Integra LifeSciences Corporation
Head Support Systems
MAYFIELD 2 Base Unit Instructions Manual Rev HA Jan 2021
Instruction Manual
143 Pages
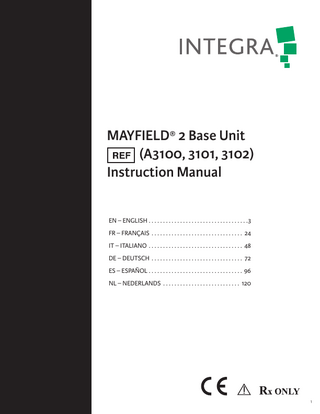
Preview
Page 1
MAYFIELD® 2 Base Unit (A3100, 3101, 3102) Instruction Manual EN – ENGLISH... 3 FR – FRANÇAIS... 24 IT – ITALIANO... 48 DE – DEUTSCH... 72 ES – ESPAÑOL... 96 NL – NEDERLANDS... 120
1
EN – ENGLISH
2
EN – ENGLISH
Symbols used on Labeling CAUTION Hazards which could result in equipment or property damage.
WARNING! Hazards which could result in personal injury or death 0123
EC REP
Product complies with the requirements of MDR 2017/745 Authorized EC Representative in the European Community. Attention, consult accompanying documents
REF
Product catalog number Manufacturer Caution: Federal (USA) Law restricts this Device to sale by or on the order of a Licensed practitioner. This device is not indicated for use in MR environment. Medical Device
Indications For Use/Intended Purpose The MAYFIELD® 2 Base Unit is intended to be used to support a patient during diagnostic examination and/or surgical procedures where a rigid support between surgical table and headrest, or skull clamp is necessary, positional freedom is required.
WARNING! Failure to read and follow instructions and warnings furnished in this instruction manual and the instructions and warnings included in the associated skull clamp instruction manual may result in skull pin slippage and serious patient injury, such as scalp lacerations, skull fracture, or even death. Failure to properly position patient and to fully tighten and secure all adjustable portions of this or any similar device may result in skull pin slippage and serious patient injury, such as scalp laceration, skull fracture, or even death. Monopolar electrosurgical equipment with operational voltages that exceed 3000 V may result in patient harm when this system is used in conjunction with a skull clamp. The user must make sure that any threaded connections are secure and starbursts have meshed (where applicable) after adjustments are complete. Failure to do so may result in serious patient injury.
CAUTION! Always make sure the base unit is properly secured to the operating table. The base unit must not be used if the device appears to be damaged or functioning incorrectly. Do not use any tools on this equipment to secure. Over-tightening any of the adjustment screws or knobs may result in damage to the unit. If unit does not appear secure after hand-tightening, do not use the unit and contact your MAYFIELD Representative or the MAYFIELD Service Team. Over-extending or overloading the base unit may result in unintended movement, shortened product life and/or damage to the unit. Do not alter the construction of this device as it may result in serious patient injury. Not all MAYFIELD products can be cleaned and decontaminated in the same manner as those labeled as MAYFIELD 2. Consult the individual instructions for use (for each device) on the proper care and cleaning procedures. 2
EN – ENGLISH
Intended Population MAYFIELD Skull Clamp fixation devices are not recommended for use on children under five (5) years of age. Extreme caution should be exercised in pediatric cases because of the thin skull.
Description The MAYFIELD 2 Base Unit (REF A3101, A3102, A3100) is designed to provide attachment from the operating room table to MAYFIELD Skull Clamps for rigid skeletal fixation or MAYFIELD Horseshoe Headrests for procedures where support only, and not rigid fixation, is required. The MAYFIELD 2 Base Unit is designed for patient positioning in the prone, supine lateral or park-bench and sitting positions. The Support Rod spacing may be readily adjusted to fit most operating room tables. No tools are required. See Attachment to Operating Room Table for instructions to adjust the Support Rods.
MAYFIELD 2 Base Unit, Standard A3101
MAYFIELD 2 Base Unit, Narrow A3100
MAYFIELD 2 Base Unit, International A3102 Figure 1 MAYFIELD 2 Base Unit Catalog Numbers A Standard MAYFIELD 2 Swivel Adaptor (A3018) is an integral component of the Base Unit. A separate, optional MAYFIELD 2 Tri-Star Swivel Adaptor (A3008) is available as an accessory product when image-guided surgery (IGS) systems are used in the procedures. The Tri-Star Swivel Adaptor provides two extra starbursts for attachment of the ancillary IGS equipment. Each MAYFIELD 2 Base Unit purchased (A3100, A3101, or A3102) includes: 1- MAYFIELD 2 Base Unit 1- MAYFIELD 2 Swivel Adaptor (A3018) OPTIONAL: MAYFIELD 2 Tri-Star Swivel Adaptor (A3008) 3
EN – ENGLISH
1. Left Bracket 2. Left Bracket Lock Knob 3. Connecting Tube 4. Base Handle Assembly 5. Locking Lever 6. Transitional 7. Swivel Lock Knob 8. SwIvel Adaptor (A3018) 9. Headrest Lock Knob 10. Right Bracket
Figure 2A MAYFIELD 2 Base Unit Components
1. Transitional 2. Locking Lever 3. Latch 4. Base Handle Assembly
Figure 2B MAYFIELD 2 Base Handle Components 4
EN – ENGLISH
Figure 3 OPTIONAL MAYFIELD 2 Tri-Star Swivel Adaptor (A3008)
The MAYFIELD 2 Base Unit is designed for use with the following equipment: A1008 MAYFIELD General Purpose Headrest A1011 MAYFIELD Horseshoe Headrest* A1012 MAYFIELD Adult Horseshoe Headrest A1015 MAYFIELD Crossbar Adaptor** A1031 MAYFIELD (A&B) NeuroGen Adaptor A1051 MAYFIELD Pediatric Horseshoe Headrest* A1059 Modified MAYFIELD Skull Clamp A1073 Posterior Cervical Support A1108 MAYFIELD Triad Skull Clamp A1109 MAYFIELD Horseshoe Conversion Adaptor A1112 MAYFIELD Infinity Support System A1113 NeuroGen Adaptor A1114 MAYFIELD Infinity Skull Clamp A1114A MAYFIELD Infinity Skull Clamp A2000 MAYFIELD 2000 Skull Clamp A3059 MAYFIELD 2 Skull Clamp *A1109 MAYFIELD Headrest Conversion Adaptor is required for use **A1060 Universal Side Rail Fittings is required for use
Note: Use of MAYFIELD products and accessories in conjunction with other manufacturer’s stabilization equipment is not recommended. 5
EN – ENGLISH
Inspection Always inspect MAYFIELD equipment before and after use. If a component appears damaged and/or does not seem to function properly, do not use the device and immediately send the instrument to an authorized Integra repair center for evaluation, repair or replacement.
Care and Maintenance Your Integra representative will regularly perform a comprehensive inspection of your MAYFIELD equipment. In addition, to ensure that factory-set calibrations remain in good working order, a Preventative Maintenance is required yearly at the Integra authorized Service & Repair Center. Integra will do its best to provide comparable Service loaner equipment while your MAYFIELD undergoes this required yearly maintenance. To ensure proper function and to extend the life and performance of the equipment, Integra LifeSciences requires the following: Required Action
Required Frequency
Return the device to the Integra LifeSciences Repairs department for detailed inspection and servicing.
Once / year
Request that Integra NeuroSpecialists perform routine inspections of the device
Twice / year
In the absence of proper care and servicing of the device, negative effects may be seen after repeated processing over time which may lead to reduced performance. Contact information: See the Service and Repair section for contact information on how to return your device for periodic servicing and to request periodic inspections. NOTE: Any serious incident that has occurred in relation to the device for the user and/or the patient should be reported to the manufacturer and the competent authority of the member state in which the user and/or patient is established.
Device Disposal NOTE: Follow hospital procedures for disposal of this device. CAUTION! If unit is dropped or mishandled, it should be inspected for damage. (REF Inspection section of this Instruction manual). If damage occurs, do NOT use; return the complete device immediately to Integra for inspection.
6
EN – ENGLISH
Directions for Use Attachment of the Base Unit to Operating Room Table: MAYFIELD 2 Base Unit (3100) Left Bracket may be adjusted along the Connecting Tube to allow the Support Rod to accommodate table receptacles spaced 4-1/2” to 8-1/4” (114mm to 209.5mm) apart. MAYFIELD 2 Base Unit (3101) Left Bracket may be adjusted along the Connecting Tube to allow the Support Rod to accommodate table receptacles spaced 5-1/8” to 8-1/4” (130mm to 209.5mm) apart. MAYFIELD 2 Base Unit (3102) Left Bracket may be adjusted along the Connecting Tube to allow the Support Rod to accommodate table receptacles spaced 6-5/8” to 15-3/4” (168mm to 400mm) apart. 1. Locate and loosen the Left Bracket Lock Knob on the backside (See Figure 4) of the Left Bracket and slide the Left Bracket smoothly along the the Connecting Tube until the desired width between the Support Rods is achieved. 2. Mount the Base Unit to the operating room table by aligning the two Support Rods with receptacles at the head end of the Operating Room table, or, in the NeuroGen Adaptor or Crossbar Adaptor. 3. Tighten the Left Bracket Lock Knob to secure the Left Bracket into position. CAUTION! Do NOT use any tools to tighten any knobs on this device. All knobs should be hand tightened only. Use caution not to overtighten. Over-tightening may damage the device.
Left bracket lock knob
Clockwise rotation to tighten
Figure 4 Left Bracket Lock Knob 4. Secure the Base Unit Support Rods to the table by tightening the table lock knobs or the knobs on the NeuroGen Adaptor or Crossbar Adaptor. 7
EN – ENGLISH
Attachment of the Swivel Adaptor (A3018 or A3008) to the Base Unit Insert screw of Swivel Adaptor into clover-shaped Swivel Lock Knob at the end of the transitional arm. Tighten by turning Swivel Lock Knob clockwise and ensure that all starburst teeth are meshed. Do not over-tighten. No tools should be used to attach or remove the Swivel Adaptor from the Base Unit.
Swivel
Swivel Lock Knob
Starburst Teeth
Transitional
Figure 5 Attachment of Swivel Adaptor CAUTION! Confirm the Base Unit stability by positioning (connected to operating table) the components as shown in Figure 6. Exert moderate force against the Swivel Adaptor in the indicated direction shown by arrow 2 in Figure 6. No movement should be observed at any of the joints. If movement is observed, do not use product and contact your MAYFIELD Representative or the MAYFIELD Service Team.
Figure 6 Stability Check 8
EN – ENGLISH
Positioning the Transitional Arm and Swivel Adaptor The handle is equipped with a self-latching feature. To free the Locking Lever, press the latch into the Locking Lever, the lever will move away from its closed position.
Latch
Figure 7 Handle Self-Latching Feature
9
EN – ENGLISH
1. Open the Locking Lever to position the Transitional Arm as desired. The Locking Lever must be in the fully opened position to perform free movement of the Transitional Arm.
Figure 8 Open Locking Lever 2. O nce the Skull Clamp is applied to the patient’s skull, the surgeon will maneuver the patient to the surgical position that is required for the procedure. With the patient in this position, the surgeon will hold the patient’s head and the Skull Clamp and request that the Transitional Arm be brought up to the proper height for attachment of the Skull Clamp to the Swivel Adaptor. a) Once the Transitional Arm is at the proper height for attachment to the Skull Clamp, the mounting screw of the large starburst on the Swivel Adaptor should be inserted into the large starburst of the Skull Clamp and turned clockwise and tightened. Care should be taken to maintain the position of the patient’s head as requested by the surgeon. b) E nsure that the Skull Clamp is securely attached to the Swivel Adaptor by turning the mounting screw on the top of the Swivel Adaptor clockwise to tighten (Figure 9A). Close the Locking Lever. Make certain that all starburst teeth are fully meshed (where applicable) on all joints of the Base Unit after adjustments are complete. (See Figure 9B)
Proper Meshing of Teeth (3x)
Figure 9A Attachment of Skull Clamp
Figure 9B Proper meshing of Starburst Teeth 10
EN – ENGLISH
CAUTION! Before fully tightening, always be certain that the starburst teeth of the Swivel Adaptor and other starburst fittings are the same size and properly mesh. Failure to do so may damage fittings and/or allow unwanted movement of the patient. Figure 10 shows a typical starburst connection and proper meshing of teeth. (See Figures 10A and 10B) Proper Meshing of Teeth
Figure 10A Proper Meshing of Teeth
Improper Meshing of Teeth
Figure 10B Improper Meshing of Teeth
(If attaching a Horseshoe Headrest, bring the Transitional Arm to the proper height. The mounting screw of the large starburst on the Swivel Adaptor should be inserted into the large starburst of either the Horseshoe Headrest or the Conversion Adaptor if used. Turn mounting screw on the top of the Swivel Adaptor clockwise to tighten.)
11
EN – ENGLISH
CAUTION! Keep fingers clear of hinge points when closing the Base Unit Locking Lever. See Figure 11 below. It is recommended that the levers be closed using the palm of the hand.
Figure 11 Locking Mechanism
CAUTION! Always be sure the locking mechanisms are secure after completing table adjustments. Verify that the Transitional Arm is secured in place by confirming that the Locking Lever is engaged. Lift up on the Locking Lever WITHOUT depressing the Latch. The Locking Lever should not be free to open.
Figure 12 Securing Locking Lever 12
EN – ENGLISH
Cleaning of the MAYFIELD 2 Base Unit These instructions are the recommendation of the manufacturer to ensure proper function and to extend the life and performance of the equipment. As the equipment is reprocessed over time, many factors, including water quality used, frequency of inspections and servicing, and method of reprocessing may impact the long term performance of the equipment. Manual cleaning has been shown to exhibit the least amount of degradation of device performance over time, and is therefore the recommended method of reprocessing to extend the long term performance of the equipment. The equipment may also be reprocessed by automated cleaning and disinfection per the instructions contained in this section. No degradation of product performance is anticipated given the device is properly cared for as recommended by the manufacturer. This care includes inspections and periodic servicing, and avoidance of hard water where recommended. In the absence of proper care and servicing, negative effects may be seen after repeated processing over time which may lead to reduced performance.
Considerations: • Follow the instructions exactly as listed in this Instruction Manual and your Hospitals procedures for decontamination, cleaning and to reprocess medical instruments safely. • It is important to know what method of cleaning/decontamination is needed based on what type of debris exposure the equipment has received. This is especially important when there is the possibility of exposure to Highly Infectious Diseases. • This protocol has been validated for cleaning effectiveness only. • Refer to the User Manual to disassemble the product before cleaning . • Refer to the User Manual for further details on product use and set-up. • The user should comply with hospital procedures and local laws and ordinances regarding reprocessing requirements. • Hospitals are responsible for decontaminating and packaging all loaner and demo equipment before returning to Integra. • Integra does not make any claims regarding the effectiveness of the decontamination processes listed in deactivating pathogens, but rather, we are indicating that the device can withstand these procedures with minimal loss of function. • Please clean product using these guidelines prior to first use.
Warnings: • Take all necessary precautions in wearing the appropriate protective equipment (eye/face, protection, gloves as specified in the instructions provided by the cleaning agent. Clean device immediately after each use. • The use of highly alkaline agents may cause some components to tarnish and/or corrode. While this does not affect the performance of the device we recommend that you use an acidic neutralizing agent immediately after each use to avoid the occurrence of cosmetic changes. • Follow all instructions of the detergent, equipment washer, and autoclave manufacturer. • Follow the detergent concentration, temperature, exposure time, material compatibility specifications, and disposal directions of the cleaning agent as recommended by the manufacturer. • Use only the cleaning tools mentioned in this manual. Never use metal brushes. • Failure to follow the instructions of this document could result in damage to the equipment.
13
EN – ENGLISH
MAYFIELD 2 Base Unit - A3101 (Including A3018 Swivel Adaptor) Preparation for Cleaning and Reassembly 1. Remove skull clamp from the base unit. 2. Remove base unit from the operating room table. Disassembly
Inspecting for cleanliness
Reassembly
1– R emove swivel adaptor (1) from the base unit (2). 2– Keep base unit (2) in the UNLOCKED position before cleaning. 3– Do not attempt to disassamble further.
Pay close attention to: 1– Area around the locking mechanism (3). 2– Teeth of the starburst (both sides) (4) .
1– Tighten swivel adaptor (1) to the base unit (2). 2– Store the base unit (2) with the locking handle (5) in the closed position.
(1) swivel adaptor
(4) teeth
(2) base unit
(3) locking mechanism (5) locking handle
14
EN – ENGLISH
MAYFIELD 2 Standard Swivel Adaptor - A3018 Disassembly
Inspecting for cleanliness
1– R emove swivel adaptor (1) from the base Pay close attention to: unit (2). 1– Teeth of the starbursts (3). 2– Do not attempt to disassamble further. 2– Area around the locking screw (2). 3– The base of the swivel adaptor for organic debris.
Reassembly
N/A
(3) teeth
(2) locking screw
(1) swivel adaptor
TriStar Swivel Adaptor - A3008 Disassembly
Inspecting for cleanliness
Reassembly
1– C ompletely remove swivel adaptor from any components. 2– Unlock the TriStar bar (1), remove Locking screw (2) and TriStar bar (1).
Pay close attention to: 1– Teeth of the starbursts (3). 2– Area around the locking screw (2). 3– The base of the swivel adaptor for organic debris.
1– Re-install the dual TriStar bar (1). 2– Engage the locking lever (4) on the TriStar bar (1). 3– Insert and firmly press the torque screw (2) in place.
(1) TriStar bar
(2) locking screw
(4) locking lever (3) teeth
15
EN – ENGLISH
Step 1: Decontamination after Exposure to highly infectious diseases* When the MAYFIELD 2 System has been exposed to pathogens that resist normal disinfection methods, the product should be handled more carefully. The following steps are recommended in accordance with the World Health Organization (WHO) Protocol for decontamination of highly infectious diseases**: • Keep soiled areas of the device moist. Do not apply gluteraldehyde, alcohol or formalin to the device until the decontamination process is complete.
NOTE: Do not subject the base unit & skull clamp to automated cleaning processes until after the decontamination procedure. 1. Remove gross debris and soil from the device components using soft cloth or paper towels. Minimize formation of aerosols or droplets during the initial preparation of the product for decontamination. 2. P lace parts in a shallow pan and add enough chlorine solution to cover the device completely. Note: Recommended concentration is 20,000 ppm available chlorine. See Bleach Dilution section-Appendix A. • Allow to soak for 60 minutes. 3. Remove the devices from the bleach solution and rinse components completely with water. • The devices may then be autoclaved at 134°C for 18 minutes to one hour. • The devices have been verified through testing to withstand this process up to 15 times without loss of performance.
*Highly infectious diseases including but not limited to transmissible spongiform encephalopathies (TSEs) and Creutzfeldt-Jakob disease (CJD), also known as prion diseases (reference WHO/CDS/CSR/APH/2000.3, “WHO Infection Control Guidelines for Transmissible Spongiform Encephalopathies”, (Switzerland, March 1999) Section 1). ** Integra makes no claims that the following protocol is effective in neutralizing any specific pathogens. The protocol is a recommendation from the World Health Organization (WHO) based on the best available evidence at the time of publication. As stated in the World Health Organization (WHO) Protocol for Decontamination of highly infectious diseases. “Immerse [instrument] in sodium hypochlorite for 1 hour; remove and rinse with water, then transfer to open pan and heat in a gravity displacement autoclave at (121° C) or porous load (134°C) for 1 hour.”(Reference WHO/CDS/CSR/APH/2000.3, “WHO Infection Control Guidelines for Transmissible Spongiform Encephalopathies”, (Switzerland, March 1999) pp 29).
16
EN – ENGLISH
Step 2: Cleaning The instrument can withstand detergents having pH values between 3 and 11. Manufacturer's instructions of the selected detergent must be followed for this device.
NOTE: The use of highly alkaline agents can tarnish and / or corrode some components. While this does not affect the performance of the device, we recommend using an acid neutralizing agent immediately after each use to keep a device looking new. 2 Cleanings are available: • Manual Cleaning • Automatic cleaning
Manual Cleaning Following these steps is recommended: 1. Remove Base Unit from operating table. 2. Remove Swivel Adaptor from Base Unit. 3. The Base Unit should be thoroughly cleaned after each use. Scrub each component with a soft brush. The Base Unit can withstand detergents that fall within pH ranges of 3-11. Clean thoroughly to remove any traces of blood and/or debris and to prevent such blood or debris from interfering with function or movement. Rinse thoroughly with clean water to remove all traces of detergent. 4. Dry all components with a soft dry towel. 5. After components are totally dry, inspect the unit for cleanliness. 6. Inspect all components to ensure that there is no visible organic debris or residue from cleaning agent. Repeat process if any visible debris or residue is detected.
17
EN – ENGLISH
Automatic cleaning (including thermal disinfection) Note: The washing machine used must comply with the NF EN ISO 15883-1. 1. Disassemble devices (Refer to PREPARATION FOR CLEANING & REASSEMBLY) 2. Rinse components under warm tap water prior to placing in washer. 3. Position the device so as to prevent contact between the elements. 4. Select the cycle for instruments and perform the proper programming for the following cycle: Phases
Time (min)
Water Temperature
Detergent type and concentration
Pre-wash 1
04:00
Cold tap H2O
Enzyme wash
04:00
Hot tap H2O*
Wash 1 Rinse 1 Thermal rinse**
10:00 00:30 02:00
60°C Hot tap H2O* 82.2°C
N/A Multi-tiered enzymatic detergent with A.P.A Concentrated neutral pH cleaner N/A N/A
Table 1 Instrument Cycle
Step 3: Disinfection The MAYFIELD 2 Base Unit must be thoroughly cleaned after each use. Where possible, keep the soiled areas moist until the disinfection process can be initiated. IMPORTANT: If the product has been exposed to persistent pathogens1, do not apply gluteraldehyde, alcohol or formalin to the device until the decontamination process is complete. After decontamination, normal cleaning processes can be employed (see Decontamination section). Disinfection of device components following normal usage may be achieved using the following methods: Method 1: Thermal Rinse • A Thermal Disinfection rinse may be added after the first rinse cycle as indicated in Table 1. Method 2: Chemical • Prepare a fresh solution for general disinfection (See below guidelines for bleach solution). • With the device disassembled, place parts in a shallow pan and add enough general disinfection solution to cover the device completely. • Allow the parts to soak for 15 minutes. • Rinse thoroughly with clean water. For General Disinfection
Verify concentration of base hypochlorite is 4.5% or more Mix 1/2 unit of bleach into 10 units of water Table 2 Hypochlorite Bleach Mixing Guidelines * No limit on tap water temperature ** Optional phase for disinfection of components – minimum water temperature as indicated or per washer manufacturer specifications for the thermal rinse cycle section 1. Persistent pathogens are resistant to deactivation by normal disinfection procedures and may require more aggressive treatment to achieve disinfection. See guidelines in Decontamination for recommended procedures.
18
EN – ENGLISH
Disinfection (continued) Method 3: Autoclave • With device cleaned and disassembled, wrap components to keep clean. • Time and temperature parameters vary widely according to the type of autoclave and packaging material. Follow manufacturer’s instructions for loading and operating the autoclave. • Make sure direct steam exposure to all surfaces is possible. • Pre cycle vacuum (2psia / 14kPa) then steam disinfect at 132°C to 134°C for 4 minutes. • Once device is removed from the autoclave, allow components to reach room temperature before reassembly, handling, storage or use. • Following the disinfection procedure, subject to routine cleaning (see Cleaning section). 5. Remove from the washing machine and ensure that all instruments are dried. If necessary, complete drying with a sterile absorbent, lint-free towel. 6. Check all components to ensure they do not contain organic debris or residue of the cleaning agent. Repeat the process if a soil is still visible. (For additionally validated cleaning cycles, refer to Appendix B)
Appendix A : Bleach Dilution Bleach solutions produce chlorine gas. Prepare in a well-ventilated area. NOTE: Hypochlorite potency decreases as bleach ages. Use only recently purchased bleach to prepare decontamination solutions. Do not use pre-diluted bleach. Prepare a fresh batch for each application. Hypochlorite bleach mixing guidelines to obtain 20,000 ppm solution: Bleach
Preparation Instructions
4.5% 5% 6%
For 4 units bleach into 5 units of water For 2 units bleach into 3 units of water For 1 unit bleach into 2 units of water
NOTE: The use of highly alkaline agents may cause some components to tarnish and/or corrode. While this does not affect the performance of the device we recommend that you use an acidic neutralizing agent immediately after each use as this will help keep your device looking like new.
Appendix B: Additionally Validated Cleaning Cycles Wash Pre- Wash
Cold water from building supply (less than 110°or 43°C)/4min
50°C/7min
19
Rinsing
Thermal Disinfection
(Drying Optional)
Alkaline (e.g. neodisher® SeptoClean)
Hot water from building supply/2 min
Optional
90°C/2o min.
Neutral Enzymatic (e.g. Enzol per manufacturer's instructions)
Hot water from building supply/ 2 min.
Optional
90°C/2o min.
Temperature
Hold Time
Detergent Treatment
93°C
1 or more min.
90°C
1 or more min.