Users Manual
108 Pages
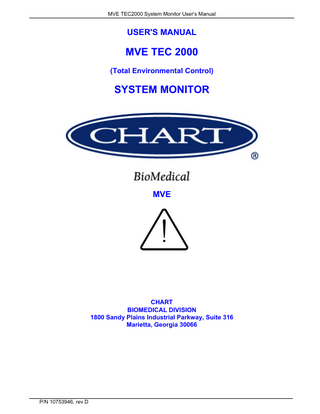
Preview
Page 1
MVE TEC2000 System Monitor User’s Manual
USER'S MANUAL
MVE TEC 2000 (Total Environmental Control)
SYSTEM MONITOR
MVE
CHART BIOMEDICAL DIVISION 1800 Sandy Plains Industrial Parkway, Suite 316 Marietta, Georgia 30066
P/N 10753946, rev D
MVE TEC2000 System Monitor User’s Manual
1. Table Of Contents 1.1 1.
Table Of Sections Table Of Contents ... 1-1
1.1 1.2 1.3 2.
Introduction ... 2-1 2.1 2.2 2.3 2.4 2.5 2.6
3.
TABLE OF SECTIONS ...1-1 TABLE OF ILLUSTRATIONS ...1-3 TABLE OF TABLES ...1-3 GENERAL ...2-1 DESCRIPTION OF CRYOGENIC STORAGE DEWARS ...2-1 MVE CRYOGENIC STORAGE SYSTEM DESCRIPTION ...2-1 HANDLING LIQUID NITROGEN ...2-2 EQUIPMENT USAGE ...2-2 SUMMARY OF TEC 2000 SYSTEM MONITOR FEATURES ...2-3
Installation ... 3-1 3.1 GENERAL ...3-1 3.2 INSPECTION AND UNPACKING ...3-1 3.3 REPACKAGING FOR SHIPMENT...3-1 3.4 DEFINITION OF REAR PANEL CONTROLS ...3-2 3.4.1 COMPUTER INTERFACE CONNECTION...3-4 3.5 HARDWARE INSTALLATION ...3-4 3.5.1 MAIN POWER CONNECTION...3-5 3.5.2 Dewar Plumbing Connections...3-5 3.5.3 “Built-In” (or “Cabinet-Style”) System Monitor Installation ...3-5 3.5.4 Stand-Alone System Monitor Hardware Installation ...3-6 3.5.5 RS-485 Interface Connections (Customer Use is Optional)...3-8 3.6 INITIAL SETUP AND SYSTEM CHECKOUT ...3-9 3.6.1 Normal Display Sequence After Successful, Start-up Self Diagnostics...3-9 3.6.2 System Fault, Alarm Displays Following Start-Up Self-Diagnostics: ...3-10 3.6.3 “Normal” (or Expected) Alarm Displays Following a Successful Self-Diagnostics: ...3-11
4.
Operation ... 4-1 4.1 GENERAL ...4-1 4.2 DEFINITION OF FRONT PANEL CONTROLS ...4-1 4.2.1 System Status Indicators...4-1 4.2.2 Two by Sixteen Liquid Crystal Display (LCD)...4-2 4.2.3 Keypad Definitions ...4-2 4.2.4 Maintenance Menu Introduction ...4-4 4.3 EXPLANATION OF LEVEL, PERCENT, AND TEMPERATURE SET-POINTS ...4-5 4.4 OPERATIONAL SETUP ...4-8 4.5 NORMAL OPERATION ...4-11 4.5.1 Maintenance Menu Functions ...4-11 4.5.2 Alarm Conditions ...4-14 4.5.3 Filling ...4-15 4.5.4 Liquid Usage Data ...4-16 4.5.5 Setting Units ...4-17 4.5.6 Locking and Unlocking the Keypad ...4-17 4.5.7 Altering the Display “Lock Code” (from Factory Default Setting) ...4-18 4.5.8 RS-485 Interface Settings for Printer Activation...4-18 4.5.9 Toggle Temperature Display...4-20 4.5.10 Settings Summary ...4-20 4.5.11 High Temperature Alarm Test Function ...4-20
Table Of Contents
1-1
XLC TEC2000 System Monitor User’s Manual Rs-485 Serial Communications Interface...5-1
5.
5.1 GENERAL ... 5-1 5.2 RS-485 INTERFACE / CONFIGURATION TO A HOST COMPUTER... 5-1 5.3 RS-232C INTERFACE COMMAND SUMMARY ... 5-2 5.4 RS-232C INTERFACE CONTROL COMMANDS... 5-3 5.5 RS-232C INTERFACE TEMPERATURE COMMANDS ... 5-6 5.6 RS-232C INTERFACE LEVEL COMMANDS... 5-9 5.7 RS-232C INTERFACE PERCENT COMMANDS... 5-13 5.8 MVE TEC 2000 DATA LOGGING CAPABILITIES ... 5-13 5.8.1 GENERAL ... 5-13 5.8.2 “EVENT LOG” DATA LOGGING FEATURE ... 5-14 5.8.3 “EVENT TABLE” DATA LOGGING FEATURE... 5-15 5.8.4 RS-232C INTERFACE DATA LOGGING COMMANDS... 5-16 6.
Maintenance And Troubleshooting...6-1 6.1 6.2 6.3 6.4 6.5 6.6
7.
GENERAL ... 6-1 MAINTENANCE ... 6-1 TROUBLESHOOTING ... 6-2 REPLACEMENT PARTS ... 6-4 FUSE DETAILS ... 6-4 RS-485 SERIAL INTERFACE CONNECTIONS AND COMPONENTS:... 6-5
Options, Accessories And Spare Parts ...7-1 7.1 GENERAL ... 7-1 7.2 CONTROLLER OPTIONS / ACCESSORIES... 7-1 7.3 OPTIONS AND ACCESSORIES FOR RS-485 SERIAL COMMUNICATIONS... 7-1 7.3.1 BATTERY BACK-OPTION ... 7-1 7.3.2 HOT GAS BYPASS OPTION... 7-2 7.4 CABINET MISCELLANEOUS SPARE PARTS ... 7-2 7.5 ELECTRICAL SPARE PARTS... 7-3 7.6 PLUMBING SPARE PARTS ... 7-3 7.7 MISCELLANEOUS SPARE PARTS... 7-3
8.
One Fill All Fill (OFAF) Network Setup And Operation...8-1 8.1 8.2 8.3 8.4 8.5 8.6
GENERAL ... 8-1 EPROM INSTALLATION ... 8-1 ONE FILL ALL FILL NETWORK SET UP ... 8-2 HOW THE OFAF SYSTEM WORKS... 8-4 RELATIONSHIPS BETWEEN FOG CLEARING AND OFAF OPERATION. ... 8-4 OFAF AND PC/PRINTER INTERFACE. ... 8-5
9.
Glossary Of Terminology...9-1
10.
Handling Of Liquid Nitrogen...10-1
10.1 10.2 10.3 10.4 10.5 11. 11.1 11.2 12.
GENERAL ... 10-1 PROPERTIES ... 10-1 HANDLING CRYOGENIC STORAGE DEWARS ... 10-1 LIQUID NITROGEN SAFETY PRECAUTIONS ... 10-2 RECOMMENDED FIRST AID... 10-3 Serial Interface With A Computer ...11-1 GENERAL ... 11-1 ‘TERMINAL’ PROGRAM SETTINGS USING MICROSOFT WINDOWS... 11-1 Temperature And Level Calibration Procedures ...12-1
12.1 TEMPERATURE SENSOR CALIBRATION PROCEDURES... 12-1 12.1.1 “FULL-RANGE” TEMPERATURE SENSOR CALIBRATION METHOD... 12-1 12.1.2 “LOW-TEMP RANGE” TEMPERATURE SENSOR CALIBRATION PROCEDURE ... 12-3 12.2 LIQUID LN2 LEVEL SENSOR CALIBRATION PROCEDURE ... 12-4
1-2
Table Of Contents
12.2.1 12.2.2
MVE TEC2000 System Monitor User’s Manual “METER/DIP STICK” LN2 LEVEL DISPLAY CALIBRATION METHOD ...12-5 “IMPOSED HEAD PRESSURE” LN2 LEVEL DISPLAY CALIBRATION METHOD...12-6
13.
Typical Wiring And Plumbing Schematics... 13-1
1.2
Table Of Illustrations
FIGURE 2-1, TEC2000 SYSTEM MONITOR FRONT PANEL... 2-2 FIGURE 3-1, “BUILT IN” XLC TEC2000 SYSTEM MONITOR REAR PANEL ... 3-2 FIGURE 3-2, “STAND ALONE” XLC TEC2000 SYSTEM MONITOR BASE... 3-2 FIGURE 3-3, BUILT IN SYSTEM MONITOR INSTALLATION... 3-6 FIGURE 3-4, STAND ALONE SYSTEM MONITOR INSTALLATION... 3-8 FIGURE 3-5, TYPICAL SERIAL INTERFACE CONNECTIONS; RS-485 TO RS-232 CONVERSION ... 3-9 FIGURE 4-3, TYPICAL DEWAR LEVEL SET-POINTS... 4-6 FIGURE 4-4, TYPICAL DEWAR TEMPERATURE SET-POINTS ... 4-7 FIGURE 6-1, RJ-45 CABLE ASSEMBLY (P/N 10740053) WIRING DETAILS... 6-5 FIGURE 6-2, RJ-45 TO DB-25S ADAPTER (P/N 10740011) WIRING DETAILS ... 6-6 FIGURE 6-3, DB-9S TO DB-25P ADAPTER (P/N 10751182) WIRING DETAILS... 6-6 FIGURE 8-1, OFAF MASTER CABLE CONFIGURATION... 8-2 FIGURE 8-2, DAISY CHAIN NETWORK CONFIGURATION ... 8-3 FIGURE 8-3, "STANDARD" REVERSE CONNECTED RJ45 PC NETWORK CABLE CONFIGURATION. ... 8-3 FIGURE 10-1, TYPICAL CRYOGENIC STORAGE DEWAR ... 10-2 FIGURE 13-1, DOMESTIC POWER SUPPLY SCHEMATIC 120V/60HZ... 13-2 FIGURE 13-2, INTERNATIONAL POWER SUPPLY SCHEMATIC 230V/50HZ... 13-3 FIGURE 13-3, CONTROL BOARD SCHEMATIC CABINET APPLICATION... 13-4 FIGURE 13-4, CONTROL BOARD SCHEMATIC STAND ALONE APPLICATION ... 13-5 FIGURE 13-5, MAIN BOARD SCHEMATIC PAGE 1, ALL APPLICATIONS ... 13-6 FIGURE 13-6, MAIN BOARD SCHEMATIC PAGE 2, ALL APPLICATIONS ... 13-7 FIGURE 13-7, PLUMBING SCHEMATIC CABINET APPLICATION... 13-8 FIGURE 13-8, PLUMBING SCHEMATIC STAND ALONE APPLICATION ... 13-9
1.3
Table Of Tables
TABLE 2-1. TEC 2000 SYSTEM MONITOR SPECIFICATIONS... 2-4 TABLE 4-1, SET-POINT SUMMARY ... 4-6 TABLE 4-2. SATURATED LN2 TEMPERATURE VERSES ALTITUDE... 4-12 TABLE 4-3. ALARM CONDITIONS AND ASSOCIATED DISPLAYS ... 4-14 TABLE 5-1, RS-485 INTERFACE SPECIFICATIONS... 5-2 TABLE 6-1, PARTS SERVICEABLE OR REPLACEABLE ONLY BY MVE ... 6-4 TABLE 6-2, FUSE DETAILS ... 6-4 TABLE 12-1 ... 12-8 TABLE 12-2 ... 12-9
Table Of Contents
1-3
XLC TEC2000 System Monitor User’s Manual
2. Introduction 2.1
General This chapter introduces the MVE, Inc. TEC 2000 System Monitor used in XLC Series Dewars. A description of cryogenic storage Dewars is provided in Paragraph Description of Cryogenic Storage Dewars. A description of the MVE cryogenic storage systems is provided in Paragraph MVE Cryogenic Storage System Description. General Liquid Nitrogen safety instructions are provided in Paragraph Handling Liquid Nitrogen. A summary of TEC 2000 System Monitor features is provided in Paragraph Summary of TEC 2000 System Monitor Features. A list of specifications is provided in Table 2-1.
2.2
Description of Cryogenic Storage Dewars Vacuum-insulated storage dewars are commonly used in the life sciences, chemistry, and in the metals conditioning industry for the treatment of materials through direct contact with liquid nitrogen or liquid nitrogen vapor. In most cases, it is critical to monitor and control the liquid level of nitrogen in Dewars under continuous use conditions. For many applications in the life sciences and chemistry, it is important to monitor the vapor phase zone inside a Dewar above the liquid level to maintain a “safe” temperature. An explanation of “safe” temperatures is as follows. There is evidence that biological materials stored at temperatures well below -79°C (the saturation temperature of CO2 at 1 ATM pressure) will be preserved more satisfactorily than at warmer temperatures. The biochemical and physical properties through which biomaterials sustain life are affected to varying degrees by temperature. Because low temperatures are successful in arresting these properties for preservation purposes, the lower the temperature is the better. It has been determined that indefinitely prolonged storage may be safely achieved below -130°C, the re-crystallization point of water (ice).
2.3
MVE Cryogenic Storage System Description The MVE Dewars are cryogenic storage systems ideal for LN2 storage applications in agriculture, breeding, chemistry, medicine, physics and the food/beverage, pharmaceutical and metallurgy fields. Materials are stored in MVE Dewars in one of two modes: vapor phase or liquid immersion. In normal vapor phase operation, a 4” to 7” level of LN2 is maintained in the bottom of the Dewar. An optional vapor platform supports the inventory system above the LN2. During steady state operation, a temperature gradient exists between the top and bottom of the inventory system. The bottom rack will be near LN2 temperature (-195.8oC or 77.4oK) and the top rack will typically be between -150oC (123.15oK) to -125oC (148.15oK). Top rack temperatures are dependent on frequency of usage, inventory system, surrounding ambient conditions, LN2 level settings and model type. In the immersion storage mode, the inventory racking system rests on the bottom of the Dewar and the lower racks are immersed in LN2. Regardless of the storage mode, the most important parameter that must be controlled in the Dewar is the level of LN2. There are four LN2 level set points to be determined. Details of how to enter these set points in the MVE System Monitor’s memory will be covered in Chapter 3, Operation. Once the set points are entered, the system monitor controls the flow of LN2 from a LOW PRESSURE, (22 to 25 psig) LN2 storage tank to maintain the liquid level in the unit. Another important parameter to consider is temperature. Up to two temperature sensors can be used. The first sensor (generally sensor “A”) can be placed at the top or warmest part of the Dewar. The second sensor (sensor “B”) may be placed at any strategic location within the Dewar. By setting respective temperature alarms in the System Monitor for each of the sensors “A” and “B”, a second layer of protection is added and another level of confidence is gained in ensuring preservation integrity. High precision, stable, platinum RTD temperature sensors are used for monitoring either liquid or vapor phase nitrogen temperatures in the Dewar. The hermetically sealed sensor is specifically designed for proper thermal behavior in a cryogenic LN2 environment. Both sensors (“A” and “B”) are interchangeable. These RTD sensors are extremely accurate from +0.0oC to -199oC (within +/- 2oC) full scale.
Introduction
2-1
XLC TEC2000 System Monitor User’s Manual
Figure 2-1, TEC2000 System Monitor Front Panel
NOTE: READ THE FOLLOWING SECTION BEFORE OPERATING THIS EQUIPMENT.
2.4
Handling Liquid Nitrogen Liquid nitrogen (LN2) is a potential asphyxiate and may cause severe frostbite. Please observe all proper safety precautions to ensure proper handling of LN2. Consult your local LN2 Dealer for detailed handling instructions. Refer to Section 10 Handling Of Liquid Nitrogen for general handling instructions. WARNING
•
Liquid nitrogen is a potential asphyxiate and can cause rapid suffocation without warning. Store and use in area with adequate ventilation. DO NOT vent container in confined spaces. DO NOT enter confined spaces where gas may be present unless area has been well ventilated. If inhaled, remove to fresh air, and SEEK MEDICAL ATTENTION. If not breathing, give artificial respiration. If breathing is difficult, give oxygen.
•
Liquid nitrogen can cause severe frostbite to the eyes or skin. DO NOT touch frosted pipes or valves. In case of frostbite, SEEK MEDICAL ATTENTION at once. If MEDICAL HELP is not readily available, warm the affected areas with water that is near body temperature.
2.5
EQUIPMENT USAGE The Equipment with which this manual is included is a cryogenic freezer that uses LN2 as refrigerant. It is intended to be used for the storage of biological samples that have been previously frozen in a controlled environment. It is not designed to be used for initial freezing of the biological samples. It is not designed
2-2
Introduction
XLC TEC2000 System Monitor User’s Manual for use with a refrigerant other than LN2. Usage for purposes other than those intended could present a hazard to the user.
2.6
Summary of TEC 2000 System Monitor Features There are two versions of the TEC 2000 System Monitor. The first is the built-in or cabinet style System Monitor that is built into the XLC cabinet freezer units. The second is the stand-alone System Monitor. Complete System Monitor accessories include a remote power supply (for stand-alone versions), Relay Terminal Mating Connectors, Temperature Sensor Input Connectors, and Level Input plastic tubing. Further details on available options and accessories are provided in Chapter 6. The following is a summary of TEC 2000 System Monitor features: •
•
•
Liquid nitrogen level measurement sensor which employs a highly durable pressure sensor: Accurately measures liquid level. Unaffected by the mechanical problems associated with ice formation around thermistor type level sensors. Because the level sensor response is linear the rate of liquid nitrogen consumption can be calculated and displayed. This is a reference value only. It cannot be used to calculate volume of LN2 consumption when items are stored in the freezer. Liquid level monitoring, fill and alarm control points are managed entirely from the instrumentation. Control instrumentation with integrated operation software enhances dewar Cryo-preservation management: The instrument offers a clearly legible, simultaneous display of level and temperature. The display is backlit for ease of reading in poorly lighted storage areas. Alarm system provides high and low set point protection for both liquid level and vapor phase temperature settings. Upon activation, the temperature (and/or level) alarm will display the error condition, sound a pulsing audible warning and make a relay closure for remote monitoring. Relay contacts are provided for switching current to a control solenoid during automatic filling. An alarm will be activated if the Dewar does not refill within 60 minutes. A serial computer interface is provided so that logged data and operating status can be monitored and ‘down-loaded’ by a computer, or recorded directly to a compatible printer. Complete Dewar operation (control of settings and alarms) is also possible through the serial communications. A full function keypad is provided to simplify operation. The alphanumeric liquid crystal display prompts the user during function selection to facilitate use. A Hot Gas Bypass Accessory is available that reduces boil-off of LN2 inside the Dewar during filling when long transfer lines are used. A Back-up Battery Accessory is available that allows for continuous operation of ALL functions up to 72 hours after main power loss. One Fill All Fill (OFAF) capability is built in. Multiple units can be networked via the serial communications port so that when one unit calls for a fill cycle, all units on the supply network will begin filling. This reduces overall LN2 consumption by filling all units while the supply system is cold Vapor phase temperature monitoring provided: Provides assurances to users that materials stored in the vapor phase portion of a Dewar are being preserved at “safe” temperatures. High and low, temperature alarm points can be established from the instrument.
Introduction
2-3
XLC TEC2000 System Monitor User’s Manual Table 2-1. TEC 2000 System Monitor Specifications Level Measurement: Number of Inputs: One Sensor Type: Dual Port Pressure Transducer Measurement Accuracy: ± 0.5 inches (± 13 mm) Liquid Level Accuracy Range: 3 inches (76 mm) to 28 inches (711mm) Level Display Update Rate: One reading per four seconds Level Control: Control Type: On - Off Control Output (“Fill” Solenoid Valve): 24 Vdc, 1 A Max LN2 Plumbing Design Pressure: 35 psig Thermometry: Number of Inputs: Two Measurement Type: Two-lead Sensor Type: Platinum RTD Temperature Range: +50oC to -200oC Measurement Accuracy: ± 2.0oC Temperature Accuracy Range: 0oC to -200oC Display Update Rate: One reading per two seconds Alarms: Number of Alarm Relays: One Alarm Conditions: Standard: Low level, High level, Low temperature, High temperature, and LN2 supply. Optional: Power failure, Low battery, and Bypass valve Alarm Contacts: SPDT: Common, one Normally Open (NO) and one Normally Closed (NC) contacts; Relay contacts rated to 1A at 30 Vdc Bypass Accessory: Control Output (Bypass Solenoid Valve): 24 Vdc, 1 A Max. Sensor Type: Platinum RTD Back-up Battery Accessory: Number of Batteries: Two 12 Vdc Batteries in Series for 24 Vdc Back-up Battery Type: Sealed, Rechargeable Battery (8 Cells in Series) Voltage and Size: Two Each at 12 Vdc, 7 amp-hr Rating at 350 ma delivery Front Panel: Display Type: 2 row by 16 character backlit alphanumeric liquid crystal Information Displayed: Level, temperature, alarms, units, fill status Display Resolution, Liquid Level: 1.0 mm or 0.1 inches; Display Resolution, Temperature: 0.1 °C, °F, or °K Keypad: Numeric and special function Interface: Computer Interface: Serial communication with RS-485 electrical format; 300, 1200, or 9600 Baud; RJ45 modular connector General: Ambient Temperature Range: 15 °C to 35 °C Monitor Input Power Requirement: 24 VAC, 50/60 Hz., 1 amp (FLA) Power Supply (Standard): 120 VAC, 60HZ, primary, 0.2 amp (FLA) Power Supply (Optional): 230 VAC, 50HZ, primary, 0.15 amp (FLA)
2-4
Introduction
XLC TEC2000 System Monitor User’s Manual
3. Installation 3.1
General This chapter provides a description of the base or rear panel layout on both the stand-alone and built-in MVE XLC TEC 2000 System Monitor. . The built-in System Monitor rear panel is shown in Figure 3-1. The stand-alone System Monitor base is shown in Figure 3-2. The Bypass, Fill, and Flush relay outputs, Temperature Inputs, and Level Input are only included on the stand-alone units. These connections are internal on cabinet style freezers and are factory connected upon receipt so that accessing the interior of the cabinet is not necessary.
3.2
Inspection and Unpacking Inspect shipping containers for external damage. All claims for damage (apparent or concealed) or partial loss of shipment must be made in writing to MVE within 48 hours of receipt of goods. If damage or loss is apparent, please notify the shipping agent immediately. Open the shipping containers. A packing list is included with shipment that identifies what items were shipped. Please use the packing list to check off each item, as the system is unpacked. Inspect for damage. Be sure to inventory all components supplied before discarding any shipping materials. If there is damage to the system in transit, be sure to file proper claims promptly with the carrier and Insurance Company. Please advise MVE of such filings. In case of parts or accessory shortages, advise MVE immediately. MVE cannot be responsible for any missing parts unless notified within 30 days of shipment.
3.3
Repackaging for Shipment If it is necessary to return any part of the MVE System Monitor for repair or replacement, a Return Materials Authorization (RMA) number must be obtained from a Customer Service representative before returning the instrument to our service department. When returning an instrument for service, the following information must be provided before MVE can attempt any repair. A. System model and serial number B. User’s name, company, address, and phone number C. Malfunction symptoms D. Description of system E. Returned Materials Authorization (RMA) number If possible, the original packing material should be retained for reshipment. If not available, consult MVE for shipping and packing instructions.
Installation
3-1
XLC TEC2000 System Monitor User’s Manual
Figure 3-1, “Built In” XLC TEC2000 System Monitor Rear Panel
Figure 3-2, “Stand Alone” XLC TEC2000 System Monitor Base
3.4
Definition of Rear Panel Controls This section provides a description of the rear panel/base controls on both the stand-alone and built-in System Monitors. The rear panel consists of power input, serial communication port, bypass, fill and flush solenoid outputs, manual fill switch, alarm relay outputs, temperature inputs, level input, and backup battery connection. Power Input. The System Monitor is provided with a separate power supply (stand-alone Units only). The power supply for cabinet style units is inside the cabinet and factory connected. The external power connection is also used when upgrading early TEC2000 equipped cabinet units to the latest TEC2000 version. The input to the power supply is tailored to individual Customer requirement. The power supply output provides the 24 VAC that is plugged into
3-2
Installation
XLC TEC2000 System Monitor User’s Manual the ‘POWER, 24 VAC’ receptacle. Fuse. A replaceable 4-amp Quick Blow Fuse is provided to protect the LN2 control solenoids. A 1-amp quick-blow fuse for the electronics is internal.
SERIAL I/O Connector. The RJ-45 Serial input/output (I/O) Connector is for the RS-485 communications interface. This port is intended for connection to a PC or a Serial Printer. It should never be connected directly to a public telecommunications network. See section 3.4.1 COMPUTER INTERFACE CONNECTION.
MANUAL FILL Switch. The ‘MANUAL FILL’ Switch is used to override the unit’s software and manually fill the Dewar. The switch is a momentary type that must be held in to operate. This switch will function as long as there is 24 VAC power applied to the unit (or 24 Vdc from a battery back-up system).
ALARM Relay Output. This output is provided for customer hook up to an external alarm. Normally Open (NO), Common (C), and Normally Closed (NC) contacts are provided. Maximum current rating of the remote alarm circuit is 1amp at 30 Vdc.
BYPASS, FILL, and FLUSH Valve Relay Outputs, and BYPASS Temperature Sensor Connector’s (stand-alone unit Only). The relay outputs provide 24 Vdc to control the Bypass, Fill, and Flush functions of the Dewar. The RTD sensor input is for the Bypass temperature sensor.
Back-up Battery (stand-alone unit only). The battery terminals are for the back-up battery connection
TEMPERATURE INPUTS (stand-alone unit only). The A and B Temperature Probe assemblies are connected here. The temperature probe assembly consists of an encapsulated sensor probe, wire, and connector. The A input is normally used for temperature readings at the top of the Dewar and reflect the warmest point in the Dewar. The B input is normally used for the second temperature probe located at the sample level (or even physically located in a sample) reflecting the coldest point in the Dewar. NOTE: Sensors A and B are connected at the front right corner of the top panel on cabinet versions.
Installation
3-3
XLC TEC2000 System Monitor User’s Manual LEVEL INPUT (stand-alone unit only). The clear vinyl level input tube is connected here. This connection is internally connected at the factory on Cabinet style units.
3.4.1 COMPUTER INTERFACE CONNECTION The RJ-45 connection on the rear control panel of XLC 500/1200 cabinet freezers, and in the base of the Stand Alone TEC 2000 controller used on all other XLC models, is an RS-485 Computer Interface connection. It is intended to be used only to connect the unit to a PC or Serial Printer. This port should not be connected to a public telecommunications network
The manufacturer/supplier:
CHART/ MVE Applied Technologies, Biological Systems 3505 County Road 42 West Burnsville, Minnesota 55306-3803
Declares that:
Cryogenic LN2 Freezers XLC 1200 XLC 1211 XLC 1370 XLC 1520HE XLC 1830 XLC 1830-2T XLC 1830HE XLC 1841 XLC 230 XLC 500 XLC 511 XLC 810 XLC 810HE
Are not intended to be connected to a public telecommunications network The connection of such equipment to a public telecommunications network in a European Community Member State will be in violation of the national law implementing Directive 91/263/EEC on the approximation of the laws of the Member States concerning telecommunication terminal equipment, including the mutual recognition of their conformity.
3.5
Hardware Installation Hardware installation instructions are provided in the following five sections. 3.5.1 . MAIN POWER CONNECTION. 3.5.2 Dewar Plumbing Connections. 3.5.3 “Built-In” (or “Cabinet-Style”) System Monitor Installation. 3.5.4 Stand-Alone System Monitor Hardware Installation. Finally, 3.5.5 RS485 Interface Connections (Customer Use is Optional).
3-4
Installation
XLC TEC2000 System Monitor User’s Manual
3.5.1 MAIN POWER CONNECTION NOTE: THE POWER CORD PLUG CONNECTION SERVES AS THE POWER CONNECT/DISCONNECT DEVICE. THE CORD EXITS THE UNIT AT THE REAR. THE UNIT SHOULD NOT BE POSITIONED SUCH THAT IT BLOCKS ACCESS TO THE RECEPTACLE TO WHICH THE UNIT IS CONNECTED. IN CASE OF EMERGENCY, THE PLUG MUST BE DISCONNECTED FROM THE RECEPTACLE TO SHUT DOWN THE UNIT. The power supply cord should be connected to an outlet with a viable earth ground connection and the appropriate voltage and current rating based on the voltage indicated on the label on the rear of the unit. NOTE: GROUND PROTECTION FOR THE ENTIRE UNIT IS ACCOMPLISHED THROUGH THE GROUND CONDUCTOR OF THE POWER CORD. DISABLING THIS GROUND PATH COULD CREATE AN UNSAFE CONDITION FOR OPERATORS AND COULD DAMAGE THE UNIT AS WELL. Domestic (US & CANADA) installation requires 120VAC, 60HZ, 0.2AMP service. The 120V unit is supplied with a NEMA 5-15P plug configuration and must be connected to a NEMA 5-15R receptacle configuration. European installation requires 230VAC, 50HZ, 0.15AMP service. The 230V unit is supplied with a Schuko plug configuration and should be connected to a Schuko receptacle. If neither plug configuration is compatible with the available receptacle, a replacement can be made. Use the configuration required to fit the receptacle. Insure that the replacement plug is rated for the voltage and current specified above and on the unit, and that it meets any and all applicable standards for the locale and application.
3.5.2 Dewar Plumbing Connections Connect a transfer line (provided) from an LN2 supply tank to the fill connection at the rear of the freezer. Optimum supply tank pressure is roughly 22 to 25 psi. The design pressure of the LN2 input delivery plumbing circuit (and optional ‘Hot Gas Bypass” plumbing) in each MVE Dewar is 35 psi. It is recommended that LN2 storage tanks feeding the cryogenic dewar operate at pressures lower than 35 psi to reduce the LN2 ‘flash-off’ rate during filling and to maximize the cryogenic valve life. (NOTE: A pressure relief valve built into the Dewar’s LN2 inlet supply plumbing will exhaust nitrogen to the surroundings if the supply tank exceeds 50 psi.) The supply line can be insulated to minimize LN2 transfer losses. Ensure all connections are leak free by opening the valve of the LN2 supply tank and apply a soap and water solution to each field joint (factory joints were leak tested at assembly). You should not see bubbles forming at any joint. Wipe away excess soap and water.
3.5.3 “Built-In” (or “Cabinet-Style”) System Monitor Installation These products are Listed to applicable U.S. and Canadian safety standards by Underwriters Laboratories Inc. Most of the required hardware connections will already be factory made for MVE’s “Built-In” (or “Cabinet-Style”) cryogenic dewars, specifically models, XLC500 and XLC1200. However, several connections should be utilized. See Figure 3-3. 1.
Installation
Although there is an audible alarm built into the System Monitor, an external alarm connection to the remote alarm contacts should also be considered. The external alarm can be any device suitable to the 1A at 30Vdc rating of the alarm relay. The ALARM output consists of a Normally Open (NO), Common (C), and Normally Closed (NC) relay contacts. To provide a hardware default power failure alarm on units not equipped with a battery backup, the remote alarm relay is energized when power is applied to the unit. When main power to the unit fails, the relay is deenergized, and thus switches the remote alarm. Typical alarm devices include alarm bells, sirens, lights, or security system. IMPORTANT: The cable connecting the freezer to the remote alarm must be rated for 1A/30Vdc and it must be shielded. The cable shield must be grounded at the freezer end via a convenient screw on the freezer. Failure to do so will allow local electrical interference (ESD, RFI, and EMF) to be transmitted into the device electronics, which could cause a malfunction of the freezer.
3-5
2.
XLC TEC2000 System Monitor User’s Manual A built-in power supply is provided with all “Cabinet-Style” XLC models (models XLC500 and XLC1200) utilizing the System Monitor. The input power cord to this power supply is tailored to individual Customer’s requirement. The output of this power supply provides 24 VAC at 2.4 amps to the System Monitor. Plug in the main power cord (120V/1/60, or 230V/1/50) when ready for operation. NOTE: The power cord plug is the sole means for “ON/OFF” control of the Dewar.
3.
Some MVE models are equipped with a 72-hour Back-up Battery option. These Dewars are shipped with the battery disconnected. IMPORTANT: Before connecting the battery always plug in the main power cord FIRST and ensure “normal” Dewar operation. Remove the rear cabinet panel. (See Figure 3-3). Connect the unplugged, blue wire receptacle to the 3/16” male (+) positive terminal (left) of the top battery as seen through the opening. Replace rear panel. After hooking up the battery, unplug the main power cord to ensure the display remains lit the alarm buzzer sounds and the display indicates a “Power Failure” condition. NOTE: These alarm indications are delayed 30 minutes to minimize nuisance alarms due to short power outages. Lastly, always remember to plug the main power cord back in.
4.
Two temperature sensor/cable assemblies (referred to as probes A and B) are shipped loose and require insertion into their mating receptacles located at the front right corner of the top panel. Insert the cable connectors into the receptacles push until fully engaged, then push in and turn the outer locking nut 1/4 turn to prevent disengagement. A sensor well approx. 3/16” ID is located on the inner vessel perimeter near the sensor connections that extends to the bottom of the Dewar. Slide one of the sensors (generally probe A) down the tube to a desired Dewar monitoring level. The second sensor (probe B) can be strategically located inside the Dewar to reflect actual sample temperatures.
Figure 3-3, Built in System Monitor Installation
3.5.4 Stand-Alone System Monitor Hardware Installation Stand-Alone System Monitor connections are as follows. See Figure 3-2, and Figure 3-4. 1.
3-6
The System Monitor for ‘Stand-Alone’ versions is a self-contained electronic device and is shipped inside the Dewar in a separate package. Carefully open the System Monitor from its packaging. The monitor will be affixed to its mounting bracket that will slide into or onto an engagement pipe on the Dewar. When the monitor is positioned at a desirable viewing position
Installation
XLC TEC2000 System Monitor User’s Manual for the customer, (ensure that the desired position does not impair lid opening or removal) tighten the setscrew on the engagement pipe to eliminate any further rotation. 2.
Connect Temperature Probe Assemblies to TEMPERATURE INPUTS A and B. Each temperature probe assembly consists of an encapsulated sensor probe, wire, and connector. The A probe is normally used for temperature readings at the top of the Dewar and reflect the warmest point in the Dewar. The B probe can be located at the sample level (or even physically located in a sample) reflecting the coldest point in the Dewar.
3.
Connect the 1/4” OD vinyl tube from the 3-way FLUSH valve (connecting to the Dewar’s liquid level sensing tube) to the LEVEL INPUT hose barb.
4.
Relay connectors are provided to power the FILL and FLUSH solenoid valves. Two terminals each are provide for these valves. These valves should be pre-wired to an 8-pole connector at the factory. IMPORTANT: Note the polarity (+ and -) of the Fill valve connector and the different colored wires for each. Refer to the wiring diagrams in Section 13 Typical Wiring And Plumbing Schematics For connections. (Also, see Error! Reference source not found..)
5.
Although there is an audible alarm built into the System Monitor, an external alarm connection to the remote alarm contacts should also be considered. The external alarm can be any device suitable to the 1A at 30Vdc rating of the alarm relay. The ALARM output consists of a Normally Open (NO), Common (C), and Normally Closed (NC) relay contacts. To provide a hardware default power failure alarm on units not equipped with a battery backup, the remote alarm relay is energized when power is applied to the unit. When main power to the unit fails, the relay is deenergized and thus switches the remote alarm contacts. Typical alarm devices include alarm bells, sirens, lights, or security system. IMPORTANT: The cable connecting the freezer to the remote alarm must be rated for 1A/30Vdc and it must be shielded. The cable shield must be grounded at the freezer end via a convenient screw on the freezer. Failure to do so will allow local electrical interference (ESD, RFI, and EMF) to be transmitted into the device electronics, which could cause a malfunction of the freezer.
6.
A separate power supply is provided with the System Monitor. This power supply is attached to the plumbing shroud or rear-mounting bracket of the freezer at the factory. The input power cord to the power supply is tailored to individual Customer’s requirement (120V/1/60 or 230V/1/50). Connect the output of the power supply to the POWER, 24 VAC connector (5-pin DIN) on the base of the control unit.
7.
Units employing the Hot Gas Bypass Option will require connection of the bypass sensor and the bypass solenoid valve to the base of the unit. These are connected using the supplied 8-pole connector that connects the fill and flush valves described earlier. If ordered with a hot gas bypass, these will be pre-wired to the connector from the factory. IMPORTANT: Note the polarity (+ and -) for the bypass valve connection as this must be properly connected
8.
Units having optional battery back up require battery connection. IMPORTANT: Note the polarity (+ and -) for the 24Vdc battery connection as this must be properly connected. See Section 13, Typical Wiring And Plumbing Schematics For appropriate wiring diagrams. (Also, Figure 3-2.) IMPORTANT: Before connecting the battery always plug in the main power cord FIRST and ensure “normal” Dewar operation. After hooking up the battery, unplug the main power cord to ensure the display remains lit the alarm buzzer sounds and the display indicates a “Power Failure” condition. NOTE: These alarm indications are delayed 30 minutes to minimize nuisance alarms due to short power outages. Lastly, always remember to plug the main power cord back in.
Installation
3-7
XLC TEC2000 System Monitor User’s Manual
Figure 3-4, Stand Alone System Monitor Installation
3.5.5 RS-485 Interface Connections (Customer Use is Optional) RS-485 Serial Communications Interface and is built into all TEC 2000 System Monitors. By using RS485 (versus RS-232), multiple Dewars can be addressed, monitored and controlled more efficiently from a single host computer located up to 4000 feet away from the farthest Dewar site. When connecting from one Dewar to a printer or host computer or from Dewar to Dewar, 8-wire communication (similar to telephone cord) cable with dual ended RJ-45 male jacks is required. Connection to a customer’s computer is from the SERIAL I/O port (female RJ-45) on the rear control panel. All (or most) IBM compatible PC’s (the host computer) communicate using RS-232 serial interface. As shown in Figure 3-5, an RS-232 to RS-485 converter is required to modify the serial interface signal from the TEC-2000 controller to RS-232 for use by the host computer (or printer). NOTE: A null modem adapter (DB-25P to DB-25S, MVE P.N. 10746324) may be required between your computer’s RS-232 serial port (DB-9P) and the RS-232 to RS-485 converter depending on your specific serial interface card. This null modem adapter essentially reverses the transmit and receive signals (pins #’s 2 and 3 of the DB-9P) and several ‘handshaking’ signals. These adapters may be ordered separately. See Chapter 5 for further details.
3-8
Installation
XLC TEC2000 System Monitor User’s Manual
Figure 3-5, Typical Serial Interface Connections; RS-485 to RS-232 Conversion
3.6
INITIAL SETUP AND SYSTEM CHECKOUT The following procedure is a room temperature setup and system checkout procedure. The intent of this procedure is to verify the installation at room temperature before adding LN2.
3.6.1 Normal Display Sequence After Successful, Start-up Self Diagnostics Upon plugging in the Control Unit Power Supply, the green POWER light turns on, display illuminates, and the following display appears for approximately 10-15 seconds:
Diagnostics Please Wait The system monitor checks for proper functionality of critical component connections and software loops during this self-diagnostics mode. If all things are found normal, the following two displays will be displayed for two seconds each before returning to the “normal” display shown below:
Diagnos Complete System OK Level and Temp Monitor Installation
3-9
XLC TEC2000 System Monitor User’s Manual If there are no faults detected during the ‘Self-Diagnostics’ mode at start-up, the ‘normal’ Level and Temperature display will now appear. Just prior to the ‘normal’ display, the screen may initially show dashes for both level and temperature. Since the Dewar is empty of LN2, the level reading will display 0.0 inches. The temperature reading from probe A will be near room temperature range as shown below:
Level + 0.0 in Temp A +25.0 C This display will show for 2 seconds, followed by a sequence of expected ‘Hi Temp A’, ‘High Temp B’ and ‘Low Level’ alarm displays as described in 3.6.2 below.
3.6.2 System Fault, Alarm Displays Following Start-Up Self-Diagnostics: Following the Power-On, Self-Diagnostics procedure, it is unlikely that ‘system fault’ alarm messages will be displayed. Among other tasks, the self-diagnostics procedure checks for these possible alarm conditions: 1. 2. 3.
An “Open” Temperature Sensor; either sensor A, B or both; An “Open” Hot Gas Bypass Sensor (applies only if the bypass option is included); A Software or Hardware Fault of the Controller.
In the event that one or all of the above three alarm conditions are detected by the self-diagnostics, the following display prompts will immediately follow the self-diagnostics routine. Each display is visible for approximately 2 seconds and is sequentially described below. If sensor A is detected to be “Open”, the display will read as shown below. [A similar display will be read for an ‘Open Sensor B’]:
Diag Err: Sens A Open or Not Conn The next display will gives you the option to permanently disable this alarm condition. [Typically, this alarm is disabled when only a single sensor is monitoring the Dewar interior temperatures.]
Disable Alarm? ➔Yes No To disable this open sensor alarm, press the [Enter] key while the display is shown, and if the rightpointing arrow is to the left of ‘Yes’. If you do not wish to permanently disable this alarm, press the [Down Arrow] key to toggle the arrow to the left of “No”, then press [Enter]. NOTE: If you wait too long before pressing any key (greater than 20 seconds), the monitor will assume the displaying prompts’ settings and automatically default to the ‘Normal’ display indicating liquid level and temperature. To return to the above prompt, turn the monitor OFF and back ON to cycle back through the self-diagnostics. An alarm message may be read as follows if the hot gas bypass sensor is “Open”. This display will only occur if the system monitor is equipped with the hot gas bypass option.
Diag Err: Hot Gas Open or Not Conn This alarm can be permanently disabled by a similar prompt as that shown above for ‘Open’ Sensor A. IMPORTANT: If you wish to utilize the hot gas bypass option (when incorporated), the bypass sensor must be connected and functional. If there is an “Open Sensor” condition, the bypass cycle will not occur. The normal filling cycle will initiate. If the “Open Sensor” condition is not detected, the bypass cycle will be initiated as intended. The bypass cycle exhausts warm LN2 gas (generated until the transfer line is cooled down to LN2 temperatures) through the hot gas bypass valve, through the muffler to atmosphere. The bypass cycle will automatically terminate If the hot gas bypass sensor is not colder than the bypass temperature (programmed in the maintenance menu, default -100oC) before the bypass time delay passes (programmed in the maintenance menu, default 5 minutes). At which time the fill valve energizes
3-10
Installation
XLC TEC2000 System Monitor User’s Manual to begin a normal fill cycle. If the bypass sensor remains open, all ‘Hot Gas Bypass’ functions can be disabled in the “Maintenance Menu” as described later in 4.5.1. When multiple alarms are simultaneously present as described in this 3.6.2, ALL applicable alarm messages are sequentially displayed for 2 seconds finally returning to the ‘Normal’ display, then recycling back through all alarms. These diagnostic alarms must be either corrected or disabled in order to continue. When all alarm displays are deactivated, the displays described in 3.6.3 below will follow. IMPORTANT: After an alarm is initiated and properly resolved disabled, it will be necessary to press the [Alarm Mute] key twice to clear the alarm from the display. Once to mute the audible alarm, then again to clear it and turn the audible alarm back ‘ON’ or to the stand by condition. If the [Alarm Mute] key was pressed to silence the audible alarm while working to correct the condition, pressing the key once more will clear and reset the alarm. This permanently removes the alarm condition from the controller’s memory. If the alarm returns, the fault condition was not properly rectified. Lastly, in the unlikely event that a ‘Major’ fault was detected by the self-diagnostics (generally either a software or hardware flaw of the system monitor) the following prompt will display continuously:
Controller Malfunction If the above display is shown, the system monitor has a non-correctable fault condition. The controller could be ‘re-initialized’, by pressing and holding the ESCAPE key for 30 seconds, to reset all programmable, memory-stored parameters to their default values. Reassign all parameters and restart the controller. If the message persists, contact the factory or your local MVE representative.
3.6.3 “Normal” (or Expected) Alarm Displays Following a Successful Self-Diagnostics: After the self-diagnostics routine, the ‘Normal’ display will scroll with expected ‘High Temp A (and B)’ and ‘Lo Level’ alarms in 2 second intervals. Immediately following the ‘Normal’ display, the green FILL and red ALARM status lights should turn on (temp. probe A will always display after power-up). You should hear the fill and flush relay solenoid valves activate along with the pulsating alarm buzzer (one second ON, one second OFF). The alarm displays will scroll as shown below. NOTE: The temperature sensors (A and/or B) may trigger an alarm display regardless which sensor is currently being displayed.
* ALARM * HIGH TEMP A * ALARM * HIGH TEMP B * ALARM * LOW LEVEL Push the [Fill Stop] key. The Fill light should turn off and you should hear the fill relay solenoid deactivate. Push the [Alarm Mute] key to mute the pulsating alarm buzzer. The MANUAL FILL switch located on the rear panel is used to override the unit’s software and manually fill the Dewar. The switch is a momentary type that must be held in to operate. This switch will function as long as there is main, 24 VAC power applied to the controller, or if 24Vdc is delivered from the back-up circuit. Push and hold the MANUAL FILL button in and listen for the fill valve to activate. Release the switch and listen for the fill valve to deactivate. Once this abbreviated checkout procedure is successfully completed, you can be reasonably sure the unit is ready for setup for normal operation. Proceed to Chapter 4 for further operational information
Installation
3-11
XLC TEC2000 System Monitor User’s Manual
4. Operation 4.1
General This chapter provides operational information for the XLC TEC 2000 System Monitor. Included are a definition of front panel controls in Section 4.2 and a description of normal operation in Section 4.3.
4.2
DEFINITION OF FRONT PANEL CONTROLS This Section provides a description of the front panel controls on the System Monitor. The front panel consists of three major sections: System Status indicators, a 2 row, 16 character Liquid Crystal Display (LCD), and a 20-position keypad. See figure below.
TEC 2000
Alarm Mute
System Monitor System Status
Level
Power
Fill Stop
Hi Level Alarm
Hi Temp Alarm
Define 100%
7
8
9
Hi Level Fill
Lo Temp Alarm
Define 0%
4
5
6
Lo Level Fill
Temp A
Inter− Face
1
2
3
Lo Level Alarm
Temp B
Units
.
+/−
Escape
Fill Alarm Temperature
Fill Start
Liquid Usage
0
Enter
Figure 4-1, TEC2000 System Monitor Front Panel
4.2.1 System Status Indicators Three Light Emitting Diodes (LED’s) provide system status as follows:
System Status Power Fill Alarm
Operation
Power Green LED indicates power is provided to the unit. (This LED will remain lit even when main power is lost if the back-up battery option is employed.) Fill
Green LED indicates that the Dewar is currently filling.
Alarm Red LED indicates that an alarm condition exists.
4-1