DENTSPLY International
Astra Tech Implant System Cleaning and Sterilization Instructions Nov 2017
Cleaning and Sterilization Instructions
12 Pages
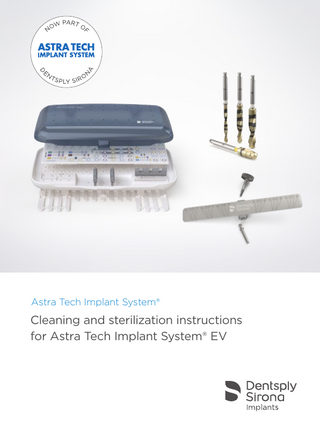
Preview
Page 1
Astra Tech Implant System®
Cleaning and sterilization instructions for Astra Tech Implant System® EV
Astra Tech Implant System® CONTENTS Introduction – Astra Tech Implant System® EV
4
Pre cleaning
4
Cleaning
6
Pre sterilization
7
Sterilization
7
Storage
7
Washtray EV – Cleaning and sterilization
8
Maintenance of products from additional manufacturers
10
General requirements
11
All products may not be regulatory cleared/released/licensed in all markets. Please, contact the local Dentsply Sirona sales office for current product assortment and availability. To improve readability for our customers, Dentsply Sirona does not use ® or ™ in body copy. However, Dentsply Sirona does not waive any right to the trademark and nothing herein shall be interpreted to the contrary. Product illustrations are not to scale.
3
Introduction / Pre cleaning
Introduction The system The system comprises dental implants, cover screws, transmucosal abutments, other prosthetic components, as well as surgical and prosthetic instruments. Astra Tech Implant System EV components may only be used together with original products and instruments. Reusable products are designed to be cleaned, disinfected and sterilized after each use.
Statement Cleaning and sterilization of Astra Tech Implant System® EV products The cleaning and sterilization instructions for Astra Tech Implant System EV assortment has been developed and validated by Dentsply Sirona. The instructions have been developed in accordance with the applicable standards stated, in respective section.
When using reprocessing procedures that are different from those described in this manual, this procedure must be validated by the respective practice or hospital. Both the VarioTD program (recommended for automated reprocessing) and the Neodisher Mediclean Forte (Dr. Weigert) detergent are recommendations and can be substituted with similar programs and detergents. For more information, please see http://www.mieleprofessional.com and/or www.drweigert.com. Large Tray EV and Small Tray EV are made of PPSU (Polyphenylsulfone) material which may be sensitive to some chemicals containing acetate e.g. ethyl acetate. Consult your detergent manufacturer for compatibility of used detergent with PPSU if Neodisher Mediclean Forte is not used.
Pre cleaning Inspection and function testing ■■
Discard blunt or damaged products.
■■
All drills, except the single use Precision Drill EV, can be used approximately ten times. If drills are not reused, dispose them in a sharps container immediately after the implant procedure is completed.
For guided surgery: ■■
Remove the sleeve from the drill. The sleeve is for single use only. For detailed information please refer to the instructions for use.
Preparation for cleaning ■■
Remove residual tissue or bone debris by immersing the used products in lukewarm water (<40 °C/104 °F).
■■
For this purpose, remove the instruments from the instrument tray and rinse them under running water while removing coarse contamination with a fine, soft nylon brush.
■■
Do not use fixation agents or hot water as this could influence subsequent cleaning results.
■■
Products should be kept in a wet environment until the next step is initiated.
■■
If cleaning is delayed more than 120 minutes, place the devices in a bath of a cleaning and disinfection solution to avoid drying of soil and/or debris, blood and other contaminations.
For drills: If using an ultrasonic bath, place the drills in a drill organizer.
4
Pre cleaning
Disassembly is required for the following products: ■■
Impression components (pick-ups/transfers)
■■
Guiding cylinder handle
■■
SmartFix® Guide
■■
Torque Wrench
■■
Trays, remove drills and instruments
■■
GS Drills and drill sleeve
Impression components (pick-ups/transfers)
Guiding cylinder handle
1.
2.
SmartFix® Guide
Torque Wrench
GS Drills and drill sleeve
Lid Lid
Overlay
Overlay
Tray base
Tray base
Base shield
Large Tray EV
Small Tray EV
5
Cleaning
Water quality
■■
FDA listed: CIDEX® OPA Manufacturer: Johnson & Johnson High level disinfectant for semi-critical medical devices Ingredients: ortho-phtalaldehyde, dipotassium hydrogen phosphate, potassium dihydrogen phosphate, benzotriazole, citric acid, D&C Green Dye #5, N-(hydroxyethyl) -ethylenediaminetriacetic acid (HEDTA)
■■
Adhere to the concentrations and exposure times recommended by the manufacturer of the cleaning, neutralization and disinfecting agents.
The water quality recommended for cleaning (especially for the final rinse phase) is fully demineralized water or water which corresponds to this level of purity.
Cleaning, neutralization and disinfecting agents The following commercially available cleaning, neutralization agents and disinfectants were used: ■■
■■
■■
Cleaning agent neodisher® MediClean forte Manufacturer: Dr. Weigert, Hamburg, Germany Ingredients for cleaning agents according to the Regulation (EC) No 648/2004 on Detergents: <5% non-ionic or anionic surfactants, and enzymes Neodisher® Z Manufacturer: Dr. Weigert, Hamburg, Germany Ingredients for detergents and cleaning agents according to EC Recommendation 89/542/EEC: organic acids ID 213 Instrument disinfection Manufacturer: DÜRR SYSTEM-HYGIENE, Germany Ingredients: alkylamines, quaternary ammonium compounds, non-ionic surfactants, complexing angents, auxiliary substances as well as citronellol and coumarin; DGHM-/VAH (2011) listed
Cleaning program in washer disinfector The recommended cleaning program is the Vario TD program with thermal disinfection which operates at the optimum temperature of 45–55 °C for the removal of blood, or any other adequate and validated program. [2.] [3.].
Thermal disinfection Thermal disinfection is part of the Vario TD program and takes into account the A0 value (A0 ≥3000). The A0 value is a measure for the reduction of microorganisms in steam disinfection processes. [2.] [3.].
Cleaning Manual procedure ■■
Apply detergent, Neodisher® MediClean forte (Dr. Weigert, Hamburg) or similar solution to all surfaces.
■■
Scrub the outer and, if applicable, the inner side of the product with a soft bristled nylon brush until all visible soil and/or debris is removed.
■■
Flush the inner channels/lumen with cleaning solution using an irrigation needle connected to a syringe. Check channels/lumen for residual soil and/or debris.
■■
6
Run the products in an ultra-sonic bath with cleaning solution for minimum ten minutes. Drills and trays excluded. Rinse under clean running water until all trace of cleaning solution is removed.
■■
Flush the inner channels/lumen with water using an irrigation needle.
■■
Prepare a bath with a disinfection solution, ID 212 instrument disinfection (DÜRR SYSTEM-HYGIENE) or similar, according to the detergent manufacturer’s instruction. Immerse the products completely for the time specified by the manufacturer.
■■
Flush minimum 3 times internal channels/lumen using an irrigation needle. Rinse under clean running water until all trace of disinfection solution is removed. Flush the inner channels/lumen with water using an irrigation needle.
■■
Dry the products using medical compressed air and clean lint free single-use wipes.
Automated procedure ■■
Place instruments in a washer-disinfector, Vario TD or similar, according to recommendations from the supplier: Example of Vario TD washing program: – Pre-wash, 20 °C – Cleaning with detergent, Neodisher® MediClean forte (Dr. Weigert, Hamburg) or similar solution 45-55 °C – Neutralization – Intermediate rinse – Disinfection, >90 °C (preferably 93 °C), 5 min – Drying
Procedures in accordance with [1.] [2.] [4.] [6.].
Pre sterilization / Sterilization / Storage
Pre sterilization Drying prior to sterilization ■■
The instruments are dried automatically during the drying cycle in the washer disinfector.
■■
Use medical compressed air for drying drill holes/ through holes.
■■
Then check the cleaned and disinfected medical devices for damage and any corrosion.
■■
Replace damaged or corroded medical devices.
Packaging prior to sterilization ■■
Thoroughly dry everything prior to the sterilization process to prevent the risk of corrosion.
■■
Assemble the tray and re-position the drills and instruments, using drill/letter numbers, where applicable. It is recommended to wrap the instruments and tray according to the sterilization wrap manufacturer’s instructions. It is recommended to place additional products in a sterilization bag.
Packaging suitable for steam sterilization must comply with the requirements according to DIN EN ISO 11607/ ANSI/AAMI ST79/AAMI TIR12:2010, e.g. disposable sterilization packages (single or double packages) temperature-resistant up to at least 137 °C (279 °F) and sufficient steam permeability, which provide sufficient protection against mechanical damage, or sterilization containers which need to be maintained according to the manufacturer’s instructions. Note: For US: Use FDA cleared sterilization bag and 16 minutes dry time at the end of the steam sterilization cycle.
Sterilization Steam sterilization ■■
Steam sterilization with a pre-vacuum cycle (134 °C for 3 minutes)
■■
Use the sterilized components within the stated time period from the sterile bag manufacturer.
Note: For US: Steam sterilization with a pre-vacuum cycle (275 °F for 3 minutes). Sterilization is performed in the autoclave. For sterilization parameters see table. Method
Cycle
Temperature
Exsposure time*
Drying time
Steam
Dynamic air removal (pre-vacuum)
132 °C (270 °F)
4 min.
20 min.
134 °C (273 °F)
3 min.
20 min.
135 °C (275 °F)
3 min.
20 min.
121 °C (250 °F)
30 min.
20 min.
Steam
Gravity displacement
* Minimum exposure times, the operating times are longer and may vary depending on the device.
Procedures in accordance with [1.][2.].
Storage The products should be stored, in their package, in a dry place, at normal temperature (18–25°C/64–77°F). Use the sterilized components within the stated time period from the sterile bag manufacturer.
7
Washtray EV
Washtray EV Mechanical/automated processing The following describes automated processing and sterilization according to DIN EN ISO 17664. ■■
All drills, except the single use Precision Drill EV, can be used for approximately ten cases. If drills are not reused, dispose them in a sharps container immediately after the implant procedure is completed. For guided surgery: Remove the sleeve from the drill. The sleeve is for single use only. For detailed information please refer to the instructions for use.
■■
Remove coarse contamination such as blood, tissue and bone residue immediately after use. For this purpose, remove the instruments from the instrument tray and rinse them under cold running water while removing coarse contamination with a fine, soft nylon brush.
■■
For automated processing, place the instruments in the appropriate positions provided in the basket of the Washtray.
■■
Disassemble instruments that can be disassembled before cleaning and place them in the sieve basket of the Washtray.
Ultrasonic pre-cleaning To ensure efficient automated processing instruments need to be pre-cleaned in an ultrasonic bath. ■■
Remove the Overlay from the Washtray and close the loaded Washtray with the lid of the basket.
■■
Place the closed Washtray in an ultrasonic bath filled with cleaning agent (neodisher® MediClean forte). The Washtray must be entirely covered by the cleaning agent.
■■
Adhere to the concentrations and exposure times recommended by the manufacturer of the cleaning agent (minimum duration of ultrasonic cleaning 5 minutes).
■■
Ensure that the liquid levels recommended by the manufacturer of the ultrasonic bath are observed.
Automated cleaning Suitable washer-disinfectors are to be used for automated cleaning, which are to be validated by the user as part of the established cleaning processes.
8
Washtray EV
Loading ■■
Insert the Miele E 327 mobile unit into the washer-disinfector.
■■
Place the closed Washtray without the Overlay in the mobile unit.
■■
Clean the overlay separately from the Washtray.
■■
Follow the instructions of the manufacturer of the washer-disinfector.
Cleaning and neutralization agents The following agents are recommended for cleaning: ■■
Cleaning agent neodisher® MediClean forte.
■■
Neutralization agent neodisher® Z.
■■
Cleaning and neutralization agents are to be dosed and used according to the manufacturer’s instructions.
Water quality The water quality recommended for cleaning (especially for the final rinse phase) is fully demineralized water or water which corresponds to this level of purity.
Cleaning program The recommended cleaning program is the Vario TD program with thermal disinfection which operates at the optimum temperature of 45–55 °C for the removal of blood, or any other adequate and validated program.
Thermal disinfection Thermal disinfection is part of the Vario TD program and takes into account the A0 value (A0>=3000). The A0 value is a measure for the reduction of microorganisms in steam disinfection processes.
Drying prior to sterilization The instruments are dried automatically during the drying cycle in the washer disinfector. ■■
Use residueless compressed air for drying drill holes/through-holes.
■■
Then check the cleaned and disinfected medical devices for damage and any corrosion.
■■
Replace damaged or corroded medical devices.
9
Washtray EV
Sterilization ■■
Prior to sterilization reassemble the disassembled medical devices and sort them into the holders provided in the Washtray for sterilization. Note: Medical devices that were cleaned in the Washtray can also be placed back into the Surgical Tray EV for sterilization.
Method
Cycle
Temperature
Exposure time*
Drying time
Steam
Dynamic air removal (prevaccum)
132 °C (270 °F)
4 min.
20 min.
134 °C (273 °F)
3 min.
20 min.
135 °C (275 °F)
3 min.
20 min.
121 °C (250 °F)
30 min.
20 min.
Steam
Gravity displacement
■■
Place the Overlay in the Washtray, close the Washtray with the lid and lock it in place.
* Minimum exposure times, the operating times are longer and may vary depending on the device.
■■
Pack the loaded Washtray in a single-use sterilization (single or double) package or in a sterilization container suitable for steam sterilization.
Storage
Every sterile packaging should display a sterilization indicator and be marked with the date of sterilization. Packaging suitable for steam sterilization must comply with the requirements according to DIN EN ISO 11607/ ANSI/AAMI ST79/AAMI TIR12:2010, e.g. disposable sterilization packages (single or double packages) temperature-resistant up to at least 137 °C (279 °F) and sufficient steam permeability, which provide sufficient protection against mechanical damage, or sterilization containers which need to be maintained according to the manufacturer’s instructions. Sterilization is performed in the autoclave. For sterilization parameters see table.
■■
The products should be stored, in their package, in a dry place, at normal temperature (18–25°C/64–77°F).
■■
Use the sterilized components within the stated time period from the sterile bag manufacturer
Maintenance of below products, follow the manufacturer’s instructions
Torque Wrench EV
W&H
10
Locator Core Tool
General requirements / Maintenance for produts from additional manufacturers
General requirements for the processing/reprocessing of medical devices The ever-present risk of contamination and infection during treatment must be excluded or reduced by specific preventive measures. These include: ■■
■■
■■
Assessment of the risks and dangers in connection with medical practice and definition of appropriate precautions Schematization and systematization of work routines with the predominant aim of avoiding contamination and injuries Careful anamnesis with special regard to patientinduced risks of infection
All used as well as unpacked but previously unused medical devices have to be considered contaminated and must therefore be processed hygienically without exception. Medical devices should not be stored in physiological saline solution as prolonged exposure may lead to corrosion. The parts must be moistened completely and bubble-free in a bath. Demineralized water is required under all circumstances for final rinsing after disinfection to avoid water stains and crystal seeding which may interfere with the subsequent process of sterilization.
be serviced at regular intervals, and all parameters must be observed in every cycle. Please observe the shelflife indicated on the sterile packaging of devices (see manufacturer’s instructions). All medical devices that are supplied non-sterile must be processed prior to their first use on a patient. All reusable medical devices must be reprocessed after every use according to the described validated procedure. All drills, except the single use drills, can be used approximately ten times. If drills are not reused, dispose them in a sharps container immediately after the implant procedure is completed. All removable parts of the medical devices must be disassembled for cleaning and disinfection and assembled prior to sterilization. If using an ultrasonic bath, place the drills in a drill organizer. Automated processing and sterilization according to DIN EN ISO 17664.
As your responsibility includes the sterility of the medical devices used, please bear in mind that only validated procedures must be used for cleaning, disinfection and sterilization. All equipment needs to
[1.] EN ISO 17664 Sterilization of medical devices – Information to be provided by the manufacturer for the preparation of re-sterilizable medical devices (ISO 17664) [2.] RKI Guideline 2012: Hygiene requirements for the reprocessing of medical devices (German Federal Health Gazette 2012; 55: 1244-1310) [3.] Guidelines of the DGKH (German Asso-ciation for Hospital Hygiene), DGSV (German Association for Sterile Services) and AKI (Working party instrument preparation) for the validation and routine monitoring of mechanical cleaning and thermal disinfection processes for medical devices, 4th edition 2014 [4.] Guidance for Industry and FDA Staff – Reprocessing Medical Devices in Health Care Settings: Validation Methods and Labeling, March 17, 2015 [5.] AAMI TIR12:2010, Designing, testing, and labeling reusable medical devices for reprocessing in health care facilities: A guide for medical device manufacturers [6.] EN ISO 15883-1 Cleaning and disinfection appliances – Part 1: General requirements, definitions and test methods (ISO 15883)
11
Dentsply Sirona does not waive any right to its trademarks by not using the symbols ® or ™. 32671332-USX-171 1 © 2017 Dentsply Sirona. All rights reserved.
About Dentsply Sirona Implants
About Dentsply Sirona
Dentsply Sirona Implants offers comprehensive solutions for all phases of implant therapy, including Ankylos®, Astra Tech Implant System® and Xive® implant lines, digital technologies, such as Atlantis® patient-specific solutions and Simplant® guided surgery, Symbios® regenerative solutions, and professional and business development programs, such as STEPPS™. Dentsply Sirona Implants creates value for dental professionals and allows for predictable and lasting implant treatment outcomes, resulting in enhanced quality of life for patients.
Dentsply Sirona is the world’s largest manufacturer of professional dental products and technologies, with a 130-year history of innovation and service to the dental industry and patients worldwide. Dentsply Sirona develops, manufactures, and markets a comprehensive solutions offering including dental and oral health products as well as other consumable medical devices under a strong portfolio of world class brands. As The Dental Solutions Company™, Dentsply Sirona’s products provide innovative, high-quality and effective solutions to advance patient care and deliver better, safer and faster dentistry. Dentsply Sirona’s global headquarters is located in York, Pennsylvania, and the international headquarters is based in Salzburg, Austria. The company’s shares are listed in the United States on NASDAQ under the symbol XRAY. Visit www.dentsplysirona.com for more information about Dentsply Sirona and its products.
THE DENTAL SOLUTIONS COMPANY™