User Manual
80 Pages
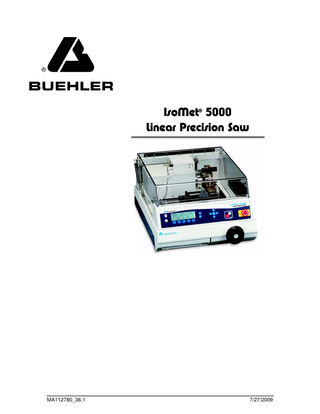
Preview
Page 1
IsoMet® 5000 Linear Precision Saw
MA112780_36.1
7/27/2009
Buehler Worldwide Mission Statement We are Buehler, the science behind materials preparation and analysis and the premier company in our field, since 1936. Our global mission is to deliver outstanding value and delight our customers by providing innovative, quality, on-time products and services. To fulfill our mission, we will continue to: •
Listen to and understand our customers to exceed their expectations.
•
Apply engineering and technical support to provide innovative solutions to our customers.
•
Achieve profitable growth.
•
Foster an environment of creativity, respect, teamwork, open communication and ethical behavior.
•
Provide the training and tools which allow all of us to achieve our mission.
•
Continually improve our performance in all aspects of the business.
About Buehler For over 70 years, Buehler has been a leading manufacturer of scientific instruments and supplies for use in materials analysis. Buehler products are used throughout the world in manufacturing facilities, quality laboratories and universities to analyze all types materials, including: •
Ferrous and Non-ferrous metals
•
Thermal spray coatings
•
Printed Circuit Boards
•
Fasteners
•
Ceramics
•
Composites
•
Semiconductors
•
Rocks
•
Glasses
•
Plastics
Companies use Buehler products to improve the material within their product, monitor production or incoming purchased material, do failure analysis and perform basic materials research. Buehler products fall into three categories: •
Sample preparation equipment for cutting, grinding and polishing specimen material (usually cross sectioning) prior to microstructural inspection.
•
Metallographic consumables for the sample preparation equipment including; cutoff wheels, saw blades, mounting compounds, grinding papers, polishing cloths and polishing suspensions.
•
Inspection and testing equipment including microscopes, image analyzers, video equipment and hardness testers.
ii MA112780_36.1
7/27/2009
Declaration of Conformity
Manufacturer:
BUEHLER, Ltd.
Of:
41 Waukegan Road Lake Bluff, Illinois60044
Declares the following product:
IsoMet® 5000 Linear Precision Saw
To be in accordance with EC Directive(s); Safety of Machinery:
EMC Directive:
98/37/EC according to the following standards:
89/336/EEC amended by 92/31/EEC and 93/68/EEC according to the following standards:
EN ISO 12100 PART 1 EN ISO 12100 PART 2 EN 60204 PART 1
EN 550011 EN 61000-3 PART 2 AND 3 EN 61000-4 PART 2 TO 6 AND 11
Position:
Director of Engineering
Name:
Boyd Schindler
Signature:
Date:
1/8/2007
THIS MANUAL IS A CUSTOM GENERATED DOCUMENT. IT INCLUDES ALL REVISIONS RELATIVE TO THIS SPECIFIC BUEHLER ITEM AS OF THE DATE SHOWN BELOW. The items covered in this communication including all attachments may be subject to the export laws of the United States of America, including without limitation the Export Administration Regulations and the Office of Foreign Asset Control Regulations. The export, re-export or diversion of these items in contravention of these or other applicable regulations is strictly prohibited. This information contained in this communication is intended only for the use of the individual or entity to which it is addressed and may contain information that is privileged, confidential and exempt from disclosure under applicable law.
iii MA112780_36.1
7/27/2009
This page was intentionally left blank.
iv MA112780_36.1
7/27/2009
Table of Contents IsoMet 5000 Linear Precision Saw ...1 Warranty ...1 Safety Information...1 Machine Use and Care ...2 Safety Terms ...2 Unpacking ...3 Installation...4 Electrical Installation ...4 Blade Installation ...5 Installing a Blade ...5 Cooling and Lubrication ...6 Vises ...6 External Recirculating System...7 IsoMet 5000 Controls and Functions ...8 Front Panel Controls ...8 Directional Buttons ...10 IsoMet 5000 Display Screens and Commands...11 Parameter Fields ...11 L1 Display Screen ...12 L1 Display Screen Commands ...12 Pause CUTTING CYCLE ...12 L2 Display Screen ...13 L2 Display Screen Commands ...13 L3 Display Screen ...14 L3 Display Screen Commands ...14 L4 Display Screen ...15 L4 Display Screen Commands ...15 Specimen Positioning ...16 Hard Home ...16 Specimen Loading ...16 Positioning a Specimen with an Unknown Thickness (without the Specimen Positioning System Installed)...17 Positioning a Specimen with a Known Thickness (without the Specimen Positioning System Installed) ...19 Positioning a Specimen with the Specimen Positioning System Installed...20 Operation ...21 Cutting a Specimen and Serial Sectioning...21 Single Cut without the Specimen Positioning System ...21 Single Cut with the Specimen Positioning System with the DATUM OFF Function ...22 Single Cut with the Specimen Positioning System with the DATUM ON Function...23 Single Cut with the Specimen Positioning System with the DATUM ON Function...23 Multiple Cuts Using the Specimen Positioning System with the DATUM OFF Function ...24 Multiple Cuts Using the Specimen Positioning System with the DATUM ON Function ...25 Manual Cutting ...26 SMART CUT: Checking and Adjusting the Feed Rate ...27
v MA112780_36.1
7/27/2009
Table of Contents Blade Dressing ...27 Dressing the Blade ...28 Automatic Blade Dressing, Rotating Chuck, and Specimen Positioning System ...29 Removing the Specimen Position System (Catalog Number 11-2699) ...29 Installing the Specimen Position System ...30 Removing the Rotating Chuck (Catalog Number 11-2695)...30 Installing the Rotating Chuck ...30 Removing the Automatic Blade Dressing System (Catalog Number 11-2696)...31 Installing the Automatic Blade Dressing System ...31 Loading and Saving Methods ...32 To Load a Method ...32 To Save a Method ...33 Warning Messages ...34 Maintenance ...35 Internal Coolant/Lubricant Recirculating System ...35 Cutting Fluid Recommendations ...35 Draining the Coolant ...35 Automatic Blade Dressing ...36 Cleaning the Automatic Blade Dressing shaft ...36 Checking the Blade Motor Total Hours ...36 Trouble Shooting Chart ...37 Accessories ...67 Vises...67 Additional Accessories ...68 Blades ...69 IsoMet 5000 Precision Saw Application Guide...70
vi MA112780_36.1
7/27/2009
IsoMet 5000 Linear Precision Saw The IsoMet 5000 is an easy to use automatic linear saw that includes the SMARTCUT system to automatically adjust the feed rate to provide consistent, quality cuts and to prevent specimen and machine damage. A 2μm Specimen Positioning System allows for precise applications and enables the cutting of delicate specimens without deformation. The IsoMet 5000 also provides automatic serial sectioning for multiple cuts to a desired thickness and has method programmability. 35 preset Buehler methods provide sectioning parameters for a variety of materials including ferrous metals, non-ferrous metals, ceramics, and geological specimens. 20 customized methods can be programmed for various cutting parameters to meet a variety of specimen sectioning requirements. Three IsoMet 5000 models are available: •
11-2780 IsoMet 5000 Precision Saw with accessories.
•
11-2781 IsoMet 5000 Precision Saw without accessories.
•
11-2775 IsoMet 5000 Precision Saw with accessories and external recirculating system.
Warranty This unit is guaranteed against defective material and workmanship for a period of 24 months or 2000 hours from the date of receipt by the customer. The warranty is void if inspection shows evidence of abuse, misuse, unsafe use, or unauthorized repair. This warranty covers all Buehler costs associated with the replacement of defective materials (e.g., parts and labor). If for any reason this unit must be returned to Buehler Ltd. for warranty service, please apply for prior authorization with shipping instructions. Please include the following information: •
Customer Purchase Order Number
•
Buehler Invoice Number and Date
•
Serial Number
•
Reason for return
Safety Information The IsoMet 5000 Linear Precision Saw is designed to section metallurgical and petrographic materials with recommended cutting wheels. For safe installation and operation of this equipment, carefully read and understand the contents of this manual. Improper operation, handling, or maintenance can result in severe personal injury and equipment damage. The IsoMet 5000 Linear Precision Saw is designed for use in dry, indoor laboratory and workshop environments away from strong electromagnetic fields and with normal temperature ranges (41° F to 104° F / 5° C to 40° C) and non-condensing humidity ranges (30-90%).
1 MA112780_36.1
7/27/2009
Machine Use and Care All operators should be trained in the use of the IsoMet 5000. If training is needed contact Buehler at 800.BUEHLER (800.283.4537) or your local Buehler Sales Representative. Always use safety glasses. Flying debris and liquids can cause severe eye injury. Dress properly. Protective equipment should be worn to handle specimens, which may be sharp or hot. Do not operate machine in explosive atmospheres, such as in the presence of flammable liquids, gases, or dust. Sparks may ignite the dust or fumes. Flammable material must not be used with the IsoMet 5000 Linear Precision Saw. Maintain the IsoMet 5000 Linear Precision Saw with care. Properly maintained machines are less likely to bind and are easier to control. Any alteration or modification is a misuse and may result in a dangerous situation. Maintain machine guards and interlocks. Do not attempt to enter the cutting bay when the IsoMet 5000 Linear Precision Saw is in use. Only qualified repair personnel must perform machine service. Service or maintenance performed by unqualified personnel could result in a risk of injury. Replace damaged or defective parts immediately and use only identical replacement parts. Use of unauthorized parts or failure to follow maintenance instructions may create a risk of electrical shock or injury. Check for misalignment or binding of moving parts, breakage of parts, and any other condition that may affect the machine operation. If damaged, have the machine serviced before using. Poorly maintained machines cause many accidents. Machine coolant can present a biological hazard if not maintained correctly. Change the coolant regularly in accordance with local regulations and safety practices. Use of extension cords is not recommended for Buehler machines and equipment.
Safety Terms indicates a hazardous situation which, if not ! DANGER DANGER avoided, will result in death or serious injury. indicates a hazardous situation which, if not avoided, ! WARNING WARNING could result in death or serious injury
! CAUTION if not avoided, may result in minor or moderate injury.
CAUTION indicates a potentially hazardous situation which,
NOTICE
NOTICE indicates practices not related to personal injury.
2 MA112780_36.1
7/27/2009
Unpacking The IsoMet 5000 Linear Precision Saw is shipped fully assembled and has been carefully packaged to protect it during transit from the factory to your location. Carefully unpack and check contents. If any components are missing or damaged, save the packing list and materials and advise the carrier and Buehler, Ltd. of the discrepancy. IsoMet 5000 Linear Precision Saw with accessories (Catalog Number 11-2780) is shipped with: •
Automatic Dressing System (11-2696)
•
Dressing Stick (11-1190)
•
IsoCut® Plus Cutting Fluid (11-2293-016)
•
IsoCut® 7-inch Wafering Blade (11-4267)
•
Set of 4-inch Stainless Steel Flanges (11-2689)
•
2µm Specimen Positioning System (11-2750)
•
3 Specimen Chucks: 11-2684 - 1 ¼-inch Round Specimen Chuck 11-2683 - Single Saddle Chuck 11-2686 - Irregular Specimen Chuck
! WARNING Equipment Damage. The IsoMet 5000 Linear Precision Saw is heavy. Follow local safety practices to lift the IsoMet 5000 Linear Precision Saw unit from the shipping carton. Improper lifting can result in machine damage. Personal Injury. Improper lifting of the IsoMet 5000 Linear Precision Saw can result in personal injury. The IsoMet 5000 Linear Precision Saw is bolted to a wooden base for protection during shipping. Open areas are provided at the corners of the base for ease of lifting. Lift the IsoMet 5000 Linear Precision Saw out of the carton and position it on a table so it overhangs the edge. Remove all bolts securing the IsoMet 5000 Linear Precision Saw to the wood base.
3 MA112780_36.1
7/27/2009
Installation
! WARNING Equipment Damage. The IsoMet 5000 Linear Precision Saw is heavy. Follow local safety practices to lift the IsoMet 5000 Linear Precision Saw unit from the shipping carton. Improper lifting can result in machine damage. Select a location for your IsoMet 5000 Linear Precision Saw that provides an adequate working space, a power source, water connections, and a drain. Allow 6 inches (150 mm) of space at the back of the IsoMet 5000 Linear Precision Saw for raising the hood.
Electrical Installation
Electrical Shock Hazard. Only a qualified electrical technician should perform electrical installation and maintenance. Electrical Shock Hazard. Do not change the power plug in any way. Buehler machines are equipped with a polarized plug (one blade is wider than the other) and a ground pin. Polarized plugs reduce the risk of electrical shock. This plug will fit in a polarized outlet only one way. The Specification Plate is located on the back of the IsoMet 5000 Linear Precision Saw. Check that the Specification Plate values for voltage, current, and power consumption are compatible with the intended electrical supply before installation. The IsoMet 5000 Linear Precision Saw can be plugged into an existing outlet rated for the voltage and frequency listed on the Specification Plate. •
Disconnect the power supply before making any electrical adjustments.
•
Capacitors inside the machine may retain a charge even if the machine is disconnected from the power supply.
•
Installation of the IsoMet 5000 Linear Precision Saw must comply with local electrical standards or codes of practice. IsoMet 5000
Voltage / Frequency
11-2780
85-264 Volt / 50-60 Hz
11-2781
85-264 Volt / 50-60 Hz
11-2775
85-264 Volt / 50-60 Hz
Table 1 IsoMet 5000 Electrical Data
4 MA112780_36.1
7/27/2009
Blade Installation Flanges support the wafering and abrasive blades. Failure to provide adequate flange support may result in curved cuts and damaged blades. When cutting always select the maximum flange diameter in proportion with the size of the specimen. (For more details see Accessories and Supplies.) Installing a Blade 1. Remove the thumbscrew and end cap bushing from drive shaft (see Figure 1). 2. Install the outer flange on the end cap bushing. 3. Install the blade against the outer flange. 4. Slip on the inner flange on the end cap bushing. 5. Tighten thumbscrew to complete the installation.
NOTICE To prevent misalignment and damage to the blade, clean the end cap bushing, screws, and flanges in a mild detergent solution to remove particles from prior cuttings before installing a wafering or abrasive blade.
Outer Flange
Inner Flange End Bolt
End Cap Bushing
Figure 1 Blade Installation Diagram
5 MA112780_36.1
7/27/2009
Cooling and Lubrication The IsoMet® 5000 has an internal pump and adjustable nozzle for lubrication and cooling. The coolant tank is covered to prevent spills and has internal baffles. Baffles provide surface area for swarf control (debris left over from a blade cut). The nozzle can be adjusted with the hood open and the pump on.
! CAUTION Equipment Damage. Do not allow the tank to become less than ½-inch below full. This will cause the water pressure to surge. Do not run the pump dry for more than 30 seconds.
NOTICE Only the pump will operate with the hood open. The pump can be used for coolant adjustment, machine cleaning, and to empty the tank. •
The internal tank holds three liters and can be filled by pouring cutting fluid into the saw bed. Fill the coolant tank with cutting fluid (IsoCut® Plus). Using only water is not recommended. Using only water will cause damage to the internal pump and will not be covered under warranty. The External Recirculating System (part number 11-2710) ) is recommended for procedures that require using just water.
•
•
Do not over fill the coolant tank. The true level of the liquid is indicated on the front of the tank and not at the drain inside the cutting chamber.
•
During high frequencies of use or when using abrasive cut-off wheels with the IsoMet® 5000 Linear Precision Saw, the coolant tank should be cleaned regularly. The drain screen should be cleaned between each cut to prevent blockage. (For high frequencies of use, it is highly recommended to use the External Recirculating System, part number 11-2710).
If the IsoMet® has not been operation for a long period of time or the protective residue on the machinery appears gummy, run the coolant first to wet the surfaces before moving the turret/hand-crank. This will extend the life of the rail seals and linear bearings.
Vises The general use vise (Catalog Number 112691) is constructed of hardened and ground tool steel. This gives the best performance and accuracy, and will hold specimens up to 2 inches (50 mm) in size.
NOTICE The vise must be oiled after each use if only water is used as a cutting fluid. Using only water is not recommended.
6 MA112780_36.1
7/27/2009
External Recirculating System
! WARNING Personal Injury. Disconnect the power supply before performing any maintenance or adjustments. 1. Find a suitable location for the External Recirculating System. 2. Set the tank on a four-wheeled recirculating cart (P/N 16-1497). 3. Slide the 1-inch drain hose over the drain outlet pipe and secure the drain hose with the supplied hose clamp (see Figure 2) 4. Connect the water supply hose to the supply fitting on the recirculating tank (see Figure 3).
Figure 2 1-inch drain outlet pipe
Figure 3 Supply fitting on the recirculating tank
5. Connect the power cord from the saw to the 12-volt power plugs from the saw to the Connect the power cord from the saw to the 12-volt power plugs from the saw to the banana plugs on the recirculating tank (see Figure 3). a. Plug the BLACK banana plug into the BLACK connector. b. Plug the RED banana plug into the RED connector.
Fill to this level.
6. Fill the recirculating tank with seven (7) gallons of mixed coolant or until the mixed coolant reaches the top of the first or third baffle (see Figure 4). 7. Insert the drain hose into the large hole on the recirculating tank. The drain hose can be cut to length to facilitated easier installation. 8. The front control panel command buttons operate the External Recirculating Tank.
Figure 4 External Recirculating Tank Baffles
7 MA112780_36.1
7/27/2009
IsoMet 5000 Controls and Functions Before operating the IsoMet 5000 lightly oil all exposed metal parts. During operation the coolant will maintain a protective film of oil on all exposed metal. When the IsoMet 5000 is not in use raise the hood. This will minimize possible corrosion. A glass-reinforced, splash-proof plastic hood encloses the entire cutting area to prevent loss of coolant and decrease noise. When raised, the counter-balanced hood will remain in the open position, activating a safety-lock switch disabling the controls for the cutting motor. 1. Activate power to the IsoMet 5000. Flip the power switch on the back of the machine to the ON position. 2. On the front control panel press the ON button. •
The front panel LCD will light up and scroll through the display screen.
•
Raise the hood to allow access to the cutting bay.
Front Panel Controls
The front panel consists of eleven (11) dedicated buttons, five (5) software/multi-function softkey buttons, an Emergency Stop button, and a large Liquid Crystal Display (LCD) with back lighting. All buttons have tactile feedback.
ON
Power ON The Power ON button will activate the IsoMet system. When first turned ON, the LCD screen will scroll through the Buehler name, logo, type of machine, and latest firmware revision. After 10 seconds the screen will change to display the BLADE SPEED, FEED RATE, and DISTANCE REMAINING parameter information as well as the softkey button commands for the L1 screen.
OFF
Power OFF The Power OFF button will deactivate the IsoMet® system. The Power OFF button will store all previous set parameters before powering off.
8 MA112780_36.1
7/27/2009
Scroll The SCROLL button scrolls through the different parameter fields highlighting each one as it is selected. The parameter fields will change depending on how many times the SCROLL button is pressed. There is a total of seven (7) parameters that can be displayed: BLADE SPEED, FEED RATE, DISTANCE REMAINING, CUTTING DISTANCE, SAMPLE THICKNESS, SPECIMEN QUANTITY, and BLADE THICKNESS.
Zero The ZERO button is used to indicate the SOFT HOME position by positioning the blade and the Micrometer Positioning System (if attached) at a starting point just before the specimen. Once a position is determined, press the ZERO button and the DISTANCE REMAINING value will change to .00, indicating the SOFT HOME position.
Increase The Increase button will incrementally increase (raise) a parameter’s value. The maximum values for the IsoMet 5000 are: •
BLADE SPEED = 5000 rpm
•
FEED RATE = .75 in/min [19 mm]
•
CUTTING DISTANCE = 8.00 inches [203 mm]
•
SAMPLE THICKNESS = .985 inch [25 mm]
•
SPECIMEN QUANTITY = 100
•
BLADE THICKNESS = .035 inch [.889 mm]
Decrease The Decrease button will incrementally decrease (lower) a parameter’s value. The minimum values for the IsoMet 5000 are: •
BLADE SPEED = 200 rpm
•
FEED RATE = .05 in/min [1.27 mm]
•
CUTTING DISTANCE = .01 inch [.26 mm]
•
SAMPLE THICKNESS = .005 inch [.12 mm]
•
SPECIMEN QUANTITY = 1
•
BLADE THICKNESS = .000 inch
NOTICE SPECIMEN QUANTITY cannot exceed the range of the CUTTING DISTANCE, SAMPLE THICKNESS, and BLADE THICKNESS total for a specimen.
9 MA112780_36.1
7/27/2009
EMERGENCY STOP Is the big red knob on the right side of the front panel. When pressed all electrical power is disconnected from the blade and all moving parts, disabling any further operations. A warning message will appear when the Emergency Stop button is pushed. To return power, turn the Emergency Stop knob clockwise. If the IsoMet was in the RUN MODE when powered off, it will return to the PAUSE MODE when powered back on. Press the CUTTING CYCLE button to continue operation.
Directional Buttons
Directional (-X, +X) X-axis Directional buttons will move the Specimen Positioning System to the left or right. These buttons are primarily used to position the specimen for cutting.
Directional (-Y, +Y) Y-axis Directional buttons will move the Blade Turret backward or forward. These buttons are primarily used to position the blade before cutting.
Home Button The Home button will automatically move the Blade Turret and Specimen Positioning System to the selected HARD HOME position.
10 MA112780_36.1
7/27/2009
IsoMet 5000 Display Screens and Commands Parameter Fields There are seven (7) different parameter fields available. Use the SCROLL button to scroll though the LCD Screens to display and highlight the parameters.
BLADE SPEED 4250rpm Functions are controlled (ON or OFF) by softkey buttons.
FEED RATE .64in/min
CUTTING BLADE CYCLE MOTOR ON ON
PUMP MOTOR ON
DISTANCE REMAINING 1.00in FEED MOTOR ON
Parameter fields are highlighted using the Scroll button.
L1 Softkey Buttons activate or deactivate a function.
BLADE SPEED, FEED RATE, and DISTANCE REMAINING parameter fields.
BLADE SPEED
FEED RATE
CUTTING LENGTH
Press the SCROLL button to display the CUTTING LENGTH parameter.
SAMPLE THICKNESS
SPECIMEN QUANTITY
BLADE THICKNESS
Continue to press the SCROLL button to display the remaining parameter fields.
11 MA112780_36.1
7/27/2009
L1 Display Screen BLADE SPEED 4250rpm
FEED RATE .64in/min
CUTTING BLADE CYCLE MOTOR ON ON
PUMP MOTOR ON
DISTANCE REMAINING 1.00in FEED MOTOR ON
L1
L1 Display Screen Commands Button [1]
CUTTING CYCLE starts, stops, and pauses the cutting cycle.
Button [2]
BLADE MOTOR toggles the blade motor ON and OFF. The blade will rotate at a set speed and the hood must be closed.
Button [3]
PUMP MOTOR toggles the coolant pump motor ON and OFF. This is the only function that will work while the hood is open.
Button [4]
FEED MOTOR toggles the feed motor ON and OFF. FEED MOTOR can be used to position the blade and will only operate when the blade is rotating.
Button [5]
Scrolls the LCD Screen between Screen L1, Screen L2, Screen L3, and Screen L4.
Pause CUTTING CYCLE To pause the cutting cycle, press the CUTTING CYCLE button once. The FEED RATE parameter will change to AUTO CUT PAUSE. When the CUTTING CYCLE is in the STOP and PAUSE mode, the L4 screen will become available.
BLADE SPEED 4250rpm CUTTING BLADE CYCLE MOTOR ON ON
AUTO CUT PAUSED PUMP MOTOR ON
DISTANCE REMAINING 1.00in FEED MOTOR ON
L1
12 MA112780_36.1
7/27/2009
L2 Display Screen
BLADE SPEED 4250rpm
FEED RATE .64in/min
CUTTING ROTATING SOFT CYCLE CHUCK START ON ON OFF
DISTANCE REMAINING 1.00in SOFT STOP OFF
L2
L2 Display Screen Commands Button [1]
CUTTING CYCLE starts, stops, and pauses the cutting cycle.
Button [2]
ROTATING CHUCK toggles the rotating chuck ON and OFF. The chuck will rotate at a constant speed.
Button [3]
SOFT START selects the Soft Start option. This will slow the selected FEED RATE for the first .06-inch [1.52 mm] of a cut.
Button [4]
SOFT STOP selects the Soft Stop option. This will slow the selected FEED RATE for the last .25-inch [6.35 mm] of a cut.
Button [5]
Scrolls the LCD Screen between Screen L2, Screen L3, Screen L4, and Screen L1.
13 MA112780_36.1
7/27/2009
L3 Display Screen BLADE SPEED 4250rpm
FEED RATE .64in/min
DISTANCE REMAINING 1.00in
SELECT CUTTING DRESS IMPERIAL ENGLISH BLADE CYCLE UNITS LANGUAGE OFF ON
L3
L3 Display Screen Commands Button [1]
CUTTING CYCLE starts, stops, and pauses the cutting cycle.
Button [2]
DRESS BLADE sets the correct blade-dressing parameters and activates the automatic dressing mechanism (if attached).
Button [3]
UNITS toggles between METRIC and IMPERIAL units of measure.
Button [4]
LANGUAGE allows the operator to select a language from the list. The languages currently available are:
Button [5]
•
English
•
French
•
German
•
Spanish
•
Portuguese
•
Japanese
•
Chinese
•
Korean
Scrolls the LCD Screen between Screen L3, Screen L4, Screen L1, and Screen L2.
14 MA112780_36.1
7/27/2009