MIDMARK
Examination and Procedure Lights
Midmark 354 and 355 Combination Lighting System MA551601 Rev P Installation Manual Jan 2014
Installation Manual
52 Pages
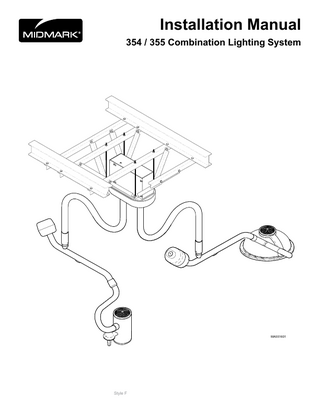
Preview
Page 1
Installation Manual 354 / 355 Combination Lighting System
MA551601
Style F
Based on 8' units with 8' Ceiling and 9' units with 9' Ceiling
Height of Lighthead Assembly Adjustable from 50.0 in. (127.0 cm) to 74.0 in. (188 cm) above floor
180˚ 29.5 in. (70.6 cm)
35˚
35˚
540˚
580˚
50.75 in. (124.5 cm)
53.75 in. (132.0 cm)
13.3 in. (33.8 cm)
580˚
580˚ 580˚
49.5 in. (125.7 cm)
13.3 in. (33.8 cm)
16 in. (40.6 cm)
11.4 in. With 9' Down Tube (28.9 cm)
3.4 in. With 8' Down tube: (8.6 cm)
27.5 in. (69.8 cm)
35˚
35˚
540˚
58.2 in. (147.8 cm)
MA706303
Based on 8' units with 8' Ceiling and 9' units with 9' Ceiling
Height of Lighthead Assembly Adjustable from 53.0 in. (135.0 cm) to 78.0 in. (198.1 cm) above floor .
180˚
Important! - Please Read First This document is broken down into three parts: This page, which provides additional information for installing a 354 / 355 combination light, a 354 Installation Manual, and a 355 Installation Manual. Additional information required to install a 354 /355 combination light.
Equipment Alert Failure to connect the correct model to the correct transformer may result in a blown fuse and / or bulb. The 354 light system’s down arm and 355 light system’s down arm must be connected to the ceiling plate in the position shown (see Figure A). This is necessary because the transformer output voltage is different for each light system and is not interchangeable. To identify the correct mounting location for each light, inspect the transformers. The model 354 transformer is labeled with part number 015-1206-00 and its secondary leads are marked as S-1 (blue wire) and S-2 (brown wire). The model 355 transformer is labeled with part number 015-1356-00 and its secondary leads are unmarked. Use the following two pages of additional information plus the instructions contained in the 354 Installation manual to install and adjust the 354 Lighting System. Use the following two pages of additional information plus the instructions contained in the 355 Installation manual to install and adjust the 355 Lighting System WIRES NOT TAGGED
354 downarm
S1 355 downarm
S2
MA551700
Figure A. Mounting Locations for the for the 354 and 355 Downarms on a 354 / 355 Combination Lighting System
(*) NOTE:
on / standby switch
blue
black
black
blue
354 fan motor
blue brown
blue
line fuses
(*)
TRANSFORMER input leads
black l
N1/114 V
N1/120 V
N1/126 V
N2/114 V
N2/126 V
N2/120 V
g
green white
on / standby switch
blue
blue
blue-s1
354 bulb assembly
brown
120 VAC (SUPPLIED BY CUSTOMER)
brown-s2
brown
blue
green / yellow
black YELLOW (117.0 VAC OR LOWER) ORANGE (117.1 VAC TO 123.0 VAC) RED (123.1 VAC OR HIGHER) YELLOW (117.0 VAC OR LOWER) ORANGE (117.1 VAC TO 123.0 VAC) RED (123.1 VAC OR HIGHER)
blue
20.82 VAC (+/- 0.62 VAC NOMINAL OUTPUT FROM TRANSFORMER LOADED)
354 Transformer
black
brown
TRANSFORMER output leads
355 transformer
24.55 VAC (+/- 0.74 VAC NOMINAL OUTPUT FROM TRANSFORMER LOADED) brown
black
brown
black
MA547901
355 bulb assembly
Select transformer input tap by measuring the input voltage. Then, connect the power lead (white wire) to one of the following according to the input voltage measured: 117.0 VAC or lower - Use the terminal marked N1/114V or N2/114V. 117.1 VAC to 123.0 VAC - Use the terminal marked N1/120V or N2/120V. 123.1 VAC or higher - Use the terminal marked N1/126V or N2/126V.
white jumper wire
Figure B. Wiring Diagram for the 354 / 355 Combination Lighting System
Go To Table Of Contents
Installation Manual 354 Lighting System
Style F
Go To Table Of Contents Owner’s Product Identification (information that you will need to provide for servicing - key information is highlighted) Date of Purchase
Serial Number
Name of Owner / Facility / Department
Model Number
Name of Authorized Dealer
Telephone # of Authorized Dealer
Address of Authorized Dealer
MODEL AND SERIAL NUMBER LOCATION MA551801
Figure 1. Model Number / Serial Number Location
CONTENTS IMPORTANT INFORMATION...2 Scope and Purpose of this Manual...2 Intended Use of Product ...2 Safety Instructions ...2 Explanation of Safety Symbols and Notes...2 Transportation and Storage Conditions ...3 GENERAL INFORMATION ...3 Lighting System ...3 Specifications...3 354 LIGHTING SYSTEM INSTALLATION ...4 Unpacking ...4 Recommended Ceiling Mounting Locations (For Dental and Medical Applications) ...5 Ceiling Support Structure Installation ...5 Electromagnetic Interference ...6 Wiring Installation ...7 Junction Box Wiring Connections ...7 Ceiling Plate Assembly Installation ...9 Down Tube Installation...11 Cross Tube Assembly Installation ...12 Housing Cap Installation...13 Operational Test...13 TROUBLESHOOTING ...13 Troubleshooting Guide ...13 ADJUSTMENTS ...16 Ball Pivot Tension Adjustment...16 Cross Tube Counterbalance Adjustment ...16 CALLING FOR SERVICE ...17 LIMITED WARRANTY ...18
Return To Table Of Contents
IMPORTANT INFORMATION
used as follows:
SCOPE AND PURPOSE OF THIS MANUAL
DANGER A DANGER is used for an imminently hazardous operating procedure, practice, or condition which, if not correctly followed, will result in loss of life or serious personal injury.
This manual covers complete instructions for the installation of the 354 Lighting System and is intended to be used by personnel involved in the installation of the 354 Lighting System. The Operation Manual (Part Number: 003-1071-xx) for the 354 Lighting System is a separate document and is intended for persons who will operate the 354 Lighting System.
WARNING A WARNING is used for a potentially hazardous operating procedure, practice, or condition which, if not correctly followed, could result in loss of life or serious personal injury.
INTENDED USE OF PRODUCT This product is intended for use in all medical environments where illumination is required for external examinations and procedures.
CAUTION
SAFETY INSTRUCTIONS
A CAUTION is used for a potentially hazardous operating procedure, practice, or condition which, if not correctly followed, could result in minor or moderate injury. It may also be used to alert against unsafe practices.
The primary concern of Midmark is that this equipment be operated and maintained with the safety of the users in mind. To assure safer and more reliable operation, do the following: (1) Read this manual before installing your light assembly; (2) Assure that appropriate personnel are informed on the contents of this manual--this is the responsibility of the purchaser; (3) Be sure that you understand the instructions contained in this manual before attempting to install this light assembly; (4) Be sure that you have read and understand the instructions contained in the Operation Manual (a separate document) before attempting to operate this equipment.
EQUIPMENT ALERT An EQUIPMENT ALERT is used for an imminently or potentially hazardous operating procedure, practice, or condition which, if not correctly followed, will or could result in serious, moderate, or minor damage to unit.
EXPLANATION OF SAFETY SYMBOLS AND NOTES
NOTE A NOTE is used to amplify an operating procedure, practice or condition.
Throughout this manual are safety alert symbols that call attention to particular procedures. These items are
Indicates that the unit is rated: Type B, Applied Part.
Indicates a protective earth ground. Indicates that the product is fragile; do not handle roughly.
Indicates that the operator’s manual should be consulted for important information. Indicates the presence of a dangerous voltage / shock hazard.
Indicates the proper shipping orientation for the product. Indicates that the product must be kept dry.
Indicates a fuse rating specification Indicates a hot surface.
© Midmark Corporation 1998
Page 2
Printed in U.S.A.
TRANSPORTATION AND STORAGE CONDITIONS •
Ambient Temperature Range: ... -22°F to 140°F (-30°C to +60°C ) • Relative Humidity ... 10% to 90% (non-condensing) • Atmospheric Pressure ... 500hPa to 1060hPa (0.5 bar to 1.06 bars) This product contains glass, so it should be transported and stored with care to limit vibrations and shocks.
GENERAL INFORMATION LIGHTING SYSTEM The 354 lighthead assembly is a compact spotlight. The spotlight design provides excellent control over the diameter of the lighted area. Through the movement of two levers, the user has complete control over the light beam diameter between 3 in. (7.6 cm) to 10 in. (25.4 cm) and over the brightness of the lighted area. The peak illumination is 4,000 fc (43,000 lux) at a distance of 36 in. (91.4 cm). The plastic handle can be easily removed for sterilization or it accepts a Devon EZ Handle™ without requiring an awkward adapter. The arm assembly has been precisely designed, assembled, and balanced so that the lighthead can be positioned with minimal force and no drifting will occur. In addition, multiple pivot points make the positioning of the lighthead easy and flexible.
SPECIFICATIONS See Table 1 for specifications on the 354 Lighting System. Model 354 Light Beam diameter @ 36 in. (91.4 cm.): ... Variable from 3 to 10 in. (7.6 to 25.4 cm) Bulb: ... 21.0 VAC, 150 W halogen bulb Color temperature: ... 4,200K Focal length: ... 36 in. (91.4 cm) Illumination @ 36 in. (91.4 cm):... 4,000 fc (43,000 lux) Electrical requirement: ... 120 VAC, 60 HZ 1.5 amps, single phase Reach of arm assemblies: ... 49.5 in. (126 cm) maximum from centerline of down tube to center of lighthead.
© Midmark Corporation 1998
Rotation of Lighthead:...180° rotation at lamp tube connection Rotation of lamp tube:...540° rotation at cross tube connection Rotation of cross tube:...580° rotation at down tube connection Vertical range of cross tube:...-35° to +35° vertical movement Rotation of down tube: ...580° rotation at ceiling plate connection Weight of 8 ft. (2.44 m) single light assembly: ...59 lbs (26.8 kg) Weight of 9 ft. (2.74 m) single light assembly: ...60 lbs (27.2 kg) Weight of 8 ft. (2.44 m) dual light assembly: ...105 lbs (47.6 kg) Weight of 9 ft. (2.74 m) dual light assembly: ...107 (48.5 kg) Certifications:...
Classified by 94XM
Underwriters Laboratories Inc. with respect to electric shock, fire, and mechanical hazards only in accordance with UL2601-1 and CAN/CSA C22.2, No.601.1. ISO-9001 Certified Classifications: ...Class 1, Type B applied part, Ordinary Equipment, Continuous Operation Fuse Rating: ...1.6 amp, 250 VAC, 5mm x 20mm, Type T, low breaking capacity, IEC 127-2/3 Equipment not suitable for use in the presence of a flammable anesthetic mixture with air, oxygen, or nitrous oxide.
Page 3
Printed in U.S.A.
354 LIGHTING SYSTEM INSTALLATION
(3) Remove one/two down tube assembly (2) and inspect.
UNPACKING
(4) Remove one/two bag(s) (3) and inventory contents; the following items should be included: 3a. Four #10-24 x 3/4” socket cap screws 3b. Two/four #10-24 x 3/8” black oxide button head screws 3c. Six/twelve 3/8”-16 hex nuts 3d. Three/six 3/8” lockwashers 3e. One/two #10-24 x 5/8” zinc plated button head screws 3f. One/two #10-24 x 3/8” pan head screws 3g. One 100 Watt Halogen Bulb 3h One/two sterilizable handle (inspect) (5) Remove one ceiling plate assembly (4) and inspect.
NOTE Below is a list of all the items which should be included in the shipping box(es). The first quantity indicates the number of items which should be present for a single lighting assembly while the second quantity indicates the number of items which should be present for a dual lighting assembly (Refer to Figure 2). (1) Cut banding and remove box lid from box. (2) Remove one / two cross tube/lighthead assembly (1, Figure 2) and inspect.
(6) Remove one ceiling cover (5) and inspect.
4 #10-24 x 3/4" Cap Screw (3a) #10-24 x 3/8" Button Head Screw (3b)
3
#3/8"-16 Hex Nut (3c) 3/8" Lockwasher (3d) #10-24 x 5/8" Button Head Screw (3e) #10-24 x 3/8" Pan Head Screw (3f)
2
100 W Halogen Bulb (3g)
5
Sterilizable Handle (3h)
1 MA9138i
© Midmark Corporation 1998
Page 4
Printed in U.S.A.
RECOMMENDED CEILING MOUNTING LOCATIONS (FOR DENTAL AND MEDICAL APPLICATIONS) See Figure 3 for recommended ceiling mounting locations. These locations allow the lighthead to be positioned over any portion of the patients body without running into a physical arm restriction; mounting the light system on the centerline of the chair or headrest will result in some areas of the patient’s body not being able to be illuminated by the lighthead. Also, the light system should be mounted on the opposite side of the table as the doctor’s work position, so the light system is not hanging above their head.
NOTE When installing ceiling plate it is recommended to leave adequate distance to access and remove junction box cover
Ceiling Mounting Locations 30" 27" Max.
27" Max. 12" Min.
CEILING SUPPORT STRUCTURE INSTALLATION Weights: • 8 ft. (2.44 m) Single 354 Lighting System (less customer supplied ceiling structure):... 59 lbs (26.8 kgs) • 9 ft. (2.74 m) Single 354 Lighting System (less customer supplied ceiling structure):... 60 lbs (27.2 kgs) • 8 ft. (2.44 m) Dual 354 Lighting System (less customer supplied ceiling structure):... 105 lbs (47.6 kgs) • 9 ft. (2.74 m) Dual 354 Lighting System (less customer supplied ceiling structure):... 107 lbs (48.5 kgs) Torques: • 8 ft. (2.44 m) Single 354 Lighting System: ...69 ft-lbs (94 N•m) • 9 ft. (2.74 m) Single 354 Lighting System: ...69 ft-lbs (94 N•m) • 8 ft. (2.44 m) Dual 354 Lighting System: ...136 ft-lbs (184 N•m) • 9 ft. (2.74 m) Dual 354 Lighting System: ...137 ft-lbs (186 N•m)
CL of Head
12" Min.
CL of Chair
NOTE
12" Min.
The illustrations in Figure 4 are for suggestion only. Midmark does not supply ceiling structures. Consult a structural engineer for the best solution for your situation.
27" Max.
Ceiling Mounting Locations MA538800
Figure 3. Recommended Ceiling Mounting Locations (For Dental and Medical Applications
The 354 lighting system requires a sturdy ceiling support structure to support the weight and the dynamic torque which will be applied to the support structure (See Figure 4)
.
© Midmark Corporation 1998
Page 5
Printed in U.S.A.
CEILING PLATE LAYOUT 29.2 cm (11.50")
18.4 cm (7.24")
10.8 cm (4.25")
15.2 cm (6.00")
(4) 1.4 cm (0.56”) DIA. MOUNTING HOLES
7.6 cm (3.00") 15.2 cm (6.00")
76.2 cm (30")
15.24 cm (6”) SQUARE
SIDE SUPPORT BRACE TO PREVENT DRIFTING
12 mm (1/2”) ALL THREADBOLTS
16.51 CM (6.5”) MINIMUM CLEARANCE
LATERAL SUPPORT BRACE TO PREVENT DRIFTING
3.8 cm - 5.1 cm (1 1/2" - 2")
SUGGESTED ACCESS HOLE TO BE 2.54 cm (1”) SMALLER THAN CEILING COVER
1.3 cm (1/2")
THIS SURFACE SHOULD BE FLUSH WITH BOTTOM OF CEILING
CEILING
1.9 cm (3/4") MA547700
Figure 4. Suggested Ceiling Support Structure Installation (Illustration applies to Single and Dual Mounted Lighting Systems) The ceiling support structure must be strong enough to uphold the weight of the system and support the rotating suspension tubes and Lighthead(s) without deflection. The 354 lighting system is engineered for ease of movement during positioning. The suspension assemblies and lighthead(s) will rotate with a minimum of force, provided the ceiling plate assembly is level and stays level. If, however, the ceiling support is weak and flexes, the weakness will have a negative impact on the operation of the tube assemblies during positioning. If the ceiling support structure flexes too much, the lighthead(s) will drift to the lowest point. Although the arms © Midmark Corporation 1998
are equipped with brakes to prevent drift, the undesirable side effect of stiffer braking, is that the arm assemblies / lighthead(s) will be harder to move. For a set of tube assemblies to rotate without drift and a minimum amount of force, the ceiling plate assembly must not be allowed to deflect more than 1/16 in. (1.58 mm) over a 12 in. (30.5 cm) distance. The ceiling plate must be level and stay level when the tube assemblies are rotated in every position and all worst case scenarios (example: two sets of tube assemblies on one side). This means that the ceiling support structure must be braced in multiple directions.
Page 6
Printed in U.S.A.
The 354 lighting system comes in two different versions: an 8 ft. (2.44 m) version for a 8 ft. (2.44 m) ceiling and a 9 ft. (2.74 m) version for a 9 ft. (2.74 m) ceiling. The bottom of the ceiling plate assembly must be installed so it is flush with the finished surface of the facility’s ceiling. See Figure 4. The ceiling cover is designed to fit up against the finished ceiling.
(4) Feed the facility supplied wiring through the knockout in the junction box (3).
WARNING Make sure the facility supplied wiring is not shorted to the junction box and does not touch wires during steps 5 and 6. Failure to do so could result in electrical shock, causing serious personal injury or death.
ELECTROMAGNETIC INTERFERENCE This product is designed and built to minimize electromagnetic interference with other devices. However, if interference is noticed between another device and this product, remove the interfering device from the room or wire this product into an isolated circuit.
(5) Turn on facility power breaker so there is power in customer supplied wiring. (6) Using a multimeter, measure the input voltage between black power lead and white neutral lead of customer supplied wiring. Record this voltage.
WIRING INSTALLATION
WARNING
The wiring, supplying power to the junction box of the 354 lighting system, must be supplied by the customer. The 354 lighting system requires 120 VAC input voltage. The wire should be a 2-conductor with ground, 14 gauge copper wiring, rated for 120 VAC. The customer supplied wiring must be connected to the junction box with some form of strain relief fitting, preferably a conduit fitting. Connect and route the wiring in accordance with local and national codes, using conduit where necessary. See wiring diagram, Figure 5.
Make sure the power to the facility supplied wiring is turned “off” for the following step. Failure to do so could result in electrical shock, causing serious personal injury or death. (7) Turn “off” facility power breaker so there is no power in customer supplied wiring. (8) If voltage measured in step 6 was 117.0 VAC or lower, connect the white neutral lead of customer supplied wiring to the terminal marked N/114V for single units or N1/114V or N2/114V for double units (see Figure 5). If voltage measured in step 6 was between 117.1 and 123.0 VAC, connect the white neutral lead of customer supplied wiring to the terminal marked N/120V for single units or N1/120V or N2/120V for double units (see Figure 5). If voltage measured in step 6 was 123.1 VAC or higher, connect the white neutral lead of customer supplied wiring to the terminal marked N/126V for single units or N1/126V or N2/126V for double units (see Figure 5).
JUNCTION BOX WIRING CONNECTIONS (SEE FIGURE 5) WARNING Make sure the power to the facility supplied wiring is turned “off” for the following step. Failure to do so could result in electrical shock, causing serious personal injury or death. (1) Turn off facility power breaker so there is no power in customer supplied wiring. (2) Loosen, but do not remove, four screws (1, Figure 7); then pull outward on box cover (2) and remove box cover from junction box (3).
(9) Connect the black power wire from customer supplied wiring to the terminal marked L.
(3) Install conduit fitting (customer supplied) in the knockout of the junction box (3).
© Midmark Corporation 1998
Page 7
Printed in U.S.A.
JUNCTION BOX YELLOW (117.0 VAC OR LOWER) ORANGE (117.1 VAC TO 123.0 VAC) RED (123.1 VAC OR HIGHER)
BLACK G N/126 V
TRANSFORMER
N/120 V N/114 V
BROWN BROWN
20.82 VAC (+/- 0.62 VAC NOMINAL OUTPUT FROM TRANSFORMER - LOADED)
BULB ASSEMBLY
BLACK
120 VAC (SUPPLIED BY CUSTOMER) BROWN BLUE
FAN MOTOR
BLUE ON / STANDBY SWITCH
(*) NOTE: Select transformer input tap by measuring the input voltage. Then, connect the power lead (white wire) to one of the following according to the input voltage measured: 117.0 VAC or lower - Use the terminal marked N/114V. 117.1 VAC to 123.0 VAC - Use the terminal marked N/120V. 123.1 VAC or higher - Use the terminal marked N/126V.
(10) Connect the green/yellow earth ground wire from customer supplied wiring to the terminal marked with a ground symbol G.
CAUTION Failure to properly connect and insulate wires in junction box could result in a short or electrical shock to personnel or improper system operation. • Always use a strain relief (conduit fitting) between facility wiring and the junction box. • Always connect the earth ground wires inside the junction box. • Double Units-Always make certain the white jumper wire is properly positioned.
© Midmark Corporation 1998
(11) If light system is a dual light, the white jumper wire on the terminal block may need to be repositioned depending on the voltage measurement taken in step 6. If the voltage measurement was 117.0 VAC or lower, use white jumper wire to connect N1/114V to N2/114V. If the voltage measurement was 117.1 VAC to 123.0 VAC, keep white jumper wire where it is; connecting N1/120V to N2/120V. If the voltage measurement was 123.1 VAC or higher, use white jumper wire to connect N1/126V to N2/126V.
NOTE It is especially important to perform steps 12 and 13 now if the ceiling is a drywall/plastered ceiling; these steps will not be able to be performed later. Page 8
Printed in U.S.A.
Figure 5 (Sheet 2 of 2). Wiring Diagram - Double Unit
BLUE BLUE
TRANSFORMER OUTPUT LEADS
BLACK
TRANSFORMER INPUT LEADS
F1 (LINE FUSE)
(*)
L
WHITE GREEN
BLACK
BLACK
GREEN/ YELLOW
Page 9
WHITE JUMPER WIRE
G
BROWN BLUE
BROWN
BLUE
120 VAC (SUPPLIED BY CUSTOMER)
(*) TRANSFORMER INPUT LEADS
L BLACK
N1/114 V
N1/120 V
N2/114 V N1/126 V
N2/120 V
N2/126 V
WHITE GREEN
FAN MOTOR
BULB ASSEMBLY
BLUE
TRANSFORMER OUTPUT LEADS
20.82 VAC (+/- 0.62 VAC NOMINAL OUTPUT FROM TRANSFORMER - LOADED)
TRANSFORMER
ON / STANDBY SWITCH
BROWN
Select transformer input tap by measuring the input voltage. Then, connect the power lead (white wire) to one of the following according to the input voltage measured: 117.0 VAC or lower - Use the terminal marked N1/114V or N2/114V. 117.1 VAC to 123.0 VAC - Use the terminal marked N1/120V or N2/120V. 123.1 VAC or higher - Use the terminal marked N1/126V or N2/126V.
(*) NOTE:
BLUE
LINE FUSES
GREEN/ YELLOW
YELLOW (117.0 VAC OR LOWER) ORANGE (117.1 VAC TO 123.0 VAC) RED (123.1 VAC OR HIGHER) YELLOW (117.0 VAC OR LOWER) ORANGE (117.1 VAC TO 123.0 VAC) RED (123.1 VAC OR HIGHER)
BLUE BLUE
BLACK
BROWN BROWN
BLUE BLUE
BROWN BROWN
BLACK
BLACK BLACK
© Midmark Corporation 1998
Printed in U.S.A.
FAN MOTOR
BULB ASSEMBLY
(12) Feed brown and blue transformer output wires out of wire hole (7, Figure 7) in bottom of junction box.
CEILING PLATE ASSEMBLY INSTALLATION
(13) Position box cover (2) on junction box (3) and secure by tightening four screws (1).
NOTE The following step describes one typical way of mounting the ceiling plate assembly. However, this method may not work for all installations; if not, use the following procedure for guidance only. (1) Install four 1/2” nuts (1, Figure 6) on four all-thread bolts (2) (not supplied).
3 1
2 THIS SURFACE SHOULD BE FLUSH WITH BOTTOM OF CEILING
4
5
MA 03 5 8 2
Figure 6. Suggested Ceiling Plate Assembly Installation
© Midmark Corporation 1998
Page 10
Printed in U.S.A.
(2) Install ceiling plate assembly (3) on four all-thread bolts (2) and secure with four 1/2” lockwashers (4) and 1/2” nuts (5).
(6) Under normal circumstances, the down tube (6) should be level enough to provide drift-free operation. If, after complete assembly and operation of the light system, drifting is observed, use a protractor or level (C) to adjust nuts (9) until down tube (6) is vertical (+/- 0.5°); then tighten nuts (4).
NOTE For the following step, make sure nuts (1) are not contacting the ceiling plate assembly (3). Otherwise, leveling of ceiling plate assembly with nuts (5) will not be possible.
(7) If light system is a dual light, repeat steps 1 through 6 for remaining down tube (6). (8) Slide ceiling cover (10) onto down tube(s) (6).
(3) Adjust four nuts (5) until bottom of ceiling plate assembly (3) is flush with surface of ceiling.
(9) Attach ceiling cover (10) to ceiling plate (11) with four #10-24 x 3/4” screws (12) (supplied).
WARNING
CROSS TUBE ASSEMBLY INSTALLATION
Failure to install nuts (5) so that there are at least two full threads visible below nuts, could result in unit falling.
EQUIPMENT ALERT
DOWN TUBE INSTALLATION
When assembling a dual light system combination consisting of a model 354 mounted in combination with a model 355, special care must be taken to ensure that the proper transformer is used for each cross tube / lighthead assembly. Failure to do so may result in a blown fuse and / or bulb. The transformer output voltage is different for the two models. The model 354 transformer is labeled with part number 015-1206-00 and its secondary leads are marked S1 and S2. The Model 355 transformer is labeled with part number 0151356-00 and its secondary leads are not marked.
(1) Thread three 3/8” x 16 hex nuts (4, Figure 7) (supplied) onto three bolts (5) until they are handtight; then back off each nut one full turn.
(1) Slide ball pivot sleeve (1, Figure 8) onto down tube (2), making sure screw hole in sleeve is on the bottom.
(2) Position down tube (6) near wire hole (7).
(2) With ball pivot sleeve (1) positioned as high as possible on down tube (2), pull blue and brown wires (6) through top window (A) of down tube.
(4) Use a level to check the levelness of ceiling plate assembly (3) in all directions. Adjust four nuts (5) as necessary until the ceiling plate assembly (3) is level in all directions and flush with surface of ceiling. (5) Tighten nuts (1) against ceiling plate assembly (3); then recheck levelness of ceiling plate and readjust if necessary.
(3) Connect brown wire (S2) from junction box (3) to brown wire (A) from down tube (6).
NOTE
(4) Connect blue wire (S1) from junction box (3) to blue wire (B) from down tube (6). (5) Install down tube (6) on three bolts (5) and secure with three 3/8” lockwashers (8) and 3/8” x 16 hex nuts (9) (supplied).
WARNING
There are three screw holes in cross tube (3); two of the holes are larger and have a courser thread. Use these two holes to secure cross tube assembly with screws (5). The other hole is for securing ball pivot sleeve. (3) Align three screw holes; then insert pivot shaft of cross tube assembly (3) into down tube (2). Secure cross tube assembly in position with two #10-24 x 3/8” black oxide button head screws (5).
Failure to install nuts (9) so that there are at least two full threads visible below nuts, could result in unit falling.
(4) Feed two wires (4) through top window (A) of down tube (2).
© Midmark Corporation 1998
Page 11
Printed in U.S.A.
Figure 7. Down Tube Installation (5) Connect brown wire (4) to brown wire (6) and blue wire (4) to blue wire (6). Push wires into top window (A). (6) Slide ball pivot sleeve (1) down into position and secure with one #10-24 x 3/8” (New Units Only) pan head screw(7) (Refer to Page 5).
HOUSING CAP INSTALLATION (1) Install housing cap (2, figure 11) on ballast housing (3) and secure with screw (1).
OPERATIONAL TEST
(7) If light system is a dual light, repeat steps 1 thru 6 for the remaining cross tube assembly. Special care must be taken when assembling a 354 / 355 combination unit as noted in the Equipment Alert.
© Midmark Corporation 1998
Page 12
(1) Turn the ON / STANDBY switch (1, Figure 9) to ON “I”. (2) Observe. The lighthead (2) should illuminate and the fan in the back of the lighthead should be operating.
Printed in U.S.A.
(5) Rotate the lighthead (2), lamp tube (3), cross tube (4), and down tube (5) through their range of motions as shown on the illustration. Release the lighthead at different positions. (6) Observe. The lighthead (2) should be able to be positioned easily through the entire range of its motion. When the lighthead is released in any position, no drifting should occur at any axis. (7) Adjust the brightness control lever (6) through its range of motion. (8) Observe. The light beam should brighten / darken as the brightness control lever (6) is adjusted. (9) Adjust the brightness control lever (6) to achieve maximum brightness, then adjust the beam size lever (7) through its range of motion. (10) Observe. The light beam pattern should change from approximately 3 in. to 10 in. (7.6 to 25.4 cm) as the beam size lever (7) is adjusted. (11) If any problems are discovered, refer to the troubleshooting guide for adjustment and repair tips.
TROUBLESHOOTING TROUBLESHOOTING GUIDE Figure 8. Cross Tube Assembly Installation If any problems are discovered during the installation process, refer to the following table (Table 1) to determine the cause of the problem.
(3) Position the lighthead (2) 36 in. (91.4 cm) from a table and aim the light beam at the table. (4) Observe. There should be a circular pattern of bright light on the table surface.
Table 1. Troubleshooting Guide PROBLEM
POSSIBLE CAUSE
SOLUTION
no light from lighthead
lighthead is on STAND-
turn ON / STANDBY switch to ON “I”
BY “ no light from lighthead, but ON / STANDBY switch is ON “I”
© Midmark Corporation 1998
“
bulb has burned out or has not been installed
refer to bulb replacement procedure in this manual
fuse in junction box is blown
inspect / replace the fuse located inside the ceiling cover
no power to the junction box
check for facility power to the junction box
transformer is malfunctioning
check for 20.8 VAC output at the transformer when it is under load.
Page 13
Printed in U.S.A.
5
1
2
540 35
3
4 35 180
580 580
A
36" (91.4 cm)
APPROXIMATELY 3” (7.6 CM) TO 10” (25.4 CM) AT A DISTANCE OF 36” (91.4 CM)
7 MA552200
6 Figure 9. Operational Test
© Midmark Corporation 1998
Page 14
Printed in U.S.A.