User Manual
140 Pages
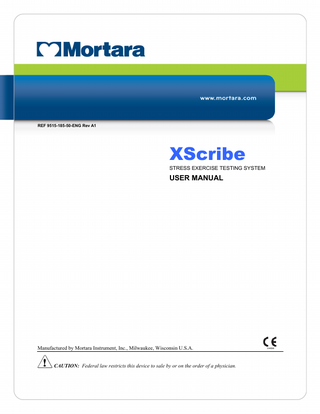
Preview
Page 1
REF 9515-185-50-ENG Rev A1
XScribe STRESS EXERCISE TESTING SYSTEM
USER MANUAL
Manufactured by Mortara Instrument, Inc., Milwaukee, Wisconsin U.S.A. CAUTION: Federal law restricts this device to sale by or on the order of a physician.
Copyright © 2013 by Mortara Instrument, Inc. 7865 N. 86th Street Milwaukee, Wisconsin 53224
This document contains confidential information that belongs to Mortara Instrument, Inc. No part of this document may be transmitted, reproduced, used, or disclosed outside of the receiving organization without the express written consent of Mortara Instrument, Inc. Mortara is a registered trademark of Mortara Instrument, Inc. AM12, RScribe, VERITAS, X12+, and XScribe are trademarks of Mortara Instrument, Inc. “SCF” (Source Consistency Filter) is a copyright of Mortara Instrument, Inc. Adobe and Acrobat are registered trademarks of Adobe Systems Inc. Microsoft and Windows are registered trademarks of Microsoft Corporation. DICOM is the registered trademark of the National Electrical Manufacturers Association for its standards publications relating to digital communications of medical information. v5.10.
TECHNICAL SUPPORT AND SERVICE
Headquarters Mortara Instrument, Inc. 7865 North 86th Street Milwaukee, WI 53224 U.S.A. Tel: 414.354.1600 Tel: 800.231.7437 Fax: 414.354.4760 Internet: http://www.mortara.com
European Union Representative Mortara Rangoni Europe, Srl (European Headquarters) Via Cimarosa 103/105 40033 Casalecchio di Reno (BO) Italia Tel: +39.051.298.7811 Fax: +39.051.613.3582
Service/Technical Support Group Mortara Instrument, Inc. 7865 North 86th Street Milwaukee, WI 53224 U.S.A. Tel: 414.354.1600 Service: 888.MORTARA (888.667.8272) Fax: 414.354.4760 E-mail: [email protected] 24-Hour Technical Support Same-Day Shipment of Replacement Parts Biomedical Training Classes Extended Warranties/Service Contracts
Sales Support/ Supplies & Accessories Mortara Instrument, Inc. 7865 North 86th Street Milwaukee, WI 53224 U.S.A. Tel: 414.354.1600 Fax: 414.354.4760 E-mail: [email protected] Mortara Instrument Germany Bonifaciusring 15 45309 Essen Germany Tel: +49.201.18 55 69 70 Fax: +49.201.18 55 69 77 Mortara Instrument Netherlands Postbus 324 5680 AH Best Industrieweg 160b 5683 CG Best Netherlands Tel: +31.499.377310 Fax: +31.499.377908 Mortara Instrument Australia PO Box 7568 Baulkham Hills NSW 2153 Unit 28, 9 Hoyle Avenue Castle Hill NSW 2154 Australia Tel: +61 2 8070 9303 Fax: +61 2 9899 9478 Mortara Dolby UK Ltd. Units 11 & 12, Scion House Stirling University Innovation Park Stirling FK9 4NF Scotland Tel: +44.1786.444980 Fax: +44.1786.446630
i
NOTICES Manufacturer’s Responsibility Mortara Instrument, Inc. is responsible for the effects on safety and performance only if: •
Assembly operations, extensions, readjustments, modifications, or repairs are carried out by persons authorized by Mortara Instrument, Inc.
•
The device is used in accordance with the instructions for use.
•
The electrical installation of the relevant room complies with the requirements of appropriate regulations.
Responsibility of the Customer The user of this device is responsible for ensuring the implementation of a satisfactory maintenance schedule. Failure to do so may cause undue failure and possible health hazards. Equipment Identification Mortara Instrument, Inc. equipment is identified by a serial and reference number on the back of the device. Care should be taken so that these numbers are not defaced. Copyright and Trademark Notices This document contains information that is protected by copyright. All rights are reserved. No part of this document may be photocopied, reproduced, or translated to another language without prior written consent of Mortara Instrument, Inc. Other Important Information The information in this document is subject to change without notice. Mortara Instrument, Inc. makes no warranty of any kind with regard to this material including, but not limited to, implied warranties of merchantability and fitness for a particular purpose. Mortara Instrument, Inc. assumes no responsibility for any errors or omissions that may appear in this document. Mortara Instrument, Inc. makes no commitment to update or to keep current the information contained in this document.
ii
WARRANTY INFORMATION Your Mortara Warranty MORTARA INSTRUMENT, INC. (hereinafter referred to as “Mortara”) hereby warrants that Mortara products (hereinafter referred to as “Product/s”) shall be free from defects in material and workmanship under normal use, service, and maintenance for the warranty period of such Product/s from Mortara or an authorized distributor or representative of Mortara. The warranty period is defined as twelve (12) months following the date of shipment from Mortara. Normal use, service, and maintenance means operation and maintenance in accordance with appropriate instructions and/or information guides. This warranty does not apply to damage to the Product/s caused by any or all of the following circumstances or conditions: a)
Freight damage;
b) Parts and/or accessories of the Product/s not obtained from or approved by Mortara; c)
Misapplication, misuse, abuse, and/or failure to follow the Product/s instruction sheets and/or information guides;
d) Accident; a disaster affecting the Product/s; e)
Alterations and/or modifications to the Product/s not authorized by Mortara;
f)
Other events outside of Mortara’s reasonable control or not arising under normal operating conditions.
THE REMEDY UNDER THIS WARRANTY IS LIMITED TO THE REPAIR OR REPLACEMENT WITHOUT CHARGE FOR LABOR OR MATERIALS, OR ANY PRODUCT/S FOUND UPON EXAMINATION BY MORTARA TO HAVE BEEN DEFECTIVE. This remedy shall be conditioned upon receipt of notice by Mortara of any alleged defects promptly after discovery thereof within the warranty period. Mortara’s obligations under the foregoing warranty will further be conditioned upon the assumption by the purchaser of the Product/s (i) of all carrier charges with respect to any Product/s returned to Mortara’s principal place or any other place as specifically designated by Mortara or an authorized distributor or representative of Mortara, and (ii) all risk of loss in transit. It is expressly agreed that the liability of Mortara is limited and that Mortara does not function as an insurer. A purchaser of a Product/s, by its acceptance and purchase thereof, acknowledges and agrees that Mortara is not liable for loss, harm, or damage due directly or indirectly to an occurrence or consequence therefrom relating to the Product/s. If Mortara should be found liable to anyone under any theory (except the expressed warranty set forth herein) for loss, harm, or damage, the liability of Mortara shall be limited to the lesser of the actual loss, harm, or damage, or the original purchase price of the Product/s when sold. EXCLUDED FROM THE LIMITED WARRANTY SET FORTH ABOVE ARE CONSUMABLE ITEMS SUCH AS PAPER, BATTERIES, BLOOD PRESSURE CUFFS, BLOOD PRESSURE HOSES, ELECTRODES, PATIENT CABLES, LEAD WIRES, CARRY CASES, AND MAGNETIC STORAGE MEDIUMS. EXCEPT AS SET FORTH HEREIN WITH RESPECT TO REIMBURSEMENT OF LABOR CHARGES, A PURCHASER’S SOLE EXCLUSIVE REMEDY AGAINST MORTARA FOR CLAIMS RELATING TO THE PRODUCT/S FOR ANY AND ALL LOSSES AND DAMAGES RESULTING FROM ANY CAUSE SHALL BE THE REPAIR OR REPLACEMENT OF DEFECTIVE PRODUCT/S TO THE EXTENT THAT THE DEFECT IS NOTICED AND MORTARA IS NOTIFIED WITHIN THE WARRANTY PERIOD. IN NO EVENT, INCLUDING THE CLAIM FOR NEGLIGENCE, SHALL MORTARA BE LIABLE FOR INCIDENTAL, SPECIAL, OR CONSEQUENTIAL DAMAGES, OR FOR ANY OTHER LOSS, DAMAGE, OR EXPENSE OF ANY KIND, INCLUDING LOSS OF PROFITS, WHETHER UNDER TORT, NEGLIGENCE OR STRICT LIABILITY THEORIES OF LAW, OR OTHERWISE. THIS WARRANTY IS EXPRESSLY IN LIEU OF ANY OTHER WARRANTIES, EXPRESS OR IMPLIED, INCLUDING, BUT NOT LIMITED TO THE IMPLIED WARRANTY OF MERCHANTABILITY AND THE WARRANTY OF FITNESS FOR A PARTICULAR PURPOSE.
iii
USER SAFETY INFORMATION
Warning:
Means there is the possibility of personal injury to you or others.
Caution:
Means there is the possibility of damage to the device.
Note:
Provides information to further assist in the use of the device.
Warning(s) •
This manual gives important information about the use and safety of this device. Deviating from operating procedures, misuse or misapplication of the device, or ignoring specifications and recommendations could result in increased risk of harm to users, patients and bystanders, or damage to the device.
•
The various manufacturers of accessories provide separate user manuals and/or instructions (e.g., monitor, laser printer, X12+, AM12, patient cables, electrodes). Read these instructions well and refer to them for specific functions. It is recommended to keep all instructions together. Refer to these instructions for a list of approved accessories. When in doubt, contact Mortara Instrument.
•
Device (stress test system) captures and presents data reflecting a patient’s physiological condition that when reviewed by a trained physician or clinician can be useful in determining a diagnosis; however, the data should not be used as a sole means for determining a patient’s diagnosis.
•
Users are expected to be licensed clinical professionals knowledgeable about medical procedures and patient care, and adequately trained in the use of this device. Before attempting to use this device for clinical applications, the operator must read and understand the contents of the user manual and other accompanying documents. Inadequate knowledge or training could result in increased risk of harm to users, patients and bystanders, or damage to the device. Contact Mortara service for additional training options.
•
To ensure that electrical safety is maintained during operation from AC (~) power, the device must be plugged into a hospital-grade outlet.
•
The device is supplied with a power isolation transformer that must be used to maintain designed operator and patient isolation from power source. The power isolation transformer must be plugged into a hospitalgrade outlet.
•
To maintain designed operator and patient safety, peripheral equipment and accessories used that can come in direct patient contact must be in compliance with UL 2601-1, IEC 60601-1, and IEC 60601-2-25. Only use parts and accessories supplied with the device and available through Mortara Instrument, Inc.
•
All signal input and output (I/O) connectors are intended for connection of only those devices complying with IEC 60601-1, or other IEC standards (e.g., IEC 60950), as appropriate to the device. Connecting additional devices to the device may increase chassis and/or patient leakage currents. To maintain operator and patient safety, consideration should be given to the requirements of IEC 60601-1-1, and leakage currents should be measured to confirm no electric shock hazard exists.
•
Patient cables intended for use with the device include series resistance (9 Kohm minimum) in each lead for defibrillation protection. Patient cables should be checked for cracks or breakage prior to use.
v
USER SAFETY INFORMATION
•
Conductive parts of the patient cable, electrodes, and associated connections of Type CF applied parts, including the neutral conductor of the patient cable and electrode should not come into contact with other conductive parts, including earth ground.
•
The personal computer and all peripheral equipment used should be approved to the appropriate safety standard for nonmedical electrical equipment per IEC 60950, or its national variants.
•
If there is a requirement for the personal computer or any peripheral equipment connected to it, including exercise equipment like an ergometer or treadmill to be situated within the patient environment it is the responsibility of the user to ensure the system provides a level of safety that ensures compliance with IEC 60601-1. Non-medical equipment should be powered through a medical grade isolation transformer of sufficient capacity, and a connection to a data network should be made through a medical grade separation device.
•
To avoid the possibility of serious injury or death during patient defibrillation, do not come into contact with device or patient cables. Additionally, proper placement of defibrillator paddles in relation to the electrodes is required to minimize harm to the patient.
•
This device was designed to use the electrodes specified in this manual. Proper clinical procedure must be employed to prep the electrode sites and to monitor the patient for excessive skin irritation, inflammation, or other adverse reactions. Electrodes are intended for short term use and should be removed from the patient promptly following testing.
•
To avoid potential for spread of disease or infection, single-use disposable components (e.g., electrodes) must not be reused. To maintain safety and effectiveness, electrodes must not be used beyond their expiration date.
•
A possible explosion hazard exists. Do not use the device in the presence of a flammable anesthetic mixture.
•
The device has not been designed for use with high-frequency (HF) surgical equipment and does not provide a protective means against hazards to the patient.
•
To maintain designed operator and patient safety when the optional network connection is being used, the network cable must be connected to the device through the Ethernet isolator module provided.
•
To maintain designed operator and patient safety, the M12xxx-USB module, TTL-trigger USB module, and conductive portions of connected antennas and cables must be positioned such that they are inaccessible during normal operation.
•
An additional Multiple Plug Socket Outlet (MPSO) or extension cord shall not be connected to the system.
•
Do not connect any items which are not specified as part of the system.
•
To avoid risk of improper electrical isolation the Tango SpO2 probe must only be connected to the proper SpO2 extension patient cable or port on the SunTech Tango blood pressure monitor.
•
The quality of the signal produced by the thermal writer may be adversely affected by the use of other medical equipment, including but not limited to defibrillators and ultrasound machines.
vi
USER SAFETY INFORMATION
Caution(s) •
Do not use the device as a method for loading or operating commercially available software. Doing so might affect the performance of the device.
•
Do not attempt to clean the device or patient cables by submersing into a liquid, autoclaving, or steam cleaning as this may damage equipment or reduce its usable life. Wipe the exterior surfaces with a warm water and mild detergent solution and then dry with a clean cloth. Use of unspecified cleaning/disinfecting agents, failure to follow recommended procedures, or contact with unspecified materials could result in increased risk of harm to users, patients and bystanders, or damage to the device.
•
No user-serviceable parts inside. Screw removal by qualified service personnel only. Damaged or suspected inoperative equipment must be immediately removed from use and must be checked/repaired by qualified service personnel prior to continued use.
•
Do not pull or stretch patient cables as this could result in mechanical and/or electrical failures. Patient cables should be stored after forming them into a loose loop.
•
Windows compatibility, updates and anti-virus policy: The XScribe software has been fully tested with Windows 7 Professional Service Pack 1. The Modality Manager software has also been tested with Windows Server 2008 R2 Service Pack 1. Although it is unlikely that Windows updates and security patches affect XScribe functionality, Mortara recommends turning automatic Windows update off, and periodically running it manually. A functional test should be executed after update, which includes conducting an exam, as well as importing an order and exporting results, if activated. Compatibility of XScribe with major corporate anti-virus software packages has been verified. Mortara recommends excluding the XScribe database folder (normally C:ProgramDataMiPgSqlData on a stand-alone system or the server) from the folders to be scanned. In addition, anti-virus patch updates and system scans should be scheduled for time periods when the system is not actively in use or performed manually.
Note(s) •
Patient movements may generate excessive noise that may affect the quality of the ECG traces and the proper analysis performed by the device.
•
Proper patient preparation is important to proper application of ECG electrodes and operation of the device.
•
There is no known safety hazard if other equipment, such as pacemakers or other stimulators, is used simultaneously with the device; however, disturbance to the signal may occur.
•
If electrode is not properly connected to the patient, or one or more of the patient cable lead wires is damaged, display will indicate a lead fault for the lead(s) where the condition is present.
vii
USER SAFETY INFORMATION
•
As defined by IEC 60601-1 the device is classified as follows: - Class I equipment - Type CF, defibrillation-proof applied parts (ECG inputs) - Tango BP monitor type BF, defibrillation-proof applied parts - Ordinary equipment - Equipment not suitable for use in the presence of a flammable anesthetic mixture - Continuous operation NOTE: From a safety perspective, per IEC 60601-1 and derivative standards/norms, this unit is declared to be “Class I” and uses a three-prong inlet to ensure an earth connection is made along with mains.
•
To prevent possible damage to the device during transport and storage (while in original packaging) the following environmental conditions must be adhered to: Ambient temperature: Relative humidity: Atmospheric pressure:
•
-20° C to 65° C (-4° F to 149° F) 10% to 95%, non-condensing 500 hPa to 1060 hPa
Allow the device to stabilize within its intended operating environment for a minimum of two hours prior to use. Refer to the computer and peripheral equipment user manuals for allowable environmental conditions. The allowable environmental conditions for the X12+ and AM12 acquisition module are as follows: Ambient temperature: Relative humidity: Atmospheric pressure:
10° C to 40° C (50° F to 104° F) 10% to 95%, non-condensing 500 hPa to 1060 hPa
•
When necessary, dispose of the device, its components and accessories (e.g., batteries, cables, electrodes), and/or packing materials in accordance with local regulations.
•
In the event of a square wave presentation on the display while using the AM12, this may be due to an improper auto-calibration. Disconnect and then reconnect the AM12 cable from the USB port, or power cycle the XScribe system to re-calibrate.
•
Proper functioning backup items such as a spare patient cable, front-end device, display monitor, and other equipment are recommended on hand to prevent delayed treatment due to an inoperable device.
viii
EQUIPMENT SYMBOLS Symbol Delineation Attention, consult accompanying documents
Alternating current
Protective earth Fuse
Defibrillator-proof type CF applied part
Input
Green light illuminates when power is ON
Green light illuminates when paper is out or an error condition is detected Advances paper to the next paper perforation and will reset a paper error condition. When depressed for approximately 7 seconds, will reset the device Do not dispose as unsorted municipal waste. Per European Union Directive 2002/96, requires separate handling for waste disposal according to national requirements Indicates compliance to applicable European Union directives
NOTE: Refer to the manual(s) accompanying the device that pertain to the computer hardware for additional definitions of symbols that may be present.
ix
EQUIPMENT SYMBOLS
x
GENERAL CARE Precautions • • •
Turn off the device before inspecting or cleaning. Do not immerse the device in water. Do not use organic solvents, ammonia based solutions, or abrasive cleaning agents which may damage equipment surfaces.
Inspection Inspect your equipment daily prior to operation. If you notice anything that requires repair, contact an authorized service person to make the repairs. • • • •
Verify that all cords and connectors are securely seated. Check the case and chassis for any visible damage. Inspect cords and connectors for any visible damage. Inspect keys and controls for proper function and appearance.
Cleaning Exterior Surfaces and Patient Cables 1. 2. 3.
4. 5. 6.
Remove cables and lead wires from device before cleaning. For general cleaning of cables and lead wires use a soft, lint-free cloth lightly moistened with a mild soap and water solution. Wipe and air dry. For disinfecting the cables and lead wires, wipe exterior with a soft, lint-free cloth using a solution of Sodium Hypochlorite (10% household bleach and water solution): minimum 1:500 dilution (minimum 100 ppm free chlorine) and maximum 1:10 dilution as recommended by the APIC Guidelines for Selection and Use of Disinfectants. Use caution with excess liquid as contact with metal parts may cause corrosion. Do not immerse cable ends or lead wires; immersion can cause metal corrosion. Do not use excessive drying techniques such as forced heat.
WARNING: Do not attempt to clean/disinfect the device or patient cables by submerging into a liquid, autoclaving, or steam cleaning. Never expose cables to strong ultra-violet radiation.
Cleaning the Device Disconnect the power source. Clean the exterior surface of the device with a damp, soft, lint-free cloth using a solution of mild detergent diluted in water. After washing, thoroughly dry off the device with a clean, soft cloth or paper towel. The device carry case can be surface cleaned with a damp cloth or a disinfectant wipe or spray. The carry case may also be machine or hand washed with detergent and air dried. Do not machine dry the carry case. Cosmetic changes may occur during washing. Inspect carry cases for structural damage after each washing cycle and replace when necessary.
xi
GENERAL CARE
Sterilization EtO sterilization is not recommended but may be required for cables and lead wires. Frequent sterilization will reduce the useful life of cables and lead wires. If required, sterilize with ethylene oxide gas (EtO) at a maximum temperature of 50° C/122° F. After EtO sterilization, follow the recommendations from the sterilizer manufacturer for required aeration.
Cautions Improper cleaning products and processes can damage the device, produce brittle lead wires and cables, corrode the metal, and void the warranty. Use care and proper procedure whenever cleaning or maintaining the device.
xii
ELECTROMAGNETIC COMPATIBILITY (EMC) Electromagnetic compatibility with surrounding devices should be assessed when using the device. An electronic device can either generate or receive electromagnetic interference. Testing for electromagnetic compatibility (EMC) has been performed on the device according to the international standard for EMC for medical devices (IEC 60601-1-2). This IEC standard has been adopted in Europe as the European Norm (EN 60601-1-2). The system should not be used adjacent to, or stacked on top of other equipment. If the device must be used adjacent to or stacked on top of other equipment, verify that the device (and optional thermal writer) operates in an acceptable manner in the configuration in which it will be used. Fixed, portable, and mobile radio frequency communications equipment can affect the performance of medical equipment. See Table X-4 for recommended separation distances between the radio equipment and the device. The use of accessories, transducers and cables other than those specified by Mortara Instrument may result in increased emissions or decreased immunity of the system.
xiii
ELECTROMAGNETIC COMPATIBILITY (EMC)
Table X-1 Guidance and Manufacturer’s Declaration: Electromagnetic Emissions The equipment is intended for use in the electromagnetic environment specified in the table below. The customer or the user of the equipment should ensure that it is used in such an environment. Emissions Test
Compliance
Electromagnetic Environment: Guidance
RF Emissions CISPR 11
Group 1
The equipment uses RF energy only for its internal function. Therefore, its RF emissions are very low and not likely to cause any interference in nearby electronic equipment.
RF Emissions CISPR 11
Class A
Harmonic Emissions IEC 61000-3-2
Complies
Voltage Fluctuations/ Flicker Emissions IEC 61000-3-3
Complies
The equipment is suitable for use in all establishments other than domestic and those directly connected to the public lowvoltage power supply network that supplies buildings used for domestic purposes.
Table X-2 Guidance and Manufacturer’s Declaration: Electromagnetic Immunity The equipment is intended for use in the electromagnetic environment specified in the table below. The customer or the user of the equipment should ensure that it is used in such an environment. Emissions Test
Compliance
Compliance Level
Electromagnetic Environment: Guidance
Electrostatic discharge (ESD) IEC 61000-4-2
+/- 6 kV contact +/- 8 kV air
+/- 6 kV contact +/- 8 kV air
Floors should be wood, concrete, or ceramic tile. If floors are covered with synthetic material, the relative humidity should be at least 30%.
Electrical fast transient/burst IEC 61000-4-4
+/- 2 kV for power supply lines +/- 1 kV for input/output lines
+/- 2 kV for power supply lines +/- 1 kV for input/output lines
Mains power quality should be that of a typical commercial or hospital environment.
Surge IEC 61000-4-5
+/- 1 kV differential mode +/- 2 kV common mode
+/- 1 kV differential mode +/- 2 kV common mode
Mains power quality should be that of a typical commercial or hospital environment.
Voltage dips, short interruptions, and voltage variations on power supply input lines IEC 61000-4-11
<5% UT (>95% dip in UT) for 0.5 cycle 40% UT (60% dip in UT) for 5 cycles
<5% UT (>95% dip in UT) for 0.5 cycle 40% UT (60% dip in UT) for 5 cycles
Mains power quality should be that of a typical commercial or hospital environment. If the user of the equipment requires continued operation during power mains interruptions, it is recommended that the equipment be powered from an uninterruptible power supply or a battery
Power frequency (50/60 Hz) magnetic field
3 A/m
3 A/m
Power frequency magnetic fields should be at levels characteristic of a typical location in a typical commercial or hospital environment.
NOTE: UT is the AC Mains voltage prior to application of the test level.
xiv
ELECTROMAGNETIC COMPATIBILITY (EMC)
Table X-3 Guidance and Manufacturer’s Declaration: Electromagnetic Immunity The equipment is intended for use in the electromagnetic environment specified in the table below. The customer or the user of the equipment should ensure that it is used in such an environment. Emissions Test
IEC 60601 Test Level
Compliance Level
Electromagnetic Environment: Guidance Portable and mobile RF communications equipment should be used no closer to any part of the equipment, including cables, than the recommended separation distance calculated from the equation applicable to the frequency of the transmitter. Recommended separation distance
Conducted RF IEC 61000-4-6
3 Vrms 150 kHz to 80 MHz
3 Vrms 150 kHz to 80 MHz
Radiated RF IEC 61000-4-3
3 V/m 80 MHz to 2.5 GHz
3 V/m 80 MHz to 2.5 GHz
⎡ 3 .5 ⎤ d=⎢ ⎥ P ⎣ 3Vrms ⎦
⎡ 3. 5 ⎤ d=⎢ ⎥ P ⎣ 3V / m ⎦
80 MHz to 800 MHz
⎡ 7 ⎤ d=⎢ ⎥ P ⎣ 3V / m ⎦
800 MHz to 2.5 GHz
Where P is the maximum output power rating of the transmitter in watts (W) according to the transmitter manufacturer and d is the recommended separation distance in meters (m). Field strengths from fixed RF transmitters, as determined by an electromagnetic site surveya, should be less than the compliance level in each frequency rangeb. Interference may occur in the vicinity of equipment marked with the following symbol:
a. Field strengths from fixed transmitters, such as base stations for radio (cellular/cordless) telephones and land mobile radios, amateur radios, AM and FM radio broadcast, and TV broadcast cannot be predicted theoretically with accuracy. To assess the electromagnetic environment due to fixed RF transmitters, an electromagnetic site survey should be considered. If the measured field strength in the location in which the equipment is used exceeds the applicable RF compliance level above, the equipment should be observed to verify normal operation. If abnormal performance is observed, additional measures may be necessary, such as reorienting or relocating the equipment. b. Over the frequency range 150 kHz to 80 MHz, field strengths should be less than [3] V/m.
xv
ELECTROMAGNETIC COMPATIBILITY (EMC)
Table X-4 Recommended Separation Distances Between Portable and Mobile RF Communications Equipment and the Equipment The equipment is intended for use in the electromagnetic environment in which radiated RF disturbances are controlled. The customer or the user of the equipment can help to prevent electromagnetic interference by maintaining a minimum distance between portable and mobile RF communications equipment (transmitters) and the equipment as recommended in the table below, according to the maximum output power of the communications equipment. Rated Maximum Output Power of Transmitter W
Separation Distance According to Frequency of Transmitter (m)
150 KHz to 800 MHz
800 MHz to 2.5 GHz
d = 1 .2 P
d = 2 .3 P
0.01
0.1 m
0.2 m
0.1
0.4 m
0.7 m
1
1.2 m
2.3 m
10
4.0 m
7.0 m
100
12.0 m
23.0 m
For transmitters rated at a maximum output power not listed above, the recommended separation distance d in meters (m) can be estimated using the equation applicable to the frequency of the transmitter, where P is the maximum output power rating of the transmitter in watts (W) according to the transmitter manufacturer. NOTE 1: At 800 MHz, the separation distance for the higher frequency range applies. NOTE 2: These guidelines may not apply in all situations. Electromagnetic propagation is affected by the absorption and reflection from structures, objects, and people.
xvi
TABLE OF CONTENTS INTRODUCTION SECTION 1 Manual Purpose ... 1 Audience ... 1 Intended Use ... 1 Indications for Use ... 1 System Description ... 2 Miscellaneous System Information ... 2 About the XScribe ... 3 XScribe System ... 4 XScribe Front End Types ... 5 XScribe Software Installation Procedure ... 6 Feature Activation ... 9 Starting the XScribe Workstation ... 10 XScribe Login and Main Display ... 10 XScribe Icon Descriptions ... 11 User Roles and Permissions ... 12 XScribe Specifications ... 13 Parts and Accessories ... 14 Support Parts ... 15
SCHEDULE/ORDERS SECTION 2 Time Filter ... 17 Group by Column Header ... 17 Schedule a New Order ... 18 Edit an Existing Order ... 20 Delete an Existing Order ... 20
SETUP AND INSTALLATION SECTION 3 XScribe System Setup and Installation... 21 XScribe Interconnect Diagram ... 22 Medical Isolation Transformer ... 23 Medical Isolation Transformer Specifications ... 23
USING THE XSCRIBE SECTION 4 Function Keys... 28 System Display ... 36
CONDUCTING A STRESS TEST SECTION 5 Patient Preparation... 41 Preparing Patient Skin ... 41 Patient Hookup ... 41 To Attach the Electrodes ... 41 Patient Hookup Summary Table ... 43
xvii
TABLE OF CONTENTS
Strain Relief and Artifact ... 44 LeadForm Patient Cable and Strain Relief ... 44 AM12 Strain Relief ... 44 Start a Stress Test ... 45 Schedule Order(s)... 45 No Scheduled Orders ... 46 Observation Phase and Local Settings... 47 Local Settings ... 47 Softkey and Using Filters ... 48 Source Consistency Filter (SCF) ... 48 AC Filter... 48 40 Hz Filter ... 48 Protocol Selection ... 49 Conducting a Stress Test ... 50 Pre-Exercise Phase ... 50 Acquiring a Resting ECG ... 50 Exercise Phase, Recovery and Recovery End ... 51 About the Recovery Phase ... 52 Final Report Phase (Report Manager with Summary Statistics) ... 52 Quick Start: System Selection to Start a Stress Test ... 53 Quick Start: System Display during the Observation Phase... 54 Quick Start: System Display during the Pre-exercise Phase ... 55 Quick Start: System Display during Exercise Phase ... 56 Quick Start: System Display during Recovery Phase ... 57 Quick Start: Report Manager Display ... 58 Using Report Manager ... 59 Patient Data ... 59 Print Report ... 59 Quick Print ... 59 Post Processing... 59 Review Exam ... 60 Page Review ... 60 Conclusions: Narrative Template ... 60 Conclusions: Acronyms ... 60 Exit ... 61 Final Report Preview ... 62 Icon Tool Bar ... 62 Sections ... 62 Exit the Preview ... 62 Open Legacy Exams ... 63
SYSTEM AND USER CONFIGURATION SECTION 6 Administrative Tasks ... 65 Manage User Accounts... 65 User’s Database ... 65 Personnel ... 65 Manage/Create Groups ... 66
xviii
TABLE OF CONTENTS
Modality Settings... 66 Profile ... 66 Real Time Display ... 66 Printout ... 67 Rhythm Events ... 67 Miscellaneous ... 67 Protocols... 68 Pre-Exercise ... 68 Exercise ... 68 Recovery ... 69 File Exchange ... 70 DICOM Settings ... 70 Unlock Exams ... 70 Manage Archive Storage ... 70 Add Archive Location ... 70 Restore Archived Exams ... 70 Audit Trail Logs ... 71 Service Logs ... 71 Configure Workflow ... 71 Workflow Config ... 72 About the Legal Signature... 72 User Preferences ... 72 Report Configuration Tool ... 73 Configuring the Final Report ... 73 RF Scan for X12+... 74
WORKLIST SECTION 7 Status Filter ... 75 Time Filter ... 75 Group By Column Header ... 75
EXAM SEARCH SECTION 8 Filters and Identifiers ... 77 Group By Column Header ... 78 Offline Exam Copies ... 78
PATIENT SEARCH SECTION 9 Filters and Identifiers ... 79 Group By Column Header ... 80 Add a New Patient ... 80 Delete a Patient ... 80 Duplicate Patient ID ... 81 Patient and Exam Reconciliation ... 81
xix