9 3.10.2 Remove instruments and deactivate PolyLock®... 10 3.11 Remove downtube SZ405R with removal wrench SZ380R . . . 10 3.12 Recouple downtube SZ405R after accidental decoupling... 10 4. Validated reprocessing procedure... 11 4.1 General safety instructions... 11 2
4.2 4.3 4.4 4.5 4.6 4.6.1 4.6.2 4.6.3 4.6.4 4.7 4.7.1 4.7.2 4.8 4.8.1 4.8.2 4.9 4.9.1 4.10 4.10.1 4.10.2 4.10.3 4.11 4.11.1 4.11.2 4.12 4.12.1 4.12.2 4.12.3 4.13 4.14 4.15 5. 6. 7.
General information... 11 Reusable products... 11 Preparations at the place of use... 11 Preparation before cleaning... 11 Disassembling... 11 Downtube SZ405R and insert pusher SZ406R... 11 Rod pusher SZ407R and set screw driver SZ408R... 11 Parallel distractor FW238R and distraction arm SZ411R... 12 Distraction spindle FW241R... 12 Cleaning/disinfection... 12 Product-specific safety notes on the reprocessing procedure 12 Validated cleaning and disinfection procedure... 13 Manual cleaning/disinfection... 14 Manual cleaning with immersion disinfection... 14 Manual cleaning with ultrasound and immersion disinfection 15 Mechanical cleaning/disinfecting... 16 Mechanical alkaline cleaning and thermal disinfecting... 16 Mechanical cleaning/disinfection with manual pre-cleaning. 16 Manual pre-cleaning with a brush... 16 Manual pre-cleaning with ultrasound and brush... 17 Mechanical alkaline cleaning and thermal disinfecting... 17 Inspection... 18 Visual inspection... 18 Function test... 18 Assembling... 18 Downtube SZ405R... 18 Parallel distractor FW238R... 18 Distraction spindle FW241R... 18 Packaging... 19 Steam sterilization... 19 Storage... 19 Technical Service... 19 Li-ion batteries... 19 Symbols on product and packaging... 19
en 1.
About this document
Note General risks of surgical interventions are not described in these instructions for use.
1.1
Scope
These instructions for use apply to all products listed in the key. Note The applicable CE mark for the product can be found on the label or packaging of the product. ► For article-specific instructions for use and information on material
compatibility, see Aesculap Extranet at https://extranet.bbraun.com
1.2
Warnings
Warnings indicate hazards to patients, users and/or products that may emerge during the use of the product. Warnings are marked as follows: DANGER Indicates a potential danger. If it is not prevented, death or severe injuries may result. WARNING Indicates a potential danger. If it is not prevented, minor or moderate injuries may result. CAUTION Indicates a potential damage to property. If these are not prevented, the product may be damaged.
2.2
Safety instructions
2.2.1
Clinical user
General safety information CAUTION Federal law restricts this device to sale by or on order of a physician! To prevent damage caused by improper setup or operation, and to not compromise the manufacturer warranty and liability: ► Use the product only according to these instructions for use. ► Follow the safety and maintenance instructions. ► Ensure that the product and its accessories are operated and used only by persons with the requisite training, knowledge and experience. ► Store any new or unused products in a dry, clean, and safe place. ► Prior to use, check that the product is in good working order. ► Keep the instructions for use accessible for the user. Note The user is obligated to report all severe events in connection with the product to the manufacturer and the responsible authorities of the state in which the user is located. Notes on surgical procedures It is the user's responsibility to ensure that the surgical procedure is performed correctly. Appropriate clinical training as well as a theoretical and practical proficiency of all the required operating techniques, including the use of this product, are prerequisites for the successful use of this product. The user is required to obtain information from the manufacturer if there is an unclear preoperative situation regarding the use of the product. 2.2.2
2.
Clinical application
2.1
Areas of application and restrictions on use
2.1.1 Intended purpose The Ennovate instruments are used for the implantation of Ennovate Spinal System implants. 2.1.2 Indications Note Use of the product contrary to the indications mentioned above and/or described applications is outside the manufacturer's liability. Indications are described in the instructions for use of Ennovate implants TA014887. 2.1.3 Absolute contraindications Absolute contraindications are described in the instructions for use of Ennovate implants TA014887. 2.1.4 Relative contraindications Relative contraindications are described in the instructions for use of Ennovate implants TA014887.
Product
Product specific safety information ► Observe the instructions for use of the Ennovate handles TA015007, Ennovate implants TA014887 and EnnovateMIS instruments TA014987 and operating manuals O48102 and O00702. ► Use only Aesculap Ennovate instruments and accessories. ► Hints on inserting the instruments into the supports: Observe the graphic/packing template. 2.2.3 Sterility The product will be delivered non-sterile. ► Clean brand-new product after removing the transport packaging and before the first sterilization.
3.
Operation
WARNING Risk of injury and/or malfunction! ► Check product for loose, bent, broken, cracked, worn or broken parts before every application. ► Always carry out a function test prior to each use of the product. CAUTION Instrument can fall in situ or on the floor! Handle can loosen during use! ► Check the seating of the coupling handles on the instruments for tightness. Note All handles and handle surfaces are black. All actuating elements that are actuated during the operation are gold colored.
3
en ► For information on preparing the screw holes and for installing
cementable screws, see usage instructions Ennovate instruments for MIS access TA014987. PolyLock® PolyLock® can be used to temporarily block the polyaxiality of a polyaxial pedicle screw by means of specialized instruments of the Ennovate system, without using a rod or a locking screw in doing so. In this way, the polyaxial screw temporarily becomes a monoaxial screw. The procedure for activating and deactivating PolyLock® is described in the relevant chapters of these instructions for use. PolyLock® can be activated and deactivated multiple times during instrumentation. Note PolyLock® does not necessarily have to be loosened before the final interlocking of the polyaxial screw using the rod and locking screw.
3.1
Couple downtube SZ405R to pedicle screw
Before a pedicle screw can be screwed into the pedicle, the screw is connected to the downtube 1. CAUTION Operation delay! Damage to the pedicle screw, the set screw and the downtube from loosening of the screw interlock from the downtube! ► Check that the pedicle screw is solidly fastened. ► Visually inspect correct seating of the support arms in the screw head. ► Tighten gold colored sleeve on downtube only by hand or with downtube locking wrench SZ379R. Do not use additional any additional tools.
1 a
b
c
d
1 a
Note If necessary, the downtube locking wrench SZ379R can be pushed over the downtube in order to additionally tighten the connection and secure it against loosening.
3.2
Screw in pedicle screw with screwdriver SZ381R
To screw in the Ennovate pedicle screw, it is connected with the screwdriver. To do so, the pedicle screw must already be fastened completely in the downtube. DANGER Injury to spinal cord, nerve root and blood vessels due to piercing of the cortex and faulty screw placement or inspection due to screw loosening when used improperly! ► Align and install pedicle screws only under radiographic control or with the aid of a navigation system. ► Ensure axial alignment of the pedicle screw to the K-wire when screwing in. When doing this, make sure that the K-wire remains in its position. ► Check the cannulation of the screwdriver for passage before every use. ► Remove K-wire before the screw is completely screwed in. ► Do not remove K-wire too early, as otherwise the pedicle screw guide will fail. CAUTION Operation delay! Damage to the pedicle screw, the set screw and by loosening the screwdriver from the screw! Torque cannot be transferred! ► Completely connect the screwdriver with the screw so that the marking line on the screwdriver terminates with the end of the downtube. ► Check that the pedicle screw is securely fastened to the screwdriver. ► Verify the axial alignment of the pedicle screw to the screwdriver. ► Do not hold the gold colored sleeve of the screwdriver when screwing in the pedicle screw. Use the clamp sleeve for holding purposes.
d
a e SZ379R Fig. 1
1
a
d
► Pull gold color sleeve a of the downtube 1 back against the spring
mechanism up to the stop so that the retaining lugs b are visible. ► Push the downtube 1 with the retaining lugs b into the interface c on
the screw head of the pedicle screw d in this position until an acoustic signal can be heard. This signals the latching of the downtube into the screw head. ► Visually inspect the connection between the downtube 1 and the pedicle screw d. ► Release the gold colored sleeve a. The downtube 1 is moved forward over the pedicle screw d via the spring mechanism. ► Fasten pedicle screw d to the downtube: tighten gold colored sleeve a counter-clockwise (left-hand thread) to the stop and simultaneously hold the downtube 1 securely against it. Fastening is complete when the marking (line and lock) is visible.
4
b
Fig. 2
c
h g f
en ► Insert screwdriver SZ381R a into the downtube 1 until the tip b of the
screwdriver is located in the inner profile of the screw head c and thus axially aligned to the screw shaft. ► Turn the screwdriver SZ381R a into the thread of the screw body by rotating the gold colored sleeve e of the screwdriver clockwise. Securely hold the gold colored sleeve d of the downtube 1 while doing so. Fastening is complete when the marking line f on the screwdriver SZ381R a terminates with the end of the downtube 1 and the polyaxial alignment of the screw (when using polyaxial screws) is completely blocked. ► Push preferred handle g (SZ222R to SZ225R) onto the hex connection of the screwdriver SZ381R a up to the stop. Note The handles have a rotation direction setting in which the three positions of screw in (IN), locked (∙), and screw out (OUT) can be set. ► Set rotation direction setting on the handle to “IN”. ► Carefully guide the connected instruments over the K-wire h and screw
in pedicle screw by rotating clockwise several rotations under radiographic control. Do not hold the screwdriver SZ381R a by the gold colored sleeve e while doing so, as otherwise the screwdriver will release from the screw. ► Once the pedicle screw has sufficient hold in the bone, remove Kwire h to prevent further advancing of the K-wire. The K-wire pliers SZ367R can be used together with the slotted hammer SZ368R for this purpose. ► Insert the pedicle screw under radiographic control up to the desired depth. – When using polyaxial screws, ensure that the polyaxial alignment of the pedicle screw is ensured and the screw body does not strike against any anatomical structures. – When using monoaxial screws, ensure that the downtubes are aligned to each other so that the other instrumentation steps can be carried out. CAUTION Operation delay! Damage to the pedicle screw, the set screw and the downtube and from loosening of the screw interlock from the downtube! ► When loosening the screwdriver, do not hold the gold colored sleeve of the downtube, or do not release the gold colored sleeve of the downtube. ► After removing the screwdriver, verify solid fastening of the pedicle screw with the downtube and tighten as applicable. ► Release screwdriver SZ381R a from the downtube 1: release screw-
driver from the pedicle screw by turning the gold colored sleeve e counter-clockwise and remove from the downtube 1. ► Remove handle g by actuating the black sleeve on the handle of the screwdriver SZ381R a. ► Verify position and size of the pedicle screw before placing the rod with intraoperative imaging.
3.3
Determine rod length with rod length caliper SZ382R
The necessary rod length is determined with the rod length caliper SZ382R. Note The determination of rod length is only an estimate. The final selection of rod length must be made by the operator. WARNING Screwing in or unscrewing of polyaxial screw by alignment (axial twisting) of the clamp sleeve after activation of PolyLock®! ► Do not axially twist clamp sleeve if the PolyLock® is activated. ► Align rod slots/rod grooves of the clamp sleeve before activating PolyLock®. WARNING Screwing in or unscrewing of monoaxial screw by alignment (axial twisting) of the downtube! ► Align rod slots/rod grooves on the downtube under radiographic control. CAUTION Rod length cannot be determined! ► Align downtubes parallel to each other for measurement of the rod length with the rod length caliper. When using monoaxial screws, the downtubes cannot be subsequently aligned parallel. ► Take any subsequent distraction into account when determining the
rod length. ► Ensure that the guide grooves a of the downtubes 1 are laterally
aligned, so that there is sufficient space later for the distraction instruments. a a
b b
c
c
1
1
d 1 e
1
e
Fig. 3 ► Guide rod length caliper b with both hollow cylinders c over both outer
downtubes 1 (cranial and caudal downtube). Ensure that both downtubes are aligned parallel to each other. ► Read the rod length through the window d in the slide unit. Note The length indicated on the scale indicates the actual rod length that is present. If the measured rod length is between two existing lengths, the two closest rod lengths are indicated in the window d with small arrows. The operator must decide which rod length to choose. Insertion tip and rod hex are already considered in the rod length specification. ► Remove rod length caliper b from the downtubes 1. ► Align downtubes 1 with the grooves in the rod direction. To do so, set
rod length caliper b inclined by 90° in recesses e of the downtubes 1.
5
en 3.4
Adjust ligamentotaxis with insert pusher SZ406R and parallel distractor FW238R
3.4.2 Mount parallel distractor FW238R on downtube SZ405R ► Mount parallel distractor 8, see Chapter 4.12.2.
WARNING Insufficient treatment or stabilization of the spinal column region to be treated! Damage to the implant and/or instruments! ► For the final tightening of the locking screws and when activating PolyLock®, use only 10 Nm torque handle SZ228R. ► Verify the correct seating of the distraction arms on the parallel distractor before every corrective maneuver. WARNING Injury to patient from initiation of high torques on the spinal column! ► Before activating PolyLock® use the premounting instrument to ensure that the clamp sleeve is completely connected to the pedicle screw. ► Before activating PolyLock® using the prefixing instrument, always use the counterholder. ► Never use parallel distractor or distraction spindle for counterholding. ► Hold counter torque handle in position and do not twist against the downtube or the inserted rod. 3.4.1
Mount insert pusher SZ406R in downtube SZ405R
8
8
a a
5
5
b
b
Fig. 5 ► Mount distractor arms 5 on inner or outer receptacles a on the parallel
distractor 8. Ensure correct alignment of the studs b on the distractor arms 5. ► Verify solid seating of the distractor arms 5 on the parallel distractor 8. Note Alternatively, the parallel distractor handle SZ231R can also be used with the distractor arms 5, see TA014987.
b 2 a
c
8 1 5 c
1 1 Fig. 6 ► Insert parallel distractor 8 with mounted distractor arms 5 with the
Fig. 4 ► Align insert pusher 2 with the side of the longer rod slot a in the cranial
studs b into the lateral guide grooves c of the cranial and caudal downtube 1 and push down to the stop in the guide grooves c. ► Carry out the same process on the contra-lateral side with a second parallel distractor 8 with mounted distractor arms 5. 3.4.3
Adjust ligamentotaxis
direction or the side from which the rod is to be inserted.
b
► Insert the pre-mounting instrument 2 from above into the clamp
sleeve 1 and turn golden threaded sleeve b of the pre-mounting instrument 2 using the handle SZ390R c in the clamp sleeve 1 clockwise all the way. In doing so, make sure that the lordosis or kyphosis correction angle has been observed and considered before the PolyLock® is activated. ► Repeat procedure for all additional clamp sleeves 1. In doing so, make sure that the clamp sleeves are arranged in a line during the activation of PolyLock®.
a c 2 1
Note The activation of PolyLock® is not required in the case of monoaxial screws. For monoaxial screws, the pre-mounting instruments only need to be tightened slightly using the handle SZ390R.
d 7
Fig. 7 6
en Note The counter torque handle can be placed on the downtube in eight different positions.
3.6
► For polyaxial screws: Activate PolyLock®:
3.7
– Slide counterholder handle SZ392R a all the way on the head of the clamp sleeve 1. – Slide the torque handle SZ228R b all the way onto the hex connection of the PolyBlockers SZ393R c. – Insert the torque handle SZ228R b with mounted PolyBlocker SZ393R c from above into the head of the clamp sleeve 1 and screw in golden threaded sleeve of the prefixing instrument 2 all the way. – Turn the torque handle SZ228R b clockwise until the acoustic signal of the triggering torque handle sounds. The acoustic signal indicates that the PolyLock® is activated. – Remove the torque handle SZ228R b with mounted PolyBlocker SZ393R c from the pre-mounting instrument 2. – Remove counter holder SZ392R a. – Repeat procedure for any additional clamp sleeves 1. ► Adjust desired ligamentotaxis by turning the golden adjusting screw d on the parallel distractor 8.
Adjust rod length with rod cutter FW206R
► If necessary, cut the rod to desired length with rod cutter FW206R to
the proper length.
Bend rod with french rod bender SZ270R
If necessary, the rod can be bent with the french rod bender SZ270R. Three different bending radiuses can be set on the french rod bender. Note Alternatively, the rod bending forceps FW024R can also be used with titanium rods. WARNING Danger of injury from damage (breakage) of the rod if bent incorrectly! Rod cannot be inserted into the downtube! Rod cannot be fastened! ► Avoid severe rod bending in the region of the pedicle screw. ► Only bend rod with provided french rod bender. ► Do not bend rod multiple times at the same location. ► Do not bend back the rod.
Note The fixation nut wrench 7 can be used to assist. ► Repeat procedure on the opposite parallel distractor 8.
From this point, the distraction is held.
c
► Check rod length again after the maneuver is performed.
3.5
Perform angle correction/reposition with distraction spindle FW241R
If necessary, the natural lordosis/kyphosis can be restored with the distraction spindle FW241R.
6 1
1 a
d a d
b
b Fig. 9
7 c
► Adjust desired bending radius on french rod bender a: pull rotary
9
knob b and set the desired radius by rotating. ► Place rod c between rotary knob b and the two rollers d.
Note The rod c has an orientation line that facilitates the alignment of the rod during the bending process Fig. 8 ► Push C-rings 6 correctly with the guide grooves a upward open on the
head of the downtube 1. Ensure that the guide grooves a point outward (laterally) so that there is sufficient space later for the distraction spindle 9. ► Mount spindle distractor 9, see Chapter 4.12.3. ► Insert the spindle distractor 9 with the studs b into the guide grooves a for the C-rings 6 on the cranial and caudal clamp sleeve 1. ► Repeat the same process on the contra-lateral side with a second distraction spindle 9. ► Adjust reposition by turning the golden adjusting screws c of the two distraction spindles 9. Ensure that downtubes 1 are aligned parallel in order to enable correct rod length measurement. Note The fixation nut wrench 7 can be used to assist.
► Bend rod c to the desired radius by actuating the handle of the french
rod bender a.
3.8
Insert rod with rod inserter SZ384R/SZ385R
WARNING Loss of the rod in situ or expansion of the skin incision required! ► Do not decouple rod inserter from the rod until the rod is completely fastened by at least one set screw. WARNING Revision required due to faulty fastening of the rod! ► Always place hex and point of the rod outside of the screw head. ► Select suitable rod lengths in consideration of any possible corrective maneuver to be performed (e.g. distraction). ► Verify rod positioning under radiographic control before fastening with the set screw. 7
en CAUTION Operation delay due to incomplete coupling of the rod on the rod inserter or incorrect alignment of the rod slot/rod grooves of the downtube! ► Insert rod up to the stop in the rod inserter and completely tighten fixation. ► Verify solid fixation of the rod in the rod inserter. ► Only tighten/loosen gold colored rotary knob on the rod inserter by hand. Do not use additional any additional tools. ► Align rod slots/rod grooves of the downtube before insertion of the rod. Note The MIS rods have a conical tip on one side for easier implantation through the soft tissue. On the opposite side of the rod, there is a hex that forms the solid interface to the rod inserter.
► Open the mouth part of the rod inserter SZ384R a/SZ385R b by turning
the gold colored rotary knob c counter-clockwise (up to the line mark with SZ384R a). ► Insert rod d with the hex into the mouth part e of the rod inserter a/b up to the stop. Note The rod can be aligned to the instrument with the orientation lines on the rod and on the rod inserter. ► Rotate the gold colored rotary knob c clockwise and tighten. Verify
solid fixation of the rod in the rod inserter and tighten if necessary. ► Guide the clamped rod d with the rod inserter a/b through the longitu-
dinal slot of the downtube 1. ► Do not decouple rod inserter a/b from the rod until the rod d is com-
pletely fastened by at least one set screw, see Chapter 3.10.
3.9 Note When using the long rod inserter SZ385R, an additional distal incision can be required.
Verify rod with rod indicator SZ387R
The rod indicator SZ387R is used in order to ensure that the rod was placed correctly by the downtubes. CAUTION Faulty display of the rod indicator due to tissue or instrument within the downtube! ► Before inserting the rod indicator, ensure that no tissue is present in the downtube and that no other instruments apart from the insert pusher are located in the downtube.
a c a c c
b
a 1
b
a 1
1
d
e d
d
Fig. 10 Fig. 12
c
c
► Insert rod indicator SZ387R a from the top into the downtube 1.
b b
1 e d
Fig. 11
8
d
d
Ensure that the rod indicator a lies flush with the large diameter on the head of the downtube. ► Read rod position on the window b of the rod indicator a. – If the "rod" label is visible, the rod was placed correctly. If the "no rod" label is visible, the rod is not in the downtube. ► If the rod is not located in the downtube: correct position of the rod. To do so, remove rod indicator SZ387R a from the downtube and insert rod again, see Chapter 3.8.
en 3.10 Press rod and insert set screw Once the rod has been placed through all downtubes and the position of the rod has been verified, the rod can be pressed into the screw head with the rod pusher. In the same step, the set screw is inserted and tightened with the set screw driver SZ408R. DANGER Risk of severe injury! Pedicle screw can tear out of the spinal column if too much force is applied when pushing the rod! ► Make sure that the forces applied when turning the gold colored sleeve of the rod pusher to the marking "0" are not high. When the marking "0" is reached, the forces are no longer transmitted to the screw, but rather converted into the interlock of the polyaxiality (PolyLock®). WARNING Insufficient stabilization of the spinal column region to be treated due to undertightening the set screw! Risk of damage to the implant or instruments due to overtightening of the set screw! ► For the final tightening of the locking screws and when activating PolyLock®, use only 10 Nm torque handle SZ228R. ► Check the recalibration/maintenance date on the torque wrench handle maintenance label prior to each use. ► When tightening or loosening the set screws, make certain that the working end of the torque wrench handle shaft is positioned entirely within the socket of the set screws. ► Apply the torque slowly and without sudden movement until the torque wrench handle release is audibly triggered. WARNING Injury to patient from initiation of high torques on the spinal column! ► For tightening of the locking screws and when activating PolyLock®, always use the counterholder SZ392R. ► Never use parallel distractor or distraction spindle for counterholding. ► Hold counter torque handle in position and do not twist against the downtube or the inserted rod. CAUTION Operation delay! Set screw cannot be screwed into screw head! Rod cannot be fixated! ► Do not use set screw driver without rod pusher when screwing set screw in and out. ► Follow correct sequence: first combine set screw driver with rod pusher and then receive set screw. ► Receive set screw correctly and completely up to the line marking with the set screw driver. ► Turn rod pusher completely downwards until the "0" marking on the gold colored sleeve of the rod pusher terminates flush with the head of the clamp sleeve. ► Do not screw rod pusher into the downtube before the insert pusher has been screwed into the downtube up to the stop. ► Never unscrew the set screw driver out of the rod pusher before the set screw is completely locked in the pedicle screw.
3.10.1 Push rod with rod pusher SZ407R and insert set screw with set screw driver SZ408R
4 e a
3
d
b
4
g
c
f
Fig. 13 ► Insert the set screw driver 4 up to the stop in the cannulation of the
rod pusher 3. ► Turn set screw driver 4 clockwise until it is visible in the front in the
rod pusher 3 and can be moved back and forth approx. 10 mm. ► Completely receive set screw with the combined instrument. To do so,
insert the working end a of the set screw driver 4 into the socket of the set screw b and push with light pressure until the line marking c on the set screw driver 4 terminates flush with the surface of the set screw b. ► Verify solid seating of the set screw b on the set screw driver 4. ► Guide combined instrument with mounted set screw b from above into the downtube 1 and turn golden sleeve d of the rod pusher 3 by hand or with rod pusher handle SZ390R e in downtube 1 clockwise. Rod f is pushed down. The scale g on the rod pusher 3 indicates the remaining reduction path.
i
g
1 h
3
f
Fig. 14 Note The counter torque handle can be placed in eight different positions. ► Push counter torque handle SZ392R h from above on the head of the
downtube 1 up to the stop. ► Push rod f down completely.
The rod f is completely in the screw head when the scale g on the rod pusher 3 reaches the "0" marking.
9
en ► Slide torque handle SZ228R i all the way onto the hex connection of
3.11 Remove downtube SZ405R with removal wrench SZ380R
the insertion instrument for the locking screw 4. ► Screw in the set screw b by turning the torque wrench handle SZ228R i clockwise. Hold the counter-holding handle h securely in position until the acoustic signal of the triggering torque wrench handle sounds. The acoustic signal indicates that 10Nm have been reached and the PolyLock® is activated. ► Remove torque handle SZ228R i and counter-holding handle h.
WARNING Operation delay! Downtube cannot be removed! ► Loosen gold colored sleeve of the downtube one to two clockwise rotations before inserting the removal wrench.
3.10.2 Remove instruments and deactivate PolyLock®
► Ensure that all instruments have been removed from the downtube 1. ► Loosen gold colored sleeve a on downtube 1 one to two clockwise rev-
olutions until the line marking is no longer visible. j i k
e
b
4 6
b
l
m 9 1
8 1
b
h
a 1 f
90°
c
1
n
Fig. 15 ► Pull set screw driver 4 out of the set screw b by pulling on the shaft
until it contacts on the inside of the shaft of the rod pusher 3. Note The handle SZ390R e can be used to facilitate unscrewing the pre-mounting instrument 2 and the rod pusher 3. ► Unscrew rod pusher 3 counter-clockwise out of the downtube 1 and
remove together with the set screw driver 4. ► Decouple rod inserter j from the rod f by turning the golden rotary knob k counter-clockwise and remove. ► Loosen golden adjusting screws m on the distraction spindles 9 and remove the distraction spindles 9 from the guide grooves of the Crings 6. ► Loosen golden adjusting screws n on parallel distractors 8 and remove parallel distractors 8 from the guide grooves of the downtubes 1. ► Remove C-rings 6 from downtubes 1. ► For polyaxial screws: Deactivate PolyLock®: – Slide torque handle SZ228R i all the way onto the hex connection of the PolyBlockers SZ393R l. – Insert torque handle SZ228R i with mounted PolyBlocker SZ393R l from above into the golden threaded sleeve of the prefixing instrument 2 and turn the torque handle SZ228R i counter-clockwise until the prefixing instrument 2 can be unscrewed without significant resistance. In doing so, hold the counterholder handle h securely in position. ► Unscrew insert pusher 2 by turning counter-clockwise and remove from downtube 1. ► Repeat procedure for additional downtubes 1.
10
Fig. 16 Note If necessary, the downtube locking wrench SZ379R can be used to make loosening easier. ► Insert removal key SZ380R b from above into the downtube 1 up to the
stop so that the line marking c terminates flush with the head of the downtube 1. ► Twist removal key b by 90° to the downtube and remove from the site together with the downtube 1 by pulling on the removal key b. ► Repeat procedure for additional downtubes.
3.12 Recouple downtube SZ405R after accidental decoupling If the pedicle screw is already screwed in and the downtube SZ405R was accidentally removed, the downtube can be reattached to the pedicle screw with the alignment instrument SZ399R. Note The procedure for recoupling is described in TA014987.
en 4. 4.1
Validated reprocessing procedure General safety instructions
Note Adhere to national statutory regulations, national and international standards and directives, and local, clinical hygiene instructions for sterile processing. Note For patients with Creutzfeldt-Jakob disease (CJD), suspected CJD or possible variants of CJD, observe the relevant national regulations concerning the reprocessing of products. Note Mechanical reprocessing should be favored over manual cleaning as it gives better and more reliable results.
4.3
Reusable products
There are no known effects of processing eresulting in damage to the product. The manufacturer provided proof of biocompatibility and processability for the product after 200 processing cycles. Careful visual and functional testing prior to next use is the best way to identify a malfunctioning product, see Chapter 4.11.
4.4
Preparations at the place of use
► If applicable, rinse non-visible surfaces preferably with deionized
water, with a disposable syringe for example. ► Remove any visible surgical residues to the extent possible with a damp, lint-free cloth. ► Transport the dry product in a sealed waste container for cleaning and disinfection within 6 hours.
Note Successful processing of this medical device can only be ensured if the processing method is first validated. The operator/sterile processing technician is responsible for this. The recommended chemistry was used for validation.
4.5
Note If there is no final sterilization, then a virucidal disinfectant must be used.
4.6.1 Downtube SZ405R and insert pusher SZ406R Note Downtube SZ405R cannot be completely dismantled.
Note For up-to-date information about reprocessing and material compatibility, see also the Aesculap Extranet at https://extranet.bbraun.com The validated steam sterilization procedure was carried out in the Aesculap sterile container system.
Preparation before cleaning
► Dismantle the product prior to cleaning, see Chapter 4.6. ► Open up products with hinges.
4.6
Disassembling
1
a
b 2
a
4.2
General information
Dried or affixed surgical residues can make cleaning more difficult or ineffective and lead to corrosion. Therefore the time interval between application and processing should not exceed 6 h; also, neither fixating precleaning temperatures >45 °C nor fixating disinfecting agents (active ingredient: aldehydes/alcohols) should be used. Excessive measures of neutralizing agents or basic cleaners may result in a chemical attack and/or to fading and the laser marking becoming unreadable visually or by machine for stainless steel. Residues containing chlorine or chlorides e.g. in surgical residues, medicines, saline solutions and in the service water used for cleaning, disinfection and sterilization will cause corrosion damage (pitting, stress corrosion) and result in the destruction of stainless steel products. These must be removed by rinsing thoroughly with demineralized water and then drying. Additional drying, if necessary. Only process chemicals that have been tested and approved (e.g. VAH or FDA approval or CE mark) and which are compatible with the product’s materials according to the chemical manufacturers’ recommendations may be used for processing the product. All the chemical manufacturer's application specifications must be strictly observed. Failure to do so can result in the following problems: ■ Optical changes of materials, e.g. fading or discoloration of titanium or aluminum. For aluminum, the application/process solution only needs to be of pH >8 to cause visible surface changes. ■ Material damage such as corrosion, cracks, fracturing, premature aging or swelling. ► Do not use metal cleaning brushes or other abrasives that would damage the product surfaces and could cause corrosion. ► Further detailed advice on hygienically safe and material-/value-preserving reprocessing can be found at www.a-k-i.org, link to Publications, Red Brochure – Proper maintenance of instruments.
Fig. 17 ► Remove mounted insert pusher 2 as applicable. To do so, turn insert
pusher 2 with rod pusher handle SZ390R in the direction of the arrow and unscrew from the downtube 1. ► Unscrew the gold-colored rotating sleeve a from the head b by turning it in the direction of the arrow and slide it in the direction of the arrow as far as the stop. 4.6.2
Rod pusher SZ407R and set screw driver SZ408R
3 4
Fig. 18 ► Remove mounted insert pusher for set screw 4. To do so, turn set screw
driver 4 in the direction of the arrow and unscrew under slight traction from the rod pusher 3.
11
en 4.6.3
4.7
Parallel distractor FW238R and distraction arm SZ411R
5
Cleaning/disinfection
4.7.1 Product-specific safety notes on the reprocessing procedure Damage or destruction of the product due to inappropriate cleaning agents/disinfectants and/or excessive temperatures! ► Use cleaning agents and disinfectants according to the manufacturer's instructions, – which are approved for plastics and high-grade steel, – that do not damage softeners (e.g., in silicone). ► Note information concerning concentration, temperature and exposure time. ► Do not exceed a disinfection temperature of 95 °C.
5
a ► Use suitable cleaning/disinfecting agents if the product is put away in
a
a wet condition. To prevent foam formation and reduced effectiveness of the process chemicals: Prior to mechanical cleaning and disinfection, rinse the product thoroughly with running water.
b b
8 Fig. 19 ► Remove mounted distraction arms 5 before cleaning as applicable. To
do so, push gold colored slide a on the distraction arm 5 in the direction of the arrow marking, hold down and remove distraction arm 5 in the direction of the arrow. ► Loosen gold colored clamping nuts b by turning in the direction of the arrow and completely remove parallel distractor 8. 4.6.4
Distraction spindle FW241R
a
9 Fig. 20 ► Unscrew gold colored clamping nuts a by turning in the direction of the
arrow and completely remove distraction spindle 9.
12
en 4.7.2
Validated cleaning and disinfection procedure
Validated procedure
Specific requirements
Manual cleaning with immersion disinfection
Chapter Manual cleaning/disinfection ■ Suitable cleaning brush and sub-chapter: ■ 20 ml disposable syringe ■ Chapter Manual cleaning with ■ Keep working ends open for cleaning. immersion disinfection ■ When cleaning products with movable hinges, ensure that these are
■ SZ408R ■ SZ411R/SZ412R ■ FW237R/FW238R ■ FW241R Manual cleaning with ultrasound and immersion disinfection
■ SZ405R–SZ407R
Reference
in an open position and, if applicable, move the joint while cleaning.
■ Drying phase: Use a lint-free cloth or medical compressed air Chapter Manual cleaning/disinfection ■ Suitable cleaning brush and sub-chapter: ■ Drying phase: Use a lint-free cloth or medical compressed air ■ Chapter Manual cleaning with ■ Before and after phase I: Clean lumens using a suitable bottle brush ultrasound and immersion disinunder running water until no residue is visible on the surface. In doing so, move moving parts.
fection
■ Phase IV: Rinse lumens with a water jet gun (3,8 bar of pressure) min. 3 times for each 20 s. Mechanical alkaline cleaning and thermal disinfection
■ Place the product in a tray that is suitable for cleaning (avoiding rins- Chapter Mechanical cleaning/disin-
■ SZ408R ■ SZ412R ■ FW237R ■ FW241R
■ Connect components with lumens and channels directly to the rins- ■ Chapter Mechanical alkaline clean-
Manual pre-cleaning with brush and subsequent mechanical alkaline cleaning and thermal disinfection
Chapter Mechanical cleaning/disin■ Suitable cleaning brush fection with manual pre-cleaning and ■ 20 ml disposable syringe sub-chapter: ■ Place the product in a tray that is suitable for cleaning (avoiding rins- ■ Chapter Manual pre-cleaning with
■ SZ411R ■ FW238R
ing blind spots).
ing port of the injector carriage.
fecting and sub-chapter: ing and thermal disinfecting
■ SZ408R: Manually pre-clean the product using a suitable cleansing brush if there are residues of bone, tissue or medical materials and supplies (e.g. casting compound, bone cement) present.
ing blind spots).
a brush
■ Chapter Mechanical alkaline cleaning and thermal disinfecting
Manual pre-cleaning with ultrasound and brush, and subsequent mechanical alkaline cleaning and thermal disinfection
■ SZ405R–SZ407R
Chapter Mechanical cleaning/disin■ Suitable cleaning brush fection with manual pre-cleaning and ■ Place the product in a tray that is suitable for cleaning (avoiding rins- sub-chapter: ing blind spots). ■ Chapter Manual pre-cleaning with ■ Connect components with lumens and channels directly to the rinsultrasound and brush ing port of the injector carriage. ■ Chapter Mechanical alkaline clean■ Manual Pre-Cleaning: ing and thermal disinfecting – Before and after phase I: Clean lumens using a suitable bottle brush under running water until no residue is visible on the surface. In doing so, move moving parts. – Phase IV: Rinse lumens using spray nozzle (3.8 bar water pressure) at least 3 times for 20 seconds each.
13
en 4.8
Manual cleaning/disinfection
► Prior to manual disinfecting, allow water to drip off for a sufficient
length of time to prevent dilution of the disinfecting solution. ► After manual cleaning/disinfection, check visible surfaces visually for
residues. ► Repeat the cleaning /disinfection process if necessary.
4.8.1
Manual cleaning with immersion disinfection
Phase
Step
T [°C/°F]
t [min]
Conc. [%]
Water quality
Chemical
I
Disinfecting cleaning
RT (cold)
>15
2
D–W
Aldehyde-free, phenol-free, and QUAT-free concentrate, pH ~ 9*
II
Intermediate rinse
RT (cold)
1
-
D–W
-
III
Disinfection
RT (cold)
15
2
D–W
Aldehyde-free, phenol-free, and QUAT-free concentrate, pH ~ 9*
IV
Final rinse
RT (cold)
1
-
FD-W
-
V
Drying
RT
-
-
-
-
D–W: Drinking water FD–W: Fully desalinated water (demineralized, low microbiological contamination: drinking water quality at least) RT: Room temperature *Recommended: BBraun Stabimed
► Note the information on appropriate cleaning brushes and disposable
syringes, see Chapter 4.7.2. Phase I ► Fully immerse the product in the cleaning/disinfectant for at least 15
min. Ensure that all accessible surfaces are moistened. ► Clean the product with a suitable cleaning brush in the solution until
all discernible residues have been removed from the surface. ► If applicable, brush through non-visible surfaces with an appropriate
cleaning brush for at least 1 min. ► Mobilize non-rigid components, such as set screws, links, etc. during
cleaning. ► Thoroughly rinse through these components with the cleaning disin-
fectant solution (at least five times), using a disposable syringe. Phase II ► Rinse/flush the product thoroughly (all accessible surfaces) under run-
ning water. ► Mobilize non-rigid components, such as set screws, joints, etc. during
rinsing. ► Drain any remaining water fully.
Phase III ► Fully immerse the product in the disinfectant solution. ► Mobilize non-rigid components, such as set screws, joints, etc. during
rinsing. ► Rinse lumens at least 5 times at the beginning of the exposure time
using an appropriate disposable syringe. Ensure that all accessible surfaces are moistened.
14
Phase IV ► Rinse/flush the product thoroughly (all accessible surfaces). ► Mobilize non-rigid components, such as set screws, joints, etc. during final rinse. ► Rinse lumens with an appropriate disposable syringe at least five times. ► Drain any remaining water fully. Phase V ► Dry the product in the drying phase with suitable equipment (e.g. cloth, compressed air), see Chapter 4.7.2.
en 4.8.2
Manual cleaning with ultrasound and immersion disinfection
Phase
Step
T [°C/°F]
t [min]
Conc. [%]
Water quality
Chemical
I
Ultrasonic cleaning
RT (cold)
>15
2
D–W
Aldehyde-free, phenol-free, and QUAT-free concentrate, pH ~ 9*
II
Intermediate rinse
RT (cold)
1
-
D–W
-
III
Disinfection
RT (cold)
15
2
D–W
Aldehyde-free, phenol-free, and QUAT-free concentrate, pH ~ 9*
IV
Final rinse
RT (cold)
1
-
FD-W
-
V
Drying
RT
-
-
-
-
D–W: Drinking water FD–W: Fully desalinated water (demineralized, low microbiological contamination: drinking water quality at least) RT: Room temperature *Recommended: BBraun Stabimed
► Note the information on appropriate cleaning brushes and disposable
syringes, see Chapter 4.7.2. Phase I ► Clean the product in an ultrasonic cleaning bath (frequency 35 kHz) for
at least 15 min. Ensure that all accessible surfaces are immersed and acoustic shadows are avoided. ► Clean the product with a suitable cleaning brush in the solution until all discernible residues have been removed from the surface. ► If applicable, brush through non-visible surfaces with an appropriate cleaning brush for at least 1 min. ► Mobilize non-rigid components, such as set screws, links, etc. during cleaning. ► Thoroughly rinse through these components with the cleaning disinfectant solution (at least five times), using a disposable syringe.
Phase IV ► Rinse/flush the product thoroughly (all accessible surfaces) under running water. ► Mobilize non-rigid components, such as set screws, joints, etc. during final rinse. ► Rinse lumens with an appropriate disposable syringe at least five times. ► Drain any remaining water fully. Phase V ► Dry the product in the drying phase with suitable equipment (e.g. cloth, compressed air), see Chapter 4.7.2.
Phase II ► Rinse/flush the product thoroughly (all accessible surfaces) under run-
ning water. ► Mobilize non-rigid components, such as set screws, joints, etc. during rinsing. ► Drain any remaining water fully. Phase III ► Fully immerse the product in the disinfectant solution. ► Mobilize non-rigid components, such as set screws, joints, etc. during
rinsing. ► Rinse lumens at least five times at the beginning of the exposure time
with an appropriate disposable syringe. Ensure that all accessible surfaces are moistened.
15
en 4.9
Mechanical cleaning/disinfecting
Note The cleaning and disinfection device must be of tested and approved effectiveness (e.g. FDA approval or CE mark according to DIN EN ISO 15883).
Note The cleaning and disinfection device used for processing must be serviced and checked at regular intervals.
4.9.1 Mechanical alkaline cleaning and thermal disinfecting Machine type: single-chamber cleaning/disinfection device without ultrasound Phase
Step
T [°C/°F]
t [min]
Water quality
Chemical/Note
I
Prerinse
<25/77
3
D–W
-
II
Cleaning
55/131
10
FD-W
■ Concentrate, alkaline: – pH = 13 – <5 % anionic surfactant
■ 0.5 % working solution – pH = 11* III
Intermediate rinse
>10/50
1
FD-W
-
IV
Thermal disinfecting
90/194
5
FD-W
-
V
Drying
-
-
-
According to the program for cleaning and disinfection device
D–W: Drinking water FD–W: Fully desalinated water (demineralized, low microbiological contamination: drinking water quality at least) *Recommended: BBraun Helimatic Cleaner alkaline
► Check visible surfaces for residues after mechanical cleaning/disinfect-
ing.
4.10 Mechanical cleaning/disinfection with manual pre-cleaning Note The cleaning and disinfection device must be of tested and approved effectiveness (e.g. FDA approval or CE mark according to DIN EN ISO 15883).
Note The cleaning and disinfection device used for processing must be serviced and checked at regular intervals.
4.10.1 Manual pre-cleaning with a brush Phase
Step
T [°C/°F]
t [min]
Conc. [%]
Water quality
Chemical
I
Disinfectant cleaning
RT (cold)
>15
2
D–W
Aldehyde-free, phenol-free, and QUAT-free concentrate, pH ~ 9*
II
Rinsing
RT (cold)
1
-
D–W
-
D–W: Drinking water RT: Room temperature *Recommended: BBraun Stabimed
► Note the information on appropriate cleaning brushes and disposable
syringes, see Chapter 4.7.2. Phase I ► Fully immerse the product in the cleaning/disinfectant for at least 15
min. Ensure that all accessible surfaces are moistened. ► Clean the product with a suitable cleaning brush in the solution until
all discernible residues have been removed from the surface. ► If applicable, brush through non-visible surfaces with an appropriate
cleaning brush for at least 1 min.
16
► Mobilize non-rigid components, such as set screws, links, etc. during
cleaning. ► Thoroughly rinse through these components with the cleaning disin-
fectant solution (at least five times), using a disposable syringe. Phase II ► Rinse/flush the product thoroughly (all accessible surfaces) under running water. ► Mobilize non-rigid components, such as set screws, joints, etc. during rinsing.
en 4.10.2 Manual pre-cleaning with ultrasound and brush Phase
Step
T [°C/°F]
t [min]
Conc. [%]
Water quality
Chemical
I
Ultrasonic cleaning
RT (cold)
>15
2
D–W
Aldehyde-free, phenol-free, and QUAT-free concentrate, pH ~ 9*
II
Rinsing
RT (cold)
1
-
D–W
-
D–W: Drinking water RT: Room temperature *Recommended: BBraun Stabimed
► Note the information on appropriate cleaning brushes and disposable
syringes, see Chapter 4.7.2. Phase I ► Clean the product in an ultrasonic cleaning bath (frequency 35 kHz) for
at least 15 min. Ensure that all accessible surfaces are immersed and acoustic shadows are avoided. ► Clean the product with a suitable cleaning brush in the solution until all discernible residues have been removed from the surface. ► If applicable, brush through non-visible surfaces with an appropriate cleaning brush for at least 1 min. ► Mobilize non-rigid components, such as set screws, links, etc. during cleaning. ► Thoroughly rinse through these components with the cleaning disinfectant solution (at least five times), using a disposable syringe.
Phase II ► Rinse/flush the product thoroughly (all accessible surfaces) under running water. ► Mobilize non-rigid components, such as set screws, joints, etc. during rinsing.
4.10.3 Mechanical alkaline cleaning and thermal disinfecting Machine type: single-chamber cleaning/disinfection device without ultrasound Phase
Step
T [°C/°F]
t [min]
Water quality
Chemical
I
Prerinse
<25/77
3
D–W
-
II
Cleaning
55/131
10
FD-W
■ Concentrate, alkaline: – pH = 13 – <5 % anionic surfactant
■ 0.5 % working solution – pH = 11* III
Intermediate rinse
>10/50
1
FD-W
-
IV
Thermal disinfecting
90/194
5
FD-W
-
V
Drying
-
-
-
According to the program for cleaning and disinfection device
D–W: Drinking water FD–W: Fully desalinated water (demineralized, low microbiological contamination: drinking water quality at least) *Recommended: BBraun Helimatic Cleaner alkaline
► Check visible surfaces for residues after mechanical cleaning/disinfect-
ing.
17
en 4.11 Inspection
► Check clamp sleeve 1 for the criteria listed below see Fig. 17:
► Allow the product to cool down to room temperature.
– Easy of operation of the thread – Can be assembled and disassembled – Moveability on the support arms ► Remove clamp sleeve1 if it is difficult to move. ► Check the ease of movement of the golden nuts on the threads of the distractor and spindle distractor, see Fig. 21/see Fig. 22. ► Check that the product functions correctly. ► Check all moving parts (e.g. hinges, locks/interlocks, sliding parts, etc.) for full and smooth movement. ► Check for compatibility with associated products. ► Immediately single out the defective product and send it to the Aesculap Technical Service, see Chapter 5..
► Dry the product if it is wet or damp.
4.11.1 Visual inspection ► Make sure all contamination has been removed. Pay particular atten-
tion to fitting surfaces, hinges, shanks, recesses, drilled grooves and the sides of teeth on rasps. ► For contaminated products: Repeat cleaning and disinfection procedure. ► Check instruments having interfaces to the implant for damage, burrs, deformation at the corresponding functional geometries as these may damage the implants before use. This applies in particular: – Torx geometry for instrument 4 – Contact surfaces to rod for instruments 1, 2 and 3 – Contact geometries to screw heads for the instruments 1, 2 and 3 ► Check product for damage, e.g. insulation, corroded, loose, bent, broken, cracked, worn, heavily scratched or missing parts. ► Check product for missing or faded labels and/or paint marks (e.g. color of handle, gold plating). ► Check products having long, narrow geometries (in particular rotating instruments) for deformations. ► Check surfaces for variations in roughness. ► Check product for burrs that may damage tissue or surgical gloves. ► Check product for loose or missing parts. ► Immediately separate out any damaged or worn products and return them to the Aesculap Technical Service, see Chapter 5..
4.12 Assembling 4.12.1 Downtube SZ405R ► Push gold colored rotation sleeve a of downtube 1 opposite the direction of the arrow onto the head b and screw on by turning opposite the direction of the arrow until it can move freely in the direction of the head b, see Fig. 17. 4.12.2 Parallel distractor FW238R
4.11.2 Function test CAUTION Damage (metal seizure/friction corrosion) to the product caused by insufficient lubrication! ► Oil moving parts (e.g. joints, spool parts and threaded rods) prior to the functional test using oil suitable for the applied sterilization process (e.g. STERILIT® Ioil spray JG600 for steam sterilization or STERILIT® I drip-feed lubricator JG598). ► Assemble dismountable products, see Chapter 4.12.
8
► Check instruments having interfaces to other instruments for ease of
movement and compatibility. – Pre-mounting instrument 2 and rod pusher 3 can be fully and smoothly screwed into clamp sleeve 1, see Fig. 4. – Rod pusher 3 can be fully and smoothly inserted into pre-mounting instrument 2. – Insertion instrument for locking screw 4 can be fully and smoothly inserted into rod pusher 3, see Fig. 13. – Check the coupling of the counterholder SZ392R to the clamp sleeve 1, see Fig. 7. – Check the connection of the polyblocker SZ393R to the pre-mounting instrument 2 and the rod pusher 3, see Fig. 7/see Fig. 15. – Check for secure coupling incl. grid function of the distraction arms 5 using the distractor 8, see Fig. 5. – Check the secure connection of the C-rings 6 to the spindle distractor 9, see Fig. 8. – Check connection of the distraction arms 5 and C-rings 6 to the clamp sleeve 1, see Fig. 6. ► Make sure that instruments having square or hexagonal connection are self-locking in Ennovate handles, see Fig. 18.
18
Fig. 21 ► Mount parallel distractor 8 according to the diagram.
4.12.3 Distraction spindle FW241R
9
Fig. 22 ► Mount distraction spindle 9 according to the diagram.
en 4.13 Packaging
6.
Li-ion batteries
► Place the product in its holder or on a suitable tray. Ensure that all cut-
ting edges are protected. ► Pack trays appropriately for the intended sterilization process (e.g. in
Aesculap sterile containers). ► Ensure that the packaging provides sufficient protection against recon-
WARNING Risk of infection from contaminated products! ► Observe national regulations when disposing or recycling the product, its components and their packaging.
tamination of the product during storage.
4.14 Steam sterilization Note FW238R/FW241R: the product may only be sterilized in a disassembled state. ► Check to ensure that the sterilizing agent will come into contact with
all external and internal surfaces (e.g. by opening any valves and faucets). ► Validated sterilization process – Disassemble the product if necessary – Steam sterilization using fractional vacuum process – Steam sterilizer according to DIN EN 285 and validated according to DIN EN ISO 17665 – Sterilization using fractionated vacuum process at 134 °C/holding time 5 min ► When sterilizing several products at the same time in a steam sterilizer, ensure that the maximum load capacity of the steam sterilizer specified by the manufacturer is not exceeded.
WARNING Risk of injury from sharp and/or pointed products! ► When disposing of or recycling the product, make sure the packaging prevents injuries from the product. Note The product must be processed by the operator before disposal,see Chapter 4.
7.
Symbols on product and packaging Oiling point
Interlock
4.15 Storage ► Store sterile products in germ-proof packaging, protected from dust, in
a dry, dark, temperature-controlled area.
5.
Technical Service
CAUTION Modifications to medical equipment may result in loss of guarantee/warranty claims and any approvals. ► Do not modify the product. ► Contact national B. Braun/Aesculap representative for service and repair. Service addresses Aesculap Technischer Service Am Aesculap-Platz 78532 Tuttlingen / Germany Phone: +49 7461 95-1601 Fax: +49 7461 16-2887 Email: [email protected] Or in the US: Aesculap Implant Systems LLC Attn. Aesculap Technical Services 615 Lambert Pointe Drive Hazelwood MO, 63042 Aesculap Repair Hotline Phone: +1 800 214-3392 Fax: +1 314 895-4420 Other service addresses can be obtained from the address indicated above.
19