Operator Manual
108 Pages
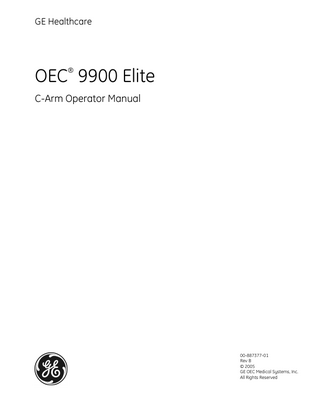
Preview
Page 1
GE Healthcare
OEC 9900 Elite ®
C-Arm Operator Manual
00-887377-01 Rev B © 2005 GE OEC Medical Systems, Inc. All Rights Reserved
Revision History Rev 1 A B
Dash -01 -01 -01
Date November 2004 June 2005 November 2005
Change Description Engineering Release Manufacturing Release Editorial Changes
CAUTION US Federal law restricts this device to sale by, or on the order of, a physician. IMPORTANT SAVE THESE INSTRUCTIONS. . PLEASE READ THIS MANUAL BEFORE USING EQUIPMENT. The text of this manual was originally written, approved and published by the manufacturer in English. This manual may not be reproduced, in whole or in part, without the written permission of GE Healthcare. Other product and company names mentioned herein are the property of their respective owners. The contents of this document are accurate at the time of publication. However, changes in design and additional features can, at any time, be incorporated in the hardware and software and may not be reflected in this version of the document. Contact GE Healthcare Technical Support for clarification, if discrepancies arise. GE OEC Medical Systems, a General Electric company, going to market as GE Healthcare. GE OEC Medical Systems, Inc. 384 Wright Brothers Drive Salt Lake City, Utah 84116 U.S.A. 801-328-9300
Page ii
Contents
Contents 1. Introduction and Safety...1-1 Overview ... 1-2 Owner Responsibilities ... 1-2 System Compatibility ... 1-2 Operator Qualifications... 1-2 Continued Compliance... 1-2 Unauthorized Modifications ... 1-2 GE OEC Responsibilities... 1-3 X-ray Equipment Certification... 1-3 After-sale Operating and Safety Practices... 1-3 Communication Center Telephone Numbers... 1-3 Ordering Consumable Items ... 1-4 Phone ... 1-4 Fax ... 1-4 On-line... 1-4 Safety Hazards ... 1-5 Safety Hazard Alerts ... 1-5 Explosion... 1-6 Implosion ... 1-6 Equipment Stability and Positioning... 1-7 Motorized Mechanical Movement ... 1-7 Improperly Attached Equipment... 1-7 Electrical Shock... 1-8 Electrical Fire... 1-8 Ground Fault ... 1-8 Radiation Exposure... 1-9 General Protection ... 1-9 Source-to-Skin Distance... 1-9 Ingress of Fluids...1-10 Cooling Efficiency ...1-10 Burns...1-10 Electromagnetic Compatibility Statement ...1-10 Equipment Malfunction...1-11 External Devices...1-11 Patient Environment...1-12 Within the United States ...1-12 Outside the United States...1-12
Page iii
Contents
2. Start up and Storage ...2-1 Overview ... 2-2 Power On ... 2-2 Draping... 2-5 Draping the X-ray Tube Cooling Kit Option... 2-5 Standby or X-rays Off... 2-6 Power Off ... 2-6 C-Arm Storage... 2-7 Temporary Storage (less than 60 days)... 2-7 Long Term Storage or Shipment (60 days or more)... 2-7
3. Operating Controls ...3-1 Overview ... 3-2 Control Panel Housing... 3-2 Control Panel ... 3-3 Image Orientation ... 3-4 Remote Workstation Operation... 3-5 Image Intensifier Field Size ... 3-6 Collimator Control ... 3-6 Contrast/Brightness/Metal Rejection... 3-7 Generator Control ... 3-7 Fast Stop Switches ...3-10 X-ray On Switch...3-11 Footswitch and Handswitch...3-12 Switching Mode Pairs...3-14
4. Mechanical Positioning...4-1 Overview ... 4-2 C-arm Identification... 4-2 Component Identification... 4-3 Standard C-Arms ... 4-3 Super C-arms... 4-5 Positioning... 4-5 C-arm Orbital Rotation... 4-6 C-arm Orbital Rotation Brake ... 4-6 Super C-arm Orbital Rotation ... 4-7 Super C-arm Orbital Rotation Brake... 4-7 Flip-Flop Rotation... 4-8 Flip-Flop Rotation Brake ... 4-8 L-arm Rotation... 4-9 L-arm Brake... 4-9 Super C-arm Radial Rotation ...4-10 Super C-arm Radial Rotation Brake...4-10 Vertical Column Operation...4-11 Vertical Column Switches ...4-11
Page iv
Contents Horizontal Cross-arm...4-12 Horizontal Cross-arm Brake ...4-12 Wig-Wag...4-13 Wig-Wag Brake ...4-13 C-Arm Wheel Brakes ...4-14 C-Arm Steering Handle ...4-14 Moving the C-Arm...4-15
5. Radiographic Film ...5-1 Overview ... 5-2 Setup and Make a Film Exposure... 5-2 Prearm for Film Exposure ... 5-4
6. Maintenance ...6-1 Overview ... 6-2 Performance Checks... 6-2 Mechanical Performance Check ... 6-2 Electrical Performance Check... 6-3 Fast Stop Performance Check ... 6-3 Fluoro Mode Performance Check ... 6-4 Film Mode Performance Check... 6-4 Cleaning ... 6-5 Periodic Maintenance... 6-5
7. Display Messages ...7-1 Overview ... 7-2 Error Recovery Steps... 7-2 Messages... 7-2
8. Labels and Symbols...8-1 Overview ... 8-2 Labels ... 8-2 Symbols... 8-4
9. Technical Specifications ...9-1 Overview ... 9-2 Camera Output Video Signal... 9-2 Classification Type ... 9-2 Electromagnetic Compatibility Statement ... 9-2 Environmental Requirements ... 9-3 Power Requirements... 9-3 X-ray Source Assembly ... 9-4 Collimation ... 9-5
Page v
Contents Tube Rating Charts ... 9-6 Radiographic Ratings ( 50 Hertz) ... 9-6 Radiographic Ratings ( 60 Hertz) ... 9-6 Heating and Cooling Charts - Tube Housing... 9-7 Heating and Cooling Charts - Anode... 9-8 Generator Specifications... 9-9 Generator Operating Parameters...9-10 Measurement Basis for Technique Factors...9-10 Radiographic mA As a Function of kV and mAs...9-11 Focal Spot ( 0.3 mm) ...9-13 Focal Spot ( 0.6 mm) ...9-13 Scatter Radiation ...9-14 9 Inch (22.8 cm) II ...9-14 Horizontal Plane...9-14 9 inch II Air Kerma Scatter Rates – Horizontal Plane...9-14 Vertical Plane...9-15 9 inch II Air Kerma Scatter Rates – Vertical Plane...9-15 12 Inch (30.5 cm) II ...9-16 Horizontal Plane...9-16 12 inch II Air Kerma Scatter Rates – Horizontal Plane ...9-16 Vertical Plane...9-17 12 inch II Air Kerma Scatter Rates – Vertical Plane ...9-17 Dimensions ...9-18 C-Arm ( 9-inch/23cm II)...9-18 C-Arm ( 12-inch/30.5cm II)...9-19 Super C-Arm...9-20 Film Cassette Dimensions...9-21 Material Safety Data Sheets...9-21 Optional Equipment...9-21 Consumables ...9-21
I. Index ...I-1 Index ...I-2
Page vi
1.
Introduction and Safety
Introduction and Safety
Overview This manual describes operation for the specified product only. It is intended for qualified medical personnel who have been trained in the use of medical imaging equipment. It is not designed to replace or substitute for certified training in the radiological or medical field. Functional capabilities and operation of the equipment are described here which can be used in a variety of diagnostic, therapeutic and surgical applications.
Owner Responsibilities The owner has the responsibility to ensure system compatibility, operator qualifications and the continued compliance of equipment and operating specifications. Systems should only be used in designated use areas with approved AC receptacles. Unauthorized changes or modifications to any part of the system could have hazardous consequences. Changes or modifications must not be made unless specifically authorized by GE OEC Medical Systems, Inc.
System Compatibility Damage may result to the system if incompatible components are connected. Read your operator manual thoroughly prior to connecting components that you are not certain are compatible.
Operator Qualifications It is the responsibility of the owner to ensure that only properly trained, qualified personnel who have obtained credentials from the appropriate authorities operate the system.
Continued Compliance The owner is responsible for verifying continued compliance with all applicable regulations and standards. Consult local, state, federal and/or international agencies regarding specific requirements and regulations applicable to the use of this type of medical electronic equipment.
Unauthorized Modifications When properly assembled this equipment meets US Federal regulations and International standards. Unauthorized modifications to the equipment may impact adherence to these standards and make the equipment unsafe to operate. Never make any modifications or adjustments to the equipment unless directed by a qualified GE OEC representative.
Page 1-2
Introduction and Safety
GE OEC Responsibilities GE OEC Medical Systems, Inc. certifies each system and X-ray source assembly. After-sale operating practices and safety are the responsibility of the owner/operator.
X-ray Equipment Certification GE OEC Medical Systems, Inc. certifies that when assembled according to manufacturer's instructions, the X-ray equipment complies with the US Federal Performance standard 21 CFR Subchapter J and applicable international standards.
After-sale Operating and Safety Practices GE OEC Medical Systems, Inc. assumes no responsibility or liability for after-sale operating and safety practices; nor can it be responsible for personal injury or damage resulting from misuse of its systems.
Communication Center Telephone Numbers If the system does not operate properly or fails to respond to the controls as described in your operator’s manual, call GE OEC Medical Systems, Inc. to request service. The communication center's telephone numbers are listed below: US: 800 874-7378 China: 800 810-8188 All others: Contact local GE Medical Systems, Inc. office. You may also call these numbers to order circuit diagrams, component part lists, calibration instructions or other information which will assist qualified service engineers to repair the system.
Page 1-3
Introduction and Safety
Ordering Consumable Items You may order GE OEC consumables such as steri-drapes and printer paper, by phone, fax, or online.
Phone 1. Call the number that corresponds to your geographical location. US: 800 558-5102 Canada: 800 668-0732 China: 800 810-8188 All other locations: Contact your local sales representative. 2. Establish an account with the customer service representative. 3. Place your order.
Fax If you have a catalog and a GE Fax Order form, complete the form and fax the form to the fax number listed on the form. If you do not have a catalog or forms, you can obtain them by dialing the number listed for your geographical location.
On-line You can order consumables on the GE Medical System, Inc. web site from any geographical location but prior to ordering you must register on-line to open an account. Registration is free. 1. Go to www.gemedicalsystems.com. 2. Register to open an account. Note:
Record your user name and password for future account access. 3. Login using the user name and password that you established when you registered. 4. Browse through the on-line catalog and locate the OEC Supplies that you want to purchase.
Note:
If you have difficulties, dial the telephone number listed previously for your geographical location or contact your local sales representative.
Page 1-4
Introduction and Safety
Safety Hazards Potential hazards exist in the use of medical electronic devices and X-ray systems. Operators using the equipment should understand the safety issues, emergency procedures, and the operating instructions provided. Questions and comments regarding safety should be addressed to the GE OEC Medical Systems, Inc. service organization nearest them. Unresolved problems should be referred to: Vice President, Quality GE OEC Medical Systems, Inc. P.O. Box 25296 Salt Lake City, Utah 84125-0296 (801) 328-9300 GE OEC Medical Systems has designated the following entity to act as the European Union (EU) representative in matters dealing with the Medical Devices Directive under Annexes I and II: GE Medical Systems, SA 283, rue de la Minière B.P. 34F 78533 Buc Cedex France +33 (0) 1 30 70 40 40 The following pages describe hazardous and potentially hazardous conditions, and how to adequately protect yourself and others from possible injury.
Safety Hazard Alerts There are three hazard classifications, which are denoted and prioritized by the alert words: Alert
Circumstances for Use
DANGER
Danger indicates an imminently hazardous situation that, if not avoided, will result in death or serious injury.
WARNING
Warning indicates a potentially hazardous situation that, if not avoided, could result in death or serious injury.
CAUTION
Caution indicates a potentially hazardous situation that, if not avoided, may result in moderate to minor injury, equipment damage or loss of data.
Page 1-5
Introduction and Safety
Explosion If your system complies with the requirements of IEC 60601-1 regarding Anesthetic Proof (AP) equipment, an AP label will be located on the equipment. An AP label means that under normal conditions certain components may be operated safely in close proximity to flammable gases. However, if an abnormal condition occurs, such as the room fills with flammable gas, steps must be taken to prevent the gas from coming in contact with non AP rated components within the equipment. Follow these guidelines: •
Do not turn the system off or unplug it from the AC receptacle.
•
Do not operate any other electrically powered equipment.
•
Evacuate all personnel from the area and ventilate with fresh air. Avoid operating any automated (electrically operated) doors or windows.
•
Contact your local fire department as soon as possible.
Implosion If your equipment has a Cathode Ray Tube (CRT) do not locate objects so that they might fall and strike the tube causing it to implode. Use caution when working around the tube. The coating on the glass can also produce toxic dust and fumes. If a CRT implodes: •
Remove power immediately.
•
Evacuate the area.
•
Contact an appropriate staff member that is familiar with hazardous material disposal.
•
Request service to replace the monitor.
Page 1-6
Introduction and Safety
Equipment Stability and Positioning If your system is mounted on wheels and casters and it is moved or operated improperly it could roll out of control. Follow these guidelines: •
Two people should maintain control of the equipment when moving up or down an incline.
•
Place all mechanical assemblies in their most compact (transport) position and lock brake handles prior to moving the equipment.
•
Use the handles designed for moving the equipment and mechanical assemblies.
•
Never attempt to move the system up or down steps.
•
Do not operate the equipment on unlevel floors.
•
Do not lock the wheel brakes and leave the equipment unattended on unlevel floors.
•
Always apply the wheel locks when the system is in its final position.
•
Do not move the equipment if the casters or wheels are not functioning properly.
•
Mechanical shocks to the equipment while disk drives are accessing information may cause damage to the disk drive.
Motorized Mechanical Movement If your equipment has motorized mechanical assemblies follow these guidelines: •
Always observe mechanical assemblies when operating the motor to avoid pinching or collision with a person or object.
•
Use care when working around equipment to avoid unintentional motor actuation. Do not carelessly place objects on the equipment or bump or lean against the equipment.
•
Observe and prevent articles of clothing from getting caught in moving parts.
Improperly Attached Equipment •
If your equipment accommodates a film cassette holder or some other piece of equipment that can be attached or removed, follow these guidelines:
•
Use only equipment supplied by GE OEC Medical Systems, Inc.
•
Note:
Attach the equipment properly. Incorrectly attached equipment could fall, causing injury to the patient or operator. Refer to the Technical Reference Chapter for the correct dimensions of items that may be used in conjunction with this product, such as radiographic film cassettes.
Page 1-7
Introduction and Safety
Electrical Shock Observe the following safety procedures to avoid electric shock or serious injury to operators and patients and to avoid system malfunction. •
Make all electrical connections to equipment while outside the patient environment. Do not touch a connector and the patient at the same time.
•
Do not bypass, jumper or otherwise disable the safety interlocks.
•
Do not remove any of the assembly covers. Only trained service representatives should perform repairs.
•
Do not place food or beverage containers on any part of the equipment. If spilled they can cause short circuits.
•
Always remove power to the equipment before cleaning. Use a slightly damp cloth or sponge for cleaning.
•
Only qualified service engineers are allowed to service or repair a system.
WARNING Electrical circuits inside the equipment may use voltages which are capable of causing serious injury or death from electric shock. To avoid this hazard, never remove any of the cabinet covers.
Electrical Fire In the event of electrical fire perform the following emergency procedure: Note:
Any emergency procedure developed by the owner, for the area in which the system is used, should include these safety measures: • Remove electrical power to the system by placing the power switch in the off position. •
Unplug the power cord from the AC receptacle.
•
Evacuate personnel from the area.
•
Only use a fire extinguisher that is approved for use on electrical fires.
•
Call your local fire department for help if necessary.
WARNING The use of the wrong type of fire extinguisher presents electrical shock and burn hazards. To avoid these hazards, a fire extinguisher which meets applicable regulations and standards must be available in the room where the equipment is being used. Remember that equipment that is equipped with batteries is a source of electrical current, even when AC power is disconnected.
Ground Fault If the operating room has a ground fault alarm and the alarm is actuated: •
Do not operate the system.
•
Call a qualified service technician.
Page 1-8
Introduction and Safety
Radiation Exposure General Protection WARNING This equipment either produces or is used in the vicinity of ionizing radiation. Observe proper safety practices during operation. •
The owner must designate areas suitable for safe operation and service of the equipment and ensure they are only used in those areas.
•
The owner must ensure that all personnel wear appropriate protective clothing and radiation monitoring devices while using the equipment.
•
Remain alert for visual indicators and audible alarms that are activated when ionizing radiation is being produced by equipment in the work area.
Source-to-Skin Distance International regulations specify that a minimum source-skin distance be maintained, except for specific surgical applications. Some medical imaging equipment may have a skin spacer attached in order to meet this requirement.
WARNING Removing the skin spacer may result in increased radiation exposure to the patient. The rate of exposure increases exponentially as the anatomy is positioned closer to the X-ray tube. The skin spacer should only be removed on the instructions of a physician. The spacer should be reattached to the collimator assembly immediately following the procedure.
Page 1-9
Introduction and Safety
Ingress of Fluids WARNING The X-ray system is not rated for water-tight operation. If liquids drip into the equipment, disconnect the power cord and do not operate the system until it can be cleaned and inspected by a qualified service engineer. Excessive amounts of fluids such as antiseptics, cleaning solutions or bodily fluids may damage internal components if they are allowed inside the equipment. Use drapes, if necessary, to protect equipment when performing procedures and do not apply excessive amounts of fluid when cleaning.
Cooling Efficiency Draping some X-ray equipment may restrict airflow to components that provide heat sinking and to vents designed to cool the equipment. Drape equipment and cover vents only when exposure to excessive fluids is unavoidable and extended use of the equipment is not required.
Burns Extended use of imaging equipment may cause components such as X-ray tubes to reach temperatures capable of inflicting burns. Use care when positioning equipment to avoid placing hot components in close proximity to patients and personnel. An anesthetized or unconscious patient is incapable of sensing and reacting to a hot component.
Electromagnetic Compatibility Statement This equipment may generate and use radio frequency energy. The equipment must be installed and used according to the manufacturer’s instructions in order to avoid radio frequency interference. If this equipment generates or receives interference do the following to correct the problem: •
Verify that the equipment is the cause by turning the system on and off.
•
In the event of unintended motor actuation, immediately remove power to the equipment.
•
In the event of unintended X-ray actuation, immediately remove power to the equipment.
•
Reorient the equipment until the interference stops.
•
Relocate the equipment with respect to other equipment in the room.
•
Plug the equipment into a different outlet so that the equipment and the receiver are on different branch circuits.
•
Use only input/output (I/O) cables supplied by GE OEC Medical Systems, Inc.
Page 1-10
Introduction and Safety
Equipment Malfunction If either the hospital or equipment circuit breakers trip, an equipment malfunction may be indicated. Do not attempt to operate the equipment until a qualified service engineer has checked it. If any of the equipment controls fail to respond as indicated in this manual, you should: 1. Remove power to the equipment by placing the power switch in the off position and unplugging the power cord from the AC receptacle. 2. Notify a qualified service engineer. 3. Do not operate the equipment until the service technician advises that it is operating properly.
External Devices To ensure patient safety, only connect external equipment that has been approved by GE OEC Medical Systems, Inc. All equipment attached to the external interface connections must meet the requirements of IEC 60601-1 when operated within the patient environment. When used outside of the patient environment, each externally connected device must comply with the relevant IEC/ISO requirements for that device. In any case, the combination of all externally connected equipment shall not cause the leakage current of any device used within the patient environment to exceed the limits stated in IEC 60601-1.
Page 1-11
Introduction and Safety
Patient Environment Within the United States Within the US the Patient Environment is defined by NFPA 99. In areas in which patients are normally cared for, the patient environment is the space with surfaces likely to be contacted by the patient or an attendant who can touch the patient. This encloses a space within the room 6 ft. beyond the perimeter of the bed (examination table, dental chair, treatment booth, etc.) in its intended location, and extending vertically 7.5 ft. above the floor.
Figure 1-1. Patient Environment Inside United States
Outside the United States Outside the US the patient environment is defined by IEC 60601-1-1. In areas in which patients are normally cared for, the patient environment is the space with surfaces likely to be contacted by the patient or an attendant who can touch the patient. This encloses a space within the room 1.5 m beyond the perimeter of the bed (examination table, dental chair, treatment booth, etc.) in its intended location, and extending vertically 2.5 m above the floor.
Figure 1-2. Patient Environment Outside United State
Page 1-12
2.
Start up and Storage
Startup and Storage
Overview This chapter describes: •
Applying power
•
Removing power
•
Storing the C-arm
Power On If you are starting the system after a period of long term storage it may be necessary to allow the system to warm up or recharge the batteries before it can be used. The system clock will sense how long the system has been in storage and display a message that describes the action required. Refer to the "Display Messages" chapter for more information. The C-arm receives power through an interconnect cable attached to the Workstation. The Carm must be connected to the Workstation and electrical power before operation.
CAUTION The C-Arm should only be used in conjunction with a compatible and appropriately configured OEC Workstation. The 9900 C-Arm is not compatible with Workstations sold as part of a 9800 system. Damage may result to the system if incompatible components are connected. 1. Insert the Workstation interconnect cable into the connector located on the right side cover of the C-arm by aligning the index marks (red dots) on the connector and pushing the connector in until it locks in place.
CAUTION If the connector does not lock in place, unrelable system operation may result.
Figure 2-1. Connect the C-Arm to the Workstation
Page 2-2