BBraun
SterilContainer System Instructions for Use
83 Pages
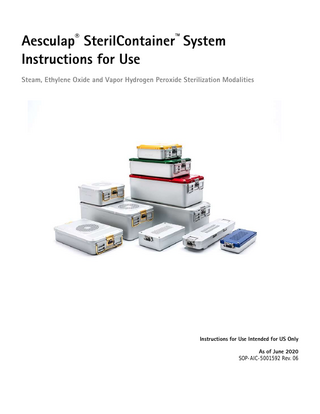
Preview
Page 1
Aesculap® SterilContainer™ System Instructions for Use Steam, Ethylene Oxide and Vapor Hydrogen Peroxide Sterilization Modalities
Instructions for Use Intended for US Only As of June 2020 SOP-AIC-5001592 Rev. 06
Aesculap® SterilContainer™ System Instructions for Use (IFU)
Table of Contents 1.0 2.0 3.0 4.0 4.1
PURPOSE OF INSTRUCTIONS FOR USE ... 4 STERILCONTAINER™ SYSTEM ... 4 STERILCONTAINER™ SYSTEM SERVICE ... 7 DECONTAMINATION AND CLEANING PROCESS... 8 Water Quality...8
4.2
Detergent Solutions...9
4.3
Decontamination and Mechanical Cleaning...9
4.4
Decontamination and Manual Cleaning ... 10
5.0 INSPECTION PRIOR TO USE ... 11 5.1 ... 12 5.2
Basket, Tray and Platforms Inspection Criteria ... 14
6.0 PREPARATION AND ASSEMBLY OF STERILCONTAINER™ SYSTEM ... 14 6.1 SterilCon ... 15 6.2
Assembly of Surgical Instrumentation ... 17
6.3
Loading of Basket, Lifting Platform and Tray ... 17
6.4
Internal Process Indicators ... 18
6.5
External Process Indicators and Tamper Evident Seals ... 18
6.6
Container Storage and Transportation ... 20
7.0 STERILCONTAINER™ SYSTEM STERILIZER CYCLE PARAMETERS - STEAM AND ETO ... 21 7.1 Steam and EtO Sterilization Modality Cycle Parameters ... 22 8.0 STERILCONTAINER™ SYSTEM STERILIZER CYCLE PARAMETERS - ASP STERRAD® ... 29 8.1 STERRAD® Sterilization Modality Cycle Parameters ... 30 9.0 STERILCONTAINER™ SYSTEM STERILIZER CYCLE PARAMETERS - STERIS® V-PRO®... 40 9.1 STERIS® Sterilization Modality Cycle Parameters ... 41 10.0 STERILCONTAINER™ SYSTEM STERILIZER CYCLE PARAMETERS - STERIZONE® ... 47 10.1 STERIZONE® Sterilization Modality Cycle Parameters ... 48 11.0 ASEPTIC PRESENTATION ... 52 11.1 ... 55 11.2
... 55
12.0 STERILE CONTAINER VALIDATION SUMMARY ... 55 12.1 Validation Testing ... 56 12.2
... 57
13.0 CUSTOMER VERIFICATION ... 58 14.0 INDICATIONS FOR USE ... 62 14.1 Steam and EtO Sterilization... 62 SOP-AIC-5001592 Rev. 06 As of June 2020
Intended for US Only Page 2 of 83
Aesculap® SterilContainer™ System Instructions for Use (IFU) 14.2
PreVac IUSS Sterilization ... 63
14.3
JK / JN744 PreVac Steam, IUSS and EtO Sterilization ... 63
14.4
TM
Lid ... 64
14.5
TM
Pro Lid ... 64
14.6
Reusable Filter ... 65
14.7
JS Series... 65
14.8
STERRAD® 100S ... 71
14.9
... 72
14.10 Steri
STERRAD® 100NX EXPRESS Cycle ... 72
14.11
STERRAD® 100NX DUO Cycle ... 73
14.12 STERIS® V-PRO® 60
Steri
... 74
14.13 STERIS® V-PRO® maX Flexible Cycle
... 76
14.14 STERIS® V-PRO® 1 and V-PRO® 1 Plus
... 77
14.15 STERIZONE® VP4 14.16 S
... 78 JS Series EtO, STERRAD®100NX DUO & STERIZONE® VP4 ... 79
List of Figures ...4 ...5 Figure 3: PrimeLineTM Pro Lid Inspection Process ... 10 Figure 4: Filters for Perforated Bottoms and Lids ... 15 Figure 5: Tamper Evident Locks ... 19 Figure 6: Indicator and Communication Cards ... 19 Figure 7: Easy Reference Handout ... 55
List of Images Image 1: Single Use Processing Supplies, Filters, Tamper Evident Locks, Indicator Cards ...6 Image 2: JK, JN and JM Lid Reusable Filter Inspection ... 12 Image 3: Filter Retention Plates and Silicone Gaskets Inspection Process... 13 Image 4: PrimeLineTM Lid Inspection Process ... 13 Image 5: Aluminum Lid with Metal Retention Plate and Reusable Filter ... 16 Image 6: Aluminum Lid with Metal Retention Plate and Single Use Filer Assembly ... 16 Image 7: PrimeLineTM Lid Inspection Process ... 16
SOP-AIC-5001592 Rev. 06 As of June 2020
Intended for US Only Page 3 of 83
Aesculap® SterilContainer™ System Instructions for Use (IFU)
1.0
Purpose of Instructions for Use
The purpose of this document is to: Describe the components of the System, how each should be used, and which components can be used together in each of the sterile processing modalities. Provide detailed instructions on how to use, decontaminate, clean and process the System properly in different sterilization modalities. Give guidance for verifying the System in your facility and application. Instructions included in this document are based on validation testing by Aesculap® in a medical device testing laboratory using worst case scenario. Each facility should ensure their processing system provides similar results. Personnel training and competency is required to perform all phases of processing. Equipment, water supply, and practices all contribute to providing an effective reprocessing system and should be monitored by the facility.
2.0
SterilContainer™ System
The Aesculap® System is a reusable rigid container system used for the packaging, transportation, and storage of instruments prior to, during, and after sterilization. It consists of the various sizes of container bottoms, container lid, and basket options, and Aesculap® accessories such as instrument holders, baskets, filters, indicator cards and tamper evident locks. The first two letters of the part number are the series name, and identify the product family and attributes of each bottom and lid. See chart. Each container bottom must ONLY be used with the specific lid designed for that series of container, and it should not be combined with other Aesculap® or non-Aesculap® series of bottoms or lids. Product Family
SterilContainer™
Bottom Series
JK Solid, Anodized PrimeLineTM4 PrimeLine Pro4
Lid Series3, 5
JK
PreVac Steam
X
X
X
PreVac IUSS
X
X
X
Gravity EtO
X
SterilContainer™ S SterilContainer™ S2 JM Perforated, Non-Anodized
JS Perforated, Anodized
JM
JS
X
X
X
X
X
X
X
X
X
X
X
X
X
X
JK X
JN Perforated, Anodized PrimeLine4 PrimeLine Pro4 X
X
Low Temp STERRAD®1 Low Temp STERIS®2 Low Temp STERIZONE6
1. See section 8.0 System Sterilizer Cycle Parameters ASP STERRAD® for more details on sterilizer cycle details. 2. See section 9.0 System Sterilizer Cycle Parameters STERIS® V-PRO® for more details on sterilizer cycle details. 3. JK, JN, JM, JS and PrimeLine Pro lids are made of aluminum. PrimeLine is made of High-Grade, Thermostable Plastic. 4. PrimeLine and PrimeLine Pro lids have a reusable filter and are only available for JK and JN Series full-size, three-quarter size and half size containers. 5. See 6.0 Preparation and Assembly of System for filter modality compatibility. 6. See section 10.0 System Sterilizer Cycle Parameters STERIZONE® for more details on sterilizer cycle details. Figure 1: SterilContainer™ System
SOP-AIC-5001592 Rev. 06 As of June 2020
Intended for US Only Page 4 of 83
Aesculap® SterilContainer™ System Instructions for Use (IFU) Throughout this IFU document, references to the System include the , S and the S2 product families. References to the only include the JK / JN Series of products, references to S only include JM Series of products, and references to S2 only include JS Series of products.
JK JK Solid Solid Bottom Bottom
The
JN Perforated Bottom
JS JS Perforated Perforated Bottom, Bottom Identified Identified by by the the Gold Gold Handle Handle & & Latch Latch
System full, three-quarter and half size JK Series and JN Series have three lid options.
JK Series Aluminum Lids with Metal Retention Plate
JP1 Series PrimeLineTM Pro
JP0 Series PrimeLine
Aesculap® has performed the required validation tests, including accepted aerosol testing methodology for medical devices, and received FDA clearance for its sterile container products when used in the following sterilizations modalities. The modalities for each container series vary. Please refer to Sections 7.0 (Steam and EtO), 8.0 (STERRAD®) and 9.0 (STERIS®) Cycle Parameters to determine appropriate container bottom, lid, filter, lock and indicator card for sterilization cycle being used. Primary Name
Steam Sterilization1
Ethylene Oxide Hydrogen Peroxide Hydrogen Peroxide and Ozone 1. 2. 3.
Which Includes Dynamic Air Removal PreVacuum Steam Dynamic Air Removal Immediate Use Gravity Ethylene Oxide Gas Plasma Vapor Hydrogen Peroxide Ozone
May Also Be Referred to As PreVacuum Steam, PreVac Steam1,2 PreVacuum Immediate Use, PreVac IUSS1,2 Gravity1 EtO1 Low Temperature1, H2O2, STERRAD®3, STERIS®3, V-PRO®3 Low Temperature1 TS033, STERIZONE3, VP43
These terms will be used throughout the remainder of the Instructions for Use (IFU). Aesculap® validations for PreVac Steam can be applied to Steam Flush Pressure Pulse (SFPP) with like cycles May also be generically referred to by the sterilizer manufacturer model name and/or cycle name. Figure 2: Sterilizations Modality Nomenclature and SterilContainer™ System Compatibility
SOP-AIC-5001592 Rev. 06 As of June 2020
Intended for US Only Page 5 of 83
Aesculap® SterilContainer™ System Instructions for Use (IFU) The System is designed to be processed on a daily basis and provide years of continual use. When selecting a container system, make sure the container and instruments match the application and sterilization requirements properly. provides guidelines on how to conduct an evaluation. System Processing Supplies include single use paper and polypropylene filters, tamper evident locks and indicator cards. See Section 6.0 Preparation and Assembly of System for more information and for filter modality compatibility. All Aesculap® filters, locks and indicator cards have been designed and validated specifically for the System. They should not be used with other brand container systems. Aesculap® does not recommend using non-Aesculap® brand filters, locks and indicator cards, and cannot guarantee proper performance with these products. All processing supplies are shipped non-sterile.
Image 1: Single Use Processing Supplies, Filters, Tamper Evident Locks, Indicator Cards
System accessories include the following: Identification labels or tags Mats Instrument Organization System (IOS) Racks and scope holding platform Instrument stringers Contact an Aesculap® sales representative or customer service for more details on accessories.
Notes:
Each facility should ensure its processing system provides similar results. Personnel training and competency is required to perform all phases of manual processing. Equipment, water supply, and practices all contribute to providing an effective reprocessing system and should be monitored by the facility. Visit www.youtube.com/Aesculapusa System section for informational videos on System proper sterile reprocessing preparation. See AAMI ST79 for more details and recommendations. Silicone instrument holders, mats and the gasket in lid and filter retention plate are not made with natural rubber latex The Aesculap® reusable PTFE filters have been validated and are FDA cleared for PreVac Steam and PreVac Immediate Use Steam Sterilization (IUSS) for up to 2,200 cycles (decontaminate wash inspect-assemble sterilize use). Using a non-toxic permanent marking pen, record the date put into service and the estimated remove from service date, in mm/dd/yy format. Calculate the remove from service date based on the average expected reprocessing levels for your facility. Do not exceed 2,200 cycles.
SOP-AIC-5001592 Rev. 06 As of June 2020
Intended for US Only Page 6 of 83
Aesculap® SterilContainer™ System Instructions for Use (IFU)
Aesculap® baskets and accessories can be cleaned and sterilized following accepted industry guidelines and by using the same processes as Aesculap® sterile container bottoms. Aesculap® IOS pieces (IOS Mounting Type B & C) and mats are made of silicone and cutting them does not change the characteristics of the material and/or its function. Aesculap® System only performs container testing with baskets and does not recommend using containers without baskets or with only mats. The only exception is the JK187 and JN187 because of their size and height, a mat only is acceptable. Aesculap® Sterilit® JF598 and JG600 are non-silicone lubricants and do not require any additional PPE during use. will provide more precise application in small area. When applying oil, a reasonable amount should be used. For the drops this would be one or two drops, and for the spray it would be a light even coating of the area that requires lubrication. Excess oil should be removed with a clear lint-free cloth after proper application. The oil should not cause build up when excess oil is removed and the instrument is cleaned properly. pH by its definition specifically requires a product to be in a water-based solution to be measured, which Sterilit products are not. Therefore it does not have a pH. MSDS sheets are available for products on Aesculap® website, www.Aesculap®usa.com/en/company/quality-assurance.html.
3.0
SterilContainer™ System Service
Like all reusable medical devices, the Prior to Use), and proper care and handling.
System requires inspection prior to use (refer to Section 5.0 Inspection
The Aesculap® System is a FDA Class II device that requires extensive testing and FDA 510(k) clearance. An Aesculap® trained technician can service containers to the original equipment manufacturer dimensions and specifications of the original containers used in the validation and replace parts such as gaskets, filter systems and handles with the same Aesculap® components. ONLY Aesculap® trained technicians are authorized to service the Aesculap® SterilContainer™ System. Using a non-Aesculap® service technician to service containers will void the Aesculap® Warranty on the container and may void any of the validation testing associated with Aesculap® containers. Aesculap® offers a wide variety of container service programs that can be performed by either our highly trained technicians at our central service facility in St. Louis, or by our mobile van service specialists. All of the service specialists are Aesculap® employees who go through extensive training on Aesculap® products. Contact an Aesculap® representative or call customer service (1-800-214-3392 or atscsr.us@Aesculap®.com) for more details.
Notes:
All products being returned for maintenance/service must be thoroughly cleaned and decontaminated before service. Retention plates should be replaced when they show wear, age and/or are damaged. The retention plate on the metal lids should not spin freely when properly installed and in proper working condition. Note that the retention plate may move a little if significant amount of pressure is applied while trying to twist or turn (especially when filter is installed). The black PEEK feet on the Aesculap® JF baskets assist in aligning the JF baskets when stacking them in a container or during the reprocessing process. These feet may wear and/or break overtime depending on the processing (number of times, chemicals, water quality), application (type of set) and use (handling of the product). Inspect basket and feet prior to use. Replace if desired, using Aesculap® part number JF112210.
SOP-AIC-5001592 Rev. 06 As of June 2020
Intended for US Only Page 7 of 83
Aesculap® SterilContainer™ System Instructions for Use (IFU)
4.0
Decontamination and Cleaning Process
Follow fa policies, procedures, and AAMI ST79 recommended guidelines for the transportation of soiled instruments and containers. Always wear appropriate personal protective equipment (PPE) per the healthcare facility and procedures when transporting and cleaning the System.
DO NOT USE abrasive cleaners, metal brushes or abrasive cleaning pads. Use of abrasive products can cause permanent damage to container surfaces. Use of abrasive cleaners or pads will result in warranty exclusion. If the container and/or lid are soiled, they must be fully cleaned. For containers and/or lids that are not soiled and have been removed from the operating room before the patient entered, the facility should determine best cleaning practice based on its established policy and procedures. Container, lids and baskets that may not be used or needed right away should be decontaminated and cleaned prior to storage. The System should be stacked neatly, either assembled or unassembled, in a dry, clean area.
Notes:
Thoroughly clean all Aesculap® container products, baskets, accessories and replacement parts prior to first use and after container service has been performed. Items are shipped nonsterile. Cleaning wipes with pH range of 6.5 to 8.5 that do not contain chlorides will not harm the aluminum surface. The effectiveness of wipes in cleaning the container system has not been evaluated by Aesculap®. The use of wipes should be determined based on established facility policy and procedures. See cleaning wipe manufacturer Instructions for Use and AAMI ST79. Aesculap® has no validation testing for the use of wipes in the decontamination and cleaning process. Remove container bottom and JK Series, JM Series and JS Series aluminum lid retention plate(s) by pushing inward simultaneously on the two buttons on the center section of the retention plate. To replace container bottom and JK Series, JM Series and JS Series aluminum lid retention plate(s), press down evenly Aesculap® baskets may be processed in an ultrasonic cleaner. The ultrasonic cleaner may loosen basket accessors and Instrument Organization System (IOS). Aesculap® has not evaluated the use of bottoms and lids in ultrasonic cleaners.
4.1 Water Quality Water quality is an important consideration in all stages of medical device reprocessing and can contribute to providing an effective reprocessing system and should be monitored by the facility. AAMI TIR34:2014 outlines the different types of water and the specific use of each.
4.1.1 Utility Water Utility water, per AAMI TIR34, is water as it comes from the tap that might require further treatment to achieve the specifications. See AAMI TIR34 for specifications table. This water is mainly used for flushing, washing, and rinsing.
4.1.2 Critical Water Critical water, per AAMI TIR34, is water that is extensively treated (usually by a multistep treatment process that could include a carbon bed, softening, DI, and RO or distillation) to ensure that the microorganisms and the inorganic and organic material are removed from the water; a final submicron filtration could also be part of the treatment process. This water is recommended for the final rinse and steam generation to avoid discoloration or damage resulting from minerals found in utility water.
SOP-AIC-5001592 Rev. 06 As of June 2020
Intended for US Only Page 8 of 83
Aesculap® SterilContainer™ System Instructions for Use (IFU)
4.2 Detergent Solutions Use detergent in a water solution where the detergent and water have a pH range of 6.5 to 8.5 to clean effectively and without causing damage to the or S containers.
Notes: The use of utility water in mechanical washers may result in the water having a high alkaline level which could be harmful to the container surface. Critical water should be used for the final rinse. If white residue is observed on the container, this may have been caused by a high pH, alkaline cleaning solution. Check pH level of water and detergent solution throughout the process reduce to a pH of 6.5 to 8.5. The white residue does not impact form, fit or function. DO NOT USE solvents such as acetone or benzene, which may be found in chemical drying rinses on the PrimeLineTM and PrimeLine Pro Lids. Use of these products can cause permanent damage to lid surfaces and/or filter housing, and result in warranty exclusion.
4.3 Decontamination and Mechanical Cleaning 1. Remove all remaining external process indicators and disposable locks. 2. Remove lid from bottom of container. 3. Remove the basket and any instruments from the container. 4. Single Use Filter a. Remove retention plate(s). b. Remove single use filter(s) and discard (if present). c. Rinse visible debris from retention plate(s). d. The metal retention plate may be washed separately or installed during mechanical washing. 5. Reusable Filter a. Remove retention plate while leaving filter in place. b. Rinse visible debris from retention plate(s). c. Do not discard reusable filter if in good working condition and within recorded date. Reusable filter may remain held in place by the retention plate during cleaning provided there is no visible sign of wear, damage and/or bioburden. The PTFE filter material is hydrophobic so blood and other liquids can be rinsed off the filter if bioburden is observed. d. Replace retention plate(s). 6. Rinse visible debris from all container components. a. Critical water is recommended for the final rinse and steam generation to avoid discoloration or damage resulting from minerals found in utility water. b. For PrimeLineTM and PrimeLine Pro - Exclusively use critical water for the final rinse and make sure no residues from the cleaning process remain on the lid. 7. Place components on washer rack facing down to avoid water collection. a. Fold the lid handles towards the inside of the lid to avoid water collection and damage. b. Retention plates should face away from the direct force of pressurized washer jets to avoid damage during wash cycles. 8. After mechanical cleaning cycle a. Thoroughly dry (either with a soft, dry cloth or air dry) all components, and retention plate and retention plate housing (PrimeLineTM and PrimeLine Pro) before proceeding to preparation and packaging. b. If retention plates were installed during mechanical washing, remove retention plate(s) and dry area between retention plate and container.
SOP-AIC-5001592 Rev. 06 As of June 2020
Intended for US Only Page 9 of 83
Aesculap® SterilContainer™ System Instructions for Use (IFU) (From Aesculap® DOC1006)
Remove filter retention plate by turning counter clockwise.
Retention plate should be free of cracks and damage.
Reusable filter may remain inside lid during inspection. Check filter integrity for rips/tears. Retention plates may be installed during mechanical washing.
Figure 3: PrimeLineTM Pro Lid Inspection Process
Notes: After cleaning, visually inspect and repeat the cleaning process if a visually clean endpoint has not been achieved. DO NOT USE solvents such as acetone or benzene, which may be found in chemical drying rinses on the PrimeLineTM and PrimeLine Pro lids. Use of these products can cause permanent damage to lid surfaces and/or filter housing, and result in warranty exclusion. The integrated filter system, and the decontamination, cleaning, inspection and aseptic presentation process are the same for PrimeLineTM and PrimeLine Pro. To remove sterilization adhesive tape remnant of surface abrasions, we recommend the use of Aesculap®-Eloxal Cleaner (Catalog number JG601). This is a non-abrasive cleaner. Apply the cream, the size of penny with a soft dry, non-linting cloth and rub to polish the surface. If needed, repeat with an increasing volume. Thoroughly remove all residual cleaning cream. Critical water is recommended for the final rinse. Cleaner may cause discoloration and/or fading of colored surfaces. DO NOT USE cleaner on PrimeLineTM lid, and PrimeLine Pro lid filter housing and stainless steel covers.
4.4 Decontamination and Manual Cleaning Each facility should ensure their processing system provides similar results. Personnel training and competency is required to perform all phases of manual processing. Equipment, water supply, and practices all contribute to providing an effective reprocessing system and should be monitored by the facility. 1. 2. 3. 4.
Remove all remaining external process indicators and disposable locks. Remove lid from bottom of container. Remove the basket and any instruments from the container. Single Use Filter a. Remove retention plate(s). b. Remove single use filter(s) and discard (if present). c. Rinse visible debris from retention plate(s). d. The retention plate should be washed separately. 5. Reusable Filter a. Remove retention plate while leaving filter in place. b. Rinse visible debris from retention plate(s). c. Do not discard reusable filter if in good working condition and within recorded date. Reusable filter may remain held in place by the retention plate during cleaning provided there is no visible sign of wear, damage and/or bioburden. The PTFE filter material is hydrophobic, so blood and other liquids can be rinsed off the filter if bioburden is observed. d. Replace retention plate(s). 6. Rinse visible debris from all container components. SOP-AIC-5001592 Rev. 06 As of June 2020
Intended for US Only Page 10 of 83
Aesculap® SterilContainer™ System Instructions for Use (IFU) a. Critical water is recommended for the final rinse and steam generation to avoid discoloration or damage resulting from minerals found in utility water. b. For PrimeLineTM and PrimeLine Pro - Exclusively use critical water for the final rinse and make sure no residues from the cleaning process remain on the lid. 7. Use a soft sponge and detergent, as described in Section 4.2 Detergent Solutions, to clean the components of the . 8. After manually cleaning a. Thoroughly dry (either with a soft, dry cloth or air dry) all components, and retention plate and retention plate housing (PrimeLineTM and PrimeLine Pro) before proceeding to preparation and packaging. b. If retention plates were installed during washing, remove retention plate(s) and dry area between retention plate and container.
Notes: After cleaning, visually inspect and repeat the cleaning process if a visually clean endpoint has not been achieved. If the container and/or lid are soiled, they must be fully cleaned. For containers and/or lids that are not soiled and have been removed from the operating room before the patient entered, the facility should determine best cleaning practice based on its established policy and procedures. Cleaning wipes with pH range of 6.5 to 8.5 that do not contain chlorides will not harm the aluminum surface. The effectiveness of wipes in cleaning the container system has not been evaluated by Aesculap®. The use of wipes should be determined based on established facility policy and procedures. See cleaning wipe manufacturer Instructions for Use and AAMI ST79. Aesculap® has no validation testing for the use of wipes in the decontamination and cleaning process. DO NOT USE Alcohol wipes alcohol will harm the PrimeLineTM lid or PrimeLine Pro filter housing. If components are too large to be immersed at the facility, then the components should be cleaned in a manner that will not produce aerosols. Please refer to AAMI ST79 for recommended practices. To remove sterilization adhesive tape remnant of surface abrasions, we recommend the use of Aesculap®-Eloxal Cleaner (Catalog number JG601). This is a non-abrasive cleaner. Apply the cream, the size of penny with a soft dry, non-linting cloth and rub to polish the surface. If needed, repeat with an increasing volume. Thoroughly remove all residual cleaning cream. Critical water is recommended for the final rinse. Cleaner may cause discoloration and/or fading of colored surfaces. DO NOT USE cleaner on PrimeLineTM lid, and PrimeLine Pro lid filter housing and stainless steel covers. DO NOT USE solvents such as acetone or benzene, which may be found in chemical drying rinses on the PrimeLineTM and PrimeLine Pro Lids. Use of these products can cause permanent damage to lid surfaces and/or filter housing, and result in warranty exclusion. The integrated filter system, and the decontamination, cleaning, inspection and aseptic presentation process are the same for PrimeLineTM and PrimeLine Pro. Aesculap® baskets and accessories can be cleaned and sterilized following accepted industry guidelines and by using the same processes as Aesculap® sterile container bottoms.
5.0
Inspection Prior to Use
Inspection of the container and its components must be conducted PRIOR TO EVERY USE. If any of the conditions described in this section are observed DO NOT USE the or S container bottom and/or lid. Contact Aesculap® for service. Using a non-Aesculap® service technician to service containers will void the Aesculap® Warranty on the container and may void any of the validation testing associated with Aesculap® containers. See Section 3.0 System Service for full details regarding service. Please refer to Sections 7.0 (Steam and EtO), 8.0 (STERRAD®), 9.0 (STERIS®) Cycle Parameters to determine appropriate container bottom, lid, filter, lock and indicator card for sterilization cycle being used. SOP-AIC-5001592 Rev. 06 As of June 2020
Intended for US Only Page 11 of 83
Aesculap® SterilContainer™ System Instructions for Use (IFU)
Notes:
After cleaning, and before use, visually inspect and repeat the cleaning process if a visually clean endpoint has not been achieved. Remove container bottom and JK Series and JM Series aluminum lid retention plate(s) by pushing inward simultaneously on the two buttons on the center section of the retention plate. To replace container bottom and JK Series and JM Series aluminum lid retention plate(s), press down evenly on retent The metal retention plate may be washed separately or installed during mechanical washing. Retention plates should face away from the direct force of pressurized washer jets to avoid damage during wash cycles.
5.1 SterilContainer™ System Inspection Criteria 1. All container components should be inspected and free from a. Observable cracking in aluminum and/or plastic. b. Any misalignment and/or dents in which the lid and bottoms do not adequately mate. c. Any pitting in the aluminum. 2. Lid silicone gasket should be inspected and free from any sign cracking or damage. 3. For metal retention plates. a. Remove retention plate by pressing in on the two tabs and lifting. For reusable filter, leave filter in place during inspection.
Reusable filter may remain in place inside lid during inspection. Check filter integrity for damage. The retention plate may be installed during mechanical washing. Image 2: JK, JN and JM Lid Reusable Filter Inspection
b. Metal filter retention plate and silicone gasket should be inspected and free from: i. Any sign of cracking or damage. ii. Any misalignment or damage in which retention pin, filter, retention plate and/or gasket do not adequately mate. c. Confirm retention plate is not bent by placing retention plate on flat surface to check for continuous contact around edge. Note that when performing the inspection, there will be a uniform space between the outer most edge of the retention plate and the surface since the retention plate has a raised gasket.
SOP-AIC-5001592 Rev. 06 As of June 2020
Intended for US Only Page 12 of 83
Aesculap® SterilContainer™ System Instructions for Use (IFU) (From Aesculap® DOC1006)
Remove filter retention plate by pressing in on the two tabs and lifting.
Place retention plate on flat surface to check for continuous contact around edge. Retention plate gasket should be free of cracks or damage.
Pin for filter retention plate must be secure and firm. The retention plate may be installed during mechanical washing.
Image 3: Filter Retention Plates and Silicone Gaskets Inspection Process
d. Confirm filter retention pin is secure and firm. e. Confirm filter retention plate is secure and firm on retention pin. f. Remove retention plate from service if it does not meet criteria above, and replace with Aesculap® part number JK100 round, JK098 rectangle. 4. For PrimeLineTM and PrimeLine Pro lids. (From Aesculap® DOC1006)
Remove filter retention plate by turning counter clockwise.
Retention plates should be free of cracks and damage.
Reusable filter may remain inside lid during inspection. Check filter integrity for rips/tears. Check that filter is within use-by date. Retention plate may be installed during mechanical washing.
Image 4: PrimeLineTM Lid Inspection Process
a. Remove retention plate by turning counter clockwise. Leaving filter in place. b. Inspect reusable filter for holes, tears and rips. If observed, remove filter from service and replace with Aesculap® part number JP050. c. Confirm filter is within use-by date (<2,200 cycles). Replace as needed. d. Filter retention plate(s) and filter housing(s) should be inspected and free from: i. Any sign of cracking or damage. ii. Any misalignment or damage in which retention plate, filter and/or filter housing do not adequately mate. e. Confirm filter, retention plate and filter housing are secure and firm. f. Remove retention plate from service if it does not meet criteria above, and replace with Aesculap® part number JP001204. g. Replace retention plate by turning clockwise. h. Confirm outside cover is secured firmly. i. PrimeLineTM lid black cover may be replaced with Aesculap® part number JP001202. PrimeLine Pro lid should be serviced by Aesculap®. See 3.0 System Service for full details regarding service.
Notes: SOP-AIC-5001592 Rev. 06 As of June 2020
Intended for US Only Page 13 of 83
Aesculap® SterilContainer™ System Instructions for Use (IFU)
If white residue is observed on the container, this may have been caused by a high pH, alkaline cleaning solution. Check pH level of water and detergent solution throughout the process reduce to a pH of 6.5 to 8.5. The white residue does not impact form, fit or function. The S is made of non-anodized aluminum which undergoes a natural oxidation process. This oxidation process produces a very thin layer on the surface which may appear brown or black. This oxidation process will continue until the entire raw surface is oxidized. This brown or black discoloration is part of the natural processes. Please contact an Aesculap® representative for more information, if needed. Retention plates should be replaced when they show wear, age and/or are damaged. The retention plate on the metal lids should not spin freely when properly installed and in proper working condition. Note that the retention plate may move a little if significant amount of pressure is applied while trying to twist or turn (especially when filter is installed). Excessive removal and replacement of reusable filter over center pin may cause tearing of the center hole. Metal retention plate may be washed separately or installed during mechanical washing. Retention plates should face away from the direct force of pressurized washer jets to avoid damage during wash cycles. Using inspection and test methods other than those outlined in this IFU are not recommended and have not been validated by Aesculap®. The integrated filter system, and the decontamination, cleaning, inspection and aseptic presentation process are the same for PrimeLineTM and PrimeLine Pro. If the PrimeLineTM or PrimeLine Pro internal or external cover falls off after sterilization and before the set is used, the set can maintain sterility if no other event related incidence has occurred since it is a sealed filter system. The broken dustcover should be replaced and/or the lid should be serviced by Aesculap®. See Section 3.0 System Service for full details regarding service.
5.2 Basket, Tray and Platforms Inspection Criteria Baskets, trays and platforms should be inspected and free from: 1. Observable cracking and/or dents 2. Any misalignment of sides, bottom or handles 3. Any loose or worn handles, parts, feet, accessories or instrument organization system components
Notes:
6.0
Baskets with or without feet maybe used with System. Using baskets with feet may help reduce the possibility of scratching of basket on the container bottom. The black PEEK feet on the Aesculap® JF baskets assist in aligning the JF baskets when stacking them in a container or during the reprocessing process. These feet may wear and/or break overtime depending on the processing (number of times, chemicals, water quality), application (type of set) and use (handling of the product). Inspect basket and feet prior to use. Replace if desired, using Aesculap® part number JF112210.
Preparation and Assembly of SterilContainer™ System
Inspection of the container and its components must be conducted PRIOR TO EVERY USE. Please refer to Section 5.0 Inspection Prior to Use to learn how to properly inspect a container and its components. Ensure all container components are completely dry. Each container bottom must ONLY be used with the specific lid designed for that series of container, and it should not be combined with other Aesculap® or non-Aesculap® series of bottoms or lids. Determine the type of bottom and lid being assembled and proceed to that section. Please refer to Sections 7.0 (Steam and EtO), 8.0 (STERRAD®), 9.0 (STERIS®) Cycle Parameters to determine appropriate container bottom, lid, filter, lock and indicator card for sterilization cycle being used. All Aesculap® filters, locks and indicator cards have been designed and validated specifically for the System. They should not be used with other brand container systems. SOP-AIC-5001592 Rev. 06 As of June 2020
Intended for US Only Page 14 of 83
Aesculap® SterilContainer™ System Instructions for Use (IFU) Aesculap® does not recommend using non-Aesculap® brand filters, locks and indicator cards, and cannot guarantee proper performance with these products. All processing supplies are shipped non-sterile. Filter Type Paper Filter w/ Indicator1
PreVac Steam
PreVac IUSS
Gravity
EtO
X1
X1
X1
X1
X
X
X
X
X
X
X
X
X
X
Low Temp
US751
Paper Filter w/o Indicator US994, US999
Polypropylene Filter w/o Indicator
X
X
MD344, MD355
Metal Retention Plate Lid PTFE Reusable Filter JK090, JK091
PrimeLineTM & PrimeLine Pro PTFE Reusable Filter JP050 1.
Filter contains a dual indicator dot, which changes from blue to brown in steam, and to orange in EtO. Figure 4: Filters for Perforated Bottoms and Lids
Notes:
Visit www.youtube.com/Aesculapusa Steril System section for informational videos on System proper sterile reprocessing preparation. All information and steps outlined in this IFU should be followed. Aesculap® DOC1006 and DOC1007 may be used as a reference guide in Prep and Pack, and the OR respectively once personnel training and competency is achieved. The Aesculap® US756, US998, US992, JK092 and JK089 filters are designed for the Aesculap® generation 2 container, circa 1980s. The Generation 2 container filters have a different size and shape compared to the current System.
6.1 SterilContainer™ System Assembly 1. ONLY USE containers and components that have passed the inspection criteria outlined in Section 5.0 Inspection Prior to Use. 2. Please refer to Sections 7.0 (Steam and EtO), 8.0 (STERRAD®), 9.0 (STERIS®) Cycle Parameters based on container system for proper filter selection. 3. For metal retention plates. Remove retention plate by pushing inward on the two buttons on the side of the center section of the retention plate. a. For single use filters. Place one sheet of the appropriate Aesculap® single use filter over each perforated section on the inside of the container lid and if used, the perforated bottom. b. For reusable filters. Leave filter in place during inspection.
SOP-AIC-5001592 Rev. 06 As of June 2020
Intended for US Only Page 15 of 83
Aesculap® SterilContainer™ System Instructions for Use (IFU)
Reusable filter may remain in place inside lid during inspection. Check filter integrity for damage. The retention plate may be installed during mechanical washing. Image 5: Aluminum Lid with Metal Retention Plate and Reusable Filter
c.
Confirm the filter lays flat, and secure each filter with the retention plate. Listen to audible to confirm filter is locked in place.
Confirm the filter is laying flat, and secure each filter with the retention plate. filter is locked in place. Image 6: Aluminum Lid with Metal Retention Plate and Single Use Filer Assembly
4. For PrimeLineTM and PrimeLine Pro retention plates. (From Aesculap® DOC1006)
Remove filter retention plate by turning counter clockwise.
Retention plate should be free of cracks and damage.
Reusable filter may remain inside lid during inspection. Check filter integrity for rips/tears. Check that filter is within use-by date. Retention plate may be installed during mechanical washing.
Image 7: PrimeLineTM Lid Inspection Process
a. Remove retention plate by turning counter clockwise. Leaving filter in place. b. Inspect reusable filter for holes, tears and rips. Confirm filter is within use-by date (<2,200 cycles). Replace as needed with Aesculap® part number JP050. Arrows on filter and filter housing will align when filter is properly installed, see photo. c. Replace retention plate by turning clockwise.
SOP-AIC-5001592 Rev. 06 As of June 2020
Intended for US Only Page 16 of 83
Aesculap® SterilContainer™ System Instructions for Use (IFU)
Notes: The orientation of the paper filter with indicator can be placed in either orientation, indicator dot facing in or out of the retention plate. Facility should determine orientation based on its established policy and procedures. Single use paper filters are not compatible with Low Temperature sterilizers. Aesculap® only used one filter under each retention plate during our validation testing. If multiple filters are placed under retention plate accidentally we recommend that the set be rejected and be reprocessed. Container lid must ONLY be used with Aesculap® brand retention plate(s). Aesculap® retention plates may be identified by the Aesculap® name, the two release buttons on the center section and/or the part number.
6.2 Assembly of Surgical Instrumentation Instruments and all components of the System must be completely dry prior to sterilization processing to allow for adequate sterilant penetration. Sort and assemble thoroughly cleaned and dried instruments into the instrument basket(s), according to established hospital procedures Instructions for Use.
6.3 Loading of Basket, Lifting Platform and Tray The Aesculap®
System may be used with a variety of baskets, trays and platforms.
Instruments set(s) should meet the following requirements: 1. Fit in the container with the proper clearance between the top of the set(s) and the lid; 2. Able to be aseptically removed in the OR; 3. whichever is lower; and 4. Instrument(s) and container IFUs parameters (time/temperature and dry time) can be reconciled. Please refer to Sections 7.0 (Steam and EtO), 8.0 (STERRAD®), 9.0 (STERIS®) Cycle Parameters to determine maximum weight of System for sterilization modality selected. 1. Place assembled instrument basket(s), lifting platform or support racks into the prepared container bottom. 2. Place assembled lid onto the container bottom, aligning handles on bottom with latches on lid. 3. Simultaneously close both locking latches on the container lid.
Notes: All instruments should be arranged per the instrumen Hospitals should refer to AAMI and accepted industry guidelines, and (IFU) regarding weights and weight limits. Hospitals should reconcile the Aesculap® Steril Trays and baskets may be stacked inside the System if clearance requirements (below) are met and the set follows proper acetic presentation guidelines. o Full-Size, Three-Quarter Size, Half-Size Wide-Body, Extra-Long Container Leave one inch of free space between the instruments and the rim of the container for effective processing. Basket handles may closure. o
Extra-Long Mini-Size Container
Instruments and baskets can be loaded to the rim of the container as
long as they o
Mini-Size and Quarter-Size Container
Leave one quarter of an inch of free space between the instruments and the rim of the container for effective processing. Basket handles may encroach into this clearance space as long as
SOP-AIC-5001592 Rev. 06 As of June 2020
Intended for US Only Page 17 of 83
Aesculap® SterilContainer™ System Instructions for Use (IFU) Baskets with or without feet maybe used with System. Using baskets with feet may help reduce the possibility of scratching of basket on the container bottom. The black PEEK feet on the Aesculap® JF baskets assist in aligning the JF baskets when stacking them in a container or during the reprocessing process. These feet may wear and/or break overtime depending on the processing (number of times, chemicals, water quality), application (type of set) and use (handling of the product). Inspect basket and feet prior to use. Replace if desired, using Aesculap® part number JF112210. The System PreVac Steam validation studies were performed with a silicone mat and non-linting "Non-linting absorbent material may be placed in the tray to material be non-linting because lint can carry microorganisms into the surgical site as well as cause foreign-body
6.4 Internal Process Indicators Per AAMI ST79, internal process indicators are used to indicate that the container has been exposed to the sterilization process. If more than one basket/tray is used inside the container system, an indicator should be placed on each basket/tray. The internal biological and/or chemical indicators may be placed in the center of each tray, unless the user feels a more challenging position exists elsewhere. In that case, place the chemical indicator where the user has determined the most challenging location. Use of internal indicators should be in accordan procedures. Process indicators are designed to indicate that the device was exposed to the sterilization process while, integrating indicators are designed to react to all critical variables, with the stated values having been generated to be equivalent to, or exceed, the performance requirements given in the ISO 11138 series for BIs. See AAMI ST79 for full description and use of each type of chemical indicator.
Notes: See Section 12.0 Customer Verification for information on chemical and biologic indicator placement and on how to perform a verification. Aesculap® does not validate containers with paper count sheets containing ink. Users to process count sheets
6.5 External Process Indicators and Tamper Evident Seals Per AAMI ST79, external process indicators are used to indicate that the container has been exposed to the sterilization process and to distinguish between processed and unprocessed containers. Use of external indicators Please refer to Sections 7.0 (Steam and EtO), 8.0 (STERRAD®), 9.0 (STERIS®) Cycle Parameters to determine appropriate container bottom, lid, filter, lock and indicator card for sterilization cycle being used. 1. If desired, select the appropriate Aesculap® Indicator Card and insert into the holding bracket on the outside of the container. A tab at one end of the indicator card will facilitate insertion and removal. 2. Insert the appropriate tamper evident lock into the locking channel on each end. 3. Secure and close the tamper evident lock.
SOP-AIC-5001592 Rev. 06 As of June 2020
Intended for US Only Page 18 of 83
Aesculap® SterilContainer™ System Instructions for Use (IFU) Tamper Evident Locks Blue / US900
PreVac Steam
PreVac IUSS
Gravity
EtO
Low Temp
X
X
X
X
X
No Indicator
Green / US905
X
Change1 Yellow to Orange
Orange / US906
X
Change1 Blue to Brown
X
X
Pink / US9102
X2
Change1 Magenta to Blue
Yellow / US399
X
Change1 Blue to Brown 1.
After sterilization, the external indicator should change from the original indicator color to indicate exposure to sterilant. The post
sterilization indicator color may vary and not be evenly shaded. 2.
Locks must be stored in a controlled room temperature, away from alkaline chemicals, acids and sources of light. Figure 5: Tamper Evident Locks
Insert the lock into the channel, close and confirm it is secure. Repeat on the other side of container. Installation Instructions for All Tamper Evident Locks
Close the latch to secure the lid to container bottom. Insert the tamper evident lock through the channel. Indicator should be facing up (away from container.)
Indicator & Communication Cards MD334, MD335 w/ Indicator
Gently pull on the lock to confirm it is fully fastened and secure. Repeat on the other side of container.
To close, insert end into the base until it clicks and locks in place.
PreVac Steam
PreVac IUSS
Gravity
EtO
Low Temp X
Change1 Blue
MD346, MD876, US754 w/ Indicator Change1,2 Brown in Steam Change1,2 Orange in EtO
US963 w/o Indicator MD399, MD345 w/ Indicator
X
X
X
X
X
X
X
X
X
X
1
Change Brown 1. After sterilization, the external indicator should change from the original indicator color to indicate exposure to sterilant. The post
sterilization indicator color may vary and not be evenly shaded. 2. Filter contains a dual indicator dot, which changes to brown in steam, and to orange in EtO. Figure 6: Indicator and Communication Cards
SOP-AIC-5001592 Rev. 06 As of June 2020
Intended for US Only Page 19 of 83
Aesculap® SterilContainer™ System Instructions for Use (IFU)
Notes: The Aesculap® tamper evident locks with indicator and/or process indicator card may be used as external process indicators. See the outside product packaging label for care and handling information. After sterilization, the external indicator should change from the original indicator color to indicate exposure to sterilant. The post sterilization indicator color may vary and not be evenly shaded. There is no industry standard for the color shift of pre- and post-sterilization indicators to distinguish if a set has been exposed to sterilization. Refer to filter, lock and indicator card charts for proper Aesculap® indicator color changes. Tamper Evident Locks US900, US905, US906 and US399 Store in a cool, dry place. Temperatures between 15° C/60° F and 30° C/86° F should be maintained. Significant changes in storage conditions for prolonged periods can have an adverse effect on the product. (Minor variations over short periods of time will have little or no effect on product.) Extreme storage conditions such as exposure to direct sunlight and/or storage on top of or near heat source should be avoided. DO NOT USE if the indicator dot color has changed before being processed. Tamper Evident Lock US910 Low Temperature external Chemical Indicators (CIs) are particularly sensitive and must be stored in a controlled room temperature, away from alkaline chemicals, acids and sources of light prior to use. DO NOT USE beyond the expiration date provided on the outside product packaging. Change of color prior to use in the sterilizer could indicate that these CIs were exposed to too much light or high temperatures during storage. After being processed, low temperature tamper evident lock should be stored at a controlled room temperature away from alkaline chemicals, acids and sources of light. Indicators may turn white post-sterilization if not stored out of direct lighting. Indicator & Communication Cards MD334, MD335 Store in original packaging until needed. Store unused indicators in controlled room temperature, away from any alkaline chemicals, acids and sources of light. DO NOT USE beyond the expiration date provided on the outside product packaging. Indicator & Communication Cards MD346, MD876, US754, MD399 Store in dry cool place. The Aesculap® MD347 external indicator card is designed for the Aesculap® current System has a slightly different card holder size than the generation 3 container. The functionality and performance of the MD347 is the same as our current MD346 external indicator card.
6.6 Container Storage and Transportation The Aesculap® rigid System is stackable. After sterilization, containers should be stored in a manner that reduces the potential for contamination, see AAMI ST79 and ASHRAE guidelines for further details. DO NOT stack more than three, 25 lbs each, containers high. Follow shelf manufacturer weight and height limit recommendations when stacking the containers during sterile storage.
SOP-AIC-5001592 Rev. 06 As of June 2020
Intended for US Only Page 20 of 83