Support Manual
34 Pages
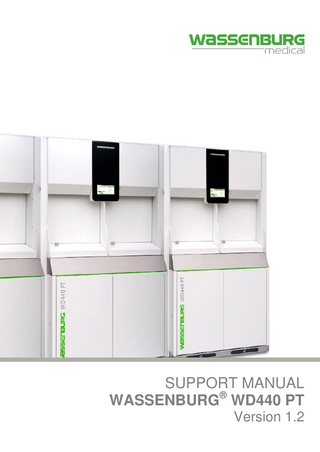
Preview
Page 1
SUPPORT MANUAL WASSENBURG® WD440 PT Version 1.2 SUPPORT MANUAL WD440 PT | AMSJ1208GB12| PAGE 1 OF 34
SUPPORT MANUAL WASSENBURG® WD440 PT WASHER-DISINFECTOR FOR FLEXIBLE ENDOSCOPES AND OTHER THERMOLABILE MEDICAL DEVICES
Machine Information Type: WD440 PT Model: Series: 302-XXX Product combination: DIS15A 0086 Document Information Support manual Version: 1.2 Language: English Date of issue: September, 2015 Ref.: AMSJ1208GB12 Manufacturer Information Wassenburg Medical B.V. Edisonring 9 6669 NA DODEWAARD THE NETHERLANDS
SUPPORT MANUAL WD440 PT | AMSJ1208GB12| PAGE 2 OF 34
© Copyright 2015 No part of this documentation may be reproduced and / or published in any form or by any means, printing, photocopying, microfilm or otherwise, without prior written permission of the publisher. All information is subject to change. Figures and photos may differ from the actual situation.
SUPPORT MANUAL WD440 PT | AMSJ1208GB12| PAGE 3 OF 34
TABLE OF CONTENTS CHAPTER 1 – INTRODUCTION _____________________________________________________________________ 5 1.1
Introduction ______________________________________________________________________________ 5
1.2
Safety symbols ___________________________________________________________________________ 5
CHAPTER 2 – PROGRAMS & PRODUCT COMBINATION ________________________________________________ 6 2.1
Programs________________________________________________________________________________ 6
2.2
Product combination _______________________________________________________________________ 6
2.3
Program sequence ________________________________________________________________________ 6
CHAPTER 3 – VALIDATION ________________________________________________________________________ 7 3.1
Introduction ______________________________________________________________________________ 7
CHAPTER 4 – IMS ________________________________________________________________________________ 8 4.1
IMS sensors _____________________________________________________________________________ 8
4.2
IMS settings on printer ticket _________________________________________________________________ 9
CHAPTER 5 – DESCALING ________________________________________________________________________ 11 CHAPTER 6 – SAMPLING _________________________________________________________________________ 12 6.1
Sampling final rinse water __________________________________________________________________ 12
CHAPTER 7 – SELF-DISINFECTION OF MACHINES CONTAMINATED WITH PRIONS ________________________ 13 7.1
Self-disinfection procedure with 2% liquid hypochlorite product _____________________________________ 13
APPENDIX 1 – DIS15A ___________________________________________________________________________ 14 APPENDIX 2 – THERMAL SELF-DISINFECTION _______________________________________________________ 17 APPENDIX 3 - CRITICAL PROCESS PARAMETERS AND PROCEDURES FOR VALIDATION __________________ 18 APPENDIX 4 – DESCALING PROTOCOL _____________________________________________________________ 21 APPENDIX 5 – SAMPLING PROTOCOL (via Validation port) ______________________________________________ 25 APPENDIX 6 – SAMPLING PROTOCOL (Optional port) __________________________________________________ 29 APPENDIX 7 - PROTOCOL FOLLOWING CONTAMINATION OF FINAL RINSE WATER _______________________ 34
SUPPORT MANUAL WD440 PT | AMSJ1208GB12| PAGE 4 OF 34
CHAPTER 1 – INTRODUCTION THIS CHAPTER CONTAINS AN INTRODUCTION AND SAFETY SYMBOLS.
1.1
Introduction
®
Thank you for using the first class WASSENBURG equipment. This support manual accompanies the WD440 PT (Pass Through) endoscope washer-disinfector. This manual is for health care professionals, who require additional supportive information regarding the use of the WD440 PT, besides the user manual. Also available are a user manual for users who operate the WD440 PT and a service manual for qualified service engineers who service the WD440 PT. The equipment may only be serviced or validated by qualified engineers. If Wassenburg is contacted for support, the machine serial number will be requested. This number can be found on the type plate in the lower section of the machine. Your authorised supplier can inform you on the approved service and validation partners. Always read the manual before use! If the equipment is used in a manner not specified by the manufacturer, the protection provided by the equipment may be impaired and all guarantees provided by the manufacturer are put at risk. Only correct use of the machine will ensure safe and effective operation of the machine according to the applicable standards. Please refer to the website www.wassenburgmedical.com for more information on the Wassenburg international distribution network.
1.2
Safety symbols
Symbols are present on the WD440 PT which indicate possible hazards. CAUTION Locations:
- Detergent suction tube; - Lower rim of the bottom plate; - In this user manual to draw attention to possible risks.
HAZARDOUS ELECTRIC POTENTIAL Location: - Screening plate of the electric equipment box (E-box) at the unload side of the machine; - Electrical entry assembly box in the upper section. MOVING PARTS Location: - Chamber lids.
HOT SURFACE Locations: - Heating element holders; - Pre-filter housing in the front section. CORROSIVE SUBSTANCES Locations: - Supply tubing from the disinfectant container; - Measuring cylinder; - Lower rim of the bottom plate. FLAMMABLE Locations: - Alcohol container (optional); - On the inside of the right door (optional). CONSULT INSTRUCTIONS FOR USE Indicates the need for the user to consult the instructions for use. NOTE! Location:
- In this manual to draw attention to important points.
SUPPORT MANUAL WD440 PT | AMSJ1208GB12| PAGE 5 OF 34
CHAPTER 2 – PROGRAMS & PRODUCT COMBINATION IN THIS CHAPTER DETAILED INFORMATION IS GIVEN CONCERNING ALL POSSIBLE PROGRAMS AND AVAILABLE PRODUCT COMBINATION. THE PRODUCT COMBINATION IS THE COMBINATION OF DETERGENT AND DISINFECTANT USED.
2.1
Programs
The available programs and accompanying process duration depend on the machine settings. An overview of all possible programs: Program
Approx. duration
Suitable for:
Processed endoscopes; Endoscopes for which the storage time limit has been exceeded after a drying and conditioning process
28 - 33 min.
Endoscopes that have just been used for patient examination and/or treatment
24 - 38 min.
Intensive
Soiled endoscopes that were not reprocessed immediately after use
29 - 48 min.
Self-disinfection (chemical)
Disinfecting the circulation system in the WD440 PT
35 min.
Self-disinfection (thermal)
Disinfecting the circulation system in the WD440 PT
70 min.
Short Dis
Normal Wash-Dis Wash-Dis-Alc.
2.2
Product combination
The combination of detergent and disinfectant for which your machine has been configured can be found by pressing the button in the bottom left corner on the display (see figure 2.1).
Changing to a different combination of detergent and disinfectant requires both mechanical and configurational changes to the machine that can only be carried out by a qualified service engineer authorized by Wassenburg. Never use a new detergent or disinfectant without first contacting your authorised WD440 PT supplier; If the WD440 PT contains the positioning bracket, the detergent and disinfectant containers should be placed in the bracket. If switching to a different type of detergent and/or disinfectant, contact the authorised WD440 PT supplier to check whether these containers also fit in the positioning bracket present in the machine.
FIGURE 2.1 | Contact information The contact information screen provides information on the manufacturer, display and PLC software versions, product combination (DIS) and the serial number of the machine.
2.3
Program sequence
Please refer to the appendices in this support manual mentioned below: Appendix 1 2 1
Document ref. AORJ0110 GB
1
DIS
Detergent
15A
®
Disinfectant
EndoHigh Detergent
®
EndoHigh GTA
AARB1701GB Program sequence thermal self-disinfection These documents may be subject to updates. Please contact your authorised supplier for up-to-date information.
SUPPORT MANUAL WD440 PT | AMSJ1208GB12| PAGE 6 OF 34
CHAPTER 3 – VALIDATION FOR USE OF THE WD440 WHICH IS COMPLIANT WITH THE ISO 15883 STANDARD, A PERIODIC VALIDATION OF THE INSTALLED EQUIPMENT IS REQUIRED.
3.1
Introduction
During validation the critical process parameters are validated against the original manufacturer specifications. Validation requirements of the ISO 15883 standard and additional manufacturer validation procedures have to be followed.
The equipment may only be validated by qualified engineers. Your authorised supplier of Wassenburg products can inform you about the approved validation partners; During validation of the equipment NO disassembly activities should be carried out, such as taking out electrical connections, sensors, etc.
Please refer to the appendix in this support manual mentioned below:
1
Appendix
Form code
Description
Version
3
KNC04JW01
Critical process parameters and procedures for validation
V1.06
1
This document may be subject to updates. Please contact your authorised supplier for up-to-date information
SUPPORT MANUAL WD440 PT | AMSJ1208GB12| PAGE 7 OF 34
CHAPTER 4 – IMS THE ISO 15883 STANDARD DEMANDS A VERIFICATION OF THE PROCESS WHEREBY THE CRITICAL PARAMETERS ARE VERIFIED AND/OR RECORDED BY A SYSTEM WHICH IS INDEPENDENT FROM THE CONTROLLER.
4.1
IMS sensors
The Independent Monitoring System (IMS) monitors critical parameters by using additional sensors. Detailed information on IMS is included in table 4.1. Parameters monitored by IMS
Condition
Control
Analogue / Digital
Position
1
Right process Additional PT100 Analogue - digits A temperatures? Conductivity final rinse Additional conductivity 2 Conductivity Analogue - digits B water? sensor Right volume of Detergent control Pulse flow sensor Digital - counter C detergent added? Right volume of Additional liquid level Digital - present / Disinfectant control D disinfectant added? relay not present Final rinse and Digital - present / Flow through bacterial filter disinfection performed Additional flow switch F not present with filtered water? Flow along the outside Additional pressure Digital - present / Circulation pressure G of the endoscope? switch not present Process carried out in Time Separate controller plc Digital - digits Not shown right time? Sprinkler rotation Does the sprinkler Digital - present / Rotation sensor H (sensor not independent) rotate? not present 1 See illustration 4.1 – Positions are highlighted yellow 2 The IMS conductivity control is an optional feature. However, local regulations may require the conductivity control. Temperature
TABLE 4.1 | Parameters monitored by IMS
SUPPORT MANUAL WD440 PT | AMSJ1208GB12| PAGE 8 OF 34
ILLUSTRATION 4.1 | IMS sensors
4.2
IMS settings on printer ticket
It is possible to print a separate printer ticket which shows the IMS settings. Select Print IMS settings in the IMS temperature offset screen. FIGURE 4.1 | IMS settings on print-out If IMS settings are changed, an IMS settings ticket should be printed. Choose PRINT to print the ticket.
The IMS SET is a unique number for the used IMS settings. In illustration 4.2 an example of the IMS settings printer ticket is shown. The example only shows the settings for the short program. A complete IMS settings printer ticket shows the settings for each possible program and the thermal selfdisinfection.
SUPPORT MANUAL WD440 PT | AMSJ1208GB12| PAGE 9 OF 34
1
2
3
4
ILLUSTRATION 4.2 | IMS Printer ticket with IMS settings
1
Product combination-batch number
2
Amount entered in disinfectant calibration screen 5% is the maximum deviation for the dosing system
3
Settings are set for 3 programs and 1 thermal disinfection
4
Settings of process steps which are not set can also be printed
SUPPORT MANUAL WD440 PT | AMSJ1208GB12| PAGE 10 OF 34
CHAPTER 5 – DESCALING IF SCALE APPEARS IN THE MACHINE, WASSENBURG ADVISES DESCALING THE MACHINE EVERY SIX MONTHS. Please refer to appendix in this support manual mentioned below:
1
Appendix
Form code
Description
Version
4
GOB09JW01
Descaling protocol
V1.02
1
This document may be subject to updates. Please contact your authorised supplier for up-to-date information.
SUPPORT MANUAL WD440 PT | AMSJ1208GB12| PAGE 11 OF 34
CHAPTER 6 – SAMPLING WASSENBURG RECOMMENDS PERIODIC SAMPLING OF THE FINAL RINSE WATER.
6.1
Sampling final rinse water
Wassenburg recommends periodic sampling of the final rinse water in the WD440 PT. This water is filtered through the EndoCap bacterial filter in the WD440 PT before coming into contact with the endoscope. Only water samples taken using the Wassenburg protocol can be used for microbiological testing. It is required that water samples are taken during the last rinse step of the final rinse step. Microbiological tests taken on water samples from other process steps or during any of the help functions may not give reliable results. Please refer to the appendices in this support manual mentioned below:
1
Appendix
Document ref.
Description
Version
5
KNE07WK01
Sampling protocol – For systems with a validation port
V1.03
6
KOM12TB01
Sampling protocol – For systems with optional sampling port
V1.01
7
KKE11GM01
Protocol following contamination of final rinse water in the WD440
n/a
1
These documents may be subject to updates. Please contact your authorised supplier for up-to-date information.
SUPPORT MANUAL WD440 PT | AMSJ1208GB12| PAGE 12 OF 34
CHAPTER 7 – SELF-DISINFECTION OF MACHINES CONTAMINATED WITH PRIONS THIS PROCEDURE SHOULD ONLY BE FOLLOWED IN THE EVENT OF KNOWN OR SUSPECTED CONTAMINATION OF THE MACHINE WITH THE PRION RESPONSIBLE FOR A TRANSMISSIBLE SPONGIFORM ENCEPHALOPATHY, SUCH AS NEW VARIANT CREUTZFELDT JAKOB DISEASE.
7.1
Self-disinfection procedure with 2% liquid hypochlorite product
This procedure should not be used for routine self-disinfection of the machine. The efficiency of this procedure against the new variant Creutzfeldt Jakob disease is not proven. However, it is a procedure which is recommended by different opinion leaders and research groups in the event of such contamination. It has also been advised to destroy all materials which have been in contact with the contact fluid. In case of a suspected case of new variant Creutzfeldt Jakob disease, follow the local regulations and advice.
Step
Action
1
Open the lid of the machine and remove and discard the red leakage test tubing from the chamber. Disposal of the (potentially) contaminated red leakage test tubing and bacterial filters should be carried out according to the procedure in use at the hospital. Check that all other channel tubing is present in the chamber;
2
Put the leakage test plug on the leakage test connector in the chamber;
3
Start the help function FILL (see § 4.6.4 in the user manual). Select filtered water. The filling stops automatically when the chamber is full. The system then contains approximately 6 litres of water;
4
Add hypochlorite to the water to give a final concentration of 2% active chlorine;
5
Close the lid and select the TOOLS tab (see § 4.6.4 in the user manual);
6
Start the help function CIRCULATE (see § 4.6.4 in the user manual);
7
Allow the circulation to continue for 60 minutes (as recommended in circular 138 from the French general health direction). When this time has been reached, stop the circulation by pressing the button STOP;
8
Start the help function DRAIN (see § 4.6.4 in the user manual);
9
When the chamber is empty, fill the chamber with water using the help function FILL (see § 4.6.4 in the user manual). Select filtered water;
10
Start the help function CIRCULATE and let this help function run for 2 minutes;
11
Empty the chamber using the help function DRAIN;
12
When the chamber is empty, start a normal program without an endoscope in the chamber;
13
At the end of the program, remove the leakage test plug and place a new red leakage test tube in the chamber. Wassenburg recommends discarding any endoscope connection material that may be contaminated with prions.
SUPPORT MANUAL WD440 PT | AMSJ1208GB12| PAGE 13 OF 34
APPENDIX 1 – DIS15A
SOLUTION AND PROGRAM SEQUENCE Reference: AORJ0110 GB Version: V1.00
Changing to a different combination of detergent and disinfectant requires both mechanical and configurational changes to the machine that can only be carried out by a qualified service engineer authorized by Wassenburg. Never use a new detergent or disinfectant without first contacting your authorised WD440 (PT) supplier. The following solutions are all suitable for use in the WD440 (PT), provided the rinse step takes place between the washing and disinfection steps. This table shows a summary of the properties as used in the WD440 (PT). Name of product
Type
®
EndoHigh Detergent Detergent ®
EndoHigh GTA
Disinfectant
Application Automatic washing Pre-cleaning Automatic disinfection
Dose
Temperature
Compatible with
0.5%
36 - 41 °C for 5 min
EndoHigh GTA
1.0%
55 - 60 °C for 5 min
EndoHigh Detergent
®
®
Validation information is available from your Wassenburg authorised supplier on request. The following pages contain details of the program sequence of the different programs in the machine. ® For machines in which EndoHigh GTA is used as disinfectant, the following programs are available: Washing and Disinfection (WASH-DIS); Washing, Disinfection and Alcohol rinse (WASH-DIS-ALC); Disinfection (DIS)* (only disinfection step). * Local regulations may prohibit use of a ‘disinfection only’ program.
SUPPORT MANUAL WD440 PT | AMSJ1208GB12| PAGE 14 OF 34
During the program, a number of controls are carried out. The descriptions of these controls are abbreviated in the table as follows: Abb.
Description
CP *
Channel pressure control; checks for the presence of blockages in the endoscope channels
PC
Circulation pressure control; checks whether the required pressure is reached in the sprinkler Temperature; checks whether the temperature of the fluid corresponds to the temperature entered for the program step concerned Temperature too high; checks whether the temperature is above the maximum allowed value
T TH W
L
Water supply; checks whether the level is reached within the set time Leakage control; checks whether the pressure in the endoscope remains high during the program, in order to prevent the penetration of fluid Leakage; checks whether fluid appears in the drip tray at the bottom of the WD440 (PT)
MD
Maximum drainage time; checks whether the maximum drainage time is exceeded
DM
Minimum drainage time; checks the minimum drainage time
DD
Detergent dosage control; checks whether the correct amount of detergent is dispensed (optional)
DC
Disinfectant dosage control; checks whether the correct amount of disinfectant is dispensed
FC
Flow control; checks whether fluid is supplied to the channel tubing
TC
Tube connection control; checks whether the channel tubing is connected to the endoscope channel
SR
Sprinkler rotation control; checks the rotation of the sprinkler
LC
th
SC
th
7 channel flow control; checks for the minimum flow in the 7 channel During process steps in which fluid is pumped through the endoscope channels, the channel pump turns until the pressure measured by the pump pressure sensor reaches 1.5 bar. The pump will then stop. Once the pressure drops to below 1.0 bar, the pump will start to turn again. The pressure drop from 1.5 to 1.0 bar should take place within a set time. If this does not occur then an error message will be given. The channel concerned could in that case be blocked.
*
STEP
PROGRAMS
1
®
DESCRIPTION
TIME
EndoHigh GTA
CONTROL
Control step
WASH-DIS
WASH-DISALC
DIS
Lid closed
X
X
X
Level switch
X
X
X
Circ. pressure switch
X
X
X
Flow switch
X
X
X
Pressure sensors
X
X
X
Fuses (if applicable)
X
X
X
Detergent level control
X
X
X
Position filter disinfection system quick coupling
X
X
X
Lid closed 2nd control
X
X
X
Leakage test 2
Pump air
Max. 150 sec
Pressure increase
X
X
X
3
Wait
6 sec
Pressure stabilization
X
X
X
4
Leakage test
1 min
Leakage
X
X
X
5
Cold water fill
Until chamber is full
6
Channel circulation
7
Drain
8
Water fill
Prerinse program (depending on program choice) W;TH;LC;L
X
X
TH;LC;L
20 sec
20 sec
X
X
Until chamber is empty
MD;TH;LC;L
W;TH;LC;L
X
X
Influx temp. 39 °C
Until chamber is full
Detergent dose
< 15 sec
TH;LC;L;DD
X
X
Washing
9
1
SUPPORT MANUAL WD440 PT | AMSJ1208GB12| PAGE 15 OF 34
STEP
PROGRAMS ®
DESCRIPTION
TIME
EndoHigh GTA
CONTROL WASH-DIS
WASH-DISALC
305 sec
305 sec
X
X
X
X
X
20 sec
20 sec
20 sec
X
X
X
TH;LC;L;DC
X
X
X
X
X
X
2
10
Channels + sprinkler circulation
CP;PC;TH;LC;L;FC ;TC; SR
11
Drain
12
Water fill
13
Channels + sprinkler circulation
14
Drain
15
Repeat steps 8 - 14
See steps 8 - 14
16
Repeat steps 12-14
See steps 12 - 14
Until chamber is empty
MD;TH;LC;L
Until chamber is full
W;TH;LC;L
DIS
Intermediate rinse 1
PC;TH;LC;L;SR Until chamber is empty
MD;TH;LC;L
Disinfection 17
Control measuring cylinder (fill)
18
Water fill and drain
Until temp is OK
T;TH;W;LC;L
19
Water fill
1
Until chamber is full
T;TH;W;LC;L
± 30 sec
TH;LC;L;DC
20
Disinfectant dose
21
Channels + sprinkler circulation
22
Drain
CP;PC;T;TH;LC;L; 2 FC ;TC;SR Until chamber is empty
TH;LC;L;MD Rinse with filtered water
23
Water fill
24
1
X
X
X
Influx temp. 59 °C
Influx temp. 59 °C
Influx temp. 59 °C
X
X
X
305 sec
305 sec
305 sec
X
X
X
3
Until chamber is full
TH;W;LC;L
X
X
X
Channels + sprinkler circulation
60 sec
PC;TH;LC;L;SR
X
X
X
25
Drain
Until chamber is empty
TH;LC;L;MD
X
X
X
26
Repeat steps 23 - 25
See steps 23 - 25
X
X
X
27
Air purge
60 sec
TH;LC;L Alcohol rinse
4
28
Air purge
60 sec
LC;L
X
29
Alcohol rinse
± 60 sec
LC;L
X
30
Air purge
60 sec
LC;L
X
31
Drain
Until chamber is empty
TH;LC;L;MD
X
32
Repeat steps 2 - 4
Leakage test TH;L
End of program During steps 6, 10, 13, 21 and 24 the fluid temperature and program step time are shown in the DASHBOARD. 1 The temperature should be adjusted according to the instructions for use of the products or as instructed by the authorised WD440 (PT) supplier. 2 Depending on the setting in the machine, the flow control can be activated during the washing and/or disinfection steps. 3 For machines linked to a reverse osmosis water treatment system, the final rinse steps are carried out using water treated by reverse osmosis. 4 Only applicable if this option is installed. SUPPORT MANUAL WD440 PT | AMSJ1208GB12| PAGE 16 OF 34
APPENDIX 2 – THERMAL SELF-DISINFECTION PROGRAM SEQUENCE Reference: AARB1701GB Version: V1.00 During the program, a number of controls are carried out. The descriptions of these controls are abbreviated in the table as follows: Abb. Description PC
Circulation pressure control; checks whether the required pressure is reached in the sprinkler
T
Temperature; checks whether the temperature of the fluid corresponds to the temperature entered for the program step concerned
TH
Temperature too high; checks whether the temperature is above the maximum allowed value
W
Water supply; checks whether the level is reached within the set time
LC
Leakage control; checks whether the pressure in the endoscope remains high during the program, in order to prevent the penetration of fluid
L
Leakage; checks whether fluid appears in the drip tray at the bottom of the WD440
MD
Maximum drainage time; checks whether the maximum drainage time is exceeded
SR
Sprinkler rotation control; checks the rotation of the sprinkler
Step
Description
1
Control step
Time
Control
Lid closed Level switch Circ. pressure switch Flow switch Pressure sensors Detergent container level control Position filter disinfection system coupling
2
Move mixing valve to hot position
Until mixing valve is in hot position
Control mixing valve; L; LC;TH
3
Start delay with timer program
Until time set in timer program is reached
L;LC
4
Water fill and drain
Until the measured exceeds 65ºC
T;TH;W;LC;L
5
Drain
Until chamber is empty
TH;LC;L;MD
6
Hot water fill
Until chamber is full
T;TH;W;LC;L
7
Channels + sprinkler circulation
1 minute
PC;TH;LC;L;SR
8
Drain
Until chamber is empty
TH;LC;L;MD
9
Hot water fill
Until chamber is full
T;TH;W;LC;L
10
Channels + sprinkler circulation Heating to set temperature (standard setting at least 80ºC)
After reaching set temp. 15 min circulation.
PC;T;TH;LC;L;SR
11
Channels + sprinkler circulation
Until temperature is lower than temperature set (standard setting at least 80ºC)
PC;TH;LC;L;SR
12
Drain
Until chamber is empty
TH;LC;L;MD
temperature
SUPPORT MANUAL WD440 PT | AMSJ1208GB12| PAGE 17 OF 34
APPENDIX 3 - CRITICAL PROCESS PARAMETERS AND PROCEDURES FOR VALIDATION Reference: KNC04JW01 Version: V1.06 Applicable for: WD440 from serial number 202-001 and WD440 PT from serial number 302-001 1. Introduction This document is intended to inform you about critical process parameters and procedures, as well as parameters which deviate from the ISO 15883 standard. Wassenburg strongly recommends you to follow the ISO 15883 standard for the validation of the system. Please use the critical process parameters listed in this document and use the Wassenburg specific procedures and parameters where necessary. 2. Validation ISO 15883-1 Annex A and ISO 15883-4 Annex C both describe possible activities and test programs. During the lifetime of the equipment a periodic validation to verify the system’s compliance with its original specifications must be performed to demonstrate the continued reproducibility of the validated process cycle. In this document the critical process parameters and some validation procedures are provided. For validation of the system use the procedures applicable for endoscope washer disinfectors described in ISO 15883-1 and ISO 15883-4.
Follow the validation procedure as described in the ISO 15883 standard; For purposes of validation, parts, assemblies and/or process parameters must not be disassembled, disconnected and/or modified unless specified in this document; Use the values as described in chapter 3 of this protocol ‘Critical process parameters’; Please bear in mind the Wassenburg specific procedures as described in chapter 4 of this protocol; Use standard measuring instruments, except for the Wassenburg specific instruments mentioned in Chapter 5 of this protocol.
3.
Critical process parameters
3.1
Temperature settings Washing step
Disinfection step
Code
Temperature
Duration
Temperature
Duration
DIS01B
36 - 41ºC
≥ 5 min
55 - 60ºC
> 10 min
DIS01C
36 - 41ºC
≥ 5 min
55 - 60ºC
≥ 5 min
DIS02F/G
36 - 41ºC
≥ 5 min
25 - 35ºC
≥ 10 min
DIS04A
40 - 45ºC
≥ 5 min
55- 60ºC
≥ 5 min
DIS14 DIS14A/B/C
40 - 45ºC
≥ 5 min
40 - 45ºC
≥ 5 min
from serial number 201-001 or 301-001 202-001 or 302-001
40 - 45ºC
≥ 3 min
40 - 45ºC
5 min
55 - 60ºC
≥ 5 min
DIS15A 36 - 41ºC ≥ 5 min Remark: temperature range is applicable when timer runs.
SUPPORT MANUAL WD440 PT | AMSJ1208GB12| PAGE 18 OF 34
Disinfection step Code
Temperature
Duration
Thermal disinfection
>80ºC
≥ 15 min
3.2
Dosing settings Detergent
Code
Disinfectant
DIS01 B/C
Dosing WD440 35 – 40 ml
Dosing WD440 PT 38 – 43 ml
Dosing WD440 64 – 68 ml
Dosing WD440 PT 71 – 75 ml
DIS02 F/G
35 – 40 ml
38 – 43 ml
64 – 68 ml
71 – 75 ml
DIS04A
35 – 40 ml
DIS14
31 – 34 ml
34 – 37 ml
93 – 95 ml
102 – 104 ml
DIS14A/B/C
31 – 33 ml
34 – 36 ml
93 – 95 ml
102 – 104 ml
DIS15A
31 – 33 ml
34 – 36 ml
62 – 64 ml
68 – 70 ml
64 – 68 ml
ISO 15883-4 §4.1.6: Accuracy of the set volume of chemicals permitted is ± 5%. 4.
Wassenburg specific validation procedures
4.1
Temperature cut-out (ISO 15883-1 §6.8.5)
Make sure you perform the temperature test referred to in 3.1 or run a normal process after this test to confirm that all sensors are in place and connected.
Use a data logger with thermosensors to obtain temperature data; Place thermosensors at the positions indicated in the standard; Remove the PT100 sensors from the pump nozzles and replace them with the dummy sensors; Start a program; The machine will continue to heat up. If a “temperature too low” alarm occurs, press RESTART; When the cut-off temperature is reached the NTC switches off the heating element; The LED on the relays (K1 for right or K4 for left) will now switch off; Abort the process with rinsing; Return the PT100 sensors. ► ►
NTC 60°C switches off between 60°C and 62°C. NTC 50°C switches off between 48°C and 52°C (product combinations at room temperature).
Requirement: The temperature cut-out must operate at a temperature not more than 5°C higher than the highest temperature provided by any of the thermosensors connected to the data logger. ►NTC 60°C switches off between 60°C and 62°C ► max. temperature = 67°C ►NTC 50°C switches off between 48°C and 52°C ► max. temperature = 57°C 4.2
Wassenburg empty bottle detection method (EN ISO 15883-1 §6.9.2) Wear protective gloves for this test
4.2.1 Equipment Protective gloves; Empty container. 4.2.2 Protocol for detergent Remove the suction tube from the empty container and place it with the tube pointing upwards; Restart the program; A failure notice will be displayed indicating an insufficient volume of detergent; Place the suction tube in the detergent container in the washer disinfector.
SUPPORT MANUAL WD440 PT | AMSJ1208GB12| PAGE 19 OF 34
4.2.3 Protocol for disinfectant Unscrew the cap of the disinfectant container; Remove the cap with the suction tube from the disinfectant container; Note! The suction tube may drip disinfectant; Place the suction tube in an empty container; Start a program on both sides; A failure notice will be displayed indicating an insufficient volume of disinfectant; Abort the program (with rinse); Place the cap with the suction tube on the disinfectant container in the washer disinfector; Clean up any spilled disinfectant residue. 4.2.4 Requirements A failure notice should appear on the display for both detergent and disinfectant, as well for the left and right sides. 4.3 Leakage test (ISO 15883-4 §6.5) If a leakage of 10 mbar or more is measured, an endoscope is considered to leak. To test this failure notice on the washer disinfector, a leakage test device is required. The maximum internal volume of the endoscope the washer disinfector can handle is a non-restricted volume of 1100 ml. 4.4
Pressure sensor verification test (ISO 15883-1 §6.6.1)
4.4.1 Equipment Pressure gauge; Connection tubes for pressure sensor calibration. 4.4.2 Protocol Attach the CPC connector to channel 1 of the washer disinfector; Pressurize the channel to 1000 mbarg (displayed on the pressure gauge); When the pressure is 1000 mbarg, check the pressure on the display of the washer disinfector. 4.4.3 Requirements +0 Pressure per channel = 1000 / -50 mbarg. 4.5
Channel flow and pressure test
4.5.1 Protocol: Channel pressure check (help function: rinse) Check the leakage from the channel pumps by checking the pressure drop on the display at a pressure of 950 – 1000 mbarg for 15 seconds; This must not be greater than 15 mbarg; Remove the tube clamp after this measurement and measure the output; Select the help function RINSE in the TOOLS tab and start the function with the lid open; Measure the output for each channel and check that the pumps switch off at a pressure of ± 1.5 bar and switch on again at a pressure of ± 1.0 bar. 4.5.2 Requirements The pumps should switch on and off at the required pressures. Specifications of channel pumps when using 4.8x1.6 channel pump tubing: Channel
Tube colour
Motor speed RPM
Min. capacity ml/min
Max. capacity ml/min
1
Yellow
48
50
90
2
Blue
48
50
90
3
Orange
310
400
550
4
Brown
310
400
550
5
White
48
50
90
6
Green
48
50
90
5. Wassenburg specific measuring equipment Surrogate endoscope for validating the blockage test (ISO 15883-4 §6.6) and several thermometric tests as described in part 1 and part 4 of the standard. The surrogate endoscope can also be used as a standardized load during test procedures. The surrogate endoscope is available under article no. 08350001. Standard PT100 measuring instrument with Ø6mm.
SUPPORT MANUAL WD440 PT | AMSJ1208GB12| PAGE 20 OF 34