Corin
4-in-1 cutting block drill (Hudson)
PS3003-01 Instrument Care, Cleaning and Sterilisation Instructions
4 Pages
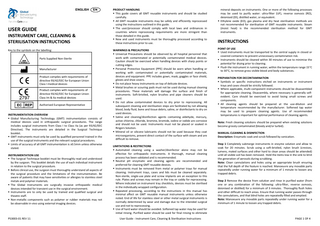
Preview
Page 1
ENGLISH
EN
USER GUIDE
INSTRUMENT CARE, CLEANING & STERILISATION INSTRUCTIONS Key to the symbols on the labelling: Parts Supplied Non-Sterile Manufacturer Product complies with requirements of directive 93/42/EEC for European Union Class I medical devices Product complies with requirements of directive 93/42/EEC for European Union Class Im & IIa medical devices Authorised European Representative INSTRUMENTATION OVERVIEW Global Manufacturing Technology (GMT) instrumentation consists of medical devices used in orthopaedic surgical procedures. The range includes surgical instruments from Class I to Class IIa (as per 93/42/EEC Directive). The instruments are detailed in the Surgical Technique booklet. GMT instruments must only be used by qualified personnel trained in the use of the surgical instruments and the relevant surgical procedures. Limits of accuracy of all GMT instrumentation is ±0.5mm unless otherwise stated. INSTRUMENTATION USE The Surgical Technique booklet must be thoroughly read and understood by the surgeon. This booklet details the use of each individual instrument in relation to the surgical procedure. Before clinical use, the surgeon must thoroughly understand all aspects of the surgical procedure and the limitations of the instrumentation. Be aware of patients that may have sensitivities or allergies to stainless steel metals and polymer materials. The Global Instruments are surgically invasive orthopaedic medical devices intended for transient use in the surgical environment. Instruments are to only be used by trained and qualified surgical and theatre staff. Non-metallic components such as polymer or rubber materials may not be observable in-vivo using external imaging devices.
PS3003-01 REV 11
PRODUCT HANDLING This guide covers all GMT reusable instruments and should be studied carefully. All GMT reusable instruments may be safely and efficiently reprocessed using the instructions outlined in this guide. The user/processor should comply with local laws and ordinances in countries where reprocessing requirements are more stringent than those detailed in this guide. New and used instruments must be thoroughly processed according to these instructions prior to use. WARNINGS & PRECAUTIONS Universal Precautions should be observed by all hospital personnel that work with contaminated or potentially contaminated medical devices. Caution should be exercised when handling devices with sharp points or cutting edges. Personal Protective Equipment (PPE) should be worn when handling or working with contaminated or potentially contaminated materials, devices and equipment. PPE includes gown, mask, goggles or face shield, gloves and shoe covers. Do not place heavy instruments on top of delicate devices. Metal brushes or scouring pads must not be used during manual cleaning procedures. These materials will damage the surface and finish of instruments. Soft-bristled, nylon brushes and pipe cleaners should be used. Do not allow contaminated devices to dry prior to reprocessing. All subsequent cleaning and sterilisation steps are facilitated by not allowing blood, body fluid, bone and tissue debris, saline, or disinfectants to dry on used devices. Saline and cleaning/disinfection agents containing aldehyde, mercury, active chlorine, chloride, bromine, bromide, iodine or iodide are corrosive and should not be used. Instruments must not be placed or soaked in Ringers Solution. Mineral oil or silicone lubricants should not be used because they coat microorganisms, prevent direct contact of the surface with steam and are difficult to remove. LIMITATIONS & RESTRICTIONS Automated cleaning using a washer/disinfector alone may not be effective for orthopaedic instruments. A thorough, manual cleaning process has been validated and is recommended. Neutral pH enzymatic and cleaning agents are recommended and preferred for cleaning GMT reusable devices. Instruments must be removed from metal or polymer trays for manual cleaning. Instrument trays, cases and lids must be cleaned separately. Non-sterile, single-use plate and screw implants are an exception to this rule. Plates and screws may remain in the tray or caddy for reprocessing. Where indicated on instrument tray checklists, devices must be sterilised in the individually wrapped configuration. Repeated processing, according to the instructions in this manual has minimal affect on GMT reusable manual instruments unless otherwise noted. End of life for stainless steel or other metal surgical instruments is normally determined by wear and damage due to the intended surgical use and not to reprocessing. Use of hard water should be avoided. Softened tap water may be used for initial rinsing. Purified water should be used for final rinsing to eliminate User Guide - Instrument Care, Cleaning & Sterilisation Instructions
mineral deposits on instruments. One or more of the following processes may be used to purify water: ultra-filter (UF), reverse osmosis (RO), deionised (DI), distilled water, or equivalent. Ethylene oxide (EO), gas plasma and dry heat sterilisation methods are not recommended for sterilisation of GMT reusable instruments. Steam (moist heat) is the recommended sterilisation method for GMT instruments.
INSTRUCTIONS POINT OF USE Used instruments must be transported to the central supply in closed or covered containers to prevent unnecessary contamination risk. Instruments should be cleaned within 30 minutes of use to minimise the potential for drying prior to cleaning. Flush the instrument in running water, within the temperature range 15°C to 30°C, to remove gross visible blood and body substances. PREPARATION FOR DECONTAMINATION Symbols or specific instructions etched on instruments or instrument trays and cases should be strictly followed. Where applicable, multi-component instruments should be disassembled for appropriate cleaning. Disassembly, where necessary is generally selfevident. Care should be exercised to avoid losing small screws and components. All cleaning agents should be prepared at the use-dilution and temperature recommended by the manufacturer. Softened tap water may be used to prepare cleaning agents. Use of recommended temperatures is important for optimal performance of cleaning agents. Note: Fresh cleaning solutions should be prepared when existing solutions become grossly contaminated (bloody and/or turbid). MANUAL CLEANING & DISINFECTION Description: Enzymatic soak and scrub followed by sonication. Step 1 Completely submerge instruments in enzyme solution and allow to soak for 20 minutes. Scrub using a soft-bristled, nylon brush (crevices, lumens, mated surfaces and other hard to clean areas should be attended) until all visible soil has been removed. Hold the items low in the sink to limit the generation of aerosols during scrubbing. Note: Clean cannulations and holes using an appropriate brush ensuring that the full depth of the feature is reached. Manoeuvre any movable parts repeatedly under running water for a minimum of 1 minute to loosen any trapped debris. Step 2 Remove the device from solution and rinse in purified water (from one or any combination of the following: ultra-filter, reverse osmosis, deionised or distilled) for a minimum of 3 minutes. Thoroughly flush holes and other difficult to reach areas. Ensure that running water passes through the cannulations, and that blind holes are repeatedly filled and emptied. Note: Manoeuvre any movable parts repeatedly under running water for a minimum of 1 minute to loosen any trapped debris.
PAGE 1 OF 4
Step 3 Pour the prepared neutral pH cleaning solution into a sonication unit and completely submerge the device in the solution and sonicate for 10 minutes at 40-50 kHz. Step 4 Rinse instrument in purified water for at least 3 minutes or until there is no sign of blood or soil on the device or in the rinse stream. Thoroughly and aggressively flush lumens, holes and other difficult to reach areas. Step 5 Repeat the sonication and rinse steps above. Step 6 Remove excess moisture from the instrument with a clean, absorbent and non-shedding wipe. Note: If stainless steel instruments are stained or corroded, an acidic, anticorrosion agent in an ultrasonic cleaner may be sufficient to remove surface deposits. Care must be taken to thoroughly rinse acid from devices. Acidic, anti-corrosion agents should only be used on an as needed basis.
sterilisation parameters that have been validated by GMT to provide a 10-6 sterility assurance level (SAL). The hospital is responsible for in-house procedures for the reassembly, inspection, and packaging of the instruments after they are thoroughly cleaned. Instruments must be disassembled and packaged in a manner that will ensure steam sterilant penetration and adequate drying. Provisions for protection of any sharp or potentially dangerous areas of the instruments should also be recommended by the hospital. Moist heat/steam sterilisation is the recommended and validated method for GMT orthopaedic instrument sets. The sterilising unit manufacturer’s recommendations should always be followed. When sterilising multiple instrument sets in one sterilisation cycle, ensure that the manufacturer’s maximum load is not exceeded. Instrument sets must be properly prepared and packaged in trays that will allow steam to penetrate and make direct contract with all surfaces. Ethylene oxide or gas plasma sterilisation methods should not be used. Gravity displacement sterilisation cycles are not recommended because cycle times are too long to be practical.
MAINTENANCE, INSPECTION & TESTING Carefully inspect each device to ensure that all visible contamination has been removed. If contamination is noted, repeat the cleaning and disinfection process. Check the action of moving parts (e.g. hinges, box-locks, connectors, sliding parts, etc.) to ensure smooth operation throughout the intended range of motion. Check instruments with long slender features (particularly rotating instruments) for distortion. Where instruments form part of a larger assembly, check that devices assemble readily with mating components. Hinged, rotating, or articulating instruments should be lubricated with a water soluble product (e.g. Instrument Milk or equivalent lubricant) intended for surgical instruments that must be sterilised. Some waterbased instrument lubricants contain bacteriostatic agents which are beneficial. Manufacturer’s expiration dates should be adhered to for both stock and use-dilution concentrations.
Table 1: Recommended Steam Sterilisation Parameters
PACKAGING & HANDLING Trays shall be wrapped in standard medical grade, steam sterilisation wrap using the AAMI double wrap method or equivalent. The user must ensure that the instrument tray is not tipped or the contents shifted once the devices are arranged in the tray. Where specialised instruments are provided by GMT to meet surgeon preferences they may not be provided in a tray. The hospital shall ensure that such Instrument sets are properly prepared and packaged in trays that will allow steam to penetrate and make direct contract with all surfaces. The instruments must not be stacked or placed in close contact and must be disassembled where possible prior to packaging.
STORAGE Sterile, packaged instruments should be stored in a designated, limited access area that is well ventilated and provides protection from dust, moisture, insects, vermin, and temperature/humidity extremes.
Note: The customised trays supplied by GMT contain areas designated for specific instruments. Hospital staff must ensure that they shall contain only those specifically intended for these areas. STERILISATION Disinfection is only acceptable as a precursor to full sterilisation for reusable surgical instruments. Refer to Table 1 for recommended minimum PS3003-01 REV 11
Cycle Type Prevacuum1 (Australia) Prevacuum4 (USA) Prevacuum5 Prevacuum5
Temperature 134°C 273 F 132°C 270 F 135°C 134°C
Pressure 44.3 Pa 443 mbar N/A
Exposure Time 4 minutes
Dry Time 30 minutes
4 minutes
30 minutes
N/A N/A
3 minutes 18 minutes
60 minutes 30 minutes
reprocessing facility have been adequately trained in order to achieve the desired result. Equipment and processes should be validated and routinely monitored. Any deviation by the processor from these instructions should be properly evaluated for effectiveness to avoid potential adverse consequences. This User Guide has been developed in accordance with ISO 17664. IMPORTANT STATEMENTS GMT validated reprocessing instructions are not applicable to GMT instrument trays that include devices that are not manufactured and/or distributed by GMT or which are not packed in accordance with GMT specifications. It is strictly prohibited to carry out any modification whatsoever on a GMT instrument. Only GMT has the competence to carry out such work. If this recommendation is not followed, GMT disclaims any liability for any subsequent consequences.
1. Local or national specifications may be followed where steam sterilisation requirements are stricter or more conservative than those listed in this table. However it is then the responsibility of the user to validate the specification. 2. Steam sterilisation cycles with longer times than those listed are also acceptable. 3. Drying times vary according to load size and should be increased for larger loads. 4. Parameters for the Unites States of America in accordance with ANSI/AAMI ST79. 5. Sterilisation specifications for individually wrapped devices, as validated and recommended by device manufacturer. Refer to instrument tray checklists for devices which are recommended to be sterilised individually.
Note: The Steriliser Manufacturer’s instructions for operation and load configuration should be followed explicitly.
ADDITIONAL INFORMATION Orthopaedic surgical instruments generally have a long service life; however, mishandling or inadequate protection can quickly diminish their life expectancy. Instruments which no longer perform properly because of long use, mishandling, or improper care should be returned to GMT to be discarded. Notify your GMT representative of any instrument problems. Loan sets must undergo all steps of decontamination, cleaning, disinfection, inspection, and terminal sterilisation before being returned to GMT. Documentation of decontamination must be provided with instruments being returned to GMT. The instructions provided in this User Guide have been validated by GMT as being capable of preparing orthopaedic devices for use. It is the responsibility of the Hospital to ensure that reprocessing is performed using the appropriate equipment and materials, and that personnel in the User Guide - Instrument Care, Cleaning & Sterilisation Instructions
Corin France SAS 157 Rue Lavoisier 38330 Montbonnot Saint-Martin France
Global Manufacturing Technology Pty Limited 17 Bridge Street Pymble NSW 2073 Australia
Made in Australia Technical alterations reserved
PAGE 2 OF 4