Instructions for Use
88 Pages
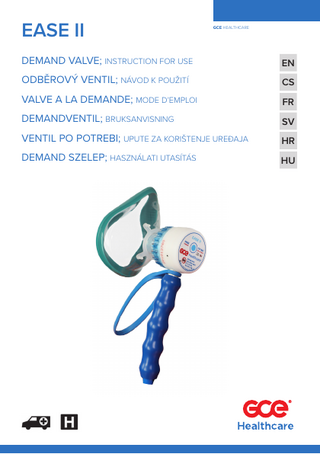
Preview
Page 1
EASE II
GCE HEALTHCARE
DEMAND VALVE; INSTRUCTION FOR USE
EN
ODBĚROVÝ VENTIL; NÁVOD K POUŽITÍ
CS
VALVE A LA DEMANDE; MODE D’EMPLOI
FR
DEMANDVENTIL; BRUKSANVISNING
SV
VENTIL PO POTREBI; UPUTE ZA KORIŠTENJE UREĐAJA
HR
DEMAND SZELEP; HASZNÁLATI UTASÍTÁS
HU
ENGLISH
INSTRUCTION FOR USE: EASE II 1. FOREWORD GCE EASE II low pressure medical demand valves are medical devices classified as class IIa according to the Medical Device Directive 93/42/EEC. Their Compliance with essential requirements of 93/42/EEC Medical Device Directive is based upon BS 4272:1996 standard.
2. INTENDED USE The GCE EASE II low pressure demand valve is designed to be fitted to medical gas pipeline systems or to quick connector outlet of medical gas regulator. EASE II demand valves are intended to be used under supervision for the administration of a medical gas in response to the patient´s inspiratory effort. The EASE II Demand valve is intended for use in the administration of the following medical gases in the treatment and care of patients and is suitable for use in the hospital or pre-hospital (emergency medical) environments: • Oxygen O2 • Nitrous oxygen mixture O2/N2O - 50/50%
3. OPERATIONAL, TRANSPORT AND STORAGE SAFETY REQUIREMENTS Keep the product and its associated equipment away from: • • • • •
heat sources (fire, cigarettes,...) flammable materials, oil or grease (take a great care in the use of hand creams), water, dust.
The product and its associated equipment must be prevented from falling over. Always maintain oxygen cleanliness standards. Use only the product and its associated equipment in well ventilated area. Before initial use the product shall be kept in its original packaging. GCE recommends use of the original packaging (including internal sealing bag and caps) if the product is withdrawn from operation (for transport and storage). Statutory laws, rules and regulations for medical gases, accident prevention and environmental protection must be observed. STORAGE AND TRANSPORT CONDITIONS
OPERATING CONDITIONS MIN
MAX
O2
-20 °C
+60°C
O2/N2O
+5 °C
+60°C
10 % 600 mbar
MIN
MAX
-30 °C
+60 °C
100 %
20 %
70 %
1200 mbar
600 mbar
1200 mbar
3/88
EN
In case of storage at a temperature below -20 °C or above 60°C do not operate the demand valve until it has been allowed to change its temperature inside operating temperature limits. For the demad valve intended to be used with mixture of gases O2+N2O, the lowest operating temperature is +5°C.
EN
Do not use the device without being properly trained! All gases under pressure can be hazardous and should be treated with caution. Do NOT use oil or grease (unless specifically approved) on any part of an EASE II system. Ensure hands are clean and free from oil and grease. Keep system away from sources of ignition at all times. Do NOT tamper with the equipment. Do NOT try to connect an EASE II valve to terminal unit/quick connector of the incorrect gas type.
4. PERSONNEL INSTRUCTIONS The Medical Devices Directive 93/42/EEC states that product provider must ensure that all personnel handling the product are provided with the operating instructions & performance data. Do not use the product without properly familiarization of the product and its safe operation as defined in this Instruction for use. Ensure user is aware of particular information and knowledge required for the gas in use.
5. PREPARATION FOR USE 5.1. CONNECTION OF THE HOSE TO THE GAS SOURCE • Connect the supply hose to the source of gas. For more information regarding gas - specific medical quick connectors, see to Appendix 2. • Regularly inspect the hose during use to ensure that the hose is not torn, bent, twisted, or affected by excessive pull. • Regularly check the supply of gas or the contents in the cylinder.
5.2. FITTING SCAVENGING ADAPTOR
Scavenging adaptor
Mask Antibacterial filter
Test button
Fig. 1: Fitting scavenging adaptor, filter and mask
• When using the scavenging adaptor, fit it to the demand valve by pushing it over the patient port. (see Fig. 1). • Then connect the exhalation pipe to scavenging adaptor. NOTE: A scavenging adaptor should be fitted when EASE II for O2/N2O is used in enclosed spaces. Failure to fit a scavenging adapter can result in supervisory personnel becoming drowsy. 4/88
5.3. FITTING MASK OR MOUTHPIECE AND FILTER Select mask or mouthpiece and filter as appropriate for the patient and fit to the demand valve by pushing it over the 22 mm insert female tapered outlet on the patient port (see Fig. 1). NOTE: Some patients find masks claustrophobic and may fight against the use of EASE II if offered in this way. With such patients use of a mouthpiece is recommended.
5.4. TESTING PRIOR TO ADMINISTRATION Units should be checked by lightly pressing the test button (see fig 1., fig.2). Gas should be heard flowing through the mask or mouthpiece. On releasing the test button, the flow should stop. NOTE: If the system does not operate i.e. does not give a gas flow on depressing the test button or the system does not stop giving flow, turn off the cylinder or disconnect from the gas source and refer to the TROUBLESHOOTING chart in Section 9.
6. OPERATIONS 6.1. ADMINISTERING OF MEDICAL GASES Medical gases 50/50% O2/N2O or 100 % O2 should only be administered by persons trained to do so and under qualified medical supervision. Cylinder contents must be checked regularly during therapy and the cylinder replaced as necessary. 1. Calmly explain to the patient purpose and operation of the demand valve. Reassure and encourage him/her to breathe normally. NOTE: Patients do not have to remove the mask or mouthpiece during exhalation. 2. Place the mask on the patient and support the mask over the mouth and nose, with the patient breathing normally and not remove the mask when exhaling. NOTE: If a mouthpiece is fitted, instruct them to hold it between their teeth, sealing on it with their lips and to breathe through their mouth only. 3. Instruct the patient to breathe through the demand valve as required to reduce the level of pain. (Continuous use is often unnecessary). NOTE: Supervisory personnel can help support the mask, if should the patient is incapable of holding it. 4. Constantly monitor the patient and the cylinder contents during administration. Check volume of gas in the cylinder and replace the cylinder if necessary. 5. The administration of 50/50 O2/N2O may cause the patient to become drowsy. The seal between the mouth and the demand valve will be lost and ambient air will be inhalated. The patient will then begin to regain consciousness and an awareness of pain; and should be encouraged to breathe the gas again.
6.2. AFTER USE 1. When treatment has been completed, close the cylinder valve and operate the test button to de-pressurize the system or disconnect the demand valve from the wall outlet or quick connector. 2. Clean the system as described in Section 7.
5/88
EN
7. CLEANING De-pressurize the system and disconnect from the gas supply prior to cleaning. Refer to the exploded view of the demand valve parts below. Inhalation disc
Demand Valve
EN
U-clip
Patient port assembly
Fig. 2: Demand valve parts
Fig. E
Fig. 3: Dismantling of EASE II before cleaning
6/88
Do not use cleaning solutions containing ammonia! Do not expose to water or any other liquid. Do not expose to high temperature (such as autoclave), unless it is stated otherwise. To apply the cleaning solution do not spray it as the spray may enter into the inner parts of demand valve and cause contamination or damage. Do not use pressure wash as it could damage or contaminate the demand valve. If the inner parts of the demand valve have been contaminated do not continue to use the demand valve under any circumstances. It must be withdrawn from service.
7.1. CLEANING THE INHALATION DISC AND PATIENT PORT ASSEMBLIES If an filter is used and bodily fluids have not contaminated the demand valve, only wiping the demand valve with a disinfectant is necessary. Remove dirt with a soft cloth damped in oil free soap water & rinsed with clean water. If demand valve has been contaminated by secretions, blood, or vomit, then cleaning as outlined below is necessary. 1. Unscrew the patient port assembly from the demand valve (Fig. A) and remove the inhale disc assembly (Fig. B). 2. Remove the silicone valve flaps from the patient port and inhale disc (see Fig.C,D). Take care not to overstretch or damage these parts during removal. 3. If an antibacterial filter is used, cleaning is not necessary after every use. However, recommended. If demand valve has been contaminated by blood or vomit, the cleaning is necessary. Follow one of cleaning procedures bellow according to your preference: a. Either wash all parts with warm water at a maximum temperature of 60°C, use an approved disinfectant. The mechanical resistance of the components (Patient port, Inhale disc, Inhale valve flap, Exhale valve flap), are guaranteed to 20 sterilization cycles under the cleaning conditions mentioned below. Example of cleaning with cold disinfectant: Meliseptol: Remove dirt with a soft cloth damped in warm water with max. duration 30 seconds. Disinfection apply on the components (application of disinfectant for 1 minute). After applying the disinfection, clean the components in running cold tap water. The components shall be carefully dried with a soft non-abrasive cloth. b. Or put the parts in an autoclave for 5 min at 134° C or for 20 min at 121° C. After the cycle is complete, wait until parts get cool and check for damage. Assembly the device (see section 5). The mechanical resistance of the components (Patient port, Inhale disc, Inhale valve flap, Exhale valve flap), are guaranteed to 20 sterilization cycles under the cleaning conditions mentioned above. Later, the degradation of plastic substances may occur.
7.2. DISASSEMBLY OF THE DEMAND VALVE 1. Unscrew the patient port assembly from the demand valve (Fig. A) and remove the inhalation disc assembly (Fig. B). 2. Remove the silicone valve flaps from the patient port and inhalation disc (see Fig.C,D). Take care not to over-stretch or damage these parts during removal.
7.3. CLEANING THE DEMAND VALVE DO NOT immerse the demand valve in disinfectant liquids. 1. Clean external surfaces of the valve with a lint-free cloth, slightly moistened in soapy water. Dry with a lint-free cloth. 2. Disinfect the outer surface. 3. If the hose connection to the demand valve is contaminated, remove the hose from the demand valve (see Chapter 7.4). Clean and dry the hose with a lint free cloth. Clean the hole in the demand valve carefully with cotton moistened with clean water and disinfect. 4. If a demand valve suffers internal contamination and normal cleaning is not effective, the valve must be returned for servicing by a qualified technician. 7/88
EN
7.4. REMOVING & REFITTING THE HOSE FROM THE DEMAND VALVE BODY
EN
To remove the hose from the Demand Valve proceed as follows: 1. Disconnect EASE II from its gas supply and de-pressurize the system fully. If in any doubt, contact Training and Technical Support Services at the address shown above. 2. Remove the patient port and inhalation disc assemblies. See fig 3 above. 3. Lift and remove the U-clip using a small screwdriver. See fig 2 above. 4. Pull the hose from the demand valve. Protect the hose connector from dirt and damage. 5. Reassembly is the reverse of the removal procedure. When refitting the U-clip ensure it is fully seated. 6. Refit the patient port and inhalation disc assemblies.
7.5. CLEANING THE MASK, MOUTHPIECE, SCAVENGING ADAPTER 1. Masks for multiply use clean or sterilize according to the manufacturer’s instructions attached to the mask. Masks for single use must be disposed after use. 2. The mouthpieces are single use only. Dispose of mouthpiece after use. 3. Scavenging adaptor can be washed in warm water (max 60°C) using approved disinfectantwater and rinsed in clean water, or autoclaved at 121°C as preferred.
7.6. CLEANING HOSE ASSEMBLY Hose assembly must be cleaned if contaminated or as part of regular cleaning. It is not necessary to clean it after every use. 1. De-pressurize hose assembly and disconnect from the gas supply. 2. The external surfaces should be cleaned using a lint-free material moistened with soapy water. Dry with a lint free material. 3. To disinfect, thoroughly wipe the outer surfaces with a disinfectant wipe. 4. Re-assemble the system and test according to the instructions in Chapter 7.7. Please ensure that no disinfectant enters the hose, as there is risk of respiratory injuries.
7.7. RE-ASSEMBLY OF EASE II AND TESTING AFTER CLEANING 1. Fit the hose back as described in section 7.3. if removed. 2. Place the inhalation flap back on the inhalation disc. Make sure the rim is placed over the inhalation disk and letters “THESE WORDS VISIBLE” are up and readable - see Fig. C. 3. Place the inhalation disc assembly into the demand valve see Fig. B and D. 4. Place the exhalation flap into the patient port, make sure the rim is placed upward - see Fig. D. 5. Screw the patient port onto the demand valve - see fig. A. 6. Test EASE II according to section 5.4. and use according to section 6. NOTE: For cylinders with a regulator, it is recommended that the regulator be attached to the cylinder, but with the cylinder turned OFF.
8/88
8. MAINTENANCE 8.1. REGULAR CHECKS AND ROUTINE MAINTENANCE 1. The cylinder contents and the operation of the system must be checked regularly and prior to use, as described in Sections 6.2. 2. Before each use, perform an audible and visual check on the hose for leaks and damage. If a leak is detected, or if there is damage, such as cracks or abrasion in the hose outer cover the hose must be replaced. Return the complete unit to an approved repairer for hose replacement. 3. The following components must also be checked on a regular basis for wear and tear and may be replaced by the user as required: • Inhalation disk • Inhalation valve flap • Patient port • Exhalation valve flap NOTE: Follow the instructions in Section 7 to change the Inhalation disc, Inhalation flap, patient port and exhalation valve flap. Observe the oxygen cleanliness warnings given in Section 4 when changing the cylinder seal. All labels on the EASE II must be kept in good, legible condition by the owner and the user during the entire product life time, replace as necessary. All spare components must be kept in their original packaging to maintain batch / suppliers identity. All spare components must be stored in a dry, dark and clean environment by the owner/ user. Use only original GCE components!
8.2. ANNUAL INSPECTION EASE II must be inspected annually. No special tools or test equipment are required for the annual inspection. The annual inspection may be carried out by the user or an approved GCE repairer. Records of the annual inspection must be made and held for the life of the product. See Chapter 8.3. for the annual inspection procedure and section 14 for an example of annual inspection record sheet. If components other than those listed in section 8.1 require replacing, the Demand Valve complete with hose assembly must be returned to an approved GCE repairer for the work to be carried out, as special tools and test equipment are required. GCE approved repairers are trained by GCE to carry out servicing in accordance with the GCE Service Manual. A Service Manual with service and test equipment is available from GCE, s.r.o. GCE, s.r.o. Tel: +420 569 661 111 Zizkova 381 Fax: +420 569 661 602 583 01 Chotebor http://www.gcegroup.com
9/88
EN
8.3. ANNUAL INSPECTION PROCEDURE 8.3.1. VISUAL INSPECTION
EN
Step
Procedure
Comment/Action
1
Depressurize and disconnect the demand valve from the pressure supply
Use the test button on the back of the EASE valve to depressurize the demand valve and hose if required
2
Check the demand valve serial number is legible
If the serial number is not legible the demand valve should be removed from service
3
Check the demand valve has not exceed its 10 year life period
The first four digits of the serial number is the year of manufacture. If the date at the time of inspection is more than 10 years after the manufacturing year the Demand Valve should be removed from service and disposed of. See 8.4.
4
Check the hose has no damage to its outer cover such as cuts, or significant abrasions.
The hose will require replacing if it has cuts, or significant abrasions in its outer cover. Send the demand valve to an approved GCE repairer for hose replacement.
5
Check that the hose is not kinked or missshaped.
A kinked or miss-shaped hose indicates the hose reinforcement has been damaged and the hose should be replaced. Send the demand valve to an approved GCE repairer for hose assembly replacement.
6
If the hose is the type which connects to a pipeline terminal outlet check the metal probe connector is not damaged or worn.
A worn or damaged metal probe connector may leak and should be replaced. Send the demand valve to an approved GCE repairer for hose assembly replacement.
7
Check the Demand Valve body and rear cap is not cracked or damaged.
If cracks or significant damage is evident on the valve body or the rear cap the Demand Valve should be withdrawn from service.
8
Check the three small grub screws securing the Demand Valve rear cap to the main body are in place.
If any of the grub screws are missing return the Demand Valve to an approved GCE repairer.
9
Check the label on the rear cap is in place and in good condition
If the label needs replacing send the demand valve to an approved GCE repairer for label replacement.
10
Unscrew patient port assembly from main valve body and remove exhalation valve flap from the patient port.
See section 7 for further information on disassembly procedure
11
Check patient port for cracks or damage.
Replace patient port if damaged
12
Examine the exhalation valve flap for tears and splits
Replace exhalation valve flap if required
13
Refit exhalation valve flap to patient port.
See section 7 for further information on refitting procedure
14
Lift inhalation disc assemble out of the Demand Valve body. Remove inhalation valve flap from the inhalation disc.
See section 7 for further information on disassembly procedure
15
Examine the inhalation disc and pin. Check the inhalation disc is flat. Check the pin is not bent and is sitting square to the inhalation disc.
Replace inhalation disc (with pin) if required
10/88
16
Examine the inhalation valve flap for tears and splits.
17
Refit inhalation valve flap to inhalation disc.
18
Refit inhalation disc assemble to the Demand Valve body. Note the pin should slide easily inside the hole in the Demand Valve body
19
Refit patient port assemble to the Demand Valve body.
Replace inhalation valve flap if required
EN Screw on hand tight only.
8.3.2. LEAK TESTING Step
Procedure
Comment/Action
1
Connect the demand valve to gas supply
Gas will briefly flow as the Demand Valve is connected to the gas supply, this is normal.
2
Using a suitable leak detection fluid check for leaks at:
The leak detection fluid should be compatible with oxygen and suitable for use on plastic components.
3
The joint between the hose and hose fittings at each end of the hose.
If a leak is found return the Demand Valve to an approved repairer for hose replacement.
4
The swivel joint between the Demand Valve body and the hose fitting.
If a leak is found return the Demand Valve to an approved repairer for repair.
5
The connection between the hose probe and the gas supply point.
If a leak is found here it may be due to a worn male hose probe or a fault in the gas supply connection. To eliminate gas supply connection try a different supply point. If leak continues hose assembly will require replacement. Return the Demand Valve to an approved repairer if the hose needs replacing.
6
Unscrew the patient port assembly from the Demand Valve body and lift out the inhalation disc assembly.
7
While the Demand Valve is connected to the gas supply hold the Demand Valve body close to your ear (with outlet holes towards your ear) and listen for leaks. No leaks should be heard.
8
Refit the inhalation disc assemble to the Demand Valve body.
9
Refit patient port assemble to the Demand Valve body.
If a leak can be heard it indicates a fault with either the main valve or pilot valve. Return the Demand Valve to an approved repairer for repair.
Screw on hand tight only.
8.3.3. DEMAND VALVE OPERATION TESTING Step
Procedure
Comment/Action
1
Connect hose to gas supply.
Test gas may be air, nitrogen, oxygen or N2O/O2 mixture.Gas will briefly flow as the Demand Valve is connected to the gas supply, this is normal.
2
Press the test button. Gas should flow when the button is pressed and stop flowing when the button is released.
If gas flows when the button is not pressed the Demand Valve is faulty and should be returned to an approved repairer for repair.
11/88
8.4. PRODUCT LIFE TIME
EN
8.4.1. PRODUCT LIFE TIME AND WASTE MANAGEMENT Maximum life time of the product is 10 years. At the end of the product’s life time, the product must be withdrawn from service. The owner shall put in place a relevant procedure to ensure the product cannot be used again. The owner of the device shall prevent the reuse of the product and handle the product in compliance with “Directive of European Parliament and Council 2008/98/EC on waste“. In accordance to Article 33 of REACH GCE, s.r.o. as responsible manufacturer shall inform all customers if materials containing 0.1% or more of substances included in the list of Substance of Very High Concern (SVHC). The most commonly used brass alloys used for bodies and other brass components contain 2-3% of lead (Pb), EC no. 231-468-6, CAS no. 7439-92-1. The lead will not be released to the gas or surrounding environment during normal use. After end of life the product shall be scrapped by an authorized metal recycler to ensure efficient material handling with minimal impact to environment and health. To date we have no information that indicates that other materials containing SVHC of concentrations exceeding 0.1% are included in any GCE product. 8.4.2. SERIAL NUMBER AND DATE OF PRODUCTION Form of nine digit serial number stamped on the product is following: YY MM XXXXX YY: year of production MM: month of production XXXXX: sequence number Example: serial number 090300521 shows the product produced in March 2009, with sequence number 521.
9. TROUBLESHOOTING The table below is provided as a means of correcting simple faults with the equipment. If the suggested remedies do not rectify the fault, the equipment must be returned for inspection and rectification by trained personnel who have completed the relevant training course (see Section 8.2). Symptoms
Equipment does not deliver gas.
Demand valve leaks or does not shut cleanly. Demand valve does not stop giving flow after test button is released.
Possible Cause
Corrective Action
Cylinder valve not turned on.
Check and turn on cylinder.
Cylinder empty.
Check contents gauge. Fit a new cylinder if necessary.
Quick coupling is not fully connected.
Remove probe and re-fit to adaptor, ensuring that it is fully engaged.
Exhalation valve flap missing.
Fit a new exhalation valve flap.
Adjustment incorrect.
Refer to Service Manual
Inhalation disc warped / damaged.
Fit a replacement inhalation disc
Incorrect adjustment.
Refer to Service Manual
12/88
10. SPECIFICATION Demand Valve - Meets the requirements of BS 4272: part 2: 1996 Gas Connection
Probes by the national standards
Gas Supply
Requirement 2.8 to 7.0 bar at >200 L/min
Inspiratory Resistance (at 2.8 bar Supply Pressure)
Cracking -0,15 to -0,2 kPa -0,2 kPa at 10 L/min. -0,7 kPa at 200 L/min.
Expiratory Resistance
Cracking Zero At flow +0,35 kPa at 120 L/min.
Operating Temperature
-20°C to +60°C when used with oxygen +5°C to +40°C when used with 50/50 O2/N2O
Storage Temperature
-30°C to +60°C
Materials
Polyacetal; Polycarbonate; silicone rubber; stainless steel
Weight / Size Envelope
85 g / 50 x 50 x 63 mm
Hose Assembly Fittings
Probes by the national standards.
Pressure
Working pressure 7 bar, Burst pressure ≥56bar/23°C and ≥40bar/40°C
Material
PVC, anti-static in accordance with ISO 5359
Weight
0.5kg (3m length)
Size Envelope
OD 12,7 mm
NOTE: Values quoted are nominal. The manufacturer reserves the right to change specifications without notice. Spare Parts and Accessories
10.1. ACCESSORIES PROVIDED WITH EASE II EASE II O2/N2O demand valve are typically used with a mask, mouthpieces, filter, cylinder thermometer and scavenging adaptor. EASE II Oxygen demand valves are typically used with a mask, mouthpieces and filter. Accessories, which is marked as disposable, or “single patient use” must not be used repeatedly. The GCE medical range of products is constantly being developed and improved. If you require any information or assistance, please telephone our Customer Services department. Contact is enclosed on last page of this manual.
10.2. OPTIONAL ACCESSORIES Those items marked by * are not manufactured by GCE. • Bag, complete with cylinder cradle, • Barrel bag blue, • Cylinder cradle only, • Disposable mouthpice - (Pack of 5)*, • Filter single use (Pack of 100)*, • Single use mask* • Reusable mask* • Thermometer for N2/N2O cylinders* • Expiration diverter (Pack of 1)* • Scavenging adapter (Expiration diverter)* • Disposable filter* 13/88
EN
11. GLOSSARY Consult instructions of use Suitable for Hospital care use
EN
Caution Keep away from heat and flammable material
Suitable for Emergency care use
Keep away from oil and grease
SN
Serial number
Temperature limit
REF
Catalogue number
Keep dry
LOT
Batch code
Humidity limit
Date of manufacture
Manufacturer
Fragile, handle with care
Use by date
Inlet pressure (P1)
Outlet pressure (P2)
12. WARRANTY The Standard Warranty period is two years from date of receipt by the GCE Customer (or if this is not known 2 years from time of the product manufacture shown on the product). The standard warranty is only valid for products cu according to Instruction for use (IFU) and general industry good practice and standards.
13. SAMPLE ANNUAL INSPECTION RECORD SHEET Please copy this form to help with your EASE II annual checks. See section 8.3 for details of the annual inspection procedure. COMPANY
VISUAL CHECK
Demand Valve SERIAL NUMBER
TICK
Check serial number legibility Check demand valve is less than 10 years old Check hose condition
14/88
COMMENTS / ACTION TAKEN
Check body condition Check label condition Check the three recap screws are in place
EN
Check patient port condition Check exhalation valve flap condition Check inhalation plate (with pin) condition Check inhalation valve flap condition LEAK CHECKS
TICK
Comments / Action Taken
TICK
Comments / Action Taken
Hose to hose fitting joints (use leak detection fluid) Hose to demand valve body joint (use leak detection fluid) Leak test Demand valve (listening for leak with patient port and inhalation disc removed) OPERATION CHECKS Test button operation Tested By:
Date:
APPENDIX: Nr 2: Quick coupling features and connecting / disconnecting procedure. MANUFACTURER: GCE, s.r.o. Zizkova 381 583 01 Chotebor Czech Republic
Tel: +420 569 661 111 Fax: +420 569 661 602 http://www.gcegroup.com © GCE, s.r.o. 15/88