2 Pages
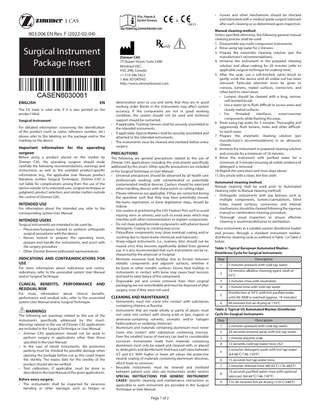
Preview
Page 1
• &
0413
803.006 EN Rev. F (2022-02-04)
Surgical Instrument Package Insert
ENGLISH
Zimmer CAS 75 Queen Street, Suite 3300 Montreal (QC) H3C 2N6, Canada +1 514 396 5422 1 866 3D ORTHO http://www.zimmerbiomet.com
EN
The CE mark is valid only if it is also printed on the product label. Surgical Instrument For detailed information concerning the identification of the product (such as name, reference number, etc.) please refer to the labeling on the package and/or the marking on the device
Important information for the operating surgeon
Before using a product placed on the market by Zimmer CAS, the operating surgeon should study carefully the following recommendations, warnings and instructions, as well as the available product-specific information (e.g., the applicable User Manual, product literature, written Surgical Technique). Zimmer CAS is not liable for complications arising from the use of the device outside of its indicated uses, surgical technique or judgment, product selection, and similar matters outside the control of Zimmer CAS.
INTENDED USE
For information about the intended use, refer to the corresponding system User Manual.
INTENDED USERS
Surgical instruments are intended to be used by: • Physicians/Surgeons trained to perform orthopedic surgical procedures with the device • Nurses trained to prepare the operating room, prepare and handle the instruments, and assist with the surgery procedure • Other Zimmer Biomet authorized representatives
INDICATIONS AND CONTRAINDICATIONS FOR USE
For more information about indications and contraindications, refer to the associated system User Manual and/or Surgical Technique.
CLINICAL BENEFITS, RESIDUAL RISK
PERFORMANCE
AND
For more information about clinical benefits, performance and residual risks, refer to the associated system User Manual and/or Surgical Technique.
WARNINGS
The following are warnings related to the use of the instruments specifically addressed by this insert. Warnings related to the use of Zimmer CAS applications are included in the Surgical Technique or User Manual. • Zimmer CAS applications should not be used to perform surgery in applications other than those specified in the User Manual. • In the case of sterile instruments, the protective packing must be checked for possible damage when opening the package before use as this could impair the sterility. The expiry date for the sterility of the product should also be verified. • Tool calibration, if applicable, must be done as described in the User Manual of the given applications. Before every surgery: • The instruments shall be inspected for excessive bending or other damages such as fatigue or
• • •
deterioration prior to use and verify that they are in good working order. Bends in the instruments may affect system accuracy. If the components are not in good working condition, the system should not be used and technical support should be contacted. If applicable, Tracking Sensors shall be securely assembled to the intended instruments. If applicable, Optical Markers shall be securely assembled and attached to the intended instruments. The instruments must be cleaned and sterilized before every surgery.
PRECAUTIONS
The following are general precautions related to the use of Zimmer CAS applications including the instruments specifically addressed by this insert. Other specific precautions are included in the Surgical Technique or User Manual. • Universal precautions should be observed by all health care professionals working with contaminated or potentially contaminated medical devices. Caution should be exercised when handling devices with sharp points or cutting edges. • If bone references are applicable, if they are contacted during the operation such that they may have potentially moved, the bone registration, or bone digitization steps, should be redone. • Use caution in positioning the CAS Fixation Pins such to avoid injuring veins or arteries, and such to avoid areas which may interfere with other instrumentation or implant components. • Do not clean polyetherimide components with phenol-based detergents. Crazing or cracking may occur. • Polysulfone components may show eventual crazing and/or cracking due to steam boiler chemicals and lubricants. • Sharp-edged instruments (i.e., reamers, bits) should not be reused once they become significantly dulled from general use. It is also recommended that such instruments not be resharpened by the physician or hospital. • Minimize excessive heat buildup due to friction between metallic components and adjacent surfaces, whether it be bone or other metallic surfaces. Excess heat buildup in instruments in contact with bone may cause heat necrosis and lead to early failure of the component. • Disposable pin and screws removed from their original packaging are not resterilizable and must be disposed of after surgery, even if they were not used.
CLEANING AND MAINTENANCE • •
•
•
Instruments must not come into contact with substances containing chlorine or fluorine. Instruments that are made wholly or partly of plastic must not come into contact with strong acids or lyes, organic or ammonia-containing solvents, aromatic and/or halogen hydrocarbons or oxidizing chemicals. Aluminium and materials containing aluminium must never come into contact with substances containing mercury. Even the smallest traces of mercury can lead to considerable corrosion. Instruments made from materials containing aluminium must only be wiped and cleaned with, or placed in, detergents and disinfectants that have a pH value between 4.5 and 8.5. With higher or lower pH values the protective neutral coating of materials containing aluminium dissolves, which leads to corrosion. Reusable instruments must be cleaned and sterilized between patient uses (also see Instructions under section SPECIAL INSTRUCTIONS FOR GENERIC INSTRUMENT CASES) Specific cleaning and maintenance instructions as applicable to each instrument are provided in the Surgical Technique or User Manual
Page 1 of 2
Screws and other mechanisms should be checked and lubricated with a medical grade surgical lubricant after each cleaning or as determined upon inspection.
Manual cleaning method Unless specified otherwise, the following general manual cleaning process shall be used: 1. Disassemble any multi-component instruments. 2. Rinse using tap water for 2 minutes. 3. Prepare the enzymatic cleaning solution (per the manufacturer’s recommendations). 4. Immerse the instrument in the prepared cleaning solution and allow soaking for 20 minutes (refer to applicable surgical technique for soaking time). 5. After the soak, use a soft-bristled, nylon brush to gently scrub the device until all visible soil has been removed. Particular attention must be given to crevices, lumens, mated surfaces, connectors, and other hard-to-clean areas. • Lumens should be cleaned with a long, narrow, soft-bristled brush. • Use a water jet to flush difficult to access areas and closely mated surfaces. • For threaded interfaces, screw/unscrew components while flushing the areas. 6. Rinse using tap water for 3 minutes. Thoroughly and aggressively flush lumens, holes and other difficultto-reach areas. 7. Prepare the enzymatic cleaning solution (per manufacturer’s recommendations) in an ultrasonic cleaner. 8. Immerse the instrument in prepared cleaning solution and sonicate for a minimum of 10 minutes. 9. Rinse the instrument with purified water for a minimum of 3 minutes ensuring all visible evidence of detergent is removed. 10. Repeat the sonication and rinse steps above. 11. Dry article with a clean, lint-free cloth. Automated cleaning method Manual cleaning shall be used prior to Automated cleaning (refer to Manual cleaning method). • Orthopedic instruments with any features such as multiple components, lumens/cannulations, blind holes, mated surfaces, connectors and internal mechanisms should be cleaned following the rigorous manual or combination cleaning procedure. • Thorough visual inspection to ensure effective cleaning is recommended prior to sterilization. Place instruments in a suitable washer-disinfector basket and process through a standard instrument washerdisinfector cleaning cycle as outlined in Table 1 or Table 2 below. Table 1: Typical European Automated WasherDisinfector Cycle for Surgical Instruments Step
Description
1
5 minutes prewash with cold tap water
2
10 minutes alkaline cleaning agent wash at 55°C
3
2 minutes rinse with neutralizer
4
1 minute rinse with cold tap water
5
Disinfection at 93°C with hot purified water until A0 3000 is reached (approx. 10 minutes)
6
40 minutes hot air drying at 110°C
Table 2: Typical US Automated Washer-Disinfector Cycle for Surgical Instruments Step
Description
1
2 minutes prewash with cold tap water
2
20 seconds enzyme spray with hot tap water
3
1 minute enzyme soak
4
15 seconds cold tap water rinse (X2)
5
2 minutes detergent wash with hot tap water (64‑66°C/146‑150°F)
6
15 seconds hot tap water rinse
7
2 minutes thermal rinse (80‑93°C/176‑200°F)
8
10 seconds purified water rinse with optional lubricant (64‑66°C/146‑150°F)
9
7 to 30 minutes hot air drying (116°C/240°F)
Note: The washer-disinfector manufacturer’s instructions should be strictly adhered to. Use only cleaning agents recommended for the specific type of automated washer-disinfector. A washer-disinfector with approved efficacy (e.g. CE mark, FDA approval, and validation according to ISO 15883) should be used. • Only agents with proven efficacy (FDA approved, VAHlisted, or CE mark) should be used. As a large variety of cleaning agents and disinfectants exists around the globe, Zimmer CAS does not recommend any specific brand. • Agents used during the validation of these processing instructions are: neodisher® MediClean forte. Valsure® Enzymatic Cleaner and Neutral Detergent, Enzol® Enzymatic Detergent.
STORAGE AND HANDLING
STERILIZATION
The user and/or patient should report any suspected serious incident related to the device by informing the manufacturer and the competent authority of the member state in which the serious incident has occurred.
•
• • •
Instruments should not be sterilized in the protective bag or packaging supplied with them. They must be cleaned and disinfected prior to sterilization. The packaging method must be suitable for the items being sterilized and the sterilization process. All sterilizations should be performed using standard and regularly maintained equipment. The steam used for sterilization must be free from impurities. For instruments sterilized within instrument cases, wrapping in two layers of 1‑ply polypropylene (or equivalent) is recommended.
• • •
•
Protective caps or other protective devices must not be removed until immediately before use. Instruments can be stored either in their original packing unopened or in the appropriate instrument tray, or in other suitable packing that protects the instruments from damage. The instruments and their components are subject to wear and therefore have to be considered as non-durable material. The integrity of the instruments has to be checked before use and if necessary, instruments must be returned to the responsible local representative for repair or disposal. Instruments that are returned must be cleaned, disinfected and sterilized prior to return, and be accompanied by a written confirmation of sterilization.
ADVERSE EVENTS/COMPLAINT HANDLING
© 2022, Zimmer Biomet.
Reusable instruments, pins and screws sold non-sterile, should be sterilized using the Steam Sterilization method as follows: Steam Sterilization (Autoclave) Cycle Type
Temperature1
Exposure Time1
Minimum Dry Time2
Minimum Cool Time3
PreVacuum
132°C (270°F)
4 minutes
30 minutes4
30 minutes4
Both the given cycle temperature and time can be increased to 134°C + 3°C (273.2°F + 5.4°F) and 18 minutes according to local requirements outside of the United States such as in the European Union. 2 Drying times vary according to load size and should be increased for larger loads. 3 Cooling times vary according to the type of sterilizer used, device design, temperature and humidity of ambient environment, and type of packaging used. Cooling process should comply with ANSI/AAMI ST79. 4 For iAssist instruments, dry time and cool down time shall be increased to 40 minutes. The door shall remain open for 10 minutes after the cooling phase. 1
SPECIAL INSTRUCTIONS FOR GENERIC INSTRUMENT CASES (CASES WITHOUT DEFINED, PRECONFIGURED LAYOUTS OR CONTAINING UNDEFINED UNIVERSAL SPACES OR COMPARTMENTS)
Universal instrument trays and cases without defined, preconfigured layouts or containing undefined universal spaces or compartments should only be used under the following conditions: • The total weight of a wrapped instrument tray or case should not exceed 11.4kg/25lbs. When placed in a sterilization container with gasketed lid the total sterilization package should not exceed 16kg/35lbs. • Any device capable of disassembly must be disassembled prior to placement in the case. • All devices must be arranged to ensure steam penetration to all instrument surfaces. Instruments should not be stacked or placed in close contact. • The user must ensure that the instrument case is not tipped or the contents shifted once the devices are arranged in the case. Silicon mats may be used to keep devices in place. • Only devices manufactured and/or distributed by Zimmer CAS or Zimmer should be included in Zimmer CAS instrument trays. Zimmer CAS validated reprocessing instructions are not applicable to Zimmer CAS trays that include devices that are not manufactured and/or distributed by Zimmer CAS or Zimmer.
Page 2 of 2