User Guide
44 Pages
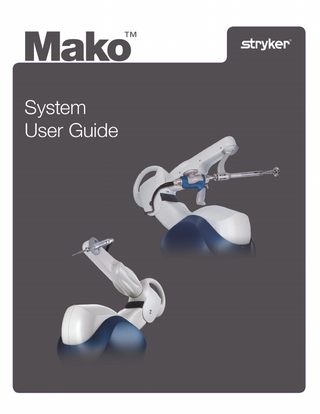
Preview
Page 1
MAKO System User Guide
1
Mako System User Guide
TABLE OF CONTENTS INTRODUCTION... 1 RIO COMPONENTS ... 3 TRANSPORTING THE RIO ... 16 CABLE CONNECTIONS... 19 POWERING THE RIO ... 20 MAKOplasty STARTUP SCREEN... 21 VIZADISC ASSEMBLY ... 22 DRAPING THE RIO... 24 CONNECTING THE BASE ARRAY ... 30 REMOVING THE DRAPE ... 32 RIO SHUTDOWN ... 34 CLEANING THE RIO ... 35 CARING FOR THE CAMERA LENSES ... 36 STORING THE RIO... 37
iii
Mako System User Guide
iv
Mako System User Guide
INTRODUCTION User Manual Terms of Use This manual is provided by MAKO Surgical Corp. (Stryker) and should be used for informational purposes only. Terms and Conditions related to the use of the Stryker Robotic Arm System (Mako/RIO) can be found in the placement agreement with the system user. About This Manual The content of this manual is the Original Instructions for setting up, transporting and cleaning the RIO. Indications for Use The RIO is intended to assist the surgeon in providing software defined spatial boundaries for orientation and reference information to anatomical structures during orthopedic procedures. The RIO is indicated for use in surgical knee and hip procedures, in which the use of stereotactic surgery may be appropriate, and where reference to rigid anatomical bony structures can be identified relative to a CT based model of the anatomy. These procedures include: Unicondylar knee replacement and/or patellofemoral knee replacement and Total Hip Arthroplasty (THA). This user guide supports RIO Model 3.0. Manufacturer Support/Feedback MAKO Surgical Corp. 2555 Davie Rd.Ft. Lauderdale, FL 33317 Customer Service Phone (855) 303-6256 Corporate Office Fax (954) 927-0446 makosurgical.com Patents Reference: U.S. Patents http://patents.makosurgical.com/15. Medical and Product Information This manual is informational only and is not intended as medical advice or a substitute for medical advice. As a manufacturer of medical devices in the field of orthopedics, Stryker does not practice medicine and does not recommend the surgical techniques referenced or discussed in this manual or any other surgical techniques for use on a particular patient. Stryker is not responsible for selection of the appropriate surgical technique to be utilized for an individual patient. Copyrights and Trademarks The content of this manual is protected under applicable copyright and trademark laws. You agree that you will not copy, distribute, republish, display, post, transmit or modify any content in this manual without Stryker’s prior permission. Any images displayed in this manual are the property of their respective copyright owners. Any reproduction, replication, modification or distribution of any art images in this manual is prohibited. The third-party trademarks in this manual are proprietary to their respective owners. These companies or their agents have granted Stryker the right to use their trademarks. Governing Law Any legal action or proceeding related to this manual or the information contained in it shall be brought exclusively in a court in Bergen County, New Jersey, and shall be governed by the laws of the State of New Jersey, without regard to conflicts of laws principles.
1
Mako System User Guide
General Warnings and Consideration There are no user serviceable parts in the RIO, refer to your Stryker authorized personnel for service.
Do not use the RIO for any purpose other than its intended use or with an unsupported implant system. Failure to comply may result in serious and/or fatal injury.
For detailed information on a specific software application work flow, consult the appropriate Application User Guide.
The main system components are suitable for use within the patient environment as long as each is prepared for surgery in accordance with the respective cleaning and/or sterilization instructions.
2
Mako System User Guide
RIO COMPONENTS The main components of the RIO are the Robotic Arm, Guidance Module, Camera Stand, Foot Pedal, and cutting system. Robotic Arm The term 'Robotic Arm' is used throughout this manual to refer to all components shown below, not just the 'arm' portion. Sub-components will be identified by another descriptor (e.g., Robotic Arm Base, Robotic Arm Articulating Arm, etc.).
Figure 1. Stryker Robotic Arm Components (Mako/RIO) Item
Description
A
Left Pedal (Raise) - A foot pump to raise Robotic Arm off of fixed feet onto rolling casters. Several (5 or 6) pumps are required to fully lift the Robotic Arm. Right Pedal (Lower) - Depressing this pedal will lower the Robotic Arm onto its stationary feet for storage and during operative use. Depress and hold for 3 - 4 seconds to lower Robotic Arm onto its support feet. Be sure to check for obstructions before lowering the system. The RIO Robotic Arm must be in the holster position before lowering it onto the stationary feet for storage or during operative use.
3
Mako System User Guide
Item B
Description Secondary Storage and User Panel (Lower) A second user panel on the RIO, located inside a locked compartment to prevent unauthorized access, houses the power cord connection, the ON/OFF switches, and other peripheral connections The control panel may differ depending on whether you have a RIO Knee System or a RIO Common Hardware System.
Figure 2 Secondary Storage and Lower User Panel (RIO System)
1. Guidance Module Connection - The termination point of the Guidance Module connection cord. 2. Power Switch/ Circuit Breaker - A circuit breaker for the Guidance Module (and Camera Stand, if connected). 3. System Serial # Label- The identification label for the Robotic Arm. The serial number label contains the system serial number, model number, part number, date of manufacture, voltage, amperage, frequency, and any applicable standards (Figure 2). 4. Ethernet Port (RIO Knee System)- For Stryker use only. Not used intra-operatively. 5. Foot Pedal Connector - Receptacle for the optional foot pedal control. 6. System Power Button -A single button which powers all of the RIO components (if connected). See the ‘Powering the RIO’ section of this manual for details. 7. System Power Switch - A switch controlling main power to the Robotic Arm (includes Guidance Module and Camera, if connected). Must be in the ON position for the Robotic Arm to function. 8. Power Cord Connection - Outlet for the Robotic Arm power cord with a fastener to hold the cord in place. The power cord should not be removed. 9. Type B Device Label and Patent Protect Label.
4
Mako System User Guide
Item
Description
C
Upper User Panel - The upper user panel of the RIO allows manual locking and release of the Robotic Arm brakes. Pressing the EMERGENCY stop (E-Stop) while the Robotic Arm is active will lock the Robotic Arm brakes and prevent motion in the Articulating Arm. The Mako Product Specialist can enable the system after an E-Stop. The control panel may differ depending on whether you have a RIO Knee System or a RIO Common Hardware System.
3
4
5
7
6
2
1
8
9
Figure 3 Control Panel
1. Emergency Stop - Pressing this button (E-Stop) at any time while the Articulating Arm is in use will lock the Robotic Arm joint brakes and prevent any Robotic Arm motion. To release the EStop, rotate the button clockwise. This will activate the enable button. Press and hold the enable button until the Robotic Arm brakes disengage. 2. Power – (RIO Common Hardware System Only) Indicates power is on.
3.
Fault Light - (yellow LED) - When lit, indicates a system fault. When not in use, the Robotic Arm should be placed in the transportation position and the Emergency Stop should be engaged.
4.
Enable Button - (and green ring LED) - Pressing this button while the LED ring is blinking will disengage the joint brakes of the Articulating Arm. This button is used during Robotic Arm setup and to enable the Articulating Arm after releasing the emergency stop or switching between hip and knee applications. 5
Mako System User Guide
Enabling the Robotic Arm can cause the Robotic Arm to move. Hold the Robotic Arm when pressing the enable button.
5. Burr Motor Connection-A socket where the Anspach cable is connected. 6. MICS Motor Connection- (RIO Common Hardware System Only). A socket where the MICS handpiece cable is connected. 7. Irrigation Pump - Used during the surgery to pump irrigation. When ejected, the lid may be opened and irrigation tubing clicked into place. The direction of irrigation flow is indicated. When not in use, the pump can be stored inside the Robotic Arm by closing the lid and pressing it into the Robotic Arm. The pump will click into place 8.
Brake Release Button - (RIO Knee System Only) Pressing this button will release the Robotic Arm brakes and allow the Articulating Arm to be moved, if necessary.
9.
Override Button- This button is a manual override for the MICS handpiece or Anspach control, which allows the MICS handpiece to be used freehand (in conjunction with the foot pedal) in the case of a Robotic Arm failure. Lift the button cover and depress the override button to use.
6
Mako System User Guide
Item D
Description Transport Handle Used for pushing, pulling, or turning the Robotic Arm when in transport position.
E
Storage Bin The storage bin on the back of the Robotic Arm contains space for the following: • Calibration End Effector • DVD-ROM Drive and Calibration data CDs for all End Effectors, Calibration End Effectors and Ball Bars included with the system • Socket wrench and hex keys • Socket Array (located under the Calibration End Effector • MICS Holder • User Manual (if required)
Figure 4. Stryker Robotic Arm Storage Bin (Mako/RIO)
7
Mako System User Guide
Item
Description
F
Base Array Tracking Arm- The Base Tracker Arm supports the Base Array during surgery. The Large Tracker Arm Knob on the lower portion of the Base Tracker Arm allows for positioning, this knob must be secured to hold the Base Array in place. For optimal setup, the Base Tracker Arm should be set and locked into position immediately following draping. Any further adjustments required for the base array may be done using the Large Tracker Arm Knob.
Loosening the larger Base Tracker Arm Knob will release three joints at once. Support the Tracker Arm before loosening.
Base Array Connector
Figure 5. Base Tracker Arm Lower Arm (left) and Upper Arm (right)
8
Mako System User Guide
Figure 5a. Quick Connect Base Array Connector*
Figure 5b. Quick Connect Base Array Assembly
* The Base Array Tracking Arm shall be configured with either the Base Array Connector with Thumb Screw or the Quick Connect Base Array Connector. Item G
Description Articulating Arm Each of the six joints in the arm has a different range of motion. Control of the Articulating Arm is handled by software and the user.
H
Calibration Slide and Locking Knobs To free the Calibration Slide, loosen both knobs by turning counter clockwise. The slide can be extended toward the right or left sides of the Robotic Arm and locked into place. Both the Calibration Slide and the locking knobs are only used for Robotic Arm calibration (performed by Stryker customer service personnel) and for pre-surgery check (performed by the Mako Product Specialist). These items are not used intra-operatively. Knobs Slide
Turnclockwise
Turnclockwise
Figure 6. Kinematic Calibration Slide and Locking Knobs.
9
Mako System User Guide
Guidance Module The Guidance Module acts as a computer workstation for the Mako Product Specialist, and houses one of the two system computers.
Figure 7. Guidance Module Components Item
Description
A
LCD Monitor - This monitor can be viewed by the Mako Product Specialist during the procedure and may also act as backup monitor if the surgeon monitor fails.
B
USB Ports - Used for data import /export and portable DVD drive connection.
C
Transport Handle - Used for pushing, pulling or turning the Guidance Module.
D
Computer Housing - Houses the computer which runs the application software.
E
Camera Stand Connection - Connection socket for the Camera Stand cord.
F
Cord Wrap - Used to bundle the Guidance Module cord.
G
Reset / Power Button - Used to reset the computer inside the Guidance Module.
Fully power down the system before disconnecting any cabling to avoid a potential electrical shock hazard.
To prevent damage to the Camera Stand connection, the cable connection cover on the Guidance Module must be attached at all times when not in use. During normal use, power to the Guidance Module is provided automatically when the Robotic Arm is powered. The Reset Button (Item G) should only be used to power the Guidance Module to recover from a failure.
10
Mako System User Guide
Figure 8. Guidance Module
Figure 9. Serial Number
Do not transport the Guidance Module unless the unit is in the storage position. The maximum threshold transition that the Guidance Module can be pushed over is 10 mm. Item
Description
H
Keyboard - A sealed keyboard for use during the pre-surgery check and surgery.
I
Mouse - A sealed, three button mouse used to navigate through the application software.
J
Storage Compartment - Stores the system Ball Bar used for system calibration and the presurgery check.
K
Wheel Brakes - Brakes on two of the four wheels can be used to secure the Guidance Module.
L
Serial Number - Serial number is located on the back of the base of the Guidance Module.
11
Mako System User Guide
Camera Stand
Figure 10. Camera Stand
Figure 11. Warning Symbol on Camera Stand Arm
Ensure the camera does not move while the Robotic Arm is in the stereotactic boundary. Movement of the camera may cause the Robotic Arm to move outside of the incision.
To avoid a potential tipping hazard, do not transport the Camera Stand unless the unit is in storage position. The maximum threshold transition that the Camera Stand can be pushed over is 10 mm.
Item
Description
A
Camera -Used for tracking MAKOplasty instruments and arrays. The camera is composed of two sensor/illuminators which provide and detect infra-red light and a central user panel described in Figure 10.
12
Mako System User Guide
Figure 12. Camera User Panel.
1. Warm up Sensor – 2 minutes are required for camera warm up with a maximum warm up time of 10 minutes. The LED will blink while booting and turn green when ready. 2. Power Indicator – This LED will turn green when power is supplied. This LED may flash blue during system boot. This is part of the normal warm up process. 3. Bump Sensor – This LED will turn orange if a major bump is detected. Notify Stryker customer service if this light is illuminated. 4. Laser Aperture – Source of the laser alignment guide. Do not look directly into the laser-emitting aperture. The Class 2 laser module on the Position Sensor emits radiation that is visible and may be harmful to the human eye. Direct viewing of the laser diode emission at close range may cause eye damage. A warning label related to laser radiation is affixed to the back of the camera.
Figure 13. Laser radiation warning and serial number label
5. Laser Alignment Button – This button produces a red laser light which may be used for alignment of the camera field of view. The light will remain on only as long as the button is pressed. Item B
Description Surgeon Monitor - An LCD monitor used for surgeon view which can be translated and rotated to achieve proper viewing angle.
13
Mako System User Guide
Item C
Description Camera Adjustment Mount - The position of the camera can be adjusted using any of the knobs outlined below.
1. To adjust the camera, activate the trigger and rotate to the desired position.
Trigger
Figure 14. Camera Adjustment Mount When adjusting the camera, always make sure the trigger is depressed. Failure to adjust the camera with the trigger depressed will damage the camera mount.
14
Mako System User Guide
Item
Description
D
Camera Stand Base and Wheel Brakes - The Camera Stand should be locked into position when in use or in storage by applying the two wheel brakes. A 'NO STEP' label is affixed to the top of the Camera Stand base.
Figure 15. No Step Label Location
A MAKO serial number label with the part number, serial number, manufacture date, and certification information can be found on the rear of the Camera Stand Base as shown in Figure 16. A secondary label is also affixed to the left of the MAKO logo showing serial number and certifications for the original equipment manufacturer.
Figure 16. Serial Number Location
To avoid a potential tipping hazard, do not step on the base of the Camera Stand.
15
Mako System User Guide
TRANSPORTING THE RIO Transporting the Robotic Arm The Robotic Arm should only be transported when all the following conditions are met: • Robotic Arm is in home position (Robotic Arm folded at elbow, centered above the Robotic Arm base) with covers attached as shown. • E-Stop switch is pressed (to engage Robotic Arm brakes). • Power is off and all cords are disconnected. • Stationary leveling legs are lifted completely off the floor (using the left foot pump). To prevent potential damage to the self-leveling feet of the RIO, please follow these recommendations before moving the system: 1. Ensure that the RIO is fully raised off the self-leveling feet and onto the casters by pumping the Lift Pedal until it will not pump anymore. 2. Pump the Lift Pedal slowly and with even strokes to provide adequate hydraulic lifting. Use the front handle to maneuver the Robotic Arm to the desired location; it takes two people to move the RIO.
Figure 17. Transport Configuration of the Robotic Arm Do not transport the system while the Robotic Arm is in use. The Robotic Arm must not be transported unless the lift mechanism is in the fully up, transport position. Ensure the Robotic Arm has been fully lifted using the foot pump. To avoid a potential tipping hazard, do not transport the Robotic Arm unless the unit is in the storage position. The maximum threshold transition that the Robotic Arm can be pushed over is 10 mm. The Robotic Arm has limited ground clearance and the user should not attempt to push it over cables or other obstacles. Always transport the Robotic Arm with the lift mechanism fully engaged (i.e., the stationary support legs fully retracted).
16
Mako System User Guide
Transporting the Guidance Module To move the Guidance Module, unlock the two wheel brakes and use the handle as a grip.
Figure 18. Transport Configuration of the Guidance Module
Transporting the Camera Stand To move the Camera Stand, unlock the brakes on the stand wheels, ensure the primary monitor and camera arms are retracted toward the center of the stand, and cover the unit with the supplied covers. Use the exposed handle to push the Camera Stand.
Do not bump the Camera Stand while moving. It could cause damage to the system.
Figure 19. Transport Configuration of the Camera Stand (new pix)
The Camera Stand may tip over if transported on an incline of more than 10°. Always transport the Camera Stand in transport position (i.e., with the monitor and camera fully stowed).
When in storage position, the upper segment of the Camera Stand may be too tall to fit through the doorway in the upright position. It may be necessary to lower the upper segment of the arm to avoid damage to the Camera Stand.
Important RIO Concepts Passive Navigation In addition to the Robotic Arm, the RIO utilizes instrumentation for wireless navigation. Unlike traditional surgical tools, these instruments are affixed with VIZADISC which reflect infrared light produced and collected by the camera system. Software in the RIO uses the information gathered by the camera to determine tip position and tool orientation of a given navigated instrument as it moves through the camera’s field of view. Additionally, bone mounted arrays are used as a reference to register the position and orientation of other objects (e.g., bones). Instruments and reference arrays equipped with passive VIZADISC must have an unobstructed line-ofsight path to the camera in order to be tracked.
17