Operating Instructions
26 Pages
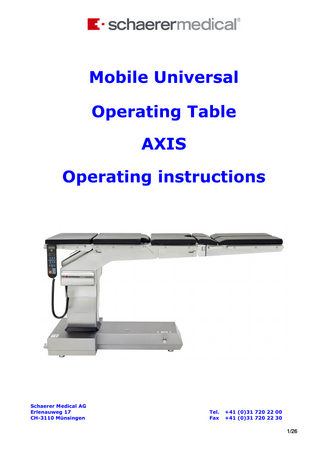
Preview
Page 1
Mobile Universal Operating Table AXIS Operating instructions
Schaerer Medical AG Erlenauweg 17 CH-3110 Münsingen
Tel. Fax
+41 (0)31 720 22 00 +41 (0)31 720 22 30
1/26
Operating instructions for Axis operating table
Published by: Schaerer Medical AG, CH-3110 Münsingen, Switzerland Version: 4.3 Date: 11.2008 © Copyright by Schaerer Medical AG, CH-3110 Münsingen, Switzerland
All rights reserved, including the right to translation into foreign languages. No part of this manual may be copied, reproduced, distributed or electronically transmitted in any form without the written permission of the publisher. All data, technical parameters and figures contained in the manual are based on the information available at the time this publication went to press. Schaerer Medical AG reserves the right to effect changes or amendments to the manual at any time without prior notice.
2/26
TABLE OF CONTENTS GENERAL
Page
4
Page Page
5 5
GENERAL PRODUCT DESCRIPTION
Page
7
OPERATING THE TABLE
Page
9
Page Page Page
11 12 13
Page
14
Page Page Page Page Page
14 15 16 16 17
TABLE CHARACTERISTICS
Page
18
MAINTENANCE
Page
19
Page Page Page Page Page
19 19 20 21 21
SPECIFICATIONS
Page
22
ADDITIONAL ASPECTS OF TABLE OPERATION
Page
23
Messages on the Hand Control Unit Display
Page
23
WARRANTY
Page
25
NON-LIABILITY STATEMENT
Page
25
ENVIRONMENTAL PROTECTION AND DISPOSAL
Page
25
EC DECLARATION OF CONFORMITY
Page
26
Meaning of Symbols Potential Hazards
Moving, Locking, Steering Main Table Positions Manual Control Unit
POSITIONING A PATIENT Motor-driven Functions of the Table Manual Adjustment of Head and Leg Boards Fixing Removable Parts of the Table Operating Conditions Emergency Operation
Cleaning the Table Disinfection Table Maintenance Procedures Notes to Technical Staff Notes to Operating Staff
3/26
GENERAL Welcome to the world of Axis! We would like to take this opportunity to congratulate you on the purchase of your SCHAERER Axis Operating Table. The Axis Operating Table is designed according to recognised international concepts well proven on our previous model, the SCHAERER S-200. Purpose and Contents of the Manual The manual provided is intended to acquaint you with the outstanding features of the SCHAERER Axis Operating Table. It contains all relevant technical information, method of operation and instructions for the servicing and maintenance of the operating table.
Target Group of and Access to the Manual SAFETY is of paramount importance to Schaerer Medical AG. Our top priority is that this device be correctly operated, serviced and maintained to safeguard the full safety of patients and medical staff. To ensure safe and reliable operation: 1.
Read all the directions in this manual and be sure you understand them prior to installing or operating the table.
2.
Take care that the contents of the manual are brought to the attention of all the staff members involved.
3.
Display the manual prominently at a place readily accessible to everyone operating the table.
Key Words in the Instructions Within the manual you will find various instructions and remarks prefaced by "NOTE", "WARNING" and "CAUTION" which warrant special attention on your part. They are used as follows: NOTE is used to explain in detail an operating procedure, a practice or a condition. WARNING is used with respect to an operating procedure, a practice or condition which, if handled incorrectly, could cause damage to the table. CAUTION is used with respect to an operating procedure, a practice or a condition which, if handled incorrectly, could cause human injury.
4/26
Meaning of Symbols
Exercise caution; heed technical documentation. Type B table Potential equalisation Type AP table Potential Hazards We list the following potential hazards for your own safety and that of your patients. Be sure you are acquainted with all of them and keep them in mind at all times. 1.
Read the manual and be sure you understand it prior to installing or operating the table.
2.
Using a current source other than 230 VAC, 50 Hz AC could result in personal injury or in damage to the table.
3.
Replace fuses as directed.
4.
Prior to operating the table, remove the sealed plug to the oil tank and replace it with a ventilated plug (supplied). Use only high quality hydraulic oil with viscosity grade 32 according to ISO (e.g. Blasol 156, hydraulic oil VG 32).
5.
If the table fails to operate as designed, release the operating button. For emergency operation of the table, see chapter "Emergency Operation" in this manual. Do not use the table again until it has been serviced and the problem is remedied.
6.
There is a risk of overturning the table if the floor slopes more than 5°.
5/26
7.
Do not exceed the maximum permissible weight for a patient from 220 kg. (AXIS 800, 180 kg)
8.
The maximum loading of the mobile head board is 40 kg.
9.
The maximum loading of the leg boards is 40 kg and only 20 kg when extended above 45°. The maximum loading of the leg section (one piece, only Axis 800) is 90 kg.
10. Operating the table when any staff members are in close proximity and without removing any tools or accessories could lead to injury or damage to the operating table. 11. When operating the table please pay attention to the position of the patient's hands in order to avoid any injury. 12. Certain movements of the operating table may result in it colliding with the floor or table base. Please take maximum care when positioning the table in order to avoid injury or damage to the table. 13. When using the "zero position", please ensure that the patient's health will not be detrimentally affected by the table's automatic sequence of movements. If at all unsure, please refrain from using the "zero position" function. 14. Please ensure that the patient's head is fully supported when changing the headboard position or injury could occur. 15. When using any high frequency equipment during surgery please ensure that you follow the relevant in-country codes of practice, i.e. regulations (VDE 753). 16. When using defibrillators, and defibrillator monitors, please ensure that you comply with the manufacturer's directions for these devices. 17. Failure to perform periodic inspections and maintenance could result in injuries or damage to the table. 18. Care should be taken making the reverse Trendelenburg movement when the single leg section is in a lowered position as contact with the floor may occur resulting in damage and/or injury.
6/26
19. For your safety This operating table has left our factory in perfect condition. If damage has occurred in transit, the operating table should not be accepted until a representative of the shipping company specified in the shipping document has examined and recorded the nature and scope of the damage. If any part of the table has been lost in transit, this should be noted and recorded on the shipping documents. Hidden defects: If any defects become apparent after unpacking the operating table, have the shipping company send a representative immediately to conduct an on-site inspection of the defects. Have the representative draw up a report on the "hidden" defects which includes the condition of the table at the time of the inspection. He is obligated to do so and you should insist that he does.
GENERAL PRODUCT DESCRIPTION Introduction This manual contains instructions for the installation, operation and normal servicing of the Axis Universal Surgical Operating Table. The table incorporates a universal design. Thanks to an eccentrically positioned column, it has superb image intensification capabilities that allow maximum access for C-Arm X-Ray equipment. The table is manufactured from stainless steel which ensures strength and a degree and ease of cleaning unmatched by conventional chrome-plated or varnished operating tables. The Axis 600 and Axis 800 Operating Tables have six motor-driven functions: floor lock position, height adjustment, lateral tilt, Trendelenburg position, seat section and leg section position. With the Axis 400, 500, 700 the leg sections are fixed (Axis 700 without leg section). The attending personnel can also adjust the table into the flex/reflex position by pressing a single button. The "Zero Position" function likewise allows the operating table to resume a flat configuration at the push of a single button.
7/26
The head board and the standard leg boards are provided with gas spring shock-absorbers and can also be adjusted manually. The Axis Operating Table can receive instructions for positioning from one of two sources: the hand control unit or the emergency control panel. The hand control unit is connected to the operating table by means of an elastic spiral cable. When not in use, the hand control unit can be hung from the equipment bars of the operating table. Each Axis Operating Table is provided with an emergency control panel located under a cover on the right-hand side of the table. From this panel, instructions can be sent for the positioning of the table when the hand control unit is inoperable. Both the hand control unit and the emergency panel can be cleaned and disinfected. Incorporating redundant (multiple) systems in the Axis Operating Table to ensure reliability and safety was a major design consideration. The table is equipped with a second motor pump in case the primary pump should fail. Should the batteries be completely discharged, you can continue operating the table for a short time from the mains by plugging it into a conventional wall socket.
8/26
OPERATING THE TABLE CAUTION - Prior to operating the table, remove the sealed plug of the oil tank and replace it with a ventilated plug. Use only a high quality hydraulic oil with a viscosity grade 32 according to ISO (e.g. Blasol 156, hydraulic oil VG32). Ventilated plug (081787):
For hydraulic movements of the table. You must remove it and replace it with the sealed plug prior to tipping the table.
Sealed plug (1235002):
Insert when table is transported or placed on its side for servicing.
To ensure optimum performance, the table should be brought to room temperature prior to being put in operation. NOTE - The table can be mains-operated (with the charging cable plugged in) or batteryoperated. We recommend you leave the Axis Operating Table plugged into the mains and allow 8 to 12 hours to fully charge the batteries prior to operation. The Axis Operating Table is equipped with a microcomputer which interprets manually input instructions. Information about the condition of the computer, batteries, table movements and operating instructions appears on the display of the hand control unit. If the microcomputer fails to operate while a patient is on the table, the table can still be operated. See the chapter "Emergency Operation" in this manual.
CAUTION - If the table is not operating correctly, release the operating button. With respect to emergency operation, refer to the chapter "Emergency Operation". Do not use the operating table again until it has been serviced and the problem is remedied.
9/26
Axis 800
4
1
3
2
5 6
7
1. 2. 3. 4. 5. 6. 7. 8. 9. 10. 11. 12.
8
9
10
11
12
Head board Leg board (Axis 800 1 piece) Locking lever for swivelling out the leg board Emergency control panel (under the lid) Sockets for hand control and footswitch Oil tank ventilated plug Terminal for equalising potentials Locking lever for direction Mains check lamp Protective cap for the mains connector Mains cable Table locking lever
NOTE - To charge the battery, connect the power cable to the mains and lower the protective cover all the way. Make sure that the mains check lamp is illuminated. NOTE - To disconnect the table from the mains, unplug the power cable.
10/26
MOVING, LOCKING AND STEERING
Moving : Shift lever 12 to position I and the table lock is released.
Locking : Shift lever 12 to position II and the table is locked. (The lever functions only when the hand control unit is connected.)
CAUTION
The table could tip over if the floor slope is more than 5°. In the "Zero Position" (transport position) 10°.
Steering : Lever 8 in position III: the rear roller is fixed in direction of travel. This function is convenient for bringing into main position B. The operating table is pushed at the shoulder board. Lever 8 in position IV: all rollers swivel, the operating table is apable of moving in all directions. Arm 8 in position V: the front roller is fixed indirection of travel. This function is convenient for bringing into main position A. The operating table is pushed at the shoulder board.
11/26
MAIN TABLE POSITIONS The sections of the Axis Operating Table can be configured into two main positions. The two positions are obtained by changing around the head and leg section. Head board
Back board
Sitting board
Leg board
AXIS 800 Locking levers
Main position A
Changing around head board and leg board results in main position B: Leg board
Back board
Sitting board
Head board
Locking levers
AXIS 800
Main position B
CAUTION: Do not exceed the maximum permissible weight of a patient of 180 kg. The maximum loading of the head board by a patient is 40 kg. The maximum loading of the leg board by a patient is 40 kg normally and 20 kg when the board is swivelled out (45 °). The maximum loading of the leg section (1 piece, only Axis 800) is 90 kg.
12/26
HAND CONTROL UNIT The hand control unit is provided with 15 buttons. Below is a sketch of the hand control unit with a short description of each function. NOTE - When operating the "lateral tilt" function, the position of the hand control cable should be noted to avoid it getting caught in the table.
LCD Display 1
2
Stop Button Button for Patient Positioning Basic Position A / Basic Position B
6
Seat Section UP / Basic Position A Back Section UP / Basic Position B
7
Leg Section UP / Basic Position A Head section UP / Basic Position B
8
Leg Section DOWN / Basic Position A Head section DOWN / Basic Position B
9
Seat Section DOWN / Basic Position A Back Section DOWN / Basic Position B
10
Raise / Lower the table
3
Lateral Tilt
4
Reverse Trendelenburg
5
Trendelenburg
Flex
11
Reflex
12
Zero Position
13
NOTE - Lowering or raising the leg boards electrically can only be carried out on the Axis 600 and Axis 800 model (Axis 400 and 500 are manually controlled.) Subsequent orders for hand control units for the AXIS Operating Table can be placed with Schaerer Medical AG by calling 084804
13/26
POSITIONING A PATIENT Motor-Driven Functions of the Table CAUTION - When moving the table, please ensure that all staff members are at a distance from the table and that any accessories or tools have been removed from it in order to avoid injuries or damage to the table. CAUTION - When changing the table position, please ensure that the patient's hands are not positioned where they can be injured. Power Supply ON/OFF When a function button is pressed on the manual control unit, the battery level condition appears on the display for 10 seconds. CAUTION - Certain movements of the operating table may result in it colliding with the floor or table base. Please take maximum care when positioning the table in order to avoid injury or damage to the table. Trendelenburg and Reverse Trendelenburg To operate the table in Trendelenburg or Reverse Trendelenburg, please press the appropriate button marked on the hand control unit, i.e. position 4 and 5, respectively. Height adjustment To raise and lower the table, please press the appropriate button marked on the hand control unit, i.e. position 2, respectively. Tilt Adjustment To tilt the table to the left or right, please press the appropriate button marked on the hand control unit, i.e. position 3, respectively. Adjustment to the Seat Section (Basic Position A) To raise or lower the seat board, please press the appropriate button marked on the hand control unit. See position 7 and 10, respectively. Adjustment to the Back Section (Basic Position B) To raise or lower the back section, please press the appropriate button marked on the hand control unit. See position 7 and 10, respectively. Adjustment to the Leg Board (Basic Position A) (Model Axis 600 and 800 only) To raise or lower the leg section, please press the appropriate button marked on the hand control unit, i.e. position 8 and 9, respectively. Adjustment to the Head Board (Basic Position B) (Model Axis 600 and 800 only) To raise or lower the head section, please press the appropriate button marked on the hand control unit, i.e. position 8 and 9, respectively. Table Flex/Reflex The Axis Operating Table has a flex/reflex function. To put the table into the flex position, whereby the head and leg sections are both lowered, please push the Flex button (position 11). To return the table to a flatter configuration after a flex position or to raise the head and leg sections at the same time, press the Reflex button (position 12).
14/26
Zero position To restore the operating table to zero position, please press down and hold the LEVEL button (position 13) on the hand control unit. The table will then move to a fully horizontal position. Stop in the neutral position The operating table stops in the neutral position during the following movements: Trendelenburg, Lateral Tilt, and Adjustment to the Sitting Board and the Leg Boards. To continue the movement, you must release the button and then press it again. CAUTION Use the "zero position" function with caution. Ensure beforehand that the patient's safety cannot be impaired by the automatic sequence of movements that returns the table to a horizontal position. If at all unsure, please refrain from using the "zero position" function.
Manual Adjustment of the Head and Leg Boards The head and leg boards can be positioned manually. A lever on the end of the head board actuates a locking mechanism. The head board can be put into any position by pressing the lever while raising or lowering the board. Please note that the movement of the board is supported by gas spring shock absorbers, which makes raising the board easier. CAUTION There is a risk of injury to the patient if his/her head is not supported while the head board is being repositioned.
15/26
Fixing Removable Parts of the Table The head and leg boards are removable. The latching mechanism for attaching and removing these parts functions as follows: Fixing 1. Turn the latching lever to the down position. 2. Push the pegs of the table part into the corresponding holes on the table until the pegs snap into place. 3. Turn the latching lever away from the table part (upwards) in order to lock the part into position. Removing 1. Turn the lever to the down position. 2. Pull out the lever and continue turning to the stop. 3. Remove the table part.
Operating Conditions The operating table should only be used in approved healthcare facilities and in conformity with the country codes, i.e. VDE 0107. Equalising the Potentials A connection for potential equalisation is located on the side of the table base. Electrostatic Charge Dissipation (ESD) All parts of the operating table are earthed in relation to each other; the table is also earthed to the floor by means of the rollers or locking cylinders. Any electrostatic charges are thus dissipated directly to earth. NOTE -Electrostatic charge dissipation can only be guaranteed when using intact anti-static cushions manufactured by Schaerer Medical AG. CAUTION - When using high frequency apparatus during surgical operations, please follow the relevant codes of practice, i.e. VDE 753 (e.g. isolating the patient from the ground.) CAUTION - When using defibrillators and defibrillator monitors, follow the manufacturer's instructions for these devices.
16/26
Emergency Operation In the event of a failure of the manual control unit or the motor pump, please use the emergency control panel located under a cover on the right-hand side of the operating table. By pressing the "system over-ride" button, the operator can bypass the micro-computer of the table. Each function of the operating table can be executed by simultaneously pressing the "system over-ride" button and the desired positioning button. As a result, table movements can be carried out without using the microcomputer for the table or the primary motor pump. As already stated, the table can be connected to the mains supply to provide it with a standby power source for the motor pumps should the batteries have discharged completely. If the batteries are empty, connect the table to the mains by plugging the power cable into the appropriate socket on the table and the mains outlet. Please wait approximately 30 seconds to 1 minute so sufficient voltage is supplied to the table to actuate the manual control unit. Otherwise you can use the emergency control panel. NOTE - Mains-powered operation is permitted only for a limited amount of time and only for the purpose of putting the table into horizontal position for the safety and comfort of the patient. Arrangement of buttons on the emergency control panel is as follows:
Trendelenburg
Reverse Trendelenburg Lower the table Lateral tilt to the right Lower the sitting board
SYSTEM OVERRIDE
Lower the leg board DISABLE
LOCK
UNLOCK
OFF button Raise the table Lateral tilt to the
Move the table Raise the sitting Raise the leg board Lock the table
NOTE - Automatic raising/lowering of leg board only possible on Axis 600 and 800 (Axis 400 and 500 have manual adjustment only).
17/26
TABLE CHARACTERISTICS Equipment Bars The table is provided with standard lateral equipment bars where accessories can be mounted. The bar system consists of five bars on either side of the table. C-Arm Access The Axis Operating Table provides optimum access for C-Arm image intensification equipment. The eccentrically installed column provides maximum freedom for image intensification. The figures below show the two positions of the table with the resulting C-Arm window.
Main position A
Main position B The two main positions of the table with the corresponding C-Arm windows. Diagnostic Function of the Table If an error or fault occurs during operation, the hand control unit displays a coded message designating the problem. This message appears on the display of the hand control unit in the form of an error code. This information can be used by the service engineer to remedy the defect.
18/26
MAINTENANCE Cleaning the Table The table design allows for easy cleaning and simplifies infection prevention. The cushions are resistant to standard types of cleaning agents, disinfectants and spots common to medical procedures. The cushions may be fully removed to facilitate cleaning or their replacement. No disinfectants containing chorine or chlorine compounds (chloride) may be used to clean the stainless steel parts of the table unless the cleaned parts are neutralised following the infection. Failure to carry out neutralisation may result in corrosion from high concentrations of built-up chloride (not covered by warranty). Schaerer Medical AG therefore recommends the use of aldehyde-based surface disinfectants. Cleaning the cushions: Use of aggressive cleansing preparations may lead to removal of colour or damage to the cushions. Prior to using any cleaning agent, please carry out an appropriate test on the cushion at a spot on it which is normally hidden. Please remember that a cushion is much less likely to sustain damage if liquid spilt on it is cleaned up immediately. Cleaning the top of the table: The table should be cleaned just prior to and immediately after an operation. Use a non-scouring disinfectant for this purpose. Wipe the table dry with a cloth to ensure that all residual cleaning agent is removed.
Disinfection Approved Means of Disinfections: We may only use the disinfections listed below: Product Name Terralin Prodect Quartamon Mikrobac forte Hexaquart plus Hexaquart plus Meliseptol rapid
Manufacturer S&M Schülke&Mayr S&M Schülke&Mayr Bode B. Braun B. Braun B. Braun
Important: The manufacturer is not liable for damages to persons and/or property as a result of use and application of other disinfections than listed above. In case of intended use of other disinfections, which are not listed above, the applicant shall contact the distributor or representation on side prior to application.
19/26
Please note: -
When performing the disinfection of the operating tables always comply with any country specific and/or legal regulations.
-
When applying the disinfection always follow the instructions given by the manufacturer with respect to application and mixture ratios.
-
The disinfection of the operating table maybe done under the following conditions: o Apply disinfection according to the instruction of the manufacturer. o After disinfection take away all remainder fluids with clear water and dry all parts of the operating table.
Table Maintenance Procedures Little routine maintenance is required apart from a periodic inspection. It is recommended you perform the following inspections weekly: Electrical Cables and Connectors: Check for any cuts and damage and be sure they are well away from moving parts. Hydraulic Piping and Valves: Check for leaks; visible traces of hydraulic oil are indicative of leaking hoses or valves or of more serious problems. Contact Discs of Lock Cylinders: These rubber discs are located at the bottom of the lock cylinders; check them for damage. You must contact an authorised service engineer* if you detect any of the above faults or other defects or damage to the operating table or its accessories. Tank Oil Level :To check the oil level, bring the table into the fully horizontal position and the column to the lowest position. Remove the breather plug to check the oil level. The level should be 25 mm below the upper edge of the tank. If lower, add oil using high quality hydraulic oil with the viscosity grade 32 according to ISO (e.g. Blasol 156, hydraulic oil VG32). Since the table consists of mechanical and electrical parts, it is recommended that an inspection be performed by authorised service staff* once every six months. CAUTION - Failure to perform periodic inspections may lead to injury to the staff or damage to the table. *
Persons authorised by the manufacturer have professional training and experience which gives them sufficient knowledge of operating tables and are familiar with the pertinent governmental work safety devices, rules of accident prevention, guidelines and generally accepted engineering practices.
20/26