2 Pages
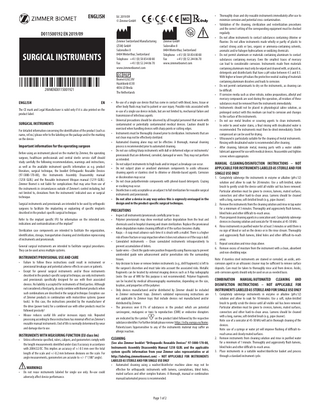
Preview
Page 1
ENGLISH
Ed. 2019/09 © Zimmer GmbH
&
& 2797
•
D011500192 EN 2019/09 Zimmer Switzerland Manufacturing (ZSM) GmbH Sulzerallee 8 8404 Winterthur, Switzerland Telephone +41/ (0) 58 854 80 00 Fax +41/ (0) 52 244 86 70 www.zimmerbiomet.com
SURGICAL INSTRUMENTS
ENGLISH
EN
•
The CE mark and Legal Manufacturer is valid only if it is also printed on the product label.
SURGICAL INSTRUMENTS For detailed information concerning the identification of the product (such as name, ref.no.) please refer to the labeling on the package and/or the marking on the device.
Important information for the operating surgeon Before using an instrument placed on the market by Zimmer, the operating surgeon, healthcare professionals and central sterile service staff should study carefully the following recommendations, warnings and instructions, as well as the available instrument specific information as e.g. product literature, surgical technique, the booklet Orthopaedic Reusable Devices (97‑5000‑170‑00), the Instruments Assembly Disassembly manual (1258 GLBL) and the Reusable Instrument lifespan manual (1219 GLBL). Zimmer Biomet is not liable for complications that may arise from use of the instruments in circumstances outside of Zimmer’s control including, but not limited to, deviations from the instruments’ indicated uses or surgical technique. Surgical instruments and provisionals are intended to be used by orthopedic surgeons to facilitate the implanting or explanting of specific implants described in the product-specific surgical technique. Refer to the implant specific IFU for information on the intended use, indications and contraindications of the implant” Sterilization case components are intended to facilitate the organization, identification, storage, transportation cleaning and sterilization reprocessing of instruments and provisionals. General surgical instruments are intended to facilitate surgical procedures. They can be used across multiple systems.
• • • • • • • • •
• • • • •
•
•
Failure to follow these instructions could result in instrument or provisional breakage and potential adverse effects on users or patients. Except for general surgical instruments and/or those instruments described in the product-specific surgical technique, use only instruments and provisionals specifically designed for use with their associated devices. No liability is accepted for instruments of third parties. Although not considered a third party, do only combine with Biomet products when such combinations are described in the surgical technique. Exception: use of Zimmer products in combination with motor/drive systems (power tools). In this case, the instructions provided by the manufacturer of the drive (power tools) for a combined use with other products must be followed precisely! Misuse reduces useful life and/or increases injury risk. Repeated processing according to these instructions has minimal effect on Zimmer’s reusable manual instruments. End of life is normally determined by wear and damage due to use.
INSTRUMENTS WITH MEASURING FUNCTION (EU class Im) •
Unless otherwise specified, rulers, calipers, and goniometers comply with the length measurements identified under class II accuracy in accordance with 2004/22/EC. This implies an accuracy of +/-0.5 mm over the total length of the scale and +/-0.2 mm between divisions on the scale. For angle measurements, goniometers are accurate to +/- 1° (180° angle).
•
Do not reuse instruments labeled for single use only. Re-use could adversely affect device performance.
WARNINGS
•
•
•
•
•
• •
Re-use of a single use device that has come in contact with blood, bone, tissue or other body fluids may lead to patient or user injury. Possible risks associated with re-use of a single use device include, but are not limited to, mechanical failure and transmission of infectious agents. Universal precautions should be observed by all hospital personnel that work with contaminated or potentially contaminated medical devices. Caution should be exercised when handling devices with sharp points or cutting edges. Instruments must be thoroughly cleaned prior to sterilization. Instruments that are not clean may not be effectively sterilized. Automated cleaning alone may not be effective. A thorough, manual cleaning process is recommended prior to automated cleaning. Do not use cutting/sharp instruments with dull or deformed edges or instruments/ provisionals that are deformed, corroded, damaged or worn. They may not perform as intended. Do not subject instruments to high loads and/or impact as breakage can occur. Do not subject plain or anodized aluminum components to acidic ultrasonic cleaning agents or stainless steel to chlorine or chloride-based agents. Corrosion or discoloration may occur. Do not clean polyetherimide components with phenol-based detergents. Crazing or cracking may occur. Disinfection is only acceptable as an adjunct to full sterilization for reusable surgical instruments and provisionals. Do not alter a device in any way unless this is expressly envisaged in the design and in the product-specific surgical technique.
PRECAUTIONS
INSTRUMENT/PROVISIONAL USE AND CARE •
Zimmer GmbH Sulzerallee 8 8404 Winterthur, Switzerland Telephone +41/ (0) 58 854 80 00 Fax +41/ (0) 52 244 86 70 www.zimmerbiomet.com
Biomet GSCC BV Hazeldonk 6530 4836 LD Breda The Netherlands
2WMEND0115001921
•
Inspect all instruments/provisionals carefully prior to use. Polymer provisionals may show eventual surface degradation from the heat and chemicals used in hospital cleaning and steam sterilization. Replace the provisional when degradation makes cleaning difficult or if the surface becomes chalky. Rasps – A rasp must advance each time it is struck with a mallet. There is a higher risk of bone fracture or rasp impaction when it does not advance or if the rasp is dull. Cannulated instruments – Clean cannulated instruments intraoperatively to prevent accumulation of debris. Guide wires – Check the guide wire position frequently using fluoroscopy to prevent unintended guide wire advancement and/or penetration into the surrounding tissues. Any decision to leave or remove broken instruments (e.g., drill fragments) is left to the surgeon’s discretion and must take into account the associated risks. Metallic fragments can be located by external imaging devices such as X‑Ray radiography (note: the use of MRI for this purpose is not recommended). Polymer fragments can be located by medical ultrasonography examination, depending on the size, location, and properties of the polymer. Only devices manufactured and/or distributed by Zimmer should be included in Zimmer instrument trays. Zimmer’s validated reprocessing instructions are not applicable to Zimmer trays that include devices not manufactured and/or distributed by Zimmer. The presences over 0.1% of substances in the product which are potential carcinogenic, mutagenic or toxic to reproduction (CMR) or endocrine disrupters are indicated by the symbol on the product label followed by the respective substance identifier. For further details please review: https://echa.europa.eu/home. Patients/users hypersensitive to any of the instruments material may suffer an allergic reaction.
CLEANING
(See also Zimmer booklet “Orthopaedic Reusable Devices” 97‑5000‑170‑00, Instruments Assembly Disassembly Manual 1258 GLBL and the applicable system specific information from your Zimmer sales representative or at http://labeling.zimmerbiomet.com) – NOT APPLICABLE FOR INSTRUMENTS LABELED AS STERILE AND FOR SINGLE USE ONLY • Automated cleaning using a washer/disinfector machine alone may not be effective for orthopaedic instruments with lumens, cannulations, blind holes, mated surfaces and other complex features. A thorough, manual or combination manual/automated process is recommended.
Page 1 of 2
• •
• •
Thoroughly clean and dry reusable instruments immediately after use to minimize corrosion and potential cross-contamination. Validation of the cleaning, sterilization and resterilization procedures and the correct setting of the corresponding equipment must be checked regularly. Do not allow instruments to contact substances containing chlorine or fluorine. Do not allow instruments made wholly or partly of plastic to contact strong acids or lyes, organic or ammonia-containing solvents, aromatic and/or halogen hydrocarbons or oxidizing chemicals. Do not permit aluminum or materials containing aluminum to contact substances containing mercury. Even the smallest traces of mercury can lead to considerable corrosion. Instruments made from materials containing aluminum must only be wiped and cleaned with, or placed in, detergents and disinfectants that have a pH value between 4.5 and 8.5. With higher or lower pH values the protective neutral coating of materials containing aluminum dissolves and leads to corrosion. Do not permit contaminants to dry on the instruments, as cleaning can be difficult. If corrosive media such as silver nitrate, iodine preparations, albotyl and mercury compounds are used during the operation, all residues of these substances must be removed from the instruments immediately. Instruments should not be placed in physiological saline solution, as prolonged contact with this medium can lead to corrosion and changes to the surface of the instruments. Do not use metal brushes or scouring agents to clean instruments. In order to avoid water stains, a final rinsing with desalinated water is recommended. The instruments must then be dried immediately. Sterile compressed air can be used for drying. Ultrasound is particularly suitable for the cleaning of metal instruments. Rinsing with desalinated water is recommended after cleaning. After cleaning, lubricate metal, moving parts with a water soluble lubricant approved for use with medical devices. Reassemble and tighten screws where appropriate.
MANUAL CLEANING/DISINFECTION INSTRUCTIONS – NOT APPLICABLE FOR INSTRUMENTS LABELED AS STERILE AND FOR SINGLE USE ONLY
1. Completely submerge the instruments in enzyme or alkaline (pH≤12) solution and allow to soak for 20 minutes. Use a soft-bristled, nylon brush to gently scrub the device until all visible soil has been removed. Particular attention must be given to crevices, lumens, mated surfaces, connectors and other hard-to-clean areas. Lumens should be cleaned with a long, narrow, soft-bristled brush (e.g., pipe cleaner). 2. Remove the instruments from the cleaning solution and rinse in tap water for a minimum of 3 minutes. Thoroughly and aggressively flush lumens, blind holes and other difficult-to-reach areas. 3. Place prepared cleaning agents in a sonication unit. Completely submerge devices in cleaning solution and sonicate for 10 minutes at 45‑50 kHz. 4. Rinse instruments in purified water for at least 3 minutes or until there is no sign of blood or soil on the device or in the rinse stream. Thoroughly and aggressively flush lumens, blind holes and other difficult-to-reach areas. 5. Repeat sonication and rinse steps above. 6. Remove excess of moisture from the instrument with a clean, absorbent and non-shedding wipe. Note: if stainless steel instruments are stained or corroded, an acidic, anticorrosion agent in an ultrasonic cleaner may be sufficient to remove surface deposits. Care must be taken to thoroughly rinse acid from devices. Acidic, anti-corrosion agents should only be used on an as-needed basis.
COMBINATION MANUAL/AUTOMATED CLEANING AND DISINFECTION INSTRUCTIONS – NOT APPLICABLE FOR INSTRUMENTS LABELED AS STERILE AND FOR SINGLE USE ONLY
1. Completely submerge instruments in enzyme or alkaline (pH≤12) solution and allow to soak for 10 minutes. Use a soft, nylon-bristled brush to gently scrub the device until all visible soil has been removed. Particular attention must be given to crevices, lumens, mated surfaces, connectors and other hard-to-clean areas. Lumens should be cleaned with a long, narrow, soft-bristled brush (e.g., pipe cleaner). Note: use of a sonicator at 45‑50 kHz will aid in thorough cleaning of the devices. Note: use of a syringe or water jet will improve flushing of difficult-toreach areas and closely mated surfaces. 2. Remove instruments from cleaning solution and rinse in purified water for a minimum of 1 minute. Thoroughly and aggressively flush lumens, blind holes and other difficult-to-reach areas. 3. Place instruments in a suitable washer/disinfector basket and process through a standard instrument cycle.
4. The following minimum parameters are essential for thorough cleaning and disinfection: Typical USA Automated Washer/Disinfector Cycle for Surgical Instruments Step
Description
1.
2 minutes prewash with cold tap water
2.
20 seconds enzyme spray with hot tap water
3.
1 minute enzyme soak
4.
15 seconds cold tap water rinse (X2)
5.
2 minutes detergent wash with hot tap water (64‑66°C / 146‑150°F)
6.
15 seconds hot tap water rinse
7.
2 minutes thermal rinse (80‑93°C / 176‑200°F)
8.
10 seconds purified water rinse with optional lubricant (64‑66°C / 146‑150°F)
9.
7‑30 minutes hot air dry (116°C / 240°F)
Typical European Automated Washer/Disinfector Cycle for Surgical Instruments Step
Description
1.
5 min pre-rinse with cold tap water
2.
10 min wash with 0.7% cleaning agent at 55°C
3.
2 min rinse with neutralizer
4.
1 min rinse with cold tap water
5.
Disinfection at 93°C with hot purified water until A0 3000 is reached (approx.10 min)
6.
40 min hot air drying at 110°C
Note: The washer/disinfector manufacturer’s instructions should be strictly adhered to. Use only cleaning agents recommended for the specific type of automated washer/disinfector. A washer/disinfector with approved efficacy (e.g., CE mark, FDA approval, and validation according to ISO 15883) should be used.
STERILE PACKAGING – ONLY APPLICABLE FOR INSTRUMENTS DELIVERED IN NON STERILE CONFIGURATION Packaging individual instruments • •
•
Devices provided non-sterile are indicated by the or symbol on the label. Single devices should be packaged in a FDA-cleared* medical grade sterilization pouch or wrap which conforms to the recommended specifications for steam sterilization provided in the table below. Ensure the package is large enough to contain the instrument without stressing the seals or tearing the pouch or wrap (*for USA only). Sterilization wraps must be free of detergent residues. Reusable wraps are not recommended.
Packaging instruments within defined, preconfigured Zimmer rigid trays and cases with lids Safety Precaution: The total weight of a wrapped instrument tray or case should not exceed 11.4 kg or 25 lbs. When placed in a sterilization container with a gasketed lid the total package should not exceed 11.4 kg or 25 lbs. • Trays and cases with lids may be wrapped in a standard, medical grade, steam sterilization wrap using the AAMI double wrap method or equivalent. • Trays and cases with lids may also be placed in an approved sterilization container with gasketed lid for sterilization. Packaging instruments in universal instrument trays and cases without defined, preconfigured layouts or containing undefined universal spaces or compartments should only be used under the following conditions: • All devices must be arranged to ensure steam penetration to all instrument surfaces. Instruments must not be stacked or placed in close contact. • The user must ensure that the instrument case is not tipped or the contents shifted once the devices are arranged. Silicon mats may be used to keep devices in place. • Only devices manufactured and/or distributed by Zimmer should be included in Zimmer instrument trays.
STERILE SINGLE USE INSTRUMENTS
Gamma irradiation is indicated by the symbol on the labeling, while Ethylene Oxide sterilization is indicated by the symbol. These devices remain sterile as long as the package integrity has not been violated. Inspect each package prior to use and do not use the component if any seal or cavity is damaged or breached, or if the expiration date has
been exceeded. Once opened, the component must be used immediately, discarded, or resterilized (if allowed). Sterile, packaged instruments should be stored in a designated, limited access area that is well ventilated, and provides protection from dust, moisture, insects, vermin, temperature and humidity extremes. Sterile, packaged instruments should be examined carefully prior to opening to ensure that there has not been a loss of package integrity.
SYMBOLS on the device: Some instruments are marked with the following symbols to aid in determining cleaning instructions. Refer to the Zimmer booklet 97‑5000‑170‑00, “Orthopaedic Reusable Devices”, (from your Zimmer sales representative or at http://labeling.zimmerbiomet.com).
a
STERILIZATION INSTRUCTIONS • • •
• •
•
• • • • •
These sterilization instructions are consistent with ANSI/AAMI/ISO standards and guidelines. They should be used for items supplied non-sterile, for reprocessing reusable devices, or sterile items that were opened but unused. Do not reuse instruments or devices labeled for single use only. In the event of inadvertent loss of sterility while preparing for surgery, sterile, single use metal instruments may be sterilized only once for immediate use. This is subject to the exceptions listed below. -- See Zimmer booklet 97‑5000‑170‑00, “Orthopaedic Reusable Devices” (from your Zimmer sales representative or at http://labeling.zimmerbiomet.com) for detailed guidelines related to proper care, maintenance, reprocessing, handling of surgical instruments, and an explanation of associated symbols. Where possible, reusable instruments and provisionals should be disassembled for sterilization. DO NOT RESTERILIZE: -- Single use only components that have been contaminated with body fluids or debris or previously implanted. -- Components with a packaging expiration date that has been exceeded. -- Single use only retractor light pipes. -- Single use instruments containing any non-metallic materials. Do not use the original plastic cavities or lids for resterilization. Single devices should be packaged in a FDA-cleared* medical grade sterilization pouch or wrap that conforms to the recommended specifications for steam sterilization provided in the table below. Ensure that the pouch or wrap is large enough to contain the devices without stressing the seals or tearing (*for USA only). Do not stack heavy items on top of any sterilization cases made from plastic. The resulting deformation can cause cracking of the plastic material. Items made from titanium and titanium alloys can form oxide layers from steam boiler treatment, chemicals or detergent residues. While these oxides are biocompatible, they can obliterate etchings and stampings. During initial sterilization runs, polyacetal and polyacetal copolymer provisionals may have a formaldehyde odor. This will disappear after a few sterilization cycles. Polysulfone provisionals may show eventual crazing and/or cracking due to steam boiler, chemicals and lubricants. Sterilized instruments must be completely dry prior to storage.
Recommended Sterilization/Resterilization Specifications
Follow the sterilizer manufacturer’s instructions for loading patterns and selection of sterilization parameters. Drying times vary according to load size and should be increased for larger loads. Steam Sterilization Type
Temperature
Exposure Time
UK Pre-vacuum/Pulsating Vacuum1
134°C (273°F)
3 minutes
Pre-vacuum/Pulsating Vacuum
132°C (270°F)
4 minutes
Pre-vacuum/Pulsating Vacuum1,2
134°C (273°F)
18 minutes
Minimum Dry Time3
Minimum Cool Time4
Metal instruments (excluding aluminum and titanium) without bores, non- metal/polymer handles, and plastic materials. Metal instruments (excluding aluminum and titanium) with
bores, without non-metal/polymer handles and a+ cannulated plastic materials.
b
Instruments made of plastic or metal instruments paired with plastic components.
with cannulated bores, made of plastic or metal b+ Instruments instruments paired with plastic components.
c
Instruments with special cleaning instructions and assembly/disassembly aids made of titanium or aluminum alloys.
STORAGE AND HANDLING •
•
Instruments provided sterile must be stored unopened in their original packaging. Before sterile instruments are removed from their packaging, the protective packaging must be examined for possible damage to the sterile barrier. If an expiration date for sterility of the product is indicated, this must be observed. If the sterile barrier system is damaged or the sterility expiration date has been reached, the instruments must not be used. Non-sterile provided instruments are to be stored in the appropriate packaging that protects the instruments from damage or in an appropriate instrument tray. Instruments must be examined for possible damage before use. Protective caps or other protective elements must not be removed until immediately before use.
DISPOSAL INFORMATION:
After use, the instrument is a potential biohazard, since it may be contaminated with blood or other body fluids, bone or other tissue. Handle and dispose this product in accordance with accepted medical practice and with applicable local, state and national laws and regulations. Any sharp objects should be disposed immediately after use into a sharps container conforming to EN ISO 23907‑1 or equivalent following the requirements in 2010/32/EU directive or equivalent national laws. The sharp must not be bent, broken or resheathed prior to disposal.
REPORTING PROBLEMS:
The user and/or patient should report any suspected serious incident related to the device by informing the manufacturer and the competent authority of the member state in which the serious incident has occurred. All trademarks and logos referred to within this package insert are the property of Zimmer, Inc. or its affiliates.
30 minutes 30 minutes
This cycle is not for use in the USA. This cycle is not to be used for the inactivation of prions. Drying times vary according to load size and should be increased for larger loads. 4 Cooling times vary according to the type of sterilizer used, device design, temperature and humidity of ambient environment, and type of packaging used. Cooling process should comply with ANSI/AAMI ST79.
Symbol for «Contents packed without sterilization» Medical Device
1 2
Do not use if package is damaged.
3
Please contact Zimmer if you have additional questions. In the USA, call 1‑800‑348‑2759. Outside the USA, call the local international access code +1‑574‑267‑6131.
INSPECTION AND FUNCTIONAL TESTING
(See also Zimmer lifespan manual 1219GLBL, Instruments Assembly Disassembly Manual 1258 GLBL and the system specific Information, from your Zimmer sales representative or at http://labeling.zimmerbiomet.com) • Carefully inspect each device to ensure that all visible blood and debris has been removed. • Check the action of moving parts to ensure smooth operation through the intended range of motion. • Check instruments with long, slender features (particularly rotating instruments) for distortion. • Where instruments form part of an assembly, check that the devices assemble readily with mating components. • If damage or wear that may compromise the function of the instrument is noted, do not use the device and contact your Zimmer representative for replacement.
Page 2 of 2
Contains hazardous substances.
Do not impact
Do not implant
Right
Left