Operation Manual
2 Pages
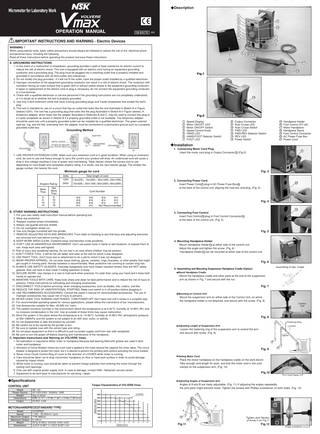
Preview
Page 1
Description
Micromotor for Laboratory Work
1 2 3
002
9
4
10
5 6 7
11 12
IMPORTANT INSTRUCTIONS AND WARNING - Electric Devices
13
WARNING ! When using electric tools, basic safety precautions should always be followed to reduce the risk of fire, electrical shock and personal injury, including the following. Read all these instructions before operating this product and save these instructions.
8
14
15
16 17
A. GROUNDING INSTRUCTIONS 1. In the event of a malfunction or breakdown, grounding provides a path of least resistance for electric current to reduce the risk of electric shock. This tool is equipped with an electric cord having an equipment-grounding conductor and a grounding plug. The plug must be plugged into a matching outlet that is properly installed and grounded in accordance with all local codes and ordinances. 2. Do not modify the plug provided - if it will not fit the outlet, have the proper outlet installed by a qualified electrician. 3. Improper connection of the equipment-grounding conductor can result in a risk of electric shock. The conductor with insulation having an outer surface that is green with or without yellow stripes is the equipment-grounding conductor. If repair or replacement of the electric cord or plug is necessary, do not connect the equipment-grounding conductor to a live terminal. 4. Check with a qualified electrician or service personnel if the grounding instructions are not completely understood, or if in doubt as to whether the tool is properly grounded. 5. Use only 3-wire extension cords that have 3-prong grounding plugs and 3-pole receptacles that accept the tool's plug. 6. This tool is intended for use on a circuit that has an outlet that looks like the one illustrated in Sketch A in Figure (below)(120V). The tool has a grounding plug that looks like the plug illustrated in Sketch A in Figure (below). A temporary adapter, which looks like the adapter illustrated in Sketches B and C, may be used to connect this plug to a 2-pole receptacle as shown in Sketch B if a properly grounded outlet is not available. The temporary adapter should be used only until a properly grounded outlet can be installed by a qualified electrician. The green-colored rigid ear, lug, and the like, extending from the adapter must be connected to a permanent ground such as a properly grounded outlet box.
Grounding Method
ADAPTER
18
19
20 21 1 2 3 4 5 6 7
Speed Display Motor ON/OFF LED Motor ON/OFF Switch Speed Control Knob HAND LED HAND/FOOT Selector Switch FOOT LED
8 9 10 11 12 13 14
Output Connector Auto Cruise LED Auto Cruise Switch FWD LED FWD/REV Selector Switch REV LED Power Switch
15 16 17 18 19 20 21
Handpiece Holder Foot Control (FC-40) Motor Handpiece Handpiece Stand Foot Control Connector AC Power Fuse Box Power Cord
METAL SCREW COVER OF GROUND OUTLET BOX GROUNDING PIN
(A)
GROUNDING MEANS
(C)
Installation
GROUNDING PIN
1. Connecting Motor Cord Plug Insert the motor cord plug in Output Connector 8 .(Fig.3)
(D)
(B)
8
7. USE PROPER EXTENSION CORD. Make sure your extension cord is in good condition. When using an extension cord, be sure to use one heavy enough to carry the current your product will draw. An undersized cord will cause a drop in line voltage resulting in loss of power and overheating. Table (below) shows the correct size to use depending on cord length and nameplate ampere rating. If in doubt, use the next heavier gauge. The smaller the gauge number, the heavier the cord.
Fig. 3
Minimum gauge for cord
Ampere Rating More Than
Not More Than
0 6 10 12
6 10 12 16
Volts 120V 240V
Total length of cord 7.5m(25ft.) 15m(50ft.) 30m(100ft.) 45m(150ft.) 15m(50ft.) 30m(100ft.) 60m(200ft.) 90m(300ft.)
2. Connecting Power Cord Insert Power Cord 21 plug in AC Power Fuse Box 20 at the back of the control unit, aligning the fuse box and plug. (Fig. 4)
20
Cord Number #18 #18 #16 #14
#14 #16 #12 #14 #12 #14 Not Recommended
#16 #16 #16 #12
Fig. 4
21
19
B. OTHER WARNING INSTRUCTIONS 1. For your own safety read instruction manual before operating tool. 2. Wear eye protection. 3. Replace cracked wheel immediately. 4. Always use guards and eye shields. 5. Do not overtighten wheel nut. 6. Use only flanges furnished with the grinder. 7. REMOVE ADJUSTING KEYS AND WRENCHES. From habit of checking to see that keys and adjusting wrenches are removed from tool before turning it on. 8. KEEP WORK AREA CLEAN. Cluttered areas and benches invite accidents. 9. DON’T USE IN DANGEROUS ENVIRONMENT. Don’t use power tools in damp or wet locations, or expose them to rain. Keep work area well lighted. 10. Risk of injury due accidental starting. Do not use in an area where children may be present. 11. DON’T FORCE TOOL. It will do the job better and safer at the rate for which it was designed. 12. USE RIGHT TOOL. Don't force tool or attachment to do a job for which it was not designed. 13. WEAR PROPER APPAREL. Do not wear loose clothing, gloves, neckties, rings, bracelets, or other jewelry that might get caught in moving parts. Nonslip footwear is recommended. Wear protective hair covering to contain long hair. 14. ALWAYS USE SAFETY GLASSES. Everyday eyeglasses only have impact resistant lenses, they are NOT safety glasses. Also use face or dust mask if cutting operation is dusty. 15. SECURE WORK. Use clamps or a vise to hold work when practical. It’s safer than using your hand and it frees both hands to operate tool. 16. MAINTAIN TOOLS WITH CARE. Keep tools sharp and clean for best performance and to reduce the risk of injury to persons. Follow instructions for lubricating and changing accessories. 17. DISCONNECT TOOLS before servicing; when changing accessories, such as blades, bits, cutters, and like. 18. REDUCE THE RISK OF UNINTENTIONAL STARTING. Make sure switch is in off position before plugging in. 19. USE RECOMMENDED ACCESSORIES. Consult the owner’s manual for recommended accessories. The use of improper accessories may cause risk of injury to persons. 20. NEVER LEAVE TOOL RUNNING UNATTENDED. TURN POWER OFF. Don’t leave tool until it comes to a complete stop. 21. For recommended operating speed for various applications, please follow the instructions of bur manufacturers. 22. Use Accessories suitable for Max. 40,000 min-1(rpm). 23. The system functions normally in the environment where the temperature is at 0-40°C, humidity at 10-85% RH, and no moisture condensation in the Unit. Use at outside of these limits may cause malfunction. 24. Store the system in the place where the temperature is at -10-60°C, humidity at 10-85% RH, atmospheric pressure at 500-1060hPa, and the system is not subject to air with dust, sulfur, or salinity. 25. Do not disassemble or alter the product by yourself. 26. Be careful not to be injured by the grinder or bur. 27. Be sure to replace fuse with the correct type and rating. 28. Do not place equipment so that it is difficult to pull cut power supply cord from rear side receptacle. 29. Be sure to turn the power off before cleaning and maintenance of the handpiece.
3. Connecting Foot Control Insert Foot Control 16 plug in Foot Control Connector 19 at the back of the control unit. (Fig. 5)
Fig. 5 4. Mounting Handpiece Holder Mount Handpiece Holder 15 at either side of the control unit. Adjust the angle and tighten the screw. (Fig. 6) *Handpiece Holder 15 can be mounted at either side of the control unit. 15
Fig. 6 Assembling of Hpc. Cradle
5. Assembling and Mounting Suspension Handpiece Cradle (Option) Mount Handpiece Cradle
Mount the handpiece cradle and other parts at the end of the suspension arm as shown in Fig. 7 and secure with the nut.
Fig. 7 Mounting on Control Unit
Mount the suspension arm on either side of the Control Unit, on which the handpiece holder is not attached, and secure with the screw. (Fig. 8) Control Unit
Fig. 8 Fastening Ring
Adjusting Length of Suspension Arm
Loosen
Loosen the fastening ring of the suspension arm to extend the arm and secure with screw. (Fig. 9) Tighten
C. Important Instructions and Warning on VOLVERE Vmax. 1. No lubrication is required to either motor or handpiece because ball bearing filled with grease are used in both motor and handpiece. 2. Activation of Circuit Breaker means too much load is applied to the motor beyond the capacity the motor takes. This circuit breaker is designed to protect the motor, but it is desired to perform the grinding work without activating the circuit breaker. 3. Never move Chuck Control Ring of Lever to the direction of LOOSEN while motor is running. 4. Care should be taken not to drop micromotor handpiece on floor or hard work surface in order to avoid damage caused by impact shock. 5. While motor is running, care should be taken to prevent foreign particles from entering the motor through the cooling vent openings. 6. Only use with original power supply cord. In case of damage, contact NSK / Nakanishi service center. 7. Equipment to be sent back to manufacturer for servicing / repair.
Specifications NE-120 AC120V/230V 50/60Hz 30W 2kg (4.44Lb) W95 (3.74") x D190 (7.48") x H180 (7.09")mm DC35V 0.6A
MOTOR&HANDPIECE(STANDARD TYPE) Model Speed Maximum Output Maximum Torque Weight Dimensions
GX35RMS 1,000 - 35,000min-1(rpm) 71W (892oz) 4.1cN-m 251g (9.35oz) (include motor cord) φ24.5 (0.96") x L143.5 (5.65") mm
Place the motor handpiece on the handpiece cradle on the work bench. Take enough cord length for work, and lock the motor cord in the cord clamps on the suspension arm. (Fig. 10)
Fig.10 Cord Clamp
Angles of A and B are freely adjustable. (Fig. 11) If adjusting the angles repeatedly, the joint parts might become loose. Tighten the screws with Phillips screwdriver on both sides. (Fig. 12)
GX35RMS Speed (min-1(rpm))
Model Power Source Weight Dimensions Output
Setting Motor Cord
Adjusting Angles of Suspension Arm
Torque Characterstics of VOLVERE-Vmax
CONTROL UNIT
Fig. 9
0.5
1.0
1.5
2.0
2.5
Torque (cN-m)
3.0
3.5
4.0
4.5
5.0
Tighten Joint Section of Arrow C on Fig.11
Fig.11
Fig.12 Philips screwdriver
4. Replacing Carbon Brush
Operation Procedures (1) Insert Power Cord 21 plug into an outlet. (2) Make sure that Speed Control Knob 4 is set to the lowest position. (3) Turn on Power Switch 14 , and check if Speed display 1 shows. (4) Select either forward or reverse direction by FWD/REV Selector Switch 12 . Every pressing alternates FWD and REV. (5) Select either hand or foot operation by HAND/FOOT Selector Switch 6 . Every pressing alternates HAND and FOOT.
After (1)-(4) operations above, go to the following procedures. (5) Select hand operation by HAND/FOOT Selector Switch 6 . (HAND LED 5 lights.) (6) To operate Motor Handpiece 17 , press Motor ON/OFF Switch 3 . (Motor ON/OFF LED 2 lights.) (7) Adjust the rotation speed by turning Speed Control Knob 4 . (8) To stop Motor Handpiece 17 , press Motor ON/OFF Switch 3 . (Motor ON/OFF LED 2 stops lighting.)
Operation-2
*Carbon Brush for GX35RM/GX35EM (Pack of 2) : Order No. E023-011S Handpiece
Cautions in connecting the handpiece and the motor
Motor
If the drive shaft of the motor does not engage the drive dog on the handpiece,do not force them to turn. It would break the motor. Turn the handpiece back a few threads, rotate the collet chuck or the tool by hand to engage the drive shaft and the drive dog. Screw them together firmly.
Operation-1 Manual Operation
Transmission Clutch
To replace carbon brushes, refer to “Replacing Carbon Brush” of the operation manual in the package of new carbon brush.
1 2 3 4 5 6
Fig.20
Handpiece Stand The service tool and the collet chuck can be mounted on the bottom of the handpiece stand.(Fig. 21)
12 14
Troubleshooting
Foot Control Operation After (1)-(4) operations above, go to the following procedures. Fig.13 (5) Select foot operation by HAND/FOOT Selector Switch 6 . (FOOT LED 7 lights.) (6) To operate Motor Handpiece 17 , apply pressure to Foot Control 16 . (7) Adjust the maximum speed by turning Speed Control Knob 4 . The rotation speed can be adjusted by foot up to the maximum speed, that is preset by Speed Control Knob 4 . (Variable operation) (8) To stop Motor Handpiece 17 , stop applying pressure to Foot Control 16. *Auto Cruise Mechanism To operate Motor Handpiece 17 at a constant speed below the maximum speed preset by Speed Control Knob 4 , press Auto Cruise Switch 10 when the motor handpiece rotates at the required speed. Auto Cruise LED 9 lights and the rotation speed would not change even if the foot Control is released. To cancel auto cruise operation, press Auto Cruise Switch 10 or Foot Control 16 once again.
Caution
Fig.21
Check followings before requesting repair. Trouble
LED Speed Display does not show.
Probable Cause
Action Taken
Power Cord is disconnected.
Insert Power Cord Securely.
Blown fuse.
Replace a fuse of same rating. If the cause of blown fuse is unknown, ask for inspection.
Faulty Power Switch.
Ask for repair.
Foot Control is loose or disconnected.
Connect Foot Control cord securely.
HAND/FOOT Selector Switch is set to HAND.
Set to FOOT.
The chuck control lever or the bur lock ring is in open position. Check if the tool can be rotated with fingers. If you have another motor and motor cord, use them and check the operation.
Lock the chuck control lever or the bur lock ring. If any abnormalities are found during rotation, ask for motor & handpiece repair. If replaced motor operates normally, original motor and motor cord are faulty. Ask for repair.
Motor rotates at high speed.
Ask for control unit repair.
Motor does not rotate.
Ask for control unit repair.
Foot Control does not turn on motor.
Error code E0 shows.
Error code E1 shows.
Make sure that the chuck control lever or the bur lock ring is at lock position when starting the motor handpiece.
Speed Control Knob or PC Board might be faulty. Ask for control unit repair.
Error code E2 shows.
Protective Circuit
Error code E3 shows.
Set HAND/FOOT Selector Switch to HAND and check the operation.
Speed Control Knob or PC Board might be faulty. Ask for control unit repair.
When the control unit is overloaded or the motor is to operate in spite of the chuck control lever or the bur lock ring is in open position, the protective circuit functions to stop the motor and Speed Display 1 shows error codes. To reset the protective circuit,
Error code E6 shows.
Stop operation for approximately 10 minutes in a cool place and check the operation again.
There is no problem if it operates normally. Make sure that it is not hot in the surroundings and storage location. If the error code frequently shows, ask for control unit repair.
Error code E7 shows.
Repeat starting and stop by Power Switch.
There is no problem if it operates normally. If the error code still shows, ask for control unit repair.
Error code E8 shows.
Repeat starting and stop by Power Switch.
If the error code still shows, ask for control unit repair.
Error code E9 shows.
Check if the tool can be rotated with fingers.
If the tool does not rotate normally, ask for motor and handpiece repair.
The speed cannot be increased.
The max speed can be set with Speed Control Knob in Foot Control operation mode.
Set Speed Control Knob to the max speed.
・ At manual operation, press Motor ON/OFF Switch 3 . ・ At foot control operation, release Foot Control 16 .
Error Code When the motor stops operation, Speed Display 1 shows error codes, which instruct what is problem.
Detection of overcurrent
・ Long-time use at excessive load (Overcurrent). ・ Short-circuited power cord. ・ Handpiece trouble. ・ Short-circuited motor winding. ・ Open collet chuck.
Problem
Cause
No rotation when the chuck control lever or the bur lock ring is locked.
Foreign objects inside the ball bearings, or bearings frozen.
Ask for repair.
Foreign objects inside the ball bearings could have worn ball bearings.
Ask for repair.
Detection of overvoltage
Faulty PC Board.
Overheating during rotation.
Detection of discontinuity in Speed Control Knob 4
No signal from Speed Control Knob 4 .
Vibration and/or noise during rotation.
Detection of discontinuity in Foot Control 16
No signal from Foot Control 16 .
Overheating inside the control unit
Long-time use at excessive load built up heat inside the control unit.
Breaking circuit error
・ Abnormal voltage in the starting or the shut-down circuit. ・ The starting or the shut-down circuit trouble.
Heavy tool run-out.
EEPROM abnormal
Internal memory faulty.
Rotor lock error
Faulty PC Board.
Tool walks out.
Worn ball bearings caused by the foreign objects.
Ask for repair.
Bent tools.
Replace tool.
Debris inside the collet chuck or inside the spindle.
Clean inside the collet chuck or the spindle.
Worn collet chuck.
Replace collet chuck.
Worn ball bearings.
Ask for repair.
Loose collet chuck.
Tighten collet chuck securely. (See
Product
Cat.# E205
Replacing AC Power Fuse There is a fuse in AC Power Fuse Box 20 . Push links at the either side of the fuse case and remove to check. If the fuse is blown, replace with a new fuse of same rating. (AC120V: 3.15AH 125V) (AC230V: T800mAH 250V) (Fig. 14)
Fig.14 Caution LOCK
OPEN
Fig.15
Handling Motor and Handpiece 1. Replacing Tool
Handling Motor and Handpiece.)
Optional Micromotor Handpieces series and spare parts
Refer to Troubleshooting for action taken when the error code shows.
Fuse is burned out when a short circuit occurs or when over-voltage flows into the primary current source. If the cause is uncertain, return the product to an authorized NSK's service shop for inspection.
Action Taken
OPEN
a.) Ring type handpiece To unlock the collet chuck and remove the tool, turn the bur lock ring to OPEN with a click. To tighten the collet chuck and mount the tool, turn the bur lock ring to LOCK with a click. (Fig. 15)
E053
GX35M & SCD For Lever Type Handpiece Standard Motor with Straight Motor Cord
E054
GX35EM & SCD E-Type Motor with Straight Motor Cord
H214
UHR-35 Ring Type Handpiece for GX35RM
H063
VH Lever Type Handpiece for GX35M
H068
VH-E E-Type Lever Type Handpiece for GX35EM
H178
VR-E E-Type Ring Type Handpiece for GX35EM
H156
VC45 Angle Type Handpiece for GX35M
E023-011S
Carbon Brush
H203-180
CHH2.35 φ2.35 chuck
E257-012
GX35SCD Straight Motor Cord
E257-013
GX35CCD Coiled Motor Cord
LOCK
b.) Lever type handpiece To unlock the collet chuck and remove the tool, make a quarter turn of the chuck control lever to OPEN. To tighten the collet chuck and mount the tool, turn the chuck control lever back to LOCK. (Fig. 16)
Fig.16
Z246
2. Cleaning and Replacing Collet Chuck
Model / Description GX35RM & SCD For Ring Type Handpiece Standard Motor with Straight Motor Cord
Vmax Handpiece Cradle
Loosen
(1) Removal of Chuck To remove the chuck, open the bur lock ring or the chuck control lever and turn the chuck counterclockwise with the provided spanner wrench. (Fig. 17) (2) Cleaning of Chuck Remove and clean the chuck as frequently as possible in the ultrasonic cleaner. Clean at least once a week.
Fig.17
Caution Neglecting to clean the chuck for a long time is very dangerous because wax, gypsum, etc., accumulate in the chuck and the bur is caught insecurely, causing runout.
Turn until snug
(3) Insertion of Chuck Thinly apply oil before insertion. Open the bur lock ring or the chuck control lever, insert the dummy bur or the bur in use into the chuck, and turn the chuck clockwise by hand until it stops. Then, lock the bur lock ring or the chuck control lever, and the chuck could hold the bur securely. (Fig. 18)
3. Connecting and Disconnecting Motor Cord and Motor To remove the motor cord, loosen the joint nut at the back of the motor. To connect, align the + marks of the motor and the joint nut. Insert the pins completely and tighten the joint nut. (Fig. 19) *If connecting inversely, the motor will run in the reverse direction.
Fig.18 molded + markings
molded + markings
Joint Nut
Fig.19
2013.08.20 005 M