Guldmann
GH3 and GH3+ Ceiling Hoist User Manual Ver 101.00 March 2021
User Manual
64 Pages
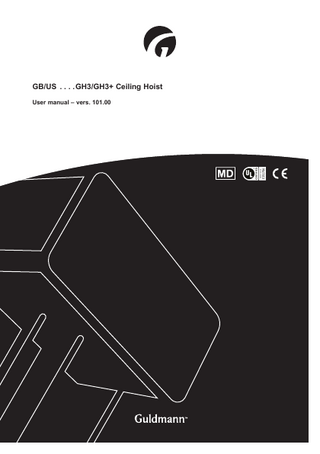
Preview
Page 1
© Guldmann GB/US-03/2021 • # 550216_101
2
+
Twin
Charg. HC xx)
UL
Excl. Turbospeed
Coating xx)
Trainer module xx)
Class III scale
x
WiFi module
Number of horizontal drive motors x)
x
Scale module
Number of lifting motors
x
CLM module
Number of lifting straps
xxx
Service module
Load in kg
(x)
IR remote xx)
Product line
GH3 GH3
© Guldmann GB/US-03/2021 • # 550216_101
Options
Guldmann hoist type
GH3 Lifting modules, configurations
Configuration code (xxxxx)
200
1
1
0-1-2
•
•
250
1
1
0-1-2
•
•
200
1
1
0-1-2
•
•
•
•
•
•
•
•
•
•
•
250
1
1
0-1-2
•
•
•
•
•
•
•
•
•
•
•
275
1
1
0-1-2
•
•
•
•
•
•
•
•
•
•
•
300
1
2
0-2
•
•
•
•
•
•
•
•
•
•
•
350
1
2
0-2
•
•
•
•
•
•
•
•
•
•
•
375
1
2
0-2
•
•
•
•
•
•
•
•
•
•
•
400
1
2
0
•
•
•
•
•
•
•
•
•
•
•
250
2
2
0
•
•
•
•
•
•
•
•
•
500
2
2
0
•
•
•
•
•
•
•
•
•
x) Drive motors are not compatible with UL xx) Not compatible with UL
3
GH3/GH3+ Ceiling Hoist Item nos: 55xxxx
1.00... GH3 use... 6 1.01... Manufacturer... 6 1.02... Intended purpose... 6 1.03... Area of use... 6 1.04... Conditions for use... 6 1.05... Important/Precautions... 7 1.06... Load limits on GH3 system... 7 1.07... Unpacking and Preparation... 8 1.08... Placing a new GH3 Hoist in an existing rail system... 8 1.09... Power supply... 9 1.10... Installation of the lifting hanger before use... 10 1.11... Lifting sling... 11 1.12... Swing kit... 14 1.13... Using swing kit in doorway... 15 1.14... GH3 with horizontal drive motor... 16 1.15... GH3 with horizontal drive motor and infrared remote (IR) control... 16
3.00... Environmental conditions... 48 4.00... Maintenance and storage... 48 4.01... Cleaning and disinfection... 48 4.02... Storage... 49 4.03... How to prevent/avoid corrosion?... 49 4.04... The owner’s daily maintenance duty... 49 4.05... Disposal of the GH3 including batteries... 49
4
© Guldmann GB/US-03/2021 • # 550216_101
2.00... Description of functions... 16 2.01... Pictograms... 17 2.02... Indicator lamps and audio signals... 17 2.03... Operation... 18 2.04... Supplementary modules, GH3+... 20 2.05... Configuration of supplementary modules, GH3+... 24 2.06... Important before using the Scale module and Class III scale... 25 2.07... Scale module (GH3+ with integrated scale module)... 26 2.08... Class III Scale (GH3+ with Class III Scale)... 29 2.09... Calibration/verification of Classe III Scale... 34 2.10... Trainer Module... 35 2.11... CLM module (GH3+ with statistical function for management use)... 39 2.12... Service module (GH3+ with service module)... 41 2.13... Safety functions... 43 2.14... Charging/connection... 45 2.15... Accessories... 45
5.00... Service and lifetime... 49 5.01... Lifetime... 49 5.02... Safety/service inspections... 50 5.03... Troubleshooting... 50 6.00... Classification... 51 7.00... Certificates... 52 8.00... Technical specifications... 53 8.01... Module label, quick info... 53 8.02... Configuration of GH3 lifting module... 53 8.03... Technical specifications... 55 9.00... EU-Declaration of conformity... 57 10.00... Type approval certificate... 58 11.00... Environmental policy statement - V. Guldmann A/S... 59 12.00... EMC Information... 59
© Guldmann GB/US-03/2021 • # 550216_101
13.00... Warranty and service conditions... 62 A... Warranty... 62 B... Service or Repair... 63
5
1.00
GH3 use
1.01
Manufacturer V. Guldmann A/S Graham Bells Vej 21-23A DK-8200 Aarhus N Tel. + 45 8741 3100 www.guldmann.com
1.02
Intended purpose The GH3 lifting module is intended for lifting and transferring a person with disabilities and for gait training.
1.03
Area of use GH3 is suitable for professional use in hospitals, nursing homes, rehabilitation centers, institutions, Riding schools, swimming pools, mortuarys and in private homes and buildings, where operators with medical/clinical training are continually on site or on call.
1.04
Conditions for use GH3 is a ceiling-mounted hoist that moves in a rail system. GH3 is designed to be used with a variety of lifting hangers and lifting slings.
• • • • • • • •
The GH3 should only be used by trained personnel. The maximum nominal load, 200 kg (440 lbs), 250 kg (550 lbs), 275 kg (600 lbs), 300 kg (660 lbs), 350 kg (770 lbs), 375 kg (825 lbs), 400 kg (880 lbs) respectively, must not be exceeded. Instruction offered by Guldmann to all customer groups in connection with the purchase of a ceiling-mounted hoist has been received. The helper pays attention to the well-being of the user when using the hoist. The hoist is used in rail systems which are installed, tested and approved according to Guldmann’s stipulation. Only technicians who have been certified by Guldmann may install and test the rail systems. The hoist is used with the Guldmann lifting hanger or with another suitable hanger (section 1.09). The hoist is used with a Guldmann lifting sling or with other suitable slings (section 1.10).
6
© Guldmann GB/US-03/2021 • # 550216_101
The use of the GH3 is subject to the following:
1.05
• • • • • • • • • • • • •
• • • •
Important/Precautions Read the instructions carefully before using the GH3 and in connection with cleaning and service of the hoist. The GH3’s maximum load must never be exceeded. The GH3 may only be used to lift a person. The red strap for the emergency stop and the emergency lowering must be adjusted to the helpers reach, and must not be removed. The GH3 must not be used where there is a risk of it being splashed with water. If a defect appears during use of the GH3, stop using the hoist and contact the Guldmann Service Team for repairs. The GH3 is controlled by a microprocessor PCB, which can be damaged by static electricity if touched without the necessary precautions, (see point 1.08) The electronics may only be serviced by Guldmann approved service technicians. The lifting hanger must not be mounted or replaced when the GH3 hoist is positioned over the patient. Do not modify this equipment without the authorization of the manufacturer The GH3 needs special precautions regarding EMC and needs to be installed and put into service according to the EMC information provided in Chapter 11 EMC Information. Portable and mobile RF communications equipment can affect the GH3. Accessories, transducers and cables must always be original Guldmann components. The use of other spare parts than those supplied by Guldmann A/S may result in poor EMC protection. This may cause damage to the GH3 lifting module as well as electrical products in the nearby surroundings. The GH3 should not be used adjacent to or stacked with other equipment and if adjacent or stacked use is necessary, the GH3 should be observed to verify normal operation in the configuration in which it will be used. Transport of this equipment should only be undertaken after conditions described in section 3.00 (Environmental conditions). Nothing should be connected to the USB port when the device is in use with a patient. Any serious incident that occurred in relation to this device should be reported to the manufacturer and the local competent authority. Re: EMC If electromagnetic or other influences occur between this product and other products, these products must not be used together.
© Guldmann GB/US-03/2021 • # 550216_101
1.06
Load limits on GH3 system Read the label which indicates the maximum load limits for each component. The component, e.g. lifting hanger, lifting sling, etc. labelled with the lowest load limit determines the maximum load limit for the entire system. This maximum load limit must not be exceeded. Please note that the max load may change when different components are used, such as lifting hangers, lifting slings, etc.
7
1.07
Unpacking and Preparation Visual check of the GH3. If the GH3 is thought to be damaged upon reception, the GH3 must not be used before it has been checked and approved by a qualified person or the Guldmann Service Team. Contents of the box 1. GH3 hoist 2. Hand control 3. Transformer 4. Manual 5. Label for rail system
1.08
1
2
3
Placing a new GH3 Hoist in an existing rail system
•
The rated max load of the rail system, must be equal to or higher than the max load of the new hoist. – If there is no max load mentioned on the rail system, the rail system must then be checked according to the guideline in the installation manual (distance between bracket according to max load) – If the brackets are not visible, then a load test with 1,5 x max load of the hoist must be performed for a minimum of 20 min. The deflection of rails must not be higher than 1/200 of the length of the rail. – If it is not possible to do any of the above mentioned, please contact Guldmann or their representative
•
If the rail system can not be rated to the same max load as the hoist, then extra brackets must be installed according to the installation manual (distance between bracket according to max load). Class I equipment Fixed rail systems are class I equipment and must be installed by a qualified technician or by Guldmann Service Team. Equipment is disconnected from Supply Mains by breaking the mains breaker switch. Emergency stop device The emergency stop device must be reset in order to connect power to the product. To do this, push the yellow reset button (see point 2.09).
8
© Guldmann GB/US-03/2021 • # 550216_101
Please notice that when, placing a new GH3 hoist in an existing rail system it must be ensured that:
1.09
Power supply GH3 is equipped with batteries that require regular recharging. The power supply for charging and the battery charging point must be connected by a qualified engineer or by Guldmann Service Team. The transformer supplied must always be used.
© Guldmann GB/US-03/2021 • # 550216_101
Safety concerning static electricity (ESD) Service technicians and installers must use an ESD-safety package consisting of a mat, a ground wire, and a bracelet. The technician/installer connects the mat to a grounding point, for instance a radiator or a water pipe. The technician/installer must then put on the bracelet and connect it to the mat. If it is not possible to find a grounding point, the mat and the bracelet must be used as a minimum. Only then is it allowed to work with the PC Board or components where it is possible to come into contact with the PC Board.
9
Installation of the lifting hanger before use Lifting hangers from other manufacturers Guldmann shall not be liable for faults or accidents that may occur as a result of using lifting hangers made by other manufacturers. If there is any doubt about the selection or use of a lifting hanger, please contact your supplier.
Fig. 1
The lifting hanger can be installed to the lifting strap without the use of any tools. 1. Press the yellow button and hold it in while the lifting strap’s hook is inserted into the opening of the top cover of the lifting hanger (fig. 2a - 2b).
Fig. 2a
2. Release the yellow button (fig. 2c) 3. Rotate the strap attachment to a vertical position (fig. 3). Check that the yellow button has returned to its locked position by checking that it is flush with the cover of the lifting hanger and that the strap attachment can rotate freely.
Fig. 2b
Fig. 2c
Fig. 3
10
© Guldmann GB/US-03/2021 • # 550216_101
1.10
1.11
Lifting sling A lifting sling with four to eight lifting straps designed for mounting on hooks should be utilized when using a Guldmann lifting hanger. Place the straps on the hooks. If a hanger with rubber fingers is used, make sure that the rubber safety catch returns to its starting position, so that the strap can not unintentionally fall off. Slings made by other manufacturers Guldmann shall not be liable for faults or accidents that may occur as a result of using lifting slings made by other manufacturers. If there is any doubt about the selection or use of a lifting sling, please contact your supplier. Guldmann shall not be liable for faults or accidents due to incorrect use of the lifting sling, or for reasons of inadequate attention on the part of the carer or user. Attaching the lifting sling Place the straps from the lifting sling on the hooks on the lifting hanger. Start with the uppermost set of straps (from the back) and then take the lowest set of straps (from the legs). Lifting hanger, 4 attachment points Caution! Be careful when attaching the lifting slings straps on the hooks. Check that the straps have been correctly placed in the lifting hangers hooks. When pressing the up button on the hand control to lift the user, check again that all straps remain correctly placed in the lifting hangers hooks (Fig. 1).
© Guldmann GB/US-03/2021 • # 550216_101
Fig. 1
11
Lifting hanger Caution! Be careful when attaching the lifting sling on the hooks. Check that the straps have been pulled completely through the rubber safety catch (A) and into place in the lifting hanger’s hooks. When pressing the up button to lift the user, check again that all the straps remain correctly placed in the lifting hanger’s hooks (fig. 1a and fig. 1b).
A
Fig. 1a
A
Fig. 1b
Lifting to and from a seated position When lifting a user from e.g. a wheelchair, move the GH3 towards the person to be lifted. The lifting hanger should be at the same height as the users chest and should be in approximately mid-thigh position. Place the lifting hanger parallel to the users shoulders. Place the lifting sling behind the users back between the back of the chair and the users back. The center marks of the lifting sling should follow the users spine. Lead the leg straps along the outer sides of the users shins and beneath the thighs between the hollow of the knees and the hip joints. Cross the leg straps in front of the user.
12
© Guldmann GB/US-03/2021 • # 550216_101
All four lifting straps are now ready to be attached. The lifting sling can now be mounted on the lifting hanger.
Lifting to and from lying position in bed Place the lifting hanger over the centre of the person to be lifted. Place the lifting hanger parallel to the users shoulders. Turn the user onto his or her side. The Basic High sling should be placed so that its top is at the same height as the top of the users head. Now position the sling over the user so that the centre band follows the users spine. Turn the user onto his or her back and pull out the remaining part of the lifting sling. Place the leg straps beneath the users thighs and cross them. All four lifting straps are now ready to be attached and the lifting sling can be mounted on the lifting hanger. It is an advantage to elevate the head of the bed so that the user is sitting up. Important! For further information, please refer to the user manual for the lifting sling in question. Only people who have received competent instruction regarding the use of lifting equipment and fitting of slings should use the hoist. Plan the move. Avoid leaving the user in the lifting sling unattended. Working with the GH3 The GH3 runs easily in the rail system and does not have any special requirements for space or power in connection with moving. Attention can thus be fully focused on the users functional level and the helpers technique. If the hoist is used correctly, the user should only be lifted to the extent that she/he is clear of the surface and should be moved at this height.
© Guldmann GB/US-03/2021 • # 550216_101
The hoist lifts quickly and powerfully. Before lifting, check that the user is completely free of his/her surroundings. The users head, arms, hands and feet must not be in danger of becoming trapped. Be careful with any tubes and wires that are attached to the user. The user should not hold the lifting strap during the moving procedure as there is a risk of crushing between the strap’s hook and the hoist. Check that the hand control and hand control cable is free of hanger, patient and other object before the hoist is activated up or down moved.
13
Swing kit The swing function is used in conjunction with a transfer e.g. through a door from one lifting module to another. Note: The swing adapter must be ordered separately.
Fig. 1
Installation of swing adapter 1. Before starting a lift involving a swing transfer the swing adapter (Fig. 1) must be installed on the lifting hanger. (Fig. 2 to 5)
Fig. 2
2. Hold the lifting hanger in the right hand and press the yellow button using the thumb (Fig. 2) 3. Insert the swing adapter in the slot on the lifting hanger top cover with the open side facing down (Fig. 3a, 3b) and release the yellow button.
Fig. 3a
4. Rotate the swing adapter to a vertical position (Fig. 4) 5. Check that the yellow button has returned to its locked position by checking that it is flush with the cover of the lifting hanger and that the swing adapter can rotate freely. 6. Install the strap attachment to the swing adapter by sliding the open side of the strap attachment over the flat area of the swing adapter (Fig. 5) 7. Rotate the strap attachment and ensure that it moves up on the circular portion of the swing adapter (Fig. 6)
Fig. 3b
Fig. 4
Fig. 5
Fig. 6
14
© Guldmann GB/US-03/2021 • # 550216_101
1.12
1.13
Using swing kit in doorway 1. Bring the two hoists as close together as possible. Adjust the height of the lifting hanger on hoist B so that the transfer can be done without the user touching the floor during the transfer from one hoist to another.
A
B
A
B
A
B
4. Disconnect the lifting strap on hoist B from the lifting hanger and raise the strap on hoist B out of the way.
A
B
5. Move the lifting hanger from hoist A to operating height and the doorway transfer is complete.
A
B
2. Take the free lifting strap from hoist A and secure it to the swing adapter on the lifting hanger (see 1.10 figures 5 and 6). In order to lower the free lifting strap on hoist A a slight pull must be applied to the strap.
© Guldmann GB/US-03/2021 • # 550216_101
3. Lower the lifting hanger using hoist B while lifting the strap on hoist A to perform the swing transfer. The transfer has been completed when there is no load on the lifting strap on hoist B.
15
1.14
GH3 with horizontal drive motor The GH3 with horizontal drive motor can operate in the rail system. Be aware that the drive motor takes time to both accelerate and brake the hoist. The drive speed can be reduced with the SIC software. It is possible to position the hoist with horizontal driving motor with a high degree of accuracy by a brief activation of the hand control. The GH3 with horizontal drive motor runs on its own power and it should not be pulled through the rail system.
1.15
GH3 with horizontal drive motor and infrared remote (IR) control The GH3 has an integrated IR receiver which is controlled by the IR remote control. The hand control should be left attached to the hoist. This means that the hoist can always be operated, in the the event that the IR remote control is misplaced or the battery is uncharged.
Description of functions Information panel on the GH3 bottom surface.
Lamp indicator
16
© Guldmann GB/US-03/2021 • # 550216_101
2.00
2.01
Pictograms Emergency stop Emergency lowering function RESET
Reset emergency stop Direction of travel (horizontal drive motor) denoted by grey arrow
2.02
Indicator lamps and audio signals Status
Indicator lamps
© Guldmann GB/US-03/2021 • # 550216_101
Communication
3 x Beep after 60 sec
Horizontal drive motor
Green
Emergency lowering
All OK
No charging Yellow, after 15 sec
Down
Off
Possible GH3 Functions Up
Off – stand by
Audio signals
x
x
x
x
x
x
x
x
x
x
x
x
x
x
Low battery
Yellow
Fault on hoist
Yellow
Beeps at button activation
Battery critical low
Yellow
Beeps at button activation for functions that are not possible
Over load
Yellow
Beeps at button activation
Service date Yellow exceeded more than 60 days
Beeps at button activation
x
x
x
x
x
Less than 60 sec of training available with Trainer module
Continuous short beeps for 60 sec
x
x
x
x
x
Yellow
17
x
x
x
x
x
x
x
x
Operation Hand control The GH3 is switched on automatically when a button on the hand control is pressed.
1
The GH3 is switched off automatically after approx. 8 minutes without activation. 2
GH3 1. Lift 2. Lower 3. PDA interface (micro USB)
3
GH3 with horizontal drive motor 1. Lift 2. Lower 3. Movement in the direction of the arrow on the GH3 information panel (section 2.00). 4. Movement in the direction opposite to the arrow on the GH3 information panel (section 2.00). 5. PDA interface (micro USB) GH3+ 1. Lift 2. Lower 5. Function selection button (section 2.05, supplementary modules) 6. Function selection button (section 2.05, supplementary modules) 7. PDA interface (micro USB) GH3+ with horizontal drive motor 1. Lift 2. Lower 3. Movement in the direction of the arrow on the GH3 information panel (section 2.00). 4. Movement in the direction opposite to the arrow on the GH3 information panel (section 2.00). 5. Function selection button (section 2.05, supplementary modules) 6. Function selection button (section 2.05, supplementary modules) 7. PDA interface (micro USB)
1 3 4 2 5
5 1 6 2 7
5 1 3
4 2
7
18
6
© Guldmann GB/US-03/2021 • # 550216_101
2.03
Parking the hand control When the hand control is not in use it can be placed on the lifting hanger.
Infrared remote control 1. Lift 2. Lower 3. Movement in the direction of the arrow on the GH3 information panel (section 2.00). 4. Movement in the direction opposite to the arrow on the GH3 (section 2.00).
1 3
© Guldmann GB/US-03/2021 • # 550216_101
Note: In order for the GH3’s lowering function to work, the strap must be carrying a load equal to the minimum capacity for Guldmann’s lifting hanger. Movement of the GH3 in the rail system The GH3 is manually pushed forward in the rail by the helper. The GH3 with 1 horizontal drive motor will run in the rail when the helper activates the hand control or IR remote control. The GH3 with 2 horizontal drive motors will run in the rail by itself, when activated by the hand control or IR remote control.
19
2 4
Supplementary modules, GH3+ There are various supplementary modules for the GH3+ • • • • •
CLM module (GH3+ with statistical function for management use) Service module (GH3+ with Service module) Scale module (GH3+ with integrated scale) Class III Scale (GH3+ with integrated Class III Scale) III Trainer module (GH3+ with integrated dynamic weight relief)
• • • •
Menu structure, GH3+ with supplementary modules Scale module Trainer module CLM module Service module
Scale
Start
Scale
Trainer
CLM
Start
Start
Show
Scale
Trainer
Nex
KG OK
20
248.0 kg Tare
30
56 kg
Exit
Exit
CLM 1-5 Lifetime total lifts 987 Next
Exit
Pop-ups Next service 2019.07.01
Service date exceeded call service
OK
Exit
Low battery
Critical low battery
OK
OK
No charging
Fault hoist
OK
OK
Scale
Trainer
0.0 kg Tare
Exit
30
56 kg Exit
CLM 2-5 Lifetime heavy lifts 232 Next
Exit
CLM 3-5 Last week total lifts 60 Next
Exit
CLM 4-5 Lifts per week avg 72 Next
Exit
CLM
5-5
Hoist ID Hoist #1 Next
20
Exit
© Guldmann GB/US-03/2021 • # 550216_101
2.04
Next service
LM
Setup
2019.07.01
how
Setup
LM 1-5 Lifetime total lifts 987
Units
Next
Exit
Change
Change
Change
LM 2-5 Lifetime heavy lifts 232
Units
Language 1-8
Language 5-8
Dansk
Espanol
Next
Change
Exit
Language
Language 4-8
English
KG
lbs OK
Change
OK
Italianio
Change
OK
OK
LM 3-5 Last week total lifts 60
Language 2-8
Language 6-8
Deutsch
Francaise
Next
Change
Exit
OK
Change
OK
Language 3-8
Language 7-8
Svenska
Portuguese BR
Next
Change
LM
© Guldmann GB/US-03/2021 • # 550216_101
LM 4-5 Lifts per week avg 72 Exit
OK
5-5
Hoist ID Hoist #1
Next
Exit
21
Change