Malmet
Top Loading Washer Disinfector Operation , Maintenance and Installation Manual sw V5.0
Operation, Maintenance and Installation Manual
33 Pages
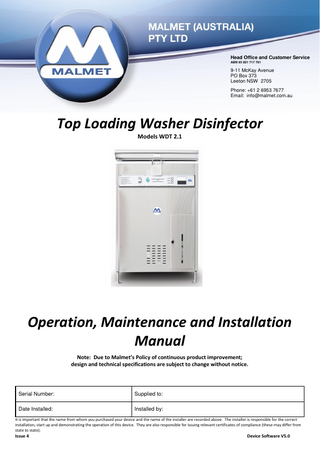
Preview
Page 1
Head Office and Customer Service ABN 95 001 717 791
9-11 McKay Avenue PO Box 373 Leeton NSW 2705 Phone: +61 2 6953 7677 Email: [email protected]
Top Loading Washer Disinfector Models WDT 2.1
Operation, Maintenance and Installation Manual Note: Due to Malmet’s Policy of continuous product improvement; design and technical specifications are subject to change without notice.
Serial Number:
Supplied to:
Date Installed:
Installed by:
It is important that the name from whom you purchased your device and the name of the installer are recorded above. The installer is responsible for the correct installation, start up and demonstrating the operation of this device. They are also responsible for issuing relevant certificates of compliance (these may differ from state to state).
Issue 4
Device Software V5.0
Washer Disinfector (WDT) - Top Loading
Operation, Maintenance and Installation Manual
Table of Contents Foreword ... 2 Certifications and Compliances ... 2 Quality Policy ... 2 Important Warranty Reminder ... 2 Malmet Head Office and Factory Contact Details ... 2 Safety Instructions -Warnings ... 3 Intended Use... 4 1.0 Design Parameters ... 4 1.1 Operating Cycle ... 5 1.2 Chemical Dosing System... 5 1.3 Detergent ... 5 1.4 Device Features ... 7 1.5 Control Display Features ... 7 1.6 Buttons & Indicators... 8 2.0 Installation and Commissioning ... 9 2.1 Installation ... 9 2.2 Service Connections ... 10 2.3 Plumbing... 10 2.4 Venting ... 11 2.5 Electrical ... 11 2.6 Service Connection Points ... 12 2.7 Device Dimensions ... 13 2.8 Installation clearances ... 13 2.9 Commissioning (To only be completed by qualified persons)... 14 3.0 Loading ... 15 4.0 Cycle of Operation... 16 4.1 Release of Processed items ... 17 5.0 Maintenance ... 18 5.1 Daily Maintenance (Operator or Maintenance Technician) ... 18 5.2 Weekly (Maintenance Technician) ... 18 1.3 Bi-Monthly (Maintenance Technician) ... 18 1.4 Post Maintenance or Repair Safety Checks ... 19 5.5 Door Safety Test ... 19 5.6 Cycle Operation Check ... 19 5.7 Post Maintenance and Repair of Electrical Systems ... 19 5.8 Replacement of Safety Devices ... 20 5.9 Validation ... 20 5.10 Requalification... 20 5.11 Device faults ... 20 5.12 Fault Indication ... 21 5.13 Making equipment safe after incomplete operating cycle ... 24 6.0 Technical Specifications ... 25 6.1 Power and Water Consumption ... 25 6.2 Device Specifications ... 25 6.3 Printed Circuit Board - Layout Diagram ... 27 6.5 Wiring Diagram... 28 Warranty Statement ... 29
Issue 4
Page 1
July 23
Washer Disinfector (WDT) - Top Loading
Operation, Maintenance and Installation Manual Foreword In order to obtain maximum life and efficiency from your Malmet Top Loading Washer Disinfector and to aid in the safe operation of the device, please read and understand this manual thoroughly and follow all instructions before operating the device. This device is not intended for use by persons (including children) with reduced physical, sensory or mental capabilities, or lack of experience and knowledge, unless they have been given supervision or instruction concerning use of the device by a person responsible for their safety. Children should be supervised to ensure that they do not play with the device. The specifications supplied in this manual were in effect at the time of publication. However, owing to Malmet (Australia)’s policy of continuous improvement, changes to these specifications may be made at any time without notice on the part of Malmet (Australia).
Certifications and Compliances ARTG Identifier:
232013
Electrical Safety Cert:
Cert No. CS10848N IEC61010-2-040 in conjunction with IEC61010-1
EMC Compliance:
Cert No. S180506_S
Watermark Cert:
Cert No. WMK21156
Quality Policy Malmet’s quality management system is certified to ISO 9001:2015 and ISO 13485:2016 and guarantees the quality of this product.
Important Warranty Reminder Should you have any problems with your device, contact the company from whom you purchased it, or Malmet (Australia) Pty Ltd. It is important that the name from whom you purchased your device and the name of the installer are recorded on the front page of this manual. The installer is responsible for the correct installation, start up and demonstrating the operation of this device. They are also responsible for issuing relevant certificates of compliance (these may differ from state to state).
Malmet Head Office and Factory Contact Details Malmet (Australia) Pty Ltd 9-11 McKay Avenue PO Box 373 LEETON NSW 2705 Telephone:
+61 2 6953 7677
E-mail:
Website:
www.malmet.com.au
Issue 4
Page 2
July 23
Washer Disinfector (WDT) - Top Loading
Operation, Maintenance and Installation Manual Safety Instructions -Warnings Please read and understand this manual before using this device, if this device is used in a manner not specified protection by the device may be impaired.
Please refer to this manual for information whenever this warning symbol is displayed -
Be aware of 240V Voltage Disconnect power when servicing Mains power ISO switch or circuit-breaker must be in an accessible position, easily reached and not obstructed so device can be isolated from mains power during service For the safe use of this device the responsible body should ensure that all operators are adequately trained to operate and maintain the device in its safe use Failure to maintain device as per the requirements of this manual may impair performance Only process items listed as per the design parameters in this manual Be aware of steam discharge Utensils and racks are hot to handle Safety gloves and goggles must be worn when changing detergent Be aware of hot surface, pipes and hoses from steam and hot water Machine to be serviced and repaired by trained personnel Safety critical devices must only be replaced by trained personnel Plumbing service connection must comply with AS/NZS 3500.1 and AS/NZS 3500.2 Not suitable for use in the presence of flammable anaesthetic mixtures with air or nitrous oxide and mode of operation as continuous
Issue 4
Page 3
July 23
Washer Disinfector (WDT) - Top Loading
Operation, Maintenance and Installation Manual Intended Use The Malmet Top Loading Washer Disinfector is intended to be used by health service organisation personnel for the cleaning and disinfection of medical devices during an automatic cycle of the types intended to be re-used as listed in the design parameters section of this manual.
1.0 Design Parameters The Top Loading Washer Disinfector has been designed within the following parameters:
Note:
a)
Hospital utensils such as wash basins and bowls, kidney dishes, tooth mugs and suction bottles can be washed and disinfected during each fully automatic cycle. The device is designed to hold six large or small wash bowls, ten mugs and/or four kidney dishes. Alternative racking will allow load variations.
b)
Holding racks are designed to ensure that the force of the water does not dislodge articles.
c)
The chamber and lid are self-cleaning and do not permit water or soil to remain after a properly completed cycle.
d)
The hot water wash with detergent is able to be pre-set by factory or service personnel to two, three, four or five minutes.
e)
The disinfection cycle is factory pre-set to 80°C for 10 Minutes to achieve an A₀ of 600 in accordance with AS/NZS 4187:2014, Section 6.3, Table 6.1. A red flashing light system has been incorporated to indicate a fault if a properly executed cycle has not been completed within a pre-set time.
*The efficacy of disinfection can be impaired if soil removal is incomplete before the start of the disinfection process. Users should be aware that some medical devices might require pre-treatment such as soaking or brushing before processing. Please follow the manufacturer’s instructions when processing re-useable medical devices. **High disinfection temperatures may affect some heat sensitive reusable medical devices; ensure items are disinfected as per the manufacturer’s instructions.
Issue 4
Page 4
July 23
Washer Disinfector (WDT) - Top Loading
Operation, Maintenance and Installation Manual 1.1
Operating Cycle The stages of the cycle are: i. Cold water wash ii. Hot water wash with detergent added automatically iii. Hot water rinse iv. Hot water disinfection cycle; and v. Cold water rinse Temperature 90°C 80°C 75°C
Time (min) 1 10 30
In accordance and complies with: Cleaning Efficacy AS/NZS 4187:2014, ISO 15883-1, ISO/TS 15883-5 Thermal Disinfection AS/NZS 4187:2014, ISO 15883-1
1.2
Chemical Dosing System
The chemical dosing system ensures the correct amount of process chemicals are delivered at the correct stage during each operating cycle. Chemical addition is controlled by the automatic cycle controller and will display a fault if the incorrect amount of chemical is injected. The dosing system is designed for use with Malmet Chemical; other chemicals may impair the operation of the system.
1.3
Detergent
Malmet Washer Disinfectors are designed and tested using Malmet specific detergent. To ensure intended performance and trouble-free operation use only Malmet branded detergent, failure to use correct detergent may void warranty. The detergent system delivers 60ml of concentrated detergent in the initial wash stage.
Issue 4
Page 5
July 23
Washer Disinfector (WDT) - Top Loading
Operation, Maintenance and Installation Manual Detergent replacement procedure
WARNING! SAFETY GLOVES AND GOGGLES MUST BE WORN WHEN CHANGING DETERGENT AND DISPOSING OF EMPTY CONTAINERS Current Safety Data Sheet for Malmet detergent is available in .PDF format from Malmet’s website. www.malmet.com.au The 5-litre detergent container is accessed by opening the bottom door. Only use Malmet approved detergent (See technical data for detergent details) 1.
Pull detergent door and open
2.
Remove detergent bottle and placing on the floor then unscrew cap and pull out with suction hose (Let hose hang on detergent chamber)
3.
Remove cap on new bottle and fit existing hose and cap
4.
Place full bottle into holder, ensuring plastic tube does not kink
5.
Close door
6.
Restart machine operation as normal
Disposal of Empty Detergent Bottles
Issue 4
1.
When handling empty containers treat as though container is full and wear appropriate PPE as per MSD sheet requirements
2.
Triple rinse container and puncture base to render unusable
3.
Dispose of containers as per facility chemical waste handling procedures, and or local government requirements
Page 6
July 23
Washer Disinfector (WDT) - Top Loading
Operation, Maintenance and Installation Manual Detergent Out Condition If insufficient detergent is available to deliver the required quantity the device will display a detergent out fault. This is identified by the fault lights scrolling from bottom row on for 1 second and then all on for 1 second. And will not allow another cycle to be started while in this condition until the detergent fault is rectified. To rectify this fault, install a new detergent bottle as per the procedure in this manual “Changing the Detergent Bottle”. On completion of changing the detergent bottle, press the “Start Cycle” button to initiate a priming sequence. During the priming sequence the progress indicators LED’s will alternate. If priming is successfully the fault will clear and device will return to normal operation, inspect the items have been cleaned sufficiently before unloading. It is recommended the items are reprocessed in the event of a detergent out fault. If priming is unsuccessful, device will remain in fault. Check a full bottle has been installed and suction tube installed correctly and not kinked. The device allows 4 priming attempts in succession, if a successful priming sequence is not completed the device will block any further attempts. To avoid the detergent out condition, check the low level through the detergent door window, replace detergent when the level falls below the window.
1.4
Device Features
For the safe use of this device the responsible body should ensure that all operators are adequately trained to operate and maintain the device in its safe use.
1.5
Issue 4
Control Display Features
Page 7
July 23
Washer Disinfector (WDT) - Top Loading
Operation, Maintenance and Installation Manual 1.6
Issue 4
Buttons & Indicators
POWER
On/Off Switch
CYCLE START
Push to start Cycle
IN PROGRESS
Cycle in Progress
CYCLE COMPLETED
Cycle Completed
FAULT INDICATED
Fault in the device
ANALOG TEMPERATURE METER
Indicates Temperature
Page 8
July 23
Washer Disinfector (WDT) - Top Loading
Operation, Maintenance and Installation Manual 2.0 Installation and Commissioning 2.1
Installation
For correct installation and to avoid problems with this device, please use the following Installation guidelines Installations must only be carried out by a qualified and licenced tradesperson. Services as noted as required for installation of the device are to be provided by the facility and are not the responsibility of Malmet.
Risk Assessment It is recommended a risk assessment is conducted by the user both prior to and after installation and any risks identified mitigated to an acceptable level using the hierarchy of control;
https://commons.wikimedia.org/w/index.php?curid=55610678
Handling Weights of Device:
Net: 114.5 kg
Shipping: 140kg Shipping with Crating: 180kg
• Handling of the device to installation site must be with fork lift or hand pallet truck. • Before unpacking device inspect carton for any damage relating to forklift forks and damage relating to device falling over or for evidence of top loading • After unpacking the device, inspect all external panels for damage. • Remove the 4 screws holding the device to the pallet. • Follow your internal manual handling guidelines to manoeuvre the device off the pallet. The device can then be placed into position by fork lift or hand pallet truck.
Disposal of Packaging Please dispose of packaging as per facility procedures or local government requirements.
Issue 4
Page 9
July 23
Washer Disinfector (WDT) - Top Loading
Operation, Maintenance and Installation Manual 2.1.1
Positioning the WDT 2.1
Model
Placement
WDT2.1
Freestanding
Access Required Front & Rear
Device Dimensions Height (mm)
Width (mm)
Depth (mm)
1030
655
850
Please allow sufficient room at front of unit for servicing purposes.
New Buildings • Service connections are normally pre-placed after planning and consultation with all interested parties. Installation is by connection to the services provided. • As the soil line (sewerage outlet) is the least flexible of all the connections, this usually influences the decision as to where to place the Top Loading Washer Disinfector. If an existing soil line can be utilised this will represent a cost saving. • The Top Loading Washer Disinfector is supplied with a Tundish & 50mm combination S & P trap as nominated by the Purchaser. The Trap connects between the Tundish & soil line and can be configured as either an “S” or “P” type trap. Refer to Diagram Service Connections Layout 2.6 for trap connections. • Potential electromagnetic or other interference between other EQUIPMENT and other devices can possibly affect the operation. Electromagnetic interference can be prevented by installing the device in non-patient areas of the facility (or similar).
2.2
Service Connections
MODEL
HOT/COLD WATER
DRAIN
SOIL LINE
ELECTRICAL
WDT 2.1
Solenoid valve GB¾ Male
1” flexible hose to tundish
50 mm ‘S’ or ‘P’ Trap
240V 1 phase @ 18 Amps 50 hertz
The following service connections must be provided by the facility for installation of the device, services must comply with the specifications as per this section of the manual to ensure correct and safe operation of the device. See the Service Connection Point 2.6 for details of device service connection points.
2.3
Plumbing
These installation guidelines must be followed to ensure the device will operate as intended. Installations must be carried out by a qualified, licensed tradesperson. Water Supply - NOTE: Plumbing connection must comply with AS/NZS 3500.1 and be Watermark Certified. HOT AND COLD-WATER CONNECTIONS ARE REQUIRED. The device can be connected to any potable mains pressure hot and cold-water supply as a back-flow prevention air gap is incorporated in the design of the water tank. Complies to AS 2845.2 Cold Water – Note: See device specifications table for water quality requirements Pressure:
40-500kPa
Temperature:
15-25°C
Nominal Flow:
9L/Min
Connection:
GB ¾” BSP
Hot – Note: See device specifications table for water quality requirements
Issue 4
Pressure:
100-500kPa
Temperature:
45-60°C
Nominal Flow:
9L/Min
Connection:
GB ¾” BSP
Page 10
July 23
Washer Disinfector (WDT) - Top Loading
Operation, Maintenance and Installation Manual Note:
Old hose sets should not be re-used; it is recommended new compliant hose sets are used on installation.
Waste Connection – Note: Waste service connection must comply with AS/NZS3500.2 The tundish supplied with the device is to suit left-hand waste connection. Where right hand connection is required, remove the tundish lid and reposition it to suit by rotating 180°. The service connections diagram shows left-hand connection. The maximum discharge temperature of the device is 90°C. 50mm combination S & P trap supplied with the device is of Polypropylene material and can withstand temperatures of up to 90°C.
Plumbing Service Connections may be on either side of the washer but not behind it. On the device all water and drain connections are on the left-hand side when facing the device, however they can be quite simply moved to the right-hand side as follows: i.
Remove the rear panel.
ii.
Remove the three plastic plugs from the holes in the right-hand back panel.
iii.
Unscrew the water inlet solenoid brackets.
iv.
Transfer the water inlet solenoids to the right-hand back panel. Be sure to put the cold-water solenoid to the top and the hot to the bottom. Tighten the brackets.
v.
Unscrew the waste outlet support.
vi.
Transfer the water outlet to the right-hand back panel. It may be necessary to loosen the hose clamps and rotate the hose. When in position, tighten the support and the hose clamps.
vii. Re-fit the plastic plugs to the three holes in the left-hand back panel. viii. Re-fit the rear panel.
2.4
Venting
No external vent pipework is required as the device is designed to condensate all visible steam within the device.
2.5
Electrical
These installation guidelines must be followed to ensure the device will operate as intended and must be carried out by a qualified, licensed electrical tradesperson. The device must be installed and serviced to national wiring rules AS/NZS 3000. The device can be fix wired or supplied with a 20A single phase plug. WDT2.1 requires single phase 240V 18 Amp 50 Hz. It is recommended that the device be connected to a 20 Amp circuit breaker. All devices must be earthed. For fix wired installations the device must be installed and serviced to national wiring rules AS/NZS 3000. For plugged installations the device must be installed and serviced to AS/NZS 3760. Note: Mains power ISO switch or circuit-breaker must be in an accessible position so device can be isolated from mains power during service
Issue 4
•
For fixed installations an ISO switch or circuit breaker must be included in the installation. (Not supplied by Malmet)
•
It must be suitably located and easily reached. Placed approximately 1200mm above floor level adjacent to device. The device is fitted with a 2.5m mains power lead that exits the rear of the device in the centre of the bottom panel.
•
It must be marked as the disconnecting device for the equipment. Page 11
July 23
Washer Disinfector (WDT) - Top Loading
Operation, Maintenance and Installation Manual •
It must have contact disconnection of all poles to provide full disconnection.
• Ensure isolator is suitably placed so device will not obstruct safe access to the isolator once installed. • For devices provided with a plug this is considered as the disconnecting device and should be marked as such. • For plugged devices ensure a suitably rated socket outlet with protective earthing is provided. Note: If the supply cord is damaged, it must be replaced by the manufacturer, its service agent or similarly qualified persons in order to avoid a hazard.
2.6
Issue 4
Service Connection Points
Page 12
July 23
Washer Disinfector (WDT) - Top Loading
Operation, Maintenance and Installation Manual
Issue 4
2.7
Device Dimensions
2.8
Installation clearances
Page 13
July 23
Washer Disinfector (WDT) - Top Loading
Operation, Maintenance and Installation Manual 2.9
Commissioning (To only be completed by qualified persons)
Ensure and that services connections have been made as per the installation instructions in this manual. Ensure all packaging has been removed from chamber, and no loose items or fittings are left inside the chamber. a)
Confirm Hot and Cold-water inlet hoses are connected to the correct supplies.
b)
Tundish is installed and connected correctly
c)
Fixed sprays are all in position and tight, and that the rotating spray arm turns freely
d)
Racks are in place
e)
Vent and Drain screens are fitted
f)
Check that the 5-litre detergent bottle has been fitted and suction hose correctly connected
g)
Check all levelling legs have been adjusted, device is level and stable
h)
Check door opens and closes smoothly
i)
Turn on water supply and confirm no leaks
j)
Turn on main power supply, and switch on power using power switch on main panel
k)
Latch door closed and start a cycle by pressing the green power button
l)
Confirm door locks on cycle start
m)
Check no leaks during cycle
n)
Check hot wash temperature is achieved
o)
Check disinfection temperature is achieved
p)
Confirm no faults at cycle completed
q)
Confirm door lock released at end of cycle and status LED indicates cycle complete.
Note:
Issue 4
DO NOT USE THE DEVICE WITHOUT THE WATER SUPPLY TURNED ON
Page 14
July 23
Washer Disinfector (WDT) - Top Loading
Operation, Maintenance and Installation Manual 3.0 Loading For the safe use of this device the responsible body should ensure that all operators are adequately trained to operate and maintain the device in its safe use.
Device Loading Diagram
Issue 4
Page 15
July 23
Washer Disinfector (WDT) - Top Loading
Operation, Maintenance and Installation Manual 4.0 Cycle of Operation The automatic operation of the Top Loading Washer Disinfector is as follows: 1.
Ensure hot and cold-water taps are on.
2.
Ensure wall isolation switch is on.
3.
Open lid and place all utensils to be washed in the racks provided for them.
4.
Close the lid and close the latch.
5.
Switch on ‘POWER ON’ button on front control panel. A Green light will illuminate.
6.
Push ‘CYCLE START’ button. The door then locks and the ‘IN PROGRESS’ light illuminates. The cleaning and disinfection process proceed as follows:
These times may vary as they are based on minimum incoming hot water supply temperature of 40°C @ 350kpa. Stage 1 – Pre-Rinse - 4 minutes 1. Cold water fill 2. Wash 3. Drain Stage 2 – Wash – 6 minutes 1. Hot water fill (temperature 55°C) 2. Detergent added 3. Wash (for factory pre-selected time) 4. Drain Stage 3 – Rinse – 4 minutes 1. Hot water fill (temperature 60°C) 2. Wash 3. Drain Stage 4 – Disinfection – Fill/Heating 15 minutes and Disinfection 10 minutes 1. Hot water fill (temperature 80°C) 2. Washing and Disinfection (heating system will stay on as necessary to complete disinfection/time requirement) 3. Drain Stage 5 – Post Rinse – 5 minutes 1. Cold water fill 2. Wash 3. Drain 4. Door Release
At completion of the cycle the “CYCLE LED” shall alternate at 1 second intervals with the temperature dial. This indicates a successful cycle and displays the current chamber temperature (CYCLE LED bottom row only) and the temperature reached during disinfection (CYCLE LED all on). ‘CYCLE COMPLETE’ light will illuminate and door may be unlatched and machine then reused. If ‘CYCLE COMPLETE’ & ‘IN PROGRESS’ lights are illuminated simultaneously the internal chamber temperature is above the safe limit and the door will remain locked until the temperature falls to a safe level. Note 1: If ‘FAULT INDICATED’ light illuminates, check the Fault Indicated in this manual (refer to page 21-22). Call Malmet for service +61 2 6953 7677. Issue 4
Page 16
July 23
Washer Disinfector (WDT) - Top Loading
Operation, Maintenance and Installation Manual Note 2: If ‘FAULT INDICATED’ light illuminates, the machine will automatically pump out the water inside the machine, however, the door lock will not release. Note 3: A typical cycle time for the Washer Disinfector with 60°C hot water input, and approximately 350 kPa water pressure will be 32 minutes. In low pressure installations the cycle time will be longer, however, removal of the flow regulators from the water inlet valves will help alleviate this problem. To remove the regulator, remove filter screens from the water solenoid valves and remove the orifice plate from the water inlet valve entirely and replace the filter screens. In areas of high-water pressure, the water fill tank could overflow. This problem can be fixed by partially turning off the water supply taps or obtaining smaller flow regulators from Malmet.
4.1
Release of Processed items
On completion of the cycle, it is recommended that all processed items are unloaded and visually inspected as clean as per the requirements AS/NZS 4187. It is recommended all items are removed on completion of the cycle and stored in a designated area to prevent any risk of contamination or mixing with unprocessed items.
If the processing status of a load or item is unknown or in question, it should be treated as unprocessed and not released.
Issue 4
Page 17
July 23
Washer Disinfector (WDT) - Top Loading
Operation, Maintenance and Installation Manual 5.0 Maintenance All maintenance, preventative or breakdown shall be carried out by a qualified person. Failure to comply with this condition may result in unsafe conditions. Preventative maintenance must be completed as per instructions below. Failure to comply may result in warranty claims being rejected. The Malmet Top Loading Utensil Washer Disinfector is self-cleaning, however proper care should be taken to ensure that the device is cleaned and maintained in accordance with maintenance instructions for Malmet Top Loading Utensil Washer Disinfector and in accordance with all other regulatory and common-sense practices. Preventative Maintenance Schedule
5.1
Daily Maintenance (Operator or Maintenance Technician)
a)
Wipe out inside of chamber with warm water and detergent.
b)
Wipe over outside panels with stainless steel cleaner.
c)
Visually check screen in the bottom of the chamber. Wash clean with hot water if necessary.
d)
Visually inspect for signs of leaking fluid from the device, as these may pose a pathogenic risk. Inspect around the chamber door, beneath the device, tundish and service connection points. If a spill or leak is observed, clean up as per the facilities infection control procedure and notify a maintenance technician to fix the cause of the leak.
e)
Check the level of detergent at front viewing panel. If the detergent bottle is empty, replace with full bottle. Remove hose complete with nozzle and bottle lid from empty bottle and place on the new bottle. Detergent is available from Malmet.
ISOLATE DEVICE FROM ELECTRICAL SUPPLY BEFORE PERFORMING MAINTENANCE TASKS!
5.2
Weekly (Maintenance Technician) Scale from the water supply may build up on the float level switches which may inhibit their operation. Float level switches should be inspected regularly and wiped clean and if necessary cleaned with a suitable descaling compound i.e. Green Pro D-Lime
5.3
Bi-Monthly (Maintenance Technician)
WARNING! 240 VOLTS ISOLATE DEVICE FROM ELECTRICAL SUPPLY BEFORE SERVICING
HOT SURFACES! ALLOW DEVICE TO COOL PRIOR TO COMMENCING SERVICE WORKS a)
Remove water hose from the water inlet solenoid valves at the rear of the device and clean filter screens.
b) Inspect for fluid leaks, check and tighten all hose clamps and visually check hoses. c)
Check and tighten, if necessary, all electrical connections.
d) Clean thermostat probe in the chamber. e)
Check that float level switches are clean and operating freely.
f)
Remove and clean out water sprays and rotating spray arms. Note: Whole spray arm can be removed by releasing the coupling at the bottom of the chamber.
Issue 4
Page 18
July 23
Washer Disinfector (WDT) - Top Loading
Operation, Maintenance and Installation Manual g)
Gently clean printed circuit board for dust build up.
Wash Arm & Nozzle Cleaning Instructions Remove and clean the sprays in sequence (do not mix sprays with other spray groups). Wash Arm Hold under tap and pressurise through the nozzle outlet in opposite direction of normal flow or clean in ultrasonic cleaner if available. An appropriately sized Oxy-Acetylene tip cleaner pin may be used to clean out spray nozzle orifices. In areas with hard water or high minerals in water supply, chemical de-scaler may be the quickest and easiest means to remove build-up of deposits. Replace before removing next spray group
Stainless Steel Maintenance/Care Under normal usage, stainless steel products require regular cleaning with a soft clean rag moistened with a mild detergent followed by a water moistened clean rag and then a dry rag. The #4 satin finish steel should be protected against Muriatic acid and caustic or abrasive materials and harsh cleaning detergents. In the event such agents cause discoloration, polish with a stainless-steel cleaner such as 3M Stainless Steel Cleaner & Polish and 3M Scotch Brite pad. Malmet will make available on request circuit diagrams, component parts lists, descriptions, calibration instructions, or information which will assist the user’s appropriately qualified technical personnel to repair those parts of the device.
5.4
Post Maintenance or Repair Safety Checks
After servicing or repair the device shall be checked to confirm correct cycle operation and that device is in a safe operating state before being returned to service.
5.5
Door Safety Test
The following three tests are required to test all safety components of the door locking and position detecting system. 1. Door Position Sensor Test – With the door open, engage the door lock in the lock position and turn off water supply taps. Press the cycle “Start” button, if the sensor is functioning correctly the door lock shall not engage. 2. Micro Switch Test – With the door closed, the water supply taps off and the door lock in the open position (tongue not engaged) press the cycle “Start” button. If the micro switch is functioning correctly the door lock shall not engage and the “In Progress” light will remain off. 3. Door Lock Test – With the door closed and the water supply taps off, lock door normally and press the cycle “Start” button. Once the “In Progress” light turns on, attempt to open the door latch. If door lock is functioning correctly the latch will be locked and unable to be opened. The supply taps can be turned on and device can complete the cycle. This cycle can be used as the operation check also.
5.6
Cycle Operation Check
After completion of the required checks above, a cycle operation check is to be completed. Run the device through a complete cycle ensuring correct sequence of operation as per 4.0 Cycle of Operation in this manual. Inspect for fluid leaks from around the chamber door, rear service connections and beneath the device. If no faults are found during the inspection, and the device displays no faults at end of the cycle the device is fit for return to operation.
5.7
Post Maintenance and Repair of Electrical Systems
Additional to the above safety tests if any repair or service work has been carried out that could affect the electrical safety of the device; it must be inspected and tested as per the requirements of AS/NZS3760 prior to being returned to service. If device fails any of the above tests it is not safe for operation, and cannot be put into service until the cause of the fault has been rectified and successful completion of tests. Issue 4
Page 19
July 23