Dräger Medical
Oxylog 3000+ Technical Documentation Rev 2.0 Nov 2009
Technical Documentation
100 Pages
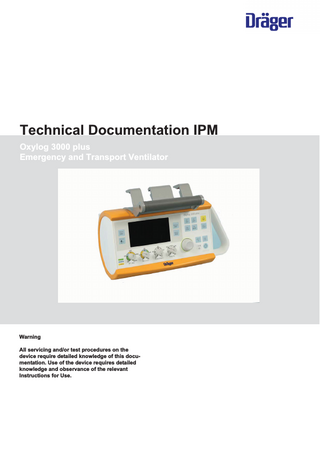
Preview
Page 1
Technical Documentation IPM Oxylog 3000 plus Emergency and Transport Ventilator
Warning All servicing and/or test procedures on the device require detailed knowledge of this documentation. Use of the device requires detailed knowledge and observance of the relevant Instructions for Use.
0000000763_Publication_11.11.09
– This page has been intentionally left blank –
2
Oxylog 3000 plus
Table of contents
Table of contents 5 6 9 10 12 16 20 23
0000000763_Publication_11.11.09
General General notes... Function descriptions General information... Pneumatic assembly... Electronic assembly... MCable-Mainstream CO2 sensor M11.1... Annex
Oxylog 3000 plus
3
Table of contents
0000000763_Publication_11.11.09
– This page has been intentionally left blank –
4
Oxylog 3000 plus
General
This chapter contains general notes and definitions that are important for the use of this documentation. 6
Oxylog 3000 plus
5
0000000763_Publication_11.11.09
General notes ...
General General notes
General notes
Notes on use
Read through the following notes thoroughly before applying this documentation. Dräger reserves the right to make changes to the device and/or to this documentation without prior notice. This documentation is intended solely as an information resource for experts, and will be updated only at their request.
Copyright and other protected rights
The content of this documentation, in particular its design, text, software, technical drawings, configurations, graphics, images, data and their selection and its composition and any amendments to it ("content") are protected by copyright. The content must not (in whole or in part) be modified, copied, distributed, reproduced, republished, displayed, transmitted or sold without the prior written consent of Dräger.
Definitions WARNING! An important advisory indicating a potentially hazardous situation which may result in death or serious injury if not prevented. CAUTION An important advisory indicating a potentially hazardous situation which may result in minor or moderate injury to the user or to patients or in damage to the device or to other assets if not prevented. NOTE An additional advisory intended to avoid problems in using or servicing the device.
=
Identification of actual condition
Maintenance
=
Measures to maintain the specified condition
Repair
=
Measures to restore specified condition
Servicing
=
Inspection, maintenance, repair
0000000763_Publication_11.11.09
Inspection
6
Oxylog 3000 plus
General General notes
Notes
Read through each section thoroughly before beginning servicing. Always use the correct tools and the specified test equipment. Otherwise the device may not work correctly or may be damaged. WARNING! – Dräger recommends using original Dräger parts for servicing. Otherwise the device's correct functioning could be compromised. –
Pay attention to the „Servicing“ section of the Instructions for Use.
CAUTION Improper servicing. Device not working or working incorrectly. –
Servicing may only be carried out by experts.
NOTE Where reference is made to legislation, regulations and standards, in respect of devices used and serviced in Germany they are based on the laws of Germany. Users and technicians in other countries must comply with their national laws and/or international standards. CAUTION Non-conforming test values. Device not working or working incorrectly. –
Do not put the device into operation.
–
Contact your local service organization.
CAUTION
0000000763_Publication_11.11.09
Before carrying out any servicing, check that the device and its components have been handed over by the user cleaned and disinfected.
Oxylog 3000 plus
7
General General notes
0000000763_Publication_11.11.09
– This page has been intentionally left blank –
8
Oxylog 3000 plus
Function descriptions
This chapter contains descriptions of the device's technical functions. 10 12 16 20
0000000763_Publication_11.11.09
General information ... Pneumatic assembly ... Electronic assembly ... MCable-Mainstream CO2 sensor M11.1 ...
Oxylog 3000 plus
9
Function descriptions General information
General information
Introduction
The following provides a brief introduction to the device. The detailed functionality of the electronic and pneumatic components is set out in the function description"Electronic assembly" and"Pneumatic assembly". How to use the device, indications of its intended purpose etc., are set out in the Instructions for Use.
Design
Fig. 1
Functional principle
Front view
The device is an emergency and transport ventilator for short-time therapy. It is powered by an internal rechargeable battery. A DC/DC converter or an AC/DC power supply unit can also be connected to it. The propellant gas is compressed oxygen. If required, ambient air can be mixed with the respiratory gas for the purpose. The respiratory gas is metered using the pneumatic system and the ventilation valve.
0000000763_Publication_11.11.09
Evaluation of the sensors and the setup parameters, on-screen display and operation of the pneumatic components is electronic.
10
Oxylog 3000 plus
Function descriptions General information
Connections and interfaces
Fig. 2
Connections Item
Designation Serial port
2
Emergency air inlets (at the left and right on the rear)
3
Connections for the flow measurement tubes
4
Ventilation tube outlet
5
Compressed O2 inlet
6
Power supply connection
7
CO2 sensor connection
0000000763_Publication_11.11.09
1
Oxylog 3000 plus
11
Function descriptions Pneumatic assembly
Pneumatic assembly
Introduction
The following details the functioning of the device's pneumatic components. The various assemblies include components for measurement and metering of the preset ventilation parameters. The assemblies are operated and evaluated electronically.
Design
Fig. 3
Overview of pneumatic components Item
Designation Metering block
2
Flow sensors
3
Connection block
0000000763_Publication_11.11.09
1
12
Oxylog 3000 plus
Function descriptions Pneumatic assembly
Functional principle
Fig. 4
Pneumatic diagram, 1 = Components in the connection block, 2 = Components in the metering block Inlet
The compressed oxygen passes through the filter F1 and the pressure regulator DR to the valves V1 to V3. The pressure regulator regulates the pressure to 3 bar. This is done to attain a stable flow control. The Control PCB monitors this pressure, which is measured with sensor S3.
Metering unit
Valves V1 to V3 are proportional valves, each delivering a flow proportional to the overall flow of 0 to 35 L/min. The flow sensor S1 measures the delivered flow and the Control PCB corrects the valve operation as necessary. Valve V3 comprises two parallel configured valves, to produce a total flow greater than 100 L/min. With the valve V1 and the ejector E1 ambient air can additionally be drawn in. Valve V1 meters a flow through the ejector. The resultant negative pressure draws ambient air through the filter F2, the flow sensor S2 and the non-return valve V9. Valve V2 adds oxygen to the ambient air depending on the preset O2 concentration. The flow sensor S2 measures the intake air flow and the Control PCB corrects valves V1 and V2 accordingly.
0000000763_Publication_11.11.09
The proportion of ambient air may be a maximum of 75%. The minimum oxygen concentration may thus be 40%. At flows less than 9 L/min the volume of intake air is so low that an oxygen concentration of 40% is no longer guaranteed. At flows greater than 35 L/min oxygen is added accordingly. An oxygen concentration of 40% is no longer guaranteed.
Oxylog 3000 plus
13
Function descriptions Pneumatic assembly
In a flow range from 9 to 35 L/min an oxygen concentration of 40% to 100% can be set. The non-return valve V9 prevents oxygen escaping into the ambient air. L1 prevents swirling, and ensures a uniform flow and so a constant oxygen concentration. Sensors and safety functions
The flow sensor S1 measures the inspiratory flow inside the unit and the Control PCB corrects the operation of valves V1 to V3 as necessary based on the measured value. The safety valve SV opens at a pressure greater than 80 mbar, or 105 mbar (US version), to prevent the patient from being exposed to high pressure in the event of unit malfunctions. The emergency breathing valve NV allows the patient to breathe spontaneously in case the unit fails. The pressure sensor S4 measures the internal patient pressure inside the unit and the PEEP pressure at the ventilation valve V10. The pressure sensor S6 (Fig. 5) measures the differential pressure above the flow sensor S8 located close to the patient (at the „flap“ a flow-dependent backpressure is created). From it, the Control PCB calculates the flow.
Fig. 5
Functional principle of the external flow sensor
Pressure sensor S5 measures the pressure at the patient. Based on this pressure value, the Control PCB makes calculations including for actuation of the PEEP valve V6. Valves V7 and V8 switch the connections of S6, S5 against atmosphere at cyclic intervals. The Control PCB thus defines the zero point of the sensors and any offset drift is prevented. PEEP valve
The PEEP valve V6 controls the PEEP setting of the ventilation valve V10.
This PEEP pressure also acts on a valve diaphragm in the ventilation valve V10 (Fig. 6/1). On expiration the preset PEEP pressure is established at the patient. During expiration an internal flow of 0.5 L/min flows through the PEEP valve V6 to hold the diaphragm of the PEEP valve still and ensure uniform opening of the PEEP valve.
14
Oxylog 3000 plus
0000000763_Publication_11.11.09
The Control PCB actuates a coil which delivers a pressure to a diaphragm. The internal tubing system vents to this preset PEEP pressure during expiration.
Function descriptions Pneumatic assembly
During inspiration the PEEP valve V6 is closed by an actuation current of 130 mA.
Fig. 6 Ambient pressure conditions
Ventilation valve
The device meters the tidal volume under BTPS (Body Temperature, Pressure, Saturated) conditions. Measurements referred to conditions of the patient's lung, body temperature 37 °C, ambient pressure, water vapor saturated gas). Sensors S7 and S9 measure the ambient pressure. S5 measures the current pressure level in the lung. In this way the Control PCB can balance fluctuating ambient pressure and the BTPS conditions.
Connections and interfaces
Fig. 7
Pneumatic connections
0000000763_Publication_11.11.09
Item
Designation
1
Connections for the flow measurement tubes
2
Ventilation tube outlet
3
Compressed O2 inlet
Oxylog 3000 plus
15
Function descriptions Electronic assembly
Electronic assembly
Introduction
The following details the functioning of the device's electronic components. The components are used to record electrical measurements and presets, and to control the screen display and the pneumatics.
Design
Fig. 8
Overview of electronic components Item
Designation Front panel with membrane cover, potentiometers, rotary knob, display, loudspeaker and alarm generator
2
Control PCB
3
Sensor PCB
4
Charging Circuit PCB
0000000763_Publication_11.11.09
1
16
Oxylog 3000 plus
Function descriptions Electronic assembly
Functional principle
Fig. 9
Electronics block diagram Charging Circuit PCB
The Charging Circuit PCB controls charging of the internal rechargeable battery and selection of the voltage supply (mains, on-board system or internal battery). The Charging Circuit PCB accommodates the input for the external voltage supply. The input is isolated from the remaining electronics by a protective circuit. The Charging Circuit PCB directly (via the Control PCB) activates the power indicator LEDs. The LEDs are located on the front membrane cover.
0000000763_Publication_11.11.09
The Charging Circuit PCB has its own processor system, and thus its own software. This software is also located on the Control PCB, and is loaded from there onto the Charging Circuit PCB. The internal rechargeable battery is a lithium-ion battery. The Charging Circuit PCB detects this battery. The temperature and charge capacity of the internal rechargeable battery is determined by the battery itself. These data are transmitted from the Charging Circuit PCB to the Control PCB.
Oxylog 3000 plus
17
Function descriptions Electronic assembly
Sensor PCB
The Sensor PCB holds all the pressure sensors of the pneumatic system and the internal temperature gauge. The Sensor PCB is the interface for pressure measurement and valve actuation between the pneumatic and electronic systems.
Front membrane cover
On the front membrane cover are the keys and LEDs. The potentiometers and the rotary knob are attached to the front membrane cover. Together with the display, the rotary knob and the potentiometers, the front membrane cover is the interface between the unit and the operator. The display is an EL display. EL stands for electroluminescent.
Control PCB
The Control PCB holds the electronic ON/OFF switch components, the voltage generation of the individual internal operating voltages, and the microprocessor system for control and monitoring of ventilation. The electronic ON/OFF circuit is directly controlled by the ON/OFF switch on the unit. The unit is switched on and off accordingly. If the unit is ON and the power fails, an alarm generator generates an audible alarm signal. A Goldcap capacitor delivers the voltage for the signal. The voltage generator generates the various operating voltages from the supply voltage. For example the +5 V for the microprocessor. The microprocessor system comprises the microcontroller, an EEPROM, a flash EPROM, a RAM, and a real-time clock (RTC). The EEPROM holds the calibration data, software options, ID number, unit and service operating hours and the start-up conditions. The flash EPROM holds the medical device firmware and the software for the Charging Circuit PCB. The real-time clock generates the time and date. The real-time clock's RAM also holds the logs. The microprocessor system evaluates the measurement signals from the sensors, the settings of the potentiometers and the rotary knob and operates the valves and the display accordingly. Software is downloaded, and other devices, e.g. a monitor, are connected, by way of the serial service port.
0000000763_Publication_11.11.09
The CO2 sensor is connected by an RS232 interface (plus power supply) to the device and measures the expiratory CO2 content of the respiratory gas (see also function description"MCable-Mainstream CO2 sensor M11.1").
18
Oxylog 3000 plus
Function descriptions Electronic assembly
Connections and interfaces
Fig. 10
Electronic connections Item
Designation Serial port
2
Power supply connection
3
CO2 sensor connection
0000000763_Publication_11.11.09
1
Oxylog 3000 plus
19
Function descriptions MCable-Mainstream CO2 sensor M11.1
MCable-Mainstream CO2 sensor M11.1
Introduction
The MCable-Mainstream CO2 sensor M11.1 measures the CO2 content in the respiratory gas. The following section describes the design and function of the MCable-Mainstream CO2 sensor.
Design
Fig. 11
MCable-Mainstream CO2 sensor Item
Principle
Designation
1
Connector
2
Test filter
3
CO2 sensor
The CO2 measurement is based on the principle that CO2 molecules absorb light at a specific wavelength. Light at a wavelength of around 4.26 μm is strongly absorbed by the CO2 molecule. Light at a wavelength of around 4.13 μm is virtually not absorbed.
Beam path
20
The beams emitted from the light source (9) are reflected by a parabolic reflector (8), travel through the cuvette (7), and reach a filter/reflector (5). The filter/reflector allows light at a wavelength of 4.13 μm to pass through, but reflects the other wavelengths. The light at a wavelength of 4.13 μm is bundled by a parabolic reflector (3) and sent to a detector (2).
Oxylog 3000 plus
0000000763_Publication_11.11.09
Function