Instruction for Use
32 Pages
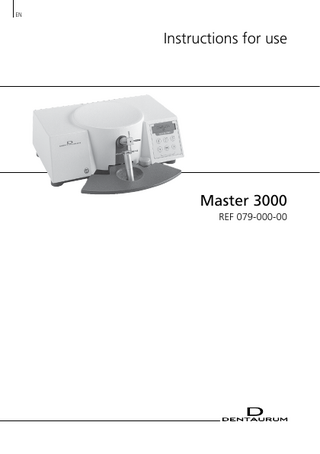
Preview
Page 1
EN
Instructions for use
Master 3000 REF 079-000-00
Features and Controls
# %
+ & *
) $ "
!
! Handrest with electrode opening mechanism " Lower click-stop electrode holder # Upper click-stop electrode holder $ Manual button % LCD display + Pad for selecting “welding” mode & Pad for selecting “soldering” mode ' Pad for selecting “continuous soldering” mode ' Pad for reducing welding or soldering power ) Pad for increasing welding or soldering power ( Pad for triggering printer function
2
'
(
1
,
0 .
-
/
- Outlet for hand electrodes / Outlet for hand electrodes 0 Combination outlet for power supply, power plug and fuse holder , Outlet for foot switch . Outlet for printer (RS-232 interface) . Housing with tray
3
Contents 1. Manufacturer ... 5 2. Safety information ... 5 2.1 Intended use ... 5 2.2 Danger symbols and markings ... 5 3. General notes and disposal ... 6 4. Description and usage ... 6 4.1 Application... 6 5. Technical data...7g 6. Components supplied ... 7 7. Unpacking and start-up procedure ... 7 7.1 Setting language for LCD display ... 7 8. Operating instructions ... 8 8.1 Spot welding ... 8 8.1.1 Spot welding with “click-stop“ electrodes ... 10 8.1.2 Spot welding with hand electrodes (optional accessory) ... 11 8.2 Soldering... 12 8.2.1 Soldering with ”click-stop“ electrodes ... 13 8.2.2 Soldering with hand electrodes (optional accessory) ... 14 8.2.3 Continuous soldering... 14 8.3 Heat treatment ... 15 8.3.1 Annealing of wires... 15 8.3.2 Tempering of wires ... 15 8.3.3 Stress relieving of wires ... 16 8.3.4 Procedure for annealing, tempering and stress relieving ... 16 9. Printer function/report printing ... 17 9.1 Connecting report printer... 17 9.2 Function: Printing in ”welding“ mode ... 17 9.3 Function: Printing in ”soldering” mode ... 18 10. Power-saving mode... 18 11. Troubleshooting ... 19 12. Dentaurum Customer Service - Equipment ... 20 13. Care and maintenance ... 20 14. Spare parts for “click-stop“ holders ... 20 15. Optional accessories ... 21 15.1 Spare parts for hand electrodes ... 21 15.2 Installation of the holder for hand electrodes... 22 16. Schematic ... 23 17. Welding charts ... 25 17.1 Noninium® wires... 25 17.2 remanium® wires ... 26 17.3 remaloy® wires ... 27 17.4 rematitan® SPECIAL wires ... 28 17.5 Other materials ... 29 18. Quality information ... 30 19. EC-Declaration of Conformity ... 31
4
Dear customer Thank you for choosing a quality product from Dentaurum. It is essential to read these instructions carefully and adhere to them to ensure safe, efficient use and ensure that you and your patients gain full benefit. Instructions for use cannot describe every eventuality and possible application. In case of questions or ideas, please contact your local representative. As our products are regularly upgraded, we recommend that you always carefully read the current Instructions for use supplied with the product and stored in the internet at www.dentaurum.com, even though you may frequently use the same product.
1. Manufacturer Dentaurum GmbH & Co. KG I Turnstr. 31 I 75228 Ispringen I Germany
2. Safety information Caution: Read through the instructions for installing and operating the unit before switching it on.
2.1 Intended use The Master 3000 is only intended for welding and soldering of orthodontic appliances. The use of the unit for any other purpose is prohibited. The use of the unit for its correct purpose also includes compliance with all the instructions contained in the Instructions for use
The Master 3000 is not suitable for prosthetics work, in particular not for the processing of: precious metal alloys cast partial denture alloys or non-precious metal alloys for ceramics
When a Dentaurum product is taken out of operation once and for all, the disposal regulations of the country of operation apply. Dentaurum or the dental trade is available to answer questions regarding the correct disposal of any specific product.
5
2.2 Danger symbols and markings In the Instructions for use, the following symbols are used to indicate sources of danger to the user: This symbol indicates direct danger to the life or health of the user. Disregarding this warning may involve a serious risk to health. This symbol indicates important safety instructions. Disregarding this warning may cause damage to the unit and / or other property. This symbol gives important information on the correct use of the unit. Disregarding this information may cause the unit to malfunction.
3. General notes and disposal Always wear safety goggles when soldering or welding. To use the Master 3000 to its full advantage, study the following notes carefully before using it for the first time. The unit requires high voltage. To avoid accidents, the unit should only be opened by Dentaurum Customer Service’s personnel or authorized service technicians. When a Dentaurum product is taken out of operation once and for all, the disposal regulations of the country of operation apply. Dentaurum or the dental trade is available to answer questions regarding the correct disposal of any specific product. Note: This symbol indicates that products with this marking should not be disposed of together with household garbage. The legislator does not allow commercial customers to return electronic waste via municipal collection points. Further information is available from Dentaurum or the dental trade.
4. Description and usage 4.1 Application The Master 3000 spot-welding unit fulfils all the requirements for producing optimum weld or solder joints in orthodontic appliances: Continuous, high resolution adjustment of welding and soldering power Easy and precise setting of welding and soldering energy due to LCD display Electronic charge and discharge logic for thyristor control Ergonomic design Outlets for optional accessories
6
5. Technical data REF 079-000-00 Mains connection: 110 V – 240 V, 50 / 60 Hz Rated power: 140 W Impulse current: 2200 A Fuse: 3.15 A, time-delay fuse Insulation class: B Dimensions: 335 x 310 x 130 mm (13 ¼" x 8" x 5 ¼") (W x D x H) Weight: approx. 8,25 kg/18 lbs. Color: housing RAL 9001 white Base and hand rest: RAL 1515 blue Manual button: RAL 9006 white-aluminum The rating plate with the number is on the back of the unit.
6. Components supplied The basic set contains the following items: Master 3000 unit REF 079-000-00 Power cable Screwdriver for changing electrodes File for solder electrodes 1 x spare fuse (3.15 A, time-delay fuse) Instructions for use
7. Unpacking and start-up procedure Should you notice any damage which may have occurred in transit, notify immediately Dentaurum Customer Service (p. 20) or the dealer who supplied the unit. Before using the unit, ensure that the power supply voltage corresponds to the operating voltage stated on the rating plate on the back of the unit. The voltage is automatically set between 110 V and 240 V. Plug the power cable into the power cable outlet 0 and then into the power supply. The unit is now ready for operation.
7.1 Setting language of LCD display The Master 3000 is able to display five different languages on the LCD display. These languages are: German (manufacturer’s setting) English French Italian Spanish
7
1. To select one of these languages, the unit must be turned off at the power switch 0. 2. Press pad ' and ) and turn the unit on at the power switch 0 at the same time. 3. The LCD display now shows a language selection e. g. German and English. 4. With the pad ' or ) the lines can be moved up or down to select other languages. The language appearing in the top line can be selected. The cursor flashes in this line. 5. Press printer pad ( to select the language in the top line.
8. Operating instructions 8.1 Spot welding Always wear safety goggles for welding work. When using the hand electrodes for welding, the electrodes must not touch each other at the electrode holders, otherwise an electric current will flow through the electrode holders and the hand electrodes, causing poor welding results. In order to meet the complex requirements for constructing orthodontic appliances, the Master 3000 is fitted with 7 different copper electrodes for welding. These have special contact tips or surfaces. The click-stop electrode holders ", # permit quick and easy changing from one electrode to the other. When the holder is turned to the desired position, the electrodes click into the correct position in relation to one another. Maximum load on unit If the unit is being used over several hours, only one welding pulse at the most should be activated every 5 seconds. However, if it is only being used for a few minutes (max. 30 min) a pulse can be activated every second.
8
Electrode combinations and designs for welding: for welding: brackets, tubes, hooks
for welding:
wire to wire
wire to bands
Upper electrode REF 085–000–00
Upper electrode REF 085–200–00
Upper electrode REF 085–100–00
Lower electrode REF 086–000–00
Lower electrode REF 086–100–00 or REF 086–300–00
Lower electrode REF 086–200–00
and loops
For recommended welding settings, see charts (p. 25ff.) Notes Electrodes must always be clean. Clean, polished and correctly set electrode tips are
essential for good welds. Objects being welded must always be free of dirt and grease and have a clean metallic
surface. Polishing the tips Fold a piece of sandpaper (grain 600) with the rough side outwards and push it between the electrodes. Draw the sandpaper back and forth between the tips until the entire surface of both tips is polished. Remove any burrs which are created on the electrodes. If the electrodes no longer function correctly after a longer period, they can generally be re-worked slightly using the electrode file REF 083-300-00. However, if the size of the electrode tip is affected, replace the electrode with a new one. Applications Welding brackets to bands When welding brackets to band material or pre-formed bands, ensure that the upper electrode is positioned fully on the welding flange of the bracket. Welding tubes to wire The wall of the tube must be in contact with the wire. If the pressure of the electrode is not sufficient to make contact, it is suggested flattening the tube slightly at the contact point with pliers.
9
Spot-welding crossed wires Where the wires are simply crossed, a single spot-weld is usually adequate to connect them properly. In many cases, it is advisable to solder the wires in addition to welding. In this case, please take into account that heating the wires when soldering them to strengthen the joint also causes the mechanical properties of the wires to deteriorate. Checking a weld The simplest method is to make a visual check of the weld quality of a specific spot-weld, e. g. a weld-on component (bracket) onto a band. Clearly visible light brown points on the inside of the band indicate a successful weld. 8.1.1 Spot welding with the click-stop electrodes Procedure 1. Turn power switch 0 to position “I”. The WELDING previously selected mode appears again. The unit % 50 is now ready for use. 2. Press pad + to select the “welding” mode. The + LCD display now shows “welding” and the last figure set, e. g. 50. ' ) 3. Set the desired welding energy using the pad ' or ). The figure selected is shown in the LCD display. The welding energy can be set in steps from 01 to 88. If one of the pads ' or ) is pressed for longer than 4 seconds, the steps change faster. 4. Press hand rest ! down and set the desired combination of copper electrodes on the click-stop electrode holders " and #. 5. Press hand rest ! down and insert workpiece. When pressure on the hand rest is reduced, the electrodes close and fix the workpiece in position. 6. Activate the welding pulse with the # manual button $ or foot switch (optional accessory). 2-3 adjacent welding pulses are enough to create a perfect welded joint. 7. Release the workpiece by pressing the hand rest ! and repeat the welding process if necessary. " 8. After completing the welding process, turn $ the unit off and turn the power switch 0 to position “0”.
10
8.1.2 Spot welding with hand electrodes (optional accessory) This process is recommended when for example wires have to be fixed against one another on the model. The components removed from the model should then be re-welded or soldered at the click-stop electrodes. Procedure 1.Turn the upper electrode head on the click-stop holder # one turn (45°) to the left or the right. The upper and lower electrodes must not touch each other. 2. Push the plugs of the hand electrodes into the WELDING outlets - and /. % 50 3. Turn power switch 0 to position “I”. The previously selected mode appears again. 4. Press pad + to select the “welding” mode. The + LCD display now shows “welding” and the last ' ) figure set, e. g. 50. 5. Set the desired welding energy using the pad ' or ). The figure selected is shown in the LCD display. The welding energy can be set in steps from 01 to 88. If one of the pads ' or ) is pressed for longer than 4 seconds, the steps change faster. 6. Clamp a notched electrode REF 081-501-00 into each of the clamping sleeves of the manual electrodes and then touch the workpiece with the notched tips at a short distance from the welding point. The notches of the electrode prevent it from slipping off the wire element. 7. Activate the welding pulse with the manual button $ or foot switch. 2-3 welding pulses are enough to create a perfect welded joint. 8. `After completing the welding process, turn the unit off and turn the power switch 0 to position “0”. Note When welding with the hand electrodes, the welding power must be set higher than with the click-stop holder. The welding energy setting depends on the cross section of the material being welded. (See separate charts p. 25ff.).
11
Recommended accessory: Connect foot switch REF 080-116-00 to outlet ,.
8.2 Soldering When soldering, always wear safety goggles. If soldering takes too long, the soldering carbon will be damaged. When using hand electrodes for soldering or heat-treating, the electrodes must not touch each other at the electrode holders. However, if they do touch one another, a fault signal will be given. If the carbon electrode is used, the current flows through the electrode holder and through the hand electrodes, causing poor soldering results. For soldering purposes, one of the copper electrodes is replaced by a carbon electrode
(soldering electrode REF 085-300-00). The heat created by the electrical resistance is stored mainly in the carbon tip, whereas the metal parts themselves absorb only a slight amount of heat. The soldering process differs from the welding process by using solder and flux. During electric soldering, the carbon electrode leads to continuous heating until the solder is melted. This then flows around the metal parts which are also heated and protected from oxidation by the flux. Before soldering, the carbon electrode should be cleaned with the emery file, REF 083-30000 to remove any flux residues, which have an insulating effect and would hinder the flow of current during the next soldering operation. Replace the carbon electrode before the brass sleeve and the electrode shaft begin to char. We recommend using a pencil sharpener to sharpen the soldering carbon REF 081-601-00. To increase the conductivity of the soldering carbon, dip the tip in water before beginning the soldering operation. The hand electrodes are not suitable for continuous soldering. The soldering carbon offers more resistance to the current than the clamping electrode REF 081-701-00, thus causing heat to build up in the tip of the soldering carbon. Always ensure that the carbon tip is placed where the heat cannot damage the parts.
12
8.2.1 Soldering with the click-stop electrodes First tack weld the parts together with a weld spot. Procedure 1. Turn power switch 0 to position “I”. The previously selected mode appears again. 2. Press pad & to select the “soldering” mode. The LCD display now shows “soldering” and the last figure set for soldering energy, e. g. 50. 3. Set the electrodes to combination A or B (cf. fig. below). 4. Apply flux to the section to be soldered and add the solder or apply universal silver soldering paste (REF 380-804-50). 5. Set the desired heat intensity from 01 to 88 using the pad ' or ). The setting is made in steps from 01 to 88. If one of the pads ' or ) is pressed for longer than 4 seconds, the steps will change faster. 6. Press the hand rest ! down and place the workpiece between the electrodes. 7. Align the carbon electrode on the workpiece without applying pressure. SOLDERING 8. Press the manual button $ or the foot switch % 50 until the solder is melted and the soldering process finished.
&
Note: Please always use the carbon soldering electrode
'
)
Electrode combination:
$
A
B
13
8.2.2 Soldering with hand electrodes (optional accessory) Procedure 1. Turn the upper electrode head on the click-stop holder # one turn (45°) to the left or the right. The upper and lower electrodes must not touch each other. 2. Push the plugs of the hand electrodes into the outlets - and /. 3. Clamp the electrode REF 081-701-00 for holding the workpiece and clamp the soldering carbon REF 081-601-00 into the clamping sleeve of the right SOLDERING and left hand electrode (cf. fig. below). % 50 4. Turn power switch 0 to position “I”. 5. Press key & to select the “soldering” mode. The green & LED & key lights up, when the unit electronics are operational. ' ) 6. Clamp the tack-welded parts in the clamping electrode as close as possible to the soldering point. 7. Place the tip of the soldering carbon as close as possible to the soldering point. 8. Proceed as below a) or b) depending on the type of solder used a) Press the foot switch. Apply the solder when the solder joint begins to turn red. b) Press the foot switch until the solder has completely melted. 9. If the unit is no longer required, turn power switch 0 to position “0”.
Hand electrode with soldering carbon
Hand electrode with clamping electrode 8.2.3 Continuous soldering Press key * to select the “continuous soldering” mode. The soldering process is initiated by pressing the manual button $ or foot switch once. It is ended by pressing the manual button $ or foot switch a second time. Disregarding this instruction will cause the electrodes to burn out.
14
%
CONTINUOUS SOLDERING 50
* '
)
8.3 Heat treatment 8.3.1 Annealing of wires Spring hard chrome nickel stainless steel wires (e. g. remanium®) can be soft annealed at a temperature of approx. 1100 °C / 2012 °F (heat color: bright red). Soft annealed CoCr wires cannot be tempered (hardened)! Complex bending operations (especially around tight radii with thick wires, e. g. outer wires of face bows) should not be done without previous local annealing of the bending area. Soft annealing is also recommended for removing the elasticity from a wire over a certain length, e. g. with a passive lingual or palatal bow. Refer to 8.3.4 for the subsequent procedure.
8.3.2 Tempering of wires Cobalt based alloys, e. g. remaloy®, or Crozat wires can be tempered (hardened). The tempering of the wire elements depends on the time and the temperature. Heat the wire element only briefly using the hand electrodes (heat color: dark brown) at a temperature of approx. 470 °C / 878 °F. In view of the different wire dimensions, it is recommended to determine the optimum hardening conditions experimentally beforehand. Refer to 8.3.4 for the subsequent procedure.
15
8.3.3 Stress relieving of wires When spring hard wires are bent, stresses are created in their crystalline structure. The bent wire element can be stress relieved using a suitable heat treatment process. This is done by heating the wire to approx. 550 °C / 1022 °F over a short period of time. (Heat color: dark red). Remember that stress relieving wire elements on the model takes longer as the plaster absorbs a considerable amount of heat. Refer to 8.3.4 for the subsequent procedure.
8.3.4 Procedure for soft annealing, tempering and stress relieving Important! 1. Turn the upper electrode head on the click-stop holder # one turn (45°) to the left or the right.
%
SOLDERING 50
The upper and lower electrodes must not touch each other. Should they touch, a fault & signal will be given. 2. Fit the hand electrodes into outlet - and / and ' ) clamp the notched electrodes REF 081-501-00 into the clamping sleeves. 3. Connect the foot switch to outlet ,. 4. Turn power switch 0 to position “I”. 5. Press pad &. The LCD display now shows “soldering” and the last figure set, e. g. 50. 6. Set pad ' or ) for continuous heat control to a low figure, e. g. 05. Increase it depending on the material’s cross section. Carry out tests! 7. Set the notched electrode tips in the area of the wire to be heat treated. 8. Operate the foot switch until the wire has reached the temperature (color) for the desired heat treatment process. Bright red approx. 1100 °C / 2012 °F soft annealing Dark red approx. 550 °C / 1022 °F stress relieving Dark brown approx. 470 °C / 878 °F tempering 9. Remove the electrodes quickly from the wire and release the foot switch. 10. On completion of heat treatment, turn the power switch 0 to position “0”.
16
Note: To soft anneal thick wires, we recommend placing these on a conductive, heat-resistant
base, e.g. a graphite slab. Instead of the notched electrode REF 081-501-00, the clamping electrode REF 081-701-00
in a hand electrode can be used to hold the wire element. To practice the techniques necessary for soft annealing, tempering and stress relieving, we
recommend experimenting with the different kinds of wire. Caution: With thin wires, only press the foot switch briefly to ensure the wires do not burn or melt!
9. Printer function with report printer Optional accessory: report printer REF 090-581-00 Using the print function, set parameters can be stored and then printed out after end of work using the report printer available as an optional accessory (REF 090-581-00). 9.1 Connecting report printer 1. Set power switch 0 on welding unit to position “0”. Connect printer cable to outlet . at the back of the unit. 2. Turn powerswitch 0 to position 'I'. The previously selected mode and figure (e.g. 50) appear again. 3. Set the operating switch of the report printer to “ON”. The printer is fitted with batteries and is ready for operation after turning on when the battery is charged. The yellow LCD lights up. If this is not the case, connect the charging unit to the charging outlet of the printer. The printer is now supplied with current through the power cable. 9.2 Function: Printing in “welding” mode 1. Connect the printer to the welding unit as described in section 9.1. 2. Press pad + on the welding unit to select “welding“ mode. The digital display now shows “welding” and the last figure set, e.g. 50. 3. Press pad ( on the welding unit. The yellow LCD lights up. All processes and weld settings are now stored in the printer’s memory. 4. After ending the welding work, again press pad ( on the welding unit. The LCD goes off and the data is transferred to the report printer. If no printer is connected, “CHECK PRINTER” appears in the display. 5. The following parameters are now printed on the report: (see 9.3)
17
9.3 Function: Printing in “solder” mode 1. Connect the printer to the welding unit as described in section 9.1. 2. Press pad & on the welding unit to select “soldering“ mode. The LCD display now shows “soldering” and the last figure set, e. g. 50. 3. Press pad ( on the welding unit. The yellow LCD lights up. All processes and solder settings are now stored in the printer’s memory. If no printer is connected, “CHECK PRINTER” appears in the display 4. After ending the soldering work, again press pad ( on the welding unit. The LCD goes off and the data is transferred to the report printer. 5. The following parameters are now printed on the report: “Welding“
“Soldering“
Note: For more detailed information on printer functions, refer to the operating instructions for the
report printer. The printer outlet . of the welding unit is intended only for the report printer described
(REF 090-581-00). Connecting printers or units of any other kind may cause irreparable damage to the electronic components of the welding unit.
10. Power-saving mode The welding unit is fitted with a power-saving mode. If the unit remains unused for longer than 10 minutes when switched on, a number of important functions are switched off automatically. The signal “STANDBY” appears in the display. This function saves power. As soon as a pad on the operating panel or the manual button $ is pressed, the welding unit turns on again. The previously selected mode appears in the display.
18
11. Troubleshooting Fault
Cause
Remedy
1.0 Unit switched on but nothing appears in display
1.1 Not connected to power supply
1.1.1 Connect unit to power supply 1.1.2 Check fuse at power outlet
1.2 Unit fuse defective
1.2.1 Replace 3.15 A time-delay fuse. *To change fuse (see below)
2.1 Electrodes or solder carbon dirty or worn
2.1.1 Clean or replace electrodes or solder carbon
2.0 Set welding and soldering power too low
The electrodes must be positioned flat in relation to each other 2.2 Welding or soldering power set too low
2.2.1 Increase power with pad '
3.0 LCD display indicates: Error 1
3.1 Unit overheated
3.1.1 Switch unit off and allow it to cool
4.0 LCD display indicates: Check electrodes
4.1 In solder function: copper electrode used instead of carbon electrode
4.1.1 Select carbon electrodes
4.2 New soldering carbon inserted (good conduction) and high power
4.2.1 Reduce power with pad )
5.1 No printer connected or printer not ready for use
5.1.1 Connect printer and check proper function
5.0 LCD display indicates: Check printer
The unit operates under high voltage! To prevent accidents, never open the unit. If malfunctions cannot be corrected in the above ways, please contact Dentaurum Customer Service (see page 20). *Replacing the fuse: Unlock the fuse insert on the right-hand side of the combination plug 0 and pull it out. The fuse is now accessible and can be removed from the fuse holder. Pull out the power plug before removing the fuse holder!
19
12. Dentaurum Customer Service Dentaurum Customer Service Dentaurum GmbH & Co. KG I Turnstr. 31 I 75228 Ispringen I Germany (P.O.B. 100 440, 75104 Pforzheim) Tel. + 49 72 31 / 803-211 I Fax + 49 72 31 / 803-295 I [email protected]
13. Care and maintenance The unit requires no maintenance. Only the copper electrodes require filing after use. Carbon electrodes must also be cleaned after use to remove flux residues. If necessary, wipe the cover with a dry or damp cloth. Do not use corrosive cleaning agents! Do not place hot objects in the tray 1.
14. Spare parts for ”click-stop“ holders Upper electrodes
Lower electrodes REF 086–000–00 1 piece REF 085–000–00
REF 086–100–00
1 piece
1 piece
REF 085–100–00
REF 086–200–00
1 piece
1 piece
REF 085–200–00
REF 086–300–00
1 piece
1 piece
Soldering electrodes
Spare carbon insert for soldering electrode REF 085–300–00
REF 086–400–00
1 piece
10 pieces
Screws for tightening electrodes
Spare fuse 3.15 A, time-delay fuse
REF 084–100–00
REF 907-037–10
10 pieces
1 piece
Screwdriver
REF 083–100–00
for changing electrodes
1 piece
Emery file for soldering carbon
REF 083–300–00
20
10 pieces