BBraun
OrthoPilot FS101, FS104, FS105
398 Pages
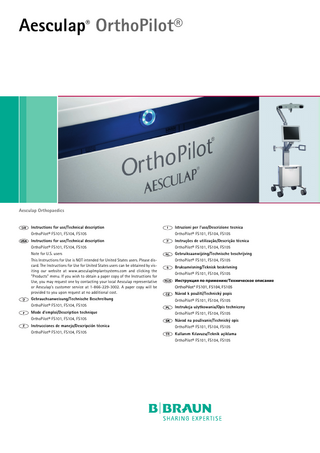
Preview
Page 1
Aesculap® OrthoPilot®
Aesculap Orthopaedics
Instructions for use/Technical description
Istruzioni per l’uso/Descrizione tecnica
OrthoPilot® FS101, FS104, FS105
OrthoPilot® FS101, FS104, FS105
Instructions for use/Technical description
Instruções de utilização/Descrição técnica
OrthoPilot® FS101, FS104, FS105
OrthoPilot® FS101, FS104, FS105
Note for U.S. users
Gebruiksaanwijzing/Technische beschrijving
This Instructions for Use is NOT intended for United States users. Please discard. The Instructions for Use for United States users can be obtained by visiting our website at www.aesculapImplantsystems.com and clicking the "Products" menu. If you wish to obtain a paper copy of the Instructions for Use, you may request one by contacting your local Aesculap representative or Aesculap's customer service at 1-866-229-3002. A paper copy will be provided to you upon request at no additional cost.
OrthoPilot® FS101, FS104, FS105
Gebrauchsanweisung/Technische Beschreibung
OrthoPilot® FS101, FS104, FS105
OrthoPilot® FS101, FS104, FS105
Instrukcja użytkowania/Opis techniczny
Mode d’emploi/Description technique
OrthoPilot® FS101, FS104, FS105
OrthoPilot® FS101, FS104, FS105
Návod na použivanie/Technický opis
Instrucciones de manejo/Descripción técnica
OrthoPilot® FS101, FS104, FS105
OrthoPilot® FS101, FS104, FS105
Kullanım Kılavuzu/Teknik açiklama
Bruksanvisning/Teknisk beskrivning OrthoPilot® FS101, FS104, FS105 Инструкция по примению/Техническое описание OrthoPilot® FS101, FS104, FS105 Návod k použití/Technický popis
OrthoPilot® FS101, FS104, FS105
Aesculap® OrthoPilot® OrthoPilot® FS101, FS104, FS105
® OrthoPilot® Aesculap FS101, FS104, OrthoPilot® FS105
Legend
CD/DVD RW combo drive
1 Camera handle with integrated laser pointer 2 19“ touch screen monitor with monitor arm 3 OrthoPilot® ultrasound module 4 OrthoPilot® module active transmitters 5 OrthoPilot® base unit 6 Polaris Spectra camera 7 Main switch 8 Handles 9 Mains power switch with power cord 10 Rolling frame (4 wheels with brakes) 11 Camera arm 12 Camera stand
Symbols on product and packages
RS232 interface Ethernet interface (100Mbit)
FireWire interface
Line-in (sound) Unlocking the monitor
Marking of electric and electronic devices according to directive 2002/96/EC (WEEE). see Disposal
Caution, general warning symbol Caution, see documentation supplied with the product Follow the instructions for use
Do not press, pull, lean against or push the stand (toppling hazard)
Equipotential bonding connector
Warning against hand injuries
Mains power switch ON
Type plate OrthoPilot® Basis Compact (FS101)
Mains power switch OFF
Standby button
Type BF applied part
Type plate OrthoPilot® module active transmitters (3 ports), FS104
Alternating current Fuse USB interface Slot for SD memory cards
2
Type plate OrthoPilot® module ultrasound FS105
Indicating label – cable strain relief
Storing the ultrasonic probe
Laser pointer – warning notice
Contents Safety notes OrthoPilot® module ultrasound (FS105)
1. 2. 3. 3.1 3.2 3.3 3.4 4. 4.1 4.2 4.3 4.4 4.5 4.6 4.7 4.8 4.9 4.10 4.11 4.12 4.13 4.14 4.15 4.16 4.17 4.18 4.19 5. 5.1 5.2 6. 6.1 7. 8. 8.1 8.2
Applicable to Safe handling Product description Scope of supply Optional components Intended use Operating principle Description of individual components and their operation Substruction Handles Stand Camera arm Laser pointer OrthoPilot® foot switch FS007 Computer Touch screen monitor Patch panel Medical power supply Uninterruptible power supply (UPS) Back plane Optical navigation system Polaris Spectra camera Transmitter technology Optional: OrthoPilot® module active transmitters for active tracking Optional: OrthoPilot® module ultrasound FS105 Optional: Framegrabber Navigated instruments Preparation and setup First use Presetting the correct voltage Working with the OrthoPilot® System set-up Operation Validated reprocessing procedure General safety instructions General information
4 4 5 5 6 6 6 7 7 7 7 8 9 9 10 10 11 11 11 11 12 12 13 14 15 17 17 17 17 18 18 18 20 21 21 21 3
Aesculap® OrthoPilot® OrthoPilot® FS101, FS104, FS105
8.3 8.4 8.5 8.6 8.7 9. 9.1 9.2 10. 11. 11.1 12. 13. 13.1 13.2 13.3 14. 14.1 14.2 14.3 14.4 15. 16.
1.
Preparations at the place of use Cleaning/disinfection Wipe disinfection for electrical devices without sterilization Manual cleaning/disinfecting Inspection, maintenance and checks Storage and transport Storage Transport Maintenance and repairs Troubleshooting list Fuse replacement Technical Service Accessories/Spare parts Accessories Spare parts Optional modules and units Technical data Classification acc. to Directive 93/42/EEC Ambient conditions OrthoPilot® module ultrasound FS105 – ultrasonic output power (B/M mode) Annex: OrthoPilot® module ultrasound FS105 – Guidelines for safe operation of diagnostic ultrasound Disposal Distributor in the US/Contact in Canada for product information and complaints
21 21 23 24 24 24 24 25 26 26 28 28 29 29 29 29 29 29 30 30 31 31 31
Applicable to
► For item-specific instructions for use and information on material
compatibility, see also www.extranet.bbraun.com
4
the
Aesculap
Extranet
at
2.
Safe handling
CAUTION Federal law restricts this device to sale by, or on order of a physician!
DANGER
WARNING
Risk of death by electric shock! ► Do not open the product. ► Connect the product only to a grounded power supply. Risk of injury caused by incorrect operation of the product! ► Attend appropriate product training before using the product. ► For information about product training, please contact your national B. Braun/ Aesculap agency.
► Remove the transport packaging and clean the new product, either
manually or mechanically, prior to its initial sterilization. ► Prior to use, check that the product is in good working order. ► Observe “Notes on Electromagnetic Compatibility (EMC)“, see
TA022130. ► To prevent damage caused by improper setup or operation, and in order
not to compromise warranty and manufacturer liability: – Use the product only according to these instructions for use. – Follow the safety and maintenance instructions. – Only combine Aesculap products with each other. – Follow the application advisories acc. to standard, see Extracts from relevant standards. ► Ensure that the product and its accessories are operated and used only by persons with the requisite training, knowledge, or experience. ► The OrthoPilot® is intended for operation in the non-sterile zone. ► Prior to use, the user must receive appropriate instruction by a person authorized by Aesculap. ► In case of failure of the OrthoPilot® or any other malfunction precluding the continued use of OrthoPilot®, the surgeon must be able to finish the operation using manual techniques. ► The user is bound to ensure and observe all applicable national and international standards pertaining to the operation of OrthoPilot®. ► The following instructions for use must be observed and kept accessible for the user: – Instructions for use for OrthoPilot® FS101, FS104, FS105 – Instructions for use “OrthoPilot® operating system, operation, software“ – Instructions for use of the implants and instruments used in the respective operation – Instructions for use of the active and passive Rigid-Bodys (transmitters) – Instructions for use and manuals for the respective software applications
► The safety instructions and maintenance advice given in the respective
instructions for use or on the device must be adhered to. ► Only combine with OrthoPilot® such devices that the manufacturer has cleared and approved for this purpose. ► Do not use OrthoPilot® in an oxygen-enriched environment or in the presence of flammable substances (e.g. benzene, anesthetics). ► Operate OrthoPilot® only with the software approved for this purpose by Aesculap. ► The system must undergo annual services by the manufacturer or by persons instructed by the manufacturer. ► There are no known contraindications for using OrthoPilot®. If this situation should change, the manufacturer will inform the user accordingly.
DANGER
DANGER
DANGER
CAUTION
CAUTION
CAUTION
CAUTION
Water condensation! ► Prior to putting it into operation, allow the OrthoPilot® to warm up at room temperature for at least 1 hour. Condensation water can form if the OrthoPilot® has been stored at an ambient temperature of <5 °C for more than 3 hours.
3.
Product description
Modification of OrthoPilot®! ► OrthoPilot® and its components must not be modified under any circumstances.
3.1
Scope of supply
Designation
Art. no.
Operating altitude of the equipment cart! ► For reasons of electrical safety, the maximum operating altitude of 2 000 m above sea level must not be exceeded!
OrthoPilot® foot control switch
FS007
Dust cover
FS101400
PC unit with integrated UPS
FS101500
Battery block for UPS
FS101501
Medical power supply
FS101502
Polaris Spectra camera system
FS101508
Touch screen monitor
FS101509
OrthoPilot® Basis Compact
FS101800
Backplane
FS101836
Patch-Pannel
FS101840
Instructions for use for "OrthoPilot® FS101, FS104, FS105"
TA012655
Instructions for use “OrthoPilot® operating system, operation, software“
TA012656 (German) TA012659 (English)
Getting started FS101
TA012657
Technical documentation – EMC
TA022130
Essential, actively connected applied parts! ► The OrthoPilot® may be used only with the following active rigid bodies: FS601, FS605. ► The ultrasonic probe used with the system is linear scanner head FS105501. ► The user must consult the respective instructions for use! Damage to system components due to fluids entering the equipment! ► Do not put fluid containers on the OrthoPilot® Flex monitor cart/OrthoPilot® equipment cart or related components. Fluids penetrating into the device can damage the electrical components in the OrthoPilot®. Use of multiple sockets/extension cables! ► Do not connect multiple sockets/extension cables at the ME system. Transport! ► Any transport outside the hospital must be carried out by persons trained and authorized by Aesculap. ► Put the OrthoPilot® into proper transport position before moving it within the hospital. ► Further information on transport can be found in the relevant chapter of this document.
5
Aesculap® OrthoPilot® OrthoPilot® FS101, FS104, FS105
3.2
Optional components
3.4
Designation
Art. no.
Ultrasound gel
FS091
Ultrasound foil
FS092
Country-specific power cord
FS096 (Europlug) FS097 (UK, Ireland) FS098 (USA, Canada, Japan)
Frame grabber
FS101522
Operating principle
The OrthoPilot® system uses a video-optical stereo camera to register the spatial position of infrared light sources (active, infrared light-emitting transmitters or passive, infrared light-reflecting transmitters). From that information, Aesculap-specific software installed on the OrthoPilot® system can compute the location and position of the transmitters relative to each other and thus the location and position of the instruments in relation to the patient. The software also allows the inclusion of further data (e.g. from preoperative planning) in the calculations and thereby assists the surgeon in achieving optimum precision in the operation.
OrthoPilot® module active transmit- FS104 ters (3 ports) OrthoPilot® ultrasound module
FS105
OrthoPilot® Rigid-Body (active)
FS601, FS605
OrthoPilot® Rigid-Body (passive)
FS633, FS634, FS635, FS608
OrthoPilot® THA ultrasound RB adapter (left)
FS910R
OrthoPilot® THA ultrasound RB adapter (right)
FS911R
Equipotential bonding cable for OrthoPilot® base unit (4 m)
GK535
Fig. 1
Getting started FS104
TA012653
Main functions and design characteristics
Getting started FS105
TA012654
Instructions for use for "OrthoPilot® FS101, FS104, FS105"
TA012958 (French) TA012968 (Spanish)
Instructions for use “OrthoPilot® operating system, operation, software“
TA012959 (French) TA012969 (Spanish)
Getting started FS007
TA013007
3.3
Intended use
OrthoPilot® FS101/FS104/FS105 is the basic equipment for using Aesculap-specific application software for computer-aided, orthopedic surgery.
6
Operating principle of the Polaris Spectra camera
■ The stereo-optical camera detects the location and position of active and passive transmitters in front of the camera, within a distance of 1.6 m to 2.4 m. ■ The system hardware is not significantly influenced by interference factors that do not exceed IEC DIN EN 60601-1-2 specifications. ■ The hardware used in the construction of the system was specially selected to ensure a very long service life and strong resistance to damage by shock. ■ The system is controlled via an OrthoPilot® foot switch and an integrated, height-adjustable touch screen. ■ The OrthoPilot® foot switch can be cleaned under running water. ■ In case of mains power interruption, the PC and a monitor are powered by an integrated UPS, which ensures that data already registered will be preserved for at least 5 minutes. ■ Mains power failure is signaled by a short acoustic warning and the power switch lighting turning off. The power failure, as well as recovery of mains power, is indicated by a message displayed on the monitor. ■ The system offers connectivity for an external video source. ■ For data saving and storing, there are several USB sockets, an SD-Card Slot and a DVD writer available. ■ The height of the camera stand can be adjusted semi-automatically through a gas pressure spring. ■ The components and gas pressure springs integrated in the camera arm system securely hold the camera in its position and allow camera rotation through 270° and camera inclination by 90°.
■ The arm system is fitted with a mechanical lock, which protects the 4.2 delicate optoelectronics of the camera against direct knocks during transport. ■ All system components have been designed to maintain their essential functions and performance characteristics under normal use for at least a year (mandatory service interval).
4.
Description of individual components and their operation
4.1
Substruction
CAUTION
Risk of overheating! ► The base unit features lateral ventilation slits to release heat generated in the unit. To avoid heat accumulation and possible consequent damage to electric components, the ventilation slits must never be covered.
The OrthoPilot® is fitted with a rolling frame with four pivoted wheels. All wheels are fitted with immobilization brakes that secure the system against inadvertent movement, see Fig. 2.
Handles
The system is fitted with handles to allow easy manipulation of the OrthoPilot® hardware. The handles serve to protect the camera in transport position and to allow a secure grip for pushing and aligning the system.
Fig. 3
Handles
4.3
Stand
CAUTION
Camera maladjustment due to knocks against the camera stand! ► Be careful to avoid knocking the camera stand during operation.
The pedal board at the back of the equipment cart, see Fig. 4, is used to adjust the stand. When the pedal board is pressed, the camera stand is either pushed up, semi-automatically, by a gas pressure spring, or it can be moved down manually by the handle, see Fig. 5, at the upper end of the stand. The camera stand is fixed in its actual position when the pedal board is released. Detailed information on the navigation-related alignment of the camera can be found in the instructions for use "OrthoPilot® operating system, operation, software“. ► First fully extend the camera stand, then adjust the monitor. Finally lower the stand to the required working height. In this way the camera and the monitor will not collide with each other.
Fig. 2
OrthoPilot® Basis Compact
7
Aesculap® OrthoPilot® OrthoPilot® FS101, FS104, FS105
4.4
Camera arm
WARNING
Fig. 4
Pedal board
Fig. 5
Stand handle
Risk of contusion while adjusting the camera arm! ► When adjusting the arm system, make certain that no part of the body or clothing are close to hazardous areas of the camera arm.
The camera system features four camera arms, which allow optimal alignment of the camera towards the operating field: ■ Camera arm 1: Vertical rotation +/- 60° ■ Camera arm 2: Horizontal rotation +/-90° ■ Camera arm 3: Horizontal rotation +/-180° ■ Camera arm 4: Horizontal rotation +/- 130° and height adjustment by up to 30 cm. For transport, the arm can be locked in a transport position, see Transport.
Fig. 6
Camera arm
► Release the camera lock. ► Swivel forward the lower camera arm (camera arm 13) and adjust the
camera height. ► Pull forward the handle and perform fine-adjustment of the camera
position with the camera arm, see Fig. 7.
8
4.5
Laser pointer
WARNING
Damage to the eye caused by laser beam! ► To avoid damage or injury to the eye, do not look directly into the laser beam.
The Laser pointer is used for preoperative and intraoperative alignment of the Polaris Spectra camera with reference to the operating field. The battery-powered laser pointer is accommodated in the camera handle. It is activated by a button integrated in the handle. The diameter of the beam produced by the infrared laser pointer is less than 5 mm at a distance of up to 10 m.
Fig. 7
4.6
OrthoPilot® foot switch FS007
CAUTION
Risk of tripping! ► When laying the mains power cord and the OrthoPilot® foot switch cable, do not create tripping hazards (avoid traffic routes within the O.R.)
CAUTION
Cable damage! ► To avoid damage to the cable or inadvertent disconnection of the OrthoPilot® foot switch during operation, the cable should be inserted in the strain relief.
Handle with laser pointer
Fig. 8
OrthoPilot® foot switch FS007
The OrthoPilot® foot switch is the central input device for navigation within the OrthoPilot® applications. It has two pedals and a push button, though which various commands can be executed by pressing them briefly or for a longer time. For detailed information, see instructions for use “OrthoPilot® operating system, operation, software”. To use the OrthoPilot® foot switch, take it from its holder behind the front door and unwind the USB cable. Connect the USB plug at the appropriate socket and insert it in the strain relief as shown in the illustration, see Fig. 9.
9
Aesculap® OrthoPilot® OrthoPilot® FS101, FS104, FS105
Now the OrthoPilot® foot switch can be positioned in the required position in reach of the user. To allow subsequent repositioning of the OrthoPilot® foot switch and for easier handling of the OrthoPilot® foot switch, the steel bow can be folded up by 90°. Through this bow the OrthoPilot® foot switch can be lifted and moved by foot from its initial position.
Fig. 9
Strain relief of the OrthoPilot® foot switch cable
4.7
Computer
CAUTION
CAUTION
CAUTION
10
Emergency shut-down of the computer! ► Pressing the main switch for a longer period (4 s) forces the computer to switch off without shutting down the operating system. This involves the loss of all data! ► It is impossible to switch off the system via the mains power switch, as the uninterruptible power supply is activated and will keep the computer powered for at least 5 minutes. Installation and maintenance of the operating system/application software! ► The operating system and application software may be installed and maintained, and the computer and monitor maintained and serviced only by Aesculap Technical Service or by persons authorized by Aesculap. Data loss and system malfunction due to improper software installation or incorrect powering down of the system! ► Software may only be installed by the manufacturer or by a person authorized by Aesculap. ► For further information, see instructions for use ”OrthoPilot® operating system, operation, software”.
A medical computer accommodated in the substruction of the system serves as the central control element of OrthoPilot®. The main switch for powering up the computer is fitted at the front of the base unit, see Fig. 10. The system is started by briefly pressing the push button, which will light up in blue. The computer can be switched off properly only via the IntroScreen. For detailed information, see instructions for use “OrthoPilot® operating system, operation, software”.
Fig. 10 Main switch
4.8
Touch screen monitor
CAUTION
Damage to the touch screen membrane! ► Do not use sharp or pointed objects for operating the touch screen. ► Clean the touch screen monitor only with the appropriate cleaning agents. For further advice, see Chapter on Validated reprocessing procedure.
In addition to the OrthoPilot® foot switch, a touch screen monitor is used for operating the navigation system and the application software. ► Prior to use, fold up the monitor from its transport position. Make certain the monitor is held upright by the lock spring and is positioned in such a way that unobstructed view of the application will be maintained throughout the operation, see Fig. 11.
► Press the locking button on the left side of the monitor arm to fold the
monitor up or down.
4.10 Medical power supply The OrthoPilot® is equipped with a multi-range power supply, which automatically detects and adapts to the local mains line voltage (100– 240V). The power supply unit can be separated from mains power supply through mains power switch 9 at the rear of the base system. For instructions on replacing the fuse sets, see Troubleshooting list.
4.11 Uninterruptible power supply (UPS)
WARNING
Fig. 11
Folding up the monitor/Releasing the monitor lock
4.9
Patch panel
DANGER
Risk of electric shock! ► Never touch an interface and the patient at the same time.
The patch panel holds various interfaces for connecting external devices and data storage media: ■ DVD-RW drive ■ SD card reader ■ Serial interface (RS232) ■ 4 x USB 2.0 sockets ■ FireWire socket ■ Ethernet interface (100Mbit/s) ■ S-Video (only available with optional frame grabber) ► Before connecting any accessories, see Connecting the accessories.
Fig. 12 Patch panel
CAUTION
Damage to sockets due to devices (e.g. USB stick) plugged in at the patch panel when closing the unit door! ► Remove all devices plugged in at the patch panel before closing the unit door.
No camera function while the system is powered by the UPS! ► Halt the operation until normal power supply is resumed and the camera signals ‘ready for operation’.
In cases of voltage drop or power failure, the computer and one monitor (monitor on the base module or monitor on the OrthoPilot® Flex monitor cart) are kept supplied by the integrated UPS for another 5 min. Although the UPS can bridge periods of mains power interruption, the application workflow can not be continued through such periods! The power interruption and, consequently, operation through the UPS is signaled by an acoustic warning (3s beep, 1s pause, 3 times) and a warning message on the monitor screen. For further information, see instructions for use “OrthoPilot® operating system, operation, software”. ► Check that the mains plug has not been pulled out inadvertently. ► If the cause of the voltage drop can not be found and remedied within 5 minutes, the computer must be shut down properly to obtain safe system status.
4.12 Back plane
CAUTION
Contamination and destruction of electrical components! ► The plug connection covers, which serve to protect the back plane against penetration by solid objects and ingress of fluids, must be kept closed. ► The covers may only be opened by a person authorized by Aesculap.
The back plane accommodates the bus system that supplies all connected modules and devices with the appropriate supply voltages and signal lines. The two plug connections, see Fig. 13, can be used to connect the additionally available modules (OrthoPilot® module ultrasound 3, OrthoPilot® module active transmitters 4).
11
Aesculap® OrthoPilot® OrthoPilot® FS101, FS104, FS105
► Optional modules may be installed only by persons authorized by
4.14 Polaris Spectra camera
Aesculap.
CAUTION
CAUTION
Malfunction of the OrthoPilot® system! ► Align the camera in such a way that the optical axis does not point towards incoming or stray light (e.g. from windows or O.R. lighting). ► For further information, see instructions for use "OrthoPilot® operating system, operation, software”. Camera warm-up effects! ► The electrical and optical components of OrthoPilot® are subject to temperature-related fluctuations. Insufficient stability of measurements can have significant detrimental effects on the system precision. Therefore, to ensure adequate stability, Aesculap recommends powering up the OrthoPilot® system 10 minutes prior to any operation. Caution: The cameras of previous OrthoPiloten® systems (FS100/FS010) do not show such warm-up effects!
Fig. 13 Back plane
4.13 Optical navigation system The navigation system consists of the “Polaris Spectra” infrared camera and a range of active and passive transmitters (Rigid-Bodys). The latter are installed, via adapters, on the instruments and their spatial location and position relative to the patient are registered. The OrthoPilot® may be used only with Aesculap-specific transmitters. The “Passive Tracking Technologie“ is licensed according to patents USA 6,351,659 and D 196 39 615. 8. In the OrthoPilot® system, the following Rigid-Bodys are used for navigation: ■ FS633, FS634, FS635 and FS608: passive transmitters (reflectors without cables) illuminated by the camera ■ FS601 and FS605: active transmitters that can be used only with the optional OrthoPilot® module active transmitters. Further detailed information on the handling and operation of the RigidBodys can be found in the respective instructions for use.
12
CAUTION
Adverse effects on system functions due to camera maladjustment and scratched or damaged lenses! ► The Polaris Spectra camera is fitted with an integrated shock indicator, which is triggered if the forces acting on the camera by shaking or knocking were found to be beyond the tolerances, with the effect of possible maladjustment of the Polaris Spectra camera. Once the shock indicator has been triggered, the Polaris Spectra camera must be inspected by an Aesculap service technician and replaced, if necessary, prior to continued application. This is necessary to ensure the continued accuracy of the measurements. ► The Polaris Spectra camera is equipped with a lens system through which infrared light is emitted and received. Damaged or scratched lenses can affect the proper functioning of the camera. Therefore, if lenses are found to be scratched or damaged, the Polaris Spectra camera must be replaced before further application of the system.
CAUTION
CAUTION
Power supply of the camera under UPS conditions! ► The navigation must be halted when the UPS warning sounds and the UPS status message is displayed on the monitor screen. ► Once the mains power supply is re-established, the camera initializes itself after some seconds and the system is operational again as soon as the UPS message disappears from the screen. ► For further information, see the instructions for use "OrthoPilot® operating system, operation, software". Detrimental effect on system precision! ► Make certain the camera is protected against knocks (especially during transport). ► For detailed information on how to secure the camera, see chapter on Transport.
The camera needs to be aligned, using the laser pointer integrated in the handle, so that the transmitters are "visible" for the camera. The distance between the camera and the operating field should be between 1.7 m and 2.1 m. The actual distance is shown in the application software, see instructions for use “OrthoPilot® operating system, operation, software”.
Power LED (A)
Status LED (B)
Error LED (C)
Significance
permanent on
permanent on
flashing
Fault, e.g. shock indicator triggered. The accuracy of measurements can not be guaranteed anymore. Call Aesculap Technical Service!
permanent on or off
permanent on
permanent on
Critical fault; system not operational. Call Aesculap Technical Service!
permanent on
–
permanent on
Critical fault; system not operational. Call Aesculap Technical Service!
4.15 Transmitter technology The OrthoPilot® is used with two types of transmitters (‘Rigid-Bodys’):
Fig. 14 Legend A Power LED B Status LED C Error LED
Fig. 15
Power LED (A)
Status LED (B)
Error LED (C)
Significance
flashing
(any status)
(any status)
Warming-up phase
permanent on
permanent on
–
Camera ready for operation
Legend A Rigid-Bodys, passive (patents USA 6,351,659 and D 196 39 615.8.) B Rigid-Bodys, active The passive transmitter technology, by which the infrared light emitted by the Polaris Spectra camera is reflected by the marker spheres on the transmitters, is the standard technology for OrthoPilot®. The passive transmitters, which are not part of the OrthoPilot® system, are documented in the respective instructions for use (TA011029, FS633, FS563, FS565/ TA011429, FS608).
13
Aesculap® OrthoPilot® OrthoPilot® FS101, FS104, FS105
The active transmitter technology uses transmitters that emit infrared light by their integrated infrared LEDs. This technology requires the optional OrthoPilot® module active transmitters. The active transmitters, which are not part of the OrthoPilot® system, are documented in the respective instructions for use (TA010803, FS601/FS605). The passive transmitters FS633, FS635, FS635 and FS608 are marked with a color code. The active transmitters FS601 can be used universally at the three ports of the OrthoPilot® module for active transmitters.
The fourth connector (bottom right) is an extension port, which is not used at present.
Note For easier identification of the active transmitters, Aesculap recommends marking the transmitters with a sterilizable and cleanable color ribbon. Fig. 16
OrthoPilot® module active transmitters (3 ports), FS104
► Connect the active transmitter FS605 at the blue port of the module.
CAUTION
Fixation of the marker spheres on the passive transmitters! ► Check that the passive, single-use marker spheres are firmly connected to the appropriate adapters of the passive transmitters. ► Ensure that the passive, single-use marker spheres click into place when connected.
4.16 Optional: OrthoPilot® module active transmitters for active tracking
WARNING
WARNING
Electrical safety! ► The OrthoPilot® may be used only with the following active Rigid-Bodys: FS601and FS605. ► Use of other applied parts results in forfeiture of the operating license. Interference by external signals! ► To avoid interference by external signals from other devices (e.g. HF), route the cables of the active transmitters into the operating area separately from other cables or leads.
The OrthoPilot® module active transmitters is an additional module for using active transmitters see Fig. 16, which emit infrared light by their integrated infrared LEDs. The SCU has 3 connectors for active transmitters.
14
Fig. 17 Labeling of the SCU ports Power LED (A)
Status LED (B)
Error LED (C)
Significance
permanent on
flashing
–
Initialization
permanent on
permanent on
–
SCU ready for operation
permanent on
permanent on
flashing
Non-critical fault; no disruption to operation. Aesculap Call Technical Service!
permanent on
permanent on
permanent on
Critical fault; system not operational. Aesculap Call Technical Service!
permanent on
flashing
permanent on
Critical fault; system not operational. Aesculap Call Technical Service!
Port LED
Significance
green light
Connected tool ready
orange light
Connected tool recognized
4.17 Optional: OrthoPilot® module ultrasound FS105
DANGER
► When connecting the active transmitters, be certain of correct pairing
(same color) of plug and port. ► Make certain the transmitter plugs are locked in their ports when connecting the active transmitters. To provide power and communication for the active transmitters, the transmitters have to be plugged in at the 3 connectors of the OrthoPilot® module active transmitters, see Fig. 16. A switch at the module back panel, see Fig. 18, allows activating and deactivating the module. Also, if necessary (as indicated by red light of the status LED) the module can be reset intraoperatively by briefly switching it off and on again.
DANGER
Fig. 18
Power supply switch on module
Further information can be found in the instructions for use “OrthoPilot® operating system, operation, software”.
WARNING
WARNING
WARNING
Risk of electric shock! ► Prior to each application, check the scanner head for: cracks in the cable and inflexibility, or cracks in the housing, and other damage to the probe head (e.g. detachment of the plastic film covering the lens). ► The device must not be used if any damage is detected. (Immediately inform Aesculap Technical Service.) ► Unwind the ultrasonic scanner head cable completely, to avoid crushing/cutting of the cable by the drawer edge. ► Prior to cleaning and disinfecting, disconnect the device from mains power. ► The scanner head is waterproof acc. to IPX7 only up to the cable exit (see Fig. 20 “OrthoPilot® ultrasonic probe”). Burn injuries to the patient caused by interactions with HF devices! ► To prevent burns to the patient – in case of a defective neutral electrode of the HF surgery set –do not use the ultrasound module concurrently with a HF device. ► To avoid power feed via HF radiation from the HF device, remove the ultrasonic probe from the patient as soon as data registration with the probe has been completed. The mechanical index (MI) provides some indication about possible biological effects caused by cavitation. It is very important for examinations of the thorax and if contrast media are used. It is less important for examinations not involving gas-filled cavities, which is the case when examining most tissue structures. ► Careful use of the ultrasonic probe ► Keep the exposure time as short as possible. Risk of contusion at the drawer! ► To prevent parts of the body or clothing getting crushed or jammed, use the handle recess for opening and closing the drawer. Integrity of the ultrasonic image information! The ultrasound device must not be used anymore if it produces irregular or inconsistent results (e.g. unsteady imaging, artifacts within the ultrasonic image and in the image environment). ► Contact Aesculap Technical Service.
15
Aesculap® OrthoPilot® OrthoPilot® FS101, FS104, FS105
CAUTION
CAUTION
Damage to the ultrasonic probe caused by excessive mechanical strains or dropping/knocking of the probe! ► Ultrasonic probes can be damaged by incorrect handling. ► Observe the instructions in the chapter on Validated reprocessing procedure Risk of overheating! ► The module is fitted with a fan unit to stabilize the temperature of its housing. To avoid overheating of the ultrasound unit, this ventilation must never be obstructed.
The OrthoPilot® module ultrasound is used for recording 2D ultrasound images during the operation. The OrthoPilot® module ultrasound consists of an ultrasound unit and a probe. The ultrasound unit is accommodated in a drawer and is not accessible. The 128 piezo elements of the probe generate ultrasonic pulsed echo signals of 5 to 7 MHz frequency. The ultrasound waves generated by the sound unit carry a small amount of energy (average intensity less than 100 mW/cm2) in terms of IEC 1157. Although there are no known effects on the patient’s health, the exposure time should be kept as short as possible. For detailed information in this respect, see Annex: OrthoPilot® module ultrasound FS105 – Guidelines for safe operation of diagnostic ultrasound.
Fig. 20 OrthoPilot® ultrasonic probe with OrthoPilot® THA ultrasoundRB adapter
1
Fig. 19 OrthoPilot® ultrasonic probe Legend 1 Cable exit Fig. 21 OrthoPilot® module ultrasound FS105 Legend A Probe interface to adapt the rigid body B Ultrasonic probe C Shaft release/locking slider D Status indicator
16
► Authorized use only to assist surgical navigation. ► There are no contraindications for using the ultrasound device. ► Some biological effects (e.g. heat-up) may occur during use, but do not
necessarily present any hazard. Any use of the ultrasound device lies in the responsibility of the operating surgeon! The maximum thermal index (TI) of the device is 0.2, which is below the relevant threshold of 1.0. ► Use the ultrasound device only in combination with sterile probe cover FS091 and ultrasound gel FS092. ► As the ultrasonic probe is applied within the sterile zone, make certain that the probe cover covers the ultrasonic probe as well as the cable. ► For image recording, connect the Rigid Body to the ultrasonic probe via the interface, see Fig. 20. ► Further instructions and advisories about using the probe cover and the ultrasound gel can be found in the instructions for use “OrthoPilot® operating system, operation, software”. ► Have single-use sterile cover and sterile gel at hand for each operation (see “OrthoPilot® operating system, operation, software”). ► Prior to their use, make certain that the cover and gel packages are unopened, undamaged and dry. The status indicator D in the housing front plate, see Fig. 21 displays the operating status of the module. LED status
Significance
LED off
Device not in use
Green
Device in recording mode
Yellow
Device in freeze mode
Red
Communication error
The ultrasound module can be activated and deactivated by a switch in the back panel of the module, see Fig. 18. ► To use the ultrasound device, open the drawer by pressing the blue locking button at the handle recess. ► Remove the ultrasonic probe from he holder and unwind the cable completely to avoid crushing it at the module. ► After the application, fully wind up the cable and position the ultrasonic probe in the holder. ► Close the drawer so that the locking button audibly engages in the locked position.
4.18 Optional: Framegrabber The Framegrabber option adds the possibility to connect imaging devices to the base unit via an S-Video cable. The Framegrabber device itself is accommodated in the base module and can not be accessed from outside. The Framegrabber allows to access within the application software current image information relevant for the operation. E.g. an endoscope can be connected. The connection is always via the S-Video interface on the patch panel, see Fig. 12. ► Before connecting any accessories, see Connecting the accessories. The connection must be made with an S-Video cable with triple shielding to exclude interference from external devices and electromagnetic fields.
4.19 Navigated instruments Detailed information on the handling and operation of the navigated instruments can be found in the respective instructions for use of the OrthoPilot® software applications.
5.
Preparation and setup
Non-compliance with the following instructions will preclude all responsibility and liability in this respect on the part of Aesculap. ► When setting up and operating the product, adhere to – national regulations for installation and operation, – national regulations on fire and explosion protection. ► The OrthoPilot® must be set up by a trained person authorized by Aesculap. ► Lay non-system cables and cords separately from the OrthoPilot® components and the OrthoPilot® main unit. HF cables in particular can cause strong interference. ► If interference from external devices is suspected, immediately deactivate those devices, if possible, until the source of interference is found. In some cases it can be necessary to consult a specialist in medical electrical devices to remedy the interference.
5.1
First use
WARNING
Risk of injury and/or product malfunction due to incorrect operation of the electromedical system! ► Adhere to the instructions for use of any medical device.
► The OrthoPilot® must be set up by a trained person authorized by
Aesculap. This also applies, particularly, to the installation of the mains power cord and its strain relief.
17
Aesculap® OrthoPilot® OrthoPilot® FS101, FS104, FS105
5.2
Presetting the correct voltage
The mains voltage must correspond to the voltage indicated on the type plate at the back of the unit. The power supply is a multi-range supply that automatically detects and adapts to the local mains line voltage (110 V–240 V).
6.
Working with the OrthoPilot®
6.1
System set-up
DANGER
WARNING
CAUTION
Risk of explosion due to the use of flammable substances (e.g. anesthetics and skin cleaning and disinfecting agents) in explosion hazard areas! ► Do not use the equipment cart in explosion hazard zones within rooms used for medical purposes. ► Do not use the equipment cart in oxygenenriched environments or in the presence of flammable substances (e.g. benzene, anesthetics). Risk of injury caused by toppling of the equipment cart or shifting objects! ► Prior to use, check the stability against toppling of the fully mounted equipment cart. ► Be careful when rolling the cart over obstacles. Equipment malfunction due to magnetic and electric fields! ► Keep adequate distance to x-ray devices, tomography equipment etc. ► Carry out function checks before using the equipment.
Connecting the accessories
DANGER
DANGER
DANGER
Risk of injury due to unapproved configuration using additional components! ► For all applied components, ensure that their classification matches that of the application component (e.g. Type BF or Type CF) of the respective device. Connection of third-party equipment! ► For license and safety reasons, connecting of peripheral equipment (e.g. video recorders, printers, etc.) that have not been cleared and approved by Aesculap is not permitted and would result in forfeiture of the operating license! System failure caused by connecting of an external USB hard drive! ► Do not connect an external USB hard drive to the system.
Combinations of accessories that are not mentioned in the present instructions for use may only be employed if they are specifically intended for the respective application, and if they do not compromise the performance and safety characteristics of the products. Also note that any equipment connected at the interfaces must demonstrably meet the respective IEC standards (e.g. IEC 60950 for data processing equipment, IEC/DIN EN 60601-1 for electromedical devices). All configurations must comply with basic standard IEC/DIN EN 60601-1. Any individual connecting devices with one another is responsible for such configuration and must ensure compliance with basic standard IEC/DIN EN 60601-1 or applicable national standards. ► Please address your B. Braun/Aesculap partner or Aesculap Technical Service with any inquiries in this respect; for a contact address, see Technical Service. Connecting the power supply
► Check all power cords and connecting cables for damage prior to each
system start-up. ► Immediately replace damaged cables and leads. ► Observe all specifications regarding ambient conditions, see Technical data.
DANGER
Risk of death by electric shock! ► Connect the product only to a grounded power supply.
► Fully unwind power cord 11 of the base unit from the cable holder and
plug it in at the wall socket of the power mains. The correct countryspecific plug for non-heating equipment must be used. ► Completely unwind the power cord before switching on the OrthoPilot® system. ► The OrthoPilot® must be set up in such a way that it can easily be disconnected from mains power.
18
Connecting the equipotential bonding cable ► Connect the equipotential bonding cable between the equipotential
bonding connector, see Fig. 22, at the rear panel of the OrthoPilot® base unit and the corresponding connector at the mains power supply. The optional OrthoPilot® Flex monitor cart is connected with its equipotential bonding cable at the connector provided at the rear of the base module. The equipotential bonding serves to ensure that all components of the OrthoPilot® system share the same ground potential with the other components in the O.R.
Fig. 23
Fig. 22 Equipotential bonding connector Positioning the OrthoPilot® To take the OrthoPilot® from the transport mode to the operating mode, unlock the system by pressing and turning the locking pin, see Fig. 23. The OrthoPilot® system has to be positioned to ensure that the transmitters remain visible during the entire length of the operation. Once the OrthoPilot® Basis Compact system has been positioned, the wheel brakes must be engaged. Fully extent the monitor stand, move the touch screen monitor from its transport position to the operating position, and adjust the monitor to the appropriate operating height. If necessary, loosen the brakes at this point to adjust the horizontal viewing angle relative to the monitor screen by swiveling the entire system. Finally lower the stand to the required working height. In this way the camera and the monitor will not collide with each other. The handle, see Fig. 7, can be used for adjusting the camera position according to individual requirements. The laser pointer should be directed to the center of the operating field.
Fig. 24 To ensure failure-free navigation, it is important that the line of view between the Rigid-Bodys and the camera will not be obstructed at any time during the operation. Detailed instructions for the installation of the transmitters can be found in the instructions for use “OrthoPilot® operating system, operation, software” and in the respective application manuals. The next step is to remove the OrthoPilot® foot switch from its holder, see Fig. 9, and position it under the operating table, in reach of the user. The cable must be laid in such a way that the traffic routes in the O.R. are not impeded. As the equipment cart can not be sterilized, it must be set up and used at a distance to the sterile zone of at least 1.5 m.
19
Aesculap® OrthoPilot® OrthoPilot® FS101, FS104, FS105
7.
Operation
WARNING
Risk of injury and/or malfunction! ► Always carry out a function check prior to using the product.
WARNING
Risk of injury when using the product beyond the field of view! ► Apply the product only under visual control.
► For intraoperative application of the ultrasonic probe, use sterile ultra-
sound gel FS092. ► Fasten ultrasound Rigid-Body adapter FS910R or FS911R, depending on the side of the patient to be operated on, to the ultrasonic probe, see Fig. 21. ► Further instructions and advisories about using the ultrasonic probe, the probe cover and the ultrasound gel can be found in the instructions for use “OrthoPilot® operating system, operation, software”.
► To activate the system, first press mains power switch 11 at the rear
panel of the base unit and at the rear panels of any additional modules connected to the system. ► Energize the ultrasound module and the module for active tracking, if part of the setup, via the power switch at the back of the respective module, see Fig. 18. ► Switch on the computer at main switch 9, which will light up in blue. The system loads the OrthoPilot® IntroScreen, see Fig. 25, which allows selecting among various software applications and tools.
Fig. 26 Quitting the application software
Fig. 25
OrthoPilot® IntroScreen
Select the appropriate OrthoPilot® software on the touch screen monitor and follow the instructions. Further information can be found in the instructions for use "OrthoPilot® operating system, operation, software". ► For using the active transmitter module, connect the color-coded active transmitters at the respective port of the module, see Fig. 17, to have the transmitters or diodes supplied with the required voltage. The passive transmitters do not have any cables or wires and do not require external voltage supply. ► For intraoperative application, fit the appropriate, sterile, single-use marker spheres on the transmitters. ► For intraoperative application of the ultrasonic probe, apply the sterile probe cover FS091 with the adhesive side on the probe head (avoiding air bubbles), and pull it fully over the probe head and cable.
20
With the workflow of the respective software completed, the software application can be closed via the X symbol in the top left corner of the monitor screen, see Fig. 26. The OrthoPilot® returns to the top-level graphic user interface (OrthoPilot® IntroScreen). The OrthoPilot® Basis Compact system is switched off by pressing the “Shutdown” field on the IntroScreen. After that, the OrthoPilot® hardware can be fully de-energized via mains power switch 9 at the back panel of the base module. ► When using the ultrasound module: Deactivate the ultrasound module via the switch at the back of the module. ► Rigid-Body is removed from adapter FS910R/ FS911R. ► Unscrew the adapter. ► Carefully detach the sterile cover from the ultrasonic probe and the cable. ► When using the module for active tracking: Deactivate the module for active tracking via the switch at the back of the module. ► Unplug the active transmitters connected to the active transmitter module. ► For further information on reprocessing the ultrasonic probe and cable, see see Validated reprocessing procedure. To protect the components, in case the OrthoPilot® is to be removed from the operating room, the system has to be set to its transport position, see Transport.