Operation Manual
192 Pages
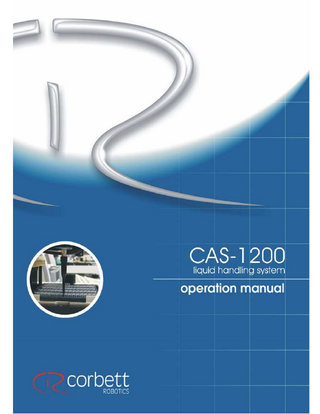
Preview
Page 1
CASCAS- 1200 Liquid Handling System Operation Manual Version 4.9 4.9
©2007 Corbett Robotics Pty. Ltd.
CAS-1200 Operation Manual By the Corbett Robotics Team
The CAS Series of Robotic Liquid Handling Systems provide a precise and labour saving means to perform a wide range of pipetting tasks. The instruments are highly configurable and can be programmed to set up a variety of tasks. The software provides a user friendly, easy to follow user interface. The screen layout corresponds to the plates set up on the robot. The status of any component can be examined by clicking it on the screen. Likewise, any alterations are executed by simply pointing to the corresponding hardware on the screen and changing the desired parameters. This manual is designed to be used as an introduction and quick reference to the CAS-1200.
CASCAS- 1200 Liquid Handling System Operation Manual
All rights reserved. No parts of this work may be reproduced in any form or by any means - graphic, electronic, or mechanical, including photocopying, recording, taping, or information storage and retrieval systems - without the written permission of the authors. Products that are referred to in this document may be either trademarks and/or registered trademarks of the respective owners. The publisher and the author make no claim to these trademarks. While every precaution has been taken in the preparation of this document, the publisher and the author assume no responsibility for errors or omissions, or for damages resulting from the use of information contained in this document or from the use of programs and source code that may accompany it. In no event shall the publisher and the author be liable for any loss of profit or any other commercial damage caused or alleged to have been caused directly or indirectly by this document.
Printed:
Oct-07
© Corbett Robotics 2007
Hardware
1
Contents 1
... ... ... HARDWARE ... ... ... ... 4 1.1 1.2 1.3 1.4 1.5
2
UNPACKING ... 5 BOX CONTENTS ... 6 THE INSTRUMENT ... 11 THE COMPUTER ... 13 SPECIFICATIONS... 14 UP ... ... ... 16 SAFETY AND SETTING U P ... ... ...
2.1 2.2 2.3 2.4 2.5 2.6 2.7 2.8 2.9 2.10 3
SAFETY ... 17 POSITIONING THE ROBOT ... 18 CONNECTING THE ROBOT... 19 SOFTWARE INSTALLATION ... 20 UN-INSTALLING THE SOFTWARE ... 25 OTHER FEATURES ON THE CD ... 25 MULTIPLE ROBOTS FROM ONE COMPUTER... 25 STARTING FOR THE FIRST TIME ... 26 CALIBRATIONS... 29 LID ... 30
... ... ... SOFTWARE IN DETAIL ... ... ... ... 31 3.1 3.2 3.3 3.4 3.5 3.6 3.7 3.8 3.9 3.10 3.11 3.12 3.13 3.14 3.15 3.16 3.17 3.18 3.19 3.20 3.21 3.22 3.23
4
SOFTWARE OVERVIEW ... 32 STARTING THE SOFTWARE ... 34 SELECTING A RUN ... 35 THE SOFTWARE WORKSPACE ... 36 TOOLBAR ... 38 FILE MENU ... 42 CONTROL MENU ... 44 WIZARDS MENU... 45 OPTIONS MENU... 46 HELP MENU ... 79 PLATE BUTTONS ... 82 TIP AVAILABILITY MENU... 83 PLATE OPERATIONS MENU ... 84 ADDING WELLS TO SAMPLE BANKS ... 86 CHOOSING THE RIGHT PLATE ... 88 RIGHT-HAND PANE ... 93 STARTING A RUN ... 137 WARNINGS ... 139 PRE-RUN REPORT ... 140 ABORTING A RUN ... 142 POST-RUN REPORT ... 143 EXCEPTION HANDLING ... 144 SHUTTING DOWN ... 146
... SETTING UP A TYPICAL PCR RUN - AN EXAMPLE ... ... 147 4.1 4.2 4.3 4.4 4.5 4.6 4.7
5
INITIAL SETUP ... 148 REAGENTS ... 152 MASTER MIX ... 154 STANDARDS ... 157 SAMPLES... 158 REACTIONS ... 159 SETTING UP THE TABLE ... 161 ... ... ... USING WIZARDS ... ... ... ... 163
5.1 5.2
PCR SETUP WIZARD... 164 OPTIMISATION WIZARD... 167 © Corbett Robotics 2007
Hardware
3
CASCAS-1200 Robotic Liquid Handling System The CAS-1200 Robotic Liquid Handling System provides a precise and labour saving means for setting up PCR reactions. The CAS-1200 can also perform a vast variety of other pipetting operations. The instrument is highly configurable and can be programmed to set up a range of reactions at the same time. It is capable of preparing multiple Master Mixes, standard dilutions and can use multiple groups of samples. For maximum precision the CAS-1200 uses graphite-impregnated conductive tips, which enables liquid level sensing. The tip moves to just below the surface of the liquid rather than the bottom of the tube preventing carry over of material on the outside of the tip. Non-conductive tips can also be used without the level sensing function. The Robotics Software provides a friendly, easy to follow user interface that has been primarily geared towards PCR set-up. The screen layout corresponds to the plates set up on the robot. The status of any component can be examined by a simple mouse point and click of the component displayed on the screen. Likewise, any alterations are executed by simply selecting the module on screen and changing the desired parameters. The progress of a run can be followed in real time. The software highlights the position of the pipette head on the screen as it moves. A progress bar and an update table show the course of a run. Reports are generated before and after a run and are automatically saved for future reference. Laborious calculations are unnecessary as the software calculates the amount of Master Mix and reagent necessary for each experiment. The Robotics Software can also be run in Virtual Mode. In Virtual Mode, runs can be set up, progress followed and files stored even if the robot is switched off or not connected. Therefore, it is possible to configure runs at a remote location. Virtual mode is also a useful tutorial tool. For customer convenience, sample data can be imported from text-based spreadsheets with flexible options to handle a variety of formats. The reaction list generated by the robot can also be exported as a spreadsheet and loaded into other programs such as the Corbett Rotor-Gene real time PCR software. For further information or assistance, please do not hesitate to contact the Corbett Team or your nearest Corbett distributor. Corbett Robotics Pty. Ltd. 42 McKechnie Dr. Eight Mile Plains Qld 4113 Australia Ph: + 61 7 3841 7077 Fax: + 61 7 3841 6077 http://www.corbettrobotics.com For general enquiries about our products and sales, contact: admin@corbettrobotics.com For technical assistance contact: support@corbettlifescience.com (or support@corbettrobotics.com)
© Corbett Robotics 2007
Hardware
4
1 Hardware Congratulations on the purchase of the CAS-1200 Robotic Liquid Handling System. This section covers the unpacking of the CAS-1200, some of its features, such as level sensing, and the accessories that are delivered as standard with your robot. Please refer to Setting Up for details on how to get started with your CAS-1200.
© Corbett Robotics 2007
Hardware
5
1.1 Unpacking Great care and attention has been taken to design the packaging for the CAS-1200 to ensure that the instrument arrives in the same condition as it left the factory. To unpack the instrument, please follow the instructions provided in the lid of the robot's shipping container. These instructions should also be used when packing the instrument. Please do not discard the packaging. The packaging must be used if the instrument is to be returned for servicing. As you unpack the instrument please ensure that the box contents matches the packing list included with the CAS-1200. Once the robot is removed from the shipping container and its foam base, the arm support must be removed. To remove the arm support and z-axis locking mechanism, follow these simple steps, 1. Unscrew the screws marked A and B on the locking plate to right of the arm. 2. Slide the arm (and pipetting head) all the way to right. 3. Lift the wooden arm support off the table of the robot. 4. Replace the locking plate and screws A and B into the arm support. 5. Look at the robot from the left hand side and identify the z-axis lock screw (shown in the picture below). Unscrew the z-axis locking screw. When this screw is removed the pipetting head will drop. Secure the removed z-axis locking screw and associated parts into the side of the arm support as shown, store the arm support with the rest of the packaging.
The most important components of the packaging are the z-axis lock screw and the wooden arm support. These must be used whenever the CAS-1200 is moved from one location to another. Failure to do so will void warranty.
© Corbett Robotics 2007
Hardware
6
1.2 Box Contents The CAS-1200 Robotic Liquid Handling System shipping container includes the items listed on the packing slip. These items typically include: • 1 x CAS-1200 • 1 x IEC Mains Cable • 1 x RS-232 Serial cable • 1 x Software CD • 1 x (5 x 5mL Tubes) Master Mix Blocks • 1 x (1 x 5mL, 4 x 1.5mL Tapered Tubes) Master Mix Blocks • 1 x Reagents/Standards Block • 2 x 96-Well Plate • 1 x 32 Well Plate set • 1 x Pipettor Service Kit • 4 x Tip Racks • 1 x Pack of Sample Tubes • 10 x Tip Disposal Boxes To operate the CAS-1200 requires a PC, which may or may not be delivered with the instrument.
IEC Mains Cable and Power A standard 3-wire IEC mains cable is required to connect the CAS-1200 Robotic Liquid Handling System to mains power. Typically these cables are the same as used to provide PCs with power. The cable must be a 3-wire cable as the earthing wire is critical for correct level sensor operation.
The CAS-1200 is available in a number of power options. Please see the Specifications.
Serial Cable A serial cable is required to connect the CAS-1200 Robotic Liquid Handling System to the host computer's RS-232 serial port. The serial cable is of the 9-pin male to 9-pin female "straight through" kind.
© Corbett Robotics 2007
Hardware
7
Software CD and User Manual The CAS-1200 Robotic Liquid Handling System is delivered with a Software Manual and the current Software CD. The Software CD contains the latest Robotics Software required to control the CAS1200 Robotic Liquid Handling System. It also contains the Operation Manual (this document) as a PDF document. Occasionally, Robotics Software updates are released to provide new functionality. To ensure you are always using the latest Robotics Software please visit the Corbett Robotics website at www.corbettrobotics.com. It is the user's responsibility to update software to ensure the instrument operates to the best of its ability. Corbett software updates are free of charge to all users of Corbett instruments. We feel this is the only way to give our users the fastest access to new features. This of course means that new versions can be released several times per year.
1.2.1
Loading Blocks and Plates
The CAS-1200 Robotic Liquid Handling System is delivered with a wide variety of loading blocks. These blocks support the tubes that are typically used on the robot. All CAS-1200 loading blocks are manufactured from high quality aluminium which is anodised to give the block a hard wearing, durable black finish. The white feet are made from high temperature silicone rubber. The blocks are fully autoclavable. They can also be kept in a fridge or freezer before placing them on the robot, thus keeping the tube contents cool. The blocks can be washed in bleach or water. Please note that some solvents or salts may stain the anodised surface. The blocks delivered as standard with the CAS-1200 are only a small sample of the variety of blocks available from Corbett Robotics. For a full list of available blocks and accessories, you can request an up-to-date plate catalogue from your nearest Corbett distributor or look in the Robotics Software under Changing Plate Type for an indication of available blocks.
Master Mix Blocks There are two Master Mix Blocks. The first is designed to hold five 5 mL free standing tubes. The second block holds one 5 mL free standing tube and four 1.5 mL tapered tubes. Both blocks are intended to hold diluent and master mix on the robot's workspace. However, their function can be re-defined if necessary. 5 x 5 mL Free Standing
1 x 5 mL and 4 x 1.5 mL Free Standing
Reagent Block One reagent block is delivered as standard. This block is designed to hold eight 1.5 mL tapered tubes, eight 2 mL free standing tubes and 16 x 200 µL PCR tubes. Typically, the larger tubes are used for reagents and the 16 smaller tubes are used for creating dilution series.
© Corbett Robotics 2007
Hardware
8
Standard Footprint Blocks The CAS-1200 is delivered with three blocks which have the standard 128 x 86mm footprint. There are two blocks that hold 96 tubes of dimensions similar to the 200 µL PCR tube. These blocks can be used to hold strip tubes, unskirted or half-skirted PCR plates.
The CAS-1200 is also delivered with a 32 x 1.5 mL well block. The design of this block allows the caps to be locked in position preventing interference with the pipette tip. This block comes with a tube lifter plate which can be placed underneath the block for easy removal of the tubes.
1.2.2
Pipettor Service Kit
The pipettor service kit should be stored in a safe place so that it can be found when the CAS-1200 pipette requires servicing (after 300,000 operations). As is the case with manual pipettes, occasionally these need to be serviced to maintain pipetting precision. This kit and its instruction sheet will allow the user (or a trained service technician) to conduct the pipettor service.
© Corbett Robotics 2007
Hardware
1.2.3
9
Tip Racks and tip rack holders
The CAS-1200 Robotic Liquid Handling System is delivered with four metal tip rack holders. Two different tip sizes (200 µL and 50 µL) are typically used, with 10 racks of 200 µL tips and 10 racks of 50 µL tips delivered with the instrument. Each rack contains 96 tips. Please note that the tips are packaged sterile. Normally, the tips used on the robot are carbon impregnated, conductive and filtered. Conductive tips allow the CAS-1200 to use its level sensor for optimal pipetting precision. Non-conductive tips can be used on the CAS-1200. However, these will not allow level sensing functionality. To use nonconductive tips, the level sensor will need to be disabled in software. The use of non-conductive tips affects the pipetting precision of the robot and is hence not recommended for critical applications. We recommend the use of filtered tips to avoid potential cross-contamination. Further, because the CAS-1200 uses both 200 µL and 50 µL tips, if 50 µL unfiltered tips are placed on the robot by mistake (instead of 200 µL tips) the pipettor may become contaminated. This situation will require a pipettor service and thus the use of non-filtered tips is not recommended.
A tip rack holder loaded with a rack of 96 x 50 µL conductive tips
To load tip rack into the tips rack holder follow this diagram:
1.2.4
Sample Tubes
The CAS-1200 Robotic Liquid Handling System can pipette from a wide variety of tubes. Some typical tubes are provided as samples with the instrument. Please note that the sample tubes provided are not guaranteed sterile.
© Corbett Robotics 2007
Hardware
10
Take great care with tubes. Tubes from different manufacturers, although they might look quite similar, can have significantly different depths and geometries. These variations can influence the calibrations (especially height calibrations) on the CAS-1200. It is recommended that once a particular consumable is chosen, the user always uses that consumable from the same manufacturer to avoid frequent re-calibration.
The sample tubes delivered with the instrument are as follows: 5 mL Free Standing tubes These tubes are typically used to hold diluent and large volumes of master mix. These tubes are normally supported in the Master Mix Block.
200 µL PCR tubes These tubes are typically used to hold samples and reactions and are supported in the 96 and 36well Loading Blocks.
1.2.5
Tip Disposal Boxes
The tip disposal boxes are provided as a way of collecting discarded tips on the side of the CAS1200. These tip boxes will hold approximately 400 used tips. However, due to the way tips fall into the box, occasional shaking of the partially filled tip box may be necessary to avoid tips stacking up on the tip ejector chute. Using the supplied tip collection boxes is optional. Alternative boxes can be used at the user's discretion and may better suit the individual situation.
© Corbett Robotics 2007
Hardware
11
1.3 The Instrument The CAS-1200 Robotic Liquid Handling System is a high-precision instrument designed primarily for the setting up of real-time PCR reactions. The instrument has a number of significant elements which are shown in the figure below.
The off-white paint used on the CAS-1200 is two part epoxy paint, which provides a very hard wearing and UV resistant finish. The paint may yellow slightly over time, and some cleaning solvents may stain the paint. The painted surfaces should be cleaned with a soft cloth with water. The paint finish has been tested to be resistant against bleach, ethanol, methylated spirits and most liquids commonly used in a laboratory environment. However, all spills of any sort should be wiped up immediately to avoid any damage to the paint. Solvents usually associated with painting such as mineral turpentine, acetone or paint thinners should never be used on the instrument. Due to the hard nature of the paint, sharp objects should never be used on the painted finish as chipping of the paint may occur. Similarly, dropping heavy items (such as master mix and reagent blocks) onto painted surfaces is likely to result in chipping. Damage to the painted surface by solvents and incorrect care is not covered by warranty. The master mix and reagent blocks on the CAS-1200 as with most other black components on the instrument (such as the table rails) are manufactured from Aluminium and anodised black. The anodising provides a hard durable finish. The black finish may stain if wiped with certain cleaning products. The arm (y-axis) on the robot provides support for the pipetting head. Under no circumstances should the user ever apply any force to the y-arm. This may misalign the arm resulting in pipetting errors. The pipetting head is the mechanism that can be seen under the pipetting head cover. It consists of a motor driven backlash-compensated pipetting mechanism. This mechanism is similar to most hand pipettes. The pipetting head can be dismantled for the purposes of servicing.
© Corbett Robotics 2007
Hardware
12
The feet are height adjustable and have a non-slip silicone base to ensure that the CAS-1200 is securely positioned on a laboratory bench. Do not attempt to slide the instrument on a bench without lifting as damage to the silicone base of the feet may result. The lid of the CAS-1200 is manufactured from impact resistant polycarbonate. Please refer to the lid section for further details. All electronics with the exception of the level sensor are housed in the rear of the machine. The instrument has a number of moving parts: the X, Y, and Z-axis as well as the pipetting head. Maintenance of these parts is low. Safety is a primary concern with the use of the CAS-1200. The lid has an electronic interlock to prevent normal operation of the instrument while the lid is open. On the rear of the machine are a number of connectors, as shown below. Use of these connectors is further described in Setting Up.
Level Sensor For maximum precision the CAS-1200 Robotic Liquid Handling System is equipped with a liquid level sensor. This level sensor relies on conductive tips and allows the robot to automatically detect when the pipette tip is touching liquid within a tube. The use of the level sensor helps prevent carry-over of material on the outside of the tip. The liquid level sensor is a very sensitive electronic device. It is capable of detecting very small amounts of liquid (see Specifications for further details). It relies on a good earth connection for the robot, typically provided via the cable which connects the robot to mains power. Further, the earth must be free of electrical noise (see Troubleshooting for further details). The level sensor on the CAS-1200 operates by detecting the change in capacitance when the tip touches the liquid inside a tube. The sensed capacitance is developed between the liquid in the tube and the metal external to the tube; the smaller the amount of liquid in the tube, the smaller the change in capacitance when the tip touches the liquid. Eventually the detectable change in capacitance "drowns" in electrical noise. This noise limit defines the minimum amount of liquid that can be sensed (see Specifications). Further, some liquids are more easily detected than others. The level sensor relies on the liquid being conductive: if a liquid is not conductive, the level sensor cannot sense any change in capacitance. For example, liquids that cannot be easily sensed include ultra-pure water and oil. Some liquids which are normally non-conductive can be made slightly conductive by impurities (typically salts). These slightly conductive liquids may be detectable by the sensor in volumes significantly larger than the level sensor minimum. In rare circumstances, the robot may need to pipette from wells that contain liquid less than the level sensor limit. It may be necessary to switch the level sensor off or set the error detection levels differently. It may also become necessary to manually calibrate the plate height closer to the base of the tube.
© Corbett Robotics 2007
Hardware
13
1.4 The Computer A personal computer running the Microsoft Windows operating system is required to control the CAS1200 Robotic Liquid Handling System. This PC can be provided by Corbett Robotics or its agent. If a PC is supplied by the user, please observe the minimum specifications to run the Robotics Software for a CAS-1200 which are listed in the Specifications section. Windows NT, Windows 2000, and Windows 98 are no longer supported. These operating systems may produce unstable or unreliable software operation.
© Corbett Robotics 2007
Hardware
14
1.5 Specifications Pipetting Volumes: Volumes: • Between 1 µL and 200 µL
Precision: Precision: • 5 µL to 200 µL, less than 1% C.V. • 2 µL to 5 µL, less than 5% C.V. into wet wells
Accuracy: Accuracy : • Accuracy can be calibrated in software •
1% calibrated, volumes > 5 µL
Level Sensing: Sensing : • 10 µL of 10 x PCR Buffer in 200 µL PCR tubes supported in an Aluminium reagent block • 20 µL of 10 x PCR Buffer in larger tubes supported in an Aluminium reagent block Please note that the level sensor cannot sense all types of liquids, including oil and very pure water (PCR-grade water is reliably detected).
Throughput: • 384 pipetting operations per hour (tested using a typical PCR setup)
Electrical Requirements: Requirements: • 220 - 240Vac 50Hz, or • 100 Vac 60Hz, or • 110 Vac 60Hz • 250 VA • Good earth connection via mains outlet
Table Capacity: • 6 standard footprint 128 x 86mm plates (up to 384 wells, with wells no smaller than 3.5mm diameter) • 37 additional tubes (combinations of 5 mL, 2 mL, 1.5 mL and 200 µL tubes)
Number of Pipetting Channels: • One
Communication: • RS-232
Lid: • Polycarbonate lid is standard on all machines • UV light for work surface sterilisation is available as factory fitted accessory • HEPA filter unit for positive pressure under lid is available as factory fitted accessory © Corbett Robotics 2007
Hardware
15
Weight: • 25kg
Dimensions: All dimensions are in mm and exclude any computer equipment. • Lid closed, 490 mm(w), 580 mm(d), 390 mm(h) • Lid open, 490 mm(w), 580 mm(d), 770 mm(h) • The connection of cables at the rear of the instrument adds 70 mm to its depth
Computer Requirements: • Platform may be one of: •
Windows XP® Pro SP2 + 2.6 GHz Pentium® 4 CPU (desktop) or 1.6 GHz Pentium® M CPU (laptop) + 512 MB RAM
•
Windows Vista® Business + Core™ 2 Duo CPU + 1 GB RAM + DirectX 9 capability
• RS-232 serial port (or USB port with separate USB-to-RS-232 converter) • DVD/CD-ROM • 80 GB hard disk (at least 100MB of free hard disk space) • Monitor with at least 1024 x 768 pixel screen resolution (1280 x 1024 preferred)
Operational Temperatures: • Constant 15 deg C to 35 deg C - temperature cycling not permitted
Operational Humidity: • 40 - 70% RH •
Lower humidity levels may affect precision due to evaporation
© Corbett Robotics 2007
Safety and Setting Up The Robot
16
2 Safety and Setting Up Before going any further, please consult the section on Safety. This section covers the setting up of the CAS-1200 Robotic Liquid Handling System.
© Corbett Robotics 2007
Safety and Setting Up The Robot
17
2.1 Safety The CAS-1200 Robotic Liquid Handling System has a variety of moving parts. There are a number of places that present significant pinch points. For your own safety and to prevent damage to the instrument, please observe the following safety requirements: • The robot is for indoor use only • Always use the packaging provided with the robot when moving the machine • Do not lift the CAS-1200 by yourself • Do not disable the lid interlock • Do not interfere with robot while it is running • Do not attempt to move any plates or tubes while the robot is operating • Do not, under any circumstance place your hand under the pipetting head while it is lowering • When calibrating plates with the lid up, always stand clear of the robot when making adjustments. Similarly, do not click on the mouse or keyboard while looking closely at plate calibrations. The lid interlock is disabled during calibration mode, wait until the robot arm has completed its movements before moving any plates or tubes. • Do not calibrate the tip ejector unless you are confident in operating the CAS-1200 • Use only recommended tips and tip racks • Keep the lid of the instrument closed whenever possible • NEVER place any items on the y-arm of the instrument • NEVER apply any force (by hand or otherwise) in the upward or downward direction on the yarm (the pipetting arm). • Use the Stop/Pause button located on the tool bar of the software to stop/pause the robot before removing plates or tubes. Please note that the CAS1200 will complete the current action before stopping or pausing.
© Corbett Robotics 2007
Safety and Setting Up The Robot
18
2.2 Positioning the Robot The location/position requirements of the CAS-1200 Robotic Liquid Handling System are not very demanding. However, a few points should be observed. • The robot can be installed on any sturdy laboratory bench or table. • The robot must not be installed near generators of static electricity (e.g. ionisers, large screen televisions etc.) • The robot should be installed in a laboratory environment free of excessive airborne dust. • The robot can operate in temperatures from 4 degrees Celsius to 30 degrees Celsius. Do not subject the robot to repeated temperature cycling. The instrument can be operated in a cool room of consistent temperature. • Do not subject the robot to a relative humidity of > 70% for extended periods of time. • Ensure that all four of the robot's feet are firmly located on the table surface (the front feet can be height adjusted using a 10mm spanner). • Ensure that the lid can fully open upwards without any obstructions. • Ensure that the on/off switch at the rear of the instrument is easily reached. If you have not done so already, please remove the arm support and z-locking screw as discussed in the Unpacking Section.
Helpful Hint Positioning the robot close to the left hand edge of a laboratory bench or table will allow tips to be readily ejected out of the robot into a rubbish bin without the use of a tip disposal box.
© Corbett Robotics 2007