Instructions for Use
32 Pages
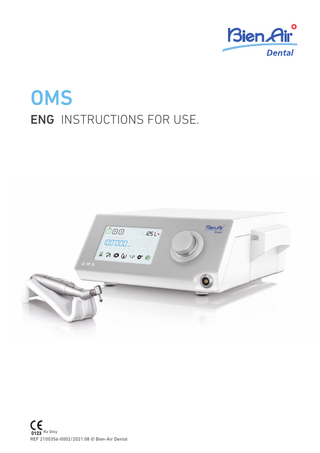
Preview
Page 1
OMS
ENG INSTRUCTIONS FOR USE.
Rx Only
REF 2100356-0002/2021.08 © Bien-Air Dental
Set OMS REF 1700769-001
REF 1601102-001 REF 1303393-001 REF 1600755-001 REF 1601069-001 REF 1600631-001 REF 1500984-005 REF 1307727-010 REF 1301575-001 REF 1502329-002
Options
REF 1600755-001
REF 1600692-001
REF 1600598-001
REF 1600785-001
REF 1600786-001
REF 1600052-001
REF 1600436-001
REF 1601055-001
REF 1600940-001
REF 1600941-001
REF 1600690-001
REF 1600386-001
REF 1600325-001
REF 1303393-001
REF 1601069-001
REF 1600631-001
REF 1301575-001
REF 1502329-002
REF 1307727-010
REF 1307312-010
REF 1501317-100
REF 1500984-010
REF 1501738-010
REF 1501635-010
REF 1501621-010
REF 1307031-001
REF 2100356-0002/2021.08 © Bien-Air Dental
1
Symbols ... 2 1.1 1.2
2
Operation screen description ... 16 Perform an operation, steps P1 and P2 ... 16 Perform an operation, steps P3, P4 and P5... 16
Operation - Surgery mode ... 18 8.1 8.2
9
OMS modes... 14 Rotating knob functions overview... 14 Sound alerts ... 15
Operation - Implantology mode ... 16 7.1 7.2 7.3
8
Install the OMS system... 13 On/off procedure... 13
Interface overview ... 14 6.1 6.2 6.3
7
OMS system overview ...5 Sets supplied...6 Options ...6 Technical data ...7 Performance...8 Environmental protection and information for disposal...8 Electromagnetic compatibility (technical description) ...9 4.7.1 Precautions of use ...9 4.7.2 Electromagnetic compatibility...9 4.7.3 Electromagnetic compatibility – emissions & immunity9
Installation ... 12 5.1 5.2
6
General information ...4 Warnings...4
Description ... 5 4.1 4.2 4.3 4.4 4.5 4.6 4.7
5
Identification ...3 Intended use ...3 Intended patient population ...3 Intended User...3 Intended medical conditions...3 Patient contra-indications and warnings...3 In case of accidents...3 Notation and chapter links ...3
Warnings & Precautions of Use ... 4 3.1 3.2
4
Description of symbols for OMS units ...2 Description of symbols for OMS accessories ...2
Identification, Intended Use and Notation .. 3 2.1 2.2 2.3 2.4 2.5 2.6 2.7 2.8
3
ENG
Table of contents
Operation screen description ... 18 Perform an operation ... 18
Settings ... 20 9.1 9.2 9.3 9.4 9.5 9.6 9.7
Operation mode ... 20 MX-i LED micromotor speed... 20 MX-i LED micromotor torque... 20 MX-i LED micromotor rotation direction ... 20 Irrigation level ... 21 Contra-angle ratio... 21 Luminosity level ... 21
10 Special modes ... 22 11 List of errors & Troubleshooting ... 24 11.1 Safety warning (operating)... 24 11.2 Device operating error... 25
12 Maintenance ... 26 12.1 Servicing... 26 12.2 Cleaning & Sterilization... 26 12.3 Important... 27 12.4 Replacement of fuses ... 27
13 Terms of guarantee ... 28 1
1 Symbols 1.1 Description of symbols for OMS units Symbol
Description
Symbol
CE Marking with number of the notified body.
General symbol for recovery/recyclable.
OFF (power).
Separate collection of electric and electronic equipment.
ON (power).
Manufacturer.
Fuse.
Lamp; lighting, illumination.
Alternating current.
Sound alerts.
Rx Only
Non-ionizing electromagnetic radiation.
REF
Description
Warning: in accordance with federal law (USA), this device is only available for sale upon recommendation by an accredited practitioner.
CAUTION: hazard that could result in light or moderate injury or damage to the device if the safety instructions are not correctly followed.
WARNING: hazard that could result in serious injury or damage to the device if the safety instructions are not correctly followed.
Refer to instruction manual/booklet (https://dental.bienair.com/fr_ch/support/download-center/).
CSA marking - Complies with U.S. and Canadian standards.
SN
Catalogue number.
Serial number.
Authorized EC Representative in the European Community.
Medical Device.
Data Matrix code for product information including UDI (Unique Device Identification).
Equipotentiality.
1.2 Description of symbols for OMS accessories Symbol
XXXX
STERILE EO
Description
Symbol
CE Marking with number of the notified body.
Thermo washer disinfectable.
Expiration date.
General symbol for recovery/recyclable.
Do not reuse.
Separate collection of electric and electronic equipment.
Sterilized with Ethylene Oxyde.
135°C
Electrical safety. Applied part type B.
REF
Catalogue number.
Does not contain DEHP.
Do not use if package is damaged. 2
Description
Sterilizable in autoclave up to the specified temperature. Manufacturer.
SN
Serial number.
Batch code.
2.1 Identification The OMS device encompasses a table-top system for dental implantology and oral surgery allowing to control a dental micromotor which drives a dental handpiece. A peristaltic pump conveys the physiological liquid via a sterile single-use irrigation line. The console includes a single knob control to set the parameters and a foot control used to turn on/off the pump, to navigate through the various steps of the selected procedure and to control the rotation direction of the motor. The device's LCD display shows many parameters of the operation, such as the handpiece gear ratio, bur speed, torque value and irrigation flow setting.
2.2 Intended use All OMS devices are intended to be used in dental implantology and oral surgery. The consoles are designed to operate a specific dental micromotor that drives dental handpieces fitted with appropriate tools to cut hard and soft tissues in the mouth and to screw dental implants.
ENG
2 Identification, Intended Use and Notation • guided and not-guided bone regeneration: when bone grafting, either with artificial or biological grafts, is needed to build a more solid platform where being able to place a dental implant; • apicoectomy: when a tooth’s root tip is removed and a root end cavity is prepared and filled with a biocompatible material. An apicoectomy is necessary when conventional endodontic root canal therapy has failed. The only alternative may be extraction followed by prosthetic replacement for instance with a dental implant; • osteotomy: when a jawbone must be cut, for instance during a ridge split treatment aiming at increasing crestal bone width to have enough room to accommodate an implant; • sequestrectomy: when a portion of necrotic bone must be removed; • hemisection: when a tooth with two roots is cut in half. This procedure may be needed when there is bone loss, or dental decay between the roots, due to periodontal disease. The tooth is cut in half to remove the damaged bone and any damaged root or crown.
2.6 Patient contra-indications and warnings
The intended electromagnetic environment (per IEC 60601-1-2 ed. 4.0) is Professional healthcare facility environment.
No specific patient contra-indication nor warning exist for the OMS device family when the device is used as intended.
2.3 Intended patient population
2.7 In case of accidents
The intended patient population of the OMS consoles includes any person visiting a dental practitioners’ office to receive treatment in line with the intended medical condition. There is no restriction concerning subject age, race, or culture. The intended user is responsible to select the adequate device for the patient according to the specific clinical application.
If an accident occurs, the OMS must not be used until repairs have been completed by a qualified and trained technician authorized by the manufacturer. If any serious incident occurs in relation to the device, report it to a competent authority of your country, as well as the manufacturer through your regional distributor. Observe relevant national regulations for detailed procedures.
2.4 Intended User The OMS is meant to be used only by dentists and dental surgeons in dental offices and hospitals.
2.5 Intended medical conditions Dental implantology is the elective treatment to replace one or more missing teeth. Teeth can be missing for various reasons, such as traumas, partial or total edentulism, and advanced decay that leads to tooth sacrifice because restorative treatments are no longer possible. Dental implantology requires to prepare jawbone to accommodate a dental implant, which is typically a titanium screw fitted with an abutment and a prosthetic crown made of ceramic material mimicking the natural missed tooth. Multi-teeth prosthetic solutions are also available, usually supported by more than one single implant. The main oral surgery treatments include: • impacted teeth extraction: when a tooth partially or totally hidden in the jawbone needs to be removed; • wisdom teeth extraction: when a third molar, either impacted or not, needs to be removed; • non salvageable decayed teeth extraction: when a tooth with a decay at an advanced status must be sacrificed because it cannot be restored anymore;
2.8 Notation and chapter links • A, B, C, etc. Text preceded by a letter indicates a procedure to be carried out step-by-step. • Indicates a procedure result. • (1), (2), (3), etc. Text preceded by a number indicates text used in conjunction with an illustration. • OK, Settings, etc. Text in bold italic font style indicates, on-screen elements such as buttons, menus, menu items, screen areas, values, fields when they are named and screen names. In order to simplify the notation, in this manual: • «Clockwise» is referred to as «CW»; • «Counterclockwise» is referred to as «CCW»; • Forward micromotor rotation mode is referred to as «FWD»; • Reverse micromotor rotation mode is referred to as «REV»; • Rotational speed unit «revolutions per minute» is referred to as «rpm»; • Torque unit «newton centimetre» is referred to as «Ncm»; • Micromotor control unit is referred to as «DMX»;
3
3 Warnings & Precautions of Use 3.1 General information The device must be used by qualified professionals in compliance with the current legal provisions concerning occupational safety, health and accident prevention measures, and these instructions for use. In accordance with such requirements, the operators: • must only use devices that are in perfect working order; in the event of irregular functioning, excessive vibration, abnormal heating, unusual noise or other signs that may indicate malfunction of the device, the work must be stopped immediately; in this case, contact a repair center that is approved by Bien-Air Dental SA; • must ensure that the device is used only for the purpose for which it is intended, must protect themselves, their patients and third parties from any danger. • Avoid contact with liquids.
3.2 Warnings ⚠ CAUTION Any use other than what is specified herein is unauthorized and may be dangerous.
⚠ CAUTION The power plug is used for disconnection in case of problems, it must be easily accessible at all times.
⚠ CAUTION Never connect a handpiece on a running MX-i LED 3rd Gen micromotor.
⚠ CAUTION Any modification of the medical device is strictly forbidden.
⚠ CAUTION The device is not designed for use in an explosive atmosphere (anaesthetic gas).
⚠ WARNING Do not attempt to open the device when it is connected to the electric mains. Risk of electrocution.
⚠ CAUTION The parameters contained in the dental procedures are indicative only. Bien-Air Dental SA cannot be held liable for them.
⚠ CAUTION The device must not be touched by the patient.
⚠ CAUTION Do not simultaneously touch the patient and the electrical connections of the unit.
⚠ CAUTION Ensure that there is no water under the unit before switching it on.
⚠ CAUTION All connectors must be dry before use. Ensure the absence of residual moisture due to cleaning. 4
⚠ WARNING To avoid the risk of electric shock, this equipment must only be connected to supply mains with protective earth.
⚠ WARNING To avoid the risk of eletric shock, this equipment must only be connected to supply mains with protective earth. 2) To avoid any risk of contamination, only control the device via the foot control during surgical procedures. If the removable knob is used during the surgical procedure and / or comes into contact with potentially contaminated surfaces or liquids, follow the procedure for the cleaning and sterilization of the knob described in section 11.
ENG
4 Description 4.1 OMS system overview 3
2 4
8 7 6 5
1
16
15
14
12
11
10
13
9
FIG. 1 (1) (2) (3) (4) (5) (6) (7) (8) (9)
Peristaltic pump lid Foot control connector Marking Bracket support Main switch Fuse box Mains connector Potential equalization connector MX-i LED micromotor
(10) Button to start/stop irrigation (11) Button to reverse the rotation of the MX-i LED micromotor (12) “Program” button to go to next operation step (13) Motor start (14) MX-i LED micromotor connector (15) Control knob (16) LCD control screen
5
4.2 Sets supplied
4.3 Options
OMS set REF 1700769-001
Designation
REF number
Designation
REF number
3-button foot control
1600631-001
OMS unit (1x)
1601102-001
MX-i LED micromotor
1600755-001
MX-i LED micromotor (1x)
1600755-001
1600786-001
3-button pedal (1x)
1600631-001
Contra-angle handpiece CA 20:1 L KM Micro-Series (light)
Cable MX-i LED (2m) (1x)
1601069-001
Contra-angle handpiece CA 20:1 L KM (light)
1600785-001
Sterile protective sheet (2x)
1502329-002
Contra-angle handpiece CA 20:1 L Micro-Series (light)
1600692-001
Pack of 5 disposable sterile irrigation lines
1500984-005 Contra-angle handpiece CA 20:1 L (light)
1600598-001
Pack of 10 attachment collars for fastening the sterile irrigation line to a cable
1307727-010
Contra-angle handpiece EVO.15 1:5 L Micro-Series (light)
1600940-001
Bracket for fluid bottle (1x)
1303393-001 Contra-angle handpiece EVO.15 1:5 L (light)
1600941-001
Handpiece support (1x)
1301575-001 Contra-angle handpiece CA 1:5 L Micro-Series (light)
1600690-001
Contra-angle handpiece CA 1:5 L (light)
1600386-001
Contra-angle handpiece CA 1:5
1600325-001
Contra-angle handpiece CA 1:2.5 L MicroSeries (light)
1601055-001
Straight handpiece PM 1:1
1600052-001
Straight handpiece PM 1:2
1600436-001
Sterile protective sheet (2x)
1502329-002
Box of 100 sterile Bur Guards
1501317-100
Pack of 10 disposable sterile lines 3.5 m
1501738-010
Kirschner/Meyer pack of 10 disposable sterile lines
1501635-010
Kirschner/Meyer type detachable irrigation set for CA 20:1 L KM and CA 20:1 L KM Micro-Series, comprising 10 rings and 10 tubes
1501621-010
Pack of 10 disposable sterile lines
1500984-010
Bracket for fluid bottle
1303393-001
Handpiece support
1301575-001
Cable MX-i LED (2m)
1601069-001
3P cable system, US, medical grade, length 3m (1x)
1307572-001
Pack of 10 attachments collars for fastening the sterile irrigation line to a cable
1307727-010
Pack of 10 fuses T4.0AH 250 VAC high breaking capacity
1307312-010
Knob
1307031-001
3P cable system, US, medical grade, length 3m (1x)
6
1307572-001
Dimensions L x W x H OMS unit...240 x 240 x 102 mm OMS unit (with bracket)...240 x 240 x 482 mm Foot control (without handle) ...206 x 180 x 60 mm Foot control (with handle)...206 x 200 x 155 mm Motor cable (REF 1601069)...L 2.0 m Foot control cable ...L 2.9 m MX-i LED micromotor...23 x 91 mm The foot control is waterproof (IP X8 in accordance with IEC 60529). Weight OMS unit...2.44 kg Foot control (with handle and cable)..877 g Foot control (without handle and cable)... 830 g Bracket ...115 g Cable ...105 g MX-i LED micromotor...115 g Electrical data Voltage...100 – 240 VAC Frequency ...50-60 Hz Environmental conditions Storage Temperature range:
0°C / +40°C
Relative humidity range:
10% - 80%
Air pressure range:
650 hPa - 1060 hPa
Transport Temperature range:
-20°C / +50°C
Relative humidity range:
5% - 80%
Air pressure range:
650 hPa -1060 hPa
Operating temperature Temperature range:
+5°C / + 35°C
Relative humidity range:
30% - 80%
Air pressure range:
700 hPa – 1060 hPa
⚠ CAUTION Do not use OMS outside the range of operating temperature. Classification Class IIa in accordance with European Regulation (EU) 2017/745 concerning medical devices. Electric insulation class Class I per IEC 60601-1 (apparatus protected against electric shocks).
⚠ CAUTION The device must be only used by the operator.
Applied parts (per IEC 60601-1): MX-i LED micromotor...REF 1600755-001 CA 20:1 L ...REF 1600598-001 CA 20:1 L Micro-Series ...REF 1600692-001 CA 20:1 L KM...REF 1600785-001 CA 20:1 L KM Micro-Series...REF 1600786-001 CA EVO.15 1:5 L Micro-Series...REF 1600940-001 CA EVO.15 1:5 L...REF 1600941-001 CA 1:5 L Micro-Series...REF 1600690-001 CA 1:5 L...REF 1600386-001 CA 1:5 ...REF 1600325-001 CA 1:2.5 L Micro-Series ...REF 1601055-001 Straight handpiece 1:1...REF 1600052-001 Straight handpiece 1:2...REF 1600436-001 Irrigation lines ...REF 1500984-010 KM Irrigation lines...REF 1501635-010 Degree of ingress protection UNIT ...IP 41 (protection against insertion of objects larger than 1mm and dripping water (vertically falling drops)) Foot control ...IP X8 Memory Memory storage of 5 steps settings including adjustment of mode, speed, torque, rotation direction, irrigation, contra-angle ratio and light intensity for each step. Languages English. Bracket for physiological liquid flask Stainless steel. Peristaltic pump Pump delivery ...From 30 to 130 ml/min. (5 levels) Hose for pump...External Ø 5.60 mm ...Internal Ø 2.40 mm Wall thickness ...1.60 mm Intended for use with: See instructions for use MX-i LED micromotor...REF 2100245 Cable MX-i LED ...REF 2100163 Contra-angle CA 20:1 L, light ...REF 2100209 Contra-angle CA 20:1 L Micro-Series, light ...REF 2100209 Contra-angle CA 20:1 L KM, light...REF 2100209 Contra-angle CA 20:1 L KM Micro-Series, light ...REF 2100209 Contra-angle handpiece EVO.15 1:5 L Micro-Series, light ...REF 2100294 Contra-angle handpiece EVO.15 1:5 L, light...REF 2100294 Contra-angle handpiece CA 1:5 L Micro-Series, light ...REF 2100294 Contra-angle handpiece CA 1:5 L, light...REF 2100294 Contra-angle handpiece CA 1:5...REF 2100294 Contra-angle handpiece CA 1:2.5 L Micro-Series, light ...REF 2100337 Straight Handpiece 1:1 ...REF 2100046 Straight Handpiece 1:2 ...REF 2100103
ENG
4.4 Technical data
⚠ CAUTION The use of the system with other handpieces, motors or cables has not been validated/certified (speed and torque values are not guaranteed in this case). List of errors & Troubleshooting See chapter “11 List of errors & Troubleshooting” on page 24.
7
4.5 Performance
4.6 Environmental protection and information for disposal
Performance
REF 1600995
Motor speed regulation
Accuracy ± 5% in the speed range 100 - 40'000 rpm (*)
Motor torque regulation
Torque adjustable from 10% to 100% of the maximum torque
Maximum motor torque
5.5 (±5%) Ncm (*)
Maximum motor power
130 (±10%) W (*)
Max motor LED current
250 (± 10%) mA rms
Max motor LED current range
Range adjustable 11 steps each 10% from 0% to 100% of max current value
Power supply output limitation
< 300 W
Irrigation flow
5 levels: 1 drop = 30ml/min 2 drops = 60ml/min 3 drops = 90ml/min 4 drops = 120ml/min 5 drops = 130ml/min
(*) Measurement realized in combination with motors MX-i LED 3rd Gen 1601008 and MXi LED 1600755, contra-angle CA 20:1 L Micro Series 1600692 and/or handpiece PML 1121 1600156. The maximum torque is measured at 1000 rpm with irrigation stopped and it corresponds to a maximum torque of 80 Ncm at the rotative tool if the motor is combined with the contra-angle CA 20:1 L Micro Series 1600692.
In accordance with 80601-2-60, no essential performance is linked to this dental equipment.
8
The disposal and/or recycling of materials must be performed in accordance with the legislation in force.
Separate collection of electric and electronic equipment and accessories in view of recycling. Electrical and electronic equipment may contain dangerous substances which constitute health and environmental hazards. The user must return the device to its dealer or establish direct contact with an approved body for treatment and recovery of this type of equipment (European Directive 2012/19/EU).
ENG
4.7 Electromagnetic compatibility (technical description) 4.7.1 Precautions of use This electronic control is in compliance with electrical safety standards in line with standard IEC 60601-1, edition 3.1, and those governing electromagnetic compatibility in line with standard IEC 60601-1-2, fourth edition.
4.7.2 Electromagnetic compatibility ⚠ CAUTION The OMS complies with the EMC requirements according to IEC 60601-1-2. Radio transmitting equipment, cellular phones, etc., should not be used in the immediate vicinity of the device, since this could affect its operation. The device is not suitable for being used close to highfrequency surgical equipment, magnetic resonance imaging (MRI) and other similar devices where the intensity of electromagnetic disturbances is high. In any case, ensure that no high frequency cables are routed above or near the device. If in doubt, contact a qualified technician or Bien-Air Dental SA. Portable RF communications equipment (including peripherals such as antenna cables and external antennas) should be used no closer than 30 cm (12 inches) to any part of the OMS, including cables specified by the manufacturer. Otherwise, degradation of the performance of this equipment could result.
⚠ CAUTION The use of accessories, transducers and cables other than those specified, with the exception of transducers and cables sold by Bien-Air Dental SA as spare parts for internal components, may result in increased emissions or decreased immunity.
4.7.3 Electromagnetic compatibility – emissions & immunity Guidance and manufacturer’s declaration – Electromagnetic emissions The OMS is intended for use in the electromagnetic environment specified below. The customer or the user of the OMS must ensure that it is actually used in such an environment.
Emissions test
Compliance
Electromagnetic environment - guidance
RF emissions CISPR 11
Group 1
The OMS uses RF energy for its internal operation only. Therefore, its RF emissions are very low and are not likely to cause any interference in nearby electronic equipment.
RF emissions CISPR 11
Class B
Harmonic emissions IEC 61000-3-2
Class A
Emissions due to voltage fluctuations IEC 61000-3-3
Conforming
The OMS is suitable for use in any building, including residential buildings and those directly connected to the public low-voltage power supply network that supplies buildings used for residential purposes.
9
Guidance and manufacturer’s declaration – Electromagnetic immunity The OMS is intended for use in the electromagnetic environment specified below. The customer or the user of the OMS must ensure that it is actually used in such an environment.
Immunity test
IEC 60601 test level
Compliance level
Electromagnetic environment - guidance
Electrostatic discharge (ESD) IEC 61000-4-2
±8 kV contact ±2 kV air ±4 kV air ±8 kV air ±15 kV air
±8 kV contact ±2 kV air ±4 kV air ±8 kV air ±15 kV air
Floors should be wood, concrete or ceramic tile. If floors are covered with synthetic material, the relative humidity should be at least 30%.
Electrical fast transient/ burst IEC 61000-4-4
±2 kV for power supply lines ±1 kV for other lines
±2 kV for power supply lines N.A.
Mains power quality should be that of a commercial or hospital environment.
Surge IEC 61000-4-5
±0.5 kV line to line ±1 kV line to line ±0.5 kV line to earth ±1 kV line to earth ±2 kV line to earth
±0.5 kV line to line ±1 kV line to line ±0.5 kV line to earth ±1 kV line to earth ±2 kV line to earth
Mains power quality should be that of a commercial or hospital environment.
0% UT for 0.5 cycle, at 0°, 45°, 90°, 135°, 180°, 225°, 270° and 315°
0% UT for 0.5 cycle, at 0°, 45°, 90°, 135°, 180°, 225°, 270° and 315°
0% UT for 1 cycle and 70% UT for 25/30 cycles at 0°
0% UT for 1 cycle and 70% UT for 25/30 cycles at 0°
0% UT for 250 cycles at 0°
0% UT for 250 cycles at 0°
Voltage dips, short interruptions and voltage variations on power supply input lines IEC 61000-4-11
Magnetic field due to mains frequency (50/60 Hz) IEC 61000-4-8
Conducted disturbances induced by RF fields IEC 61000-4-6
Radiated RF EM fields IEC 61000-4-3
10
30 A/m
30 A/m
3 VRMS 0,15 MHz – 80 MHz
3 VRMS 0,15 MHz – 80 MHz
6 VRMS in ISM bands 0,15 MHz – 80 MHz
6 VRMS in ISM bands 0,15 MHz – 80 MHz
80% AM at 1 kHz
80% AM at 1 kHz
3 V/m 80 MHz – 2,7 GHz 80 % AM at 1 kHz
3 V/m 80 MHz – 2,7 GHz 80 % AM at 1 kHz
Mains power quality should be that of a commercial or hospital environment. If the user of the OMS requires continued operation during mains power interruptions, it is recommended that the OMS be powered from an uninterruptible power supply or a battery. Magnetic fields generated by the mains frequency should be at levels characteristic of a typical location in a typical commercial or hospital environment. Field strengths from fixed RF transmitters, as determined by an electromagnetic site surveya should be less than the compliance level in each frequency range. Interference may occur in the vicinity of equipment marked with the following symbol:
Proximity fields from RF wireless communications equipment IEC 61000-4-3
IEC 60601 test level
Compliance level
Test freq. [MHz]
Max. power [W]
Immunity test level [V/m]
385
1.8
27
450
2
28
710, 745, 780
0.2
9
810, 870, 930
2
28
1720, 1845, 1970
2
28
2450
2
28
5240, 5500, 5785
0.2
9
Electromagnetic environment - guidance
ENG
Immunity test
Distance: 0.3 m
NOTE: UT is the AC mains voltage prior to application of the test level. a. Field strengths from fixed transmitters, such as base stations for radio (cellular/cordless) telephones and mobile field radios, amateur radios, AM and FM radio broadcasts and TV broadcasts cannot be predicted theoretically with accuracy. To assess the electromagnetic environment due to fixed RF transmitters, an electromagnetic site survey should be considered. If the measured field strength in the location in which the OMS is used exceeds the RF compliance level mentioned above, the OMS should be observed to verify that it is operating normally. If abnormal operation is observed, additional measures may be necessary, such as reorienting or relocating the OMS.
11
5 Installation 1
2
1
1
FIG. 1
2 FIG. 3
FIG. 2
2
1
FIG. 4
1
2
AAAA-MM-JJ
12
FIG. 5
FIG. 6
FIG. 7
FIG. 9
FIG. 10
FIG. 11
FIG. 8
3
FIG. 1 A. Place the OMS on a flat surface capable of bearing its weight.
⚠ CAUTION It may be positioned on a table, on a trolley or any other surface but in no circumstances on the floor. FIG. 2 B. The fuse box may be opened with a screwdriver. 100 - 240 VAC = fuse T4.0AH 250 VAC REF 1307312-010. To replace a fuse, see chapter “12.4 Replacement of fuses” on page 27. C. Connect the power cable (1) to the connector (2). Note 1
⚠ CAUTION The power plug is used for disconnection in case of problems, it must be easily accessible at all times. FIG. 3 D. Connect the foot control cable to the input provided on the rear panel, guiding the connector and plug by means of the index pin on the connector.
⚠ CAUTION Do not lift the foot control holding the connection cable. To disconnect the foot control cable pull the cable socket connector (1). Do not pull the cable (2) without disconnecting the cable socket before. FIG. 4 E. Connect the MX-i LED micromotor cable to the motor output, guiding the connector and plug by means of the index pin on the connector. FIG. 5 F. Align and attach the bracket to the housing provided on the rear of the console and suspend the flask or bottle.
FIG. 7 I. Connect the flexible hose of the irrigation line to the spray tube of the handpiece or contra-angle. FIG. 8 J. Install the peristaltic cassette (1) in the peristaltic pump (2). Check that the cassette is clipped correctly. FIG. 9 K. Close the pump lid (3). If there is resistance to closing, open the lid again and check the correct positioning of the cassette. When the lid is correctly closed, the user should hear a click sound.
ENG
5.1 Install the OMS system
⚠ CAUTION Do not run the pump while the lid is open.
⚠ CAUTION Do not run the pump without irrigation line.
⚠ CAUTION Risk of pinching! FIG. 10 L. Perforate the cap of the physiological liquid flask with the pointed end of the irrigation line after removing the protective cap.
⚠ CAUTION There is no detection of empty physiological liquid flask! Always check the content of the flask before operating. FIG. 11 M. Attach the irrigation line on the motor cable using the 3 attachment collars REF 1307727-010.
5.2 On/off procedure The device can be switched on and off in complete safety using the main switch on the OMS.
⚠ CAUTION Do not switch off the device while the motor is running.
FIG. 6 G. Check the packaging integrity, as well as the expiry date of the irrigation line on the label (1).
⚠ WARNING The medical device must be used only with lines supplied by Bien-Air Dental to ensure trouble-free operation. These lines are sterile and for single use. Re-use may result in microbiological contamination of the patient. H. Remove the single-use sterile irrigation line (2) from its pouch.
NOTES 1 The equipment is powered by the mains power supply (100 240 VAC / 300VA / 50-60Hz).
13
FIG. 1
FIG. 2
6 Interface overview 6.1 OMS modes
6.2 Rotating knob functions overview
The OMS allows to visualize and control operation parameters by the means of the LCD display. A unique screen allows to use the following modes: FIG. 1 • Operation mode (to perform an operation in 3 steps) See chapter “7 Operation - Implantology mode” on page 16 for details.
Note 2
FIG. 2 • Settings mode (to set up operation parameters) See chapter “9 Settings” on page 20 for details. FIG. 3 • Special modes (to test system and reset settings) See chapter “10 Special modes” on page 22 for details. FIG. 4 A. Long press on the rotating knob (1) to switch between Operation and Settings modes. Note 1 See chapter “6.2 Rotating knob functions overview” on page 14 for details. See chapter “10 Special modes” on page 22 for entering special modes.
14
Knob action
Description
CW rotation
Increase current value, go to the element on the right
CCW rotation
Decrease current value, go to the element on the left
One short press (Operation mode)
Go to the next programmed step, acknowledge error messages
One short press (Settings mode)
Enter selected setting, validate and store the current setting value, exit the current setting, acknowledge error messages
One long press
Switch between Operation and Settings modes
Double short press
Enter special modes (only when gear ratio is selected in settings mode)
ENG 1
FIG. 3
FIG. 4
6.3 Sound alerts
NOTES Sound alert
Description
One short beep
Activating irrigation, going to next step, and switching rotation direction to FORWARD
Two short beeps
Deactivating irrigation,and switching rotation direction to REVERSE
Two long beeps
Switching from low speed to high speed programmed step
Alternate short beeps
Warning notifications
Alternate medium beeps
Micromotor REVERSE running indicator
Alternate long beeps
System failure notification
1
The Operation mode is the default startup mode.
2 Any knob or foot control action will be ignored when the motor is running.
15
1
2
3
5
4
6
1
7
8
FIG. 1
FIG. 2
7 Operation - Implantology mode 7.1 Operation screen description FIG. 1 The Operation screen differs whether the micromotor is stopped or running and depending on the active step. It allows to perform an operation in 3, 4 or 5 predefined steps P1, P2, P3, P4, P5 (which can respectively be used to program settings for the bone preparation, drilling, threading and implant insertion phases), and displays the following information: (1) Step P1 (inactive step, in black) (2) Step P2 (inactive step, in black) (3) Step P3 (active step, in green) P4 and P5 steps are disabled by default, see “ Number of steps” on page 22 for enabling them. (4)
Speedometer
Note 1 (5) Torquemeter Note 2 (6) Contra-angle ratio Note 3 (7) Bar graph for torque Note 4 (8) Operation settings symbols See chapter “9 Settings” on page 20 for details on adjusting settings.
7.2 Perform an operation, steps P1 and P2 FIG. 2 A. Operate by pressing the foot control to adjust the MX-i LED 3rd Gen micromotor speed.
Inactive steps symbols turn off when the motor is running. Speedometer displays real-time speed value in black.
Note 5 - 6 - 7 FIG. 3 B. If necessary, release the foot control to perform the following actions:
Speedometer (1) displays the set micromotor maximum reachable speed in cyan. 16
• Turn the knob CW or CCW to respectively increase or decrease the micromotor maximum reachable speed (quick setting mode).
The speedometer is cyan and displays the set micromotor maximum reachable speed (1).
Note 8 • Long press on the knob to change operation settings.
The Settings mode is displayed.
See chapter “9 Settings” on page 20 for details. • Long press on the orange button to activate the 5 Ncm torque boost. Note 9 C. Short press on the foot control’s orange button or on the knob to go to the next step.
The next step symbol turns green and the step’s last used settings are restored. Note 7 - 10
7.3 Perform an operation, steps P3, P4 and P5 FIG. 4 A. In steps P3 (1), P4 and P5, operate by pressing the foot control to adjust the MX-i LED 3rd Gen micromotor speed.
All inactive steps symbols turn off when the motor is running. Speedometer (2) displays real-time value. Torquemeter (3) displays real-time value. The torque bar (5) displays ratio between the real-time torque value (represented by cyan dots when the micromotor is running) and the maximum reached torque (represented by green dot). Note 5 - 6 - 7 B. If necessary, release the foot control to perform the following actions:
Torquemeter (3) displays maximum reached value together with the
symbol (4).
Torque bar (5) dots that were displayed in cyan turn black, except for the maximum value dot which turns green.
ENG 1
1
FIG. 3 • Turn the knob CW or CCW to respectively increase or decrease the micromotor maximum reachable torque (quick setting mode).
The torquemeter (3) turns cyan and displays the set
2
3
FIG. 4
4
5
NOTES
micromotor maximum reachable torque. Note 11 • Long press on the knob to change operation settings. See chapter “9 Settings” on page 20 for details. • Long press on the orange button to activate the 5 Ncm torque boost. Note 9 C. Short press on the foot control’s orange button or on the knob to go to the next step.
The next step symbol turns green and the step’s last used settings are restored. Note 7 - 10
1 Real-time speed value is displayed in black when the MX-i LED 3rd Gen micromotor is running. Maximum reachable speed value stored is displayed in cyan when the MX-i LED 3rd Gen micromotor is not running, in steps P1 and P2. 2 Torquemeter is only displayed when micromotor speed is below 100 RPM in steps P1 and P2. 3 The contra-angle ratio is cyan-colored for direct-drive and green-colored for reduction gears. 4 Torque bar graph is only displayed when micromotor speed is below 100 RPM. 5 Each step settings are restored from the corresponding step last used settings, excluding quick settings made directly in the Operation mode. 6 In REVERSE mode, the rotation direction symbol blinks and there is a sound alert (alternate medium beeps). The Torque value is automatically increased in REVERSE mode when torquemeter is displayed. The torque value can be increased from 0 to 10 Ncm, see chapter see “ Reverse torque boost value” on page 22 to adjust it. 7 Actions on foot control’s buttons have no effect when the micromotor is running. 8 Changing the torque in steps P1 or P2 can only be performed through the Settings mode. 9 The torque boost can only be activated when the torquemeter is displayed in Operation mode, in low speed steps (<100 RPM). 10 For safety reasons, the speed setting icon turns red and blinks together with the speedometer for 2 seconds when switching from low speed to high speed (≥100 RPM) step. 11 Changing the speed in steps P3, P4 and P5 can only be performed through the settings mode.
17
1
2
3
1
5
4
6
FIG. 1
FIG. 2
8 Operation - Surgery mode 8.1 Operation screen description
8.2 Perform an operation
FIG. 1 The Operation screen differs whether the micromotor is stopped or running and depending on the active step. It allows to perform an operation in 3, 4 or 5 predefined steps P1, P2, P3, P4, P5, and displays the following information: (1) Step P1 (active step, in green) (2) Step P2 (inactive step, in black) (3) Step P3 (inactive step, in black) P4 and P5 steps are disabled by default, see “ Number of steps” on page 22 for enabling them.
FIG. 2 A. Operate by pressing the foot control to adjust the MX-i LED micromotor speed.
(4)
Speedometer
Note 1 (5) Contra-angle ratio Note 2 (6) Operation settings symbols See chapter “9 Settings” on page 20 for details on adjusting settings.
Inactive steps symbols turn off when the motor is running. Speedometer displays real-time speed value in black.
Note 3 - 4 - 5 FIG. 3 B. If necessary, release the foot control to perform the following actions:
Speedometer (1) displays the set micromotor maximum reachable speed in cyan. • Turn the knob CW or CCW to respectively increase or decrease the micromotor maximum reachable speed (quick setting mode). Note 6
The speedometer is cyan and displays the set micromotor maximum reachable speed (1).
Note 7 • Long press on the knob to change operation settings.
The Settings mode is displayed.
See chapter “9 Settings” on page 20 for details. C. Short press on the foot control’s orange button or on the knob to go to the next step.
The next step symbol turns green and the step’s last used settings are restored. Note 5
18