Linvatec
Trinkle to 1/4 in. Jacobs Adaptor, Trauma Drill, Hall Series 4 System
Hall Series 4 Instruction Manual
36 Pages
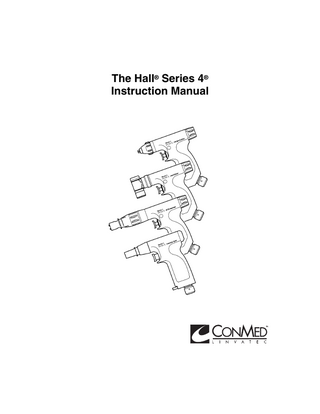
Preview
Page 1
The Hall® Series 4® Instruction Manual
Proprietary Information This manual contains information deemed proprietary to Linvatec Corporation. The information contained herein, including all of the designs and related materials, is the sole property of ConMed Linvatec and/or its licensors. ConMed Linvatec and/or its licensors reserve all patent, copyright and other proprietary rights to this document, including all design, manufacturing methodology and reproduction. This document, and any related materials, is confidential and is protected by copyright laws and shall not be duplicated, transmitted, transcribed, stored in a retrieval system, or translated into any human or computer language in any form or by any means, electronic, mechanical, magnetic, manual or otherwise, or disclosed to third parties, in whole or in part, without the prior express written consent of ConMed Linvatec. ConMed Linvatec reserves the right to revise this publication and to make changes from time to time in the contents hereof without obligation to notify any person of such revision or changes, unless otherwise required by law.
Linvatec Corporation 2000, 2003, 2006, 2008. All Rights Reserved. Printed in USA
Record the Model and Serial Numbers of the handpiece(s), and date received. Retain for future reference. Handpiece Model No.
Serial No
Date
Handpiece Model No.
Serial No
Date
Handpiece Model No.
Serial No
Date
Handpiece Model No.
Serial No
Date
Table of Contents
1.0
INTRODUCTION 1.1
Intended Use... 1
1.2
Warnings and Cautions... 1
1.3
2.0
Page
1.2.1
Warnings... 1
1.2.2
Cautions... 2
Symbol Definitions... 3
INSTALLATION and OPERATION 2.1
Power Source and Regulator Installation and Operation... 3
2.2
Equipment Installation and Operation... 6 2.2.1
2.2.2
2.2.3
Drill/Reamer... 7 2.2.1.1
Connecting Attachments... 8
2.2.1.2
Mode Selection and Operation... 9
Oscillating Saw... 10 2.2.2.1
Blade Attachment Instructions... 10
2.2.2.2
Rotating Head Instructions... 12
2.2.2.3
Operating Instructions... 12
Reciprocating Saw... 13 2.2.3.1
2.2.4
Blade Attachment and Operation Instructions... 13
Trauma Drill... 15 2.2.4.1
Connecting Attachments... 15
2.2.4.2
Mode Selection and Activation... 17
i
Table of Contents
3.0
Page
MAINTENANCE 3.1
Cleaning and Sterilizing... 19 3.1.1
Care and Cleaning Precautions... 19
3.1.2
Cleaning Instructions... 19
3.1.3
Sterilization... 20 3.1.3.1
Sterilization Warnings, Precautions and Notes... 20
3.2
Troubleshooting... 22
3.3
Specifications... 26
3.4
3.3.1
Drill/Reamer Handpiece (5067-001)... 26
3.3.2
Trauma Drill Handpiece (5067-004)... 27
3.3.3
Oscillating Saw (5067-002)... 27
3.3.4
Reciprocating Saw (5067-003)... 28
3.3.5
Environmental Requirements... 28
Attachments and Accessories... 29
ii
1.0 INTRODUCTION
1.2.1
It is recommended that personnel study this manual before attempting to operate, clean or sterilize the Hall® Series 4® Handpieces. The safe and effective use of this equipment requires the understanding of and compliance with all warnings, caution notices and instructions marked on the product and included in this manual.
Warnings
1.
Eye protection is always necessary when operating equipment. Eye injury may result without protection.
2.
Prior to each use, perform the following: •
Inspect all equipment for proper operation.
•
Ensure all attachments, accessories and hoses are able to be correctly and completely attached to the handpiece.
The intended use for the Hall Series 4 handpieces is in large bone surgery.
•
Inspect pneumatic hoses for signs of wear or damage prior to use. Discontinue use and replace immediately if any signs of wear or damage are detected.
1.2
•
Check all equipment for any air or nitrogen leakage. If leakage is noticed, return for service.
1.1
Intended Use
Warnings and Cautions
This equipment is designed for use only by medical professionals who are completely familiar with the required techniques and instructions for use of the equipment. Read and follow all warnings and cautionary notices and instructions marked on the product and included in this manual. Regular service is required to keep the Series 4 handpieces at their optimum operating performance. Refer to page 18 for details on service intervals.
1
3.
Put the instrument in the “SAFE” position before changing blades, bits, accessories or hoses, and when the instrument is not in use. Accidental activation of the instrument could cause injury.
4.
Dull bits and blades may cause heat buildup in the handpiece and the bone. It is recommended that single-use bits and blades be used.
1.2.2 1.
9.
Cautions
Handpieces are factory sealed. Do not disassemble or lubricate, as this may void the warranty. Also, do not lubricate attachments. There are no user-serviceable parts inside.
2.
Use only ConMed Linvatec and Hall accessories and attachments.
3.
Handle all equipment carefully. If a handpiece or attachment is dropped or damaged in any way, return it immediately for service.
4.
Always inspect for bent, dull or damaged blades or drill bits before each use. Do not attempt to straighten or sharpen. Do not use if damaged. After use, dispose of properly.
5.
Continually check all parts of the instrument or its attachments for overheating. If overheating is noticed, discontinue use and return the equipment for service.
6.
Never insert or remove attachments or cutting devices while the handpiece is operating.
7.
Do not pressurize hose until all fittings have been connected and checked.
8.
Use the appropriate mode selection for the appropriate function. •
Never set bone screws with the Drill/ Reamer in the “REAM” or “DRILL” position.
•
Always use the “SCREW” position for tapping threads and seating screws.
Never operate instrument above 100 psi (7 kg/cm2) dynamic pressure unless an extension hose is added to the standard 10 foot hose. Excessive pressure may cause damage to instrument and exert unusual stress on the hose.
10. The nitrogen regulator is for use only with pneumatically powered surgical devices. Adequate preventive maintenance includes servicing the regulator once every year. 11. Do not restrict exhaust vents on hose, or severely bend or kink hose, or roll equipment over hose. Damage will occur. 12. After each use, thoroughly clean and sterilize handpieces and accessories (See 3.1 “Cleaning and Sterilizing” on page 19).
2
1.3
2.0 INSTALLATION and
Symbol Definitions
OPERATION
Attention, consult accompanying documents.
2.1
Single Use Only.
WARNING: Nitrogen is not for inhalation. Does not support life. For use with powered surgical devices only.
Eye Protection Required. No user service recommended. Refer servicing to qualified ConMed Linvatec service personnel.
Research and experience have shown that waterpumped dry nitrogen is the ideal source for pneumatically-powered surgical instruments. Water-pumped dry nitrogen is 99.97% pure, and will not support combustion or corrosion. Compressed dry nitrogen is recommended as the pneumatic power source. It is available in standard cylinders.
Indicates product component should not be sterilized. Indicates product component should not be immersed in any type of fluid.
Compressed dry nitrogen must meet the following specifications to ensure optimum safety for both patient and instrument.
Indicates handpiece should not be immersed in any fluid.
Nitrogen Content: 99.97% pure, dry nitrogen.
Indicates product should not be oiled or lubricated. Rx ONLY
Power Source and Regulator Installation and Operation
Quality Assurance: To obtain the quality of gas needed, “water-pumped dry nitrogen, or liquid nitrogen, pumped dry” should be specified.
Caution: Federal Law restricts this device to sale by or on the order of a physician
Nitrogen is readily available from gas supply houses in H cylinders holding slightly more than 300 cubic feet (8.50 cubic meters). Initial set-up costs are relatively inexpensive as compared to compressed air. Nitrogen can be placed in the operating room or in a storage area and piped into the operating room. Manifold systems are available to eliminate frequent tank changes.
3
2.
CAUTION: Do not exceed 100 psi (7 kg/cm2) operating pressure unless a hose longer than the standard 10 ft. Universal Hose (5052-010) or extension hose is used. Add an additional 1 psi for every extra foot of hose. The Series 4 handpieces should be operated at 100 psi (7 kg/cm2) for maximum operating efficiency, and should be monitored by the operating pressure gauge of the regulator. Lower pressure setting can be set for lower speed and torque requirements. Pressure must be set with the instrument running to ensure proper operating pressure.
NOTE: The threaded adaptor of the nitrogen regulator is designed to fit nitrogen fittings only. Incompatibility of the regulator and tank indicates a gas source other than nitrogen or an improper regulator for use with a nitrogen tank.
Never start a procedure if the operating pressure gauge indicates less than 500 psi (35.1 kg/cm2) in the tank. Never run the tank pressure below 200 psi (14.0 kg/cm2). The tank should be thoroughly wiped off with disinfectant and draped prior to placement in the operating room. Always have the tank securely fastened to a stable object. 1.
Install the regulator with a 1 1/8 inch wrench, or adjustable wrench.
3.
Prior to set-up in the operating room, open the tank valve (counterclockwise) slowly and allow enough gas to escape to blow out any debris that may have accumulated in the valve. Stay clear of the opening and the back of the tank during this procedure. Return the valve to the closed position.
4
Once the regulator is securely installed, ensure the regulator knob is in the full off position by turning the regulator control knob counterclockwise. SUDDEN PRESSURE EXERTED TO THE REGULATOR MAY CAUSE INTERNAL DAMAGE.
4.
7.
Slowly turn the tank valve fully open (counterclockwise). This will allow nitrogen to pressurize the regulator.
Before removing the instrument from the regulator: (a) Close the tank valve by turning it clockwise. (b) Activate the instrument to bleed off line pressure. (c) Turn the pressure regulator knob counterclockwise until it stops. (d) Turn the female Schrader to the right to disengage the male Schrader fitting.
5.
Insert the male Schrader end of the hose into the female Schrader on the regulator with an upward thrust.
6.
Operating pressure is established by gradually turning the regulator control knob clockwise. ALWAYS establish the designated pressure on the operating pressure gauge with the instrument running.
(e) The hose can then be removed from the connector. Hold the end of the hose securely when disengaging the male Schrader fitting to prevent possible damage to the diffuser.
5
2.2
Equipment Installation and Operation
1.
Place the handpiece in the “SAFE” position.
2.
To connect the handpiece to the hose. (a) Insert the coupling end of the hose into the fitting on the bottom of the handpiece.
3.
Attached to the Universal Hose (5052-010) is the Hall Hose Handler*. This clip allows fixation of the hose to the surgical drape, reducing the problem of the hose slipping off the patient.
4.
The Velcro® strap allows the hose to be coiled, thus reducing excess hose length. In addition, the VELCRO strap may be used with any additional hose and/or cable.
* U.S. Patent 4,639,980
(b) Twist the hose coupling to the right (clockwise) and slightly pull on the hose so the internal pins securely engage in the indentations.
6
❶
❹
2.2.1
❷
❸
❷ Direction Control Knob - Used to select
Drill/Reamer
the operating direction between “FWD” (forward) “REV” (reverse) and “SAFE”.
❶ Mode Selector - Used to select the
Place the control knob in the “SAFE” position when changing accessories. To activate the handpiece, place the control knob in either “FWD” or “REV”.
operating mode of the handpiece between “DRILL” “SCREW” and “REAM”. “DRILL” Position: Used for Drilling and Pin Insertion.
❸ Activation Trigger - Used to activate the
“REAM” Position: Used for Femoral Reaming, Acetabular Reaming and Pin Insertion.
handpiece when the direction control knob is in either “FWD” or “REV”.
❹ Zimmer/Hudson Snap-Lock Chuck -
“SCREW” Position: Used for Tapping and Setting Bone Screws.
Used to quickly attach accessories.
7
2.2.1.1
1.
Connecting Attachments
To connect attachments: (a) Place the Direction Control Knob in the “SAFE” position.
The Drill/Reamer Handpiece has a combination collet which will accept all the illustrated shank styles below, without the need for an adaptor. AO shanked products (not pictured) may also be used with the Drill/Reamer Handpiece, utilizing the Zimmer to AO Adaptor. Zimmer Hudson Modified Hudson Shank Shank Shank
(b) Firmly grasp the chuck and pull back toward the handpiece. When inserting Trinkle or AO products, care should be taken to pull back on the adaptor itself, not the handpiece snap-lock chuck.
Trinkle shank accessories must utilize the Zimmer to Trinkle adaptor (1384-028). Affix the Trinkle adaptor into the Zimmer/Hudson snap-lock chuck as described in step 1.
(c) Insert the shank of the attachment into the chuck, then release the chuck.
AO Shank accessories must utilize the AO adaptor (1384-034). Affix the AO adaptor into the Zimmer/Hudson snap-lock chuck as described in step 1.
NOTE: Be certain the Trinkle or AO Adapter is properly seated. When properly affixed, the inner housing will be flush with the outer housing.
8
The Drill/Reamer is cannulated and will accept pins up to 0.156 inch diameter or 4.0mm.
2.2.1.2
Mode Selection and Operation
WARNINGS:
2.
To attach the Torque Control Handle to the instrument:
(a) Insert the handle into the torque control receptacle on the side of the handpiece.
•
Always make sure you are in the proper mode before the handpiece is activated.
•
Never set bone screws with the handpiece in the “REAM” or “DRILL” position. Always use the “SCREW” position for tapping threads and seating bone screws.
1.
Twist the mode selector ring until the arrow is aligned with the arrow on the handpiece for the desired position.
2.
Twist the direction control knob from “SAFE” to the desired operating direction (“FWD” or “REV”).
3.
Depress the trigger to activate the handpiece.
(b) Twist the Torque Control Handle until it locks securely into position. 3.
The Torque Control handle is easily removed by twisting and pulling out on the handle.
NOTE: Securely attach the torque control handle when using heavy reamers or attachments. The torque control handle will assure maximum control of the handpiece.
9
❶
❷
❸ ❹
❺ ❻
2.2.2
Oscillating Saw
2.2.2.1
❶ Control Knob - Place this knob in the
1.
“ON” position to activate the handpiece. Place in the “SAFE” position before changing blades, bits, accessories or hoses, and when the instrument is not in use.
Blade Attachment Instructions
To affix a blade to the blade-locking collet*: (a) Place the control knob in the “SAFE” position.
❷ Head Locking Collar - Allows the rotating head to be rotated and locked in any of 12 positions.
❸ Rotating Head - Houses the cutting blade and rotates to any of 12 positions at 30° intervals for appropriate surgical access.
❹ Blade Locking Collet - Holds the blade in place.
❺ Blade Locking Knob - Locks the blade securely in place.
❻ Activation Trigger - Press to operate the
handpiece when the control knob is in the “ON” position.
* U.S. Patent 5,265,343 10
(b) Open the blade-locking collet by rotating the blade-locking knob in the direction of the arrow to the “OPEN” position.
(d) Rotate the blade locking knob to the closed position. (c) Insert the blade at the desired angle and align the blade holes with the bladepositioning pins. Be sure that the proper saw blades are used with the collet. Micro Sagittal Saw Blades may not be used in the wrenchless collet, only Hall series 5071-xxx blades can be used.
11
2.2.2.2 1.
Rotating Head Instructions
2.2.2.3
The rotating head may be set in any of 12 positions at 30° intervals for appropriate surgical access. To change positions and cutting planes:
1.
Operating Instructions
To operate the handpiece: (a) Twist the control knob from the “SAFE” position to the “ON” position:
(a) Grasp the head locking collar firmly and pull towards the back of the handpiece.
(b) Depress the activation trigger.
(b) Rotate the head and blade to the desired position. Release the head locking collar.
12
❶
❷
❸
❹
2.2.3
Reciprocating Saw
2.2.3.1
❶ Blade Collet - Holds the blade in place.
1.
❷ Collet Locking Knob - Used to lock the
Blade Attachment and Operation Instructions
To affix a blade to the handpiece: (a) Place the control knob in the “SAFE” position.
blade collet.
❸ Control Knob - Place this knob in the
“ON” position to activate the handpiece. Place in the “SAFE” position before changing blades, bits, accessories or hoses, and when the instrument is not in use.
❹ Activation Trigger - Press to operate the
handpiece when the control knob is in the “ON” position.
13
2.
(b) Open the blade collet by turning the collet locking knob clockwise for adequate blade width.
To operate the handpiece: (a) Twist the control knob from the “SAFE” position to the “ON” position.
(c) Insert the shank of the blade into the slot and seat completely.
(b) Depress the activation trigger.
(d) Blades may be locked in any position. Four (4) detents are provided for accurate 90° positioning. Before locking the collet, grasp the blade at the base of the collet and turn to the desired position.
(e) Turn the collet locking knob counterclockwise to firmly secure the blade.
14
2.2.4
Trauma Drill
2.2.4.1 1.
❶
Connecting Attachments
Place handpiece in the “SAFE” position. (a) Rotate the trigger either left or right.
❷
❸ Attachment of Trinkle Shank Accessories:
❶ Combination Trinkle/AO Collet -
Accepts the various Trinkle and AO shank accessories.
❷ Safety/Activation Trigger - Rotate either
left or right to the “SAFE” position when attaching/removing attachments, accessories and hoses. Rotate to the vertical position to activate the handpiece (See illustration in 2.2.4.1 “Connecting Attachments” on page 15).
❸ Direction Control Lever - Used to select
the operating direction between “FWD” (forward) “SCREW” and “REV” (reverse).
15
1.
Pull back the outer collet sleeve.
2.
Insert the Trinkle shank into the collet. The spring-loaded inner sleeve will retract.
3.
Attachment of AO Drill Accessories:
Release the collet sleeve.
4.
Once the shank has been totally inserted, rotate the accessory until it becomes completely engaged. Pull the accessory firmly to ensure proper engagement.
5.
To remove the accessory, pull back the outer sleeve and pull the accessory out.
16
1.
Align the flat portion of the accessory shank with the black arrow on the collet sleeve, and insert the accessory into the collet.
2.
Insert the shank as far as it will go without pulling back the collet sleeve. Twist the shank to make sure it is aligned properly. If it is, it will not spin in the collet.
3.
Pull back on the collet sleeve while pushing the shank further into the collet.
4.
Release the collet sleeve. The shank is now locked into the collet. Pull the accessory firmly to ensure proper engagement.
5.
To remove the accessory, pull back the outer sleeve and pull the accessory out.