SensorMedics
VELA Diamond Series Service Manual Ver A
Service Manual
111 Pages
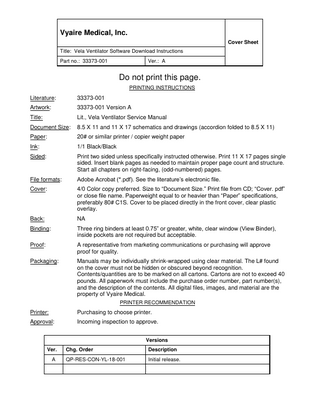
Preview
Page 1
Vyaire Medical, Inc. Cover Sheet Title: Vela Ventilator Software Download Instructions Part no.: 33373-001
Ver.: A
Do not print this page. PRINTING INSTRUCTIONS
Literature:
33373-001
Artwork:
33373-001 Version A
Title:
Lit., Vela Ventilator Service Manual
Document Size:
8.5 X 11 and 11 X 17 schematics and drawings (accordion folded to 8.5 X 11)
Paper:
20# or similar printer / copier weight paper
Ink:
1/1 Black/Black
Sided:
Print two sided unless specifically instructed otherwise. Print 11 X 17 pages single sided. Insert blank pages as needed to maintain proper page count and structure. Start all chapters on right-facing, (odd-numbered) pages.
File formats:
Adobe Acrobat (*.pdf). See the literature’s electronic file.
Cover:
4/0 Color copy preferred. Size to “Document Size.” Print file from CD; “Cover. pdf” or close file name. Paperweight equal to or heavier than “Paper” specifications, preferably 80# C1S. Cover to be placed directly in the front cover, clear plastic overlay.
Back:
NA
Binding:
Three ring binders at least 0.75” or greater, white, clear window (View Binder), inside pockets are not required but acceptable.
Proof:
A representative from marketing communications or purchasing will approve proof for quality.
Packaging:
Manuals may be individually shrink-wrapped using clear material. The L# found on the cover must not be hidden or obscured beyond recognition. Contents/quantities are to be marked on all cartons. Cartons are not to exceed 40 pounds. All paperwork must include the purchase order number, part number(s), and the description of the contents. All digital files, images, and material are the property of Vyaire Medical. PRINTER RECOMMENDATION
Printer:
Purchasing to choose printer.
Approval:
Incoming inspection to approve. Versions
Ver. A
Chg. Order
Description
QP-RES-CON-YL-18-001
Initial release.
VELA™ Ventilator Service Manual
33373-001 Version A
ii
This document is protected by United States and International Copyright laws. This document may not be copied, reproduced, translated, stored in a retrieval system, transmitted in any form, or reduced to any electronic medium or machine-readable form, in whole or in part, without the written permission of Vyaire. Information in this document is subject to change without notice. This document is for informational purposes only and should not be considered as replacing or supplementing the terms and conditions of the License Agreement. © 2019 Vyaire. Vyaire, the Vyaire logo, and all other trademarks or registered trademarks are property of Vyaire Medical, Inc., or one of its affiliates. 33373-001 Version A (2019-01)
USA Vyaire Medical, Inc. 26125 North Riverwoods Blvd. Mettawa, IL 60045 1-833-327-3284 [email protected] vyaire.com
33373-001 Version A
iii
Warranty THE VELA™ ventilator systems are warranted to be free from defects in material and workmanship and to meet the published specifications for two (2) years or 8,000 hours, whichever occurs first. The turbine only is warranted to be free from defects in material or workmanship for five (5) years or 40,000 hours whichever occurs first. The liability of Vyaire (referred to as the Company) under this warranty is limited to replacing, repairing or issuing credit, at the discretion of the Company, for parts that become defective or fail to meet published specifications during the warranty period; the Company will not be liable under this warranty unless (A) the Company is promptly notified in writing by Buyer upon discovery of defects or failure to meet published specifications; (B) the defective unit or part is returned to the Company, transportation charges prepaid by Buyer; (C) the defective unit or part is received by the Company for adjustment no later than four weeks following the last day of the warranty period; and (D) the Company’s examination of such unit or part shall disclose, to its satisfaction, that such defects or failures have not been caused by misuse, neglect, improper installation, unauthorized repair, alteration or accident. Any authorization of the Company for repair or alteration by the Buyer must be in writing to prevent voiding the warranty. In no event shall the Company be liable to the Buyer for loss of profits, loss of use, consequential damage or damages of any kind based upon a claim for breach of warranty, other than the purchase price of any defective product covered hereunder. The Company warranties as herein and above set forth shall not be enlarged, diminished or affected by, and no obligation or liability shall arise or grow out of the rendering of technical advice or service by the Company or its agents in connection with the Buyer's order of the products furnished hereunder. Limitation of Liabilities This warranty does not cover normal maintenance such as cleaning, adjustment or lubrication and updating of equipment parts. This warranty shall be void and shall not apply if the equipment is used with accessories or parts not manufactured by the Company or authorized for use in writing by the Company or if the equipment is not maintained in accordance with the prescribed schedule of maintenance. The warranty stated above shall extend for a period of TWO (2) years from date of shipment or 8,000 hours of use, whichever occurs first, with the following exceptions: 1. Components for monitoring of physical variables such as temperature, pressure, or flow are warranted for ninety (90) days from date of receipt. 2. Elastomeric components and other parts or components subject to deterioration, over which the Company has no control, are warranted for sixty (60) days from date of receipt. 3. Internal batteries are warranted for ninety (90) days from the date of receipt. 4. The turbine only is warranted to be free from defects in material or workmanship for five (5) years or 40,000 hours whichever occurs first. The foregoing is in lieu of any warranty, expressed or implied, including, without limitation, any warranty of merchantability, except as to title, and can be amended only in writing by a duly authorized representative of the Company.
33373-001 Version A
iv
Contents Chapter 1: Introduction ... 1-1 1.1 General Instructions ... 1-1 1.2 Recommended Tools & Equipment ... 1-1 1.3 Recommended Maintenance Schedules ... 1-2 Chapter 2: Theory of Operation ... 2-1 2.1 General Device Description ... 2-1 2.2 Pneumatic System Overview ... 2-1 2.3 Oxygen Blending System... 2-2 2.4 Electronic Overview ... 2-2 Chapter 3: Disassembly and Assembly ... 3-1 3.1 General Instructions and Warnings ... 3-1 3.2 Required Tools ... 3-1 3.3 Disassembly and Reassembly Procedures... 3-2 3.4 Right Panel Containing the Power PCB ... 3-4 3.5 Front Panel P/N 16345A ... 3-5 3.6 Front Panel for VELA ColdFire 2 ... 3-6 3.7 Main PCB... 3-7 3.8 Flow Sensor Receptacle assembly ... 3-8 3.9 Exhalation Valve Assembly... 3-8 3.10 Blender Assembly ... 3-9 3.11 Turbine and Muffler Assembly ... 3-10 3.12 Inlet Filter Screen ... 3-11 3.13 Oxygen Sensor ... 3-11 3.14 Rear Panel ... 3-12 3.15 Fan and Filter Assembly ... 3-12 3.16 Manifold Base Assembly... 3-13 Chapter 4: Software Download Procedure ... 4-1 4.1 Prior to Software Download ... 4-1 4.2 Software Download ... 4-1 4.3 Ventilator Upgrade Procedure ... 4-4 Chapter 5: One-Year P.M. Procedure ... 5-1 5.1 Contents of PM kit P/N 11416... 5-1 5.2 General Instructions and Warnings ... 5-1 5.3 Required Tools ... 5-2 5.4 Procedure ... 5-2 5.5 Two Year PM ... 5-14 Chapter 6: Calibration Procedure... 6-1 6.1 Calibration... 6-1 6.2 Calibration and Test Kit... 6-2 Chapter 7: Operational Verification Procedure ... 7-1 7.1 UVT Functions Screen ... 7-1 7.2 Performance Test ... 7-2 7.3 Operational Verification Procedure Checklist... 7-7
33373-001 Version A
v
Chapter 8: Troubleshooting/Codes/Messages... 8-1 8.1 UVT Test Troubleshooting... 8-1 8.2 Delivered Volumes Test Troubleshooting ... 8-2 8.3 Monitored Volume Test Troubleshooting ... 8-2 8.4 FiO2 Performance Test Troubleshooting... 8-2 8.5 Battery Performance Test Troubleshooting ... 8-3 Chapter 9: Frequently Asked Questions ... 9-1 Chapter 10: Maintenance and Cleaning ... 10-1 10.1 Cleaning & Sterilization ... 10-1 10.2 Cleaning ... 10-1 10.3 Sterilization ... 10-2 10.4 Other Accessories ... 10-2 10.5 Recommended Periodic Maintenance ... 10-3 Chapter 11: Specifications ... 11-1 11.1 Oxygen Supply ... 11-1 11.2 Electrical Supply ... 11-1 11.3 Data Input / Output ... 11-2 11.4 Atmospheric & Environmental Specifications ... 11-3 11.5 Physical Dimensions ... 11-4 Appendix A: Contact and Ordering Information ... A-1 Appendix B: Reordering Instructions ... B-1 Appendix C: Schematics & Diagrams ... C-1 Appendix D: Index ... 1
33373-001 Version A
vi
Notices EMC Notice This equipment generates, uses, and can radiate radio frequency energy. If not installed and used in accordance with the instructions in this manual, electromagnetic interference may result. The equipment has been tested and found to comply with the limits set forth in EN60601-1-2 for Medical Products. These limits provide reasonable protection against electromagnetic interference when operated in the intended use environments described in this manual. The ventilator has been tested to conform to the following specifications: MIL-STD-461D:1993, MIL-STD-462D:1993, EN55011:1991, IEC 1000-4-2:1994, IEC 1000-43:1994, IEC 1000-4-4:1994, IEC 1000-4-5:1994, QUASI-STATIC:1993 This ventilator is also designed and manufactured to comply with the safety requirements of IEC 601-1, IEC 601-2-12, CAN/CSA-C22.2 No. 601.1-M90, and UL 2601-1.
MRI Notice This equipment contains electromagnetic components whose operation can be affected by intense electromagnetic fields. Do not operate the ventilator in a MRI environment or in the vicinity of high-frequency surgical diathermy equipment, defibrillators, or short-wave therapy equipment. Electromagnetic interference could disrupt the operation of the ventilator.
Intended Use Notice The Vela Ventilator is intended to provide continuous or intermittent ventilatory support for the care of individuals who require mechanical ventilation. The ventilator is a restricted medical device intended for use by qualified, trained personnel under the direction of a physician. Specifically, the ventilator is applicable for adult and pediatric patients weighing at least 5 kg (11 lbs), who require the following general types of ventilation support, as prescribed by an attending physician:
Positive pressure ventilation
Assist/Control, SIMV, or CPAP modes of ventilation
The ventilator is suitable for use in institutional and transport settings. It is not intended for use as an emergency medical transport ventilator or for homecare applications.
Regulatory Notice Federal law restricts the sale of this device except by or on order of a physician.
IEC Classification Type of Equipment: Medical Equipment, Class 1 type B Adult/Pediatric Lung Ventilator
33373-001 Version A
vii
Safety Information Please review the following safety information prior to operating the ventilator. Attempting to operate the ventilator without fully understanding its features and functions may result in unsafe operating conditions. Warnings and Cautions which are general to the use of the ventilator under all circumstances are included in this section. Some Warnings and Cautions are also inserted within the manual where they are most meaningful. Notes are also located throughout the manual to provide additional information related to specific features. If you have a question regarding the installation, set up, operation, or maintenance of the ventilator, contact VASYS Healthcare Customer Care as shown in Appendix A, Contact & Ordering Information.
Terms WARNINGS WARNINGS identify conditions or practices that could result in serious adverse reactions or potential safety hazards.
CAUTIONS CAUTIONS identify conditions or practices that could result in damage to the ventilator or other equipment.
NOTES NOTES identify supplemental information to help you better understand how the ventilator works.
Warnings Warnings and Cautions appear throughout this manual where they are relevant. The Warnings and Cautions listed here apply generally any time you operate the ventilator.
The VELA Ventilator is intended for use by a trained practitioner under the direction of a qualified physician.
When the ventilator is connected to a patient, a trained health care professional should be in attendance at all times to react to an alarm or other indications of a problem.
Alarm loudness must be set above ambient sound in order to be heard.
Always have an alternate means of ventilation available whenever the ventilator is in use.
The operator should not touch the electrical connectors of the ventilator or accessories, and the patient simultaneously.
Due to possible explosion hazard, the ventilator should not be used in the presence of flammable anesthetics.
An audible alarm indicates an anomalous condition and should never go unheeded.
33373-001 Version A
viii
Anti-static or electrically conductive hoses or tubing should not be used within the patient circuit.
If a mechanical or electrical problem is recognized while running the Operational Verification Tests, or while operating the ventilator, the ventilator must be removed from use and referred to qualified personnel for servicing. Using an inoperative ventilator may result in patient injury.
When a low gas supply alarm occurs, the oxygen concentration delivered to the patient will differ from that set on the O2 control setting.
A source gas failure will change the FIO2 and may result in patient injury.
The functioning of this equipment may be adversely affected by the operation of other equipment nearby, such as high frequency surgical (diathermy) equipment, defibrillators, shortwave therapy equipment, “walkie-talkies,” or cellular phones.
Do not block or restrict the Oxygen bleed port located on the instrument back panel. Equipment malfunction may result.
Electric shock hazard - Do not remove any of the ventilator covers or panels. Refer all servicing to an authorized Vyaire, service technician.
A protective ground connection by way of the grounding conductor in the power cord is essential for safe operation. Upon loss of protective ground, all conductive parts including knobs and controls that may appear to be insulated, can render an electric shock. To avoid electrical shock, plug the power cord into a properly wired receptacle, use only the power cord supplied with the ventilator, and make sure the power cord is in good condition.
Cautions The following cautions apply any time you work with the ventilator.
When replacing fuses, ensure that new fuses are of the same type and value as those being replaced. Incorrect fuses can cause damage to the ventilator.
A battery that is fully drained (i.e. void of any charge) may cause damage to the ventilator and should be replaced.
All accessory equipment that is connected to the ventilator must comply with CSA/IEC601/UL2601.
To avoid damage to the equipment, clean the air filter regularly.
The following cautions apply when cleaning the ventilator or when sterilizing ventilator accessories.
Do not sterilize the ventilator. The internal components are not compatible with sterilization techniques.
Do not gas sterilize or steam autoclave tubing adapters or connectors in place. The tubing will, over time, take the shape of the adapter, causing poor connection and possible leaks.
DO NOT submerge the ventilator or pour cleaning liquids over or into the ventilator.
33373-001 Version A
ix
Equipment Symbols The following symbols may be referenced on the ventilator or in accompanying documentation Symbol
Meaning General warning Caution This symbol indicates a FUSE. This symbol indicates INPUT. This symbol indicates OUTPUT This symbol indicates protective EARTH (ground). This symbol indicates the EQUIPOTENTIAL connection used to connect various parts of the equipment or of a system to the same potential, not necessarily being the earth (ground) potential (e.g., for local bonding). This symbol indicates TYPE BH equipment, which indicates equipment that provides a particular degree of protection against electric shock, particularly with regards to allowable leakage current and reliability of the protective earth connection. This symbol indicates the equipment is suitable for alternating current. This Symbol indicates the ON condition for a part of the equipment. When pressed the ventilator will operate from the MAINS voltage (if connected) or internal or external batteries if the battery charge is within operating specifications. Indicates ON (Power) Indicates OFF (Power)
ACCEPT
Horizontal return with line feed. Indicates ACCEPT entered values for a specific field. This symbol indicates CANCEL. Do not accept entered values. The ventilator continues to operate at previous settings.
CANCEL Pressing the button with this symbol will FREEZE the current display.
This symbol indicates a CONTROL LOCK.
This symbol represents a NEBULIZER.
33373-001 Version A
x
Symbol
Meaning This symbol indicates ALARM SILENCE
This symbol indicates ALARM RESET
Increase OXYGEN
Indicates VARIABLE ORIFICE FLOW SENSOR This symbol indicates DIRECT CURRENT (DC) This symbol indicates the INTERNAL BATTERY STATUS display
This symbol indicates INSPIRATORY HOLD
This symbol indicates EXPIRATORY HOLD
This symbol indicates MANUAL BREATH
33373-001 Version A
1-1
Chapter 1: Introduction 1.1 General Instructions When disassembling or assembling the VELA, refer to the pneumatic schematic, tubing diagram, and the wiring diagram shown in Appendix B and the appropriate schematics and assembly drawings for each assembly. The illustrations shown in this manual are for reference only, current revisions of these diagrams and schematics are available to qualified personnel from Vyaire, Technical Support. Always take standard ESD precautions when working on VELA ventilator systems. Ensure the ventilator is disconnected from the AC power supply before performing and repairs or maintenance. When you remove any of the ventilator covers or panels, immediately disconnect the internal battery “Molex” connector (see Figure 3-1) before working on the ventilator.
1.2 Recommended Tools & Equipment NOTE Use of a calibrated flow/volume analyzer will be necessary to confirm the function of the Vela. The flow/volume analyzer should be calibrated as per manufacturers’ recommendations. Long & short Philips screwdrivers Flat bladed screwdriver
1/8” ID Tubing tee P/N 00358 D (10pk)
¼” Nut Driver
1/8” ID silicone tubing P/N 04029 X (50ft)
5/16” Nut Driver
Adult Test Lung P/N 33754
11/32” Nut Driver
Adult Patient Circuit P/N 10684
Digital Volt Meter
Variable Orifice Flow Sensor assembly P/N 15972
Tack puller or Needle nosed pliers
Valve Body P/N 20005
Diagonal cutters
Tapered nipple P/N 00680
1” and ¾” open ended wrenches
Hex nut P/N 00822
Calibrated Pressure Manometer (cmH2O and psig)
Regulator P/N 6754
33373-001 Version A
1-2
Chapter 1: Introduction
1.3 Recommended Maintenance Schedules 1.3.1 Schedules Every 500 hours, the fan and ambient air filters should be cleaned and replaced if necessary. Every year, the following preventive maintenance procedure should be performed (see chapter 4 for instructions). This procedure includes:
Install PM kit P/N 11416
Replace the 40 psi Regulator and the Blender Screws
Replace the Internal Oxygen Sensor, P/N 27750-001 (Analytical Industries) or 27751-001 (Maxtec)
Perform verification procedures described in Chapter 4
Calibration of the transducers & solenoids if necessary.
Every two years, internal batteries P/N 16048, includes the battery tray should be replaced along with the annual PM parts and procedures. Maintenance on the VELA should only be carried out by a Vyaire trained and authorized service technician. Vyaire will make available to qualified technicians, service manuals and such items as circuit diagrams, component parts lists, calibration instructions and other information to assist in repair of those parts of the ventilator designated by the manufacturer as repairable items. The drawings, diagrams and schematics included in this manual are for reference only and may be updated separately from this manual after publication. For current revisions of all documentation, contact Vyaire, Technical Support at the numbers provided in Appendix A.
33373-001 Version A
2-1
Chapter 2: Theory of Operation 2.1 General Device Description The VELA Ventilator uses a revolutionary turbine gas delivery system with sophisticated microprocessor control. Its Graphical User Interface provides support for pediatric to adult patients. The VELA can deliver clinically advanced modes of ventilation like Pressure Support, APRV, NPPV and PRVC, and can be powered with an internal battery or AC power for a more extensive patient range.
2.2 Pneumatic System Overview The VELA ventilator pneumatic system is electromechanical and comprises four major subsystems, each containing several components. These systems are the flow delivery system, the exhalation system, the safety system and the inspiratory hold valve. Individual subsystems are discussed in detail below.
2.2.1 Flow Delivery System This electromechanical system controls all inspiratory flow to the patient. The system delivers flow to satisfy criteria for many breath types, including volume controlled, pressure controlled, pressure supported, APRV, NPPV and PRVC. The system comprises a turbine, differential pressure transducer, 2 auto-zero valves, and an optical encoder speed transducer. When a breath is initiated, the microprocessor controls the speed of the turbine to achieve the required flow rate. The speed and differential pressure transducer signals function as control inputs to ensure that the proper flow rate is delivered even when backpressure varies. Periodically, the auto zero valves activate to reference both sides of the differential pressure transducer to ambient pressure. The offset is recorded by the microprocessor, and is used as a correction for future pressure measurements. This compensates for long term and temperature drift. Materials exposed to patient gases include compatible plastics, aluminum, and plated steel.
2.2.2 Exhalation System The exhalation system controls the flow of gas from the patient’s lungs during the exhalation phase of a breath. This electromechanical subsystem is made up of an exhalation valve, a flow transducer, a differential pressure transducer, an airway pressure transducer, and three auto zero solenoid valves. During exhalation, the outflow of gases is regulated by the exhalation valve to achieve the set PEEP. The exhalation valve is comprised of an electromagnetic linear actuator operating against a mechanical poppet/seat. The gas flow travels through the flow transducer. The flow transducer is a variable orifice type and creates a differential pressure proportional to flow. This differential pressure is transmitted to the differential pressure transducer, which converts the pressure signal to an electrical signal. The microprocessor uses this signal for flow triggering and to monitor exhaled tidal volume. The airway pressure transducer reads pressure in the exhalation leg of the patient circuit. This signal is used as a feedback signal for controlling PEEP, pressure control, pressure support, and various pressure monitors. Periodically, the auto zero valves activate to reference the differential and airway pressure transducers to ambient pressure. The offset is recorded by the microprocessor, and is used as an offset for future pressure measurements. This compensates for long term and temperature drift. Materials exposed to patient gases include compatible plastics, aluminum, and stainless steel.
33373-001 Version A
2-2
Chapter 2: Theory of Operation
2.2.3 Safety System The mechanical safety system ensures that the patient can breath spontaneously from room air and that the patient pressure is limited to a maximum preset value in the event of a ventilator malfunction. This mechanical system consists of a pressure relief valve and a sub ambient relief valve. In the event of a ventilator malfunction that results in high pressure, the pressure is limited by a relief valve. The relief valve consists of a user-adjustable, spring-loaded poppet acting against a seat. In the event the ventilator fails to deliver a breath, the patient may inspire spontaneously by drawing room air through the sub ambient relief valve. Materials exposed to patient gas are aluminum, compatible rubber, and compatible plastics.
2.2.4 Inspiratory Hold Valve The inspiratory hold valve is an electromechanical solenoid valve. If activated, the inspiratory hold valve blocks flow between the flow delivery system and the patient. This valve is activate during inspiratory hold and maximum inspiratory pressure maneuvers. Materials exposed to patient gases are aluminum and compatible rubber and plastic.
2.3 Oxygen Blending System The oxygen blending system is made up of an O2 inlet transducer, an O2 inlet pressure regulator, seven solenoid valves, five flow orifices, one nebulizer orifice, an inlet filter, and an accumulator. When a breath is initiated, the turbine draws mixed gas from the accumulator. Filtered air is drawn into the accumulator through the filter. Oxygen is supplied to the accumulator through the solenoids and orifices. The microprocessor opens and closes the valves as required to supply the correct amount of oxygen to satisfy the O2 setting and the flow demand. The signal from the O2 inlet pressure transducer is used to compensate delivered O2 for O2 inlet pressure variations. The blender can be used to supply nebulized flow at 100% oxygen. A safety solenoid is used to shut off the flow of oxygen when the ventilator is turned off or has gone inoperative. The O2 inlet pressure regulator helps minimize variations in the oxygen supply. Surfaces exposed to patient gas are constructed from compatible plastics, plated steel, and aluminum. There is also an oxygen inlet port, which allows for low-flow titration of oxygen into the gas output of this device.
2.4 Electronic Overview The VELA ventilator electronic system is comprised of several subsystems, each containing numerous components. These subsystems are the GUI System, the Power System, the Main Microprocessor System, and the Exhalation and Flow Delivery systems. Individual subsystems are discussed in detail.
2.4.1 User interface module (UIM) The UIM consists of a 10.4-inch, 800x600 active matrix LCD with an analog resistive touch screen overlay, a back light inverter, a set of membrane key panels, an optical encoder, and the Main System PCB. Software and the touch screen provide a set of context sensitive soft keys. The membrane panel provides a set of hard (permanent) keys for dedicated functions. Selecting the function with a soft key and adjusting the setting using the optical encoder changes a parameter. A parameter is accepted or canceled by pressing the appropriate membrane key. The UIM performs all ventilator control functions, gas calculations, monitoring and user interface functions. The UIM uses a Graphical User Interface (GUI) via the active matrix SVGA LCD and
33373-001 Version A
2-3
Chapter 2: Theory of Operation
resistive touch screen to provide system and patient information to the user and to allow the user to modify ventilator settings. The Main System PCB handles all user interface requirements, including updating the active matrix liquid crystal display (LCD), monitoring the membrane keypad, analog resistive touch screen, and optical encoder for activity. The Main System PCB also performs all the input/output functions of the UIM, including RS-232 (GSP and VOXP), printer, video output, and IEEE 1073 Medical Information Bus (MIB).
Liquid Crystal Display The liquid crystal display (LCD) provides graphical and digital feedback to the clinician. The panel is a 10.4” SVGA, 800x600 pixel, active matrix LCD. The LCD is used to implement the graphical user interface (GUI). It provides all of the adjustable controls and alarms, as well as displays waveforms, loops, digital monitors and alarm status in real time.
Touch Screen The touch screen is a 10.4” analog resistive overlay on a piece of glass, which is placed over an LCD screen. The touch screen and the LCD together provide a set of software configurable soft keys. The software enables the keys to be context sensitive. The touch screen has a resolution of 1024x1024. Physically, the touch screen consists of two opposing transparent resistive layers separated by insulating spacers. Touching the screen brings the two opposing layers into electrical contact. The Y coordinate is determined by applying a voltage from top to bottom on the top resistive layer. This creates a voltage gradient across this layer. The point of contact forms a voltage divider, which is read by the analog-to-digital converter. The X coordinate is determined by applying a voltage from left to right on the bottom resistive layer. Again this creates a voltage gradient and the point of contact forms a divider, which is read with an analog-to-digital converter.
Membrane Panel The membrane panel provides a set of permanent dedicated keys, which enable control of ventilator functions. The membrane panel also provides visual display using embedded light emitting diodes (LEDs). The membrane panel consists of membrane switches, which are read by the microprocessor. The switches form a matrix of rows and columns. A key closure causes an interrupt to the microprocessor, which responds by scanning the key matrix to determine which key has been pressed.
Light Emitting Diodes (LED) Some of the membrane keys require LED’s to indicate when the key is active. The LED’s are embedded into the membrane panel.
Optical Encoder The optical encoder is used to modify control settings. A setting is selected by pressing a soft key on the touch screen and then modified by turning the optical encoder (data dial) to change the value. When the encoder is rotated two pulse streams are generated, phase A and B. When the encoder is turned clockwise, phase A leads B by 90 degrees. When the direction is counter clockwise, phase B leads A by 90 degrees. The electronics uses the phase information to drive an up-down counter, which is read by the microprocessor. The optical encoder is not interrupt-driven and therefore must be polled by the microprocessor.
Back Light Inverter The back light inverter converts 12 VDC into the high frequency AC voltage necessary to power the LCD back light, which is used to illuminate the LCD.
33373-001 Version A
2-4
Chapter 2: Theory of Operation
2.4.2 Power System The Power System conditions and controls electrical energy from the AC line input and the internal batteries. The Power System supplies 24VDC, 8VDC, and 5VDC to the Main System PCB. When energy is available from the AC line, the ventilator operates from this source, and also recharges the internal batteries. When AC line power is not available, the power system draws energy from the internal batteries. The power system uses energy efficient DC-to-DC converter technology to convert energy from the AC line or batteries to appropriate voltages and currents to supply power to ventilator components and systems.
2.4.3 Main System PCB The Main System PCB is comprised of three pressure transducers, an analog-to-digital converter, two digital-to-analog converters, solenoid valves, and the Watchdog and Hardware Fault Monitors. One of the pressure transducers measures the patient circuit pressure. This pressure is an input to the control system. A differential pressure transducer measures the pressure across the turbine. This pressure is also an input to the control system. A second differential pressure transducer is used to measure the flow at the outlet of the exhalation valve. This pressure is also an input to the control system. Analog to digital converters are used to change the analog pressure signals into measured binary numeric values for use by the microprocessor. Digital to Analog converters are used to change the binary numeric commands generated by the microprocessor in the control system into analog signals which drive the turbine and exhalation valve. The microprocessor also performs several repetitive tasks such as generating the refresh signals for the display system, cycling the A-to-D converters through a pattern of measurements from the multiple signal sources, and scanning the control panel for pressed buttons. Solenoid Valves and Valve Drivers (including the Auto Zero valves) are employed on the Circuit Pressure transducer and on the Turbine Differential Pressure Transducer. These valves allow the control systems software to compensate for long term drift and temperature induced zero shift in the pressure transducers by periodically rechecking the zero pressure readings. Similar solenoid valves are employed in the Oxygen Blending System. The valve drivers for the Auto Zero and Blender valves are similar. The Main System PCB controls all ventilator functions. All user settings for alarms, controls, ventilation mode, waveform, and monitoried data are stored here and are combined with measured pressure, flow, and speed data to cause the ventilator to function. The algorithms, formulae, and control functions which define ventilator behavior are contained in the software program executed by the microprocessor.
2.4.4 The Watchdog Circuit and Hardware Fault The Watchdog circuit requires the microprocessor to periodically send a signal. If the signal is not received by the Watchdog Circuit then the ventilator will be shut down. When the Watchdog shuts down the CPU it forces the ventilator hardware to a safe state. The Hardware Fault Monitors check the status of the power supplies to the ventilator electornics. If any is out of the safe operationg range, the ventilator will shut down and cannot be made to operate until the fault is corrected.
33373-001 Version A
2-5
Chapter 2: Theory of Operation
2.4.5 Exhalation System The electrical portion of the exhalation system is comprised of the Exhalation Valve Driver Circuitry. The driver converts the low voltage signal output by a D-to-A converter into a controlled constant current which energizes the linear solenoid positioner in the exhalation valve.
2.4.6 Flow Delivery System The electrical portion of the flow delivery system is comprised of a 3 Phase Brushless Motor Driver, and an Optical Speed Transducer. The 3 Phase Brushless DC Motor Driver converts the low voltage signal output by a D-to-A converter into three controlled currents which energize the three motor phases and cause the motor to create a torque, resulting in motor rotation. The torque generated is a function of current, and therefore of the control voltage from the D-to-A converter. The speed of rotation is monitored by the optical Speed Transducer. The transducer outputs a train of pulses with a frequency proportional to the rotational speed of the motor. This pulse train is a control feedback input to the microprocessor.
2.4.7 Oxygen Blending System The electrical portion of the oxygen blending system is made up of a safety solenoid, a pressure regulator set to 40 PSI, an O2 Inlet Transducer, five Solenoid Valves, one Nebulizer solenoid, and the driver circuitry for the solenoid valves. The Oxygen Blender Pressure Transducer measures the system gas pressure after the regulator so that O2 delivery can be compensated for inlet pressure fluctuations. The Solenoid Valves are energized and deenergized under software control by the Main System microprocessor to supply the correct amount of oxygen to satisfy the current O2 setting and current gas flow demand. The driver circuitry translates the binary logic signals presented by the microprocessor to larger voltage and currents suitable for energizing the Solenoid Valves.
33373-001 Version A
2-6
Chapter 2: Theory of Operation
This page intentionally left blank.
33373-001 Version A
3-1
Chapter 3: Disassembly and Assembly 3.1 General Instructions and Warnings When performing the procedures in this chapter, refer to the VELA wiring and tubing diagrams. Reference copies of these are located in Appendix B of this manual. Ensure that you follow these safety warnings and precautions:
Figure 3-1. Battery Disconnect Molex Connector
WARNING Always disconnect the main power cable before removing the instrument cover and disconnect the battery once the top cover and battery tray have been removed to prevent injury and/or damage to the VELA Ventilator System (Figure 3-2).
CAUTION The VELA contains ESD susceptible components. Ensure you are properly grounded through a current-limiting connection before performing any service or maintenance procedures, and store ESD susceptible electrical components in anti-static bags to prevent damage to the components.
NOTE When the batteries are disconnected, the system will automatically re-set the battery status memory and will initiate a 30-hour re-charge cycle upon re-connect. If the DC status light is not green after the initial charging period has expired, contact Vyaire tech support as described in Appendix A.
NOTE The terms left and right refer to a view from the front of the unit looking towards the rear.
3.2 Required Tools Long & short Philips screwdrivers Digital Volt Meter Flat bladed screwdriver Tack puller or Needle nosed pliers ¼” Nut Driver Diagonal cutters 5/16” Nut Driver 11/32” Nut Driver 7/8” Nut Driver 1” and ¾” open ended wrenches
33373-001 Version A