Smith & Nephew
Orthopaedic Processing Cleaning, Disinfection and Sterilization Guide
16 Pages
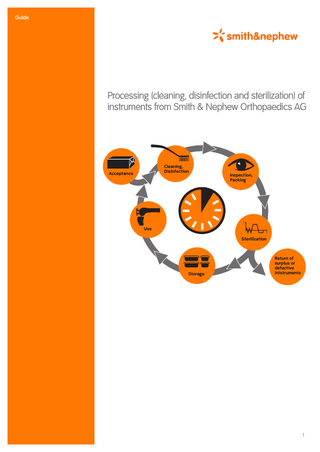
Preview
Page 1
Guide
Processing (cleaning, disinfection and sterilization) of instruments from Smith & Nephew Orthopaedics AG
Cleaning, Disinfection
Acceptance
Inspection, Packing
T
Use
t
Sterilization
Storage
Return of surplus or defective intstruments
1
Contents
1
Purpose ... 3
2
Scope ... 3
3
General instructions... 3
4
Warnings... 3
5
Classification of reusable instruments from Smith & Nephew Orthopaedics AG... 4
5.1
Definition of product groups... 4
6
Pretreatment before cleaning:... 5
6.1
Pretreatment procedure... 5
7
Manual cleaning / disinfection... 5
7.1
Manual cleaning procedure... 6
7.2
Manual disinfection procedure... 6
8
Machine cleaning/disinfection with WD (washer and disinfector)...7
8.1
Machine cleaning / disinfection procedure... 8
9
Inspection and maintenance... 9
10
Packing...10
11
Sterilization...10
11.1
Steam sterilization...10
12
Storage...11
13
Restriction on reprocessing...11
14
Material resistance...11
15
Special instructions... 12
Guide to the processing of instruments from Smith & Nephew Orthopaedics AG
1 Purpose This document was prepared to provide instructions for the care, maintenance, cleaning, and sterilization of the medical devices produced by Smith & Nephew Orthopaedics AG. These methods were developed using standard equipment and practices common to health care facilities. Validation testing to support these instructions was based on recognized guidelines and standards for reusable devices.
2 Scope These instructions apply to all reusable medical devices from Smith & Nephew Orthopaedics AG that are initially supplied nonsterile and require the user to process them after initial/subsequent use.
3 General instructions •
• • •
• • • • • • •
ll instruments must be cleaned, disinfected and sterilized before each use particularly before the A first use after delivery, since all instruments are supplied non-sterile (clean and disinfect instruments after removing the protective transport packaging; sterilize after packing in sterilization trays). Thorough cleaning and disinfection is an essential requirement for effective sterilization. Use only freshly prepared solutions. Please separate contaminated instruments during use and do not place them back in the instrument tray to avoid further contamination of the other instruments in the tray. Please ensure the following as part of your responsibility for sterility of the instruments during use: – Only properly validated equipment- and product-specific cleaning/disinfection and sterilization procedures should be used. – The equipment employed (WD (washer-disinfector), sterilizer) is regularly maintained and inspected. – The validated parameters are observed during each cycle. An automated procedure (WD (washer-disinfector), sterilizer) should be used wherever possible to clean and disinfect the instruments. Since a manual procedure is much less effective and reproducible – even using sonication – it should be employed only if an automated procedure is not available. In both cases, the instruments should be pretreated. The user is responsible for ensuring that suitably detailed standard operating procedures are available if a manual cleaning and disinfection procedure is employed. After cleaning/disinfection, the instruments are put back in their appropriate places in the instrument tray. The fully loaded instrument tray should be then sterilized. Please also observe the legal requirements applicable in your country and the hygiene regulations of the medical practice or hospital. All procedures described in this document must only be conducted by trained personnel.
4 Warnings • • •
• • •
•
Do not use any rinse aids (residues!). Do not use any instrument care products. Instrument oil may be used only for products in the group of “Products with a joint" and only then if the joints are stiff -> see also the “Inspection and maintenance” and “Special instructions” sections. The cleaning agents must have a pH between 5.5 and 11 -> see also the “Material resistance” section (recommendation: alkaline cleaners with pH > 10). Always observe the cleaning agent and disinfectant concentrations, temperatures, contact times and final rinse instructions specified by the manufacturer. Only sterile or near-sterile water (max. 10 microorganisms/ml) with a low endotoxin content (max. 0.25 endotoxin units/ml) may be used for the final rinse (e.g. purified water / highly purified water), The air used for drying must be oil-free, near-sterile and have a low particle count. 3
Guide to the processing of instruments from Smith & Nephew Orthopaedics AG
5 Classification of reusable instruments from Smith & Nephew Orthopaedics AG This cleaning guide for reusable instruments from Smith & Nephew Orthopaedics AG is based on product groups that are characterized by geometrical aspects of the instruments.
5.1 Definition of product groups Seven product groups can be differentiated based on geometrical features of the instruments from Smith & Nephew Orthopaedics AG. Product Group
Description of Product attribute
A/C
Products with ring lumen
B/D
Products with through lumen
D
Products with blind lumen
F
Products with diffuse lumen (not to be assigned to another group)
G
Products with joints
H
Products without lumen
O
Products with O-Rings
T
Trays
4
Guide to the processing of instruments from Smith & Nephew Orthopaedics AG
6 Pretreatment before cleaning: Coarse contaminants must be removed from the instruments directly after use (within a maximum of 2 hours):
6.1 Pretreatment procedure • • • • • • •
Disassemble the instruments as much as possible Rinse the instruments for at least 1 min under running water (T < 35°C/95°F) Remove all visible contaminants manually using a clean soft brush (or a clean, soft, lint-free cloth) that is used only for this purpose; never use wire brushes or steel wool Brush out cavities, holes and crevices with a suitably sized clean, soft brush using rotary movements. Ensure that the full width and depth of the relevant cavity, hole or crevice is reached. Next, rinse all cavities, holes and gaps at least five times using a disposable syringe -> for volumes see “Special instructions” section Move and/or slide moving parts back and forth at least 5 times and remove contaminants with a clean, soft brush Rinse them again for at least 1 min under running water (T < 35°C/95°F)
If you use a cleaning agent or disinfectant during the pretreatment – e.g. for health and safety reasons – please note that this must be aldehyde-free (otherwise there is a risk of blood contaminant fixation), of proven efficacy (e.g. VAH/DGHM or FDA/EPA approval/clearance/registration, CE marking), and be suitable for instrument disinfection and compatible with the instruments (see “Material resistance” section). Please note that the disinfectant used during pretreatment is for personal protection only and is not intended to replace the post-cleaning disinfection step.
7 Manual cleaning / disinfection Please ensure that the selected cleaning agents and disinfectants satisfy the following conditions: • they must be suitable for cleaning or disinfecting metal or plastic instruments, • the cleaning agent – if used – must be suitable for cleaning by sonication (no foam formation), • a suitable disinfectant of proven efficacy (e.g. VAH/DGHM or FDA/EPA approval/clearance/ registration or CE marking) which is compatible with the cleaning agent must be used • all chemicals used must be compatible with the instruments (see "Material resistance" section). • only sterile or near-sterile water (max. 10 microorganisms/ml) with a low endotoxin content (max. 0.25 endotoxin units/ml) may be used for the final rinse (e.g. purified water/highly purified water), • the air used for drying must be filtered, i.e. oil-free, near-sterile and have a low particle count • the WD must be regularly maintained and inspected Combined cleaning agents/disinfectants should be avoided if possible. Only if the contamination is minimal (no visible contaminants) may combined cleaning agents/disinfectants be used (not applicable for the USA).
5
Guide to the processing of instruments from Smith & Nephew Orthopaedics AG
7.1 Manual cleaning procedure • • • • • • • • • • • • •
isassemble the instruments as much as possible D Place the disassembled instruments in the ultrasonic cleaning bath, ensuring that the instruments are adequately covered. Ensure that the instruments are not touching each other. Assist the cleaning process by completely brushing all internal and external surfaces with a soft brush and by sonication (min. 5 min) Brush out cavities, holes and crevices with a suitably sized clean, soft brush using rotary movements. Ensure that the full width and depth of the relevant cavity, hole or crevice is reached. Next, rinse all cavities, holes and gaps at least five times at the start and end of the contact time using a disposable syringe -> for volumes see “Special instructions” section Move and/or slide moving parts back and forth at least 5 times and remove contaminants with a clean, soft brush Next, remove the instruments from the cleaning bath and thoroughly rinse them at least five times with water (at least 1 min. each time) Rinse all cavities, holes and gaps at least five times with water using a disposable syringe -> Volumes Move and/or slide moving parts back and forth at least 5 times during the rinsing with water Use only sterile or near-sterile water (max. 10 microorganisms/ml) with a low endotoxin content (max. 0.25 endotoxin units/ml) for rinsing (e.g. purified water/highly purified water), Use only filtered air for drying (oil-free, near-sterile and with a low particle count) Check the instruments (see “Inspection” and “Maintenance” sections). Repeat cleaning if contaminants are still visible
The fundamental suitability of the instruments for an effective manual cleaning was demonstrated by an independent, governmentally accredited and recognized (§ 15 (5) MPG) test laboratory by application of an ultrasonic bath of the SONOREX series with 35 kHz (BANDELIN electronic, Berlin) for manual cleaning as well as the cleaning detergent Cidezyme/Enzol (Johnson & Johnson GmbH, Norderstedt) considering the specified procedure.
7.2 Manual disinfection procedure • • • • • • • • •
lace the dismantled, cleaned and checked instruments in the ultrasonic disinfection bath for P the specified contact time, ensuring that the instruments are adequately covered. Ensure that the instruments are not touching each other. Move and/or slide moving parts back and forth at least 5 times during disinfection Rinse all cavities, holes and gaps at least five times at the start and end of the contact time using a disposable syringe, for volumes see “Special instructions” section Next, remove the instruments from the disinfection bath and thoroughly rinse them at least five times with water (at least 1 min. each time) Rinse all cavities, holes and gaps at least five times using a disposable syringe, for volumes see “Special instructions” section Use only sterile or near-sterile water (max. 10 microorganisms/ml) with a low endotoxin content (max. 0.25 endotoxin units/ml) for rinsing (e.g. purified water/highly purified water) Dry the instruments by blowing off/out with filtered compressed air (oil-free, near-sterile and with a low particle count) If possible, pack the instruments immediately after removal (see “Packing” section, if applicable after additional drying in a clean location). 6
Guide to the processing of instruments from Smith & Nephew Orthopaedics AG
The fundamental suitability of the instruments for an effective manual disinfection was demonstrated by an independent, governmentally accredited and recognized (§ 15 (5) MPG) test laboratory by application of an ultrasonic bath of the SONOREX series with 35 kHz (BANDELIN electronic, Berlin) and the cleaning detergent Cidezyme as well as the disinfectant detergent Cidex OPA (Johnson & Johnson GmbH, Norderstedt) considering the specified procedure.
8 Machine cleaning/disinfection with WD (washer and disinfector) Ensure that the selected WD satisfies the following conditions: • the WD must be of proven efficacy (e.g. DGHM or FDA approval/clearance/registration or CE marking according to ISO 15883) • if possible, a tested program for thermal disinfection should be used (A0 value > 3000 or – for older devices – min. 5 min at 90°C/194°F). • the program used must be suitable for the instruments and include a sufficient number of rinse cycles (at least three degrading steps after cleaning (respectively neutralization, if applied) or conductance based rinsing control recommended in order to prevent effectively remnants of the detergents). • only sterile or near-sterile water (max. 10 microorganisms/ml) with a low endotoxin content (max. 0.25 endotoxin units/ml) may be used for the final rinse (e.g. purified water/highly purified water), • the air used for drying must be filtered, (oil-free, near-sterile and with a low particle count) and • the WD must be regularly maintained and inspected. N.B.: chemical disinfection entails the risk of disinfectant residues on the instruments! Please ensure that the selected cleaning agent used satisfies the following conditions: • it must be suitable for cleaning metal or plastic instruments • for chemical disinfection, a suitable disinfectant with proven efficacy (e.g. VAH/DGHM or FDA/ EPA approval/clearance/registration or CE marking) should be used • the chemical disinfectant should be compatible with the cleaning agent used • the chemicals used must be compatible with the instruments (see "Material resistance" section). Do not use any rinse aids or instrument care products, as these can leave residues on the instruments.
7
Guide to the processing of instruments from Smith & Nephew Orthopaedics AG
8.1 Machine cleaning / disinfection procedure • •
• • • •
Disassemble the instruments as much as possible Place the disassembled instruments in the WD such that all construction elements of the instruments are accessible for cleaning and construction elements in which fluid can accumulate are able to drip dry (for example, hinges should be opened and cavities and holes positioned such that accumulated fluid can drain off). Ensure that the instruments are not touching each other. Start the program. On completion of the program, remove the instruments from the WD. If possible, check and pack the instruments immediately after removal (see sections on “Inspection and Maintenance” and “Packing”), if applicable after additional drying in a clean location.
The basic suitability of the instruments for effective automated cleaning and disinfection has been verified by an independent accredited test laboratory using the washer disinfector G 7836 CD (thermal disinfection, Miele & Cie. GmbH & Co., Gütersloh) and the cleaning agent Neodisher Mediclean Forte (Dr. Weigert GmbH & Co. KG, Hamburg). The procedure described above was followed.
8
Guide to the processing of instruments from Smith & Nephew Orthopaedics AG
9 Inspection and maintenance All Instruments must be inspected and controlled for proper functioning after cleaning/disinfection according to the instructions in the table below Instrument Type/Feature
Instructions
All reusable instruments
Check the instruments for no missing components. Visually inspect all instruments after Cleaning/Disinfection for corrosion, damaged surface, chippings, breakages, deformation, contamination and discoloration.
Instruments with joint *
Check for smooth movement of the joint without excessive “play”. For instruments with joint-/mating surfaces, a surgical-grade lubricant* that is compatible with steam sterilization should be added to the hinged area while the instrument is in the open position. Use as little as possible amount of oil.
Locking mechanism
Check locking mechanism with matching counterparts for secure connection.
Cutting instruments
Check edges for distortion and/or large nicks. Edges should be continuous.
Trials
Surfaces should be smooth and free of cracks and deep nicks.
Interface between instruments
Make sure interfaces match properly.
Drill bits / Reamer
Check connecting parts for burrs and wear.
Hitting surface
Check for burrs and large nicks.
Impactor
Check plastic parts for burrs and deep nicks.
Marking
Marking must be readable.
Cavities
Cavities, cannulae and rinsing holes have to be free from residues or blockages and are to be checked for consistency.
Multi-part instruments** and connecting mechanism
Check functionality for free movement by assembly /disassembly.
Fixed connections (grouting, bonding, weald seams)
Check for strength and stability.
*only use instrument oil consisting exclusively of medical-grade white oil (without anti-corrosion additives) that is approved for steam sterilization – taking account of the maximum sterilization temperature used – and is of proven biocompatibility. **separate instructions for assembly / disassembly of multi-parts instruments can be found on: https://www.smith-nephew.com/key-products/orthopaedic-reconstruction/ • •
amaged or improper functioning instruments should no longer be used. They need to be D decontaminated and returned back to the manufacturer for proper disposal. Instruments that are still contaminated must be recleaned and disinfected.
Serious incidents related to a Smith+Nephew instrument should be reported to Smith+Nephew and the competent authority. 9
Guide to the processing of instruments from Smith & Nephew Orthopaedics AG
10 Packing • •
rrange the cleaned and disinfected instruments in the corresponding sterilization tray. A The weight of the fully loaded trays must not exceed 16 kg (this must be observed if additional instruments are placed loosely in the tray)
Please pack the sterilization trays in sterilization containers that satisfy the following requirements: • ISO/ANSI AAMI ISO 11607 (for USA: FDA clearance) • they must be suitable for steam sterilization (temperature-resistant up to at least 142°C (288°F), adequate vapour permeability) • the sterilization packages should be adequately protected against mechanical damage • the sterilization containers should receive regular maintenance in accordance with the manufacturer's directions
11 Sterilization Only the fractionated steam sterilization methods listed below may be used for sterilization. The following sterilization methods are not permitted: • Gravitation method • Flash sterilization • Hot air sterilization • Radiation sterilization • Formaldehyde sterilization • Ethylene oxide sterilization • Plasma sterilization
11.1 Steam sterilization • • • • • •
T he weight of the fully loaded trays must not exceed 16 kg (this must be observed if additional instruments are sterilized loosely in the tray) Fractionated vacuum method 3 (with adequate product drying5) Steam sterilizer according to EN 13060/EN 285 or ANSI AAMI ST79 (for USA: FDA clearance) Validated according to DIN EN ISO 17665 (valid IQ/OQ (Commissioning) and product-specific qualification (PQ) Maximum sterilization temperature 138°C (280°F plus tolerance in accordance with DIN EN ISO 17665) Sterilization conditions are defined below
Country
Sterilization Time (min)*
Sterilization Temp.
Drying Time
USA
4 min
132°C
20-30 min
D / EU
5 min
134°C
Not specified
CH
18 min
134°C
Not specified
All other
at least 4 min
132/134°C
Not specified
* exposure time at the sterilization temperature at least three vacuum steps Since the drying time required in practice depends directly on parameters for which the user is solely responsible (load configuration and density, sterilizer condition, ...) this must be determined by the user. Nevertheless, drying times should not be shorter than 20 min. 3
5
10
Guide to the processing of instruments from Smith & Nephew Orthopaedics AG
The basic suitability of the instruments for effective steam sterilization using an instrument oil has been verified by an independent accredited test laboratory using the steam sterilizer HST 6x6x6 (Zirbus technology GmbH, Bad Grund) in the fractionated vacuum method and – for products in the group “Products with hinge” – using IP Spray (Dr. Weigert GmbH & Co. KG, Hamburg).
12 Storage The instruments must be stored in the sterilization packaging in a dry, dust-free place after sterilization.
13 Restriction on reprocessing The repeated processing of reusable medical instruments has a minimal influence on the instruments. The end of the service life is usually determined by damage and wear resulting from use.
14 Material resistance Cleaning agents and disinfectants should not contain any of the following constituents: • organic, mineral and oxidizing acids (minimum permitted pH: 5.5) • strong alkalis (maximum permitted pH: 11, alkaline cleaners with 10 < pH > 11 recommended) • organic solvents (e.g. alcohols, ethers, ketones, benzines) • oxidants (e.g. hydrogen peroxides) • halogens (chlorine, iodine, bromine) • aromatic/halogenated hydrocarbons Never clean any instruments, sterilization trays or sterilization containers with wire brushes or steel wool. Do not expose any instruments, sterilization trays or sterilization containers to temperatures higher than 138°C (280°F)!
11
O
T
Thoroughly brush all surfaces. Rinse gaps in moving parts at least 5x with a disposable syringe.
Thoroughly brush external surfaces. Thoroughly brush cavities and gaps around the O-Ring. If possible move the O-Ring inside the groove during pretreatment and rinse at least 5x with a disposable syringe.
Thoroughly brush all surfaces.
Thoroughly brush external surfaces. Thoroughly brush all joints and rinse at least 5x with a disposable syringe Move joints at least 5x during cleaning.
Thoroughly brush external surfaces. Thoroughly brush cavities, gaps and holes and rinse at least 5x with a disposable syringe. Move moving parts at least 5x during cleaning.
Thoroughly brush external surfaces. Thoroughly brush blind lumen and rinse at least 5x with a disposable syringe.
Thoroughly brush all surfaces. Rinse gaps in moving parts at least 5x with a disposable syringe.
Thoroughly brush external surfaces. Thoroughly brush cavities and gaps around the O-Ring. Move the O-Ring inside the groove during cleaning and rinse at least 5x with a disposable syringe.
Thoroughly brush all surfaces.
Thoroughly brush external surfaces. Thoroughly brush all joints and rinse at least 5x with a disposable syringe Move joints at least 5x during cleaning.
Thoroughly brush external surfaces. Thoroughly brush cavities, gaps and holes and rinse at least 5x with a disposable syringe. Move moving parts at least 5x during cleaning.
Thoroughly brush external surfaces. Thoroughly brush blind lumen and rinse at least 5x with a disposable syringe.
Thoroughly brush external surfaces. Thoroughly brush through lumen and rinse at least 5x with a disposable syringe.
Thoroughly brush external surfaces. Thoroughly brush cavities, gaps and holes and rinse at least 5x with a disposable syringe.
manual cleaning / disinfection
Special/additional procedure for
Rinse aids not permitted
Oils / care products not permitted
Oils / care products not permitted
Oils / care products not permitted
Rinse aids not permitted Rinse aids not permitted
Care products not permitted. Oils: targeted use on the joint permitted
Rinse aids not permitted
Oils / care products not permitted
Oils / care products not permitted
Rinse aids not permitted
Rinse aids not permitted
Oils / care products not permitted
Oils / care products not permitted
Maintenance
Rinse aids not permitted
Rinse aids not permitted
Automated cleaning/ disinfection
See sec. 10
See sec. 10
See sec. 10
See sec. 10
See sec. 10
See sec. 10
See sec. 10
See sec. 10
Packing
See sec. 11
See sec. 11
See sec. 11
See sec. 11
See sec. 11
See sec. 11
See sec. 11
See sec. 11
Sterilization
* 03389-en V3 For cavities: (1363) Ed. 11/19 Outer diameter of brush shall be at least 1mm wider than inner diameter of cavity For blind holes: Brush shall be at least as long as cavity For through holes: Brush (Pipe Cleaner) The pipe cleaner should be long enough to be able to be guided through the entire inner surface of the cavity.
Standard*
10 - 200ml depending on the size of the respective cavity
Products without lumens
H
Standard*
10 - 200ml depending on the size of the respective cavity
Trays
Products with joints
G
Standard*
10 - 200ml depending on the size of the respective cavity
Standard*
Products with diffuse lumen (not to be assigned to groups 1 - 4)
F
Standard*
10 - 200ml depending on the size of the respective cavity
10 - 200ml depending on the size of the respective cavity
Products with blind lumen
E
Thoroughly brush external surfaces. Thoroughly brush through lumen and rinse at least 5x with a disposable syringe.
Standard*
10 - 200ml depending on the size of the respective cavity
Products with O-Rings
Products with through lumen
B/D
Thoroughly brush external surfaces. Thoroughly brush cavities, gaps and holes and rinse at least 5x with a disposable syringe.
Standard*
10 - 200ml depending on the size of the respective cavity
Standard
Products with ring lumen
A/C
Pretreatment
Brush
Rinsing volume Disposable syringe
-
Description / Product aspect
Product Group
15 Special instructions
Notes
13
Notes
14
Notes
15
Smith & Nephew Orthopaedics AG Oberneuhofstrasse 10d CH-6340 Baar Switzerland www.smith-nephew.com
™Trademark of Smith & Nephew
03389-en (1363) V3 11/19
0