Malmet
Warming Systems
Drying Cabinets Models DCxx Operation , Maintenance and Installation Manual Issue 23
Operation , Maintenance and Installation Manual
23 Pages
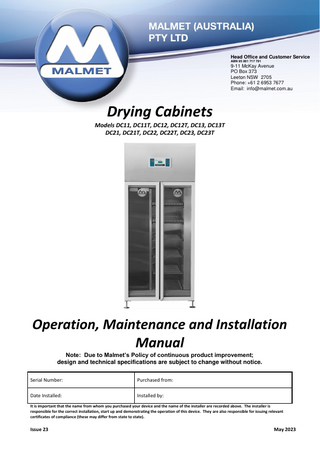
Preview
Page 1
Head Office and Customer Service ABN 95 001 717 791
9-11 McKay Avenue PO Box 373 Leeton NSW 2705 Phone: +61 2 6953 7677 Email: [email protected]
Drying Cabinets Models DC11, DC11T, DC12, DC12T, DC13, DC13T DC21, DC21T, DC22, DC22T, DC23, DC23T
Operation, Maintenance and Installation Manual Note: Due to Malmet’s Policy of continuous product improvement; design and technical specifications are subject to change without notice. Serial Number:
Purchased from:
Date Installed:
Installed by:
It is important that the name from whom you purchased your device and the name of the installer are recorded above. The installer is responsible for the correct installation, start up and demonstrating the operation of this device. They are also responsible for issuing relevant certificates of compliance (these may differ from state to state).
Issue 23
May 2023
Drying Cabinet
Operation, Maintenance and Installation Manual
Table of Contents Foreword ...2 Certifications and Compliances ...2 Quality Policy ...2 Important Warranty Reminder ...2 Malmet Head Office and Factory Contact Details ...2 Safety Instructions - Warnings ...3 1.0 Design Parameters ...4 1.1 Device Operation ...5 1.2 Control Display Features ...5 1.3 Operating Features ...6 1.4 Changing the set temperature (lock out feature) ...7 1.5 Setting the Timer (DC11T/DC12T/DC13T/DC21T/DC22T/DC23T) ...7 1.6 Timer Errors...9 1.7 Door Lock Operation (DC21/DC21T/DC22/DC22T/DC23/DC23T) ...10 2.0 Installation ... 11 2.1 Service Connections ...12 2.2 Device Dimension and Clearances ...12 2.3 Wall Recessed Devices ...13 3.0 Maintenance ... 15 3.1 Preventative Maintenance ...15 3.2 Trouble Shooting Guide ...15 4.0 Technical Specification ... 16 4.1 Device Specifications ...16 4.2 Wiring Diagram (DC11/DC12/DC13/DC21/DC22/DC23)...17 4.3 Wiring Diagram model with timer (DC11T/DC12T/DC13T/DC21T/DC22T/DC23T) ...18 Warranty Statement ... 19
Issue 23
Page 1
May 2023
Drying Cabinet
Operation, Maintenance and Installation Manual Foreword To obtain maximum life and efficiency from your Malmet Drying Cabinet and to ensure safe operation, please read this manual thoroughly and follow all instructions before operating the device. This manual provides information on the operation of the device. It is recommended that all persons operating the device have access to this manual for training purposes. This device is not intended for use by any person without the proper training, experience or knowledge. The specifications supplied in this manual were in effect at the time of publication. However, owing to Malmet (Australia)’s policy of continuous improvement, changes to these specifications may be made at any time without notice on the part of Malmet (Australia).
Certifications and Compliances ARTG Registration Number:
188763 Class 1
Electrical Safety:
Certificate of suitability CS11149N AS/NZS 60335.1:2020
EMC Compliance:
IEC 60601-1-2 Ed 4.0 Emissions CISPR11
Quality Policy Malmet’s quality management system is certified to ISO 9001:2015 and ISO 13485:2016 and guarantees the quality of this product.
Important Warranty Reminder Should you have any problems with your device, contact the company from whom you purchased it, or Malmet (Australia) Pty Ltd. It is important that the name from whom you purchased your device and the name of the installer are recorded on the front page of this manual. The installer is responsible for the correct installation, start up and demonstrating the operation of this device. They are also responsible for issuing relevant certificates of compliance (these may differ from state to state).
Malmet Head Office and Factory Contact Details Malmet (Australia) Pty Ltd 9-11 McKay Avenue PO Box 373 LEETON NSW 2705 Telephone: +61 2 6953 7677 E-mail:
Website: www.malmet.com.au
Issue 23
Page 2
May 2023
Drying Cabinet
Operation, Maintenance and Installation Manual Safety Instructions - Warnings Please read and understand this manual before using this device, if this device is used in a manner not specified by the manufacturer protection by the device may be impaired.
Please refer to this manual for information wherever this warning symbol is displayed -
Be aware of 240 Voltage. Disconnect power when serving. Mains power GPO must be in an accessible position so device can be isolated from mains power during service. If the supply cord is damaged it must be replaced by a special cord or assembly from the manufacturer or its service agent. Do not overload shelves. Do not obstruct air inlets or hot air outlet. Drying Cabinet should be located on a level floor surface and should never be operated on a sloping surface. Install temperature probes, thermostat over temp limiter and element thermal over temperature cut-out correctly. Place instruments and utensils upside down where applicable.
Issue 23
Page 3
May 2023
Drying Cabinet
Operation, Maintenance and Installation Manual 1.0 Design Parameters The Drying Cabinet is designed to dry surgical instruments and metalware, respiratory tubes or other tubing, face masks, anaesthetic bags and other ancillary equipment. A total of six (6) stainless steel shelves are provided. The shelves are removable, with 6 positions including the base. The Drying Cabinet is insulated with 25mm approved insulation. Magnetic door latches are fitted with toughened bi-parting glass doors and gasket to ensure an effective seal when the doors are closed. All external panels are fabricated from satin finish stainless steel 0.9mm thick, 304/4 type. A centrifugal fan is provided to circulate air throughout the chamber. A solenoid operated damper is provided to allow air to be exhausted from the chamber. An inlet for make up air is provided. The heating bank (located in the air duct leading to the chamber) is controlled by a micro-processor, which can be incremental, set to 70°C. The temperature of the air in the chamber is indicated on the controller mounted on the front panel. Heating element over temperature cut out protection.
Issue 23
Page 4
May 2023
Drying Cabinet
Operation, Maintenance and Installation Manual 1.1 Device Operation NOTE The Drying Cabinet is factory set to 70°C
Before starting the Drying Cabinet The Drying Cabinet should be run initially on a power supply not protected by an earth leakage circuit breaker for approximately three hours. This will allow any moisture in the heaters to dry out. The Drying Cabinet can then be connected to an earth leakage circuit breaker protected circuit if required. Plug into standard 15A 240V outlet.
Note: The Drying Cabinet is recommended for use in a controlled temperature environment. Starting the Drying Cabinet Press the Power ON button on the display, the pre-set temperature of the cabinet appears for approximately five seconds. After five seconds the unit switches to display the actual cabinet temperature and will heat to the set target temperature
1.2 Control Display Features
Issue 23
Page 5
May 2023
Drying Cabinet
Operation, Maintenance and Installation Manual
1.3 Operating Features Power ON / OFF
UP and DOWN Temperature Buttons
CYCLE START
“TIME SELECT” for Hrs or Mins “TIME SET” to advance the hrs or Mins
DISPLAY
Issue 23
Page 6
May 2023
Drying Cabinet
Operation, Maintenance and Installation Manual 1.4 Changing the set temperature (lock out feature) AUTHORISED PERSONNEL ONLY Authorised operators can change the temperature by holding the up and down temperature buttons at the same time for a total of 5 seconds. The temperature can then be adjusted. The setting will revert back to tamper proof 5 seconds after the temperature is adjusted or if the up and down temperature buttons are not pressed within 5 seconds. The Drying Cabinet has a built in electronic over temperature cut out which will switch off the elements if the selected temperature is exceeded by 5°C, and ‘Ot’ will flash on the display panel. (See Fig 1) Thermostat Over Temperature Limiter
Note: This safety cut out is an automatic reset device.
Fig 1
1.5 Setting the Timer (DC11T/DC12T/DC13T/DC21T/DC22T/DC23T) Load the Drying Cabinet chamber with components; place instruments and utensils upside down where applicable. Press ‘Power On’ and Set Timer To Set Timer: 1) Press ‘Time Select’. The first digit will begin to flash (hour first) 2) Use ‘Time Set’ to advance the hours (0-6 hours). 3) Press ‘Time Select’ again. The second digit will flash (minutes x 10). 4) Use ‘Time Set’ to advance minutes in tens. 5) Press ‘Time Select’ again. The third digit will flash (minutes x 1) 6) Use ‘Time Set’ to advance minutes.
Note: Issue 23
Time may only be adjusted before ‘Cycle Start’ key is pressed. Page 7
May 2023
Drying Cabinet
Operation, Maintenance and Installation Manual Wait 5 seconds until all 3 digits are flashing in unison. Press ‘Cycle Start’. Once ‘Cycle Start’ is pressed, ‘Time Select’ is locked out. To reset ‘Time Select’ turn off unit and repeat steps 1 to 6. Once ‘Cycle Start’ is pressed, the timer will start counting back. When the unit reaches its set temperature (70°C) the display will stop flashing to indicate count down. If a buzzer sounds when the unit reaches 70°C then ‘Time Select was not pressed after setting the time. Press ‘Time Select’. At completion of cycle, timer panel will display ‘END’. (See Fig 2) Note: For next cycle, ‘Time Select’ will resort to default setting unless reset to another time setting.
Fig 2
Issue 23
Page 8
May 2023
Drying Cabinet
Operation, Maintenance and Installation Manual
1.6 Timer Errors If there is an error a buzzer will sound and ‘err’ will be displayed on timer board. (See Fig 3)
Fig 3
The error could be one of the following:
Issue 23
Problem
Suggested Remedy
Temperature drops by 10°C during cycle
Turn Drying Cabinet off and restart cycle. If problem reoccurs, switch off power supply at main and call for Service.
Door is opened during cycle and temperature drops 10°C.
Turn Drying Cabinet off and restart. Press Cycle Start.
Page 9
May 2023
Drying Cabinet
Operation, Maintenance and Installation Manual 1.7 Door Lock Operation (DC21/DC21T/DC22/DC22T/DC23/DC23T)
Pass through units are fitted with a lock mechanism to prevent the opposite set of doors from those in use being opened at the same time.
To access the unit the operator must unlock the door first, to do this the operator must press and hold the Green “UNLOCK” button while opening the door.
Once the door is open the orange light marked “DOOR OPEN” will illuminate, and the “UNLOCK” button can be released.
When opened the “DOOR OPEN” indicator light on the opposite side of the unit will also illuminate, whilst the light is on the doors on this side cannot be unlocked until the open set of doors have closed and the “DOOR OPEN” indicator light has switched off. On closing the door will lock automatically and the “DOOR OPEN” light will switch off.
Issue 23
Page 10
May 2023
Drying Cabinet
Operation, Maintenance and Installation Manual 2.0 Installation The Drying Cabinet must be installed level on adjustable legs.
Risk Assessment It is recommended a risk assessment is conducted by the user both prior to and after installation and any risks identified mitigated to an acceptable level using the hierarchy of control;
https://commons.wikimedia.org/w/index.php?curid=55610678
Handling Weights of Device:
Net: 185 kg
Shipping: 200 kg
Shipping with crating: 275 kg.
• Handling of the device to installation site must be with fork lift or hand pallet truck. • Before unpacking device inspect carton for any damage relating to forklift forks and damage relating to device falling over or for evidence of top loading • After unpacking the device, inspect all external panels for damage. • Remove the 4 screws holding the device to the pallet.
• Follow your internal manual handling guidelines to manoeuvre the device off the pallet. The device can then be placed into position by fork lift or hand pallet truck.
Disposal of Packaging • Please dispose of packaging as per facility procedures or local government requirements.
Issue 23
Page 11
May 2023
Drying Cabinet
Operation, Maintenance and Installation Manual 2.1 Service Connections Provide 98mm OD duct to atmosphere. Electrical Connection – 240 Volt 15 Amp Plug into 15 Amp G.P.O.
2.2 Device Dimension and Clearances DC11/DC11T/DC12/DC12T/DC13/DC13T
Issue 23
Page 12
May 2023
Drying Cabinet
Operation, Maintenance and Installation Manual DC21/DC21T/DC22/DC22T/DC23/DC23T
2.3 Wall Recessed Devices Plug into standard 240 Volt outlet (plug shall be accessible after installation). Outside dimensions pass through – 1850H x 755W x 690D. Clearance space dimensions are required; at least 150mm per side and 500 mm on top. Drying cabinet sides are to fit through the wall cavity, ensuring that the power cord and filter are not obstructed. Placement should be typically 150mm from the operating panel side doors. A 5-10mm gap between the side panel and the timber is required. Clearance on the top of the Drying Cabinet needs to be typically 500mm. This allows access to replace the electric motor, heating elements etc. Allowing for this 500mm may require the facility to install a false panel in the dividing wall. All electrical service work must be accessible through the top of the Drying Cabinet. Position the Drying Cabinet in the cavity, ensuring that the doors can open and close with clearance for the doors at hinge point. Issue 23
Page 13
May 2023
Drying Cabinet
Operation, Maintenance and Installation Manual
Note: This Drying Cabinet is not intended for use by persons (including children) with reduced physical, sensory, or mental capabilities, or lack of experience and knowledge. Children should be supervised to ensure they do not play with the Drying Cabinet. If the supply cord is damaged, it must be replaced by the manufacturer or its service agent or a similarly qualified person in order to avoid a hazard.
Issue 23
Page 14
May 2023
Drying Cabinet
Operation, Maintenance and Installation Manual 3.0 Maintenance 3.1 Preventative Maintenance Daily
Wipe out inside doors and chamber with warm water and detergent. Wipe over outside panels with stainless steel cleaner.
Monthly
Remove Cabinet Air Intake Filter (Mid right-hand side panel) and clean, use a vacuum to clean the external side of the filter. (Do not use a mechanical cleaning attachment as this may damage the filtration material and affect the performance of the filter)
Half Yearly Check electrical connections. Remove top panel and clean off accumulated dust and dirt.
Note: Disconnect power before removing top panel
Yearly
Check and if necessary replace rubber in tube holding trays. Replace HEPA Cabinet Air Intake Filter. (Part No. 87-3010SP)
3.2 Trouble Shooting Guide Problem Display not on or won’t turn on.
Probable Cause No Mains power supply. Power point not turned on. Display will not turn on. Faulty display board. Interconnecting harness failure. Relay board fault.
Display turns on. (Runs for approximately ½ - 1 hour then turns off). Display is on but unit not heating.
Fan failure.
Display indicates Ot
Display indicates O/C Display on but unit cooling down.
Issue 23
Heating element failure. Relay board failure. Cabinet thermostat O/T limiter auto reset open circuit Element O/T Thermal cut-out manual reset open circuit. Fan Failure. Heating element on. Continuously unable to switch off. (Relay Board Failure) Control Temperature Thermistor is broken or unplugged. Heating element failure. Cabinet thermostat O/T limiter auto reset open circuit Element O/T Thermal cut-out manual reset open circuit. Relay board failure Page 15
Suggested Remedy Check power supply and lead plugged in. Check power switched on. Press Standby button. Switch off power supply at main and Call for Service. Switch off power supply at main and Call for Service. Switch off power supply at main and Call for Service. Switch off power supply at main and Call for Service. Switch off power supply at main and Call for Service.
Switch off power supply at main and Call for Service.
Switch off power supply at main and Call for Service. Switch off power supply at main and Call for Service. Switch off power supply at main and wait 1 minute. Switch mains on. Switch on unit. If problem re-occurs, Call for Service. May 2023
Drying Cabinet
Operation, Maintenance and Installation Manual 4.0 Technical Specification 4.1 Device Specifications Electrical Rating Environment operating conditions Electrical Connection Elements
Volts Phase / Hz Amps Temperature Relative Humidity IEC Power Cord with 3 Pin Plug Rated Over temp cut out protection Microprocessor Control Relay
Control PCB Overtemp Protection Cabinet Temperature Control Cabinet Secondary Overtemp Protection
Incremental 1°C – 70°C High Limit 80°C Doors
Materials
Door Gasket Cabinet Air Vent spigot 98Ø outside
Air Circulation
Air Filter Air Bleed Off
HANDLING & STORAGE CONDITIONS
220-240V 1 ph / 50 Hz 13.8 Amps +10C to +25C +30% to +70% 15 Amp (into standard GPO 240 Volt) 1500 watt x 2 Manual reset thermal cut-out switch NC 115°C Action 2 B,K PCB (SKCM325) Access via compatible RS232 Electronic cutout @ 5°C above set point Factory set at 70°C Auto reset thermostat factory set 80°C Action 2 B Bi-parting, protruding 330mm out when open. Silicon Rubber 304/4 stainless steel Automatic Damper Control, to be vented to outside atmosphere. 150mm x 150mm x 12mm – Mini Pleat H13 HEPA Filter Automatic Damper Control
Fragile
Do not stack Keep away from rain
DIMENSIONS & WEIGHTS Nett
Shipping
Shipping(crated)
185 Kg
200 Kg
275 Kg
755 x 665 x 1850 (mm)
1000 x 810 x 2100 (mm)
Weight
Dimensions (W x D x H) (mm)
Issue 23
Page 16
May 2023
Drying Cabinet
Operation, Maintenance and Installation Manual 4.2 Wiring Diagram (DC11/DC12/DC13/DC21/DC22/DC23)
Issue 23
Page 17
May 2023
Drying Cabinet
Operation, Maintenance and Installation Manual 4.3 Wiring Diagram model with timer (DC11T/DC12T/DC13T/DC21T/DC22T/DC23T)
Issue 23
Page 18
May 2023
Drying Cabinet
Operation, Maintenance and Installation Manual
Warranty Statement This warranty is provided, and operates in addition to, the statutory warranties Malmet (Australia) Pty Ltd ("Malmet") provides to any consumer under the Australian Consumer Law (if applicable) or by virtue of any other applicable legislation. Subject to the following conditions, we provide, from the date of purchase, the following warranty on Malmet devices and spare parts for products manufactured by Malmet and sold in Australia: • Functional components found within the device to be defective in workmanship or material will be repaired or replaced free of charge subject to the periods of warranty specified in the table below. • A decision regarding whether the defective components will be repaired or replaced will be determined at the sole discretion of Malmet or its authorised agents or representatives. • The structural warranty covers any structural components within the device, which fail to perform their intended function due to faulty manufacture or deterioration within the warranty period. • Parts replaced in devices under warranty are warranted for the balance of the original warranty period for that device.
Malmet Devices Device Components Structural Guarantee All other components
Parts & Labour 2 Years from Date of Purchase 2 Years from Date of Purchase Malmet Spare Parts 1 Year from Date of Purchase
The installer is responsible for the correct installation, start up and demonstrating the operation of the product. They are also responsible for issuing the relevant certificates of compliance (these may differ from state to state). CONDITIONS AND EXCLUSIONS • Device must be installed and commissioned according to Malmet’s instructions (outlined in Malmet Operation, Maintenance and Installation Manual) and operated to the purpose it was designed. • Device must be serviced as instructed in the Operation, Maintenance and Installation Manuals. • To the extent permitted by law, this warranty shall not cover damage, malfunction or failure resulting from accident, misuse or misapplication, improper or unauthorised repair, neglect or modification or use of unauthorised replacement parts or accessories, inclusive of detergent, or improper voltage. The warranty may be void if the serial number is removed or altered. • Parts damaged in transit back to Malmet Leeton due to poor packaging could result in warranty claim being rejected in part or in full. • Any part tampered with or which has been altered by unauthorised repairs and/or modifications will be rejected under a warranty claim to the extent permitted by law (to the extent the Australian Consumer Law applies, Malmet will assess the extent to which the tampering or unauthorised repairs contributed to the failure). • Reasonable access must be allowed for maintenance. If any additional equipment is needed to provide access to the device, this must be provided (and paid for) by the owner. • It is the owner's responsibility to provide safe access to the device. Malmet, or any of its authorised service agents, may refuse to perform maintenance or warranty work if access is unsafe, as determined by Malmet or any of its authorised service agents acting reasonably. Issue 23
Page 19
May 2023