Boston Scientific
Rotablator Rotational Angioplasty System
Rotablator Console Instructions for Use Oct 2002
Instructions for Use
47 Pages
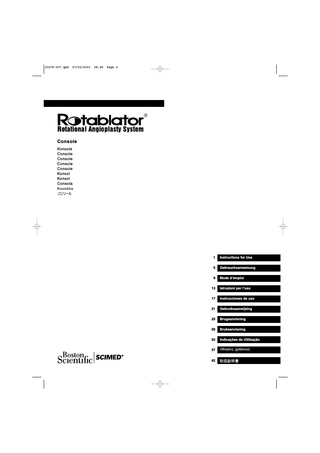
Preview
Page 1
23278-007.qxd
07/02/2003
08:29
Page 6
Description of the Rotablator Rotational Angioplasty System Console
Rotablator™ Rotational Angioplasty System Description The Rotablator rotational angioplasty system is a catheter-based angioplasty device utilizing a diamond-coated elliptical burr at the tip of a flexible drive shaft. Tracking coaxially over a guide wire and rotating at up to 190,000 RPM, the burr ablates plaque into fine particles that are disposed of by the body’s reticuloendothelial system. The three main components included in the system are the guide wire, control console system, and the advancer/catheter.
Rotational Speed Display Procedure Timer Reset Button
The console monitors and controls the rotational speed of the burr and provides the operator with performance information throughout the procedure. In the control console, the gas is filtered and then regulated by a fixed-pressure regulator. The resultant pressure is gated by a pilot-actuated valve, and gas flow is automatically adjusted by a proportional pneumatic valve in order to maintain proper Rotablator system operating speed. The gas then enters the gas turbine, and after expanding in the turbine, is exhausted at the bottom of the Rotablator advancer. Compressed gas is also supplied to the foot pedal through a triple hose. When the foot pedal is depressed, the gas is returned to the console, where it activates the pilot valve, permitting flow of regulated compressed gas to the Rotablator advancer via the front panel turbine connector. With this pilot valve arrangement, the gas flow to the Rotablator advancer cannot be throttled by using the foot pedal.
Turbine Pressure Gauge Stall Indicator Dynaglide Light Event Timer
Advancer Fiber Optic Connector Dynaglide Connector Turbine Connector
Figure 1 Control Console Front Panel
Intended Use The Rotablator console is intended for use with the Rotablator rotational angioplasty system. Refer to guide wire and advancer package inserts for specific information on the use of these components.
The symbols used on the console are listed in Appendix A. The main features and functions of the console are described below.
Front Panel
Restrictions, Warnings and Precautions
•
Restrictions Federal (USA) law restricts this device to use by or on the order of a physician. For coronary use, federal (USA) law further restricts this device to a physician trained and/or experienced in coronary balloon angioplasty. Governing law outside the USA restricts this device to sale by or on the order of a physician.
•
Warnings •
Never use oxygen as the propellant for the Rotablator system. Never connect the regulator to an oxygen cylinder. Oxygen combined with oil or other combustibles in the system can result in an explosion. • This device is not to be used in the presence of flammable anesthetics. • If a hissing noise is detected from the console, check to make sure that the pressure of the gas supplied to the air or nitrogen connector does not exceed 758.4 kPa (110 psi). The console is equipped with a pressure relief valve to protect against excessive inlet pressure. Do NOT operate the Rotablator console with gas pressures in excess of 758.4 kPa (110 psi), as a gas hose may burst. • If patient defibrillation becomes necessary, the physician should take the appropriate measures to protect themselves against electrocution from the defibrillator.
•
•
Precautions • •
Turbine Pressure Control Knob
Power Switch
Care must be taken not to spill saline or other fluids on the console. Saline spilled in the console may result in corrosion or electrical hazard. User should take precautions when using the console in conjunction with other medical electrical equipment, as electromagnetic interference between the equipment may affect the performance of the console or other devices. The console complies with IEC 60601-1-2 regulations for radiation of and immunity from electromagnetic energy.
•
•
•
1
Power Switch: Power is supplied to the console when the switch is in the depressed position. The push button power switch is located in the lower right corner of the front panel. The green light to the left of the switch illuminates to indicate that the power has been turned on. Turbine Pressure Control Knob: The knob located above the power switch is used to adjust the gas pressure to the turbine and consequently, the rotational speed. Turning the knob clockwise increases the turbine pressure (speed) as indicated on the turbine pressure gauge. Counterclockwise rotation decreases the turbine pressure (speed). Turbine Pressure Gauge: Located above the turbine pressure control knob, the pressure gauge displays the pressure of the compressed gas being supplied to the advancer gas turbine. Generally the greater the gas pressure to the gas turbine, the higher the rotational speed. The pressure should not be allowed to exceed 482.6 kPa (70 psi) during normal operation. Flow restrictions have been incorporated into the pneumatic system to prevent the delivery of excessive energy to the advancer. For additional information on operating range, accuracy and precision, see Table 1. Rotational Speed Display (Tachometer): The rotational speed display located in the upper left corner of the console indicates the speed in RPM of the burr and gas turbine. When the gas turbine is not operating, the display is blank. When the foot pedal is depressed, the rotational speed is shown on the rotational speed display. For additional information on operating range, accuracy and precision, see Table 1. STALL Light: The STALL light is located directly below the rotational speed display, and is visible only when illuminated. If the rotational speed of an advancer falls below 15,000 RPM for more than 0.5 second, the red STALL light is illuminated and delivery of compressed gas to the advancer is discontinued. A stall condition may also be detected if the fiber optic connection is not properly engaged. Stall detection is a safety feature designed to discontinue delivery of compressed gas to the advancer in the event of excessive mechanical loading or incorrect connection of the fiber optic. Releasing the foot pedal will clear the stall condition and extinguish the STALL light. DYNAGLIDE Light: The DYNAGLIDE light is located adjacent to the STALL light, and is visible only when illuminated indicating that the Dynaglide feature is activated. The Dynaglide feature provides a controlled low speed rotation (approximately 60,000 - 90,000 RPM) of the Rotablator burr for use during intraprocedure exchange of Rotablator advancer/catheters. The Dynaglide foot pedal button is used to turn Dynaglide on or off. Event Timer: Located below the tachometer, the event timer records how long the foot pedal has been continuously depressed with the air turbine and burr spinning. When the foot pedal is released, the timer continues to display the previous event time. Depressing the foot pedal resets and restarts the timer. For additional information on operating range, accuracy and precision, see Table 1.
23278-007.qxd
•
07/02/2003
08:29
Page 7
Note: It may also be possible to operate this system from a hospital (house) gas system, as discussed in Appendix C. The Rotablator console is not suitable for use with in-hospital (house) compressed gas lines in Germany due to pressure and flow incompatibilities, unless connections are made in accordance with DIN 13 260.
Procedure Timer: The procedure time is the sum of the individual event times and indicates the total time the burr has been spinning during the procedure. For additional information on operating range, accuracy and precision, see Table 1. Table 1
Display Turbine Pressure Gauge
Cylinder Regulator
Operating Range Accuracy Precision 0-689.5 kPa or 0-100 psi ± 5% 6.9 kPa or 1 psi
Rotational Speed Display 0 - 250,000 RPM
± 1.5%
1,000 RPM
Event Timer
00:00 - 59:59
± 0.1%
1 second
Procedure Timer
00:00 - 59:59
± 0.1%
1 second
Recorder Connector
0 - 1 VDC
± .015VDC Infinite
Supply Hose
Cylinder Advancer Hose
•
Reset Button: Pushing the reset button resets the event and procedure timers to zero. • Turbine Connector: The gas line connector on the right-hand side receives the advancer gas hose and supplies filtered, regulated compressed gas to the advancer when the foot pedal is depressed. • Dynaglide™ Connector: The gas line connector on the left-hand side receives the Dynaglide foot pedal pink hose, and is used to activate or deactivate the Dynaglide mode of operation. • Fiber Optic Tachometer Cable Connector: These two female connectors receive the mating male connectors from the fiber optic tachometer cable. The orientation of the cable to the female connector is not important. The fiber optic tachometer cable carries light pulses which the console uses to determine the rotational speed of the gas turbine and burr.
Foot Pedal Hose
Saline Infusion Port Advancer Catheter
Turbine Connector Fiber Optic Connector
Rear Panel •
•
•
•
•
•
Dynaglide Foot Pedal
Line Cord: This cable plugs into a conventional 100-120 V a.c. or 220-240 V a.c. receptacle (as indicated on the name plate located on the rear of the console) and provides power to the console. In Germany, line cord connections must be to a VDE 0107 compliant installation. The ground wire of the line cord is internally connected to the console chassis. Fuses: The fuses protect the console’s electrical components in the event of a serious electrical fault. If a fuse should fail, refer to Appendix B for replacement instructions. Potential Equalization Connector: Located to the left of the fuse, the potential equalization connector is provided to allow potential equalization between various hospital electrical instruments. In Germany, the potential equalization connections must be made to a VDE 0107 compliant installation. Compressed Gas Inlet: This male connector, located in the top center of the rear panel, mates to the corresponding connector on the supply line from the compressed gas source. Pressure at this inlet should always be between 620.5 and 758.4 kPa (90 and 110 psi) with a minimum flow capacity of 140 l/min (5 standard cubic feet per minute (scfm)). Pressure will be reduced by the console to operating limits. An internal pressure-relief valve protects against input pressures in excess of 792.9 kPa (115 psi) and creates a loud hissing noise in the console when the pressure exceeds 792.9 kPa (115 psi). Dynaglide Foot Pedal Connectors: These two connectors receive the mating pair of connectors from the Dynaglide foot pedal. The green hose connects to the right-hand connector and the blue hose to the left-hand connector. Recorder Connector: The recorder connector is used to connect a standard chart recorder or similar device to record the burr rotational speed over time. It allows the physician to monitor the rotational speed of the burr throughout the procedure. The output impedance is 100 ohms. For additional information, see Table 1.
Figure 2 Control Console System To put the Rotablator console into service, proceed as follows: WARNING NEVER use oxygen as the propellant for the Rotablator rotational angioplasty system. NEVER connect the regulator to an oxygen cylinder. Oxygen combined with oil or other combustibles in the system can result in an explosion. WARNING This device is not to be used in the presence of flammable anesthetics. 1. Procure a compressed gas cylinder containing either compressed air or nitrogen. In Germany, only compressed air may be used, gas cylinder fittings must be according to DIN 477 Teil 1 (Druckluft), and compressed gas cylinders must be approved by the German government (Bauartzugelassen). A cylinder capacity of at least 2250 l (80 standard cubic feet) is recommended, and will provide approximately 20 minutes of service with the Rotablator advancer running at full speed. Larger cylinders may be used. A fully charged spare cylinder should always be available. 2. Secure the compressed gas cylinder in accordance with hospital procedures. 3. Obtain a cylinder regulator (relieving type is preferred) capable of delivering at least 140 l/min (5scfm) at 620.5 - 758.4 kPa (90 - 110 psi) . Make certain that the cylinder regulator fitting is compatible with the gas cylinder being used. In Germany, only compressed air may be used, gas cylinder fittings must be according to DIN 477 Teil 1 (Druckluft), and compressed gas cylinders must be approved by the German government (Bauartzugelassen). 4. Connect the supply hose gas coupling (provided with the Rotablator console) to the outlet port of the cylinder regulator.
Other •
•
Console
Dynaglide Foot Pedal: The foot pedal is used as an on/off control for the advancer gas turbine. The foot pedal is also fitted with a valve which vents any compressed gas in the foot pedal hose when the pedal is released, permitting the burr to stop rapidly. The foot pedal is mounted in a protective shroud which inhibits accidental actuation. The Dynaglide button located on the right side of the foot pedal housing is used as an on/off control for the Dynaglide mode of operation. When Dynaglide is on, the green DYNAGLIDE light is illuminated on the console front panel.
Unless local government regulations require otherwise, the gas coupling is configured with 1/4” MNPT threads. Verify the type of gas coupling provided with the Rotablator console prior to procuring a cylinder regulator. If necessary, use suitable adapters to make the connection. In some countries, the regulator end of the gas supply hose has a permanently attached warning tag to remind users not to connect it to oxygen sources. Do NOT remove this tag. 5. Remove the cylinder cap and attach the regulator, tightening the cylinder fitting firmly.
Assembly and Setup of the Rotablator™ Rotational Angioplasty Console
The regulator should be adjusted so that the outlet pressure is in the range 620.5 - 758.4 kPa (90 - 110 psi). 6. Connect the supply hose to the inlet connector on the back of the console.
The recommended control console system, illustrated in Figure 2, consists of an air or nitrogen pressure regulator mounted on a compressed gas cylinder, connected to the Rotablator console via a supply hose (provided with the console). The gas cylinder is shown for illustration only, and is not of the recommended size. Gas cylinders must be properly secured per standard procedures.
In most countries, the inlet connector is marked AIR OR NITROGEN. In Germany, the inlet connector is marked ‘Druckluft’. Verify that the compressed gas being placed into service is in accordance with the inlet connector marking.
2
23278-007.qxd
07/02/2003
08:29
Page 10
7. Connect the foot pedal to the console by first locating the three connectors at the end of the foot pedal triple hose.
Appendix A - Console Symbols (Including Caution/Warning Symbols)
Insert the green hose connector in the right hand and the blue hose connector in the left hand mating receptacles on the rear of the Rotablator™ console. These receptacles are labeled FOOT PEDAL or marked with a foot pedal symbol. Connect the pink hose connector to the left-hand connector on the front panel.
The symbols shown below may be present when required by specific safety testing agencies such as Underwriters Laboratories (UL), Canadian Standards Association (CSA), etc.
8. Connect the power cord to a properly rated hospital grade receptacle (as indicated on the nameplate located on the rear of the console).
Dangerous voltage. To reduce risk of electric shock, do NOT remove cover. Refer servicing to qualified service personnel.
In Germany, power connections must be made to a VDE 0107 compliant installation, and the potential equalization stud must be connected. 9. Open the compressed gas cylinder valve, or line valve if running on house air (see Appendix C), to supply compressed gas to the console.
Potential equalization connector. Provides means of achieving potential equalization between hospital instruments. In Germany, connection must be to a VDE 0107 compliant installation.
Note that the cylinder regulator gauge indicates the pressure of the gas remaining in the cylinder. The regulator should be adjusted so that it never supplies more than 758.4 kPa (110 psi) to the console, and no less than 620.5 kPa (90 psi). Do not initiate the procedure if less than 3,447.35 kPa (500 psi) of gas remains in the tank.
Indicates that a fire hazard may exist if fuses are not replaced as marked.
Indicates type CF equipment.
WARNING If a hissing noise is detected from the console, check to make sure that the gas pressure supplied to the air ornitrogen connector does not exceed 758.4 kPa (110 psi). The console is equipped with a pressure relief valve to protect against excessive inlet pressure. Do NOT operate the Rotablator console with gas pressures in excess of 758.4 kPa (110 psi), as a compressed gas hose may burst.
Attention! See Instructions for Use. Console power is OFF when the power switch is in the OUT position.
10. Push the console power switch and confirm that the green light illuminates indicating power is on.
Console power is ON when the power switch is in the IN position.
The Rotablator rotational angioplasty console is now ready for use. Console placement, ventilation, splash protection and cleaning instructions may be found below in the section entitled: “Operation, Cleaning and Disposal Instructions”.
Rotational Speed. Displays speed of the burr in RPM.
Operation, Cleaning and Disposal Instructions Event Time. Displays the length of time the foot pedal has been continuously depressed.
1. Ventilation The Rotablator console uses natural convection cooling to maintain the proper operating temperature for internal components. Cooling vents are located on the bottom and rear of the console enclosure. In order to ensure proper ventilation of the console, it must be placed on a hard, flat surface with a minimum of 2.5 cm (1”) clearance maintained around all sides and bottom of the enclosure. Do not set on drapes or bedding.
Procedure Time. Displays the sum of the individual event times.
2. Splash Reset. Resets the event and procedure timers to zero.
The Rotablator console is designed to be placed outside of the sterile field. Care should be taken to protect the console from splash and ingress of liquids which may cause damage to internal components. 3. Cleaning
Turbine Pressure. Displays the pressure of the compressed gas being supplied to the advancer gas turbine.
The Rotablator console and Dynaglide™ foot pedal should be cleaned regularly by wiping with a soft cloth dampened with a mixture of water and mild detergent. Never immerse in fluids. The use of solvents or abrasive cleaners may cause damage to the plastic parts of the console and should be avoided.
Turbine pressure increases with clockwise rotation. Fiber optic connector.
4. Disposal The user should follow local and national regulations for disposal of electronics when disposing of this unit. The console contains no batteries or heavy metals.
Turbine. Connector for the advancer gas hose.
References For coronary use, please refer to the Rotablator system physician training program course materials for a listing of publications, or contact your local sales representative. Additional articles, including publications on the use of the Rotablator system in the peripheral vasculature are available upon request. Please contact your local sales representative to obtain a listing.
Compressed Gas Inlet. Connector for the supply line from the compressed gas source.
Foot pedal connectors.
Graphical recorder connector.
3
23278-007.qxd
07/02/2003
08:29
Page 11
With the console connected to AC power and compressed gas, and with the Dynaglide™ foot pedal connected, turn on the unit, cycle the Dynaglide button on the foot pedal, and verify that the DYNAGLIDE indicator illuminates and goes blank.
Appendix B - Service and Maintenance Information Technical Specifications Electrical Specifications:
7. Check the operation of the STALL display.
Catalog Number
Voltage
Frequency
Power
Fuses
H802220200391 M001138000
100-120 V a.c.
50-60 Hz
70 W
2 x 2.0 A, 250V
H802220200331 H802220200341 H802220200361 H802220200381 M001138400 M001138410 M001138420 M001138430
220-240 V a.c.
50-60 Hz
70 VA
2 x 2.0 A, 250V
Recorder Output:
Service Information
Voltage: Impedance:
Pneumatic Input Gas: Specifications: Pressure: Flow: Operating Conditions:
Storage Conditions:
Without connecting the advancer (i.e., no fiber optic connector plugged in), activate the foot pedal and check for stall light illumination. Verify that the stall light goes blank when foot pedal is released.
Fuse: In the event of a fuse failure, turn off the power and unplug the line cord from the power outlet. The power cord may also be unplugged from the rear of the console to improve fuse access. Using a tool such as a screwdriver, remove the fuse drawer by depressing the locking tab. See Figure 3 below.
0.4 Volts per 100,000 RPM 100 ± 5 ohms Power Cord Receptacle
Compressed Air or Nitrogen 620.5 - 758.4 kPa (90 - 110 psi) Minimum, 140 l/min (5 scfm) at rated pressure.
Ventilation:
Minimum 2.5 cm (1”) clearance on all sides, with console on a hard flat surface. Temperature: +10º to +40ºC Humidity: 10% to 90% non condensing
Locking T
Temperature: -30º to +60ºC Humidity: 10% to 95% non condensing
ab
Fuse Drawer
Safety Agency Underwriters Laboratory (UL) recognized component: UL544. Registration: Canadian Standards Association (CSA) certified to CSA Std. C22.2 Nos. 0, 0.4, & 125, risk class 3. National Australia Testing Agency (NATA) Type CF equipment (IEC 601). TUV certifications to IEC 601, EN550011, Class B and EN60601-1-2.
Figure 3 Fuse Replacement Replace both fuses with the same type and rating as specified on the rear of the console. Reinsert the fuse drawer until the locking tab snaps into place. Reconnect the power cord and restore power to the console. If a fuse fails again, disconnect all power to the console and contact your Customer Service representative.
Quarterly Inspections These inspections should be performed once per quarter. If console fails any of the inspections listed below, contact your Customer Service representative.
All other service must be performed by Boston Scientific Corporation personnel. Field repair, other than the console’s external fuse replacement, voids all warranties and may not be performed without express authorization from Customer Service.
1. Check the physical condition of the power cable, strain relief, and plug. Make sure that there are no frayed ends on the power cable connector, the strain relief is attached, the plug has no bent prongs, and the ground prong in the plug is present and secure. Verify that there are no unacceptable scratches or punctures on the exterior of the AC cord set. 2. Check for loose or missing screws, sharp edges, or loose connectors. By hand, check the console pneumatic connectors and verify that they are not loose. Verify that all screws are in place on covers. Hold console in both hands and shake in two different directions to verify that there is no loose hardware inside the console. 3. Perform an external visual inspection for mechanical damage. Verify that there are no unacceptable chips, dents, scratches, or marks on the console enclosure or foot pedal. Verify that the knobs are secured properly and are not loose. Tighten any loose knobs. Make sure that the pneumatic connectors are in working order, not stuck open, and are tight against the console. 4. Check the front panel indicators. With the console connected to AC power and compressed gas, cycle the Power switch to apply power to the console and verify that: a) The green Power LED illuminates. b) The EVENT TIME display reads 00:00. c) The PROCEDURE TIME display reads 00:00. d) The RPM display is blank. e) The STALL display is blank. 5. Check the operation of the turbine pressure gauge. Connect the console to AC power and compressed gas. Starting with the SPEED ADJUST knob fully counterclockwise, verify that clockwise rotation of the SPEED ADJUST knob results in an increasing reading on the console TURBINE PRESSURE gauge. 6. Check the operation of the DYNAGLIDE display.
Appendix C - Running the System From Low Pressure (House) Lines Note: This appendix does NOT apply to equipment used in Germany. The Rotablator™ rotational angioplasty system is designed to be operated from compressed gas cylinders via a cylinder regulator. However, if a house air or nitrogen system is available, the control console can be supplied directly, eliminating the need for a cylinder and cylinder regulator. The requirements are as follows: 1. The compressed gas must be air or nitrogen only. 2. The gas must be clean, dry, and oil free. 3. The gas pressure must be between 620.5 kPa (90 psi ) and 758.4 kPa (110 psi) at the inlet to the control console. 4. The system must be capable of supplying gas at a rate of 140 l/min (5 scfm) or more. An adapter fitting is supplied with the Rotablator console. This fitting has a female quick-connect on one end and .6cm (1/4”) MNPT threads on the other. The .6 cm (1/4”) MNPT end is a standard .6cm (1/4”) pipe male fitting and will readily fit most gas handling equipment or connectors on the house lines. The quick-connect mates directly to the connector on the end of the supply hose which normally would attach to a regulator.
4
23278-007.qxd
07/02/2003
08:29
Page 13
ÐáñÜñôçìá Á - Óýìâïëá Êïíóüëáò (ÓõìðåñéëáìâÜíïíôáé ôá Óýìâïëá Ðñïöýëáîçò / Ðñïåéäïðïßçóçò)
ÐáñÜñôçìá  - Ðëçñïöïñßåò ÓõíôÞñçóçò êáé Åðéóêåõþí Ôå÷íéêÝò ÐñïäéáãñáöÝò
Ôá óýìâïëá ðïõ öáßíïíôáé ðáñáêÜôù ìðïñåß íá õðÜñ÷ïõí üôáí áðáéôïýíôáé áðü óõãêåêñéìÝíïõò öïñåßò, üðùò ôï Underwriters Laboratories (UL), ôï Canadian Standards Association [Êáíáäéêüò Óýíäåóìïò Ðñïôýðùí], êëð Åðéêßíäõíç ôÜóç.
ÇëåêôñéêÝò ÐñïäéáãñáöÝò:
Ãéá íá ìåéþóåôå ôïí êßíäõíï çëåêôñïðëçîßáò, íá ÌÇÍ áöáéñåßôå ôï êÜëõììá. ÁíáèÝóôå ôç óõíôÞñçóç óå åîïõóéïäïôçìÝíï ðñïóùðéêü óõíôÞñçóçò. ÓõíäåôÞñáò åîéóïññüðçóçò äõíáìéêïý. ÐáñÝ÷åé ìÝóá åðßôåõîçò åîéóïññüðçóçò äõíáìéêïý ìåôáîý ôùí íïóïêïìåéáêþí ïñãÜíùí. Óôç Ãåñìáíßá, ç óýíäåóç ðñÝðåé íá ãßíåôáé óýìöùíá ìå ôï ðñüôõðï åãêáôÜóôáóçò VDE 0107. Êáèïñßæåé üôé ìðïñåß íá õðÜñ÷åé êßíäõíïò öùôéÜò åÜí äåí áíôéêáôáóôáèïýí ïé áóöÜëåéåò üðùò áíáãñÜöåôáé.
Áñ. Êáôáëüãïõ
ÔÜóç
Óõ÷íüôçôá
Éó÷ýò
ÁóöÜëåéåò
H802220200391 M001138000
100 - 120 V AC
50 - 60 Hz
70 Watts
2 x 2,0 A, 250V
H802220200331 H802220200341 H802220200361 H802220200381 M001138400 M001138410 M001138420 M001138430
220 - 240 V AC
50 - 60 Hz
70 VA
2 x 2,0 A, 250V
Êáèïñßæåé åîïðëéóìü ôýðïõ CF.
Ðñïóï÷Þ! Äåßôå ôéò Ïäçãßåò ×ñÞóåùò.
¸îïäïò ÊáôáãñáöÝá:
ÔÜóç: Áíôßóôáóç:
0,4 Âïëô áíÜ 100.000 ÓÁË 100 +/- 5 ohms
ÐñïäéáãñáöÝò áåñïêßíçôïõ:
ÁÝñéï Åéóüäïõ: Ðßåóç: ÑïÞ:
ÐeðéeóìÝíïò ÁÝñáò Þ Áæþôï 620.5 - 758.4 kPa (90 - 110 psi) ÅëÜ÷éóôç, 140 ëßôñá/ëåðôü (5 scfm) óe ôéìÞ ðßeóçò
ÓõíèÞêåò Ëåéôïõñãßáò:
ÅîáÝñùóç:
Èåñìïêñáóßá: Õãñáóßá:
ÅëÜ÷éóôç áðüóôáóç 2.5 cm (1“) áðü êÜèe ðëeõñÜ, ìe ôçí êïíóüëá óe óêëçñÞ êáé eðßðeäç eðéöÜíeéá. +10°C Ýùò +40°C 10% Ýùò 90% ÷ùñßò óõìðýêíùóç
ÓõíèÞêåò ÁðïèÞêåõóçò:
Èåñìïêñáóßá: Õãñáóßá:
-30° Ýùò +60°C 10% Ýùò 95% ÷ùñßò óõìðýêíùóç
Ðéóôïðïßçóç ÖïñÝá Áóöáëåßáò:
ÁíáãíùñéóìÝíï åîÜñôçìá áðü ôï Underwriters Laboratory (UL). UL 544. ÐéóôïðïéçìÝíï ãéá ôï ðñüôõðï CSA C22.2 Áñ. 0, 0.4, & 125 êáôçãïñßá êéíäýíïõ 3, áðü ôï Canadian Standards Association (CSA). National Australia Testing Agency (Åèíéêüò ÖïñÝáò ÅëÝã÷ùí Áõóôñáëßáò - NATA). Åîïðëéóìüò ôýðïõ CF (IEC 601). ÐéóôïðïéÞóåéò TUV ãéá ôá IEC 601, EN550011, ÊëÜóçò B êáé EN60601-1-2.
Ç éó÷ýò åßíáé OFF [ÊËÅÉÓÔÇ] óôçí êïíóüëá üôáí ï äéáêüðôçò çëåêôñïäüôçóçò åßíáé óôç èÝóç OUT [ÅÎÙ]. Ç éó÷ýò åßíáé ÏÍ [ÁÍÏÉÊÔÇ] óôçí êïíóüëá üôáí ï äéáêüðôçò çëåêôñïäüôçóçò åßíáé óôç èÝóç ÉÍ [ÌÅÓÁ]. ÐåñéóôñïöéêÞ ôá÷ýôçôá: ÐáñïõóéÜæåé ôçí ôá÷ýôçôá ôçò öñÝæáò óå ÓÁË.
×ñüíïò óõìâÜíôïò: ÐáñïõóéÜæåé ôï ÷ñüíï ðïõ ï ðïäïäéáêüðôçò Þôáí ðéåóìÝíïò óõíå÷þò.
×ñüíïò äéáäéêáóßáò: ÐáñïõóéÜæåé ôï óýíïëï ôùí áôïìéêþí ÷ñüíùí óõìâÜíôùí.
Ìçäåíéóìüò: ÅðáíáöÝñåé ôï ÷ñïíüìåôñï ôïõ óõìâÜíôïò êáé ôçò äéáäéêáóßáò óôï ìçäÝí.
Ôñéìçíéáßåò ÅðéèåùñÞóåéò
Ðßåóç Óôñïâßëïõ [Ôïõñìðßíáò] Äåß÷íåé ôçí ðßåóç ôïõ ðåðéåóìÝíïõ áåñßïõ ðïõ ðáñÝ÷åôáé óôï óôñüâéëï ôïõ ðñïùèçôÞ.
Èá ðñÝðåé íá ðñáãìáôïðïéåßôå áõôÝò ôéò åðéèåùñÞóåéò ìéá öïñÜ êÜèå ôñßìçíï. ÅÜí áóôï÷Þóåé ç êïíóüëá óå ïðïéáäÞðïôå áðü ôéò ðáñáêÜôù áíáãñáöüìåíåò åðéèåùñÞóåéò, åðéêïéíùíÞóôå ìå ôïí Áíôéðñüóùðï ÅîõðçñÝôçóçò Ðåëáôþí.
Ç ðßåóç óôï óôñïâéëïêéíçôÞñá áõîÜíåé ìå äåîéüóôñïöç ðåñéóôñïöÞ.
1. ÅëÝãîôå ôç öõóéêÞ êáôÜóôáóç ôïõ êáëùäßïõ éó÷ýïò, ôçí áóöÜëåéá óõíäÝóìïõ êáé ôï âýóìá. Âåâáéùèåßôå üôé äåí õðÜñ÷ïõí êáìÝíá Üêñá óôï óõíäåôÞñá ôïõ êáëùäßïõ çëåêôñïäüôçóçò, üôé åßíáé óõíäåìÝíç ç áóöÜëåéá óõíäÝóìïõ, üôé ôï âýóìá äåí Ý÷åé óôñåâëùìÝíïõò áêñïäÝêôåò, êáé üôé ï áêñïäÝêôçò ãåßùóçò óôï âýóìá åßíáé åêåß êáé óå êáëÞ êáôÜóôáóç. Åðáëçèåýóôå üôé äåí õðÜñ÷ïõí ìç áðïäåêôÝò ãñáôóïõíéÝò Þ ôñõðÞìáôá óôï åîùôåñéêü ìÝñïò ôïõ óåô ôïõ êáëùäßïõ çëåêôñïäüôçóçò AC. 2. ÅëÝãîôå ãéá ôõ÷üí ÷áëáñÝò âßäåò Þ ãéá âßäåò ðïõ ëåßðïõí, ôá áé÷ìçñÝò ãùíßåò Þ ÷áëáñïýò óõíäåôÞñåò. ÅëÝãîôå ìå ôï ÷Ýñé óáò ôïõò áåñïêßíçôïõò óõíäåôÞñåò ôçò êïíóüëáò êáé åðáëçèåýóôå üôé äåí åßíáé ÷áëáñïß. Åðáëçèåýóôå üôé üëåò ïé âßäåò åßíáé óôç èÝóç ôïõò óôá êáëýììáôá. ÊñáôÞóôå ôçí êïíóüëá êáé ìå ôá äýï ÷Ýñéá êáé áíáêéíåßóôå ôçí óå äýï äéáöïñåôéêÝò êáôåõèýíóåéò ãéá íá åðáëçèåýóåôå üôé äåí õðÜñ÷ïõí ÷áëáñÜ õëéêÜ ìÝóá óôçí êïíóüëá. 3. ÐñáãìáôïðïéÞóôå åîùôåñéêÞ ïðôéêÞ åðéèåþñçóç ãéá ôõ÷üí ìç÷áíéêÞ æçìéÜ. Åðáëçèåýóôå üôé äåí õðÜñ÷ïõí ìç áðïäåêôÜ êïììÜôéá, ÷áñáãìáôéÝò, ãñáôóïõíéÝò, Þ óçìÜäéá óôï ðåñßâëçìá ôçò êïíóüëáò Þ óôï ðïäïóôÞñéï. Åðáëçèåýóôå üôé ôá êïõìðéÜ åßíáé óùóôÜ áóöáëéóìÝíá êáé äåí åßíáé ÷áëáñÜ. Óößîôå ïðïéïäÞðïôå ÷áëáñü êüìðï. Âåâáéùèåßôå üôé ïé áåñïêßíçôïé óõíäåôÞñåò åßíáé óå èÝóç ëåéôïõñãßáò, üôé äåí Ý÷ïõí êïëëÞóåé óôçí áíïéêôÞ èÝóç êáé üôé åßíáé óöéêôÜ óõíäåìÝíïé ìå ôçí êïíóüëá.
ÓõíäåôÞñáò ïðôéêÞò ßíáò.
Óôñüâéëïò: Óýíäåóìïò ãéá ôïí áãùãü áåñßïõ ôïõ ðñïùèçôÞ.
Åßóïäïò ÐåðéåóìÝíïõ Áåñßïõ: Óýíäåóìïò ãéá ôïí áãùãü ðáñï÷Þò áðü ôçí ðçãÞ ðåðéåóìÝíïõ áåñßïõ.
ÓõíäåôÞñåò ðïäïóôçñßïõ (ðåíôÜë).
ÓõíäåôÞñáò ãñáöéêïý êáôáãñáöÝá.
40
23278-007.qxd
07/02/2003
08:29
Page 12
4. ÅëÝãîôå ôá üñãáíá Ýíäåéîçò ôïõ åìðñüóèéïõ ìÝñïõò ôçò êïíóüëáò. Ìå ôçí êïíóüëá óõíäåìÝíç óôçí çëåêôñïäüôçóç êáé ôï ðåðéåóìÝíï áÝñéï, ðáôÞóôå ôï äéáêüðôç çëåêôñïäüôçóçò ãéá åöáñìïãÞ éó÷ýïò êáé åðáëçèåýóôå üôé: á) ÁíÜâåé ç ðñÜóéíç åíäåéêôéêÞ ëõ÷íßá (LED) Éó÷ýïò. â) Ç ïèüíç EVENT TIME [×ÑÏÍÏÓ ÓÕÌÂÁÍÔÏÓ] äåß÷íåé 00:00. ã) Ç ïèüíç PROCEDURE TIME [×ÑÏÍÏÓ ÄÉÁÄÉÊÁÓÉÁÓ] äåß÷íåé 00:00. ä) Ç ïèüíç RPM [ÓÁË] åßíáé êåíÞ. å) Ç ïèüíç STALL [ÁÊÉÍÇÔÏÐÏÉÇÓÇ] åßíáé êåíÞ. 5. ÅëÝãîôå ôç ëåéôïõñãßá ôïõ ïñãÜíïõ Ýíäåéîçò ðßåóçò óôñïâéëïêéíçôÞñá. ÓõíäÝóôå ôçí êïíóüëá óôçí çëåêôñïäüôçóç AC êáé ôï ðåðéåóìÝíï áÝñéï. Îåêéíþíôáò ìå ôï ÷åéñéóôÞñéï SPEED ADJUST [ÑÕÈÌÉÓÇ ÔÁ×ÕÔÇÔÁÓ] óå ðëÞñùò áñéóôåñüóôñïöç èÝóç, åðáëçèåýóôå üôé ç äåîéüóôñïöç ðåñéóôñïöÞ ôïõ ÷åéñéóôçñßïõ SPEED ADJUST [ÑÕÈÌÉÓÇ ÔÁ×ÕÔÇÔÁÓ] Ý÷åé óáí áðïôÝëåóìá ôçí áýîçóç ôçò ôéìÞò ôçò Ýíäåéîçò óôï üñãáíï TURBINE PRESSURE [ÐÉÅÓÇ ÓÔÑÏÂÉËÏÊÉÍÇÔÇÑÁ] ôçò êïíóüëáò. 6. ÅëÝãîôå ôç ëåéôïõñãßá ôçò ïèüíçò DYNAGLIDE. Ìå ôçí êïíóüëá óõíäåìÝíç óôçí çëåêôñïäüôçóç AC êáé ôïí ðåðéåóìÝíï áÝñá êáé ìå ôï ðïäïóôÞñéï Dynaglide™ óõíäåìÝíï, áíïßîôå ôç ìïíÜäá, ðáôÞóôå ôï êïõìðß Dynaglide óôï ðïäïóôÞñéï êáé åðáëçèåýóôå üôé áíÜâåé ç åíäåéêôéêÞ ëõ÷íßá DYNAGLIDE êáé ìåôÜ óâÞíåé. 7. ÅëÝãîôå ôç ëåéôïõñãßá ôçò ïèüíçò STALL [ÁÊÉÍÇÔÏÐÏÉÇÓÇ]. ×ùñßò íá Ý÷åôå óõíäÝóåé ôïí ðñïùèçôÞ (äçë. äåí Ý÷åé óõíäåèåß êáíÝíáò óõíäåôÞñáò ïðôéêÞò ßíáò), åíåñãïðïéÞóôå ôï ðïäïóôÞñéï êáé åëÝãîôå ãéá ôï åÜí áíÜâåé ç åíäåéêôéêÞ ëõ÷íßá áêéíçôïðïßçóçò. Åðáëçèåýóôå üôé ç ëõ÷íßá áêéíçôïðïßçóçò óâÞíåé üôáí áðåëåõèåñþóåôå ôï ðïäïóôÞñéï.
ÐáñÜñôçìá à - Ëåéôïõñãßá ôïõ ÓõóôÞìáôïò áðü Áãùãïýò ×áìçëÞò Ðßåóçò (Ïéêéáêïýò) Óçìåßùóç:
Áõôü ôï ðáñÜñôçìá ÄÅÍ éó÷ýåé ãéá åîïðëéóìü ðïõ ÷ñçóéìïðïéåßôáé óôç Ãåñìáíßá.
Ôï ðåñéóôñïöéêü óýóôçìá áãã åéïðëáóôéêÞò Rotablator™ åßíáé ó÷åäéáóìÝíï íá ëåéôïõñãåß áðü öéÜëåò ðåðéåóìÝíïõ áåñßïõ ìÝóù ñõèìéóôÞ öéÜëçò. ÐÜíôùò, åÜí õðÜñ÷åé äéáèÝóéìï ïéêéáêü óýóôçìá áÝñá Þ áæþôïõ, ôüôå ìðïñåßôå íá ôñïöïäïôÞóåôå áð' åõèåßáò ôçí êïíóüëá, åëá÷éóôïðïéþíôáò ôçí áíÜãêç ãéá öéÜëç êáé ñõèìéóôÞ öéÜëçò. Ïé áðáéôÞóåéò Ý÷ïõí ùò åîÞò: 1. Ôï áÝñéï õðü ðßåóç ðñÝðåé íá åßíáé ìüíï áÝñáò Þ Üæùôï. 2. Ôï áÝñéï ðñÝðåé íá åßíáé êáèáñü, îçñü êáé ÷ùñßò ëÜäéá. 3. Ç ðßåóç ôïõ áåñßïõ ðñÝðåé íá åßíáé ìåôáîý 620.5 kPa (90 psi) êáé 758.4 kPa (110 psi) óôçí åßóïäï ôçò êïíóüëáò åëÝã÷ïõ. 4. Ôï óýóôçìá ðñÝðåé íá åßíáé óå èÝóç ðáñï÷Þò áåñßïõ áðïôßìçóçò 140 ëßôñá/ ëåðôü (5 scfm) Þ ðåñéóóüôåñï. ÐáñÝ÷åôáé ìéá ðñïóáñìïãÞ ðñïóáñìïãÝá ìå ôçí êïíóüëá Rotablator. Ç ðñïóáñìïãÞ Ý÷åé Ýíá èçëõêü âýóìá ãñÞãïñçò óýíäåóçò óôï Ýíá Üêñï êáé óðåéñþóåéò óùëÞíá 0,6 cm (1/4“) óôï Üëëï Üêñï. Ôï Üêñï 0,6 cm 1/4 ÌÍÑÔ åßíáé ìéá ôõðéêÞ èçëõêÞ ðñïóáñìïãÞ óùëÞíá 0,6 cm (1/4“) êáé èá ôáéñéÜîåé ìå ôçí ðëçèþñá åîïðëéóìïý ÷åéñéóìïý áåñßùí Þ ìå óõíäåôÞñåò óôïõò ïéêéáêïýò áãùãïýò. Ôï Üêñï ãñÞãïñçò óýíäåóçò ôáéñéÜæåé áð' åõèåßáò ìå ôï óõíäåôÞñá óôï Üêñï ôïõ óùëÞíá ðáñï÷Þò, ï ïðïßïò êáíïíéêÜ èá ðñïóáñìïæüôáí óå Ýíá ñõèìéóôÞ.
Ðëçñïöïñßåò ÓõíôÞñçóçò ÁóöÜëåéá: Óôçí ðåñßðôùóç áóôï÷ßáò áóöÜëåéáò, êëåßóôå ôçí çëåêôñïäüôçóç êáé áðïóõíäÝóôå ôï êáëþäéï ñåýìáôïò áðü ôçí ðñßæá. Ìðïñåßôå åðßóçò íá áðïóõíäÝóåôå ôï êáëþäéï ñåýìáôïò áðü ôï ðßóù ìÝñïò ôçò êïíóüëáò ãéá âåëôßùóç ðñüóâáóçò óôéò áóöÜëåéåò. ×ñçóéìïðïéÞóôå Ýíá åñãáëåßï üðùò Ýíá êáôóáâßäé ãéá íá áöáéñÝóåôå ôçí áóöáëåéïèÞêç, ðéÝæïíôáò ôï áóöáëéóôéêü ðôåñýãéï. Äåßôå ôçí Åéêüíá 3 ðáñáêÜôù.
Õðïäï÷Þ Êáëùäßïõ Ôñïöïäüôçóçò
Ðôåñýãéï ÁóöÜëéóçò ÁóöáëåéïèÞêç
Åéêüíá 3 ÁíôéêáôÜóôáóç ÁóöÜëåéáò ÁíôéêáôáóôÞóôå êáé ôéò äýï áóöÜëåéåò ìå áóöÜëåéåò ôïõ ßäéïõ ôýðïõ êáé áðïôßìçóçò üðùò êáèïñßæåôáé óôï ðßóù ìÝñïò ôçò êïíóüëáò. ÅðáíåéóÜãåôå ôçí áóöáëåéïèÞêç ìÝ÷ñé íá áóöáëßóåé ôï áóöáëéóôéêü ðôåñýãéï óôç èÝóç ôïõ. ÅðáíáóõíäÝóôå ôï êáëþäéï çëåêôñïäüôçóçò êáé åðáíáöÝñåôå ôçí éó÷ý óôçí êïíóüëá. ÅÜí êáåß îáíÜ ç áóöÜëåéá, áðïóõíäÝóôå êÜèå ðçãÞ éó÷ýïò óôçí êïíóüëá êáé åðéêïéíùíÞóôå ìå ôïí Áíôéðñüóùðï ÅîõðçñÝôçóçò Ðåëáôþí. ÊÜèå Üëëç åñãáóßá óõíôÞñçóçò ðñÝðåé íá ðñáãìáôïðïéçèåß áðü ôï ðñïóùðéêü ôçò åôáéñßáò Boston Scientific Corporation. Ôõ÷üí åðéóêåõÞ åðß ôüðïõ, åêôüò áðü ôçí áíôéêáôÜóôáóç ôùí åîùôåñéêþí áóöáëåéþí ôçò êïíóüëáò, áêõñþíåé êÜèå åããýçóç êáé äåí ìðïñåß íá ðñáãìáôïðïéçèåß ÷ùñßò ñçôÞ åîïõóéïäüôçóç áðü ôï ÔìÞìá ÅîõðçñÝôçóçò Ðåëáôþí.
41
23278-007.qxd
07/02/2003
08:29
Page 9
42
23278-007.qxd
13/02/2003
12:50
Page 8
43
23278-007.qxd
07/02/2003
08:29
Page 5
44
23278-007.qxd
07/02/2003
08:29
Page 4
45
23278-007.qxd
07/02/2003
08:28
Page 1
One Boston Scientific Place, Natick, MA USA 01760. Customer Service 1-800-832-7822. EU Authorized Representative: Boston Scientific International 91, Boulevard National 92257 La Garenne Colombes Cedex France
10/2002 ©2002 Boston Scientific Corporation. All Rights Reserved. 23278-008