HELMER
Platelet Systems- Incubators and Agitators
Models PC900 and PC1200 Operation, Service and Maintenance Manual Ver K
Operation, Service and Maintenance Manual
28 Pages
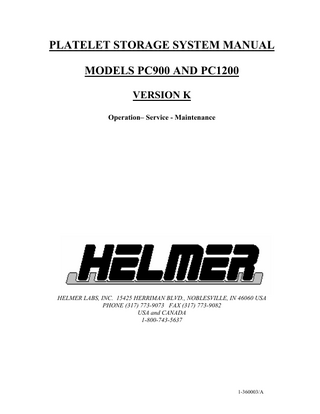
Preview
Page 1
PLATELET STORAGE SYSTEM MANUAL MODELS PC900 AND PC1200 VERSION K Operation– Service - Maintenance
HELMER LABS, INC. 15425 HERRIMAN BLVD., NOBLESVILLE, IN 46060 USA PHONE (317) 773-9073 FAX (317) 773-9082 USA and CANADA 1-800-743-5637
1-360003/A
Contents Page Installation.……………………………………………………………….……. 2
Controls and Components.……………………………………………….… 3 Operating Instructions.……………………………………………………… 5 A. Description of Digital Controller Parts B. Controller Program - Functions and Values C. Setting the Chamber Temperature D. Setting the Alarm E. Setting the "Lockout" Function F. Alarm Timer Adjustments G. Power Failure Alarm H. Installation of Platelet Agitator
Quality Control.……………………………………………………………….
10
A. Calibration of the Digital Controller B. Calibration of the Chart Recorder C. Alarm System Test
Central Alarm Hook-up.…………………………………………………….
12
Cleaning.………………………………………………………………………… 13 Periodic Maintenance.……………………………………………………….
13
Parts List.……………………………………………………………………….
14
Refrigeration Recharging Chart.……………………………………….…
15
Wiring Schematic.…………………………………………………………….
16
Troubleshooting.………………………………………………………………. 21 A. Electrical B. Alarms and Controller C. Chart Recorder D. Chamber Temperature E. Other Limited Warranty: Helmer incubators are warranteed for one year on materials and labor at our factory. Liability in all events is limited to the purchase price.
1
1-360003/A
Installation 1) Carefully unpackage your new Helmer Platelet Incubator. 2) Select a permanent location keeping the following points in mind: 1. Allow at least 4 inches of air space at the back of the unit for adequate air circulation - do not push the unit tight against a back wall. 2. There must be a grounded outlet with adequate power specifications as listed on the specifications label on the back of the unit. 3. Keep away from direct sunlight or high temperature areas. 3) Turn the power switch to "I" (on) and allow the chamber temperature to stabilize (30 minutes) at the factory preset controller values. While waiting for the chamber temperature to stabilize, carefully continue reading through the instruction manual. All functions in the controller system have been "locked out" at the time of shipment. The settings cannot be altered without proper understanding of the unit and controller. The section entitled "Setting the Lockout Function" describes how to change the lockout feature to make any controller value changes. Before doing so, it is imperative to first understand how the unit operates. The closing of the chamber door is controlled by a gas cylinder. DO NOT force the door to close faster than it does by itself. Doing so could damage the cylinder.
2
1-360003/A
Controls and Components Control Panel: The main control panel is conveniently located in the upper right hand corner of the unit and contains the main power switch, alarm and digital controller. Audible Alarm Shutoff: The audible alarm can be silenced with the shutoff switch that is activated with a key. On the PC900 it is located on the right wall. On the PC1200 it is located on the left side of the control panel components. The key is shipped in the switch in the "alarm off" position. Main Power Switch: The main power switch is located on the control panel and controls all electrical current to the unit. When the switched is turned to "I" (on) the fan, refrigeration, heating and electrical systems all become operative. All unit functions are shut down when the main power switch is turned to "O" (off). Digital Controller: Your Helmer Platelet Incubator incorporates a state-of-the-art PID digital controller system located on the control panel. The controller system provides visual readouts and controlling of the chamber temperature, alarms and other pertinent functions. All settings and calibration inputs are made through the controller touch keys. Chart Recorder: The inkless 7-day temperature recorder monitors the chamber temperature independent of the controller system. Refrigeration and Heating System: Cooling of the chamber is accomplished through a refrigeration system in which the compressor unit runs continuously. Heaters are directed to turn on by the controller system to maintain the set temperature. Chamber Fan: Air circulation is maintained within the chamber by a fan located in the back of the chamber. The fan operates continuously and is off only when the main power switch is turned off. Thermostat Switch (115V only): A high temperature switch is mounted inside the chamber to discontinue power to the heater in the event of heating circuit failure. Specifications: Weight: PC900 - 150 lbs., PC1200 - 195 lbs. For 115 Volt Units; Amps - 9.0; Watts - 1035 For 230 Volt Units; Amps - 4.5; Watts - 1035
3
1-360003/A
4
1-360003/A
Operating Instructions A. Description of Digital Controller Parts (1) Chamber Temperature Present Value - This green readout provides the actual temperature reading that the controller is sensing within the chamber in degrees C. There will be fluctuations in this readout value as it is sensing momentary chamber temperatures. (2) Chamber Temperature Set Value - This orange readout is the set temperature value. This value does not change during normal operation unless changed by the user. It is simply a continuous display of the desired set temperature. (3) Alarm Indicator - If the unit goes into the alarm mode this red lamp will light as a visual indicator. This indicator light turns on immediately when the controller has sensed that the chamber temperature has gone beyond the deviation alarm set values. The audible alarm will delay alarming for a period of time set by the alarm timer adjustment on the circuit board after the controller has sensed an alarm condition. The built-in audible alarm delay prevents unnecessary warnings that may be caused by temporary temperature fluctuations. The small, push-button switch located next to the audible alarm is the alarm interrupt switch. If you wish to silence your audible alarm, yet do not want to turn it off, push this switch. It will reset the time and start the delay period over. (4) Heater on Indicator - This green indicator lamp turns on when the controller is providing output to the heater. It will turn on and off often for short periods of time during normal operation. (5) Set Key - Used for entering into the various programming modes. (6) Digit Shift Key (<) - Used to shift to the various digit placings. (7) Set-Value Decrement Key - Used to reduce the digit values. (8) Set-Value Increment Key - Used to increase the digit values.
5
1-360003/A
B. Controller Program Functions and Values The PID digital controller contains internal programs that effect the operation and accuracy of the controller and alarm system. There are some internal program functions that may be altered by the operator for specific requirements (alarm settings, security lockout and calibration). The remaining program functions must not be altered. The following is a summary of the internal program functions with their proper value settings: Controller Program Name
Instructions to Enter the Program
Function Display Function Readout Value
1. Temperature Selection
press SET key
SV blinks
* 022.0
2. First Program Mode
press SET key for 5 seconds
AL ATU P I D Ar T LCY
* 002.0 0000 (value varies) (value varies) (value varies) 0100 0001 * 0101
SL1 SL2 SL3 SL4 SL5 SL6 SL7 SL8 Pb oH AH SLH SLL
0101 0000 1000 0010 0000 0001 0010 0000 * value varies 000.2 000.1 040.0 015.0
3. Second Program Mode
press SET key and Digit Shift Key for 5 seconds
* - These values may be altered by the operator. All other values must not be changed. Once again, only the:
"SV" (set chamber temperature value) "AL" (deviation alarm value) "LCY" (security lockout) "Pb" (controller calibration)
function values may be altered by the operator, all other function values must remain as set by the factory. The above values have been listed as a reference guide as to the proper function value settings. If you have any questions on the function values, please call a Helmer customer service representative. 6
1-360003/A
C. Setting the Chamber Temperature To alter the chamber temperature set value (controller part #2), press the SET key (5). The least significant orange indicator digit will be bright and the other digits will be fluttering (the digit values cannot be changed if the controller is locked out - refer to section E, Setting the "Lockout" Function). The bright digit may be changed by pressing on the up (8) and down (7) keys. To alter to the other digits, press the digit shift key (6) and then press the up and down keys as needed to change the value. After finishing the desired setting, press the SET key. All of the set-value digits light brightly and the controller returns to the display mode. The controller will now proceed in bringing the chamber temperature to the new set value temperature. D. Setting the Alarm The alarm used in this system is called a "deviation alarm." A deviation alarm is a plus/minus setting based off of the set temperature value (SV). The factory setting for the alarm deviation is 2.0 degrees C. Thus, with the set temperature value at 22.0, the controller would go into the alarm mode if the chamber temperature rose to 24.0 (+2.0 degrees) or declined to 20.0 (-2.0 degrees). alarm on)_______________<>________________(alarm on -value set point +value The digit values cannot be changed if the controller is locked out - refer to section E, Setting the "Lockout" Function. To change the deviation alarm value, press and hold the SET key for 5 seconds until the controller displays the first program mode (The first setting is "AL" in the first program mode - refer to the Controller Program Values, section B). The green display will read "AL" which is the deviation alarm function and the orange display will show the deviation alarm value with the least significant digit brightly lit. Using the arrow keys, change the value to the desired setting. To save the new input value into memory, press the SET key once, otherwise the new input value will not be stored in memory. To exit, hold the SET key for 5 seconds until the normal operating mode appears.
7
1-360003/A
E. Setting the "Lockout" Function The controller has been set in the full "lockout" mode at the factory. This means that the setting values cannot be changed until the "lockout" value is changed. This security feature allows you to protect various input values from any unauthorized changes. To change the lockout function, press and hold the SET key for 5 seconds to get into the first program mode. There are many program functions within the first program (refer to section B, Controller Functions and Values). Pressing once on the SET key will advance you to the various functions within the program. Continue pressing the SET key until the "LCY" (lockout) function appears. The various "LCY" input values with descriptions that may be used are as follows: Input Value
Description
0000
None of the input data is locked and all controller values can be freely changed at any time.
0101
All of the input data is locked and cannot be changed without resetting this function (this is the input value set at the factory).
0110
Only the chamber temperature set value (SV) can be changed.
If you are desire to change the chamber temperature set value (SV), alarm value (AL), or controller calibration value (Pb), the LCY function needs to read 0000 (or 0110 to change only the set value). This will allow you to change any of the function values. After making any changes it is important to reset the LCY function to the desired value. To return to the normal operating mode, press the SET key once to save any changed values into memory and then hold the SET key for 5 seconds. Do not change any other functions in the parameter mode except for the "AL" and "LCY" functions. Alteration of remaining functions will affect operation and accuracy.
8
1-360003/A
F. Alarm Timer Adjustments The temperature alarm has a variable delay setting, which can be changed to set the length of time desired before triggering the audible and central alarm relays. The time can be set from approximately 0 to 8 minutes. The adjustment is made with a dial located on the internal circuit board. Turning the dial to its extreme clockwise position sets the delay time to 8 minutes. Turning the dial to its extreme counter-clockwise position sets the delay time to 0 minutes. See the schematic for the "Alarm Timer Adjustment" location and access to this dial. G. Power Failure Alarm The same circuit board mentioned above also has a line-connected rechargeable battery, which powers a power failure alarm. In the event of a power interruption caused by a power outage, an unplugged cord, a tripped circuit breaker or a blown fuse, the audible alarm will sound and the central alarm relay will trigger. To disable this alarm, use the keylock switch located on the front control panel of the unit. Disabling the power failure alarm also disables the audible portion of the temperature alarm. However, in this disabled mode the red alarm light on the controller and the central alarm output are still functional. It is recommended to place the key for this switch in a location separate from the switch. H. Installation of Platelet Agitators To install a platelet agitator, open the roll-top door and carefully place the platelet agitator into the center of the incubator chamber. Plug the platelet agitator power cord into the outlet located on the back wall of the chamber. Make sure that the power cord is properly secured to prevent cord damage when the drawers are rolled in and out. Turn the platelet agitator power switch "On" and verify that it is centered within the chamber.
9
1-360003/A
Quality Control A. Calibration of Digital Controller To verify that the digital controller is calibrated correctly, place a calibrated mercury thermometer inside the incubator chamber. Allow the chamber temperature to stabilize for 30 minutes and then take a reading from the thermometer. If the thermometer reads the same as the green PV display then the controller is calibrated correctly. If there is a variance in the temperature readings, then the digital controller display needs to be calibrated. The operating temperature and alarm settings should operate within a +/- 1.0 degrees C of the set values. To recalibrate the PV value, first set the "LCY" (lockout) function to 0000. Press the SET key once to store the new 0000 value into memory. Next, press and hold the SET key and the Digit Shift Key (<) until "SL1" appears in the green display. Press the SET key to move through the various functions (refer to Controller Program Functions and Values section of this manual) until you get to the "Pb" function. The "Pb" funciton is the calibration function that allows you to alter the green display reading to the proper set temperature. As an example, if the thermometer reads 21.5 when the controller reads 22.0, then the controller display needs to be reduced by 0.5 of a degree. Using the touch key arrows reduce the "Pb" value by 0.5 of a degree. If the thermometer reads 22.5 when the display reads 22.0, then increase the "Pb" value by 0.5 of a degree. After the desired change has been made, press the SET key once to hold the new input value into memory. Then return to the operating display by holding both the SET key and the Digital Shift Key (<) until the temperature display re-appears. Allow 30 minutes for the chamber temperature to stabilize and make a new reading to verify that the controller is giving the proper temperature readout. Make any additional adjustments as needed until the controller readout is properly calibrated. B. Calibration of the Chart Recorder Allow the chamber temperature to stabilize at 22.0 degrees (30 minutes). Then observe what temperature the chart recorder is indicating. If the chart recorder is marking at 22.0 degrees, then the chart recorder is properly calibrated. If the chart recorder is not marking at 22.0 degrees, then the marking stylus needs to be adjusted. To adjust the marking stylus, loosen the small screw at the top of the stylus. Set the stylus point at 22.0 degrees and tighten the screw down. The chart recorder stylus should now mark at 22.0 degrees.
10
1-360003/A
C. Alarm System Tests To test that the deviation alarm system is working properly, it is recommended to follow methods that may be recommended by the AABB or governing organizations for such alarm system checks. Two ways of conducting a deviation alarm system test are as follows: Method 1: This first alarm system check method requires only a short period of time to conduct. Note that this first method does not test the high and low temperature limits. This method simply verifies that the general alarm system is working properly. Referring back to a previous section on "Setting the Alarm," go into the first program mode and set the "AL" function value to "000.0" degrees. Next, press the SET key once to advance to the next function (ATU). The alarm indicator light should turn on saying that the controller is in the alarm mode. The audible alarm will not sound for about 10 minutes as a result of the built-in alarm delay system. Remember to reset the "AL" function to the desired value when finished with this test. Method 2: This second method will test the high and low alarm points without altering the actual chamber temperature. The controller thermocouple is located within the chamber on the bottom portion of the back wall. Turn the platelet agitator power switch to off. Remove the cover channel mounted on the sidewall by pulling it forward. Pull the thermocouple out of the holding clip and extend the thermocouple out to the front of the unit. Open the incubator door. With the thermocouple located outside of the incubator, place it into a container with cool water -- the water should be just slightly cooler than the low alarm activation point. Watch for the alarm indicator light to come on. When the alarm light illuminates, take a reading of the controller temperature readout (PV). Do not wait for the audible alarm to sound. It will delay alarming for a period of time set by the alarm timer adjustment on the circuit board. This will take place after the controller has sensed an alarm condition. To test the high alarm activation point place warmer water in the container (slightly warmer than the high alarm activation point) and make a reading when the alarm indicator light comes on. After testing, place the thermocouple back in its holding clip and carefully place the excess thermocouple wire in the plastic holding channel to prevent any wire damage. Note: The controller probe and chart recorder probe are separate probes. This allows the controller to have an exceptionally quick response time, which will give greater temperature uniformity. When this alarm test is done, the chart recorder probe is still mounted in the chamber. This probe responds to temperature change at a much slower rate than the controller probe. Therefore, it would not reflect the correct solution temperature properly at the moment of alarm. Do not leave the controller probe in your test solution for a long period of time. The controller will compensate for what it thinks is a change in chamber temperature by increasing or decreasing the amount of heat to the system.
11
1-360003/A
Central Alarm Hook-up To connect a central alarm system into the platelet incubator you will need to do the following: 1. Turn the power switch off and unplug the unit. 2. Remove the top exterior back panel. 3. Locate the three terminals on the right side of the secondary circuit board. These three outputs are for connecting to a central alarm system. The outside terminal (#16) is the common, the next terminal to the left (#15) is the normally closed contact and the second terminal to the left (#14) is the normally open contact. 4. Connect the central alarm wires to the proper terminals for your alarm system. 5. Cable tie the wires as necessary for stability. 6. Run the central alarm wires through the small grommet located in the back of the exterior panel that was removed. 7. Replace the panel into its correct position. To connect a central alarm system to the agitator alarms in the platelet incubator, see the agitator or motion alarm instructions. A hole is provided on the right side of the chamber wall for wire access to the chamber. Remove the plug on the exterior side of the wall for access.
12
1-360003/A
Cleaning The importance of proper cleaning of your Helmer Platelet Incubator cannot be under estimated. Lack of cleaning of items, such as the condensor fins, can significantly cut down on the life expectancy of this equipment. Painted Exterior - A soft cotton cloth and non-abrasive liquid cleaner should be used for cleaning the exterior surfaces. The doors should be cleaned with a soft cotton cloth and window cleaner. The black condensor fins located on the upper left side in the rear of the unit should be cleaned and vacuumed often. Roll-Top Door - The clear portion of the roll-top door is made of a ploycarbonate material, which is very durable but does scratch easily. Therefore, great care must be taken when cleaning this part of the unit. Lightly wipe the door with a clean and very soft cotton cloth - do not push hard when cleaning and do not rub back and forth across the door. Lightly wipe in one direction. If a cleaner must be used to clean debris off of the door then spray some window cleaner onto the clean rag and then wipe - do not spray the cleaner directly onto the clear part of the roll-top door. Interior - Always turn the power switch off when cleaning the interior of the incubator. A disinfectant cleaner should be used to wipe down the inside stainless steel walls, drawer and interior water drain tray on a regular basis.
Periodic Maintenance It is recommended to conduct the following maintenance items to help keep your Helmer Platelet Incubator in good working condition: Quarterly:
Clean and vacuum condenser grill. Conduct alarm and calibration checks.
13
1-360003/A
Parts List (Model PC900 and PC1200) To order parts for your Helmer Platelet Incubator, indicate the quantity, part number and description with your purchase order number. Please provide the model number and serial number as well. Stock Number
Description
400211 400247 120160 120157 120158 120074 120097 400157 400158 120081 120038 220064 120170 120171 120182 120183 120255 120256 400172 400173 220210 120198 120220 120197 120227 120250
Digital Controller Secondary Circuit Board Audible Alarm On/Off Power Switch - 120V On/Off Power Switch - 240V Chamber Electrical Outlet - 120V Chamber Electrical Outlet - 240V Chart Recorder Assembly - 120V Chart Recorder Assembly - 240V Chart Recorder Motor - 120V Chart Recorder Motor - 240V Chart Recorder Paper (50/box) Chamber Fan Motor - 120V Chamber Fan Motor - 240V Cartridge Heater - 120V Cartridge Heater - 240V Compressor - 120V Compressor - 240V Chamber Cover Assembly (PC900) Chamber Cover Assembly (PC1200) Chamber Cover Damping Cylinder Fuse, 6.3 Amp - 240V Circuit Breaker, Amp - 120V Alarm Delay Switch Audible Alarm Shutoff Switch Heater Thermostat (115V units only)
14
1-360003/A
Refrigeration Recharging Chart
Approximate recharging weight is as follows: PC900 & PC1200 - 5 oz. (Note: Refrigerant is R134A) After recharging follow the procedure below: Allow the incubator chamber temperature to stabilize at 22.0 degrees C. With a pressure gauge set on the refrigeration lines, the refrigerant pressure should be as follows:
Room Temperature C 18 19 20 21 22 23 24 25 26 27 28 29 30
Low Side (suction) Pressure
F
PSI
64.4 66.2 68.0 69.8 71.6 73.4 75.2 77.0 78.8 80.6 82.4 84.2 86.0
29.0 29.5 30.0 30.5 31.0 31.5 32.0 32.6 33.3 33.5 34.3 34.8 35.4
A fluorescent additive has been added to the refrigeration system. Leaks may be diagnosed with the aid of an ultraviolet light. Shine the light on joints where leaks may be occurring. A leak is identified by a bright film residing at the site of the leak.
15
1-360003/A
Wiring Descriptions PC900 & PC1200 (C100 Voltage Pulse) Digital Controller Terminals Terminal
Wire Color
Description
1
----
This terminal is not used.
2
red
Voltage output to secondary circuit board and audible alarm (12 volts (+) dc).
3
----
This terminal is not used.
4
orange
Voltage output to secondary circuit board for heater system (1.2 volts (+) dc).
5
blue
Voltage output to secondary circuit board for heater system (1.2 volts (-) dc).
6
white or blue
Incoming power supply from secondary circuit board and power to chart recorder.
7
black or brown
Incoming power supply from secondary circuit board and power to chart recorder.
8
blue
Type "T" thermocouple input(+)
9
red
Type "T" thermocouple input (-)
16
1-360003/A
Secondary Circuit Board Terminals (PC900 and PC1200) Terminal (T1) Wire Color
Description
1
orange
Voltage input for heater system (1.2 volts (+) dc).
2
yellow
Voltage output to alarm(12 volts (-) dc).
3
----
This terminal is not used.
4
red
Voltage input for alarm delay system (12 volts (+) dc).
5
dark blue
Voltage input for heater system (1.2 volts (-) dc).
6
black or brown
Power input from switch.
7
black or brown
Power output to chamber heater.
8
black or brown
Power output to controller.
9
white or blue
Power input from switch.
10
----
This terminal is not used.
11
white or blue
Power output to controller.
12
black or red
Power output to chamber heater.
13
----
This terminal is not used.
14
Central Alarm (normally open).
15
Central Alarm (normally closed).
16
Central Alarm (common).
Terminal (T2) Wire Color
Description
A1
black or brown
Main power input to unit and power failure alarm.
A2
black or brown
Main power to power switch.
B1
white or blue
B2
white or blue
Main power input to unit and power failure alarm. Main power to power switch.
17
1-360003/A
Terminal (T3) Wire Color
Description
1
black or brown
Power output to chamber fan.
2
black or brown
Power output to chamber outlet.
3
black or brown
Power output to compressor unit.
4
white or blue
Power output to chamber fan.
5
white or blue
Power output to chamber outlet.
6
white or blue
Power output to compressor unit.
18
1-360003/A
Component List for Schematic Component
Location
Access
A - Audible alarm
Front control panel
Remove back panel
B - Alarm delay switch (NC)
Front control panel
Remove back panel
C - Main power switch
Front control panel
Remove back panel
D - Chart recorder
Top front panel
Open chart panel
E - Chamber fan
Inside chamber(back wall)
Remove chamber back wall
F - Chamber heater
Inside chamber(behind back wall)
Remove chamber back wall
G - Compressor
Top of unit
Remove top access panel
H -Thermocouple
Inside chamber (bottom of back wall)
Remove from clip
I - Temperature controller
Front control panel
Remove back panel
J - Secondary circuit board
Top of unit (inside)
Remove back panel
K - Condensor fan
Rear of unit(behind condensor grill)
Remove top access panel
L - Chamber outlet
Inside chamber(back wall)
Remove chamber back wall
M - Power failure alarm switch Top front panel
Remove back panel
N - Thermostat Switch (115V units only)
Remove chamber back wall(back wall)
Inside chamber
Components on secondary circuit board P1 - Alarm Timer Adjustment
See secondary circuit board above
19
1-360003/A