Ohio Medical Corporation
care-e-vac3 Portable Suction Operator Manual
Operator Manual
16 Pages
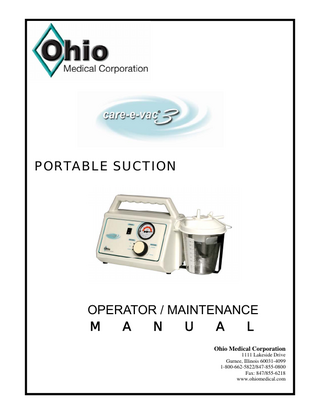
Preview
Page 1
PORTABLE SUCTION
OPERATOR / MAINTENANCE M A N U A L Ohio Medical Corporation 1111 Lakeside Drive Gurnee, Illinois 60031-4099 1-800-662-5822/847-855-0800 Fax: 847/855-6218 www.ohiomedical.com
Page 2 The care-e-vac®3 is a portable medical aspirator to suction fluids or foreign bodies from a patient. The medical device may be powered by a 110 VAC outlet or 12 VDC source. It is equipped with an internal battery. The primary intended use of the care-e-vac 3 is to aspirate saliva, mucous, vomitous or other aspirant from the mouth and or airway to allow adequate respiration or ventilation of the patient. Dual power capabilities of the care-e-vac®3 is ideal for the following applications: ● ● ● ● ●
Hospital crash cart suction Patient transport Surgi-center backup suction Emergency medical service Home health care/nursing homes
The care-e-vac®3’s suctioning capabilities are generated by a diaphragm pump. It comes equipped with a disposable in-line hydrophobic filter, 14” of tubing, and a disposable 800 cc collection canister. This manual covers the care-e-vac®3 in the following sections: I.
Definitions and Symbols Legend
Page 3
II.
Instructions for Use
Page 4
III.
Maintenance
Page 5
IV.
Troubleshooting / Removal of Service Components
Page 8
V.
Device Specifications
Page 9
VI.
800 cc Canister Instructions
Page 10
VII.
OSHA Hazard Communications Standard
Page 11
VIII.
Warranty
Page 12
IX.
Accessories
Page 13
X.
Service Parts
Page 13
XI.
EMC Information
Page 14
XII.
Environmental Conditions
Page 14
XIII.
General Warnings and Cautions
Page 14
XIV.
Electromagnetic Compatibility Declarations
Page 15
For additional information, please contact Ohio Medical Corporation Customer Service Department at 800-662-5822 or your local Ohio Medical Dealer.
Ohio Medical Corporation, 1111 Lakeside Drive, Gurnee, Il 60031-4099 (800) 662-5822-Fax: (847) 855-6218 www.ohiomedical.com -– 550542 (Rev.2) 02/2007
Page 3 CAUTION: Federal law restrict this device to sale or distribution by an order of a licensed medical practitioner. This device should be used only by qualified medical personnel properly trained in medical suction techniques and in the operation of suction equipment. Improper use may cause injury. This operation manual should be read prior to the operation of this device. WARNING: POSSIBLE EXPLOSION HAZARD IF USED IN THE PRESENCE OF FLAMMABLE ANESTHETICS. I.
Symbols Legend HIGH VACUUM HIGH FLOW
=
High vacuum, high flow
=
Pump ”Off”
=
Pump ”On”
=
Type B Applied Part
=
Fully charged battery
=
Low battery
=
Connected to AC power
=
Attention-Consult Accompanying Documents
Decrease Vacuum
Increase Vacuum
+
LED Lights The care-e-vac®3 has been equipped with a set of three LED lights, which indicate the current status of the battery. Green Light = OK. The unit will operate at its maximum performance. WARNING: Red Light = LOW. The unit will continue to operate for less than 10 minutes and should be recharged immediately. Amber Light = CHARGING / AC. Unit is properly connected to the power source. This light will remain illuminated as long as the unit is connected to the power source.
Ohio Medical Corporation, 1111 Lakeside Drive, Gurnee, Il 60031-4099 (800) 662-5822-Fax: (847) 855-6218 www.ohiomedical.com -– 550542 (Rev.2) 02/2007
Page 4 II. INSTRUCTIONS FOR USE Please perform the following initial tests to ensure that your care-e-vac®3 is in good working order and that no damage has occurred during shipment. A) Preliminary Check 1. Visually inspect unit for physical damage that may have occurred during shipping. 2. Start without A/C power, depress the “VAC” switch to turn the unit ON ☼ and listen to verify the pump starts and that the Green LED is on. If the red LED illuminates, recharge the battery per instructions in section II.C, Recharging Battery. 3. Occlude the vacuum port with your fingertip and adjust the regulator knob. Verify that the gauge reflects a change in vacuum level while turning the regulator knob. Also, verify the presence of vacuum at your fingertip. Adjust the regulator to full vacuum ensure the gauge indicates “FULL VAC”. 4. Connect the AC power cord to the proper electrical outlet. Verify that the unit is charging by ensuring the Amber LED is on. 5. The bottle bracket is adjustable to accept any collection device up to 1200 cc. The bottle bracket can be adjusted by placing the unit on its side and locating the plastic clamp, which secures the bracket. Using a Phillips head screwdriver, loosen (DO NOT REMOVE) the screws and adjust the bracket to the desired position. Retighten the screws. The care-e-vac®3 is designed to use any size collection device up to 1200 cc. However, if you are not using an Aeros disposable collection canister, make sure the collection device being used is equipped with a SAFETY OVERFLOW MECHANISM to protect the pump from accidental overflow. Ensure that you have the appropriate collection device, suction tubing and aspirator tip (catheter) for patient use. The care-e-vac®3 is now ready to be used. B) Operating Instructions 1. Check the battery level by turning the unit on and verifying that the “OK” Green LED illuminates. Turn the unit off. 2. Ensure that the hydrophobic filter is in-line between the vacuum port of the care-evac®3 and the vacuum port on the collection bottle. If using another canister that comes with a built-in filter, do not use external inline filter. Also, confirm the aspirating tip is connected to the patient port on the collection bottle. 3. Turn the care-e-vac®3 on and occlude to set, pinch the patient tubing closed, to adjust the vacuum to the desired vacuum level by using the vacuum regulator knob. Set the vacuum level to the least amount of vacuum necessary to properly suction the patient.
Ohio Medical Corporation, 1111 Lakeside Drive, Gurnee, Il 60031-4099 (800) 662-5822-Fax: (847) 855-6218 www.ohiomedical.com -– 550542 (Rev.2) 02/2007
Page 5 4. Release the pinched tubing and proceed with the suction procedure. CAUTION: When operating unit in battery mode, the user must monitor the LED’s to ensure enough battery power is left to finish procedure. C) Recharging Battery 1. To recharge the battery, plug the AC power cord into its respective electrical outlet. Verify the Amber LED is on. Charging times varies depending on the condition of the battery. 2. It is recommended to discharge the battery down to almost no charge 2 times a year to optimize your battery performance and life. D) Processing and Cleaning Instructions 1. WARNING: Please discard all contaminated parts after any suctioning procedure according to law, region / national, or your hospital policy requirements for the disposition of hazardous waste materials. These components may include the connection canister, in-line hydrophobic filter, and all suction tubing. 2. Wipe the surface of the unit clean with a mild antiseptic and a clean soft cloth. Do not allow any cleaning solution to spill into the vents on the unit. 3. Turn unit on to check the condition of the battery. If the “LOW” Red LED illuminates, recharge the battery. Verify the unit can regulate to “FULL VAC” as outlined in section II.A.3 4. Place a new collection canister, suction tubing and filter with the care-e-vac®3. III. Maintenance WARNING: Never disassemble the care-e-vac®3 when the power cord is connected to an electrical outlet. To access the internal components of the care-e-vac®3 , place the unit right side up and remove the six (6) (Philips) screws located on the back side of the unit. Slide the two front and back covers away from each other. A) Pump Cleaning The heart of the care-e-vac®3 is a diaphragm pump. Over time, foreign particles may accumulate on the internal parts from aerosolized aspirant. It is recommended that the pump head be disassembled and cleaned when a decrease performance is noticed. Preventative maintenance is recommended every six months depending on frequency of use. WARNING: Remove device from A/C power source prior to cleaning. Ohio Medical Corporation, 1111 Lakeside Drive, Gurnee, Il 60031-4099 (800) 662-5822-Fax: (847) 855-6218 www.ohiomedical.com -– 550542 (Rev.2) 02/2007
Page 6 1. Disconnect the pump wires from the printed circuit board (PCB), then disconnect all tubing from the pump output elbow. 2. Remove the three (3) (phillips) screws from the vibration bumpers. Also, remove the four (4) screws located on top of the pump head. Remove the pump head. This will expose the diaphragm. 3. Using a mild soap solution, wash the surface of the diaphragm. DO NOT allow any solution to ingress to the diaphragm and into the pump chamber.
CAUTION: Never flush your pump with any liquid solution, as this may damage your pump.
Wash the underside of the pump head with the same soap solution as used on the diaphragm. 4. Thoroughly dry with a soft cloth. Next, reassemble the pump head, reinstall, and tighten the four screws. Reconnect the pump wires to the PCB and all tubing to the pump and regulator and follow reverse order of disassembly. Ensure that your unit performs according to the Device Specifications Section. B) Vacuum Regulator Cleaning The suction regulator may accumulate aspirant after the pump has been in service for an extended period of time. When disassembling the pump for cleaning, it is suggested that the regulator also be cleaned as a preventative measure. 1. Remove the regulator by disconnecting the silastic tubing and loosen the locknut (make note of the orientation of all tubing and the regulator body). 2. Disassemble the regulator and wash all parts with a mild soap solution. Wipe all parts thoroughly dry with a piece of cotton cloth before reassembling the regulator. Reinstall and reconnect the tubing. C) Battery Replacement / Maintenance CAUTION: If the device is not to be used for long periods of time, the battery should be removed to prevent damage to the battery and device. CAUTION: To ensure the proper life of the battery, please follow the steps provided below. WARNING: Remove device from A/C power source prior to changing. Risk of Electric Shock.
A number of factors may affect the life of the battery, such as the frequency of use, the frequency of charging, proper battery maintenance and mechanical abuse. Ohio Medical recommends changing the battery every 3 years, depending on the frequency of use. Ohio Medical Corporation, 1111 Lakeside Drive, Gurnee, Il 60031-4099 (800) 662-5822-Fax: (847) 855-6218 www.ohiomedical.com -– 550542 (Rev.2) 02/2007
Page 7 Inability to retain a charge is the most detectable sign of a deteriorated battery. 1. If unit is plugged in to AC outlet, remove from AC outlet. Disconnect wires from the battery terminals. Disconnect wire harness from power supply (see diagram below). When re-connecting ensure that BLACK wire is connected to the BLACK terminal (-) and the RED wire is connected to the RED terminal (+). Turn on the switch and verify IDT Connector
that the pump will run to ensure proper placement of the battery wires. In addition, make sure IDT connector is placed in correct position. 2. Note the orientation of the battery being replaced. D) WARNING: Decontamination In the event that contaminated fluids have ingressed beyond the hydrophobic filter, follow the procedure outlined below. In addition, always use proper protective gear (i.e. rubber/ latex gloves, goggles, etc.) when in contact with contaminated parts: 1. Remove the device from the AC power source prior to cleaning and clean the interior of the chassis. 2. Disconnect the battery from the PC board to prevent damaging the PC board. 3. Disinfect the unit using a mild surface disinfectant, such as a 10:1 mixture of water and bleach. 4. Depending on the amount of contamination ingression within the pump system, remove and replace, or clean, all affected components. a. Items that can be cleaned: Housing, Gauge and Regulator b. Items that must be replaced if exposed to fluids and contaminates: Tubing, Control Circuit, Power Supply, Pump, Switch. 5. Should the care-e-vac3 reach the end of it’s usefull life, ensure unit is disposed of in
Ohio Medical Corporation, 1111 Lakeside Drive, Gurnee, Il 60031-4099 (800) 662-5822-Fax: (847) 855-6218 www.ohiomedical.com -– 550542 (Rev.2) 02/2007
Page 8 IV. TROUBLESHOOTING PROBLEM
CAUSE
Pump does not turn on 1. Battery is not charged. when the "VAC" switch 2. Faulty electrical connections. is depressed. 3. Damaged power supply or control board. 4. Pump is non-operational. 5. Blown fuse
Low or no vacuum on running unit.
6. Battery wires are on wrong terminals. 1. Improper tubing connection or crimped tube in the system. 2. Mechanical shut-off is activated in the collection canister. 3. Regulator is dirty. 4. Faulty pump. 5. Collection canister improperly installed or defective.
Battery will not hold a charge
1. Battery is old and cannot retain a charge. 2. Blown fuse 3. Faulty control board.
Gauge does not register vacuum level.
CORRECTION 1. Charge battery. 2. Make sure that all wires are secured tightly on the lugs and the lugs themselves are secured on the terminals. 3. Replace appropriate component. 4. Replace the pump. 5. Replace the power supply and / or fuse* on control board. 6. Switch battery wires to proper terminals (follow steps in section III.C.1). 1. Check all external vacuum parts for crimped tubing. If still no vacuum, check all internal tubing connections. 2. If the mechanical shut-off has been activated on a full canister, replace the canister. 3. Clean per the Vacuum Regulator Cleaning section. 4. Clean the pump per the Pump Cleaning Section or replace pump. 5. Check canister for any cracks. Verify that all ports on the canister lid are tight. 1. Replace battery per Battery Replacement section. 2. Replace power supply and / or fuse* on control board. 3. Replace control board.
1. Gauge is either not connected or is 1. Check that tubing is properly connected faulty. between vacuum regulator and gauge. 2. Blockage in vacuum lines. 2. Ensure the vacuum regulator is not completely turned off and that there are no obstructions in the line.
accordance with all local, federal, and/or hospital policy requirements. Proper disposal of contaminated components will significantly minimize the risk of patient and/or user exposure. A) Removal of service components: 1. Pump: Follow directions outlined in pump cleaning - Section III.A. 2. Power Supply: Remove power supply from back housing using standard Phillips head screw driver by removing the four screws holding it in place.
*Warning: Replace fuse with 5mm x 20mm, 6.3A 250V fast acting fuse only. Using incorrect fuse may cause significant damage to equipment or system, and may cause a fire.
Ohio Medical Corporation, 1111 Lakeside Drive, Gurnee, Il 60031-4099 (800) 662-5822-Fax: (847) 855-6218 www.ohiomedical.com -– 550542 (Rev.2) 02/2007
Page 9 3. Control Circuit: Remove control circuit from control bracket using a #2 Phillips head screw driver. 4. Battery: Follow directions outlined in Battery Replacement – Section III.C. 5. Gauge: Back out positioning screws from gauge bracket. Once gauge bracket is loose, hold both gauge and bracket and turn gauge counter-clockwise to remove. 6. Canister Bracket: Remove all six (6) cover screws and slide covers apart. Loosen screws that hold bracket in place. Slide bracket out and replace with new bracket. 7. Silencer: Remove all six (6) screws and slide covers apart. Unscrew silencer from pump using a 3/8” box wrench. 8. Regulator: Follow directions outlined in vacuum regulator cleaning – Section III.B. V.
Device Specifications PUMP 12 VDC oil-less diaphragm type PERFORMANCE Vacuum Range: Free Air Flow:
0 to 580 mmHg [0-21.7 inHg] 50 lpm [1.8 cfm] for 60 minutes
CONTROLS Vacuum Regulator: Vacuum Gauge:
Rotary type on panel Calibrated to 0-500 mmHg [20 mmHg]
BATTERY Type: Capacity: Average Run Time:
Rechargeable sealed lead acid 12V, 5 A-Hr When fully charged 50 lpm [1.8 cfm] for 60 minutes
Charge Time:
6 hours or less to 85% charging, depending on initial charge 8 hours full charge time 110 VAC outlet
Charge Method: COLLECTION DEVICE Canister: shut-off
800 cc disposable plastic with mechani-
ISO 13485
cal
(1200 cc version is also available) FM 33489
Ohio Medical Corporation, 1111 Lakeside Drive, Gurnee, Il 60031-4099 (800) 662-5822-Fax: (847) 855-6218 www.ohiomedical.com -– 550542 (Rev.2) 02/2007
Page 10 VI.
800 cc Suction Canister System Operating Instructions
1. Place lid on canister and press firmly around entire perimeter. Check to determine if the lid has been sealed properly by letting your fingers walk around the edge twice in order to BE certain the lid has been sealed on all sides. 2. Detach the pouring spout cover from the side of the lid, place it firmly and secure it on the pouring spout port. 3. Tubing is attached directly to the patient and vacuum ports. Check tubing for a snug fit. 4. Prior to use, check all points of closure one more time and test the assembly for vacuum leaks by turning on the vacuum source and occluding the patient tubing. 5. WARNING For Disposal: a. Disconnect tubing. b. Seal vacuum and patient ports with attached port covers. c. Transport to disposal area with all openings sealed. d. At disposal area, remove pour spout cap and pour contents from canister. e. To discharge, either replace pour spout cap and dispose of it sealed or remove the lid and nest the canister for transport.
Ohio Medical Corporation, 1111 Lakeside Drive, Gurnee, Il 60031-4099 (800) 662-5822-Fax: (847) 855-6218 www.ohiomedical.com -– 550542 (Rev.2) 02/2007
Page 11 VII. OSHA Hazard Communications Standard
OSHA HAZARD COMMUNICATION STANDARD 29CFR Section 1910.1200 OSHA BLOODBORNE PATHOGEN STANDARD 29 CFR Section 1910.1030
Dear Customer: The Code of Federal Regulations (CFR) requires us to inform our customers who utilize our products in processes which contaminate them with either radioactive, biological, toxic or hazardous chemical substances, the following information: Our facility does not have the ability to properly identify all the possible hazardous substances which could be present in our products returned for service. Since we can not properly identify all hazards, we do not have the protective equipment and means to safely repair these products when returned for service. Therefore, if product has been contaminated with radiological, biological, toxic or hazardous chemical substances, we can not accept it for service at any of our facilities. Prior to the return of used product a request for a Security Declaration form is required. This form is filled out and sent back with the used product. This declaration informs the service department that the product returned, possesses no health or safety risks due to contamination by radioactive material, biological substances or hazardous chemicals. If there are any questions pertaining to this subject, please call our Customer Service Department at (800) 662-5822. Thank you for your cooperation. OHIO MEDICAL CORPORATION 1111 Lakeside Drive Gurnee, Illinois 60031
Ohio Medical Corporation, 1111 Lakeside Drive, Gurnee, Il 60031-4099 (800) 662-5822-Fax: (847) 855-6218 www.ohiomedical.com -– 550542 (Rev.2) 02/2007
Page 12 VIII. WARRANTY
OHIO MEDICAL CORPORATION warrants its Portable Suction Machines to be free from any defects in workmanship and materials as of the date they are shipped to the original purchaser. For a period of three (3) years from the date on which the same shall have been delivered to the original purchaser, OHIO MEDICAL CORPORATION will repair or replace at its sole discretion any PORTABLE SUCTION MACHINE which is proven to be defective in either workmanship or material. All warranty determinations will be made by OHIO MEDICAL CORPORATION, and its responsibility shall be limited to providing in its sole discretion, new or similar rebuilt replacement parts to replace any component part found to be defective within the three year period. This warranty covers only failures due to defects in workmanship or materials, which occur during normal use. It does not cover failures due to damage, which occurs in shipment, or failures, which result from accident, misuse, abuse, neglect, mishandling, alteration, misapplication, or damage that may be attributable to acts of God. Similarly this warranty does not apply to units that are re-sold or rented to others by the original purchaser. This warranty gives you specific rights. You may have other rights, which may vary from state to state. To obtain service within the three year period, first contact your authorized OHIO MEDICAL CORPORATION dealer or OHIO MEDICAL CORPORATION Customer Service Department. Before returning any unit to the factory proper return authorization must first be obtained from the OHIO MEIDCAL CORPORATION Customer Service Department. Labor to repair any unit proved to be defective within the three year period will be provided at no charge for any unit returned to our factory adequately packaged and insured with shipping costs prepaid. Standard surface freight shipping costs to return the unit to the original purchaser will be paid by OHIO MEDICAL CORPORATION. Any product returned must be free from contamination by toxic or hazardous substances in accordance with OSHA HAZARD COMMUNICATION STANDARD 29 CFR, Section 1910.1200 and OSHA BLOOD BORNE PATHOGEN STANDARD 29 CFR, Section 1910.1030. Decontamination of items prior to their return is the responsibility of the customer. In the event a returned item is found to be contaminated, it shall be regarded as regulated waste and disposed of and no credit for the item shall be issued to the customer. THIS WARRANTY IS EXPRESSLY IN LIEU OF ANY OTHER WARRANTIES, EXPRESS OR IMPLIED, INCLUDING ANY WARRANTY OF MERCHANTABILITY OR FITNESS FOR A PARTICULAR PURPOSE. OHIO MEDICAL CORPORATION SHALL NOT BE LIABLE FOR INCIDENTAL, COLLATERAL, CONSEQUENTIAL OR SPECIAL DAMAGES. Outside of the United States, a different warranty may apply. For details please contact your authorized Ohio Medical Corporation dealer or the Customer Service Department.
550119 (Rev.3) 08/2005
Ohio Medical Corporation, 1111 Lakeside Drive, Gurnee, Il 60031-4099 (800) 662-5822-Fax: (847) 855-6218 www.ohiomedical.com -– 550542 (Rev.2) 02/2007
Page 13 IX. ACCESSORIES Part Number
Description
749144
REPLACEMENT SEALED LEAD ACID BATTERY
AI4080000
CANISTER, COLLECTION, 800cc
AI4080010
CANISTER ONLY REPL. KIT, 800 cc, LID INCL., PACKAGE OF 10
AI4080025
CANISTER ONLY REPL. KIT, 800 cc, LID INCL, PACKAGE OF 25
AI4120000
CANISTER, COLLECTION, 1200 cc
AI4120010
CANISTER ONLY REPL. KIT, 1200 cc, LID INCL., PACKAGE OF 10
AI4120025
CANISTER ONLY REPL. KIT, 1200 cc, LID INCL., PACKAGE OF 25
7551102
FILTER, HYDROPHOBIC W/ 14” TUBING
751150
KIT, HYDROPHOBIC FILTER/TUBING
749002
TIP, YANKAUER SUCTION
750810
KIT, 800 cc ASPIRATING CHANGE-OUT, CASE OF 10
750825
KIT, 800 cc ASPIRATING CHANGE-OUT, CASE OF 25
749003
TUBING, CONNECTING 72”, 1/4" ID
X. SERVICE PARTS PART#
DESCRIPTION
QTY
758035
Pump, 12 VDL
1
751106
Power Supply
1
758052
Control Circuit
1
749144
Battery, 5 Ampere-Hour
1
754041
Gauge, 0-500mm Hg
1
758001
Bracket, Canister
1
758032
Silencer
1
736050
Regulator
1
WARNING: The use of accessories, service parts, and/or cables, other than those listed above, my result in increased electromagnetic emissions and/or decreased electromagnetic immunity of the equipment or system.
Ohio Medical Corporation, 1111 Lakeside Drive, Gurnee, Il 60031-4099 (800) 662-5822-Fax: (847) 855-6218 www.ohiomedical.com -– 550542 (Rev.2) 02/2007
Page 14 XI.
EMC Information: The care-e-vac®3 device meets the following EMC/EMI requirements for medical devices: IEC 60601-1-2 CAUTION:
XII.
Medical electrical equipment needs special precautions regarding EMC and needs to be installed an put into service according to the EMC information provided in the accompanying documents. Portable and mobile RF communications equipment can affect medical electrical equipment. (See page 16)
Environmental Conditions: Specifications:
XIII.
Storage Temperature Range: Storage Relative Humidity Range: Pressure:
-40ºC to 60ºC (-40˚F to 140˚F) 40% to 70% Non-Condensing 50-106 kPa
Operating Temperature Range: Operating Relative Humidity:
-20ºC to 50ºC (-4oF to 122˚F) 95% Non-Condensing
General Warnings 1. To reduce the risk of electric shock, do not remove cover. Refer servicing to qualified personnel. 2. Risk of fire. Replace fuse as marked. 3. To insure proper grounding reliability, connect to "HOSPITAL GRADE" receptacle or equivalent. 4. The care-e-vac®3 device is powered by a 120 VAC source or by a 12 VDC battery. Disconnecting main source 120 V does not disconnect battery.
XIV.
Battery Recycling and Disposal A used battery is a valuable resource. Insulate the battery terminals and dispose the battery by taking it to a battery recycling center.
Ohio Medical Corporation, 1111 Lakeside Drive, Gurnee, Il 60031-4099 (800) 662-5822-Fax: (847) 855-6218 www.ohiomedical.com -– 550542 (Rev.2) 02/2007
Page 15 XIV. Electromagnetic Compatibility Declarations for care-e-vac 3 Guidance and Manufacturer's Declaration - Electromagnetic Emission's The care-e-vac 3 is intended for use in the electromagnetic environment specified below. The user of the care-e-vac 3 should assure that it is used in such an environment. Emissions Test Compliance Electromagnetic Environment- Guidance The care-e-vac 3 uses RF energy only for its internal function. Therefore, it's RF emissions are very low and are not likely to cause any RF Emissions interference in nearby electronic equipment. Group 1 CISPR 11 RF Emissions CISPR 11 Harmonic Emissions IEC 61000-3-2 Voltage Fluctuations/ Flicker Emissions IEC 61000-3-3
Class B
The care-e-vac 3 is suitable for use in all establishments, including domestic establishments and those directly connected to the public lowvoltage power supply network that supplies buildings used for domestic purposes.
Class A Complies
Guidance and Manufacturer's Declaration - Electromagnetic Immunity The care-e-vac 3 is intended for use in the electromagnetic environment specified below. The user of the care-e-vac 3 should assure that it is used in such an environment. Immunity Test
IEC 60601 Test Level
Electromagnetic Environment- Guidance
Compliance Level
±6 kV contact ±6 kV contact Floors should be wood concrete or ceramic tile. If the floors are covered with synthetic material, the relative Electrostatic ±8 kV air humidity should be at least 30%. Discharge (ESD) IEC ±8 kV air 61000-4-2 ±2 kV for power supply Mains power quality should be that of a typical commercial or hospital environment. ±2 kV for power Electrical Fast lines supply lines Transient/Burst ±1 kV for input/output ±1 kV for input/output IEC 6100-4-4 lines lines Surge ±1 kV line(s) to line(s) ±1 kV line(s) to line(s) Mains power quality should be that of a typical commercial or hospital environment. IEC 6100-4-5 ±2 kV line(s) to earth ±2 kV line(s) to earth Voltage Dips, short <5% U t <5% U t Mains power quality should be that of a typical commercial or hospital environment. If the user of the care-e-vac 3 interruptions and (< 95 % dip in U t) (< 95 % dip in U t) requires continued operation during power mains interruptions, it is recommended that the care-e-vac 3 be powered voltage variations for 0,5 cycle for 0,5 cycle from an uninterruptible power source or a battery. on power supply input lines 40 % U t 40 % U t (60% dip in U t) (60% dip in U t) IEC 6100-4-11 for 5 cycles for 5 cycles
Power Frequency (50/60 Hz) Magnetic Field IEC 61000-4-8
70 % U t (30% dip in U t) for 25 cycles
70 % U t (30% dip in U t) for 25 cycles
<5% U t (< 95 % dip in U t) for 5 sec 3 A/m
<5% U t (< 95 % dip in U t) for 5 sec 3 A/m
Power frequency magnetic fields should be at levels characteristic of a typical location in a typical commercial or hospital environment.
Portable and mobile RF communications equipment should be used no closer to any part of the care-e-vac 3, including cables, than the recommended separation distance calculated from the equation applicable to the frequency of the transmitter. Recommended separation distance Calculated RF IEC 61000-4-6
3 Vrms 150 kHz to 80 MHz
Radiated RF IEC 61000-4-3
3 V/m 80 MHz to 2,5 GHz
3 Vrms
d = 1,2√P
3 V/m
d = 1,2√P 80 MHz to 800 MHz d = 2,3√P 800 MHz to 2,5 GHz where P is the maximum output power rating of the transmitter in watts (W) according to the transmitter manufacturer and d is the recommended separation distance in metres (m). Field strengths from fixed RF transmitters, as determined by an electromagnetic site survey*, should be less than the compliance level in each frequency range**. Interference may occur in the vicinity of equipment marked with the following symbol:
Note 1 U t is the a.c. mains voltage prior to application of the test level. Note 2 At 80 MHz and 800 MHz, the higher frequency range applies. * Field strengths from fixed transmitters, such as base station for radio (cellular/cordless) telephones and land mobile radios, amateur radio, AM and FM radio broadcast and TV broadcast cannot be predicted theoretically with accuracy. To asses the electromagnetic environment due to fixed RF transmitters, an electromagnetic site survey should be considered. If the measured field strength in the location in which the care-e-vac 3 is used exceeds the applicable RF compliance level above, the care-e-vac 3 should be observed to verify normal operation. If abnormal performance is observed, additional measures may be necessary, such as re-orienting or relocating the care-e-vac 3. ** Over the frequency range 150 kHz to 80 MHz, field strengths should be less than 3 V/m. Recommended Separation Distances Between Portable and Mobile Communications Equipment and the care-e-vac 3 The care-e-vac 3 is intended for use in an electromagnetic environment in which radiated RF disturbances are controlled. The user of the care-e-vac 3 can help prevent electromagnetic interference by maintaining a minimum distance between portable and mobile RF communications equipment (transmitters) and the care-e-vac 3 as recommended below, according to the maximum output power of the communications equipment. Separation Distance according to frequency of transmitter Rated maximum output power of m transmitter 150 kHz to 80 MHz 800 MHz to 2,5 GHz 80 MHz to 800 MHz W d =1,2 √P d =2,3 √P d =1,2 √P 0,12 0,12 0,01 0,23 0,1 0,38 0,73 0,38 1 1,2 2,3 1,2 10 7,3 3,8 3,8 12 23 100 12 For transmitters rated at a maximum output power not listed above, the recommended separation distance d in metres (m) can be estimated using the equation applicable to the frequency of the transmitter, where P is the maximum output power rating in watts (W) according to the transmitter manufacturer. Note 1 At 80 MHz and 800 MHz, the separation distance for the higher frequency range applies Note 2 These guidelines may not apply in all situations. Electromagnetic propagation is affected by absorption and reflection from structures, objects and people.
Ohio Medical Corporation (800)662-5822-Fax: (847) 855-6218 www.ohiomedical.com -– 550542 (Rev.2) 02/2007 1111 Lakeside Drive Gurnee, IL 60031-4099 Phone: 800-662-5822 or 847-855-0800 Fax: 847-855-6218 Email: [email protected]