SERVOMEX LIMITED
SERVOPRO MultiExact Operator Manual Rev 4
Operator Manual
141 Pages
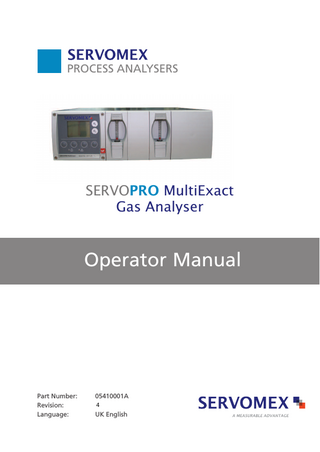
Preview
Page 1
PROCESS ANALYSERS
SERVOPRO MultiExact Gas Analyser
Operator Manual
Part Number: Revision: Language:
05410001A 34 UK English
MultiExact Gas Analyser
Contents
CONTENTS Section
Page
1 1.1 1.2 1.3 1.4
DESCRIPTION AND DEFINITIONS... 1 Scope of this manual ... 1 Safety information ... 1 Description ... 2 Ordering options ... 2
2 2.1 2.2 2.3 2.4 2.5
SPECIFICATION ... 5 General ... 5 Environmental limits... 5 Electrical data ... 6 Sample gas ... 7 Calibration gas ... 8
3
UNPACK THE ANALYSER ... 11
4 4.1 4.2 4.3 4.4 4.5 4.6 4.7 4.8 4.9 4.10
ANALYSER USER INTERFACE ... 12 Introduction ... 12 Start-up and measurement screens ... 12 Soft key legends ... 14 System and measurement status icons ... 15 Scroll bars ... 16 Menu options/screens and password protection ... 16 The menu screen ... 18 The settings screen ... 19 The information screen ... 19 Editing on-screen data ... 20
5 5.1 5.1.1 5.1.2 5.1.3 5.1.4 5.2 5.2.1 5.2.2 5.2.3 5.2.4 5.2.5 5.2.6 5.2.7 5.3 5.4 5.4.1 5.4.2 5.4.3 5.4.4
INSTALLATION AND SET-UP ... 21 Mechanical installation... 21 Bench mounting ... 21 Panel mounting ... 21 Rack with slide mounting ... 23 Valve block connections (option) ... 26 Electrical Installation ... 27 Electrical Safety ... 27 Analogue output connections ... 28 Fault and range relay connections ... 29 Alarm and status relay connections (option) ... 30 Auto validate/calibrate connections (option) ... 31 Modbus RS485 and ethernet connections (option) ... 33 Connect the electrical supply... 34 Connect the sample/calibration gas pipeline(s) ... 35 Switch on/set-up ... 36 Selecting the security level and password(s) ... 36 Selecting the security level ... 37 Changing passwords ... 38 Adjusting the contrast ... 38
05410001A / Revision 4
i
Contents
ii
MultiExact Gas Analyser
5.4.5 5.4.6 5.4.7 5.4.8 5.5 5.5.1 5.5.2 5.5.3 5.5.4 5.5.5 5.5.6 5.5.7 5.6 5.7 5.7.1 5.7.2 5.7.3 5.7.4 5.8 5.8.1 5.9 5.9.1 5.9.2 5.10 5.11 5.11.1 5.11.2 5.11.3 5.11.4 5.12
Adjusting the backlight timer... 39 Setting the clock ... 39 Changing regional settings ... 40 Selecting communications type ... 40 Setting up automatic validation/calibration (option) ... 41 Overview of automatic validation/calibration ... 41 Automatic validation/calibration sequence ... 42 Remote calibration or automatic validation/calibration ... 45 Automatic validation/calibration target and tolerance ... 46 Automatic validation/calibration type and mode ... 47 Automatic validation/calibration phases ... 47 Automatic validation/calibration timers ... 49 Calibration linking ... 50 Configuring and using the mA outputs (option) ... 51 Overview ... 51 Introduction to the mA output parameters ... 51 Setting up the mA output parameters ... 53 Calibrating the mA output ... 56 Configuring and using the voltage outputs (option) ... 57 Overview ... 57 Correcting O2 measurements for background gases (purity or control only) 57 Overview of measurement errors ... 57 Entering a cross-interference (X-Interference) compensation ... 58 Selecting display units ... 58 Configuring the measurement alarms ... 60 Alarm modes and levels ... 60 Latching/non-latching alarms... 62 Hysteresis levels ... 62 Viewing the measurement alarm status ... 63 Setting up the flow alarm (option) ... 64
6 6.1 6.2 6.2.1 6.2.2 6.2.3 6.2.4 6.3 6.4
CALIBRATION ... 66 Manual calibration ... 66 Automatic validation/calibration ... 68 Initiating an automatic validation/calibration ... 68 Automatic validation/calibration status indications ... 69 Stopping an automatic validation/calibration ... 70 Viewing validation/calibration history ... 71 Calibrating the pressure transducer (O2 purity only) ... 72 Calibrating the flow alarm (option) ... 73
7 7.1 7.2 7.2.1 7.2.2 7.2.3 7.3 7.4 7.5
GENERAL OPERATION ... 74 Checking the relay signal outputs ... 74 Pressure Compensation (O2 purity and control only) ... 75 Introduction ... 75 Switching pressure compensation on/off ... 75 Viewing pressure effected measurements (option) ... 76 Viewing flow levels (option) ... 76 Checking the mA output (option) ... 77 Checking the voltage output (option) ... 77
05410001A / Revision 4
MultiExact Gas Analyser
Contents
7.6
Switching off the analyser ... 77
8 8.1 8.2 8.3 8.4 8.5 8.6 8.7
ROUTINE MAINTENANCE ... 78 Cleaning the analyser ... 78 Inspecting/replacing the fuse (when necessary) ... 78 Inspecting the optional filter element (O2 purity / control only) ... 80 Inspecting the filter element (CO2 / N2O trace only) ... 81 CO2 scrubber ... 82 Use of the analyser with toxic gases ... 82 Preventative maintenance ... 83
9 9.1 9.1.1 9.1.2 9.2 9.2.1 9.2.2 9.3 9.4
FAULT FINDING ... 84 Fault, maintenance required and SIP statuses ... 84 Status definitions ... 84 Status annunciations ... 84 Viewing messages ... 90 Active messages ... 90 View history messages ... 90 Diagnostics ... 91 General fault finding... 92
10 10.1 10.2
STORAGE AND DISPOSAL... 95 Storage ... 95 Disposal ... 95
11
SPARES ... 96
A1 A1.1 A1.2 A1.3 A1.4 A1.5
RS232 CONNECTION DETAILS ... 97 Overview ... 97 Connecting the analyser to a PC ... 98 Configuring the RS232 serial output parameters ... 98 ® Capturing data using Windows and Hyper Terminal™ ... 99 Configuration transfer ... 100
A2
SERIAL OUTPUT FORMATS... 103
A3 A3.1 A3.2 A3.3 A3.4 A3.5 A3.6 A3.7 A3.8 A3.9 A3.10 A3.11 A3.12 A3.13 A3.14 A3.15
IMPLEMENTATION GUIDE FOR MODBUS COMMUNICATIONS (OPTION)104 Introduction ... 104 References ... 104 Modbus Setup ... 104 Supported function codes ... 105 Exception codes ... 105 Addressing ... 105 Floating point numbers ... 106 System data mapping ... 106 Transducer data mapping ... 106 System Fault Mapping ... 108 Transducer fault and alarm mapping ... 109 System set-up mapping ... 112 Transducer set-up mapping ... 112 System control ... 115 Transducer control ... 115
05410001A / Revision 4
iii
Contents
MultiExact Gas Analyser
A4 A4.1 A4.2
CONFIGURING THE MODBUS PARAMETERS (OPTION) ... 117 RS485 ... 117 TCP (Ethernet) ... 119
A5
DISPLAY UNIT CONVERSION FACTORS... 120
A6
SAMPLE WETTED MATERIALS ... 121
A7
DISPOSAL IN ACCORDANCE WITH THE WASTE ELECTRICAL AND ELECTRONIC EQUIPMENT (WEEE) DIRECTIVE ... 123
A8
COMPLIANCE AND STANDARDS INFORMATION ... 124
A9 A9.1 A9.2 A9.3 A9.4 A9.5 A9.6 A9.7
PERFORMANCE DATA ... 125 O2 purity measurement ... 125 Performance data: O2 control measurement ... 126 Performance data: O2 trace measurement ... 127 Performance data: CO2 trace measurement ... 128 Performance data: N2O trace measurement ... 129 Performance data: TCD Argon in N2, O2, air or N2 in argon ... 130 Performance data: flow alarm ... 131
A10
RECOMMENDED CALIBRATION PERIODS ... 132
A11
CROSS INTERFERENCE OFFSETS ... 133
®
Windows and Excel are registered trademarks of Microsoft Corporation.
™
HyperTerminal is a trademark of Hilgraeve Inc.
©
This manual is copyright, and no part of it may be reproduced without Servomex's written approval.
iv
05410001A / Revision 4
MultiExact Gas Analyser
1 – Description and definitions
1
DESCRIPTION AND DEFINITIONS
1.1
Scope of this manual This manual provides installation, operation and routine maintenance instructions for the SERVOPRO MultiExact Gas Purity Analyser, abbreviated to "analyser" in the remainder of this manual.
1.2
Safety information Read this manual and ensure that you fully understand its content before you attempt to install, use or maintain the analyser. Important safety information is highlighted in this manual as WARNINGs and CAUTIONs, which are used as follows: WARNING Warnings highlight specific hazards which, if not taken into account, may result in personal injury or death.
CAUTION Cautions highlight hazards which, if not taken into account, can result in damage to the analyser or to other equipment or property.
This manual also incorporates 'Be aware of' information, which is used as follows:
+
This highlights information which it is useful for you to be aware of (for example, specific operating conditions, and so on).
05410001A / Revision 4
1
1 – Description and definitions
1.3
MultiExact Gas Analyser
Description The analyser is designed to meet the needs of the control and product quality applications of industrial gas producers and users, who require fast, accurate and reliable gas analysis. The analyser can support up to two gas measurements, using paramagnetic, zirconia infrared and thermal conductivity transducers to determine the content of gas samples. Gas sample measurements are shown on the analyser display, and can also be output to a serial device connected to the analyser, or as milliAmp (mA) / voltage outputs, or over a selection of digital communications (Modbus RS485 or TCP and Profibus). The analyser conforms to the requirements of the NAMUR (Normenarbeitsgemeinschaft für Mess Und Regeltechnik in der Chemischen Industrie) standards NE43 (4 – 20 mA output) and NA64 (status outputs). The analyser is simple to operate, with an intuitive user interface. The analyser is 3U in height and is suitable for 19 inch rack, panel or bench mounting. The analyser requires little routine maintenance, other than calibration which is essential for the accuracy of sample gas measurements (see Section 6) and replacement of filter / scrubber elements (if fitted: see Sections 8.3, 8.4 and 8.5).
1.4
Ordering options For the latest ordering options please contact your local Servomex agent or visit www.servomex.com.
2
05410001A / Revision 4
MultiExact Gas Analyser
1
2
3
4
DA/1142/C
A
1 – Description and definitions
5
SERVOMEX
FILTER
SERVOPRO MultiExact
11
B
10
9
1
FILTER
Serial No. 05410/P0001
8
7
2
6
3
12
13
14
15
SERVOMEX
Bypass
SERVOPRO MultiExact
11
A. B.
10
9
Sample
Bypass
Sample
Serial No. 05410/P0001
8
7
6
Analyser with external filters Analyser with flowmeters
Key Description
Key Description
1. 2. 3. 4. 5. 6. 7. 8.
9. 10. 11. 12. 13. 14. 15.
Display Sample 2 gas label Sample 1 gas label Sample 2 external filter * Sample 1 external filter * Soft key 4 Soft key 3 Fault LED
* †
Soft key 2 Alarm LED Soft key 1 Sample 2 bypass flowmeter † Sample 2 flowmeter Sample 1 bypass flowmeter † Sample 1 flowmeter
TCD, O2 purity and O2 control transducers only. Pressure-driven transducers only.
Figure 1 – Front of the analyser
05410001A / Revision 4
3
1 – Description and definitions
MultiExact Gas Analyser
Key Description
Key Description
1. 2. 3. 4. 5. 6. 7. 8.
12.
9. 10. 11.
Regional compliance symbols ** Transducer 1 sample gas inlet # WEEE compliance symbol Transducer 2 sample gas inlet * Transducer 2 sample gas inlet † AC supply voltage symbol Functional earth (ground) terminal Electrical supply plug and on/off switch Ethernet or profibus connector (option) Earth (ground) terminals for cable screening Transducer 2 mA output/voltage output connector
13. 14. 15. 16. 17. 18. 19. 20. 21. 22. 23.
Transducer 2 status relay connector (option) Transducer 2 auto val/cal connector (option) Transducer 1 mA output/voltage output connector # Transducer 1 status relay connector (option) # Transducer 1 auto val/cal connector (option) # RS485 connector (option) "Caution – refer to manual" symbol RS232 connector "Earth (ground)" symbol Transducer 2 sample gas outlet † Transducer 2 sample gas outlet * Transducer 1 sample gas outlet #
*
CO2 and N2O trace transducers and valve block. TCD, O2 trace, O2 purity and control transducers. # Analysers configured for 2 measurements only. ** This product has been tested to the requirements of CAN/CSA–C22.2 No. 61010–1, second edition, including Amendment 1 or a later version of the same standard incorporating the same level of testing requirements. †
+
Optional external filters (not shown) may be fitted to the sample gas inlet (1, 2) on an analyser with a CO2 or N2O trace transducer. Refer to Section 8.4 for details of these external filters. Trace O2 transducers have internal oil and particle filters which are not replaceable. Figure 2 – Rear of the analyser
4
05410001A / Revision 4
MultiExact Gas Analyser
2
2 – Specification
SPECIFICATION WARNING The protection, accuracy, operation and condition of the equipment may be impaired if the analyser is not installed in accordance with the requirements of this and subsequent sections of the manual.
2.1
General Dimensions: length x height x width Rack mountable analyser (L x H x W)
478 x 133 x 435 mm (18.8 x 5.2 x 17 in.) * 478 x 133 x 483 mm (18.8 x 5.2 x 19 in.) †
Bench mounted analyser (L x H x W)
478 x 146 x 435 mm (18.8 x 5.7 x 17 in.) # 478 x 180 x 435 mm (18.8 x 7 x 17 in.) ‡
Mass
< 12 kg
Electrical supply requirements
See Section 2.3
* † # ‡
2.2
* Add 100 mm to length (L) if valve block is fitted to allow for the connector and cable.
Without 19-inch rack mounting brackets. With 19-inch rack mounting brackets fitted. With front mounting feet retracted. With front mounting feet extended.
Environmental limits Equipment is suitable for indoor use only Ambient temperature range Operation
5 to 45 °C
Storage
–20 to 60 °C
Operating ambient pressure range
101.3 kPa ± 10% (1.013 bar ± 10%)
Operating ambient humidity range
10 to 90% RH, non-condensing
Operating altitude range
–500 * to 2000 † metres
Ingress protection
IP20
* †
Below sea level. Above sea level.
05410001A / Revision 4
5
2 – Specification
2.3
MultiExact Gas Analyser
Electrical data Electrical supply Voltage
100 to 240 Vac, 50 to 60 Hz (± 10% maximum fluctuation)
Fuse rating / type
T 3.15 AH / 250 V size: 20 x 5 mm
Maximum power consumption
100 VA
Interface signal relay ratings *
30 V (dc or ac) / 1 A
mA output (active) Maximum load resistance
1 K Ohms
Isolation voltage (to earth)
500 V (dc or ac)
Output range Normal sample measurement
0 to 20 mA or 4 to 20 mA †
Fault condition
0 mA or 21.5 mA †
Under range #
0 – 4 mA
Voltage output (active) Maximum load resistance
100 K Ohms
Isolation voltage (to earth)
500 V (ac or dc)
Output range Normal sample measurement
0 to 10 V
Fault condition
0 or 10.75 V
Under range #
Not applicable
Signal / voltage / mA / RS485 output terminals suitable for
* † #
6
Flexible conductors
0.5 to 1.5 mm² (20 to 16 AWG)
Solid conductors
0.5 to 1.0 mm² (20 to 18 AWG)
The relay output signals are volt-free signals. User selectable: see Sections 5.7.2 and 5.7.3. Only available when the 4 to 20 mA output range is selected: see Sections 5.7.2 and 5.7.3.
05410001A / Revision 4
MultiExact Gas Analyser
2.4
2 – Specification
Sample gas
+
The sample gases must be non flammable, clean, non-corrosive, free from oil and condensates and compatible with the materials listed in Appendix A6.
Paramagnetic transducer (% O2) Flow rate *
100 to 250 ml min-1
Dew point
5 °C below ambient temperature (minimum)
Temperature
5 to 45 °C
Particulate size
< 2 µm (2 micron)
Zirconia transducer (trace O2) Flow rate *
200 to 400 ml min-1
Dew point
5 °C below ambient temperature (minimum)
Temperature
5 to 45 °C
Particulate size
< 2 µm (2 micron)
Infrared (GFX) transducer (trace) Flow rate *
200 to 500 ml min-1
Dew point
5 °C below ambient temperature (minimum)
Temperature
5 to 45 °C
Particulate size
< 2 µm (2 micron)
Thermal Conductivity transducer (%)
*
Flow rate *
100 to 200 ml min-1
Dew point
5 °C below ambient temperature (minimum)
Temperature
5 to 45 °C
Particulate size
< 2 µm (2 micron)
The flow rates apply to flow-driven transducers only. On pressure-driven transducers, the sample gas pressure must be in the range 14 to 56 kPa (2 to 8 psig).
05410001A / Revision 4
7
2 – Specification
2.5
MultiExact Gas Analyser
Calibration gas
+
The calibration gases must be clean, non-corrosive, free from oil and condensates and compatible with the materials listed in Appendix A6.
+
For optimum calibration results, the calibration gas flow rate/pressure should be the same as the flow rate/pressure of the gases to be sampled.
O2 purity transducer calibration gases High calibration setpoint
0.5 – 100% O2 (100% O2 N4 [99.99] recommended)
Low calibration setpoint
0 – 99.5% O2 (0% zero grade nitrogen recommended)
Minimum difference
0.5%
Low calibration tolerance level * Calibration gas < 5% O2 Calibration gas ≥ 5% O2
± 0.5% O2 ± 10% O2
High calibration tolerance level * Calibration gas < 5% O2 Calibration gas ≥ 5% O2
± 0.5% O2 ± 10% O2
O2 control transducer calibration gases
8
High calibration setpoint
0.5 – 100% O2
Low calibration setpoint
0 – 99.5% O2 (0% zero grade nitrogen recommended)
Minimum difference
0.5%
Low calibration tolerance level * Calibration gas < 5% O2 Calibration gas ≥ 5% O2
± 0.5% O2 ± 10% O2
High calibration tolerance level * Calibration gas < 5% O2 Calibration gas ≥ 5% O2
± 0.5% O2 ± 10% O2
05410001A / Revision 4
MultiExact Gas Analyser
2 – Specification
TCD transducer calibration gases High Calibration setpoint
90 – 110% of range**
Low Calibration setpoint
-10 – 10% of range**
Minimum Calibration difference between low and span
85% of range**
Low Calibration tolerance level *
± 10%
High Calibration tolerance level *
± 10%
* Range and background gas as per analyser specification. N2O and CO2 trace transducer calibration gases High calibration setpoint
40 to 120% of full scale (80 to 110% pref)
Low calibration setpoint
0% (zero grade nitrogen recommended)
Minimum calibration difference between low and span
8% of full scale
Low calibration tolerance level *
± 10% of full scale
High calibration tolerance level *
± 20% of full scale
O2 trace transducer calibration gases High calibration setpoint
18 to 25% O2
Low calibration setpoint #
0.01 ppm to 5000 ppm O2
Minimum calibration difference between low and span
17.5% O2
Low calibration tolerance level *
± 10% O2
High calibration tolerance level *
± 10% O2
#
The low calibration gas must be a high quality certified mixture (usually nitrogen N6.0) containing trace Oxygen. Mixtures between 1000 ppm to 4000 ppm are preferred. * If, during a calibration or validation routine, the measurement is outside the specified range, a status message is displayed to indicate that there may be a problem (for example, the wrong calibration gas has been introduced, or the transducer has drifted excessively). The status can be over-ridden but the history will still remain. ** Range and background gas as per analyser specification. For optimal performance use either low or high calibration point to be a single component gas.
05410001A / Revision 4
9
2 – Specification
MultiExact Gas Analyser
CAUTION It is recommended that sample/calibration gas flow is monitored or the flow alarm option is purchased from Servomex to ensure a representative sample is being measured for control systems.
10
05410001A / Revision 4
MultiExact Gas Analyser
3
3 – Unpack the analyser
UNPACK THE ANALYSER WARNING The analyser is heavy (see Section 2.1). Care must be taken when handling. it is recommended that they are lifted with hands positioned on either side on the base of the chassis. 1.
Remove the analyser and any other equipment from its packaging.
2.
Remove any protective plastic covers from the sample gas inlets and outlets on the rear of the analyser (see Figure 2).
+
It is advisable that the protective covers are kept on just prior to fitting.
3.
Inspect the analyser and the other items supplied, and check that they are not damaged. If any item is damaged, immediately contact Servomex or your local Servomex agent.
4.
Check that you have received all of the items that you ordered. If any item is missing, immediately contact Servomex or your local Servomex agent.
5.
If you do not intend to use the analyser immediately: • Refit any protective plastic covers. • Place the analyser and any other equipment supplied back in its protective packaging. • Store the analyser as described in Section 10.1. Otherwise, read Section 4 (Analyser user interface), then continue at Section 5 onwards to install, set up, and use the analyser.
+
Retain the shipping documentation and packaging for future use (for example, return of the analyser to Servomex for servicing or repair).
05410001A / Revision 4
11
4 – Analyser user interface
4
ANALYSER USER INTERFACE
+ 4.1
MultiExact Gas Analyser
Throughout this manual, reference is made to product ordering options (such as "auto validate") which must be specified at the time of purchase. Associated menus and menu options will not be available if your analyser does not have the corresponding product options.
Introduction The analyser user interface comprises the following (shown on Figure 1):
4.2
Display
Shows various screens: see Section 4.2 onwards
Soft keys
The function of each of the soft keys depends on the screen currently being shown on the display: see Section 4.2
Alarm LED
On when an alarm condition exists: see Section 5.11
Fault LED
On when a fault condition exists: see Section 9
Start-up and measurement screens When you first switch on the analyser, a 'start-up screen' is displayed while the analyser carries out a self-test. The start-up screen shows the Servomex name, a 'self-test time elapsed/remaining' indicator, and messages identifying the tasks being carried out as part of the self-test. The screen will initially display the "System Check" task message. The measurement screen is then displayed, as shown in Figure 3 below. Note that: • If your analyser is configured for a single sample gas measurement, the 1-measurement screen will be shown, as in detail A. • If your analyser is configured for two sample gas measurements, the 2-measurement screen will be shown, as in detail B.
12
05410001A / Revision 4
MultiExact Gas Analyser
4 – Analyser user interface
(A) 1 measurement screen: Gas being measured Measurement units Pressure compensation indicator * Transducer number ("1" always shown)
Current measurement Fault icon (see Section 9)
Status icon bar (see Section 4.4)
Alarm icon (see Section 5.11.1)
Software health indicator
mA Range (see Section 5.7.1)
Soft key legends
(B) 2 measurement screen: Gases being measured Measurement units
Transducer numbers
Pressure compensation indicator * Current measurement 1
#
Service in progress icon (see Section 6.2.2)
Flow icon (see Section 7.3)
mA Ranges (see Section 5.7.1)
Status icon bar (see Section 4.4)
Current measurement 2 Maintenance required icon (see Section 6.2.2)
Software health indicator
Soft key legends
* #
Only shown when unit is installed with O2 purity measurement and pressure compensation is on: see Section 7.2. Only shown when unit is installed with flow alarm option.
Figure 3 – The measurement screen
05410001A / Revision 4
13
4 – Analyser user interface
+ + 4.3
MultiExact Gas Analyser
During normal analyser operation, the software health indicator continuously moves from left to right and then back again, below the status icon bar. If the indicator stops moving, this means that the analyser is not operating correctly, and you must refer to Section 9. If no soft key is pressed for 10 minutes, the measurement screen will be automatically displayed. (You will also then have to enter the password again to access any password-protected screens: refer to Figure 4 and to Section 4.6.)
Soft key legends The four soft key legends at the bottom of the measurement screen (Figure 3) correspond to the four soft keys on the front of the analyser. (The first, left-most, legend corresponds to the function of soft key 1, the second legend corresponds to the function of soft key 2, and so on.) On the measurement screen, the soft key functions are as follows: Legend
*
14
Meaning
Function (when soft key pressed)
Menu
Displays the menu screen: see Section 4
Calibrate *
Displays the calibrate screen: see Sections 6 and 6.2
Alarm *
Displays the alarm option screen: see Section 5.11.1
–
None (no effect)
These soft keys are 'shortcuts' to the described functions, which are also accessible from the menu structure.
05410001A / Revision 4
MultiExact Gas Analyser
4 – Analyser user interface
Other soft key legends which are used on the various screens are as follows: Legend
4.4
Meaning
Function (when soft key pressed)
Back
Cancels the current screen and displays the previous screen in the menu structure
Accept
Accepts the currently selected option or data. (A new screen may be displayed accordingly.)
Edit
Allows the highlighted data to be edited
Up
Moves the cursor up a list (or increases a digit during editing)
Down
Moves the cursor down a list (or decreases a digit during editing)
Left
Moves the cursor left
Right
Moves the cursor right
Stop
Stops an automatic validation/calibration
System and measurement status icons System status is on the status icon bar and can be shown with a fault icon or a maintenance required icon, see table below. Measurement status is on the right hand side of the measurement reading and can be shown with a fault icon, a maintenance required icon, a service in progress icon or a warming icon, see table below. Icon
Meaning Indicates that a fault has been detected Indicates that maintenance is required Indicates that service is in progress Indicates that the transducer is warming up
To determine the cause of these status icons, see Section 9.2.
05410001A / Revision 4
15