Operation and Maintenance Manual
14 Pages
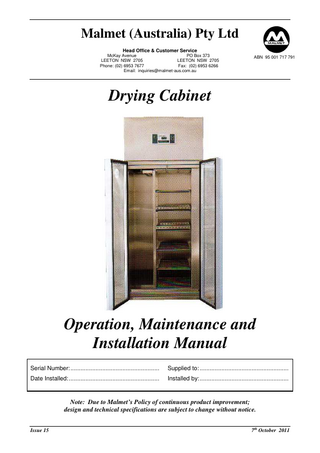
Preview
Page 1
Malmet (Australia) Pty Ltd Head Office & Customer Service McKay Avenue PO Box 373 LEETON NSW 2705 LEETON NSW 2705 Phone: (02) 6953 7677 Fax: (02) 6953 6266 Email: [email protected]
ABN 95 001 717 791
Drying Cabinet
Operation, Maintenance and Installation Manual Serial Number:...
Supplied to: ...
Date Installed:...
Installed by:...
Note: Due to Malmet’s Policy of continuous product improvement; design and technical specifications are subject to change without notice. Issue 15
7th October 2011
Table of Contents Forward... 3 Design Parameters ... 3 Quality Policy... 4 Section A – Unit Operation ... 5 Section B – Unit Maintenance... 6 Trouble Shooting Guide ... 7 Wiring Diagram ... 8 Section C – Unit Installation ... 9 Unit Specifications ... 10 Malmet Warranty Statement... 11
Issue 15
Page 2
7th October 2011
Drying Cabinet
Operation, Maintenance and Installation Manual Forward In order to obtain maximum life and efficiency from your Malmet Drying Cabinet and aid in the safe operation of the unit, please read and understand this manual thoroughly and follow all instructions before operating the unit. The specifications put forth in this manual were in effect at the time of publication. However, owing to Malmet (Australia)’s policy of continuous improvement, changes to these specifications may be made at any time without notice on the part of Malmet (Australia).
Design Parameters The cabinet is designed to dry surgical instruments and metalware, respiratory tubes or other tubing, face masks, anaesthetic bags and other ancillary equipment. A total of six (6) stainless steel shelves is provided. The shelves are removable, with 6 positions including the base. The cabinet is insulated with 25mm approved type insulation. Magnetic door latches are fitted with toughened bi-parting glass doors and gasket to ensure effective seal when the doors are closed. All external panels are fabricated from satin finish stainless steel 0.9mm thick, 304/4 type. A centrifugal fan is provided to circulate air throughout the chamber. A solenoid operated damper is provided to allow air to be exhausted from the chamber. An inlet for make up air is provided. The heating bank (located in the air duct leading to the chamber) is controlled by a microprocessor, which can be incremental set to 70°C. The temperature of the air in the chamber is indicated on the controller mounted on the front panel.
Issue 15
Page 3
7th October 2011
Drying Cabinet
Operation, Maintenance and Installation Manual Quality Policy Malmet (Australia) is Quality Certified to ISO 9001, AS 3902, NZS 9002 and guarantees the quality of this product. Should you have any problems with your machine, contact the company from whom you purchased it, or Malmet (Australia).
Malmet (Australia) Pty Ltd Head Office and Factory PO Box 373 LEETON NSW 2705 Telephone: Facsimile: E-mail: Web Site:
Issue 15
(02) 6953 7677 (02) 6953 6266 [email protected] www.malmet.com.au
Page 4
7th October 2011
Drying Cabinet
Operation, Maintenance and Installation Manual
Section A – Unit Operation NOTE The Drying Cabinet is factory set to 70°C
Before starting the Unit The unit should be run initially on a power supply not protected by an earth leakage circuit breaker for approximately three hours. This will allow any moisture in the heaters to dry out. The unit can then be connected to an earth leakage circuit breaker protected circuit if required. Plug into standard 240V outlet. NOTE:
The unit is recommended for use in a controlled temperature environment.
Starting the Unit Power ON, the preset temperature of the cabinet appears for approximately five seconds. After five seconds the unit switches to display the actual cabinet temperature.
Changing the set temperature (lock out feature) AUTHORISED PERSONNEL ONLY Authorised operators can change the temperature by holding the up and down temperature buttons at the same time for a total of 5 seconds. The temperature can then be adjusted. The setting will revert back to tamper proof 5 seconds after the temperature is adjusted or if the up and down temperature buttons are not pressed within 5 seconds. The unit has a built in electronic over temperature cut out which will switch off the elements if the selected temperature is exceeded by 5°C, and ‘Ot’ w ill flash on the display panel. (See Fig 1) Note: This safety cut out is an automatic reset device.
Fig 1 Place instruments and utensils upside down where applicable. Issue 15
Page 5
7th October 2011
Drying Cabinet
Operation, Maintenance and Installation Manual
Section B – Unit Maintenance Preventative Maintenance Daily
Wipe out inside doors and chamber with warm water and detergent. Wipe over outside panels with stainless steel cleaner.
Weekly
Remove filter on air intake (top right hand side panel) and wash in warm water and replace when dry.
Half Yearly
Check electrical connections. Remove top panel and clean off accumulated dust and dirt. Note: Disconnect power before removing top panel.
Yearly
Issue 15
Check and if necessary replace rubber in tube holding trays.
Page 6
7th October 2011
Drying Cabinet
Operation, Maintenance and Installation Manual Trouble Shooting Guide Problem Display not on or wont turn on.
Probable Cause No Mains power supply.
Suggested Remedy
Power point not turned on.
Check power supply and lead plugged in.
Display will not turn on.
Check power switched on.
Faulty display board.
Press Standby button.
Interconnecting harness failure.
Switch off power supply at main and Call for Service.
Relay board fault.
Switch off power supply at main and Call for Service. Switch off power supply at main and Call for Service.
Display turns on. (Runs for approximately ½ - 1 hour then turns off).
Fan failure.
Switch off power supply at main and Call for Service.
Display is on but unit not heating.
Element failure.
Switch off power supply at main and Call for Service.
Relay board failure.
Switch off power supply at main and Call for Service. Display indicates Ot
Fan Failure. Element on. Continuously unable to switch off. (Relay Board Failure)
Switch off power supply at main and Call for Service. Switch off power supply at main and Call for Service.
Display indicates O/C
Control Temperature Thermistor is broken or unplugged.
Switch off power supply at main and Call for Service.
Display on but unit cooling down.
Element failure.
Switch off power supply at main and Call for Service.
Relay board failure.
Switch off power supply at main and wait 1 minute. Switch mains on. Switch on unit. If problem reoccurs, Call for Service.
Issue 15
Page 7
7th October 2011
Drying Cabinet
Operation, Maintenance and Installation Manual Wiring Diagram
Issue 15
Page 8
7th October 2011
Drying Cabinet
Operation, Maintenance and Installation Manual
Section C – Unit Installation The cabinet must be installed level on adjustable legs.
Service Connections Provide 98mm OD duct to atmosphere. Electrical Connection – 240 Volt 15 Amp cycle. Plug into 15 Amp G.P.O. Wall Recessed Units Plug into standard 240 Volt outlet. - Plug shall be accessible after installation. Outside dimensions pass through – 1850h x 755w x 690d. Cabinet clearance space dimension (eg at least 150mm per side and 500 mm on top) are to be provided for the appliance. Drying cabinet sides are to fit through the wall cavity ensuring that the power cord and filter are not obstructed. Placement should be typically 150mm from the operating panel side doors. There is to be a 5 to10mm gap between the side panel and the timber. Clearance on the top of the Drying Cabinet needs to be typically 500mm. This allows access to replace the electric motor, heating elements etc. Allowing for this 500mm may require the facility to install a false panel in the dividing wall. All electrical service work must be accessible through the top of unit. Position the unit in cavity, assuring that doors can be open and shut in corner manner. NOTE:
This appliance is not intended for use by persons (including children) with reduced physical, sensory, or mental capabilities, or lack of experience and knowledge, unless they have been given supervision or instruction concerning use of the appliance by a person responsible for their safety. Children should be supervised to ensure they do not play with the appliance. If the supply cord is damaged, it must be replaced by the manufacturer or its service agent or a similarly qualified person in order to avoid a hazard.
Issue 15
Page 9
7th October 2011
Drying Cabinet
Operation, Maintenance and Installation Manual Unit Specifications
Electrical Rating
Volts Phase / Hz Amps
Electrical Connection
IEC Power Cord with 3 Pin Plug
Elements
Rated Microprocessor Control Relay
Control PCB Overtemp Protection Temperature Control Secondary Overtemp Protection
Incremental 1°C – 70°C Hight Limit Doors
Materials
Door Gasket Cabinet Air Vent
Air Circulation
Air Filter (mm) Air Bleed Off
Issue 15
Page 10
240V 1 ph / 50 Hz 13.8 Amps 15 Amp (into standard GPO 240 Volt) 1500 watt x 2 PCB (SKCM325) Access via compatible RS232 Electronic cutout @ 5°C above set point Factory set at 70°C Auto reset Bi-Metallic Disc 80°C Bi-parting, protruding 330mm out when open. Silicon Rubber 304/4 stainless steel Automatic Damper Control, to be vented to outside atmosphere. 150mm x 150mm x 15mm washable Automatic Damper Control
7th October 2011
Drying Cabinet
Operation, Maintenance and Installation Manual
Warranty Statement – Australia Only Subject to the following conditions we provide, from the date of purchase, the following warranty:
• •
Functional components found within the unit to be defective in workmanship or material will be replaced free of charge subject to the periods of warranty specified. The structural warranty covers any structural components within the unit, which fail to perform their intended function due to faulty manufacture or deterioration within the warranty period.
This warranty only covers products manufactured by Malmet (Australia) Pty Ltd.
Conditions and Exclusions
• •
• • • • • • • • •
Equipment must be installed according to our instructions (outlined in our Operation, Maintenance and Installation Manual) and operated to the purpose it was designed. Warranty shall not cover damage, malfunction or failure resulting from accident, misuse or misapplication, improper or unauthorised repair, neglect or modification or use of unauthorised replacement parts or accessories, or improper voltage. The warranty shall be void if the serial number is removed or altered. Parts damaged in transit back to Malmet Leeton due to poor packaging could result in warranty claim being rejected. Any part tampered with or has unauthorised repairs and modifications will be rejected as a warranty claim. Reasonable access must be allowed for maintenance. If any additional equipment is needed to provide access to the unit, this must be provided (and paid for) by the owner. It is the owner’s responsibility to provide safe access to the unit. Malmet, or any of its authorised service outlets, may refuse to do maintenance or warranty work if access is unsafe. Should a warranty claim be rejected you will be advised in writing with a full explanation of our reasons. It is our policy to have a Warranty Claim Procedure that is fair to our customers and provides an efficient system of replacement and/or repair of faulty parts. If at any time you believe we are not meeting our commitment to you please contact Malmet Head Office – Leeton. No responsibility will be accepted for outside elements such as storms, pest and vermin that may cause damage to the unit. No responsibility will be accepted for damage contributed by electrical surges or brown outs or any other consequential damages. If there is no certificate of compliance for plumbing or electrical, Malmet reserves the right to refuse service on non-compliant installations.
Issue 15
Page 11
7th October 2011
Drying Cabinet
Operation, Maintenance and Installation Manual •
A charge will be made for work done or service call where:
•
There is nothing wrong with the unit.
•
The defective operation of the unit is due to failure of electricity or water supply.
• • • • • • •
Defects are caused by neglect, incorrect application, abuse or by accidental damage of the unit. An unauthorised person has attempted to repair the unit.
Harsh environmental situations such as water quality that may cause the water tank damage can not be considered warranty. Claims for damage to contents, carpet, ceilings, foundations or any other consequential loss either direct or indirect resulting from, power spikes, incorrect operation, incorrect installation or faulty product are excluded. All warranties are NOT transferable. Unauthorised use of non-genuine Malmet Parts in units covered by Warranty will void all warranty and warranty claims. To the extent permitted by law Warranty labour (service work) shall not include units located outside of city metropolitan areas and costs outside these areas shall be borne by the Customer. The Customer shall be notified of this prior to the warranty call out.
Warranty on Replacement Parts Parts replaced under warranty are warranted for the balance of the original warranty period for that product.
Unit Components
Parts
Labour
Structural Guarantee
1
1
All other components
1
1
Date Sold: ...
Warranty Expiry Date: ...
Sold To:
Issue 15
For Service Contact:
Page 12
7th October 2011
Drying Cabinet
Operation, Maintenance and Installation Manual Proof of Purchase It is important that the name of the distributor from whom you purchased your product and the name of the installer are recorded at the front page of this manual. The installer is responsible for the correct installation, start up and demonstrating the operation of this product. They are also responsible for issuing the relevant certificates of compliance. (These may differ from state to state) Please attach your proof of purchase. Your receipt/invoice is your warranty and will be required to validate any warranty.
E.&O.E. In the interest of continued product improvement, Malmet (Australia) reserves the right to alter specifications without notice.
Issue 15
Page 13
7th October 2011
Manufactured by Malmet (Australia) ABN 95 001 717 791 www.malmet.com.au
P/N 8-M00-87-900