SensorMedics
CareFusion 3100B Service Manual Rev J
Service Manual
156 Pages
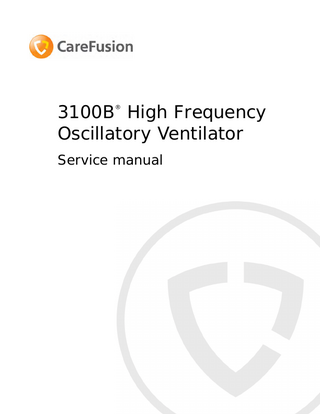
Preview
Page 1
3100B High Frequency Oscillatory Ventilator ®
Service manual
This document is protected by United States and International Copyright laws. This document may not be copied, reproduced, translated, stored in a retrieval system, transmitted in any form, or reduced to any electronic medium or machine-readable form, in whole or in part, without the written permission of CareFusion. Information in this document is subject to change without notice. This document is for informational purposes only and should not be considered as replacing or supplementing the terms and conditions of the License Agreement. © 2009–2011 CareFusion Corporation or one of its subsidiaries. All rights reserved. 3100B is a registered trademark of CareFusion Corporation or one of its subsidiaries. All other trademarks are property of their respective owners. USA CareFusion 22745 Savi Ranch Parkway Yorba Linda, California 92887-4668
Authorized European Representative CareFusion Germany 234 GmbH Leibnizstrasse 7 97204 Hoechberg Germany
800.231.2466 tel +1.714.283.2228 tel +1.714.283.8493 fax
+49.931.4972.0 tel +49.931.4972.423 fax
carefusion.com
Literature number: 771434 Revision J
ii
771434 Rev. J
Service manual
3100B® High Frequency Oscillatory Ventilator
Contents Chapter 1
Introduction ...1–1
Definition of Terms ... 1–1 System Description ... 1–1 Component Description ... 1–2 Chapter 2
Maintenance Procedures...2–1
Patient Circuit Calibration Procedure ... 2–1 Ventilator Performance Checks ... 2–2 Scheduled Maintenance ... 2–3 Chapter 3
Schematics ...3–1
Pneumatic Diagram 3100B (773942) ... 3–1 Driver Controller Schematic (771421) ... 3–2 Driver Displacement DDI Indicator Schematic (771418) ... 3–3 Alarm Display Schematic (766508) ... 3–4 Alarm Board Schematic (771402)... 3–5 Interconnect Wiring Diagram, 3100B (770875) ... 3–7 Chapter 4
Assembly Drawings ...4–1
Unit Assembly, 3100B Ventilator (770155) ... 4–2 Unit Assembly, 3100B Ventilator (770880) ... 4–11 Unit Assembly, 3100B Ventilator (770881) ... 4–19 Unit Assembly, 3100B Ventilator (770882) ... 4–28 Pneumatics Assembly (772757) ... 4–35 Driver Cover Assembly (770864) ... 4–43 Control Panel Assembly (770871) ... 4–47 Electronics Assembly (770873) ... 4–53 Lower Power Supply Assembly (768931) ... 4–62 Driver Power Module Assembly (772714)... 4–68 Driver Assembly, 3.0 Ohms (773937) ... 4–69
771434 Rev. J
iii
3100B® High Frequency Oscillatory Ventilator
Chapter 5
Service manual
Troubleshooting ... 5–1
Pneumatic Failure ... 5–1 Electronic Failure ... 5–3 Mechanical Failure ... 5–5 Chapter 6
iv
Parts List... 6–1
771434 Rev. J
Service manual
Chapter 1
3100B® High Frequency Oscillatory Ventilator
Introduction
This manual contains all the necessary technical information to repair the 3100B High Frequency Oscillatory Ventilator (HFOV). To truly understand the operation of this ventilator, you must also become familiar with the Operator’s Manual (part number 767164).
Definition of Terms The following table describes the use of Note, Caution, and Warning statements in this document. Note
Provides supplemental information to help you understand how the ventilator works.
Caution
Identifies a condition or practice that can cause damage to the ventilator or other equipment.
Warning
Identifies a condition or practice that can cause a serious, adverse reaction or is a potential safety hazard.
System Description The 3100B HFOV uses a linear motor to oscillate a column of bias-flow gas that flows in front of the motor. The column of air creates a pressure within the patient circuit by a variable reduction of the egress of a variable bias-flow gas. The gas flow is restricted by the inflation of three mushroom valves mounted on the circuit. Two of the three mushroom valve inflation pressures can be varied to adjust the mean airway pressure. The third mushroom valve is a safety valve inflated by a solenoid valve that is deactivated whenever the mean airway pressure is greater than 60 cmH2O or less than 5cmH2O. We refer to the mushroom valves as Cap/Diaphragms. Anyone expected to perform emergency service repairs on this device should have three “KNOWN GOOD” Cap/Diaphragms. This column of bias-flow gas is then oscillated by a plate suspended by the rubber diaphragm, which can be seen when the patient circuit is removed. The screws toward the center of the plate attach the plate to a wire coil suspended within a permanent magnet. The coil is excited with a square wave of variable amplitude, frequency, and duty cycle. The electromagnetic effects on the coil move the plate, causing an oscillating pressure wave that is dependent on the driving current through the coil and the consequent collapsing or expanding magnetic field. The driving signal is generated by the Driver Controller Module that is located in the lower, support column of the device just beneath the Driver Assembly. This module produces a square wave of varying frequency, amplitude, offset potential, and duty cycle dependent on four user-set potentiometers. Refer to the Operator’s Manual for further information on these controls.
771434 Rev. J
1–1
Introduction
3100B® High Frequency Oscillatory Ventilator
The pressures generated by the 3100B are measured by a transducer located in the upper Electronics Enclosure. A 1/8” tube leads from the ET Tube connection to the bulkhead. This line incorporates a positive flow to clear it of any condensation from the humidified Bias Gas. A length of coiled tubing before the transducer connection serves to filter out any components of the pressure wave that do not contribute to ventilation. The signal generated by the transducer is detected and conditioned on the Alarm Board that is located at the base of the Electronics Enclosure. If any alarm condition is occurring, the appropriate LED illuminates and the appropriate safety circuit activates. The position of the oscillating Driver is measured by a photo sensor at the rear of the Driver and displayed on the front of the instrument by the Driver Displacement Indicator Board. An elapsed-time meter records the time during which the instrument has been turned on regardless of whether or not the driver is activated. Refer to the Theory of Operation Section in the Operator’s Manual for more detailed descriptions. The only ties between electricity and the pressures generated by the 3100B are the solenoid valve and the movement of the oscillating piston. This is very important in the troubleshooting of the system. Once the solenoid valve has been eliminated as a problem and the Mean Airway Pressure can be maintained and controlled by the Adjust control, the problem can be isolated to the Driver, or one of its supporting components, including the Bellows/Water Trap assembly and the Patient Circuit Body.
Component Description Lower Power Supply There are four separate power supplies generated in the Lower Power Supply Assembly (page 4–62). The ±15 VDC and +5 VDC originate on a separate subassembly mounted on a bracket of the larger assembly. The current ratings are 2 A for the +5 VDC supply and 400mA for the ±15 VDC supply. Both of the AC input lines are fused at 500mA. The fuses are used to drive all TTL logic ICs and all bipolar operational amplifiers. All three are adjustable, and the corresponding potentiometers are labeled on the circuit board. The remaining supply generated by the Lower Power Supply Assembly is the +60 VDC supply. This power supply is simple in design, using a full-wave rectifier, a 9000 µF capacitor, and load resistors. Refer to the Interconnect Wiring Diagram for the schematic of this supply. It is used to develop the +24 VDC on the Driver Controller Board and is the source of current for the PWM. (See Driver Controller Module Theory of Operation.)
1–2
771434 Rev. J
3100B® High Frequency Oscillatory Ventilator
Introduction
Pneumatics Operation The pneumatics operation of the 3100B can be divided into six distinct pneumatic systems. Refer to Pneumatics Diagram P/N 773942. • Input from blender. • Bias flow. • Limit. • Pressure measurement. • Dump and control. • Driver cooling. Input from Blender The input gas from the mixed Air/O2 supply must be 40 - 60 psi and capable for flow of 60 L/min. This pressure opens a normally closed pressure switch that is set to open at 30 psi. The switch is factory adjusted. In parallel with the switch is a 75 psi pop-off valve that is self resetting. This input gas goes to PR7 and PR4 (Pressure Regulator) where the input pressure is then fed to PR2, PR3, and PR6 for other functions. Bias Flow PR7 feeds the flow meter on the front panel and supplies the pressure necessary for the maximum flow rate of the 3100B, which is 60 L/min. To adjust this regulator, simply open the front panel flow meter fully CCW and adjust PR7 for a reading of 60 L/min. This bias flow leaves the electronics enclosure after passing a factory adjusted 5 psi pop-off valve. The air would then be heated and humidified and finally be connected to the underside of the patient circuit assembly. This flow creates a positive pressure inside the patient circuit. Limit PR2 reduces the pressure from PR4 to approximately 1.6 psi. In the event that the proximal pressure exceeds the set MaxPa alarm setting, an audible and visual alarm occurs. The ventilator immediately limits the mean airway pressure to a value calculated between the set Max and Min Paw alarm settings. The limit-valve solenoid re-pressurizes to its normal operational state. If the high mean airway pressure condition persists, the alarm repeats until the condition is resolved. On the patient circuit is a limit cap/diaphragm that, when inflated, occludes the opening in the patient circuit at the LIMIT valve just above the bias flow connection. The occlusion of this opening allows the bias flow to create pressure within the circuit. Pressures that exceed the cap/diaphragm inflation pressure bleed off through the opening. This cap/diaphragm inflation therefore sets a LIMIT for any point downstream in the patient circuit.
771434 Rev. J
1–3
Introduction
3100B® High Frequency Oscillatory Ventilator
Pressure Measurement PR6 reduces the pressure from PR4 to approximately 135 cmH2O. This is passed to a tee fitting that leads to the pressure sense line and the pressure transducer. A length of coiled 1/8” tubing is used for coupling to the pressure transducer to eliminate noise. This pressure of 135 cmH2O is used to create a flow of air away from the pressure transducer and towards the measuring point on the patient circuit, removing any condensation in the humidified biasflow gas from the humidifier. Dump and Control PR3 reduces the pressure from PR4 approximately 3 – 7 psi under normal operating conditions. This is a user adjustment, located on the right side of the top cover, and should never exceed 7 psi when properly adjusted. This pressure is fed to the normally closed port of solenoid valve one. When the solenoid valve is energized this pressure inflates the DUMP cap/diaphragm. This cap/diaphragm is closest to the patient connection on the patient circuit and totally occludes the opening there. When any alarm condition is encountered that necessitates the opening of the DUMP valve, the solenoid valve is de-energized and the pressure at the cap/diaphragm vents to atmosphere through the normally open port of the solenoid valve, allowing the pressure in the patient circuit to drop to atmosphere. PR3 also supplies pressure to the CONTROL cap/diaphragm. This pressure is not as high as the pressure at the DUMP cap/diaphragm, because it is also sent to two variable orifices. FV1 at the bottom of the pneumatics enclosure is a factory adjusted flow restrictor and should be adjusted during the pneumatics alignment procedure in the adjustments section. The other variable orifice is the front-panel Pa adjust valve. Closing this restrictor with a clockwise turn causes greater occlusion of the opening in the patient circuit body at the CONTROL valve. This is the last exit for the bias flow, and restricting this outlet causes a higher pressure in the patient circuit. Keep in mind that even if the CONTROL cap/diaphragm were inflated to maximum, some bias flow is allowed to escape through a separate hole near this valve as a safety feature. Driver Cooling The requirements of the compressor air source used to cool the driver are 40 – 60 psig and capable of 28 L/min minimum flow. This input gas is detected at a 30 psi, normally closed, pressure switch. The switch opens at a pressure greater than 30 psig. This input gas is also detected at a 75 psi pop-off valve that attempts to release pressures above 75 psi. It is selfresetting. PR8 reduces this input pressure to approximately 20 psi and feeds into an air flow amplifier on the underside of the driver assembly. This device entrains room air into the flow of compressed air to enhance the cooling of the driver.
1–4
771434 Rev. J
3100B® High Frequency Oscillatory Ventilator
Introduction
Pressure Transducer Transducer Type The Pressure Transducer used in the 3100B is Model 143PC03D manufactured by Micro Switch, a division of Honeywell. It is a differential transducer with an input pressure range of ±2.5 psi. The excitation voltage is +10 VDC generated on the Alarm Board. This voltage can be measured at TP5. The output characteristics are well beyond those necessary to accurately measure the 15 Hz waveform. Calibration It is necessary to check the calibration of the Pressure Transducer every 2000 hours of operation. Refer to the Maintenance Section of this manual for instructions on this and other regular maintenance requirements.
Alarm Board The Alarm Board (page 3–5) can be broken down into several separate circuits that integrate to serve the following functions: • Driving the AUDIO buzzer. • Detecting and utilizing the battery. • Driving the warning and alarm LEDs. • Generating a signal to stop the oscillator when a pressure alarm has occurred. • Detecting the user-adjustable thumbwheel switches. • Detecting the pressure signals, Pa and ∆P. • Determining if an alarm has occurred. • Detecting the pressure signal. The signal generated by the pressure transducer comes on to the board at J1 pin 1 and is conditioned by three stages of U2, a quad operational amplifier. U2-A is a current amplifier. U2-C provides high frequency filtering and a voltage gain of three. This stage also incorporates an offset adjustment with potentiometer R6. U2-D provides adjustable gain with feedback potentiometer R2. Both potentiometers can be adjusted through the rear panel. TP1 (Test point one) provides easy measurement of the pressure signal by using TP6 as a reference ground test point. See the Maintenance Section of this manual for instructions on performing this calibration. Input capacitors C2 and C3 provide input to quad operational amplifier U1-A allowing only changing pressure signals through. U1-C amplifies the negative portions of the pressure signal, and this voltage is stored in capacitor C5 due to its relatively long discharge time through R10. Similarly C1 stores the positive peaks of the pressure signal. The output of U3-C is proportional to the difference
771434 Rev. J
1–5
Introduction
3100B® High Frequency Oscillatory Ventilator
between positive and negative peaks. This signal is sent to the “AMPLITUDE” digital panel meter and is commonly referred to as the ∆P measurement. Oscillator Stopped Alarm Comparator U12-A compares a reference voltage of approximately 3 VDC to the difference between the positive and the negative peak. If the difference voltage is less than approximately 0.3 VDC (6 cmH2O on the digital panel meter labeled “AMPLITUDE”) then diode CR3 does not conduct. The output of the comparator goes to the low state creating an “OSC STOPPED” signal and activating the warning light. “OSC STOPPED ALARM DISABLE” is active high when the “START/STOP” front panel switch is in the stop mode and the LED is extinguished. This signal originates on the Driver Displacement Indicator Board. Mean Airway Pressure and Alarms Operational amplifier U11-D provides buffering and low pass filtering of the pressure signal. The average pressure or “MEAN AIRWAY PRESSURE” is sent out J2 pin 5 and 6 by way of voltage divider R47 and R40. The front panel thumbwheel switches for minimum and maximum pressure alarms are variable resistances that provide feedback for operational amplifiers U3-B and U3-A. The signal is generated by a 10V reference, Q1. The variable resistance of the thumbwheels add 100Ω with each increase in the units digit, and 1KΩ with each increase in the tens digit. Quad comparator U5 is used to determine if a pressure alarm has occurred. The signal “MEAN HI” is used as a positive input on U5-A and U5-B. The negative input of U5-A is the “Set Min” signal selected by a thumbwheel. The negative input of U5-B is 0.250V. These comparisons determine if a low pressure alarm is occurring, and the output of the comparator is driven low if an alarm is occurring. Conversely, U5-C has its negative input tied to the signal “MEAN HI” and compares it to the full “Set Max” selected by the thumbwheel switch. And U5-D has “MEAN HI” on the positive input and a fixed 3.0V on the negative. These comparisons determine if a high pressure alarm is occurring. The output of U5-C is driven low when an alarm is occurring. The output of U5-D is driven high when the “MEAN HI” signal is greater than 60 cmH2O or 2.5 VDC. The >60cmH2O alarm function is delayed by the alarm delay board for 1.5 seconds. The conversion factor for voltage to pressure is 1 cmH2O = 50mV or 1V = 20 cmH2O. The 3100B high pressure alarm is set by U5-D when the “MEAN HI” pressure signal rises above 60 cmH2O or 3.0 volts. This high level is felt at OR gate U10-D forcing its output high. This signal is then inverted by U14-B to turn the LED on the Alarm Display Board on. The output of U5-D is also used to trigger U6-A, a monostable multivibrator. This positive pulse clocks the output of U4-A high. U4-A can be reset by the operator by pressing the “RESET” switch that generates a reset pulse to U4-A via Q2. This should only be done after correcting the cause for the high pressure alarm, because the DUMP valve closes on reset and the driver begins to oscillate again.
1–6
771434 Rev. J
3100B® High Frequency Oscillatory Ventilator
Introduction
This alarm stops the oscillator, opens the DUMP valve and sounds the audio alarm via U10 and U14 along with Q5 and associated circuitry. When the “MEAN HI” signal falls below 5 cmH2O then the “LO ∆P LIMIT” signal goes low. This signal is inverted by U14-A and goes to pin 1 of OR gate U10-A. The output of U10-A is high when either “HI ∆P LIMIT” or “LO ∆P LIMIT” is active. The signal is inverted by U14-D and goes off the circuit board to the Driver Displacement Indicator Board where it is NANDed with two other signals to stop the oscillating piston. (See DDI Theory of Operation.) The output of U14-D is also sent to OR gate U10-B. An active alarm causes the output of this OR gate to be driven low and transistor Q5 to be turned off, de-energizing the solenoid valve in the pneumatics enclosure. This causes the pressure within the patient circuit to vent to atmosphere. The LO ∆P LIMIT alarm needs no reset. Once the fault has been corrected the DUMP valve closes, and the oscillator begins to run. The output of U14-D is also sent to AND gate U7-B where it is ANDed with three other signals “OSC STOPPED”, “MIN MAP” and “MAX MAP,” which were discussed earlier. A low signal on any of these inputs drive the output of U7-B low. Turning Q7 on sounds the audio alarm. AND gate U7 provides the input signal when the alarm should be active. These signals are active low. Timer U13 provides a 45 second silence triggered by a front panel switch at J1 pin 4. Power Failure Alarm When power is removed from the 3100B, relay U8 returns to its off position. Relay U9, however, stays in the energized state, since the battery voltage on the contacts is fed back to the coil. The de-energized contacts allow the battery voltage to drive the audio alarm and the power failure light. The audible alarm and the power failure light activates immediately. Pressing the reset button allows Q3 to conduct, breaking the circuit in the normally open U9. Comparator U12-B generates a battery low signal when the battery voltage falls below 6.5 volts. Quad op-amp buffers this reference voltage to supply power to the pressure transducer. Oscillator Overheated Quad comparator U12-C and U12-D take the resistance of a thermistor, mounted on the coil inside the oscillator, and determines if 170 or 190 °C has been reached. Signals are active lows. At 190 °C, a signal from U12-D is sent to the DDI Board.
Driver Controller Module The Driver Controller Module (page 3–2), generates the square wave necessary to cause the oscillations of the drive. It consists of three separate subassemblies: • Driver controller board • Choke board • PWM amplifier
771434 Rev. J
1–7
Introduction
3100B® High Frequency Oscillatory Ventilator
Driver Controller Board Integrated circuit U3 (ICL8030) is a waveform generator that produces a sawtooth, square, and triangle wave. The triangle wave at pin 3 is used to drive the controller circuitry. The negative voltage at pins 4 and 5 determine the frequency of the waveform, and a 10 kΩ potentiometer mounted on the front panel, connected at P1 pins 7 and 8, determines the voltage. This allows an adjustment of between 3 and 15 Hz. Fine tuning of this frequency can be made with R18 and R19 as measured at TP8. Operational amplifier U1 supplies a signal to the front panel display meter and can be adjusted with R17. It is not necessary to make any adjustments to the potentiometers on the rear of the meter itself. Operational amplifier U2 provides offset and gain adjustments for the triangle wave with potentiometers R1 (offset) and R2 (gain). Test point 2 should approximate a 0 – 10 V triangle waveform. This signal goes to comparator U4 (LTI011) on the negative input. The positive input is governed by the output of U2-D and the setting of a 10 kΩ potentiometer mounted on the front panel labeled “% Inspiratory.” JP2 should be jumpered. Do not jumper JP1. Fine tuning of the 30 and 50% Inspiratory Time limits can be made with the offset and gain potentiometers R1 and R2. A meter is connected at J22 and J23 for display. R16 adjusts the reading on the meter. The output of comparator U4 is a square wave with the selected frequency and duty cycle (% Inspiratory Time) inspirations during the high portion of the wave at TP7. There are two reference voltages created by +15V, VR1, U8-A and U8-B. These reference signals are sent to U5, a dual analog gate. The reference voltages are +5 V and –5 V. Each voltage goes to a separate gate on U5. The gates are enabled with a low signal. NAND gate U6-C inverts the square wave so that each gate is enabled alternately. The output of the two gates is tied together and the resultant signal is sent to the inverting input of U2-B. The signal at TP6 should be 10V p–p and centered at 0 V. R4 is used as an offset adjustment, and R3 is for gain. However, these adjustments are very interactive and repetitive adjustment may be necessary. The signal at TP6 should be present whenever the instrument has power applied. The signal at TP6 is then sent to a 10 kΩ potentiometer used to send a variably-attenuated signal to U2-C. U2-C has two possible feedback paths. When the start light is illuminated, the “DISABLE OSC” signal at J1 pin 6 is a positive voltage. By following the logic for the three NAND gates of U6, you can see that the gate of U5 is open and the gain of U2-C is approximately one. When the gate is closed (“DISABLE OSC” is high) the gain of U2-C goes to near zero. This is when the oscillator is off. The output of U2-C is the drive signal for the PWM servo amplifier discussed later, and positive portions of the waveform move the piston forward during inspiration and negative portions expiration. U7 is an optical isolator that provides an enable signal to the PWM servo amplifier.
1–8
771434 Rev. J
3100B® High Frequency Oscillatory Ventilator
Introduction
Q1, CR1, C17, R40 and C18 reduce and regulate the 60 V input from the Lower Power Supply Assembly (page 5–3) to 24 V. This is then sent through F1, a 500mA slow-blow fuse, to power the cooling fan, the solenoid valves, and the pressure transducer. PWM Servo Amplifier The PWM servo amplifier is used to provide a safe and reliable switching of the current needed to drive the oscillator. It is extremely efficient (97%) and is fully protected against over-voltage, over-current, over-heating, and any shorting across the oscillator’s coil assembly. Loop gain, current-limit input gain, and offset can be adjusted. The amplifier receives its main drive power directly from the 60 VDC power supply located in the Lower Power Supply assembly. It also takes the drive signal and an inhibit signal from the Driver Controller board. Please refer to the 4000 hour procedure for details. We do not recommend any service to this subassembly beyond adjustment and inspection of connectors. Choke Board The Choke board comprises two coils that act as a high-frequency choke to remove any spurious, low-level noise from the drive signal that is generated by the circuits on the PWM servo amplifier.
Driver Displacement Indicator Board The DDI Board (page 3–3) has several circuits that integrate to serve the following functions: • Display movement of the oscillator. • Start or stop the oscillator. • Movement of the oscillator Mounted through the rear of the driver, the DDI probe generates a current proportional to the position of the driver by sensing light from an LED that is also mounted on the probe. The light is modulated at approximately 8 kHz by U5 and Q3. Power is sent to both the emitter and detector in the probe via J1 pin 6. The modulated light source is reflected by the rear side of the piston inside the driver assembly. The reflections are sensed by the detector on the probe and translated into an 8 kHz signal varying in amplitude, depending on the distance between the piston plate and the detector. This signal is buffered by U1 and demodulated by the filtering of C2, C5, C6, R13, R14, R15, and U4. Referring to the schematic on page 3–3, this signal splits at TP1. The top circuit is a high-pass amplifier that allows only the fast changes in the resultant amplitude to be passed by C10. The bottom is a low-pass amplifier that uses C12 as the storage capacitor. These signals are then summed by the final stage of U4. The final signal, which can be measured at each output line, activates an individual LED on the display ICs (DS1 and DS2). R4 adjusts the high-pass gain and determines the width of the LED display when the oscillator is oscillating. See the section “4000-hour or 3-year Interval” on page 2–7 for instructions when making these adjustments. There is also a procedure for this in the maintenance section of the operator’s manual.
771434 Rev. J
1–9
Introduction
3100B® High Frequency Oscillatory Ventilator
Starting and Stopping the Oscillator Switch 1 is the START/STOP switch that toggles the output of U6 and changes the output of U7. A low at U7 pin 1 disables the oscillator via U8 and also activates the “STOP OSC ALARM DISABLE.” This signal disables the “OSCILLATOR STOPPED” alarm via the Alarm Board and is active high. The output of U8 is the “DISABLE OSC” signal that is sent to the Driver Controller Board to stop the oscillator. This pin is ACTIVE high, meaning the oscillator stops if this line is high. This signal leaves the board at J1 pin 9 and is generated by any of three conditions: • The START/STOP switch is disabled. • A “∆P LIMIT” alarm is active, meaning there is either a Mean Airway Pressure greater than 60 cmH2O or less than 5cmH2O. • The OVERTEMP signal going low, meaning the driver coil is at greater than 190 °C.
Driver Assembly The heart of the 3100B is the Driver Assembly (page 4–69). It is composed of a toroidal, permanent magnet and housing elements with a coil of wire suspended within the magnet by from what are referred to as spiders. The spiders are similar to speaker cones, but have much deeper convolutions to allow for greater travel. A plate is mounted at the front of the coil. This plate can be seen when the disposable Bellows/Water Trap Assembly is removed. A circular, rubber ring called a diaphragm surrounds the piston plate and attaches it to the front housing. Every 4000 hours of use or three years (whichever occurs first), the driver should be reworked to incorporate new spiders and diaphragms, because they suffer fatigue over time and usage (see the section “4000-hour or 3-year Interval” on page 2–7). Cooling Flow The total cooling flow required by the driver assembly is approximately 108 L/min. 28 L/min of this comes directly from the cooling gas regulator PR8. An additional 80 L/min of ambient air flows into the driver through a port on the bottom of the driver referred to as the Air Amplifier port. As the 28 L/min flow moves through the device, it causes a negative pressure on this port, entraining the additional ambient air flow. Driver movement is controlled by a square-wave driver referred to as the Driver Controller Module (page 3–2). During positive portions of the square wave, the driver’s coil moves forward, toward the patient connection, and in the opposite direction during the negative portion. A thermistor is mounted on the coil to determine if the oscillator is overheating. The circuitry that senses the temperature is located on the Alarm Board. There are no user-maintainable parts on the Driver Assembly. All rework or repair should be performed only at a CareFusion service facility.
1–10
771434 Rev. J
Service manual
Chapter 2
3100B® High Frequency Oscillatory Ventilator
Maintenance Procedures
Patient Circuit Calibration Procedure This procedure describes the steps necessary to calibrate the patient circuit to the 3100B.
Figure 2.1 Patient Circuit Calibration Label
771434 Rev. J
2–1
Maintenance Procedures
3100B® High Frequency Oscillatory Ventilator
Ventilator Performance Checks The Ventilator Performance Checks label, shown in the following illustration, provides the step for setting the power, mean pressure adjust, and bias flow controls to achieve specific ranges of ∆P and Pa.
Figure 2.2 Ventilator Performance Checks label
2–2
771434 Rev. J
3100B® High Frequency Oscillatory Ventilator
Maintenance Procedures
Scheduled Maintenance This section describes the required maintenance for the 3100B HFOV. Before every use, perform the start-up and verification procedure as outlined in the operator’s manual. Check the rubber on the driver for rips, cracks, or tears before placing the patient circuit on the unit. After every use, inspect and clean, if necessary, the air filter at the base of the ventilator. Four small, black snaps release the cover of the filter. Store the ventilator with the plastic driver cover on the driver between patient use.
Seven-year Interval We recommend that every seven years the driver power module (part number 24-772714) be replaced. The 4000 hour PM calibrations should be performed after installation of the power module. This procedure is to be performed by CareFusion factory-trained personnel only. At every 500-hour interval, replace the input gas filters (one for the blended gas input and one for the cooling gas input). There is a package of ten filters sent with each ventilator. Additional filters may be purchased (P/N-767163).
2000-hour Interval Every 2000 hours, adjust the DC power supply, the pressure transducer, and the driverdisplacement indicator as described in the following procedures. Adjusting the DC Power Supply Note: Refer to Figure 2.3 while performing the steps in this procedure. 1. Turn off power to the 3100B HFOV and unplug the unit from the AC receptacle. 2. Remove the rear column cover. 3. Plug the 3100B HFOV back into the receptacle and turn the power on. The power supply (Figure 2.3) is located directly below the Driver Power Module. 4. Connect the negative lead of a digital voltmeter to the +5V COM terminal of the DC power supply. 5. Connect the positive lead of a digital voltmeter to the +5V terminal of the DC power supply. Note: If adjustments are necessary, remove the front column cover. 6. If necessary, adjust R9 for a reading of +5 V +/- ± 0.25 V.
771434 Rev. J
2–3
Maintenance Procedures
3100B® High Frequency Oscillatory Ventilator
7. Connect the negative lead of the digital voltmeter to the 15V COM terminal on the DC power supply. 8. Connect the positive lead of a digital voltmeter to the –15 V terminal on the DC power supply. 9. If necessary, adjust R57 for a reading of -15 V ±0.75 V. 10. Connect the positive lead of a digital voltmeter to the +15V terminal on the DC power supply. 11. If necessary, adjust R82 for a reading of +15 V ± 0.75 V. 12. Turn power off to the 3100B HFOV and unplug the unit from the AC receptacle. 13. Ensure that the 9800 µF capacitor connections are secure and clean. 14. Plug the unit back into the wall and apply power. 15. Measure the voltage across the 9800 µF capacitor. It should read greater than 59 VDC.
Figure 2.3 DC Power Supply Calibrating the Airway Pressure Monitor Transducer Note: The driver is turned off throughout this procedure. 1. Locate the pressure transducer ZERO and SPAN, screwdriver-adjustable controls on the rear panel of the control package below the battery compartment. Have a suitably small screwdriver available to make any necessary adjustments. 2. Attach the patient circuit. (Only use a 3100B non-filtered circuit for testing.) Attach a digital readout type pressure transducer meter inline with the bottom leg of a 1/8 inch T fitting.
2–4
771434 Rev. J
3100B® High Frequency Oscillatory Ventilator
Maintenance Procedures
Attach one of the arms of the T fitting directly to the pressure sense fitting of the patient Y. Attach the 3100Bs 1/8 inch PVC pressure sense tubing directly to the other arm of the T fitting. 3. Plug the end of the patient circuit T with a #1 rubber stopper. Turn on the bias-flow gas pressure, press reset until the Pa comes up, and create a mean pressure of 39–43 cmH2O (as read on the external meter) by using the Mean Pressure and Bias Flow. 4. Zero: Ensure that both gases are on. Remove the rubber stopper from the patient circuit Ycoupler and verify that the MEAN PRESSURE display reads –0.5 to +0.5 cmH20. Adjust the Zero potentiometer to match the digital pressure meter within ± 0.3 cmH2O and ensure that, after adjustment, the mean pressure reads between –0.5 and + 0.5 cmH2O. 5. Span: Reinsert the rubber stopper, and then depress the RESET switch until the mean pressure is reestablished to 39–43 cmH2O. Observe that the MEAN PRESSURE display on the ventilator reads the same as the Digital Pressure meter reading within ±0.3 cmH2O. Adjust the Span potentiometer as required. 6. Repeat steps 4 and 5 until no further adjustments are needed. 7. Disconnect pressure meter. Adjusting the Driver Displacement Indicator Refer to Figure 2.4 while performing the steps in this procedure. 1. Turn on the gas supply pressure to the Input From Blender port and the cooling air for the driver. 2. Turn power on. Make sure the oscillator is disabled. 3. Place the stopper in the ET tube connection. 4. Set Bias Flow to 20 L/min. 5. Set the Max Pa thumbwheel switch to 40. 6. Set the frequency to 15 and % I-Time to 33. 7. Depress RESET and establish a mean pressure of 20 cmH2O. 8. Press the START/STOP button, start the oscillator. Adjust the Power Control for a Delta P of 90. 9. Adjust R4 on the DDI board so that a total of three segments are lit on the bar graph. 10. Turn the power off.
771434 Rev. J
2–5
Maintenance Procedures
3100B® High Frequency Oscillatory Ventilator
Figure 2.4 DDI potentiometers
2–6
771434 Rev. J