Thermo Electron Corp
BBD 6220 Operation Instructions
Operation Instructions
45 Pages
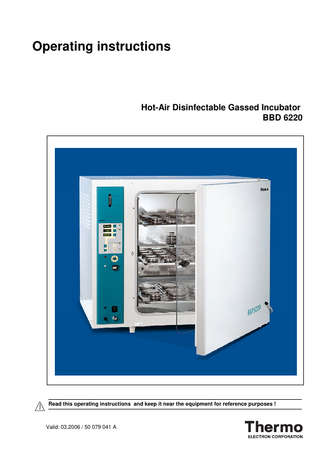
Preview
Page 1
Operating instructions
Hot-Air Disinfectable Gassed Incubator BBD 6220
Read this operating instructions and keep it near the equipment for reference purposes !
Valid: 03.2006 / 50 079 041 A
Postal adress Germany Thermo Electron LED GmbH Robert-Bosch-Straße 1 D - 63505 Langenselbold
Postal address USA Thermo Electron Corporation 275 Aiken Road Asheville, NC 28804 USA
Enquiries from Germany Phone Sale 0800 1 536376 Service 0800 1 112110 Fax Sale/Service 0800 1 112114 E-Mail info.labequipment.de@thermo.com
Enquiries from North America Phone +1 800-879 7767 Fax +1 828-658 0363 E-Mail info.labequipment.de@thermo.com
Enquiries from Europe, Middle East and Africa Tel. + 49 (0) 6184 / 90-6940 Fax + 49 (0) 6184 / 90-7474 E-Mail info.labequipment.de@thermo.com
Enquiries from Latin America Phone +1 828-658 2711 Fax +1 828-645 9466 E-Mail iinfo.labequipment.de@thermo.com Enquiries from Asia Pacific Phone +852-2711 3910 Fax +852-2711 3858 E-Mail info.labequipment.de@thermo.com
Copyright © Thermo Electron GmbH, D-63505 Langenselbold, Deutschland No part of this publication may be reproduced or transmitted in any form or by any means, including photocopying and recording, without the written permission of Thermo Electron GmbH. Various sections of this instruction manual may be copied only for in-house use by the equipment operator, e.g. to provide employees with instructions on accident prevention measures. These sections are clearly marked in the list of contents. Thermo Electron GmbH can accept no liability or responsibility for the marketability or the suitability of this instruction manual for a certain purpose other than that specified under "Areas of application of equipment". Thermo Electron GmbH reserves the right to change the content of this instruction manual at any time and without prior notice. As regards foreign-language translations, the German version of this instruction manual is binding. This edition of the instruction manual applies to the BBD 6220 unit specified on the front page. Date of publication: 03.2006 Nominal charge
Safety with regard to the protection of persons, the environment and the material under process largely depends on the conduct of the persons using the equipment. This instruction manual is important for your safety as well as for the setup, installation, use and maintenance of the equipment! To avoid errors and any resulting damage, especially personal injuries, be sure to read this manual carefully before using the equipment and follow all instructions.
2/43
50 079 041
LIST OF CONTENTS
PAGE
1. GENERAL... 5/7 Explanation of icons in the instructions manual... 5 Explanation of icons in the short instructions... 6 General instructions... 7 Equipment log book... 7 Operating instructions... 7 2. AREAS OF APPLICATION... 8 3. SAFETY INSTRUCTIONS... 9 4. SETUP AND INSTALLATION... 10-12 Transport... 10 Place of installation... 10 Stacking... 10 Clearances... 11 Supply connections... 11 Mains connection... 11 Gas supply connection... 12 RS 232 interface... 12 "Potential-free contact" connection... 12
5. DESCRIPTION OF THE UNIT... 13/14 Levelling the shelves... 13 Functional principle... 13 Heating system... 13 Gassing... 13 Humidification... 14 Door switch... 14 Internal fittings... 14 Six-piece Gas-tight glass screen... 14 Lockable outside door... 14 Disinfection routine... 14 "Potential-free contact" connection... 14 6. OPERATE... 15-30 Switch panel... 15 Water supply... 16 Mains switch... 16 Temperature protection device (temperature limit controller)... 18 Control and display panels... 18-21 Disinfection routine... 21/22 auto-start routine / auto-zero routine... 23/24 Error code enquiry... 23/25 Switching functions... 27 Switching function: Acoustic alarm ON/OFF... 27 Switching function: Humidification ON/OFF... 28 Switching function: Manual zero calibration of CO2 measuring system... 29 Switching function: Setpoint lock-in ON/OFF... 30 Switching function: Door heater ON/OFF... 31
50 079 041
3/45
LIST OF CONTENTS
PAGE
7. START-UP... 32 8. OPERATION... 33 Guidelines for use... 33 Before putting the unit into operation... 33 During operation... 33 Operation interruptions... 33 9. SHUTDOWN
... 34
10. MAINTENANCE... 35/36 Cleaning/Disinfection... 35 Testing... 36 Equipment log book... 36 Replacing of electrical parts... 36 11. AUTHORIZED EQUIPMENT PARTS AND ACCESSORIES... 37 12. TECHNICAL SPECIFICATIONS... 38/39 13. MATERIALS USED / DISPOSAL... 40 14. GAS CONSUMPTION... 41 15. PH-VALUE OF CULTURE MEDIA... 42 Basic rules of sound microbiological engineering practice... 43/44 General rules... 43 Handling of pathogenes... 43/44 Handling of human- and animal-pathogenic biological agents... 44 APPENDIX Statement of conformity Log Book Explanation of confirmation of safety Information request form regarding maintenance and servicing contract Communication-protocol of RS 232-device
4/43
50 079 041
1. GENERAL EXPLANATION OF ICONS IN THE INSTRUCTIONS MANUAL
In chapters of the instruction manual which deal with safety, this icon appears under the title of the chapter. Displayed on the equipment, this icon denotes that special attention must be paid to the information given in the instruction manual or accompanying documents. Marks information in the instruction manual for optimizing use of the equipment "Water supply" vent/overflow "Add/drain water" quick release coupling aqua dest
I 0 des start/ stop "des"
Unit ON Unit OFF "Disinfection mode" key-operated switch Marks information for higher surface temperature in the disinfection mode Overtemperature protection, temperature limit controller Selection of switching/interlocking functions
i
Error code enquiry / acknowledgment of "acoustic signal"
control
"Change switching functions activated" display
auto-start
Automatic startup of unit and calibration of measuring systems
auto-zero
"auto-zero" calibration active display
des
"Disinfection mode" display Information on proper disposal / recovery of raw materials
50 079 041
5/45
1. GENERAL
EXPLANATION OF ICONS TO THE SHORT INSTRUCTIONS 0
Switch on unit (operate the main switch)
I max.
aqua dest.
Check the water level
min. > + 2 °C
Set the temperature limit controller
°C
Close unit doors
L &
Read the operating instructions
des
start/ stop
Start "disinfection routine"
≥ 1 sec
auto-start
automatical "auto-start"
Open unit doors for at least 30 seconds ≥ 30 s &
&2
Set the desired setpoints
2
U +
auto-start
"activate" the auto-start
≥ 5s &
start / stop
End of the auto-start, bring in the samples
auto-start
Take out the samples, open unit doors for at least 30 seconds > 30 s 180 °C
Flow chart of disinfection routine t
6/43
50 079 041
1. GENERAL
General instructions To avoid errors and causing damage, especially personal injuries, be sure to read this manual carefully before using the equipment, and follow all instructions. When setting up and operating the unit, be sure to comply with the instructions contained in this manual as well as all applicable laws, regulations and directives in your country (FRG: ZH 1/119, ZH 1/342, ZH 1/343, ZH 1/598). The unit meets the following safety requirements DIN 12880 Part 1/11.78 DIN VDE 0700 Part 1 (IEC 335-1; EN 60335-1/11.90) EN 61010 When you have an enquiry, order replacement parts or file a complaint, please state the data on the nameplate and, if applicable, the fault code. Equipment log book We advise you to keep an equipment log book. Keep a record of inspections and testing, calibration work and any major work carried out on the unit - such as maintenance, agents loaded, etc. - in this log book (refer to APPENDIX). Operating instructions The operator (employer) is expected to provide anyone who works on or with the equipment with written instructions, based on this instruction manual, for the tasks to be performed. These instructions should be easy to understand and in the language of the persons operating the equipment. This also applies to disinfecting and cleaning the unit (also refer to Chapter 10: Maintenance).
50 079 041
7/45
2. AREAS OF APPLICATION
The BBD 6220 gassed incubator is an item of laboratory equipment for cell and tissue cultures and can be used to simulate the physiological environmental conditions of cells. The unit is generally suitable for setup and operation in the following areas: In laboratories for microbiological and biotechnological work. Medical and microbiological laboratories to DIN 58956. Central laboratories in clinics and hospitals. Laboratories operating at safety levels L1, L2 and L3. Only organisms which comply with the requirements for safety levels L1, L2 and L3 may be handled in the unit. The unit must be set up and operated in accordance with all applicable regulations in your country. (FRG: ZH 1/119, ZH 1/342, ZH 1/343, ZH 1/598) It is not permitted to handle gases or agents whose vapours are combustible or can form a hazardous, potentially explosive atmosphere when mixed with air. Be sure to comply with the applicable regulations in your country. (FRG: ZH 1/10)
8/43
50 079 041
3. SAFETY INSTRUCTIONS In the case of biological incubators, biological safety with regard to the protection of persons, its surroundings and the load is heavily dependent on the observance of the applicable regulations by the persons using the equipment. Even then, however, the possibility of hazards, especially health hazards, arising cannot be ruled out. The residual risk depends on the work performed in each individual case. To avoid errors and causing damage, especially personal injuries, be sure to carefully read this manual before putting the equipment into operation, and follow all instructions. Safe and reliable operation of the unit can only be guaranteed if the necessary inspections, maintenance and repair work are carried out by Heraeus Service Department personnel or by personnel authorized by our company. Gas is to be supplied to each unit by means of a pressure reducer with the inlet pressure set to between 0.8 and max. 1 bar. This setting must not be changed for safety reasons (FRG: ZH 1/119). The place of installation must be thoroughly ventilated in order to expel the gases escaping around the pressure relief valve to the outside. To maintain the temperature protection function, the functioning of the overtemperature protection device, temperatur limit controller must be checked at reasonable intervals. Only original replacement parts authorized by the manufacturer are to be used. Refer to the Appendix titled "BASIC RULES OF SOUND MICROBIOLOGICAL ENGINEERING PRACTICE".
50 079 041
9/45
4. SETUP AND INSTALLATION When setting up, installing and operating the unit, be sure to comply with all applicable regulations in your country. (FRG: ZH 1/119, ZH 1/342, ZH 1/343, ZH 1/598) Transport Handle the unit with care during transport. Do not lift up the unit by its door. Refer to TECHNICAL SPECIFICATIONS for weights and dimensions. Place of installation The place of installation must be dry and draught-free. The unit should not be placed or operated in recesses which cannot be ventilated. To avoid or at least minimize deviations from the technical specifications, the temperature at the place of installation must be in the range +18°C to +30°C. Set up the unit on a solid, non-flammable surface (laboratory tables, subframes). Make sure that the unit is in a stable and perfectly upright position. Do not cover or obstruct the fresh air or exhaust vents in the unit housing (please observe the minimum clearances - see page 11). CO2 are admitted into the gassed incubator. CO2 is a health risk hazard. The place of installation must therefore be well-ventilated. Gases discharged from the pressure relief valve must be safely expelled outside by means of the ventilation systems. It may be necessary to take special measures in order to ensure proper ventilation when several units are installed in the same room. For information on gas flow during operation, refer to the APPENDIX. Stacking The unit is not suitable for stacking when operated in the manner intended.
10/43
50 079 041
4. SETUP AND INSTALLATION Clearances When setting up the unit, the minimum clearances between the unit and adjacent surfaces and other units must be maintained.
100
300
Larger clearances are recommended to facilitate accessibility for installation and the supply connections. 150
100
Fig. 1: Minimum clearances in mm Supply connections
Mains socket C02 gas connection 02/N2 gas connection (option) Label: supply connection Potential-free contact RS 232 interface
Fig. 2: Supply connections (rear panel of unit) Mains connection Prior to connecting the unit to the mains, make sure that the power supply ratings match those stated on the nameplate. Your unit is equipped with a power supply cable with a grounding contact-type plug. Fuse protection required: Use a type G 16 circuit-break switch or a type T 16 A fusible cutout. Refer to the Chapter titled TECHNICAL SPECIFICATIONS for unit power consumption.
50 079 041
11/45
4. SETUP AND INSTALLATION Gas supply connection The gas connection are located on the back of the unit. The gas must be supplied to each unit via a pressure reducer with the inlet pressure set to between 0.8 and max. 1 bar. This setting must not be changed for safety reasons (FRG: ZH 1/119). The gases must have at least 99.5% purity. If several units are placed in the same room, special ventilation measures are required. CO2 gassing Connect the gas cylinder to the gas nozzle on the unit. O2 / N2 gassing (optional) If you intend to run the unit with an oxygen content above 21%, connect an oxygen cylinder. If you intend to run the unit with an oxygen content less than 21%, connect a nitrogen cylinder. To deactivate the oxygen control, set the nominal value to 21.0% (average oxygen content of ambient atmosphere). RS 232 interface Serial interface for computer-aided acquisition and documentation of critical operating parameters (temperature, CO2, relative humidity, error codes, etc.). The RS 232 interface can connect a single unit in combination with the "Kelvilog" software package, and can be expanded to connect 31 units with the "Netcontrol" hard- and software package. "Potential - free contact" connection The "Potential-free contact" (1 changeover contact) is rated for the following circuits: Circuit
Voltage
Fuse to be installed by customer
Mains-operated circuits
max. 250 V AC
max. 6 A
SELV / SELV - E - circuits (cf. VDE 0100 Part 410)
25/50 V AC 60/120 V DC
max. 2/1 A max. 1/0.5 A
L
F1x T2A
3
1 2
H1x
Kx
S1x
X
Kx
View X PE
H2x
Kx
A1
1
1s
3 2
A2 N
Fig. 3 : Application example of "Potential - free contact" connection
12/43
50 079 041
5. DESCRIPTION OF THE UNIT Levelling the shelves
The shelves can be aligned with the aid of a spirit level with height-adjustable feet.
Functional principle The atmosphere in the chamber can be regulated in relation to its temperature, CO2 concentration, O2 concentration (optional) and relative humidity. Heating system The temperature inside the unit can be regulated in the range of +7°C to +50°C, but must be at least +5°C (approx. +7°C for the O2 version) above the ambient temperature of the unit. Condensation on the glass door is largely prevented by heating the unit door. If the unit door is left open for a long period of time, however, condensation cannot be ruled out. The unit door heater can be switched off as required (refer to Chapter headed OPERATION). This enables the unit to be operated at high ambient temperatures or when the operating temperature is only supposed to exceed the ambient temperature by approx. +4°C. Example: Ambient temperature
Operating temp.
Heating of unit door
+25°C
+37°C
ON
+24°C
+28°C
OFF
+32°C to +33°C
+37°C
OFF
Gassing Connection to the gas supplies (CO2,, O2 or rather N2) are located on the rear panel of the incubator. The CO2 content of the atmosphere in the chamber can be regulated in the range 0% to 20%. The O2 concentration inside the unit can be regulated in the range 3% to 90% O2 by admitting N2 (< 21% O2) or O2 (> 21% O2). The sum of the nominal values for CO2 + O2 must not exceed 90%. Example: 10% CO2 + 80% O2 = 90% (possible) 20% CO2 + 80% O2 = 100% (impossible) Before entering the chamber, all gases pass through a filter where particles larger than 0.3 µm are retained. Filter efficiency is 99.998%. A fan integrated in the rear of the interior wall ensures that the gases and the incubator atmosphere are thoroughly mixed. The sensors for CO2, O2 (option) and relative humidity are also located on the rear panel of the interior wall. These sensors measure the parameters inside the unit and transmit corresponding signals to the closed-loop controller. A pressure compensation vent on the rear panel of unit avoids undesirable pressure build-up inside the unit during the admission of gases. The place of installation must be thoroughly ventilated in order to expel the gases escaping around pressure compensation vent.
50 079 041
13/45
5. DESCRIPTION OF THE UNIT Humidification The atmosphere in the chamber is humidified through the admission of steam generated in a aktiv humifier. Relative humidity (rH) can be regulated between 60% and 95%. To ensure reliable operation of the steam generator, only fill the reservoir with fully desalinated or distilled water! The capacity of the reservoir is approx. 4.7 ltr (difference between min. and max. levels: 2.2 ltr). Door switch The heating system, gas supply and humidifier are switched off when the unit door is opened. The unit door can only be closed when all glass doors are sealed properly. If the unit door is not properly closed while the unit is in operation, a visual alarm is given (all LEDs flashing). If the door is open for longer than 10 minutes, an acoustic alarm sounds when this monitoring function is activated by way of function level 1 (refer to Page 26). Internal fittings Pull-out shelves, with support brackets to prevent tilting, are arranged inside the units. The support can be offset in the carrier racks at intervals of 46 mm. Six-piece gas-tight glass screen By virtue of the small vent cross-section, unnecessary cooling and discharge of the atmosphere in the chamber is largely avoided when a glass door is opened of the six-piece gas-tight glass screen. Lockable outside door The outside door is lockable. Disinfection routine This routine is for disinfecting the interior of the unit. In this process, the unit is heated to 180°C and kept at the disinfection temperature for approx. 3 hours. The unit is then automatically cooled down again and the nominal values for temperature, gases and relative humidity are reset. The entire procedure lasts approx. 13 hours, after which the unit is ready for operation again. "Potential - free contact" connection Connection for the customer's own signalling system, e.g. telephone system, building services management systems. If the overtemperature-protection device trips or an error is detected by the diagnosis system, a fault message is sent to the customer's own signalling system.
14/43
50 079 041
6. OPERATE Switch panel
max
(5) min
(A) "Control and display panel" (refer to Fig. 7) (1) Indicator lamp
"Fault, overtemp. protection"
(2) Indicator lamp
"Disinfection mode"
(3) Indicator lamp
"Master Switch"
(4) Vent/overflow
"Water supply"
(5) Level gauge
"Water supply"
(6) Setting knob
"Temperature protection device"
Duto-start
(7) Press button
"Disinfection mode"
control
(8) Master switch
Heraeus
des
(A)
&
autozero
&2
2
U+ L
(9) Quick-release coupling "Add/drain water" (1) (6) (2) d es s tart/ s top
(3)
(7)
(8)
, (9)
(4) a qua des t
Fig. 4: Switch panel
50 079 041
15/45
6. OPERATE Water supply Level gauge (5) indicates the water level. The water level should be in the range between "min and max". This range is equivalent to a volume of 2.2 ltr. If the water supply falls below the "min." level, a reserve of 0.5 ltr. is still available. Filling the water reservoir For humidification of the incubator, water of the following quality must be used: demineralised water that has been sterilised. or sterile water that has been demineralised. Distilled or autoclaved water is suitable. Fill the canister with the water and leave the screw cap off. Hang the canister on the bracket located on the upper left of the incubator. (fig 1) Connect the tubing connector (fig 1) into the quick fit coupling, the water reservoir will be filled under the force of gravity. Should the water not flow, there may be an airlock in the tube, in which case press on the tube bulb to move the air through. Attention: If the reservoir is overfilled the excess water any will flow from the overflow pipe. After filling place the filling canister on the floor and allow water in the filling tube to return to the canister before removing the quick fit connection. (fig 2) Attention: After filling completely empty and dry the filling canister, store the canister dry to prevent the formation of contamination.
Figure 1
16/43
Figure 2
50 079 041
6. OPERATE As the outlet not only functions as an overflow but also as a vent, it must be unsealed while the unit is in operation. To drain the empty filling canister, place it on the floor and connect it using the quickrelease coupling (9). Take care that the filling canister does not overflow. Disconnect the quick-release coupling if necessary. Always drain the water reservoir before transporting the unit.
Mains switch
0 I
Unit OFF Unit ON (the green indicator lamp (3) indicates that unit is ready for operation).
Fig. 5: Mains switch (8)
50 079 041
17/45
6. OPERATE Temperature protection device (temperature limit controller)
A temperature protection device is built into the unit and acts as a temperature limit controller. It conforms to Thermal Safety Class 3.1 to DIN 12880 Part 1/11.78. In a functional state, the temperature limit controller assumes the control function if the set temperature is exceeded. The red indicator lamp (1) "Fault" lights up as soon as the temperature limit controller responds. Fig. 6: Temperature limit controller (6)
The cutout temperature of the temperature limit controller can be adjusted in the range +20°C to +55°C using a coin or screwdriver.
Have your temperature protection device tested for proper operation at reasonable intervals. This applies in particular before prolonged work processes. Operational test: Condition: Nominal temperature (controller) reached/constant. To run this test, turn the dial on the Temperature Limit Controller so that it shows approx. +5°C less than the temperature indicated on the temperature controller. If the Temperature Limit Controller responds and the red indicator lamp (1) "Fault" comes on, the Temperature Limit Controller is operating properly. Now set the Temperature Limit Controller to the required value depending on the max. cutout temperature. If the Temperature Limit Controller is set to the upper temperature limit, it assumes the function of unit protection (protection of unit and surroundings). If the Temperature Limit Controller is set to approx. +2°C above the nominal temperature set at the temperature controller, it assumes the function of load protection (protection of unit, its environment and loaded material). The load protection function is only effective above room temperature. If "Fault" is displayed during operation: Check the settings on the Temperature Limit Controller and the controller, and correct them if necessary. If the fault cannot be rectified, contact our service department. Control and display panel (A) Microprocessor-controlled controller with digital temperature, CO2, O2 (optional) and relative humidity displays. The controller has the following functions: Temperature "set, display and control" CO2 concentration "set, display and control" O2 concentration "set, display and control" (OPTIONAL) Relative humidity "set, display and control" Error code "scan" auto-start function "activate" Switching functions - Acoustic alarm "switch ON/OFF" - Humidification "switch ON/OFF" - Manual calibration of CO2 measuring system "execute" - Setpoint lock-in "select ON/OFF - Door heater "switch ON/OFF"
18/43
50 079 041
6. OPERATE
(11)
(1)
(2)
des
&
(12)
(3)
autozero
(13)
&2
(14)
2
(15)
U+
(16)
(4) (5) (6) (7) (8)
auto-start
(9)
L
(18)
(10)
(17)
control
(19) (20)
Fig. 7: Control and display panel (A) (1) Indicator lamp "HEATING"
(11) Indicator lamp
"Disinfection mode"
(2) Display
(12) Key
"Temperature setpoint"
(13) Indicator lamp
"auto-zero"
(14) Key
"CO2 setpoint"
(5) Indicator lamp "O2/N2 GASSING" (optional)
(15) Key
"O2 setpoint" (optional)
"O2 concentration" (optional)
(16) Key
"Relative humidity setpoint"
(7) Indicator lamp "HUMIDIFICATION"
(17) Indicator lamp
"auto-start"
(8) Display
"Relative humidity"
(18) Key
"Error code inquiry" / Start calibration routines
(9) Key
"Increase reading"
(19) Indicator lamp
"Control"
(10) Key
"Decrease reading"
(20) Key
"Switching functions"
"Temperature"
(3) Indicator lamp "CO2 GASSING" (4) Display
(6) Display
"CO2 concentration"
50 079 041
19/45
6. OPERATE In its as-delivered condition, the unit is preset to the following values: Temperature: 37.0°C 0.0% CO2 concentration: 21.0% (optional) O2 concentration: Relative humidity: 60.0%, humidity control activated via function level 2 Setting the temperature setpoint: Instruction
Entry / Keys / Remarks
Switch on unit (master switch = " I ")
All display elements come on for approx. 15 seconds. - Auto-test of controller -
Display temperature setpoint Select temperature setpoint
Adopt NEW temperature setpoint
Display / Remarks / Status Example:
Actual setpoint is displayed and decimal point flashes
°C
press
°C
&
press
Setpoint increases
°C
&
press
Setpoint decreases
°C
release
Temperature inside unit is displayed
Setting the CO2 setpoint: Instruction
Entry / Keys / Remarks
Display CO2 setpoint
%CO 2
press
Select CO2 setpoint
%CO 2
&
drücken
Setpoint increases
%CO 2
&
drücken
Setpoint decreases
%CO 2
release
Adopt NEW CO2 setpoint
Display / Remarks / Status Actual setpoint is displayed and decimal point flashes
CO2 concentration inside unit is displayed
Setting the O2 setpoint (optional): Instruction
Entry / Keys / Remarks
Display / Remarks / Status
Display O2 setpoint
Actual setpoint is displayed, decimal point flashes
Select O2 setpoint
Setpoint increases Setpoint decreases
Adopt NEW O2 setpoint
O2 concentration inside unit is displayed
The control is deactivated when the unit is set for 21% O2 since this corresponds to the O2 content of air.
20/43
50 079 041