Malmet
Top Loading Washer Disinfector Operation and Maintenance Manual Issue 15 Oct 2011
Operation and Maintenance Manual
22 Pages
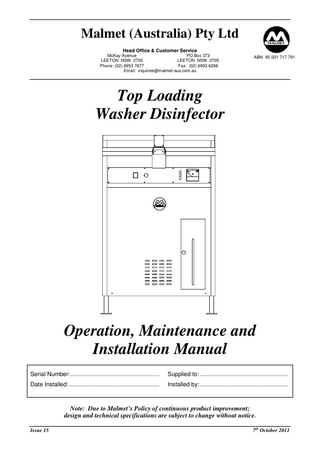
Preview
Page 1
Malmet (Australia) Pty Ltd Head Office & Customer Service McKay Avenue PO Box 373 LEETON NSW 2705 LEETON NSW 2705 Phone: (02) 6953 7677 Fax: (02) 6953 6266 Email: [email protected]
ABN 95 001 717 791
Top Loading Washer Disinfector
Operation, Maintenance and Installation Manual Serial Number:...
Supplied to: ...
Date Installed:...
Installed by:...
Note: Due to Malmet’s Policy of continuous product improvement; design and technical specifications are subject to change without notice. Issue 15
7th October 2011
Table of Contents Forward... 3 Design Parameters ... 3 Quality Policy... 4 Section A – Unit Operation ... 5 Unit Loading Diagram ... 5 Cycle of Operation ... 6 Section B – Unit Maintenance... 8 Printed Circuit Board - Layout Diagram... 9 Wiring Diagram ... 10 Fault Finding Guide... 11 Resistance Temperature Chart... 14 Section C – Unit Installation ... 15 Service Connections ... 15 Electrical ... 15 Plumbing ... 16 Service Connection - Layout Diagram... 17 Unit Specifications ... 18 Malmet Warranty Statement... 19
Issue 15
Page 2
7th October 2011
Washer Disinfector Top Loading
Operation, Maintenance and Installation Manual Forward In order to obtain maximum life and efficiency from your Malmet Top Loading Washer Disinfector and to aid in the safe operation of the unit, please read and understand this manual thoroughly and follow all instructions before operating the unit. This unit is not intended for use by persons (including children) with reduced physical, sensory or mental capabilities, or lack of experience and knowledge, unless they have been given supervision or instruction concerning use of the unit by a person responsible for their safety. Children should be supervised to ensure that they do not play with the unit. The specifications put forth in this manual were in effect at the time of publication. However, owing to Malmet (Australia)’s policy of continuous improvement, changes to these specifications may be made at any time without notice on the part of Malmet (Australia).
Design Parameters The Top Loading Washer Disinfector has been designed within the following parameters: a)
Hospital utensils such as wash basins and bowls, kidney dishes, tooth mugs, suction bottles and some types of surgical instruments can be washed and disinfected during each fully automatic cycle. The unit is designed to hold six large or small wash bowls, ten mugs and/or four kidney dishes. Alternative racking will allow load variations.
b)
Holding racks are designed to ensure that the force of the water does not dislodge articles.
c)
The chamber and lid are self-cleaning and do not permit water or soil to remain after a properly completed cycle.
d)
The stages of the cycle are: i.
Cold water wash
ii.
Hot water wash with detergent added automatically
iii.
Hot water rinse
iv.
Hot water disinfection cycle; and
v.
Cold water rinse
e)
The hot water wash with detergent is able to be pre-set by factory or service personnel to two, three, four or five minutes.
f)
The disinfection cycle is able to be pre-set by factory or service personnel to any of the following options in accordance with AS/NZS 4187:2003, Section 10, Clause 10.2.1 – Thermal Disinfection.
Note: Higher temperature settings may affect reusable instruments and equipment placed in the Washer Disinfector for disinfection. Malmet factory setting is at 80°C. Temperature 90°C 80°C 75°C
Note:
Issue 15
Time (min) 1 10 30
A red flashing light system has been incorporated to indicate a fault if a properly executed cycle has not been completed within a pre-set time. Page 3
7th October 2011
Washer Disinfector Top Loading
Operation, Maintenance and Installation Manual Quality Policy Malmet (Australia) is Quality Certified to ISO 9001, AS 3902, NZS 9002 and guarantees the quality of this product. Should you have any problems with your machine, contact the company from whom you purchased it, or Malmet (Australia).
Certifications Electrical Safety SAA090423
Watermark WMKA21156
Malmet (Australia) Pty Ltd Head Office and Factory PO Box 373 LEETON NSW 2705 Telephone: Facsimile: E-mail: Web Site:
Issue 15
(02) 6953 7677 (02) 6953 6266 [email protected] www.malmet.com.au
Page 4
7th October 2011
Washer Disinfector Top Loading
Operation, Maintenance and Installation Manual
Section A – Unit Operation Unit Loading Diagram
Issue 15
Page 5
7th October 2011
Washer Disinfector Top Loading
Operation, Maintenance and Installation Manual Cycle of Operation The automatic operation of the Top Loading Washer Disinfector is as follows: 1.
Ensure hot and cold water taps are on.
2.
Ensure wall isolation switch is on.
3.
Open lid and place all utensils to be washed in the racks provided for them.
4.
Close the lid and close the latch.
5.
Switch on ‘POWER ON’ button on front control panel. A white light will illuminate.
6.
Push ‘CYCLE START’ button. The door then locks and the ‘IN PROGRESS’ light illuminates. The cleaning and disinfection process proceeds as follows:
These times may vary as they are based on minimum incoming hot water supply temperature of 40°C @ 350kpa. Stage 1 – Pre-Rinse - 4 minutes. 1. Cold water fill 2. Wash 3. Drain Stage 2 – Wash – 6 minutes. 1. Hot water fill – Temperature 55°C 2. Detergent added 3. Wash (for factory pre-selected time) 4. Drain Stage 3 – Rinse – 4 minutes. 1. Hot water fill – Temperature 60°C 2. Wash 3. Drain Stage 4 – Disinfection – Fill/Heating 15 minutes and Disinfection 10 minutes. 1. Hot water fill – Temperature 80°C 2. Washing and Disinfection (heating system will stay on as necessary to complete disinfection/time requirement) 3. Drain Stage 5 – Post Rinse – 5 minutes. 1. Cold water fill 2. Wash 3. Drain 4. Door Release
Issue 15
Page 6
7th October 2011
Washer Disinfector Top Loading
Operation, Maintenance and Installation Manual Cycle of Operation (continued) ‘CYCLE COMPLETE’ light will illuminate and door may be unlatched and machine then reused. Note 1: If ‘FAULT INDICATED’ light illuminates, check the Fault Finding Guide in this manual (refer to page 15-17). Call Malmet for service (02) 6953 7677. Note 2:
If ‘FAULT INDICATED’ light illuminates, the machine will automatically pump out the water inside the machine, however, the door lock will not release.
Note 3:
A typical cycle time for the Washer Disinfector with 60°C hot water input, and approximately 350 kPa water pressure will be 32 minutes. In low pressure installations the cycle time will be longer, however, removal of the flow regulators from the water inlet valves will help alleviate this problem. To remove the regulator, remove filter screens from the water solenoid valves and remove the orifice plate from the water inlet valve entirely and replace the filter screens. In areas of high water pressure, the water fill tank could overflow. This problem can be fixed by partially turning off the water supply taps or obtaining smaller flow regulators from Malmet.
Issue 15
Page 7
7th October 2011
Washer Disinfector Top Loading
Operation, Maintenance and Installation Manual
Section B – Unit Maintenance Preventative Maintenance Daily (Operator) 1.
Wipe out inside of chamber with warm water and detergent.
2.
Wipe over outside panels with stainless steel cleaner.
3.
Visually check screen in the bottom of the chamber. necessary.
4.
Check the level of detergent at front viewing panel. If the detergent bottle is empty, replace with full bottle. Remove hose complete with nozzle and bottle lid from empty bottle and place on the new bottle. Detergent is available from Malmet.
Wash clean with hot water if
Weekly (Operator or Maintenance Technician) Scale from the water supply may build up on the float level switches which may inhibit their operation. Float level switches should be inspected regularly and wiped clean and if necessary cleaned with a suitable descaling compound. After One Months Operation (Maintenance Technician) 1.
Remove water hose from the water inlet solenoid valves at the rear of the unit and clean filter screens.
2.
Check for water leaks. Tighten hose clips and glands where necessary.
3.
Check and tighten, if necessary, all electrical connections.
4.
Clean thermostat probe in chamber.
5.
Check that float level switches are clean and operating freely.
6.
Remove and clean out water sprays and rotating spray arms. Note: Whole spray arm can be removed by releasing the coupling at the bottom of the chamber.
7.
Top up oil in lid damper if necessary (use 30 grade).
8.
Clean dust away from printed circuit board.
Issue 15
Page 8
7th October 2011
Washer Disinfector Top Loading
Operation, Maintenance and Installation Manual Printed Circuit Board - Layout Diagram
Issue 15
Page 9
7th October 2011
Washer Disinfector Top Loading
Operation, Maintenance and Installation Manual Wiring Diagram
DRG: WD_83-3_E
Issue 15
Page 10
7th October 2011
Washer Disinfector Top Loading
Operation, Maintenance and Installation Manual Fault Finding Guide Fault Indicated The ‘FAULT INDICATED’ light will be switched on if the total cycle time exceeds one hour or a fault is detected. Check the input water temperature if the cycle time exceeds 80 minutes.
PCB Repair Computer circuits, while robust, are not designed for human fingers etc to be placed across the pins. Handle all circuit boards by the edges and do not touch components. As an added precaution, always touch the metal frame of the Washer Disinfector before removing circuit boards. This allows for any static electricity to discharge to ground rather than through the PCB. Please Note: Any unauthorised repair work carried out to the circuit boards will void any warranty on these components
Power Supply Check As the first step of any fault finding, check the power supply to the unit and that the water taps are open. If the fault still exists, remove the front cover of the Washer Disinfector to expose the circuit board and power cable loom. The next stage of fault finding is to test the computer board power supplies. 1.
Check for 240V AC between TB1-4 and TB3-2, TB1-6 and TB3-2. If this is absent then check for open circuit on mains supply.
2.
Check for 240V across ST1 mains connection at top right hand side of main PCB.
3.
Check fuse F1 located under ST1 for continuity.
4.
Check fuse for 5V DC at the right hand pin of the 7805 voltage regulator. If no voltage is detected, the main PCB requires service.
If all tests prove correct, then the main PCB has all the correct voltages to operate. The next stage is to test the various sensors and switches which provide input to the main PCB.
Issue 15
Page 11
7th October 2011
Washer Disinfector Top Loading
Operation, Maintenance and Installation Manual PCB Input checks (Please read in conjunction with PCB layout diagram)
Door Lock and catch Remove SK6 on main PCB and test for continuity between the two pin plug with the door locked and catch locked.
High Water Level Remove SK3 on main PCB and test for continuity between the top and middle pins.
Low Water Level Remove SK3 on main PCB and test for continuity between the top and middle pins.
Temperature Probe Remove the temperature probe plug T2 and measure resistance across plug. Refer to Resistance Temperature Chart (refer page 18) for temperature readings.
Start Button Remove SK3 on display PCB and test for continuity with the start button pressed. This check will involve the removal of the control panel to gain access to the display PCB which is behind the analogue temperature meter. It is not expected that in the normal sequence of checks that this check will be required.
Issue 15
Page 12
7th October 2011
Washer Disinfector Top Loading
Operation, Maintenance and Installation Manual PCB Output Check The circuit board has indication lights to show which output device should be switched on during the cycle as detailed below: LED 1
Selected time (On bit switch board)
LED 2
Heater 1
LED 3
Heater 2
LED 4
Heater 3
LED 5
Wash / recirc pump
LED 6
Detergent pump
LED 7
Cold Water Solenoid
LED 8
Hot Water Solenoid
LED 9
Drain pump
LED 10
Power to Door Solenoid
LED 11
Selects between open and close
LED 1.1
Door is closed.
If the red indication light comes on and no action takes place, test the device separately from the PCB to confirm that it works. If the pump, motor or solenoid works correctly, then the PCB needs repair.
Issue 15
Page 13
7th October 2011
Washer Disinfector Top Loading
Operation, Maintenance and Installation Manual Resistance Temperature Chart TEMP
THERMISTOR (OHMS)
TEMP
THERMISTOR (OHMS)
TEMP
THERMISTOR (OHMS)
-10.00
107.8E x 10³
27.00
20.3E x 10³
64.00
5.2E x 10³
-9.00
102.0E x 10³
28.00
19.5E x 10³
65.00
5.0E x 10³
-8.00
97.6E x 10³
29.00
18.7E x 10³
66.00
4.9E x 10³
-7.00
92.8E x 10³
30.00
18.0E x 10³
67.00
4.7E x 10³
-6.00
88.4E x 10³
31.00
17.3E x 10³
68.00
4.6E x 10³
-5.00
84.2E x 10³
32.00
16.6E x 10³
69.00
4.4E x 10³
-4.00
80.2E x 10³
33.00
16.0E x 10³
70.00
4.3E x 10³
-3.00
76.4E x 10³
34.00
15.4E x 10³
71.00
4.1E x 10³
-2.00
72.8E x 10³
35.00
14.8E x 10³
72.00
4.0E x 10³
-1.00
63.1E x 10³
36.00
14.2E x 10³
73.00
3.9E x 10³
0.00
66.2E x 10³
37.00
13.7E x 10³
74.00
3.8E x 10³
1.00
63.1E x 10³
38.00
13.2E x 10³
75.00
3.7E x 10³
2.00
60.2E x 10³
39.00
12.7E x 10³
76.00
3.5E x 10³
3.00
57.5E x 10³
40.00
12.2E x 10³
77.00
3.4E x 10³
4.00
54.9E x 10³
41.00
11.7E x 10³
78.00
3.3E x 10³
5.00
52.4E x 10³
42.00
11.3E x 10³
79.00
3.2E x 10³
6.00
50.1E x 10³
43.00
10.9E x 10³
80.00
3.1E x 10³
7.00
47.8E x 10³
44.00
10.5E x 10³
81.00
3.0E x 10³
8.00
45.7E x 10³
45.00
10.1E x 10³
82.00
2.9E x 10³
9.00
43.7E x 10³
46.00
9.8E x 10³
83.00
2.9E x 10³
10.00
41.8E x 10³
47.00
9.4E x 10³
84.00
2.8E x 10³
11.00
40.0E x 10³
48.00
9.1E x 10³
85.00
2.7E x 10³
12.00
38.2E x 10³
49.00
8.8E x 10³
86.00
2.6E x 10³
13.00
36.6E x 10³
50.00
8.4E x 10³
87.00
2.5E x 10³
14.00
35.0E x 10³
51.00
8.2E x 10³
88.00
2.5E x 10³
15.00
33.5E x 10³
52.00
7.9E x 10³
89.00
2.4E x 10³
16.00
32.1E x 10³
53.00
7.6E x 10³
90.00
2.3E x 10³
17.00
30.8E x 10³
54.00
7.3E x 10³
91.00
2.3E x 10³
18.00
29.5E x 10³
55.00
7.1E x 10³
92.00
2.2E x 10³
19.00
28.2E x 10³
56.00
6.8E x 10³
93.00
2.1E x 10³
20.00
27.1E x 10³
57.00
6.6E x 10³
94.00
2.1E x 10³
21.00
26.0E x 10³
58.00
6.4E x 10³
95.00
2.0E x 10³
22.00
24.9E x 10³
59.00
6.2E x 10³
96.00
2.0E x 10³
23.00
23.9E x 10³
60.00
6.0E x 10³
97.00
1.9E x 10³
24.00
22.9E x 10³
61.00
5.8E x 10³
98.00
1.8E x 10³
25.00
22.0E x 10³
62.00
5.6E x 10³
99.00
1.8E x 10³
26.00
21.1E x 10³
63.00
5.4E x 10³
100.00
1.7E x 10³
Issue 15
Page 14
7th October 2011
Washer Disinfector Top Loading
Operation, Maintenance and Installation Manual
Section C – Unit Installation Please Note Installations must be carried out by qualified and licensed tradespeople.
Service Connections Service Connections required for the Top Loading Washer Disinfector are: Cold Water Hot Water Drain Electrical
¾” BSP flexible hose (supplied) ¾” BSP flexible hose (supplied) 1” flexible hose to Tundish (supplied) refer to Service Connection Layout Diagram WDT2 – 240V single phase draws 18 Amps 50 Hz
Note1: New Hose sets supplied with the unit are to be used. Old hose sets should not be re-used. Note2: The Service Connections may be on either side of the washer but not behind it. On the unit all water and drain connections are on the left hand side when facing the unit, however they can be quite simply moved to the right hand side as follows: i.
Remove the rear panel.
ii.
Remove the three plastic plugs from the holes in the right hand back panel.
iii.
Unscrew the water inlet solenoid brackets.
iv.
Transfer the water inlet solenoids to the right hand back panel. Be sure to put the cold water solenoid to the top and the hot to the bottom. Tighten the brackets.
v.
Unscrew the waste outlet support.
vi.
Transfer the water outlet to the right hand back panel. It may be necessary to loosen the hose clamps and rotate the hose. When in position, tighten the support and the hose clamps.
vii.
Re-fit the plastic plugs to the three holes in the left hand back panel.
viii.
Re-fit the rear panel.
The electrical connections are in the centre of the bottom back panel.
Electrical WDT2 requires single phase 240V draws 18 Amp 50 Hz. It is recommended that the unit be connected to a 25 Amp circuit breaker. All units must be earthed. An isolating switch is to be fixed to the building wall (approximately 1200mm above floor level) adjacent to the Washer Disinfector’s electrical entry point which is positioned at the rear of the unit in the centre of the bottom panel. Note: If the supply cord is damaged, it must be replaced by the manufacturer, its service agent or similarly qualified persons in order to avoid a hazard. Issue 15
Page 15
7th October 2011
Washer Disinfector Top Loading
Operation, Maintenance and Installation Manual Plumbing NOTE: Plumbing connections must comply to AS3500 Hot Water All models can be connected direct to any hot water supply of at least 40°C minimum. For the quickest operating cycles water at 60°C is ideal. There is an airbreak incorporated within the unit. The hot water supply should be connected to a 15∅ hot water chrome plated isolating valve with ¾” BSP male connection, placed above the unit and to the sides of the unit. The water entry point is on the left hand side of the unit as shown in the service connection diagram. Minimum Inlet Water Pressure = 40 kPa Maximum Inlet Water Pressure = 500 kPa
Cold Water All models can be connected direct to any cold water supply. There is an airbreak incorporated within the unit. The water entry point is on the left hand side of the unit as shown in the service connection diagram. Minimum Inlet Water Pressure = 40 kPa Maximum Inlet Water Pressure = 500 kPa
Waste The tundish supplied with the units is to suit left-hand waste connection. Where right hand connection is required, remove the tundish lid and reposition it to suit by rotating 180°. The service connections diagram (Fig 1) shows left-hand connection. The maximum discharge temperature of the unit is 90°C. 50mm Combination S & P trap supplied with the unit is of Polypropylene material and can withstand temperatures of up to 90°C .
Issue 15
Page 16
7th October 2011
Washer Disinfector Top Loading
Operation, Maintenance and Installation Manual Service Connection Layout Diagram
Fig 1
Issue 15
Page 17
7th October 2011
Washer Disinfector Top Loading
Operation, Maintenance and Installation Manual Unit Specifications
Electrical Rating
Element
Volts
240V
Phase / Hz
1 ph / 50 Hz
Amps
18 Amps
Rated
3.6 kW
APPROVALS
PCB (Printed Circuit Board) Temperature Control
Factory set at 80°C 75°C – 30 minutes
Disinfecting Times
80°C – 10 minutes
AS/NZS 4187:2003 – Section 10, Clause 10.2.1
90°C – 1 minute Detergent
Malmet (5 litre)
Backflow Prevention
Air Gap (RAG)
Water Supply Cold
Temp – Pressure (Static)
5 - 25°C @ 40 – 500 kpa
Water Supply Hot
Temp – Pressure (Static)
43 – 60°C @ 40 – 500 kpa
Inlet Valve
Solenoid
¾” Inlet
WRAS Certified
Tundish End Connection to Waste
Combination S – P Trap
90°C PP
Cert to AS/NZS 1260: 2002
Hoses – Inlet Valve to Water Tank
s/steel Braided
10mm
WRAS Certified
Hoses – Water Supply to Inlet Valve
s/steel Braided Assy H/C Water
G¾ Hex Nut Each End
Cert to AS/NZS 3499-2006
AS 2845.2 - 1996
Water Capacity
18.5 Litres
Cold Water Consumption/Cycle
32 Litres
Hot Water Consumption/Cycle
48 Litres
Materials
Issue 15
Wash chamber and external panels
Page 18
304/4 stainless steel
7th October 2011
Washer Disinfector Top Loading
Operation, Maintenance and Installation Manual
Warranty Statement – Australia Only Subject to the following conditions we provide, from the date of purchase, the following warranty:
• •
Functional components found within the unit to be defective in workmanship or material will be replaced free of charge subject to the periods of warranty specified. The structural warranty covers any structural components within the unit, which fail to perform their intended function due to faulty manufacture or deterioration within the warranty period.
This
warranty
only
covers
products
manufactured
by
Malmet
(Australia)
Pty
Ltd.
Conditions and Exclusions
• •
• • • • • •
• •
Equipment must be installed according to our instructions (outlined in our Operation, Maintenance and Installation Manual) and operated to the purpose it was designed. Warranty shall not cover damage, malfunction or failure resulting from accident, misuse or misapplication, improper or unauthorised repair, neglect or modification or use of unauthorised replacement parts or accessories, or improper voltage. The warranty shall be void if the serial number is removed or altered. Parts damaged in transit back to Malmet Leeton due to poor packaging could result in warranty claim being rejected. Any part tampered with or has unauthorised repairs and modifications will be rejected as a warranty claim. Reasonable access must be allowed for maintenance. If any additional equipment is needed to provide access to the unit, this must be provided (and paid for) by the owner. It is the owner’s responsibility to provide safe access to the unit. Malmet, or any of its authorised service outlets, may refuse to do maintenance or warranty work if access is unsafe. Should a warranty claim be rejected you will be advised in writing with a full explanation of our reasons. It is our policy to have a Warranty Claim Procedure that is fair to our customers and provides an efficient system of replacement and/or repair of faulty parts. If at any time you believe we are not meeting our commitment to you please contact Malmet Head Office – Leeton. No responsibility will be accepted for outside elements such as storms, pest and vermin that may cause damage to the unit. No responsibility will be accepted for damage contributed by electrical surges or brown outs or any other consequential damages.
Issue 15
Page 19
7th October 2011
Washer Disinfector Top Loading
Operation, Maintenance and Installation Manual • If there is no certificate of compliance for plumbing or electrical, Malmet reserves the right to refuse service on non-compliant installations.
•
A charge will be made for work done or service call where:
•
There is nothing wrong with the unit.
•
The defective operation of the unit is due to failure of electricity or water supply.
• • • •
• • •
Defects are caused by neglect, incorrect application, abuse or by accidental damage of the unit. An unauthorised person has attempted to repair the unit.
Harsh environmental situations such as water quality that may cause the water tank damage can not be considered warranty. Claims for damage to contents, carpet, ceilings, foundations or any other consequential loss either direct or indirect resulting from, power spikes, incorrect operation, incorrect installation or faulty product are excluded. All warranties are NOT transferable. Unauthorised use of non-genuine Malmet Parts in units covered by Warranty will void all warranty and warranty claims. To the extent permitted by law Warranty labour (service work) shall not include units located outside of city metropolitan areas and costs outside these areas shall be borne by the Customer. The Customer shall be notified of this prior to the warranty call out.
Issue 15
Page 20
7th October 2011