Hall Surgical
Hall PowerPro Pneumatic Handpieces and Attachments
The Hall Mini-Driver Pneumatic Handpiece Instruction Manual Rev A Aug 2001
Instruction Manual
42 Pages
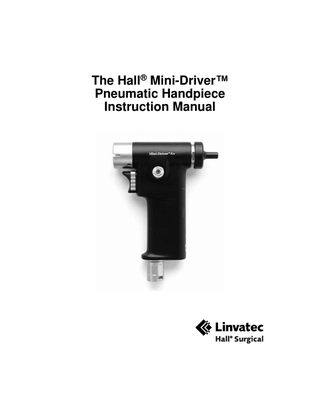
Preview
Page 1
The Hall® Mini-Driver™ Pneumatic Handpiece Instruction Manual
Proprietary Information This manual contains information deemed proprietary to Linvatec Corporation. The information contained herein, including all of the designs and related materials, is the sole property of Linvatec and/or its licensors. Linvatec and/or its licensors reserve all patent, copyright and other proprietary rights to this document, including all design, manufacturing methodology and reproduction. This document, and any related materials, is confidential and is protected by copyright laws and shall not be duplicated, transmitted, transcribed, stored in a retrieval system, or translated into any human or computer language in any form or by any means, electronic, mechanical, magnetic, manual or otherwise, or disclosed to third parties, in whole or in part, without the prior express written consent of Linvatec. Linvatec reserves the right to revise this publication and to make changes from time to time in the contents hereof without obligation to notify any person of such revision or changes, unless otherwise required by law.
Linvatec, Hall, and Mini-Driver are trademarks or registered trademarks of Linvatec Corporation.
© Linvatec Corporation 2001. All Rights Reserved. Printed in USA
Record the Model and Serial Numbers of the handpiece(s), and date received. Retain for future reference. Handpiece Model No. Handpiece Model No. Handpiece Model No. Handpiece Model No.
Serial No Serial No Serial No Serial No
Date Date Date Date
Page
Table of Contents
1.0
2.0
INTRODUCTION 1.1
Intended Use... 1
1.2
General Warnings... 1
1.3
Symbol Definitions... 2
1.4
Pneumatic Handpiece (K200)... 3
SYSTEM INSTALLATION and OPERATION 2.1
Power Source and Regulator Installation and Operation... 4
2.2
Attachments and Accessories... 8 2.2.1
Connecting/Removing Attachments... 8
2.2.2
Pin and Wiredriver Attachments... 9 2.2.2.1
Pin Driver Attachment (K211)... 9
2.2.2.2
Wiredriver Attachment (K111A)... 10
2.2.2.3
Pin and Wire Insertion... 10
2.2.3
Sagittal Saw Attachment (K120)... 11
2.2.4
Sagittal Saw Attachment (K220)... 13
2.2.5
All Jacobs Chuck Attachments... 14
2.2.6
2.2.5.1
5/32” Jacobs Chuck (K110)... 14
2.2.5.2
1/4” Jacobs Chuck (K109)... 15
2.2.5.3
High-Torque Jacobs Chuck (K210)... 15
Trinkle Chuck Attachment (K112)... 16 2.2.6.1
Automatic Screwdrivers for the Trinkle Chuck Attachment (D520/D524)... 17
2.2.7
Hudson Chuck Attachment (K113)... 18
2.2.8
ASIF/AO Twist Drill Chuck Attachment (K114A)... 19
i
Page
Table of Contents
3.0
MAINTENANCE 3.1
Cleaning and Sterilizing... 22 3.1.1
Cleaning Precautions... 22
3.1.2
Handpiece and Attachment Cleaning Instructions... 22
3.1.3
Handpiece and Attachment Lubricating Instructions... 23
3.1.4
General Sterilization Information... 24 3.1.4.1
3.2
4.0
5.0
Sterilizing Warnings, Precautions and Notes... 24
Troubleshooting... 26
TECHNICAL SPECIFICATIONS 4.1
Handpiece... 29
4.2
System Environmental Requirements... 30
CUSTOMER SERVICE and WARRANTY 5.1
Customer Service... 31
5.2
Handpieces, Attachments and Accessories... 33
5.3
Linvatec® and Hall® Surgical Instrument Warranty... 34
ii
1.0 INTRODUCTION
1.2
t is recommended that personnel study this manual before attempting to operate, clean or sterilize the Hall® Mini-Driver™ Pneumatic Instrument System. The safe and effective use of this equipment requires the understanding of and compliance with all warnings, caution notices and instructions marked on the product and included in this manual.
I
1.1
Intended Use
he Mini-Driver Pneumatic Instrument System, combined with the many available attachments, is intended for sawing, reaming, drilling, wiring and pinning small bones or joints and connective tissue during orthopedic surgery.
T
1
General Warnings
1.
This equipment is designed for use by medical professionals completely familiar with the required techniques and instructions for use of the equipment. Read and follow all warning and caution notices and instructions marked on the product and included in this manual.
2.
Eye protection is recommended when operating equipment.
3.
Use only associated Hall® Surgical and Linvatec® attachments and accessories (i.e., saw blades, bits, etc.).
4.
Handle all equipment carefully. If any equipment is dropped or damaged in any way, return it immediately for service.
5.
Prior to each use, perform the following: •
Inspect all equipment for proper operation.
•
Ensure all attachments, accessories and hoses are correctly and completely attached to the handpiece.
•
Check all pneumatic equipment for any air or nitrogen leakage. If leakage is noticed, return for service.
•
Always inspect pneumatic hoses for signs of wear or damage. Do not use worn or damaged hoses. Replace immediately.
•
Always inspect for bent, dull or damaged blades or drill bits. Do not attempt to straighten or sharpen. Do not use if damaged. After use, dispose of properly.
6.
Sagittal saw blades and drill bits are single use only. Do not resterilize. After use, dispose of properly.
1.3
Symbol Definitions
7.
Handpieces are factory sealed. Do not disassemble.
Attention, consult accompanying documents.
8.
Do not pressurize hoses until all fittings have been connected and checked.
9.
Never operate pneumatic handpiece above 110 psi (7 kg/cm2) dynamic pressure unless an extension hose is added to the standard 10 foot hose. Excessive pressure may cause damage to the instrument and exert unusual stress on the hose.
No user service recommended. Refer servicing to qualified Linvatec service personnel. Indicates product component should not be sterilized. Indicates product component should not be immersed in any type of fluid.
10. The nitrogen regulator is only for use with pneumatically powered surgical devices.
Indicates handpiece should not be immersed in any type of fluid.
11. Continually check all handpieces and attachments for overheating. Discontinue use and return equipment for service as necessary. Overheating of the bit or blade may cause damage to the bit or blade and may cause thermal necrosis.
Indicates product should not be oiled or lubricated. Single Use Only.
12. Do not attach, insert or remove accessories or attachments while the handpiece is operating. Place the handpiece safety to the appropriate safe position prior to installation or removal of items.
Eye Protection Required.
Rx ONLY
13. After each use, thoroughly clean the handpiece and attachments (See “3.1 Cleaning and Sterilizing” on page 22).
2
Caution: Federal Law restricts this device to sale by or on the order of a physician
1.4
❹ Hose Connector - The air hose attaches
Pneumatic Handpiece (K200)
here from the air supply tank. The connector swivels 360° to help eliminate hose binding.
❺ Attachment Lock/Release Collet - Push inward to connect an attachment. Release to lock attachment in place.
❶
❺
❻ Cannulation - Used to stabilize long
❻
wires or pins.
❷ ❸
❹
The Mini-Driver handpiece will accept all the attachments listed on pages 8 through 19.
❶ Activation Trigger - Used to activate the handpiece when the direction button is in either the forward or reverse position.
❷ Safety Slide - Slide the safety slide upward to place the handpiece in the safe, or non-operating position. Slide downward to place the handpiece in an operating mode.
❸ Direction Button - Press this button inward to place the handpiece in the forward (clockwise) direction. Press in the opposite direction for reverse (counterclockwise).
3
2.0
2.1
SYSTEM INSTALLATION and OPERATION
CAUTION: Do not exceed 110 psi (7 kg/cm2) operating pressure unless a hose longer than the standard 10 ft. Air Hose (REF A201) or extension hose is used. Add an additional 1 psi for every extra foot of hose.
Power Source and Regulator Installation and Operation
The Mini-Driver pneumatic handpiece should be operated at 110 psi (7 kg/cm2) for maximum operating efficiency, and should be monitored by the operating pressure gauge of the regulator. Lower pressure setting can be set for lower speed and torque requirements. Pressure must be set with the instrument running to ensure proper operating pressure.
WARNING: Not for inhalation. Does not support life. For use with powered surgical devices only. Research and experience have shown that waterpumped dry nitrogen is the ideal source for pneumatically-powered surgical instruments. Water-pumped dry nitrogen is 99.97% pure, and will not support combustion or corrosion. Compressed dry nitrogen is recommended as the pneumatic power source. It is available in standard cylinders.
Never start a procedure if the operating pressure gauge indicates less than 500 psi (35.1 kg/cm2) in the tank. Never run the tank pressure below 200 psi (14.0 kg/cm2). The tank should be thoroughly wiped off with disinfectant and draped prior to placement in the operating room. Always have the tank securely fastened to a stable object.
Compressed dry nitrogen must meet the following specifications to ensure optimum safety for both patient and instrument. Nitrogen Content: 99.97% pure, dry nitrogen.
1.
Quality Assurance: To obtain the quality of gas needed, “water-pumped dry nitrogen, or liquid nitrogen, pumped dry” should be specified. Nitrogen is readily available from gas supply houses in H cylinders holding slightly more than 300 cubic feet (8.50 cubic meters). Initial set-up costs are relatively inexpensive as compared to compressed air. Nitrogen can be placed in the operating room or in a storage area and piped into the operating room. Manifold systems are available to eliminate frequent tank changes.
4
Prior to set-up in the operating room, open the tank valve (counterclockwise) slowly and allow enough gas to escape to blow out any debris that may have accumulated in the valve. Stay clear of the opening and the back of the tank during this procedure. Return the valve to the closed position.
2.
Install the regulator with a 1 1/8 inch wrench.
NOTE: The threaded adaptor of the nitrogen regulator is designed to fit nitrogen fittings only. Incompatibility of the regulator and tank indicates a gas source other than nitrogen or an improper regulator for use with a nitrogen tank. 3.
4.
Slowly turn the tank valve fully open (counterclockwise). This will allow nitrogen to pressurize the regulator.
5.
Insert the male Schrader end of the hose into the female Schrader on the regulator with an upward thrust.
6.
To connect the handpiece to the hose.
Once the regulator is securely installed, ensure the regulator knob is in the full off position by turning the regulator control knob counterclockwise. SUDDEN PRESSURE EXERTED TO THE REGULATOR MAY CAUSE INTERNAL DAMAGE.
(a) Place the handpiece safety slide in the safe (up) position.
5
(b) Before connecting the hose to the handpiece, ensure that the O-Ring on the end of the hose coupling is in place. If damage is present, replace the O-Ring (REF 8026).
8.
Operating pressure is established by gradually turning the regulator control knob clockwise. ALWAYS establish the designated pressure on the operating pressure gauge with the instrument running.
9.
To operate the handpiece:
(c) Grasp the hose coupling and insert it into the handpiece hose connector on the bottom of the handpiece.
8026 O-Ring
(a) Release the safety by sliding the safety slide downward. (b) Place the directional control button to the desired operating position, either forward (F) or reverse (R).
(d) Grasp the handpiece hose connector to prevent it from turning and twist the hose coupling to the right (clockwise). Slightly pull on the hose so the internal pins securely engage in the indentations.
(c) Depress the trigger.
(e) To remove the hose from the handpiece, reverse steps 6a and 6b. 7.
a
With the safety slide still in the safe position, install the desired attachment and accessory at this time by referencing “2.2.1 Connecting/Removing Attachments” on page 8.
c
6
b
10. While depressing the trigger adjust the nitrogen regulator until the gauge indicates 110 psi.
12. If the Hall Pneumatic Connector* is being used: (a) Locate the button marked “PRESS”.
11. Before removing the instrument from the regulator:
(b) Depress and hold the button until the audible release of residual gas is completed.
(a) Close the tank valve by turning it clockwise. (b) Activate the instrument to bleed off line pressure. (c) Turn the pressure regulator knob counterclockwise until it stops. (d) Turn the female Schrader to the right to disengage the male Schrader fitting. (e) The hose can then be removed from the connector. Hold the end of the hose securely when disengaging the male Schrader fitting to prevent possible damage to the diffuser.
(c) Release the button and remove the hose. (d) If the hose cannot be easily removed, depress the “PRESS” button again, release it and remove the hose.
* U.S. Patent 4,863,201 7
❶
❷
❺
❸
❹
❻ ❼
❽
2.2
❾ ❿
Attachments and Accessories
2.2.1
❶ High Torque Jacobs Chuck (K210)
Connecting/Removing Attachments
All Mini-Driver Handpiece attachments connect/disconnect in the same manner. See pages 9 through 16 for attachment information.
❷ 1/4” Jacobs Chuck (K109) ❸ 5/32” Jacobs Chuck (K110)
1.
❹ Automatic Pin Driver (K211)
To connect an attachment: (a) Ensure the handpiece is in the safe, or off position.
❺ Automatic Wire Driver (K111A)
(b) Press the lock/release collet and insert the arbor end of the attachment into the handpiece. Release the lock/release collet to secure the attachment to the handpiece.
❻ ASIF/AO Twist Drill Chuck (K114A) ❼ Sagittal Saw (K220) ❽ Sagittal Saw (K120) ❾ Hudson Chuck (K113)
(c) Ensure the attachment is secure by pulling it outward.
❿ Trinkle Chuck (K112)
8
NOTE: On attachments that contain alignment pins, guide the alignment pin into one of the four available slots on the nosepiece.
2.2.2
Pin and Wiredriver Attachments
Insertion of pins and wires, and the functionality of the handpiece with either pins or wires, is the same with either attachment.
2.2.2.1
Pin Driver Attachment (K211)
Nosepiece Adjustment Sleeve
(d) To remove the attachment, repeat steps 1(a) and 1(b) and pull out the attachment.
Pin Grasping Lever
The Automatic Pin Driver is designed to drive pins (wires) and drill bits compatible with the specifications below: Through Cannulation: 1.6 - 4.0 mm (0.062 in to 0.156 in.) (1/16 - 5/32 in.)
9
2.2.2.2
Wiredriver Attachment (K111A)
2.2.2.3 1.
Pin and Wire Insertion
To insert a pin or wire: (a) Ensure the handpiece is in the safe position before inserting or removing a pin or wire. (b) Rotate the adjustment sleeve until the desired pin/wire size graduation appears on the shaft of the nosepiece. Do not turn the adjustment sleeve more than one turn past the marked graduation limits.
Nosepiece Adjustment Sleeve Wire Grasping Lever
The Automatic Wire Driver has a quick release for easy wire insertion, removal and advancement. Through Cannulation: 0.7 - 1.8 mm (0.028 in to 0.071 in.) (1/32 - 5/64 in.)
(c) Insert the pin or wire. While holding the nosepiece, tighten the adjustment sleeve until the pin or wire is held firmly in place.
10
(d) Loosen the adjustment sleeve one half turn. The pin or wire should slide freely within the Pin/Wire Driver until the grasping lever is depressed.
2.2.3
(e) For pin/wire sizes that fall between the pin/wire size graduation, loosen the adjustment sleeve one full turn. The pin or wire should slide freely within the Pin/Wire Driver until the grasping lever is depressed. 2.
NOTES: 1.
The K120 Sagittal Saw attachment only accepts K120 and K130 series blades.
2.
For more precise osteotomies, lower cutting temperatures, and reduced instrument wear, use a new blade for each procedure.
3.
Sagittal Saw blades are single-use only. Dispose of properly after use.
1.
To attach the Sagittal Saw attachment, reference “2.2.1 Connecting/Removing Attachments” on page 8.
To operate the handpiece: (a) Release the safety and place the handpiece in the forward position. (b) To grip and drive the wire or pin, depress the grasping lever until flush with the handpiece and depress the trigger.
3.
Sagittal Saw Attachment (K120)
To reposition the handpiece on the wire or pin: (a) Release the trigger and grasping lever. (b) Slide the handpiece along the wire or pin. (c) Follow step 2 to further drive the wire or pin.
4.
To remove threaded wires from the patient: (a) Insert the wire into the front of the attachment (see step 1(a) through 1(e)). (b) Place the handpiece in the reverse position. (c) Simultaneously squeeze the grasping lever and depress the trigger.
11
2.
The Sagittal Saw attachment may be placed in any of four positions at 90 degree angles.
3.
To attach a blade:
5.
To operate the handpiece, release the safety and depress the trigger.
6.
To remove a blade:
(a) Ensure the handpiece is in the safe position before attaching or removing blades. (b) Press the blade down and onto the holding pins, then push down and back to allow the center retaining button to pop up and lock the blade in place. (c) Ensure the blade is secured by pulling outward on the blade.
(a) Ensure the handpiece is in the safe position. (b) Depress the center retaining button, pull the blade forward and lift off the pins.
4.
The blade may be placed in five positions with a 180 degree radius.
12
2.2.4
(c) Tighten the blade by inserting the K201 Wrench and turning clockwise until secure.
Sagittal Saw Attachment (K220)
NOTES: 1.
The K220 Sagittal Saw attachment only accepts K140 and K150 series blades.
2.
For more precise osteotomies, lower cutting temperatures, and reduced instrument wear, use a new blade for each procedure.
(d) Ensure the blade is secured by pulling outward on the blade.
3.
Sagittal Saw blades are singleuse only. Dispose of properly after use.
1.
To attach the Sagittal Saw attachment, reference “2.2.1 Connecting/Removing Attachments” on page 8.
2.
The Sagittal Saw attachment may be placed in any of four positions at 90 degree angles.
3.
To attach a blade:
4.
To operate the handpiece, release the safety and depress the trigger.
(a) Ensure the handpiece is in the safe position before attaching or removing blades.
5.
To remove a blade: (a) Ensure the handpiece is in the safe, or off position.
(b) Insert the blade into the blade holder in the desired blade position. Blades may be placed in any of five positions with a 180 degree radius.
(b) Insert the wrench and turn one-half turn counterclockwise while simultaneously pulling out the blade.
13
2.2.5
All Jacobs Chuck Attachments
2.2.5.1
5/32” Jacobs Chuck (K110)
CAUTION: Do Not use burs in any Jacobs Chuck attachment. 1.
To attach any Jacobs Chuck attachment, reference “2.2.1 Connecting/Removing Attachments” on page 8).
2.
Insert the desired accessory into the chuck and secure it with the appropriate key. This attachment is designed to drive straight plain shank twist drill bits, pins, and wires compatible with the specifications below: Specifications: Jaw Cannulation:
0 - 4.0 mm (0 to 0.156 in.) (0 to 5/32 in.)
Through Cannulation: 4.0 mm (0.156 in.) (5/32 in.) Associated Chuck Key:REF D298K and 5044-999-53
14
2.2.5.2
1/4” Jacobs Chuck (K109)
2.2.5.3
This attachment is designed to drive large (6 mm - 14 mm) cannulated drill bits and pins. Accepts drill bits and other accessories compatible with the specifications below:
This attachment is designed to drive straight shank twist drill bits, pins, and wires compatible with the specifications below: Specifications: Jaw Cannulation:
High-Torque Jacobs Chuck (K210)
Specifications:
0 - 6.35 mm (0 to 0.25 in.) (0 to 1/4 in.)
Jaw Cannulation:
Through Cannulation: 4.0 mm (0.156 in.) (5/32 in.)
0 - 6.35 mm (0 to 0.25 in.) (0 to 1/4 in.)
Through Cannulation: 2.4 mm (0.094 in.) (3/32 in.)
Associated Chuck Key:REF D298L and 5044-999-52
Associated Chuck Key:REF D298L and 5044-999-52
15
2.2.6
(c) Ensure the attachment is secure by pulling it outward.
Trinkle Chuck Attachment (K112)
(d) Ensure the accessory is securely seated in the attachment before use by pulling outward on it. 3. This attachment is designed to drive drill bits, automatic screwdrivers, and other accessories with Trinkle fittings. Specifications: Through Cannulation: 4.0 mm (0.156 in.) (5/32 in.)
1.
To attach a Trinkle Chuck attachment, reference “2.2.1 Connecting/Removing Attachments” on page 8).
2.
To insert a Trinkle Shank accessory into the Trinkle Chuck attachment: (a) Pull the locking sleeve chuck back. Insert the accessory and release the locking sleeve. (b) Turn the accessory in the chuck until it locks.
16
To remove the accessory, pull back the locking sleeve chuck and remove the accessory.