GE Healthcare
Broad-spectrum micro- convex biopsy transducer 80º 1-6 MHz
Addendum for Cleaning and Disinfection
1794 Pages
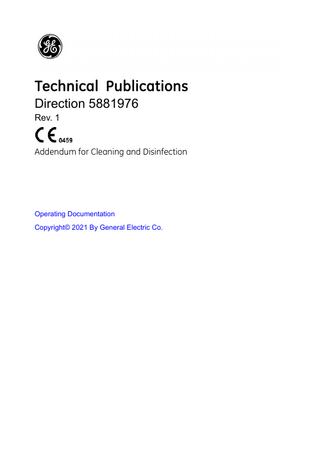
Preview
Page 1
Technical Publications Direction 5881976 Rev. 1
Addendum for Cleaning and Disinfection
Operating Documentation Copyright© 2021 By General Electric Co.
Regulatory Requirement This product complies with regulatory requirements of the following European Directive 93/42/EEC concerning medical devices.
This manual is a reference for the LOGIQ S8, LOGIQ E8 and LOGIQ S7 XDclear2.0. It applies to all versions of the LOGIQ S8, LOGIQ E8 and LOGIQ S7 XDclear2.0 ultrasound system.
GE P.O. Box 414, Milwaukee, Wisconsin 53201 U.S.A. (Asia, Pacific, Latin America, North America) GE Ultraschall: TEL: 49 212.28.02.207 Deutschland GmbH & Co. KG: FAX: 49 212.28.02.380 Beethovenstrasse 239 Postfach 11 05 60 D-42655 Solingen GERMANY
Revision History Reason for Change DATE (YYYY/MM/DD)
REV Rev. 1
2021/10/29
REASON FOR CHANGE Initial release
List of Effective Pages
PAGE NUMBER
REVISION NUMBER
PAGE NUMBER
REVISION NUMBER
Title Page
Rev. 1
Regulatory Requirements
Rev. 1
Revision History
Rev. 1
Addendum
Rev. 1
Please verify that you are using the latest revision of this document. Information pertaining to this document is maintained on MyWorkshop. If you need to know the latest revision, contact your distributor, local GE Sales Representative or in the USA call the GE Ultrasound Clinical Answer Center at 1 800 682 5327 or 1 262 524 5698.
Addendum for Cleaning and Disinfection Direction 5881976 Rev. 1
i-1
This page intentionally left blank.
i-2
Addendum for Cleaning and Disinfection Direction 5881976 Rev. 1
Regulatory Requirements
Authorized EU Representative European registered place of business: GE Medical Systems SCS 283 rue de la Minière 78530 BUC, France
Manufacturer GE Ultrasound Korea, Ltd. 9, Sunhwan-ro 214beon-gil, Jungwon-gu, Seongnam-si, Gyeonggi-do, KOREA
Full Listing For a full listing of regulatory requirements, see Table i-1: Product Name and Software version
Basic User Manual Direction number
LOGIQ S8 R1
5340705-1XX/5433845-1XX
LOGIQ S8 R2
5457578-1XX
LOGIQ S8 R3
5501921-1XX
LOGIQ S8 R4
5747566-1XX
LOGIQ S7 XDclear2.0 R4
5836006-1XX
LOGIQ E8 R2
5454477-141
LOGIQ E8 R3
5654239-141
LOGIQ E8 R4
5761723-141
Addendum for Cleaning and Disinfection Direction 5881976 Rev. 1
i-3
i-4
Addendum for Cleaning and Disinfection Direction 5881976 Rev. 1
Chapter 1 Addendum for Cleaning and Disinfection ATTENTION LOGIQ S8 Version R1 or later, LOGIQ E8 and LOGIQ S7 XDclear2.0 USERS: This document contains information concerning the use of your ultrasound system. Precautions and instructions are included that supplement the Basic User Manual and address specific concerns related to software Version cited above. Keep this document with the Basic User Manual and have all users become familiar with its contents and organization before using your system under this software version.
Addendum for Cleaning and Disinfection Direction 5881976 Rev. 1
1-1
Addendum for Cleaning and Disinfection
Addendum
Overview The content in these Release Notes includes an Addendum to the Basic User Manual. Important system Notes and Workarounds are also provided. Information included in these Release Notes supersedes Basic User Manual content.
Updates Made to the Basic User Manual The following updates/changes have been incorporated into the Instructions for Use:
1-2
•
Update System Care and Maintenance
•
Update Probe Care and Maintenance
Addendum for Cleaning and Disinfection Direction 5881976 Rev. 1
System Care and Maintenance
System Care and Maintenance
Overview The user must ensure that safety inspections are performed at least every 12 months according to the requirements of the patient safety standard IEC 60601-1 (2012). Refer to the Service manual, Chapter 10. Only trained persons are allowed to perform the safety inspections mentioned above. Technical descriptions are available on request. To ensure that the unit constantly operates at maximum efficiency we recommend that the following procedures be observed as part of the customer’s internal routine maintenance program. Contact the local Service Representative for parts or periodic maintenance inspections.
Expected Service Life Description The expected service life for the ultrasound system and probes is identified in this table: Table 1-1:
Expected Service Life
Equipment / Accessory
Expected Service Life
LOGIQ S8/LOGIQ E8/LOGIQ S7 XDclear2.0
The expected service life for the ultrasound system is at least seven (7) years from the manufacturing date under the provision of regular maintenance by authorized service personnel.
Probes
The expected service life for the probes meets or exceeds five (5) years from the date the probe is placed in service, under the provision that the customer follows the care instructions provided on the Probe Care Card / Accompanying Instructions for Use.
Addendum for Cleaning and Disinfection Direction 5881976 Rev. 1
1-3
Addendum for Cleaning and Disinfection Maintenance Schedule Follow this Maintenance Schedule to maintain optimum system function and patient care: Table 1-2:
Maintenance Schedule
Monthly
Weekly
Inspect the following on a monthly basis: • Connectors on cables for any mechanical defects. • Entire length of electrical and power cables for cuts or abrasions. • Equipment for loose or missing hardware. • Control panel and keyboard for defects. • Casters for proper movement and locking operation. • Trackball movement. If the trackball is dusty, please clean it. See ‘Trackball’ on page 1-11 for more information.
Clean the following on a weekly basis. See Basic User Manual for detail.: • System Cabinet • Probe holder If the probe holder is dusty, please clean it. • Gel warmer If the gel warmer is dusty, please clean it. • Air Filters (weekly, or as needed) If the air filter is dusty, please clean it. • Footswitch • B/W Printer • CD/DVD-R Multi Drive
NOTE:
DANGER
Daily Clean the following areas where Cross Contamination can occur: • Monitor • LCD panel and the Touch Panel • Operator Controls Panel • Front and Rear Handles
After Each Patient Clean the following after each patient: • Probe • Biopsy Bracket, as applicable Additionally, Clean any area on the system that has visible contamination from the previous exam. Note: Biopsy Accessories must be cleaned and disinfected or disposed of after each patient. Refer to the Probes Chapter, for probe cleaning and disinfecting instructions.
Frequency of the cleaning and disinfection is depended on environment. Failure to perform required maintenance may result in unnecessary service calls. To avoid electrical shock hazard, do not remove panels or covers from console. This servicing must be performed by qualified service personnel. Failure to do so could cause serious injury. If any defects are observed or malfunctions occur, do not operate the equipment but inform a qualified service person. Contact a Service Representative for information.
1-4
Addendum for Cleaning and Disinfection Direction 5881976 Rev. 1
System Care and Maintenance Cleaning and Disinfecting the system These cleaners/disinfectants can be used anywhere on the console (Operator Panel, Monitor, Probe Holders, etc.), except for the probes. See ‘Probe Care and Maintenance’ on page 1-17 for more information. Always consult the cleaner or disinfectant manufacturer’s instructions for proper use of their product. Wear appropriate PPE as indicated by the manufacturer. Appropriate cleaners/disinfectants for the console that have been validated for compatibility are shown below: Table 1-3: Cleaning/ Disinfectant Agent
Appropriate Cleaning and Disinfectant Agents
LCD Panel (Glass)
Monitor Frame
System Cabinet
Touch Panel
Operator Controls
Mild, Non-Abrasive Soap and Water
OK
OK
OK
OK
OK
Ammonia
N/A
OK
N/A
N/A
N/A
<Disinfectant> Bleach (10 to 1 Ratio of 5% Home Bleach)
N/A
OK
N/A
N/A
OK
<Cleaner/ disinfectant> Hydrogen Peroxide / Hydrogen Peroxide Wipes
N/A
OK
N/A
N/A
N/A
For Blue-based system; Other recommended Cleaner/ Disinfectants
N/A
N/A
N/A
N/A
PDI - Super Sani Cloth Clorox - Multi Surface Wipes Hartmann Kohrsolin Extra Hartmann Kohrsolin FF For R4 and later
Addendum for Cleaning and Disinfection Direction 5881976 Rev. 1
1-5
Addendum for Cleaning and Disinfection Table 1-3: Cleaning/ Disinfectant Agent
Appropriate Cleaning and Disinfectant Agents
LCD Panel (Glass)
For Black and Silver based system; Other recommended Cleaner/ Disinfectants
N/A
Notes
Never use thinner, benzene, alcohol (ethanol, methanol, or isopropyl alcohol), abrasive cleaners, or other string solvents, as these may cause damage to the monitor.
Monitor Frame N/A
System Cabinet
Touch Panel
Operator Controls
N/A
N/A
Cleanisept Wipes Clinell Universal Sanitising Wipes Clorox Healthcare Bleach Germicidal Wipes Mikrobac Tissues Mikrozid Sensitive Wipes Sani-Cloth HB Germicidal Disposable Wipe Sani-Cloth Plus Germicidal Disposable Cloth Sani-Cloth Prime Germicidal Disposable Cloth SONO ULTRASOUND WIPES (Super Sani-Cloth Germicidal Disposable Wipes) Tristel Distel Clinell Clorox Wipes Acryl-Des Wipes Protex Ultra Wipes Trophon Companion Cleaning Wipes
Cloth should be damp, not dripping wet.
Cloth should be damp, not dripping wet.
DO NOT USE: Any cleaning/ disinfecting solution BESIDES recommended cleaner.
OK = Available agent, N/A = Not Available
NOTE:
1-6
Effective cleaning for parts with narrow gaps and holes (e.g. Keyboard, trackball...) is not possible. For more information, visit to http://cleaning.gehealthcare.com/.
Addendum for Cleaning and Disinfection Direction 5881976 Rev. 1
System Care and Maintenance
WARNING
All cleaners and disinfectants NOT on this list are unapproved by GE. Failure to follow guidelines could result in damage to the device.
CAUTION
When reprocessing the operator control panel, make sure not to spill or spray any liquid on the controls, into the system cabinet, or in the probe connection receptacle.
CAUTION
To avoid liquids entering the product, DO NOT spray any liquid directly onto the surfaces. ALWAYS use a cloth or wipe.
Addendum for Cleaning and Disinfection Direction 5881976 Rev. 1
1-7
Addendum for Cleaning and Disinfection Cleaning and Disinfecting the system (continued)
1-8
CAUTION
Avoid using ALCOHOL (ISOPROPANOL) 70% inside the trackball. ALCOHOL (ISOPROPANOL) 70% may also compromise the durability of the paint used on the console controls.
CAUTION
Oxivir TB Wipes may compromise the durability of the paint used on the console handles and controls.
Addendum for Cleaning and Disinfection Direction 5881976 Rev. 1
System Care and Maintenance Cleaning the system
CAUTION
Note that the following procedures describe cleaning of the ultrasound system components to a general housekeeping level only. The recommended disinfectants are verified to be chemically compatible with product materials. Prior to cleaning any part of the system turn off the power. If possible, disconnect the power cord. The system includes the System cabinet, Monitor Frame, LCD panel, Touch Panel, Operator Control Panel and Probe Holders. Follow the cleaning frequency suggested in ‘Maintenance Schedule’ on page 1-4.
Monitor Frame To clean the Monitor Frame: 1. Use the cleaner and disinfectant listed in Table 1-3 on page 1-5. Or moisten a soft, non-linting cloth folded cloth with a mild, general purpose, non-abrasive soap and water solution. NOTE:
The cloth should be damp, not dripping wet. 2. Wipe down the top, front, back, and both sides of the monitor. 3. Wipe off excess cleaning agents with a soft, non-linting, and non-abrasive folded cloth and allow to dry.
NOTE:
For disinfection processing, refer to ‘Disinfecting the system’ on page 1-16.
NOTE:
Never use thinner, benzene, alcohol (ethanol or methanol), abrasive cleaners, or other strong solvents, as these may cause damage.
NOTE:
DO NOT scratch or press on the panel with any sharp objects, such as pencils or pens, as this may result in damage to the panel.
Addendum for Cleaning and Disinfection Direction 5881976 Rev. 1
1-9
Addendum for Cleaning and Disinfection LCD Panel and Touch Panel To clean the LCD Panel and the Touch Panel: 1. The surface can be cleaned with a non-linting cloth and soft cloth, such as cloths for cleaning glasses. 2. If necessary, stubborn stains can be removed by moistening part of a cloth with water to enhance its cleaning power. NOTE:
For disinfection processing, refer to ‘Disinfecting the system’ on page 1-16
NOTE:
Never use thinner, benzene, alcohol (ethanol or methanol), abrasive cleaners, or other strong solvents, as these may cause damage.
NOTE:
DO NOT scratch or press on the panel with any sharp objects, such as pencils or pens, as this may result in damage to the panel.
Operator Control Panel To clean the operator control panel: 1. Use the cleaner and disinfectant listed in Table 1-3 on page 1-5. Or moisten a soft, non-linting cloth folded cloth with a mild, general purpose, non-abrasive soap and water solution. NOTE:
The cloth should be damp, not dripping wet. 2. Wipe down operator control panel. 3. Use a cotton swab to clean around keys or controls. Use a toothpick to remove solids from between keys and controls. 4. Wipe off excess cleaning agents with a soft, non-linting, and non-abrasive folded cloth and allow to dry.
NOTE:
For disinfection processing, refer to ‘Disinfecting the system’ on page 1-16
NOTE:
When cleaning the operator control panel, make sure not to spill or spray any liquid on the controls, into the system cabinet, or in the probe connection receptacle.
NOTE:
In case of SARS, use bleach, alcohol, or Cidex in a normal diluted form for cleaning/disinfecting the operator panel.
NOTE:
DO NOT use T-spray or Sani Wipes on the control panel.
CAUTION
1-10
Before cleaning the control panel, make sure the key cap is firmly in place.
Addendum for Cleaning and Disinfection Direction 5881976 Rev. 1
System Care and Maintenance System Cabinet To clean the system cabinet: 1. Moisten a soft, non-linting folded cloth with a mild, general purpose, non-abrasive soap and water solution. NOTE:
The cloth should be damp, not dripping wet. 2. Wipe down the top, front, back, and both sides of the system cabinet. 3. Wipe off excess cleaning agents with a soft, non-linting, and non-abrasive folded cloth and allow to dry.
NOTE:
For disinfection processing, refer to ‘Disinfecting the system’ on page 1-16
NOTE:
Do not spray any liquid directly into the unit.
Trackball 1. Power off the system. 2. Rotate the retainer counterclockwise until it can be removed from the keyboard.
Figure 1-1.
Remove the retainer
3. Separate the trackball and the retainer. Wipe off any oil or dust from the trackball, retainer and the trackball housing using a cotton swab or microfiber cloth.
Addendum for Cleaning and Disinfection Direction 5881976 Rev. 1
1-11
Addendum for Cleaning and Disinfection Trackball (continued) 4. If the Trackball does not move smoothly, you may need to clean the sensor in two places.
Figure 1-2.
CAUTION
Trackball sensor
Gently use the cotton swab to clean the Trackball sensors; avoid using excessive force as this may shift the sensor's position and scratch its lens. 5. Assemble the trackball and retainer, then put it into the housing and rotate it clockwise until its notches are set in position.
CAUTION
1-12
When cleaning, make sure not to spill or spray any liquid into the trackball housing (keyboard or system).
Addendum for Cleaning and Disinfection Direction 5881976 Rev. 1
System Care and Maintenance Prevention of static electricity interference Interference from static electricity can damage electronic components in the system. The following measures help to reduce the likelihood of electrostatic discharge: •
Wipe the alphanumeric keyboard and monitor with lint-free tissue or a soft cloth dampened with anti-static spray on a monthly basis.
•
Spray carpets with anti-static spray because constant walking on carpets in or near the scanning room may be a source of static electricity.
Addendum for Cleaning and Disinfection Direction 5881976 Rev. 1
1-13
Addendum for Cleaning and Disinfection Probe Cleaning Refer to ‘Probe Care and Maintenance’ on page 1-17, for probe cleaning and disinfecting instructions. NOTE:
CAUTION
The image of the system that is shown in this section could look different from the real system. NEVER use any cleaner or disinfectant containing alcohol.
When cleaning/disinfecting probes using a spray cleaner/ disinfectant, DO NOT spray the probe while the probe is set in its probe holder on the Ultrasound system. Overspray can damage the TGC controls.
Figure 1-3.
1-14
DO NOT Spray a Probe While in its Holder
Addendum for Cleaning and Disinfection Direction 5881976 Rev. 1