Operation Manual
15 Pages
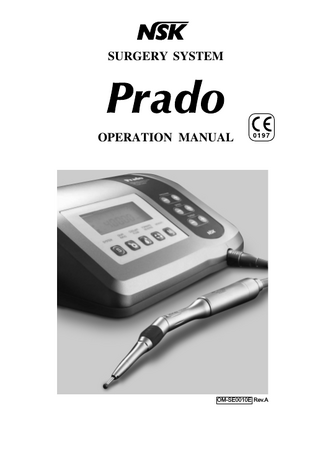
Preview
Page 1
SURGERY SYSTEM
OPERATION MANUAL
0197
OM-SE0010E Rev.A
The EU directive 93/42/EEC was applied in the design and production of this medical device. Thank you for purchasing the Prado. Read this Operation Manual carefully before use with regard to operating instructions, care and maintenance. Keep this Operation Manual for future reference. Classification of equipment • Type of protection against electric shock : – Class l equipment • Degree of protection against electric shock : – Type BF applied part • Method of sterilization or disinfection recommended by the manufacture : – See 8. Sterilization • Degree of protection against ingress of water as detailed in the current edition of IEC 60529 : – Foot Control: IPX8 ( Protected against the effects of continuous immersion in water ) • Degree of safety of application in the presence of a flammable anesthetic mixture with air or with oxygen or nitrous oxide : – EQUIPMENT not suitable for use in the presence of a flammable anesthetic mixture with air or with oxygen or nitrous oxide • Mode of operation : – Continuous operation
CONTENTS 1. Safety precautions prior to use... 2. Package Contents... 3. Control Unit with an Irrigation Pump... 4. Foot Control... 5. Installation... 6. Operation... 7. Care and Maintenance... 8. Sterilization... 9. Optional Accessories... 10. Specifications... 11. Disposing Product...
1 2 3 5 6 9 11 12 13 13 13
SAFETY PRECAUTIONS Please read these safety precautions carefully before use and follow the instructions when operating the device. These instructions are intended to avoid potential hazards that could result in personal injury or damage to the device. They are classified as follows in accordance with the seriousness and must be followed. Classification
Degree of Risk A hazard that could result in bodily injury or damage to the device if the safety WARNING precautions are not followed. A hazard that could result in slight or moderate bodily injury or damage to the CAUTION device if the safety precautions are not followed. N O T I C E General information needed to operate the device safely.
WARNING • Keep away from explosive substances and flammable materials. Do not use especially on patients anesthetized with nitrous oxide gas. • A possibility of malfunction may exist if the system is used in the presence of electromagnetic interference wave. Do not install the system in the vicinity of a device which emits magnetic waves. Turn off the power switch on the system's Control Unit if an ultrasonic oscillation device or an electrode knife is being used in the vicinity.
CAUTION • Prado is intended for use in surgical procedures. • Patient safety is a priority. • Read this Operation Manual before use, and make sure the functions of all parts are fully understood before commencing operation. • Inspect the operating status of the equipment before use, and use only after confirming that no abnormalities exist. • Test run the product to ensure its correct operation prior to using it. • If the product should ever malfunction (excessive vibration, noise, heat, etc) please turn it off immediately and return it to your Authorized Dealer for inspection. • If the product is used frequently, it is advisable to keep a small stock of replaceable parts. • Always use an earthed electrical socket. • To avoid possible injury or product damage, ensure that the Micromotor has completely stopped before changing burs. • Severe shock - Eg. Dropping the product - may cause damage. • Do not bend the Irrigation Tube while the water pump is operating. It could cause tube breakage. • Never attempt to disassemble the Control Unit, the Foot Control or the Micromotor. • Handpiece Attachments should be cleaned, lubricated and sterilized immediately after use. • Do not lubricate the Micromotor. Oil could generate excessive heat and cause damage. • The Control Unit and the Foot Control should under no circumstances be sterilized regardless of method. • The Control Unit may be cleaned with a damp cloth. Disconnect the power supply before cleaning. • Do not clean the Control Unit with any solvent solutions. • Do not disconnect the motor cord from the motor. • Make sure that the cover is not fitted during calibration. • Be sure to dispose of the irrigation tube as medical waste after use. • The system functions normally in the environment where the temperature is at 0-40 °C (32-104°F), humidity at 10-85% RH, atmospheric pressure at 500- 1060hPa, and no moisture condensation in the Control Unit. Use at outside of these limits may cause malfunction.
NOTICE • Turn off the Power Switch after each use. • Please read the Hand Piece Instruction Manual before use. • For service requirements and spare parts please contact your dealer. • The use of NSK genuine pre-sterilized, disposable Irrigation Tube Kit is recommended. • Store the system in the place where the temperature is at -10-60°C (14-140°F), humidity at 1085%RH, atmospheric pressure at 500-1060 hPa, and the system is not subject to air with dust, sulfur, or salinity.
–1–
English
1 Safety precautions prior to use
2 Package Contents
Item No.
Description
Quantity
1
Control Unit
1
2
Foot Control
1
3
Power Cord
1
4
Micromotor with Motor Cord
1
5
Irrigation Tube
5
6
Coolant Solution Hanger Post
1
7
Tube Holder
10
8
Autoclave Plug
1
–2–
English
3 Control Unit with an Irrigation Pump
Irrigation Pump
Program Key Speed Key Torque Key
Fuse Holder Micromotor Cord Jack Coolant Flow
Main Power Switch Power Cord Connection
Memory Key
Coolant Solution Hanger Post Holder
Gear Ratio Key
Foot Control Cord Jack
Forward/Reverse Key System Key
Description of Operation Keys on the Unit (1) Program key This key is used to select any one of 10 available programs. Press [+] to ascend program numbers and [- ] to descend the numbers. By pressing either [+] or [- ] the numbers rotate continuously through all available programs. (2) Speed key This key is used to set the micromotor speed. Press [+] to increase speed by one step, and [- ] to decrease speed by one step. When [+] is pressed and the speed setting reaches maximum or [- ] is pressed and the speed setting reaches minimum, an audible intermittent beep sounds, and the speed cannot be changed any further. (3) Torque key This key is used to set the torque. Press [+] to increase torque by one step and [- ] to decrease torque by one step. When [+] is pressed and the torque setting reaches maximum, or [- ] is pressed and the torque setting reaches minimum, an audible intermittent beep sounds, and the torque cannot be changed any further. The range of torque setting steps vary according to the gear ratio selected to match the handpiece attachment in use. (4) System key This key is used to calibrate the handpiece attachment before use. To activate the automatic calibration mode, connect the handpiece attachment to the micromotor and press this key. The micromotor will automatically operate for a few moments and, when it automatically stops, the handpiece attachment will be calibrated to the micromotor. (5) Gear Ratio key This key is to select match ratio of the handpiece attachment, before use, to the unit. Press this key until the LCD exhibits the correct gear ratio of the handpiece attachment. (6) Coolant Flow key This key is used to select the coolant solution flow volume. 6 flow volume rates are available for selection, plus the flow can be turned off. (7) Forward/Reverse key This key is used to change the rotational direction of the micromotor. Press this key once to change the rotational direction. (8) Memory key This key is used to memorize the program parameters set by the operator. Press this key for approx. 1 second to memorize the parameters. An audible beep confirms that new program parameters have been memorized. –3–
LCD on the unit Program Number
Gear Ratio
Forward/Reverse
Speed/Torque
Coolant flow level
Speed/Torque Bar Graph
(1) Coolant Flow Displays the selected coolant solution flow volume level. The selected flow volume level is indicated by one of 5 levels of illuminated indicators. No light indicates the coolant solution flow is off. (2) Program Number Displays the selected program number. (3) Gear Ratio Displays the gear ratio of the handpiece. (4) Forward/Reverse Indicator Displays the rotational direction of the micromotor. (5) Speed/Torque Displays the selected speed and torque. Normal speed is shown when the unit is switched on and also when a program is changed. To display speed, press the [Speed] key on the Control Unit. To display torque, press the [Torque] key on the Control Unit. When using the 1:1 direct drive or Speed Increasing Handpiece, the torque is not displayed. (6) Speed/Torque Bar Graph During operation displays an approximate percentage indication of the actual operating speed or torque relevant to the preset maximum speed or torque. When all bars illuminate, the operating speed or torque is at maximum. When bars are half illuminated then the operating speed is approximately 50% of the preset speed.
CAUTION The LCD panel is produced from liquid crystal and should always be treated with care.
–4–
English
4 Foot Control
Foot Control Cord and Plug
PRG (Program) Button
Coolant Solution Flow Volume Button
Forward/Reverse Button
Speed Control Pedal
Speed Control Pedal This pedal is used to start and stop the motor and to vary the speed during operation.
–5–
5 Installation 5-1 Connecting the Motor Cord Face the [ ] mark on the Micromotor Cord plug upward then insert the plug into the Micromotor Cord jack on the Control Unit (Fig. 1). A click is heard when the motor cord plug is correctly inserted into the control unit. To disconnect the plug, pull back the lock joint, then disconnect the cord (Fig. 2).
Fig. 1
Lock Joint
Marking
Fig. 2
5-2 Connecting the Handpiece • Please read the Instruction Manual for the relative Hand Piece and follow the instructions therein. • Insert the Motor Insert into the Hand Piece fully, then screw it firmly until it locks with a clicking sound. (Fig. 3) • To disconnect hold the motor in one hand and the Hand Piece in the other and pull straight apart.
Motor Insert
Fig. 3
5-3 Connecting the Foot Control Face the screw on the foot pedal control cord plug downward then insert the plug into the Foot Control cord jack on the control unit. Secure the plug by fastening the lock nut. See Fig. 4. Fig. 4
5-4 Connecting the Power Cord Align correctly then insert the power cord into the power cord connection at the back of the control unit (Fig. 5). Fig. 5
–6–
Mount the irrigation tube in the irrigation pump, with the irrigation tube needle facing towards the back of the unit. Position the stoppers of the tube in the guide securely. (Fig. 6)
Position
Tube Guide
Position
CAUTION
lrrigation Tube Needle End
Make sure that the tube is securely set on the rollers when closing the pump cover. If the tube is not correctly positioned on the rollers and the cover is closed, the tube could be cut or severed as a result. (Fig. 7)
Stopper
Fig. 6 Pump Roller
Pump Cover Lever
Rollers
Fig. 8
Fig. 7
Only when the tubes are correctly positioned, close the pump cover by turning the pump cover lever 180 degrees to the left. (Fig. 8)
5-6 Mounting the Coolant Solution Bottle Insert the coolant solution bottle hanger post into the holder on the Control Unit. Place the bottle as shown in Fig. 9.
Fig. 9
–7–
English
5-5 Installing the Irrigation Tube
5-7 Insertion of the Irrigation Tube
Tube Clamp
(1) Close the tube clamp, between the irrigation tube needle and the irrigation pump, as shown in Fig. 10
(2) Insert the irrigation tube needle into the bottle cap. (Fig. 11)
Fig. 10
Bottle Cap
(3) Open the tube cap to allow air into the bottle. (Fig. 12)
lrrigation Tube Needle
Fig. 11
(4) Open the tube clamp.
Tube Cap
Fig. 12
CAUTION Do not operate the irrigation pump if the tube is bent or the tube clamp is in the closed position. This could cause the tube to burst or slip out of the bottle.
5-8 Attaching the Tube Holder Use the tube holder to hold the motor cord and the irrigation tube together. For best results, first insert the motor cord and then the irrigation tube.
Motor Cord Tube Holder
Irrigation Tube
Fig. 13
–8–
English
6 Operation 6-1 Programming the Micromotor Operation The control unit can memorize 10 sets of programs. Each program includes the following functions which will be automatically performed when the appropriate program number is selected. Gear ratio of handpieces Speed Direction of rotation Torque upper limit Coolant solution flow Display selection for the speed and torque Power Switch
(1) Turn on the power by pushing the main switch toward [-]. Symbol Mark Whenever the main power switch is turned ON, program Function OFF ON number 1 is always displayed. (2) Select a program number by using either step (a) or step (b): (a) Press the [Program] key on the unit control panel until the program number you require is displayed OR (b) Press the [Program] button on the foot control until the program number you require is displayed. (3) Select the gear ratio of the handpiece relevant to the program. Press the [Gear Ratio] key, The gear ratio of the handpiece to be used is displayed. (4) Setting the speed. Set the speed by pressing the [Speed] key. -Each time this key is pressed the display changes to the next speed level. Pressing this key for more than 1 second brings the speed quickly to the next level until the speed display reaches its maximum or minimum limit. (5) Setting the torque. Set the torque upper limit by pressing the [Torque] key on the unit control panel. -Each time this key is pressed the display changes to the next torque level. Pressing this key for more than 1 second brings the torque quickly to the next level until the torque display reaches its maximum or minimum limit. (6) Select the rate of coolant solution flow volume. Select the rate of the coolant solution flow volume by pressing the [Coolant Flow] key. -The rate of coolant solution flow volume has 5 flow rate steps plus "no coolant flow". (7) Select [Speed] key or [torque] key to display the speed or torque. (8) Memorize settings. After completing steps 1-6 press the [Memory] key for more than 1 second until a long audible beep is heard. PROGRAM
SPEED
TORQUE
SPEED
TORQUE
Repeat the above steps 1-7 to program any one of the 10 available programs.
–9–
6-2 Calibration Function The Prado unit incorporates an automatic function to recognize the level of the resistance of any handpiece attached to the micromotor, and to calibrate the micromotor to rotate the handpiece attachment to the specific speed and torque settings required. (1) Attach the handpiece to the micromotor and remove the bur. (2) Press the [System] key for approx. 3 seconds until a long beep is heard. "CAL" is displayed. (3) Press the [Gear Ratio] key and select the gear ratio of the attached handpiece.
CAUTION • This equipment is optimized to obtain the highest accuracy at a gear ratio of 1/20. When using another gear ratio, please note that the accuracy decreases with an increase in the ratio relative to 1/20. • Micro saw handpiece should not be calibrated. Because the rotation speed is raised up to 40,000min-1 during calibration, it may cause a malfunction. (4) Press the [System] key again. The micromotor starts automatically. Once the brief period of impedance diagnosis is completed, the display returns to normal display mode and the micromotor will automatically stop. Calibration of the handpiece is now completed.
CAUTION • Because the handpiece starts AUTOMATICALLY, any bur must be removed from the handpiece before beginning the calibration process. Leaving a bur in the handpiece may cause harm to the operator. Care should be exercised never to add any load to a handpiece during calibration, because an incorrect diagnosis would result in incorrect torque control. • If ” FAIL” is displayed on the LCD panel, check the mounting of each part and operate again. If ” FAIL” is still displayed, contact your dealer.
6-3 Standard Operation All standard operational functions can be controlled at the foot control. (1) Turn on the main switch. (2) Select the desired program number. Step on the foot control PRG (Program) button and the program display ascends to the next program number. (3) Verify the details of the program on the display. (4) Operate the micromotor. Step on the speed control pedal in the middle of the foot control and the micromotor will start. When the coolant solution flow is programmed to operate, the pump will also automatically function. Speed increases as the pedal is depressed. When the pedal is fully depressed the speed reaches the maximum set value. (5) Activation of the torque limiter. During operation of the micromotor, when the drilling load reaches the programmed torque maximum limit the integrated torque limiter automatically activates to prevent torque application excessive to the set requirement. When the torque limiter activates, the motor stops over beeping after 5 seconds. To reactivate the micromotor, step on the foot pedals twice. (The first step-on is to release the stop condition, and the second step-on is to restart the micromotor.) (6) Stop the micromotor Release the foot control pedal, and the micromotor will automatically stop. (7) Reverse the micromotor rotational direction To reverse direction of the micromotor (and bur) simply step on the foot control Forward / Reverse button. A warning beep can be heard when the rotational direction is in reverse mode. – 10 –
English
7 Care and Maintenance 7-1 Protection Circuit An electronic circuit breaker operates automatically to protect the micromotor and the control unit if the micromotor should become overloaded. Power supply to the micromotor will automatically be terminated and the Error code will be displayed on the control unit.
Resetting the Protection Circuit. To reset the protection circuit, release and then depress the speed control pedal.
7-2 Error Code If an operational problem occurs the display shows the error code to allow an immediate problem diagnosis. Error Code Display
Error
Cause of Error
E0
System Error
• Erroneous memory. • Memory failure.
E1
Excessive Current Detected
• Extended use under heavy load. • Short circuit in the motor cord.
E2
Excessive Voltage Detected
The motor cord failure.
E3
E4
E5
E6
Motor Sensor Error
• Micromotor sensor failure (Hall IC). • Micromotor cord failure. • Signal line failure.
Remedy Request repair. Electrical contact may be insufficient. Securely re-connect the motor cord. When an error cannot be eliminated, request repair.
Ingress of water into a motor.
Request repair. Make sure to put a steam control cap when autoclaving it.
Unit Interior Over-heating Error
• Overheating by extended use under heavy load. • Operation of the unit under an extremely high temperature.
Allow it to cool down before use. To allow the heat to be adequately diffused, the periphery of the main unit should be well-ventilated wherever possible. When an error cannot be eliminated, request repair.
Braking Error
If rotation and stop are repeated in short frequencies, a circuit may be • Abnormal voltage generated in the activated which limits acceleration start / stop circuit. at start. Wait a few seconds and • Failure in the start / stop circuit. then use. When an error cannot be eliminated, request repair. • Handpiece attachment failure. • Micromotor failure.
The chuck may be opened, or may not be sufficiently closed. Securely close the chuck. When an error cannot be eliminated, request repair.
When the motor stops for more than 5 seconds after reaching the torque upper limit.
This is not a failure. The motor stops as a safety measure. After resetting the error, normal use can be continued.
Motor Rotation Failure Error
– 11 –
Error Code Display E7
Pump excess voltage
E8
Pump excess current
E9
Foot control abnormality
Remedy
Cause of Error
Error
• The irrigation tube is detached from the pump roller.
• Check the irrigation tube.
• The pump fails.
• An error code is displayed even when the irrigation tube is normal, please request repair.
Connection failure of the connector. Failure inside the foot control.
Check the connection state of the connector. The error code is displayed even when the connector is normally connected, please request repair.
7-3 Replacement of the Fuse
Fuse Box
If the control unit does not function, check the fuses. To take the fuse box out, simply press the ”nail” located on the left side the fuse box with a finger or a driver to unlock it. Insert new fuses (2 pcs) into the fuse box and then push the fuse box into the original position until hearing a sound click. Fuse (for 120V) : T3.15AL/250V Fuse (for 230V) : T1.6AL/250V (refer to Optional Accessories)
Fuse
Fig. 14
7-4 Maintenance of the Control Unit and Foot Control If blood or saline solution soil the control unit or foot control, remove the power code, wipe off the unit or foot control with a damp cloth, and wipe off with the alcohol-absorbed cloth.
8 Sterilization Autoclave sterilization is recommended. Sterilization required after each patient as noted below. The following items are autoclavable. • Micromotor with Motor Cord • Autoclave Plug • Tube Holder • Handpiece : follow the instruction manual for each.
CAUTION Do not autoclave any parts (the control unit, foot control, Power cord and irrigation tube) other than those that can be subjected to autoclave sterilization.
– 12 –
1 Remove blood and debris from the micromotor. 2 Do not attempt to spray lubricant into the micromotor. 3 Attach the micromotor autoclave plug to the micromotor. (Fig. 15 & 16) 4 Place the micromotor in an autoclave pouch (not included in the package) and seal it. 5 Autoclavable up to a max. 135°C.
ex.) Autoclave for 20 min. at 121°C, or 15 min. at 132°C.
Autoclave Plug
Fig. 15
Fig. 16
Caution for Autoclaving • Make sure the Micromotor together with the Motor Cord is placed in a sealed autoclave pouch. • Do not sterilize it by autoclave sterilization exceeding 135°C. This causes the micromotor to malfunction. • Do not use the autoclave drying cycle if the temperature at this cycle could exceed 135°C. • The irrigation tube is disposable and cannot be autoclaved.
9 Optional Accessories Part No.
Description
Z900-113
Irrigation Tube
U370-246
Tube Holder
E211-701
Autoclave Plug
U195-152
Fuse (for 120V)
U197-152
Fuse (for 230V)
10 Specifications <Control Unit>
<Micromotor>
Power Supply Voltage
AC120 / 230V 50/60Hz
Speed Range
200 - 40,000min-1 (rpm)
Power Consumption
48VA
Input Voltage
DC30V
Max. Pump Output
75mL / min.
Dimensions
ø 23 x L110mm
Dimensions
W268 x D230 x H103mm
Weight
287g (With the motor cord)
Weight
3.1kg
11 Disposing Product Please consult your dealer from whom you purchased the product, regarding the latest guidelines concerning the disposal of medical products.
– 13 –
English
Autoclave Procedure