Stryker
1024.1 Reducer, Oral/Maxillofacial Drill Attachments
Micro Power Electric and Pneumatic Micro Systems Processing Instructions
40 Pages
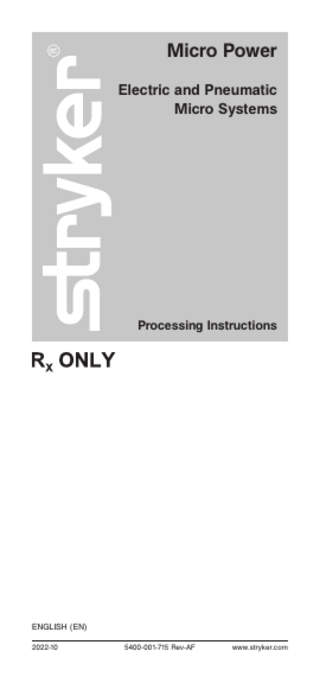
Preview
Page 1
Micro Power Electric and Pneumatic Micro Systems
Processing Instructions
ENGLISH (EN) 2022-10
5400-001-715 Rev-AF
www.stryker.com
EN
5400-001-715 Rev-AF
Contents Introduction . . . . . . . . . . . . . . . . . . . . . . . . . . . . . . 3 Audience . . . . . . . . . . . . . . . . . . . . . . . . . . . . . 3 Conventions . . . . . . . . . . . . . . . . . . . . . . . . . . . . 3 Contact Information . . . . . . . . . . . . . . . . . . . . . . . . 3 Intellectual Property . . . . . . . . . . . . . . . . . . . . . . . . 3 Definitions . . . . . . . . . . . . . . . . . . . . . . . . . . . . . . . 4 Description . . . . . . . . . . . . . . . . . . . . . . . . . . . . . . 4 Safety Directives . . . . . . . . . . . . . . . . . . . . . . . . . . . . 4 Limitations of Processing . . . . . . . . . . . . . . . . . . . . . . . 5 Preparation for Cleaning . . . . . . . . . . . . . . . . . . . . . . . . 5 Equipment and Materials . . . . . . . . . . . . . . . . . . . . . . 5 Accessories . . . . . . . . . . . . . . . . . . . . . . . . . . . . 6 Water Quality . . . . . . . . . . . . . . . . . . . . . . . . . . . 7 Cleaning Agents . . . . . . . . . . . . . . . . . . . . . . . . . . 8 Point of Use (Post-Surgery) . . . . . . . . . . . . . . . . . . . . 9 Transport to Decontamination Area . . . . . . . . . . . . . . . . . 9 Cleaning . . . . . . . . . . . . . . . . . . . . . . . . . . . . . . . 10 Manual Cleaning . . . . . . . . . . . . . . . . . . . . . . . . . 11 Automated Cleaning . . . . . . . . . . . . . . . . . . . . . . . 17 Disinfection (optional) . . . . . . . . . . . . . . . . . . . . . . . . . 19 Drying . . . . . . . . . . . . . . . . . . . . . . . . . . . . . . . . 20 Inspection . . . . . . . . . . . . . . . . . . . . . . . . . . . . . . 20 Visual Inspection . . . . . . . . . . . . . . . . . . . . . . . . . 20 Lubrication . . . . . . . . . . . . . . . . . . . . . . . . . . . . 21 Preparation for Sterilization . . . . . . . . . . . . . . . . . . . . . . 21 Equipment and Materials . . . . . . . . . . . . . . . . . . . . . 22 Pneumatic Hose Connector . . . . . . . . . . . . . . . . . . . . 23 Loading and Packaging . . . . . . . . . . . . . . . . . . . . . . 24 Stacking and Constraints . . . . . . . . . . . . . . . . . . . . . 25 Sterilization . . . . . . . . . . . . . . . . . . . . . . . . . . . . . . 25 Steam Sterilization . . . . . . . . . . . . . . . . . . . . . . . . 26 Immediate-Use Steam Sterilization . . . . . . . . . . . . . . . . . 27 Storage and Transportation . . . . . . . . . . . . . . . . . . . . . . 27 Sterile Equipment . . . . . . . . . . . . . . . . . . . . . . . . . 27 Non-sterile Equipment . . . . . . . . . . . . . . . . . . . . . . . 28 Disposal/Recycle . . . . . . . . . . . . . . . . . . . . . . . . . . . 28 Appendix A: Special Cleaning Considerations Table . . . . . . . . . . 29 Appendix B: Inspection Table . . . . . . . . . . . . . . . . . . . . . 35 Appendix C: Lubrication Table . . . . . . . . . . . . . . . . . . . . . 37 Appendix D: Extended Dry Time Table . . . . . . . . . . . . . . . . . 39
2
www.stryker.com
5400-001-715 Rev-AF
EN
Introduction This processing instructions manual contains information intended to ensure the safe, effective, and compliant sterile processing of your product. Processing equipment, operators, cleaning agents, and procedures all contribute to the efficacy of medical device processing. The healthcare facility should make sure that the combination used results in a medical device that is safe for use. Alternative methods of processing may be equally suitable. NOTE: The user/processor should comply with local laws and ordinances in countries where processing requirements are more stringent than those detailed in these instructions.
Audience This manual is intended for in-service trainers, biomedical equipment technicians, and central supply/sterile processing technicians. Keep and consult this reference manual during the life of the product.
Conventions The following conventions are used in this manual: • A WARNING highlights a safety-related issue. ALWAYS comply with this information to prevent patient and/or healthcare staff injury. • A CAUTION highlights a product reliability issue. ALWAYS comply with this information to prevent product damage. • A NOTE supplements and/or clarifies procedural information.
Contact Information For additional information, including safety information, inservice training, or current literature, contact your Stryker sales representative or call Stryker customer service at 1-269-323-7700 or 1-800-253-3210. Outside the US, contact your nearest Stryker subsidiary.
Intellectual Property Trademarks not the property of Stryker Corporation are the property of their respective owners.
www.stryker.com
3
EN
5400-001-715 Rev-AF
Definitions The symbols located on the equipment and/or labeling are defined in this section or in the Symbol Definition Chart. See the Symbol Definition Chart supplied with the equipment. SYMBOL
DEFINITION General warning sign
Description This comprehensive reference provides processing instructions and recommendations for Stryker Micro Power (Electric and Pneumatic) components and equipment.
Safety Directives WARNINGS: • Before processing this equipment, read and understand the processing instructions. Pay particular attention to safety information. • Only individuals trained and experienced in the processing of reusable medical devices should process this equipment. • DO NOT reuse, reprocess, or repackage a device that is intended for single use only. - A single use device may not withstand chemical, chemical vapor, or high temperature sterilization reprocessing. - Design features may make cleaning difficult. - Reuse may create a contamination risk and compromise structural integrity resulting in operational failure or fragmentation during use. - Critical product information may be lost during repackaging. Failure to comply may lead to infection or cross infection and result in patient and/or healthcare staff injury. CAUTION: Reuse of cutting accessories significantly increases wear on the handpiece and attachment.
4
www.stryker.com
5400-001-715 Rev-AF
EN
Limitations of Processing Repeated processing has a minimal effect on this equipment. See the Inspection section for additional guidance on evaluating device functionality.
Preparation for Cleaning Equipment and Materials WARNING: Use only Stryker-approved equipment, unless otherwise specified. DO NOT modify any system component or accessory. The following equipment is required to process devices per the instructions in this manual: • Warm water (See the Water Quality section.) • Prepared, specially formulated cleaning agents (See the Cleaning Agents section.) • Absorbent wipes • Soft, nonlinting cloth • Syringe • Non-abrasive, soft, flexible, synthetic bristle brushes • Washer-disinfector (complies with ISO 15883 series) • Cleaning agents as required by the washer-disinfector manufacturer • Instrument air1 < 140 kPa [< 20 psi] • Oven Instrument air is medical gas that falls under the general requirements for medical gases as defined by the National Fire Protection Association (NFPA) Health Care Facilities Code, is not respired, is compliant with the American National Standards Institute (ANSI)/ International Society of Automation (ISA) Quality Standard for Instrument Air, and is filtered to 0.01 microns, free of liquids and hydrocarbon vapors, and dry to a dew point of -40 °C [-40 °F]. 1
www.stryker.com
5
EN
5400-001-715 Rev-AF
Accessories The following optional equipment may be purchased to aid in processing: DESCRIPTION
REF
Light Mineral Oil
1605-010-000
Blu62® Pretreatment Foam
3000-00X-000 series
Blu62 Instrument Detergent
3000-00X-000 series
Battery Powered Micro (BPM) Sterilization Case
4300-462-000
Sports Medicine/Small Bone Trauma (SMT) Sterilization Case
4300-452-000
TPS™ ENT/ORAL MAX Sterilization Case
5100-172-000
TPS Handpiece Sterilization Case
5100-176-000
TPS Sterilization Cases
5100-27X-000 series
CORE™ Sterilization Cases
5400-27X-000 series
Maestro Sterilization Case
5400-279-000
The Mill Sterilization Case
5400-705-000
RemB® Electric Sterilization Cases
6400-27X-000 series
Small Bone Insert Tray
6400-277-010
Aesculap Rigid Sterilization Containers and Accessories
7102-XXX-XXX series
Hybrid Insert Tray
1900-375-010
Aesculap Rigid Sterilization Containers and Accessories
JN340 (Perforated bottom with retention plates)
®
JK340 (Solid Bottom) JK38X (Half size lid) JN440 (Perforated bottom with retention plates) JK440 (Solid Bottom) JK48X (Full size lid) Signature Sterilization Tray, Small
5407-476-000
Signature Sterilization Tray, Large
5407-478-000
NTOC cassette for TPX®
700001911909 (NTOC211103151)
NOTE: For a complete list of components or ordering information, contact your Stryker sales representative or call Stryker customer service. See the Contact Information section. Outside the US, contact your nearest Stryker subsidiary.
6
www.stryker.com
5400-001-715 Rev-AF
EN
Water Quality WARNING: Use the appropriate water quality for each stage of the cleaning process. Mineral residues from hard water can stain the equipment and/or prevent effective cleaning and decontamination. • Use utility water for flushing, washing, and rinsing the equipment. Utility water is water that comes from the tap. • Use potable water for diluting cleaning agents. Potable water is water that is treated and delivered in a manner so that it meets United States (US) Environmental Protection Agency (EPA) or local guidelines as suitable for drinking. • Use critical water for final rinsing of the equipment prior to sterilization. Critical water is water that is extensively treated usually by a multistep treatment process that could include a carbon bed, softening, deionization, and reverse osmosis or distillation to ensure that the microorganisms and the inorganic and organic material are removed from the water. A final submicron filtration could also be part of the treatment process. CAUTION: Poor water quality can adversely affect the life of medical devices. ALWAYS follow the water quality requirements per Association for the Advancement of Medical Instrumentation (AAMI) TIR 34. Warm water with an optimum temperature range of 27 to 44 °C [80 to 110 °F] is recommended for manual cleaning. The water should not exceed 60 °C [140 °F] and should be warm to the touch.
www.stryker.com
7
EN
5400-001-715 Rev-AF
Cleaning Agents WARNINGS: • To clean the equipment, use specifically formulated cleaning agents only. • Read, understand, and follow the indications, instructions, and safety information supplied with the cleaning agent for correct handling and use of the product. CAUTIONS: • Alkaline agents may be used to clean instruments in countries where required by law or local ordinances, or where prion diseases such as Transmissible Spongiform Encephalopathy (TSE) and Creutzfeldt-Jakob Disease (CJD) are a concern. It is critical that alkaline cleaning agents are thoroughly neutralized and completely rinsed from devices. • ALWAYS prepare the cleaning agent according to the manufacturer’s recommendations. Pay particular attention to the concentration used and the total dispersion. • To clean the equipment, a neutral cleaning agent is preferred. • An alkaline cleaning agent (neat, up to pH 11) is allowable, but not preferred. Alkaline cleaning agents may cause cosmetic damage or reduce the life of the product. • If a washer-disinfector is used, make sure the cleaning agent used is suitable for use in a washer-disinfector. • ALWAYS use a cleaning agent that is suitable for use on aluminum, stainless steel, plastic, rubber, and titanium surfaces. Stryker validated the manual and automated (washer-disinfector) cleaning processes using the following cleaning agents: Supplier
Product
Suitability
Process
Stryker
Blu62 Instrument Detergent
All materials
Manual Cleaning
Steris
Prolystica 2x Concentrate Enzymatic
Aluminum, stainless steel, soft metals, and plastics
Automated Cleaning
Prolystica 2x Concentrate Neutral
Prepare the cleaning agent according to the manufacturer's recommendations.
8
www.stryker.com
5400-001-715 Rev-AF
EN
Point of Use (Post-Surgery) CAUTIONS: • Dry, soiled surgical instruments are more difficult to clean. Do not allow contaminated devices to dry prior to processing. All subsequent cleaning and sterilization steps are facilitated by not allowing blood, body fluids, bone and tissue debris, saline, or disinfectants to dry on used instruments. • DO NOT use saline to wet or soak the equipment before transport to the decontamination processing area. • Pretreatment foam will minimize the drying of soil and facilitate later processing. DO NOT allow pretreatment foam to dry on the equipment. 1. Separate reusable equipment from disposable waste. 2. Discard waste into an appropriate container; use a punctureresistant container for sharps. See the Disposal/Recycle section. 3. Use absorbent wipes to remove gross soil from the equipment. 4. If transport to the decontamination processing area is delayed, cover the equipment with a damp cloth or spray the equipment with a pretreatment foam as often as necessary to maintain moisture.
Transport to Decontamination Area WARNING: During transport, pay particular attention to sharp, cutting edges to avoid injury. CAUTION: Avoid mechanical damage during transport. DO NOT mix heavy devices with delicate devices. Clean the equipment as soon as practical, typically within two hours, to preclude extended or repeat cleaning procedures.
www.stryker.com
9
EN
5400-001-715 Rev-AF
Cleaning NOTE: These cleaning instructions are appropriate for handpieces, attachments, bone mill, cords, sterilization trays/cases, sterilization plugs, and non-sterile single use cutting accessories (e.g., K-wires). To properly clean consoles, foot pedals, and pneumatic hose adaptors, see the instructions for use and/or processing instructions supplied with the device. WARNINGS: • Clean the equipment as indicated before first and every use. Use the cleaning methods as indicated in these instructions. Other cleaning methods may prevent proper sterilization of the equipment. Failure to comply with the processing instructions may lead to infection or cross infection and result in patient and/or healthcare staff injury. • Prior to cleaning, separate all detachable components and remove single use cutting accessories from the handpieces. Detachable components include cords, handswitches, bur guards, shields, irrigation clips, and attachments. CAUTIONS: • ALWAYS handle the equipment with care. DO NOT drop the equipment. • DO NOT use solvents, lubricants, rinse aids, or other chemicals, unless otherwise specified. • DO NOT use ultrasonic cleaning equipment. • DO NOT immerse or soak any equipment in liquid, unless otherwise specified. Equipment may be placed briefly under running water to ensure thorough wetting and contact with liquid while actuating moving parts. • DO NOT allow moisture or liquid to enter electrical plugs, receptacles, or openings. Moisture or liquid may cause corrosion and damage the equipment. • DO NOT use pipe cleaners or cotton swabs to clean lumens or connector receptacles. • DO NOT bend connector pins during cleaning. • ALWAYS make sure the cleaning agent is completely rinsed from the interior and exterior of the equipment before drying the equipment.
10
www.stryker.com
5400-001-715 Rev-AF
EN
• Use of instrument air is only recommended for drying of equipment. • (For Signature Portfolio MIS Attachments only): Make sure the MIS nose tube is disassembled from the hub prior to cleaning and sterilization. • Prior to cleaning a Right Angle Head Attachment, ensure the reducer and head are assembled. • Before cleaning a handswitch, ALWAYS set slide-style switches between the RUN and SAFE positions, and set button-style switches into the SAFE (‘S’) position. • When cleaning a bur guard, DO NOT force a brush or cleaning tool through the bur insert hole. • Use extreme care when handling a Dura Guard Attachment to prevent damaging its foot. NOTE: Two methods of cleaning are described, a manual cleaning method and an automated cleaning method. Removal of all gross soil is required for both cleaning methods. Select the desired cleaning method per facility protocol.
Manual Cleaning 1. Remove the lid and insert tray(s) or NTOC cassette(s) from the base of the sterilization tray/case. 2. Remove all soiled medical devices from the insert tray(s) or NTOC cassette(s) and base. 3. (For pneumatic handpieces): Remove and discard the diffuser from the exhaust port of the handpiece hose. 4. Remove all traces of pretreatment foam and any remaining gross soil from the equipment using absorbent wipes or a soft, nonlinting cloth moistened with the prepared cleaning agent. Devices may be placed briefly under running water or flushed with a water filled syringe to assist in the removal of gross soil. 5. (For Hummer/ESSx® handpieces only): Place the handpiece and cable in a horizontal position in a clean pan large enough to allow complete immersion of the device. Add a sufficient amount of prepared cleaning agent to cover the handpiece. Allow the handpiece to soak per the cleaning agent manufacturer's recommended time period to reduce the amount of debris on the handpiece.
www.stryker.com
11
EN
5400-001-715 Rev-AF
6. Thoroughly clean the equipment. See the Special Cleaning Considerations Table (Appendix A) for critical areas and brush sizes. • Use suitable brushes and the prepared cleaning agent to clean all surfaces. Pay particular attention to rough surfaces, crevices, and difficult-to-reach areas where soil may be shielded from brushing. • (For TPX™ handpieces only): TPX handpieces may be held under the surface of the prepared cleaning agent during manual cleaning. Do not soak any equipment.
• Use soft brushes of appropriate diameters to clean the entire length of each lumen. For dead-ended lumens, use light pressure and do not force the brush any farther after you feel resistance. Insert brushes as illustrated: COLLET • Gently insert a brush (2.0 mm for wire collets, 2.5 mm for pin collets) approximately 20 mm deep inside of the nose. Use light pressure to remove debris. Insert a 6 mm brush approximately 66 mm into the back of the collet to clean the rest of the lumen. 20 mm
2.0 mm/ 2.5 mm
12
66 mm
6 mm
www.stryker.com
5400-001-715 Rev-AF
EN
UNIVERSAL COLLET (REF 4500-12X-000 SERIES) • Gently insert a brush (6.0 mm) into the back of the collet, and continue through the entire length of the lumen. NOTE: For the adjustable collet (REF 4500-126-000), set the pre-adjust knob to L (Large) before inserting the brush.
6 mm
S2 STRAIGHT ATTACHMENT 2.5 mm
16 mm
S2 ANGLED ATTACHMENT 77 mm 2.5 mm
16 mm
SIGNATURE PORTFOLIO FOOTED ATTACHMENT
SIGNATURE PORTFOLIO NON-FOOTED ATTACHMENT
www.stryker.com
13
EN
5400-001-715 Rev-AF
SIGNATURE PORTFOLIO MIS HUB AND NOSE TUBE CAUTION: For MIS nose tubes, the diameter of the brush handle (not the bristles) must be less than the smallest inner diameter of the tube (1.19 mm [0.0467 inches]).
34 mm
ELITE ATTACHMENT 71 mm
HEAVY DUTY ATTACHMENT 68–122 mm
• Use a syringe filled with the prepared cleaning agent to flush difficult-to-reach areas. For the universal collet, flush the lumen from the back of the collet. • Ensure the reciprocating saw blade retention mechanism is thoroughly flushed during cleaning. • For irrigation clips, hold the equipment on an incline, distal end pointing up, and rinse the lumen under warm running water. • Actuate all holding, clamping, and latching mechanisms on sterilization trays/cases, lids, and insert trays. CAUTION: DO NOT actuate the attachment interface on the S2 Drill during cleaning.
14
www.stryker.com
5400-001-715 Rev-AF
EN
• Actuate all moving parts to clean hidden surfaces. Perform these additional steps to access all surfaces on the following devices: HANDSWITCH - Completely extend the finger rest.
SAGITTAL SAW - Pull out and slightly rotate the blade mount, and depress the button to open the blade mount.
OSCILLATING SAW - Actuate the blade mount collar.
XL OSCILLATING SAW - Disassemble the blade retention screw to access interior.
www.stryker.com
15
EN
5400-001-715 Rev-AF
7. Thoroughly rinse the equipment with warm, running water until all traces of cleaning agent are removed. • For equipment with lumens, hold the equipment on an incline, distal end pointing up, and rinse the lumen. • For dead-ended lumens, once the water comes back out of the equipment, immediately point the distal end of the equipment down to allow the water to drain out. Repeat this step one or two more times until the water draining from the equipment is clear. • For all other equipment, hold the equipment on an incline, distal end pointing down.
• Pay particular attention to rough surfaces, lumens, hinges, blind holes, and joints between mating parts. • Actuate all moving parts to rinse hidden surfaces. For sterilization trays/cases and insert trays, actuate all holding, clamping, and latching mechanisms. NOTE: A final rinse of the equipment using critical water is recommended. 8. Visually inspect the equipment for any remaining soil or cleaning agent. If soil or cleaning agent remains, repeat the cleaning procedure using freshly prepared cleaning agent. 9. Allow the equipment to drain on absorbent wipes. If possible, orient the equipment vertically to assist in drainage. 10. After manual cleaning, dry the equipment immediately (see the Drying section), or proceed with step 2 in the Automated Cleaning section.
16
www.stryker.com
5400-001-715 Rev-AF
EN
Automated Cleaning 1. Perform the following pre-cleaning steps: • Remove the equipment from the insert trays or NTOC cassettes. • Remove all visible soil from the equipment using a syringe filled with the prepared cleaning agent. Pay particular attention to lumens and moving parts, using brushes and syringes as necessary. • Rinse the equipment to remove all excess cleaning agent. WARNINGS: • ALWAYS load the equipment carefully to prevent movement that may inhibit proper cleaning during the automated washerdisinfector cycle. • Only the Small Bone Insert Tray, Hybrid Insert Tray, Signature Sterilization Tray, Large, and Signature Sterilization Tray, Small may be used to hold equipment in the washer-disinfector (see the Accessories section). All other insert trays and sterilization cases are for use with the sterilization process only and must be washed separately. • ALWAYS separate the sterilization tray components before loading into the washer-disinfector. Load each tray component separately. • When using the Small Bone Insert Tray or Hybrid Insert Tray during automated washing, make sure the top and bottom trays are separated when placed in the washer-disinfector to ensure products receive adequate exposure to the washer-disinfector cycle. NOTES: • The equipment illustrated is representational only and may not reflect the actual configuration. See the instructions for use supplied with the insert tray or NTOC cassette for devicespecific loading configurations. • It is recommended to ensure the XL Oscillating Saw blade retention screw is reassembled to the handpiece prior to placement in a washer-disinfector. 2. Load the equipment into the washer-disinfector in an appropriate insert tray (see the Accessories section), a wire basket, or other washer-disinfector equipment holder. • Avoid contact between components. • If possible, orient the equipment vertically to assist in drainage. Placing the equipment in a horizontal position is also acceptable. • Place moving parts in the open position.
www.stryker.com
17
EN
5400-001-715 Rev-AF
• For pneumatic handpieces, orient the hose connector so that the exhaust port is facing to the side or down, to avoid filling the hose with water. Be sure to drain the hose upon removal from the washer-disinfector. • For handswitches, ALWAYS set slide-style switches between the RUN and SAFE positions, and set button-style switches into the SAFE (‘S’) position.
• When cleaning an empty insert tray or sterilization tray/ case, orient the equipment vertically to assist in drainage.
18
www.stryker.com
5400-001-715 Rev-AF
EN
CAUTION: DO NOT use any type of lubricant or rinse aid in the automated washer-disinfector. Lubricants and rinse aids are not required and may leave residue on the equipment after cleaning. 3. Operate the washer-disinfector. Use the following validated phase parameters as required: Phase
Time
Water Temperature
Cleaning Agent
Pre-rinse
2 to 4 minutes
< 21 °C [< 70 °F]
Prepared cleaning agent (optional)
Wash1
2 to 4 minutes
60 to 82 °C [140 to 180 °F]
Prepared cleaning agent
Rinse
2 to 4 minutes
43 to 82 °C [110 to 180 °F]
–
Thermal Rinse2
1 minute
90 °C [194 °F]
–
Dry3
15 minutes
–
–
Wash may include enzymatic wash. Thermal rinse is optional. Thermal rinse does not replace sterilization. A thermal rinse phase may be used for up to 5 minutes at a water temperature of not more than 95 °C. 3 A temperature of up to 120 °C (248 °F) may be used during the dry phase. 1 2
4. Unload the washer-disinfector and visually inspect the equipment for remaining soil or cleaning agent. If soil or cleaning agent remains, repeat the cleaning procedure using freshly prepared cleaning agent. 5. Allow the equipment to drain on absorbent wipes. If possible, orient the equipment vertically to assist in drainage. 6. After automated cleaning, dry the equipment immediately (see the Drying section).
Disinfection (optional) Disinfection processes do not ensure the margin of safety associated with sterilization processes. Therefore, disinfection is optional. See the Automated Cleaning section and information related to the thermal rinse phase.
www.stryker.com
19
EN
5400-001-715 Rev-AF
Drying 1. Dry the equipment with a soft, nonlinting cloth or instrument air, or by heating the equipment in an oven below 110 °C [230 °F]. 2. After drying, inspect the equipment immediately (see the Inspection section).
Inspection WARNINGS: • Only individuals trained and experienced in the maintenance of reusable medical devices should inspect this equipment. • Perform recommended inspection as indicated in these instructions. • DO NOT disassemble, modify, or service this equipment, unless otherwise specified. CAUTION: Failure to comply with the stated minor service interval may compromise the effective use of the equipment. NOTES: • If the equipment fails to meet the inspection criteria, contact your Stryker sales representative or call Stryker customer service. Outside the US, contact your nearest Stryker subsidiary. • The useful life of this equipment is dependent upon many factors including, but not limited to, the method and duration of each use, and the handling of the equipment between uses. • Routine inspection is the best method for determining the serviceable life span of the equipment.
Visual Inspection Visually inspect the equipment before sterilization and as described in the Inspection Table (Appendix B). Pay particular attention to the following: • Locations where soil may become trapped, such as mating surfaces, hinges, and shafts • Recessed features, such as holes and lumens • Features where soil may be pressed into contact with the equipment
20
www.stryker.com