Carl Zeiss
QEVO Reprocessing Instructions
96 Pages
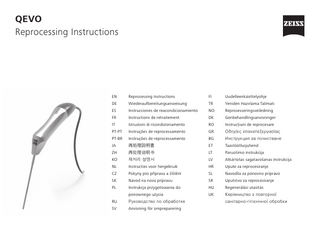
Preview
Page 1
QEVO Digital Exploration Tool Reprocessing Instructions Copyright © 2016, Carl Zeiss Meditec AG, Jena Trademarks QEVO is a trademark/are trademarks or registered trademark(s) of Carl Zeiss Meditec AG or other companies of the ZEISS Group in Germany and/or other countries. All other trademarks in this document are the property of the relevant proprietor. 1 Information about the Reprocessing Instructions 1.1 Scope of application The reprocessing instructions specified here apply to the following product: QEVO (REF# 7212). 1.2 Product name QEVO is a hand-held, digital exploration tool and is referred to as the “product” in these reprocessing instructions. 2 Responsibility and obligations of the operator Reprocessing personnel In many countries, the qualifications required by personnel responsible for the reprocessing of medical devices are regulated by law. In any event, the reprocessing of medical devices must always fall under the responsibility of qualified personnel who have the necessary knowledge and expertise. This knowledge and expertise can be acquired by completing further training in this field or as a result of completing a dedicated qualification with practical experience, supplemented by appropriate further training measures, where required. 3 Pre-cleaning NOTE Malfunction during operation! The product must not be used if it is damaged. –– To prevent damage to the product during reprocessing, use the reprocessing tray InstruSafe® supplied with the product. Requirements –– Enzymatic cleaning solution, e.g. Cidezyme / Enzol (ASP®), which has been prepared according to the manufacturer’s instructions for use. –– Two dry, lint-free cloths –– InstruSafe® reprocessing tray (IN-1000-SY, Summit Medical Inc.) –– Sterile gloves Procedure 1. Pre-clean the product immediately after use, as described below. 2. Wipe the product, cable and plug with the damp, but not dripping, cloth until visible surgical residues are removed as fully as possible, and for at least one minute. 3. Wipe the product, cable and plug with a dry, lint-free cloth. 4. Fill the InstruSafe® reprocessing tray:
4 Reprocessing 4.1 General WARNING! Contamination with pathogenic germs! If the product is reprocessed using unsuitable methods or cleaning agents, pathogenic microorganisms can settle on the product. –– Reprocess the product only according to the validated methods for this product. –– Only allow briefed and trained personnel to reprocess the product. –– Only use compatible cleaning agents when reprocessing the product. –– Dispose of the product as soon as there is any suspicion of prion contamination. Observe the respective prevailing national regulations for the disposal. The following disinfection steps within this instruction are not applicable for the treatment in the US. Specific instructions for the US are mentioned in chapter 4.3 and 4.5.
Procedure –– New products and products that have undergone maintenance and have been returned from ZEISS Service must be completely reprocessed before use. –– Use cleaning and disinfection machines that meet the requirements of ISO 15883-1. –– Service and inspect these cleaning and disinfection machines regularly. –– Fill the cleaning and disinfection machines so that all the contents are fully rinsed through and cleaned. There must be no “rinsing blind spots”. –– Do not clean the product in an ultrasonic bath. –– When pre-cleaning, do not use fixing temperatures in excess of 45 °C. –– Only use cleaning and disinfecting agents and process chemicals that are approved for the product. –– Follow all the chemical manufacturer’s application specifications regarding temperature, concentration, and contact time. –– Do not use process chemicals that can cause stress cracking or brittleness of plastic materials. –– When pre-cleaning, do not use fixing detergents or disinfectants (containing: aldehyde or alcohol). –– Avoid contact of the product with chloride-based solutions, e.g. contained in surgical residues, tinctures, medicinal products, saline solution and cleaning/disinfecting agents. Should the product nevertheless come into contact with chloride-based solutions, rinse the product thoroughly with deionized water and dry it fully. –– Adhere to national statutory regulations, national and international standards and directives, and the infection control practices that are in place at your institution for reprocessing. –– Note that the optimum and most reliable reprocessing results are achieved using automated cleaning and disinfection with subsequent steam sterilization using the fractionated vacuum procedure. –– Note that the alternating use of different reprocessing methods can cause premature aging of the product. 4.2 Manual Cleaning and Disinfection (not for USA)
Work Step
Cleaning
Temperature (°C/°F)
20-25 / 68-77
Time (min)
30
Water Quality
Drinking water
Cleaning Solution
Alkaline cleaning solution e.g. min. 0.5 % “neodisher® MediClean forte” (in accordance with manufacturer’s specifications), pH > 10
Stage II Work Step
Intermediate rinse
Temperature (°C/°F)
Room temperature (cold)
Time (min)
3x1
Water Quality
Drinking water
Cleaning Solution
–
Work Step
Disinfection
Temperature (°C/°F)
20-25 / 68-77
Time (min)
12
Water Quality
–
Cleaning Solution
Disinfectant solution (undiluted), e.g. “Cidex OPA” (ASP)
Stage IV
The reprocessing procedure for the product described in this document consists of the following steps: –– Pre-cleaning immediately after use –– Manual cleaning and disinfection or automated cleaning and disinfection –– Sterilization The specified procedures for manual cleaning and disinfection, automated cleaning and thermal disinfection, and steam sterilization have been validated for effectiveness. It is the operator’s responsibility to introduce, document, implement, and maintain a validated reprocessing procedure.
Stage I
a. Place the handpiece with the shaft first onto the instrument holder. b. Gently press the shaft and handpiece into the pre-formed instrument holder so the product cannot slip out of place. c. Wind the cable around the cable guides four times, making sure that the cable is not pulled too tight. d. Place the plug onto the corresponding instrument holder. e. Gently press the plug into the pre-formed instrument holder so the plug cannot slip out of place. f. Place the lid on the reprocessing tray and close it tight. 5. Send the product for reprocessing, making sure that it is reprocessed within six hours.
Stage III
Work Step
Final rinse
Temperature (°C/°F)
Room temperature (cold)
Time (min)
3x2
Water Quality
DI water*
Cleaning Solution
–
Stage V
*
Work Step
Drying
Temperature (°C/°F)
–
Time (min)
–
Water Quality
–
Cleaning Solution
–
DI water = Deionized water (demineralized, low bacteria, max. 10 bacteria/ml, as well as low endotoxin contaminated, max. 0.25 endotoxin units/ml)
Validated cleaning and disinfecting agents: –– Manual cleaning: “neodisher® Mediclean forte (Chem. Fabrik Dr. Weigert GmbH & Co. KG) –– Manual disinfection: “Cidex OPA” (Johnson & Johnson) A material compatibility approval also exists for the cleaning agent “Cidezyme/Enzol” (Johnson & Johnson). NOTE Damage to the product due to incorrect handling or operation! The product must not be used if it is damaged. –– Handle the product with care. –– Do not knock or bend the shaft of the product. –– Put down the product with care. NOTE Damage to the product due to incorrect handling or operation! The product must not be used if it is damaged. –– Do not use metal brushes, metal objects, or abrasive cleaners for manual cleaning to avoid scratching the surfaces. –– To remove soiling on optical surfaces, use pads impregnated with cleaning solution only. –– Do not use excessive doses of basic cleaners.
Requirements –– Cleaning agent “neodisher® Mediclean forte (Chem. Fabrik Dr. Weigert GmbH & Co. KG) or “Cidezyme/Enzol” (Johnson & Johnson) –– Disinfectant “Cidex OPA” (Johnson & Johnson) –– Compressed air connection with medical-quality filtered compressed air (max. 0.5 bar) –– Magnifying glass –– Product is pre-cleaned Procedure 1. Read and observe the cleaning and disinfecting agent manufacturer’s user information and follow the specifications regarding concentration, temperature, usage time, water quantities, and contact time. 2. Fully immerse the product in an alkaline cleaning solution for 30 minutes. Make sure that the cleaning solution reaches all accessible surfaces. 3. While the device soaks in the solution, use a soft wipe or suitable brush to remove all visible residue from its exterior surfaces. 4. Brush all surfaces of products with hidden crevices or complex geometry for at least one (1) minute or until no more residues can be removed.
5. Fully rinse all accessible surfaces three times for at least one (1) minute each. Use fresh water for each rinse. 6. Allow water to drip off for a sufficient length of time. 7. Fully immerse the product in the disinfectant solution for 12 minutes. Make sure that the disinfectant reaches all accessible surfaces. 8. Remove all adherent air bubbles from the product’s surfaces. 9. Fully rinse the device three times for at least two (2) minutes each time. Use fresh water for each rinse (DI water). 10. Allow water to drip off for a sufficient length of time. 11. Dry the device using a soft, lint-free wipe. 12. Use medical-quality filtered compressed air (pmax = 0.5 bar) to dry the areas you cannot reach with the wipe. 13. After drying, visually inspect the product in a well-lit area and make sure it is completely dry, undamaged and free of visible residues. Use a magnifying glass for the visual inspection. 14. Repeat the cleaning and disinfection process if necessary. 15. Reject the product if it has any sharp edges or corners, bulges, or rough or scratched surfaces that might cause injury to the patient. 16. Place the product in the InstruSafe® reprocessing tray. 17. Sterilize the product. 4.3 Manual Cleaning (only valid for USA) Stage I Work Step
Cleaning
Temperature (°C/°F)
in accordance with manufacturers specifications
Time (min)
2–5
Water Quality
Drinking water
Cleaning Solution
Enzymatic cleaning solution e.g. Enzol® (ASP, in accordance with manufacturer’s specifications)
Stage II Work Step
Intermediate rinse
Temperature (°C/°F)
Room temperature (cold)
Time (min)
2x1
Water Quality
Drinking water
Cleaning Solution
–
Stage III
Work Step
Rinse I
Temperature (°C/°F)
according to the CDM standard cycle*
Time (min)
1
Damage to the product due to incorrect handling or operation! The product must not be used if it is damaged. –– Do not use metal brushes, metal objects, or abrasive cleaners for manual cleaning to avoid scratching the surfaces. –– To remove soiling on optical surfaces, use pads impregnated with cleaning solution only. –– Do not use excessive doses of basic cleaners.
Water Quality
Drinking water
Cleaning Solution
–
NOTE
Requirements –– Cleaning agent “Enzol®” (ASP) –– Compressed air connection with medical-quality filtered compressed air (max. 0.5 bar) –– Magnifying glass –– Product is pre-cleaned Procedure 1. Read and observe the cleaning agent manufacturer’s user information and follow the specifications regarding concentration, temperature, usage time, water quantities, and contact time. 2. Fully immerse the product in enzymatic cleaning solution 2 to 5 minutes. Make sure that the cleaning solution reaches all accessible surfaces. 3. While the device soaks in the solution, use a soft wipe or suitable brush to remove all visible residue from its exterior surfaces. 4. Brush all surfaces of products with hidden crevices or complex geometry for at least one (1) minute or until no more residues can be removed. 5. Fully rinse all accessible surfaces three times for at least one (1) minute each. Use fresh water for each rinse. 6. Fully rinse all accessible surfaces three times for at least one (1) minute each. Use DI-Water for each rinse. 7. Allow water to drip off for a sufficient length of time. 8. Dry the device using a soft, lint-free wipe. 9. Use medical-quality filtered compressed air (pmax = 0.5 bar) to dry the areas you cannot reach with the wipe. 10. After drying, visually inspect the product in a well-lit area and make sure it is completely dry, undamaged and free of visible residues. Use a magnifying glass for the visual inspection. 11. Repeat the cleaning and disinfection process if necessary. 12. Reject the product if it has any sharp edges or corners, bulges, or rough or scratched surfaces that might cause injury to the patient. 13. Place the product in the InstruSafe® reprocessing tray. 14. Sterilize the product.
Final rinse
4.4 Automated cleaning and disinfecting (not for USA)
Temperature (°C/°F)
Room temperature (cold)
Stage I
Time (min)
1
Work Step
Pre-rinsing
Water Quality
DI water*
Temperature (°C/°F)
< 25/77
Cleaning Solution
–
Time (min)
2
Water Quality
Drinking water
Work Step
Drying
Cleaning Solution
–
Temperature (°C/°F)
–
Stage II
Time (min)
–
Work Step
Cleaning
Water Quality
–
Temperature (°C/°F)
55/131
Cleaning Solution
–
Time (min)
10
Water Quality
Drinking water
Cleaning Solution
Alkaline cleaner, e.g. 1 % neodisher® SeptoClean (in accordance with manufacturer’s specifications), pH > 10
DI water = Deionized water (demineralized, low bacteria, max. 10 bacteria/ml, as well as low endotoxin contaminated, max. 0.25 endotoxin units/ml)
Validated cleaning agents: –– Manual cleaning: “Enzol®” (ASP)
Stage III
Damage to the product due to incorrect handling or operation! The product must not be used if it is damaged. –– Handle the product with care. –– Do not knock or bend the shaft of the product. –– Put down the product with care. NOTE
Work Step
Stage IV
*
A material compatibility approval also exists for the cleaning agent „neodisher® MediClean forte” (Chem. Fabrik Dr. Weigert GmbH & Co. KG).
Stage IV Work Step
Rinse II
Temperature (°C/°F)
according to the CDM standard cycle*
Time (min)
1
Water Quality
DI water**
Cleaning Solution
–
Stage V Work Step
Thermal disinfection
Temperature (°C/°F)
> 90/194
Time (min)
5
Water Quality
DI water**
Cleaning Solution
A0-Wert > 3000
Stage VI Work Step
Drying
Temperature (°C/°F)
according to the CDM standard cycle*
Time (min)
according to the CDM standard cycle*
Water Quality
–
Cleaning Solution
–
* CDM = cleaning and disinfection machine ** DI water = Deionized water (demineralized, low bacteria, max. 10 bacteria/ml, as well as low endotoxin contaminated, max. 0.25 endotoxin units/ml) Automated reprocessing can cause color-anodized or plastic components (e.g. plug, cable) to fade. This does not affect the performance of the product. Validated cleaning and disinfecting agents: The automated cleaning process was validated with “neodisher® SeptoClean” (Chem. Fabrik Dr. Weigert GmbH & Co. KG) For the cleaning agent “neodisher® Mediclean forte (Chem. Fabrik Dr. Weigert GmbH & Co. KG) there is also a material compatibility approval. Requirements –– Cleaning agent “neodisher® SeptoClean” (Chem. Fabrik Dr. Weigert GmbH & Co. KG) or “neodisher® MediClean forte” (Chem. Fabrik Dr. Weigert GmbH & Co. KG) –– Cleaning/disinfection machine with validated effectiveness meets the requirements of ISO 15883-1 and the applicable country-specific versions –– Deionized water for thermal disinfection –– Heat-resistant safety gloves –– Magnifying glass –– Product is pre-cleaned –– Product is in closed InstruSafe® reprocessing tray
Procedure 1. Read and observe the cleaning agent manufacturer’s user information and follow the specifications regarding concentration, temperature, usage time, water quantities, and contact time. 2. Load the cleaning and disinfection machine according to the validated loading plan, and observe the manufacturer’s specifications and instructions for use for the cleaning/disinfection machine. 3. When loading, take care to avoid creating rinsing blind spots. 4. Start the cleaning/disinfection cycle in accordance with the manufacturer’s instructions and instructions for use for the cleaning/disinfection machine. 5. CAUTION! Risk of burns from a hot reprocessing tray! Wear safety gloves when removing the reprocessing tray. 6. Remove the InstruSafe® reprocessing tray from the cleaning/disinfection machine at the end of the cleaning cycle. 7. Open the InstruSafe® reprocessing tray. 8. After drying, visually inspect the product in a well-lit area and make sure it is completely dry, undamaged and free of visible residues. Use a magnifying glass for the visual inspection. 9. Repeat the cleaning and disinfection process if necessary. 10. Reject the product if it has any sharp edges or corners, bulges, or rough or scratched surfaces that might cause injury to the patient. 11. Place the product in the InstruSafe® reprocessing tray. 12. Sterilize the product. 4.5 Automated cleaning (only valid for USA) Stage I Work Step
Pre-rinsing
Temperature (°C/°F)
< 25/77
Time (min)
2
Water Quality
Drinking water
Cleaning Solution
–
Stage II Work Step
Cleaning
Temperature (°C/°F)
55/131
Time (min)
10
Water Quality
Drinking water
Cleaning Solution
Alkaline cleaner, e.g. 0.5 % neodisher® MediClean forte (in accordance with manufacturer's specifications), pH > 10
Stage III Work Step
Rinse I
Temperature (°C/°F)
according to the CDM standard cycle*
Time (min)
1
Water Quality
Drinking water
Cleaning Solution
–
Stage IV Work Step
Rinse II
Temperature (°C/°F)
according to the CDM standard cycle*
Time (min)
1
Water Quality
DI water**
Cleaning Solution
–
Stage V Work Step
Final rinsing
Temperature (°C/°F)
> 90/194
Holding time
18 minutes (effective sterilization time)
Time (min)
5
Holding time for US
4 minutes (effective sterilization time)
Water Quality
DI water**
Pulse
4
Cleaning Solution
A0 value > 3000
Drying time
At least 30 minutes
Stage VI Work Step
Drying
Temperature (°C/°F)
according to the CDM standard cycle*
Time (min)
according to the CDM standard cycle*
Water Quality
–
Cleaning Solution
–
* CDM = cleaning and disinfection machine ** DI water = Deionized water (demineralized, low bacteria, max. 10 bacteria/ml, as well as low endotoxin contaminated, max. 0.25 endotoxin units/ml) Automated reprocessing can cause color-anodized or plastic components (e.g. plug, cable) to fade. This does not affect the performance of the product. Validated cleaning and disinfecting agents: The automated cleaning process was validated with “neodisher® MediClean forte” (Chem. Fabrik Dr. Weigert GmbH & Co. KG) For the cleaning agent “neodisher® SeptoClean” (Chem. Fabrik Dr. Weigert GmbH & Co. KG) there is also a material compatibility approval. Requirements –– Cleaning agent “neodisher® SeptoClean” (Chem. Fabrik Dr. Weigert GmbH & Co. KG) or “neodisher® MediClean forte” (Chem. Fabrik Dr. Weigert GmbH & Co. KG) –– Cleaning/disinfection machine with validated effectiveness meets the requirements of ISO 15883-1 and the applicable country-specific versions –– Deionized water for thermal disinfection –– Heat-resistant safety gloves –– Magnifying glass –– Product is pre-cleaned –– Product is in closed InstruSafe® reprocessing tray Procedure 1. Read and observe the cleaning agent manufacturer’s user information and follow the specifications regarding concentration, temperature, usage time, water quantities, and contact time. 2. Load the cleaning and disinfection machine according to the validated loading plan, and observe the manufacturer’s specifications and instructions for use for the cleaning/disinfection machine. 3. When loading, take care to avoid creating rinsing blind spots. 4. Start the cleaning/disinfection cycle in accordance with the manufacturer’s instructions and instructions for use for the cleaning/disinfection machine. 5. CAUTION! Risk of burns from a hot reprocessing tray! Wear safety gloves when removing the reprocessing tray. 6. Remove the InstruSafe® reprocessing tray from the cleaning/disinfection machine at the end of the cleaning cycle. 7. Open the InstruSafe® reprocessing tray. 8. After drying, visually inspect the product in a well-lit area and make sure it is completely dry, undamaged and free of visible residues. Use a magnifying glass for the visual inspection. 9. Repeat the cleaning process if necessary. 10. Reject the product if it has any sharp edges or corners, bulges, or rough or scratched surfaces that might cause injury to the patient. 11. Place the product in the InstruSafe® reprocessing tray. 12. Sterilize the product. 4.6 Sterilization Steam sterilization parameters The user is responsible for ensuring that the sterilizer used fulfills the following sterilization parameters: Work Step
Fractionated vacuum process
Temperature
134 °C (273 °F)
Temperature for US
132 °C (270 °F)
Requirements –– Deionized water, according to the requirements of EN 285 –– Heat-resistant safety gloves –– Manual or automated leaning and disinfection of the product is complete –– Product is in closed InstruSafe® reprocessing tray Procedure 1. Validated sterile barrier systems: Pack the closed InstruSafe® reprocessing tray either with two individual layers of polypropylene wrap or place the reprocessing tray in an Aesculap sterile container system (JK444). Note for US: Use only FDA cleared wrap. 2. CAUTION! Risk of burns when loading the sterilizer! Wear safety gloves when loading the sterilizer. 3. Load the sterilizer according to the validated loading plan, and observe the manufacturer’s specifications and instructions for use for the sterilizer. 4. Start the sterilization cycle in accordance with the manufacturer’s instructions and instruction for use for the sterilizer. Use validated parameters for steam sterilization specified above. 5. CAUTION! Risk of burns from a hot reprocessing tray! Wear safety gloves when removing the reprocessing tray. 6. Remove the InstruSafe® reprocessing tray containing the product from the sterilizer. 7. Ensure that the product remains sterile after reprocessing. QEVO is RoHS compliant in accordance with Directive 2011/65/EU. QEVO complies with the Medical Device Directive 93/42/EEC.
0297
Carl Zeiss Meditec AG Goeschwitzer Strasse 51–52 07745 Jena Germany Fax: +49 (0) 7364-20 4823 E-Mail: [email protected] www.zeiss.com/med
QEVO Digitales Sondierungsinstrument Wiederaufbereitungsanweisung Copyright © 2016, Carl Zeiss Meditec AG, Jena Marken QEVO ist eine Marke oder eingetragene Marke der Carl Zeiss Meditec AG oder anderer Unternehmen der ZEISS Gruppe in Deutschland und anderen Ländern. Alle anderen Marken in diesem Dokument sind Eigentum des betreffenden Inhabers. 1 Hinweise zur Wiederaufbereitungsanweisung 1.1 Geltungsbereich Die hier aufgeführte Wiederaufbereitungsanweisung gilt für folgendes Produkt: QEVO (REF# 7212). 1.2 Produktname QEVO ist ein handgehaltenes, digitales Sondierungsinstrument und wird in dieser Wiederaufbereitungsanweisung „Produkt“ genannt. 2 Verantwortung und Pflichten des Betreibers Aufbereitungspersonal Die Qualifikationsanforderungen an Personal, das mit der Aufbereitung von Medizinprodukten betraut