User Guide
20 Pages
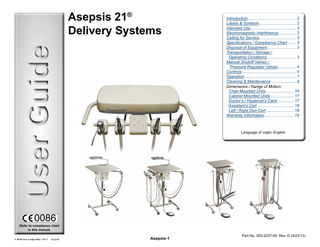
Preview
Page 1
User Guide
Asepsis 21® Delivery Systems
Introduction... 2 Labels & Symbols... 2 Intended Use... 3 Electromagnetic Interference... 3 Calling for Service... 3 Specifications / Compliance Chart ... 3 Disposal of Equipment... 3 Transportation / Storage / Operating Conditions... 3 Manual Shutoff Valves / Pressure Regulator Valves... 4 Controls... 5 Operation ... 7 Cleaning & Maintenance... Chair Mounted Units... 16 Cabinet Mounted Units ... 17 Doctor’s / Hygienist’s Carts... 17 Assistant’s Cart ... 18 Left / Right Duo Cart ... 18 Warranty Information... 19
Language of origin: English
0086 Refer to compliance chart in this manual.
Asepsis-1
Part No. 003-2237-00 Rev. D (4/23/13)
Introduction Your Asepsis 21 Delivery system has been designed and manufactured with care and you in mind. It is constructed of the highest quality material to provide years of trouble-free service. The instrument head provides for the control of up to five air operated handpieces and a 3-way syringe. The handpieces are stored in their respective holders which may be rotated to your preferred position. When the handpiece is removed from the holder, it is automatically selected to operate when the foot control is depressed. Your new Asepsis 21 also features a handpiece lubricant collection system. The handpiece exhaust tubes from the four port handpiece tubes are connected to a collector jar which is located on the bottom center of the instrument head. The collection jar can be removed to be emptied and cleaned simply by unscrewing it from the unit. The collector jar should be inspected daily and emptied when approximately 1/2 inch of oil has accumulated. The aerodynamic shape of the instrument head lends itself to easy cleaning or wrapping for infection control.
Symbols These symbols may appear on your equipment and/or in the manuals Warning and cautions are provided in the manuals where applicable. Consult Manuals
Type B, Applied Part
warning
Indicates a potentially hazardous situation which could result in serious injury if not avoided.
Pressure Limit
Type BF, Applied Part
Caution
Indicates a potentially hazardous situation which may result in minor or moderate injury if not avoided. It may also be used to alert against unsafe practices
Equipment Alert
Indicates a potentially hazardous situation which could result in equipment damage if not avoided.
100 F
Protective Earth Ground
38 C
Temperature Limit
23 F -5 C
Proper Shipping Orientation
Humidity Limit
Fragile
Maximum stacking height (Refer to “n” number on package.)
NOTE
Amplifies a procedure, practice, or condition. Keep Dry
© Midmark Corporation 2010
Asepsis-2
Intended Use
Specifications
Midmark delivery systems are intended to provide dental professionals with air, water and suction to operate dental handpieces, syringes, and Midmark authorized accessories during dental examinations and procedures.
Air / Water Pressure Operating Ranges:
Air: 80/100 PSI Water: 30/50 PSI
Classifications
Class I, Type B, Applied Part, Ordinary Equipment. [IPXO]
Optional Accessories:
Electromagnetic Interference
Handpiece tubing and connectors intended to be used with ISO 7785-1 or ISO 7785-2 compliant air-driven handpieces
Midmark dental operatory components are designed and built to minimize electromagnetic interference with other devices. However, if interference is noticed between another device and this operatory, remove the interfering device from room and / or plug product into an isolated circuit.
Type B Applied Part
warning
Equipment is not suitable for use in the presence of a flammable anesthetic mixture with oxygen, air, or nitrous oxide.
Calling For Service
Clarification: Equipment is suitable for use in the presence of oxygen, air, or nitrous oxide.
Direct all service inquiries to your authorized Midmark dealer. When calling for service, you must provide the following information:
Disposal of Equipment
Model / serial number Date of purchase Symptom(s) of malfunction
At the end of this product’s life, the unit, accessories and other consumable goods may be contaminated from normal use. Consult local codes and ordinances for proper disposal of this equipment and other consumable goods.
Authorized CE Representative Countries in the EEC should direct all questions, incidents, and complaints to Midmark’s Authorized CE representative listed below. Midmark Europe SAS 22, Rue De St. Denis 53500 Ernee, FRANCE Phone: 33-2-430-517-76 Fax: 33-2-430-569-10
Transportation / Storage / Operating Conditions Transportation / Storage Temperature:...23°F to 100°F (-5°C to +38°C) Relative Humidity:... 10% to 90% (non-condensing) Atmospheric Pressure:... 7.2 PSI to 15.3 PSI (50 kPa to 106 kPa) Operating Temperature Range: ...59°F to 95°F (15°C to 35°C) Complies To:
Description
Mounted on (Type)
Asepsis 21 Delivery Systems
Ultra Chair
Asepsis 21 Delivery Systems
Knight Chair or Carts
© Midmark Corporation 2010
UL 60601-1 (2nd Edition)
•
CAN / CSA 22.2, #601.1 - M90
Electrical Ratings:
ES/IEC/ EN 60601-1
EN 60601-1-2 (EMC Standards)
CAN / CSA 22.2, #60601.1
CE
•
•
•
•
• Asepsis-3
Volt +/- 10%
Maximimum Connected Load
Cycles (Hz) Power Supply Model No.: 153808-001, -002
N/A 120
15 A
50/60
240
7.5 A
50/60
Manual Shut-Off Valves / Pressure Regulator Valves Manual shut-off valves allow you to stop the air and/or water supply at the point of input to the operatory. This is recommended during extended periods of non-use (ex. vacation, holidays, etc.), or in the event of an equipment malfunction. Pressure regulator valves allow you to control the air and water pressure supplied to the instruments of the delivery system.
City Water Gauge
Water Bottle Regulator DO NOT ADJUST
City Water Regulator Adjustment Knob
Shut-off Valves Rotate clockwise 1/4 turn to Shut off.
Air Regulator Adjustment Knob Water Manual Shut-off Valve
To Adjust the Pressure Regulators...
A) Pull up knob and turn to adjust. B) Watch regulator gauge as you turn knob to achieve desired setting.
40
20
2
60
3 4
5 0
80
0
1
6 7 100
Air Manual Shut-off Valve
Air Regulator Gauge
Turn Clockwise for more pressure
Turn Counter-Clockwise for less pressure
Recommended Settings:
Water Bottle Regulator Setting
Factory set to 30 psi DO NOT adjust
Delivery components were designed to operate at the recommended settings. Poor performance or damage to the equipment may result if recommended settings are not maintained.
4 5
80
Air Pressure 80 psi RegulatorGauge Setting
Equipment Alert
6 7 0
10 0
City Water 30 psi RegulatorGauge Setting
KA947002
© Midmark Corporation 2010
Asepsis-4
Controls Asepsis 21 Instrument Head: A complete set of handpiece and syringe adjustments are located directly under the magnetically held cover for protection against contamination. Lift up either back corner of the cover for easy removal. All controls are labeled with symbols identifying their function.
1
2
3
9 Coolant Air Volume Adjustment
Handpiece Coolant Water Volume
This adjustment controls the volume of coolant delivered to each handpiece. It affects the spray pattern of air and water at the handpiece. If the handpiece has a coolant air connection in the handpiece itself, this adjustment will have no effect and can be completely shut off.
Adjusts the amount of coolant water to each respective handpiece.
4
5
6
Drive Air Pressure Setting
10
Individual adjustments are provided - one for each respective handpiece. Set the maximum handpiece pressure indicated on the gauge. Refer to the handpiece manufacturer’s specifications for proper setting.
Handpiece Pressure Gauge Indicates individual handpiece pressure when the handpiece is operating.
7
11
12
13
Syringe Air Volume Adjustment
Magnetic Latches
Controls the volume of air to the syringe and effects water spray pattern.
These hold the cover in place.
8 14
Syringe Water Volume Adjustment
Handpiece Coolant Water Flush Button
Controls the volume of water to the syringe and effects water spray pattern.
© Midmark Corporation 2010
Controls the coolant water flush valve and is located on the underside of the delivery head.
Asepsis-5
Controls - continued External Controls Main ON / OFF Valve
Arm Lock (chair mtd. units only)
Located on the bottom center of the instrument head directly behind the handpiece holder bar support, this two position toggle control turns the main air and water ON / OFF. (See illustration below)
Located on the bottom of the instrument head adjacent to the handle, this two position toggle controls the arm lock mechanism.
Assistant’s Instrumentation
Water Outlet and Flow Control
A saliva ejector, HVE and syringe are standard instrumentation on the unit. They are positioned on a movable holder located on the console. Syringe tip, saliva ejector valve assembly and HVE valve assembly are easily removed for sterilization.
Located on the front panel of the console, the water outlet provides water for hydrocolloid tubing or other accessories. The water is controlled by a flow control knkob located next to the water outlet. Turning the knob clockwise decreases water flow, and counterclockwise increases the flow.
Water Selector Switch
Automatic Handpiece Activation
This switch, located on the front of the console or the LR arm, allows you to choose the water source for the delivery system. You may select either “City” water (tap water), or water from the Self-Contained Water System bottle.
The automatic kink valves are designed to permit activation of the selected handpiece when it is removed from its holder. Drive air will be delivered to the withdrawn handpiece when the foot control is depressed.
“City” water
Water ON / OFF Valve
Blue dot indicates “wet” operation
Located on the foot control, this switch provides water for coolant spray to the handpiece when the switch is moved forward to the ON position (toward the blue dot) and the foot control is depressed (wet cutting). When the valve is in the OFF position, water will not be delivered to any handpiece. (See illustration below).
Self-Contained Water System
Wet / Dry Foot Control The disc-type foot control operates the selected handpiece at varying speeds depending upon the foot pressure applied to the disc. Positioning the coolant water selector toggle allows coolant water for wet cutting to be selected by the motion of the foot. Applying foot pressure to the disc will operate the selected handpiece and, if turned ON, water spray. (See illustration below).
© Midmark Corporation 2010
Asepsis-6 DA
Operation The automatic kink valves are designed to permit activation of the selected handpiece when it is removed from its holder. Drive air will be delivered to the withdrawn handpiece when the foot control is depressed. (See the illustration) Basic Operation:
Step 1:
Turn ON the master valve lever located on the underside of the Asepsis 21 instrument head.
Step 2:
Flip the wet/dry toggle on the foot control to the desired position.
Step 3:
Lift the handpiece from its holder and depress the foot control.
Step 4:
© Midmark Corporation 2010
If necessary, make adjustments by lifting the cover off the Asepsis 21 head and adjusting the control knobs as desired. (See Controls section)
Asepsis-7
Cleaning, Disinfecting & Maintenance ATTENTION
Midmark assumes no responsibility or liability for any result, expressed or implied. These are suggested practices, based on the best information available at this time this is written..
Barrier
Scheduled Maintenance Chart Area
Frequency
Unit surfaces
as necessary
Hoses
as necessary
Vacuum system
as necessary
Solids collector
daily
Regulator filters (air / water)
every 3 months
Barrier Barrier DA178400i
Barriers Single-use barriers and disposable items significantly reduce the need for chemical disinfectants, thus prolonging the life of the equipment. Barrier material must be impervious to moisture / fluids. Examples of protective barriers: Read all labels carefully!
• Plastic covers (available from your dealer or equipment manufacturer) • Clear plastic wrap • Plastic bags • Plastic sheets • Plastic tubing • Plastic-backed paper • Materials similar to those listed here
© Midmark Corporation 2010
Asepsis-8
Cleaning, Disinfecting & Maintenance (continued) Barriers
General Purpose Cleaning
Midmark recommends the use of disposable barriers on all clinician controls that may be in contact with clinician hands and fingers during dental procedures. The use of barriers significantly reduces the need for chemical cleaners, thus prolonging the life of the equipment.
Use cleaners and disinfectants that are appropriate for the situation, such as warm water and mild detergents, or a 10% solution of bleach with water.
Only use barrier material that is intended for use with dental equipment. Midmark recommends the use of an FDA market-cleared barrier such as Pinnacle Cover-all™. Follow barrier manufacturer instructions for proper use of these products.
Visual Inspection
Cleaning and Disinfecting
After cleaning, visually inspect the product for deterioration of covers and touch pads. Do not use the delivery system if excessive discoloration, cracking, or other signs of wear are noticeable (see Calling for Service instructions).
Cleaning and Disinfecting Assistance
In addition to the use of barriers Midmark recommends the use of an EPA registered and FDA market-cleared cleaner/disinfectant such as Cavicide™ to be used on all clinician controls or surfaces that may come in contact with dental instruments during dental procedures. Follow cleaner/disinfectant manufacturer instructions for proper use of the product. Care should be taken to avoid excessive application and pooling of liquids.
For assistance with cleaning and disinfecting instructions contact the Midmark Technical Service Department at 1-800-Midmark, it is helpful to provide the delivery system model number and serial number when asking for assistance. Additional information is available from the organizations listed below:
Handpiece Accessories
• Organization for Safety & Asepsis Procedures http://www.osap.org
Only use dental handpiece accessories with the delivery system that are FDA market-cleared and refer to manufacturer’s instructions for proper cleaning and disinfecting. Either an autoclavable syringe tip or a single use disposable syringe tip may be used.
• American Dental Association: http://www.ada.org
• European Dental Association: http://www.eda-eu.org
Equipment Alert
AUTOCLAVABLE SYRINGE TIP STERILIZATION The autoclavable syringe tips supplied with the delivery system must be sterilized prior to use with each patient, including initial use. Be sure to thoroughly rinse and clean syringe tips prior to sterilization, any debris may reduce the effectiveness of the sterilization. Recommended sterilization process is steam autoclave. Recommended parameters are 125°C (250°F) and 106 kPa (15 PSI) for 40 minutes at temperature and pressure.
© Midmark Corporation 2010
• Dept. of Health & Human Resources Centers for Disease Control & Prevention (CDC): http://www.cdc.gov
Asepsis-9
Cleaning the Delivery System
At the beginning of each day...
Fill the Self contained water bottle with fresh water and perform a Purging Procedure. Note: See Purging Procedure described in this manual.
DA101201i
Note:
Water must be safe for drinking. Distilled water is not required.
For each new patient...
Replace disposable tips, instruments, etc. and perform a Purging Procedure. Note: See Purging Procedure described in this manual.
DA2536i
© Midmark Corporation 2010
Asepsis-10
Cleaning the Delivery System - At the end of each day... Equipment Alert
B) Mix approximately 10% bleach (use only 5.25% bleach solution) with 90% water.
A) Remove disposable tips, instruments, etc.
Use only 5.25% bleach solution. Do not use bleach with scents, color guards, or other additives. Mix fresh every day.
Note: Use fill marks on the newer Midmark water bottles for quick measures..
DA2536i
C) Perform a purging procedure. Leave the bleach mixture in the system for 10 - 20 minutes, then remove. Empty and rinse the water bottle Note: See Purging Procedure described in this manual.
~90% ~10%
D) Fill the water bottle with fresh water and perform a purging procedure. Repeat as many times as needed, until all the bleach odor is gone.
Equipment Alert
Do not leave bleach mixture in system longer than 30 minutes. Doing so may damage the delivery system .
E) Turn Master Switch OFF. Press and hold the foot control pedal until all pressure is released.
DA2538i © Midmark Corporation 2010
Asepsis-11
Purging Procedure for the Delivery NOTE:
The purging procedure removes debris from the tubing to the handpieces and syringe. Performing this procedure frequently may help reduce the accumulation of biofilm on your instruments.
To begin the purging procedure...
Flush the tubing to the handpieces ...
A) Turn Master Switch ON. B) Turn Water Selector Switch to bottle setting C) Move the foot control switch to the water setting. D) Disconnect handpiece from tubing.
A) Press and hold the foot control pedal for 30 seconds. B) Press and hold the flush button for 30 seconds. C) Repeat for all tubing to the handpieces.
Master Switch
SLIDE
ON Position
Water Selector Switch Water
Foot Control Switch
Flush the Syringe Tubing... Caution
Hold the tubing and syringe over a container or drain while flushing.
A) Press and hold both syringe buttons (air and water) for 30 seconds.
DA255901i © Midmark Corporation 2010
Asepsis-12
Air/Oil Separator - Cleaning and Maintaining Periodically check the fluid level in the air / oil separator container. When the container is approximately 2/3 full, clean the air/oil separator as shown below.
To clean the air/oil separator...
A) Turn master ON/Off switch Off. B) Remove (unscrew) air/oil separator container. C) Dispose of the fluid and saturated gauze. D) Disinfect container and mounting cap. E) Install clean gauze and reinstall the container.
© Midmark Corporation 2010
Asepsis-13
Maintaining and Replacing the Regulator Filters Step 1:
Shut off manual valves to turn off water and air supplies to the operatory.
Manual Shut Off Valves
40
20
60
3
2
4 5
0
80
0
1
6 7
100
40
20
2
60
3 4
5 0
80
0
1
6 7 100
Step 3:
Unscrew retainer nut and remove filter.
Retainer Nut
Filter
Unscrew filter cap.
Note: Use 9/16” wrench.
Step 5: KA947500
© Midmark Corporation 2010
Install new filter. Secure with retainer nut.
Note: Install the filter & retainer nut with the ridged side up (as shown).
Filter Cap
Step 2:
Step 4:
Asepsis-14
Reinstall filter cap.
Assistant’s Units - Cleaning
Note:
Every dental practice is different, and no single disinfectant is the best choice for every facility. See the list of organizations that may assist you in choosing the best disinfectants available for your practice, in the front of this manual.
To clean the facility vacuum system...
Refer to the instructions provided by the vacuum system’s manufacturer.
To clean the solids collector... A) Turn facility vacuum OFF. B) Remove lid and basket. C) Clean basket and housing. D) Reinstall basket and lid.
Caution
Always dispose of biohazardous debris according to local regulations.
DA178800i
© Midmark Corporation 2010
Asepsis-15
Dimensions / Range of Motion Chair Mounted Units
Maximum load on Flex Arm mounted units is 7 lbs (3.2 KG)
18.12"
14.3"
Asepsis 21 Delivery Head KA940100
CONCEPT LR UNIT
© Midmark Corporation 2010
Asepsis-16
CHAIR MOUNTED CONSOLE UNIT
KA940200
Dimensions / Range of Motion - continued Cabinet Mounted Units
Doctor’s / Hygienist’s Carts
16.50"
18.15"
18.86"
28.25" TO 36.75"
13.00"
© Midmark Corporation 2010
Asepsis-17
AF1119
Dimensions / Range of Motion - continued Assistant’s Cart
© Midmark Corporation 2010
Left / Right Duo Cart
Asepsis-18
Warranty Information SCOPE OF WARRANTY
5.
Midmark Corporation (“Midmark”) warrants to the original purchaser its Dental products and components (except for componentsnot warranted under “Exclusions”) manufactured by Midmark to be free from defects in material and workmanship under normaluse and service. Midmark’s obligation under this warranty is limited to the repair or replacement, at Midmark’s option, of the parts or the products the defects of which are reported to Midmark within the applicable warranty period and which, upon examination by Midmark prove to be defective.
INTEGRA™ DENTAL CASEWORK AND ARTIZAN™ DENTAL FURNITURE PRODUCTS are warranted against defect in material and workmanship for the period indicated below from the time of delivery: (a) Five (5) years for all products and components (except for the shorter periods in (b and c), including plastic laminate top surfaces, door and drawer fronts, casters, and electrical components such as task lights and cords. (b) Three (3) years for task light ballast. (c) One year (1) for plastic laminate, solid surface countertops and accessories.
APPLICABLE WARRANTY PERIOD
EXCLUSIONS
The applicable warranty period, measured from the date of delivery to the original user, shall be as follows:
This warranty does not cover and Midmark shall not be liable for the following;
1.
DENTAL PRODUCTS are warranted against defect in material and workmanship for the period indicated below from the time of delivery: (a) Two (2) years for all products and components (except for the periods in b thru e). (b) “KINK-VALVE” module carries a ten (10) year warranty. (c) The original light bulb on a new light carries a one (1) year warranty. (d) Accessories not manufactured by Midmark are excluded. (e) Replacement parts and accessories carry a ninety (90) day warranty.
EXCLUSIVE REMEDY
2.
Oral Surgery PRODUCTS are warranted against defect in material and workmanship for a period of one (1) year from the time of delivery.
3.
STERILIZERS PRODUCTS are warranted against defect in material and workmanship for a period of one (1) year from the time of delivery.
4.
ULTRASONIC CLEANER PRODUCTS when used in accordance with manufacturer’s instructions and under normal use, are guaranteed for two (2) years after date of shipment. Within the period guaranteed, the manufacturer will repair or replace free of charge, at its sole discretion, all parts that are defective because of material or workmanship including costs for removing or installing parts. Repairs are made on a FOB repair depot basis. Manufacturer’s liability, whether based on warranty, negligence or other cause, arising out of and/or incidental to sale, use or operation of the transducer elements, or any part thereof, shall not in any case exceed the cost of repair or replacement of the defective equipment, and such repair or replacement shall be the exclusive remedy of the purchaser, and in no case shall manufacturer be responsible for any and/or all consequential or incidental damages including without limitation, and/or all consequential damages arising out of commercial losses.
© Midmark Corporation 2010
(1) repairs and replacements because of misuse, abuse, negligence, alteration, accident, freight damage, or tampering; (2) matching of color, grain, or texture except to commercially acceptable standards; (3) changes in color caused by natural or artificial light; (4) products which are not installed, used, and properly cleaned as required in the Midmark “Installation” and or “Installation/Operation” Manual for this applicable product; (5) products considered to be of a consumable nature; (6) accessories or parts not manufactured by Midmark; (7) specially manufactured products; (8) charges by anyone for adjustments, repairs, replacement parts installation, or other work performed upon or in connection with such products which is not expressly authorized in writing in advance by Midmark.
Midmark’s only obligation under this warranty is the repair or replacement of defective parts. Midmark shall not be liable for any direct, special indirect, incidental, exemplary or consequential damages or delay including, but not limited to, damages for loss of profits or loss of use. NO AUTHORIZATION No person or firm is authorized to create for Midmark any other obligation or liability in connection with the products.
THIS WARRANTY IS MIDMARK’S ONLY WARRANTY AND IS IN LIEU OF ALL OTHER WARRANTIES, EXPRESSED OR IMPLIED. MIDMARK MAKES NO IMPLIED WARRANTIES OF ANY KIND INCLUDING ANY WARRANTIES OF MERCHANTABILITY OR FITNESS FOR ANY PARTICULAR PURPOSE. THIS WARRANTY IS LIMITED TO THE REPAIR OR REPLACEMENT OF DEFECTIVE PARTS.
Asepsis-19